
- •ОГЛАВЛЕНИЕ
- •ВВЕДЕНИЕ
- •2.5.3. Чугуны
- •ГЛАВА 3. ПРОИЗВОДСТВО МЕТАЛЛИЧЕСКИХ КОНСТРУКЦИОННЫХ МАТЕРИАЛОВ
- •ГЛАВА 4. СПОСОБЫ ФОРМООБРАЗОВАНИЯ ЗАГОТОВОК ДЕТАЛЕЙ МАШИН
- •ГЛАВА 5. ЛИТЕЙНОЕ ПРОИЗВОДСТВО – СПОСОБ ПЕРВИЧНОГО ФОРМООБРАЗОВАНИЯ ЗАГОТОВОК ИЗ ЖИДКОПОДВИЖНЫХ КОНСТРУКЦИОННЫХ МАТЕРИАЛОВ
- •5.3.3. Модельный комплект
- •5.3.5.1. Литье по выплавляемым моделям
- •5.3.5.3. Литье в кокиль
- •5.3.5.4. Литье под давлением
- •5.3.5.5. Центробежное литье
- •6.5.2.1. Прессование
- •6.5.2.2. Волочение
- •ГЛАВА 7. ТЕХНОЛОГИЯ ПОЛУЧЕНИЯ СВАРНЫХ И ПАЯНЫХ ЗАГОТОВОК
- •7.2.1. Электродуговая сварка
- •7.4. Пайка
- •ГЛАВА 8. КОМБИНИРОВАННЫЕ СПОСОБЫ ПОЛУЧЕНИЯ ЗАГОТОВОК
- •ГЛАВА 9. ПОЛУЧЕНИЕ ЗАГОТОВОК ДЕТАЛЕЙ МАШИН ИЗ НЕМЕТАЛЛИЧЕСКИХ И КОМПОЗИЦИОННЫХ МАТЕРИАЛОВ
- •9.1.3. Спекание
- •ГЛАВА 10. ТЕХНОЛОГИЧЕСКИЕ ПРОЦЕССЫ ОБРАБОТКИ ЗАГОТОВОК В СОВРЕМЕННОМ МАШИНОСТРОЕНИИ. ТЕОРЕТИЧЕСКИЕ И ТЕХНОЛОГИЧЕСКИЕ ОСНОВЫ МЕХАНИЧЕСКОЙ ОБРАБОТКИ
- •10.1.8. Смазывающе-охлаждающие технологические среды
- •10.9.1. Резьбонарезание
- •10.9.2. Зубонарезание
- •ГЛАВА 12. ТЕХНОЛОГИЧЕСКИЕ ПРОЦЕССЫ ФОРМИРОВАНИЯ ЗАДАННЫХ ФИЗИКО-МЕХАНИЧЕСКИХ И ЭКСПЛУАТАЦИОННЫХ СВОЙСТВ ПОВЕРХНОСТНЫХ СЛОЕВ
- •ГЛАВА 13. ОСНОВЫ СБОРОЧНЫХ РАБОТ И ТЕХНОЛОГИЧЕСКОЙ ПОДГОТОВКИ ПРОИЗВОДСТВА
- •ГЛАВА 14. ПРОБЛЕМЫ СОВРЕМЕННОГО МАШИНОСТРОИТЕЛЬНОГО ПРОИЗВОДСТВА И ОБЕСПЕЧЕНИЕ ЭКОЛОГИЧЕСКОЙ БЕЗОПАСНОСТИ ПРОИЗВОДСТВЕННЫХ ПРОЦЕССОВ
- •БИБЛИОГРАФИЧЕСКИЙ СПИСОК

ГЛАВА 9. ПОЛУЧЕНИЕ ЗАГОТОВОК ДЕТАЛЕЙ МАШИН ИЗ НЕМЕТАЛЛИЧЕСКИХ И КОМПОЗИЦИОННЫХ МАТЕРИАЛОВ
9.1. Порошковаяметаллургия
Порошковой металлургией называется область техники, охватывающая совокупность методов изготовления: порошков металлов и сплавов, полуфабрикатов и изделий из них или их смесей с неметаллическими порошками.
Технологический процесс производства изделий методом порошковой металлургии состоит из следующих основных операций: получение металлического порошка или смеси порошков разнородных материалов, формование, спекание и дополнительная обработка спеченных порошковых изделий (механическая обработка, калибровка, термическая и химико-термическая обработка и др.). Однако в производственной практике нередко встречаются отклонения от этой совокупности элементов технологии. Например, процессы формования и спекания можно совместить в одной операции. При этом использование порошкообразного вещества в качестве исходного и применение нагрева до температур ниже точки плавления основного компонента смеси остаются неизменными в любом из вариантов технологии порошковой металлургии.
Основные направления развития порошковой металлургии связаны прежде всего с преодолением затруднений в осуществлении процесса литья тугоплавких редких металлов (вольфрам, молибден, тантал и др.) и с возможностями производства порошковых материалов и изделий со специфическими свойствами, не достижимыми другими технологическими способами, например получение композитов типа: вольфрам – медь, твердых сплавов, пористых подшипников, фильтров и пр.
Метод порошковой металлургии позволяет изготовлять многие изделия (например, детали машин и приборов) из обычных материалов и с обычными свойствами, но с лучшими технико-экономическими показателями производства по сравнению с изделиями, полученными традиционной технологией. При изготовлении изделий методом порошковой металлургии потери материалов составляют до 5–7 %, а при металлообработке литья и даже проката в стружку теряется до 60–70 %.
Наконец, важным направлением порошковой металлургии является производство металлических порошков, предназначенных для непосредственного использования (краски, пиротехнические взрывчатые смеси, катализаторы, сварочные материалы и др.), в том числе для упрочнения и защиты от коррозии деталей машин и приборов методами напыления.
Метод получения порошков и природа материала определяют свойства порошков:
Технология конструкционных материалов. Учебное пособие |
-255- |
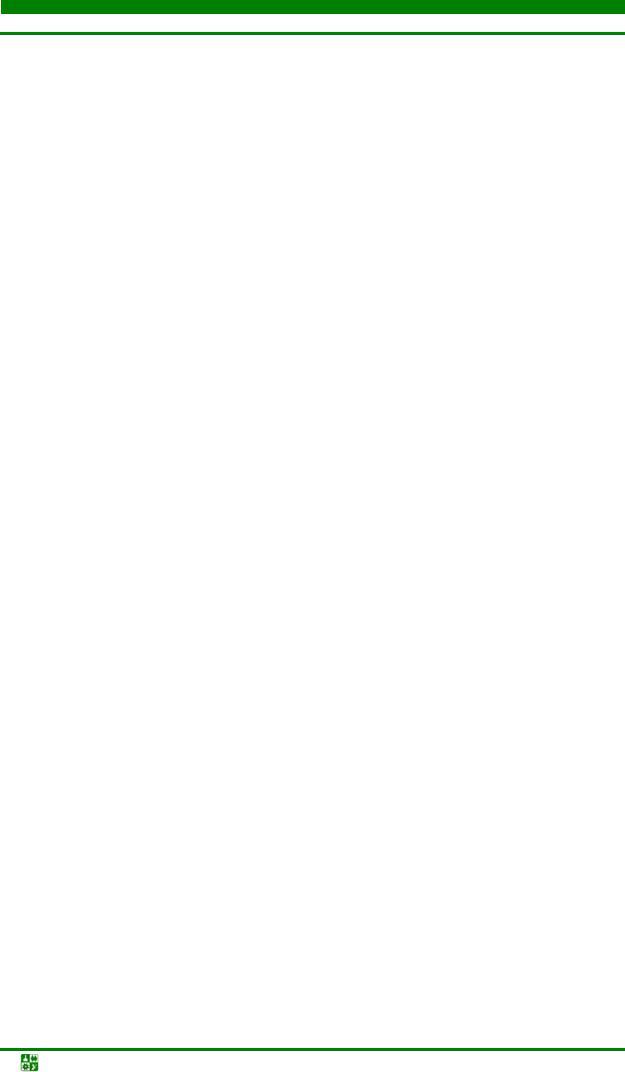
ГЛАВА 9.ПОЛУЧЕНИЕ ЗАГОТОВОК ДЕТАЛЕЙ МАШИН ИЗ НЕМЕТАЛЛИЧЕСКИХ И КОМПОЗИЦИОННЫХ МАТЕРИАЛОВ
9.1. Порошковая металлургия
химические (содержание компонентов, примесей и загрязнений, пирофорность и токсичность);
физические (форма, размер, удельная поверхность, истинная плотность и микротвердость частиц);
технологические (насыпная плотность, текучесть, формуемость и прессуемость порошка).
В некоторых случаях необходимо знание и более специфических свойств порошка, например цвета, блеска, кроющей способности красителяиз него и пр.
Очень часто некоторые свойства порошка одного и того же металла существенно изменяются в зависимости от метода производства. Порошки, идентичные по химическому составу, могут иметь разные физические характеристики и резко различаться по технологическим свойствам, что приводит к значительным изменениям условий дальнейшего превращения порошка в готовые изделия и влияет на их свойства.
9.1.1. Методыполученияпорошков
Разнообразие требований, предъявляемых к порошкам в зависимости от области их применения, а также свойства самих металлов объясняют существование большого числа различных методов производства металлических порошков. Общепринятым является условное деление этих методов на физико-химические и механические.
К физико-химическим методам относят технологические процессы производства порошков, связанные с глубокими физико-химическими превращениями исходного сырья. В результате получаемый порошок по химическому составу и структуре существенно отличается от исходного материала. Основными являются методы восстановления металлов, электролиз и термическая диссоциация карбонилов.
Механические методы обеспечивают превращение исходного материала в порошок без существенного изменения его химического состава. Чаще всего используют размол твердых материалов в мельницах различных конструкций и диспергирование расплавов.
Физико-химические способы получения порошков в целом более универсальны, чем механические. Возможность использования дешевого сырья (отходы производства в виде окалины, оксидов и т. д.) делает многие физико-химические способы экономичными. Порошки ряда тугоплавких металлов, а также порошки сплавов и соединений на их основе могут быть получены только физико-химическими способами.
Выбирая метод получения металлического порошка, учитывают прежде всего необходимость обеспечения требований, предъявляемых к конечной продукции из него, а также экономическую оценку соответствующих технологических процессов − себестоимость порошка, размер капиталовложений, стоимость дальнейшей переработки порошка в изделия.
Технология конструкционных материалов. Учебное пособие |
-256- |
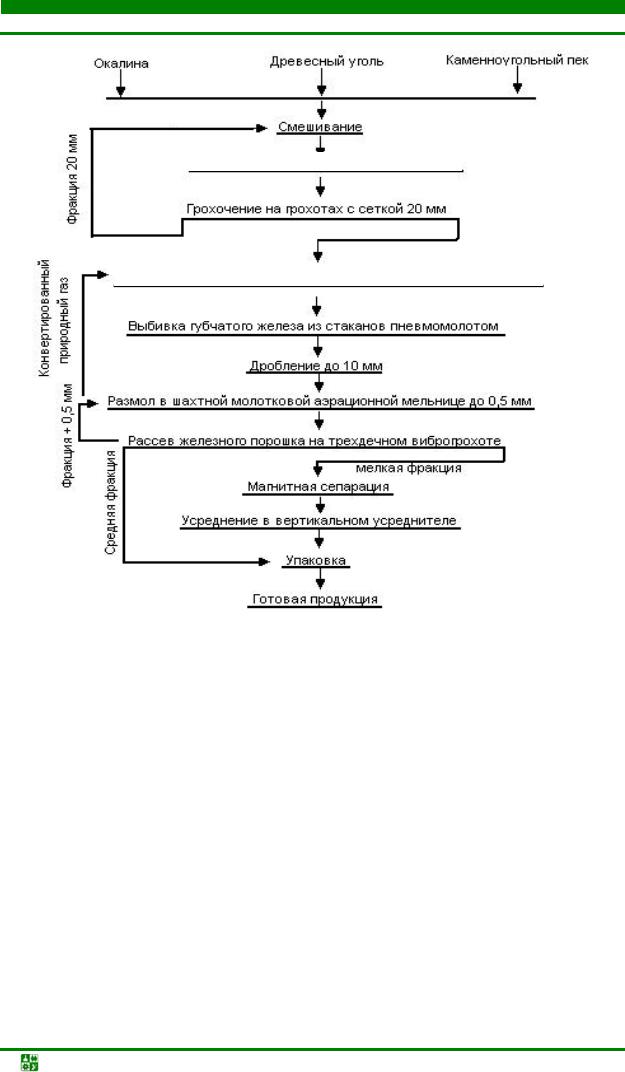
ГЛАВА 9.ПОЛУЧЕНИЕ ЗАГОТОВОК ДЕТАЛЕЙ МАШИН ИЗ НЕМЕТАЛЛИЧЕСКИХ И КОМПОЗИЦИОННЫХ МАТЕРИАЛОВ
9.1. Порошковая металлургия
Брикетирование при давлении 15−20 МПа
Восстановление в вертикальной электропечи при 1000−1100 °С
Рис. 9.1. Разновидность технологической схемы получения железного порошка методом восстановления окалины
Механические методы получения порошков могут применяться как самостоятельные, а также входить в схему производства порошка физикохимическими методами (рис. 9.1).
Диспергирование расплавов – это способ получения металлического порошка распылением расплавленного металла или сплава струей сжатого газа, жидкости или механическим путем.
Распылением получаются порошки железа, сталей, чистых металлов, в том числе легких и тугоплавких, а также сплавов на их основе.
Распыление эффективно для получения порошков многокомпонентных сплавов и обеспечивает объемную равномерность химического состава, оптимальное строение и тонкую структуру каждой частицы. Методы диспергирования позволяют увеличить выпуск порошков с контролируемыми свойствами.
Технология конструкционных материалов. Учебное пособие |
-257- |
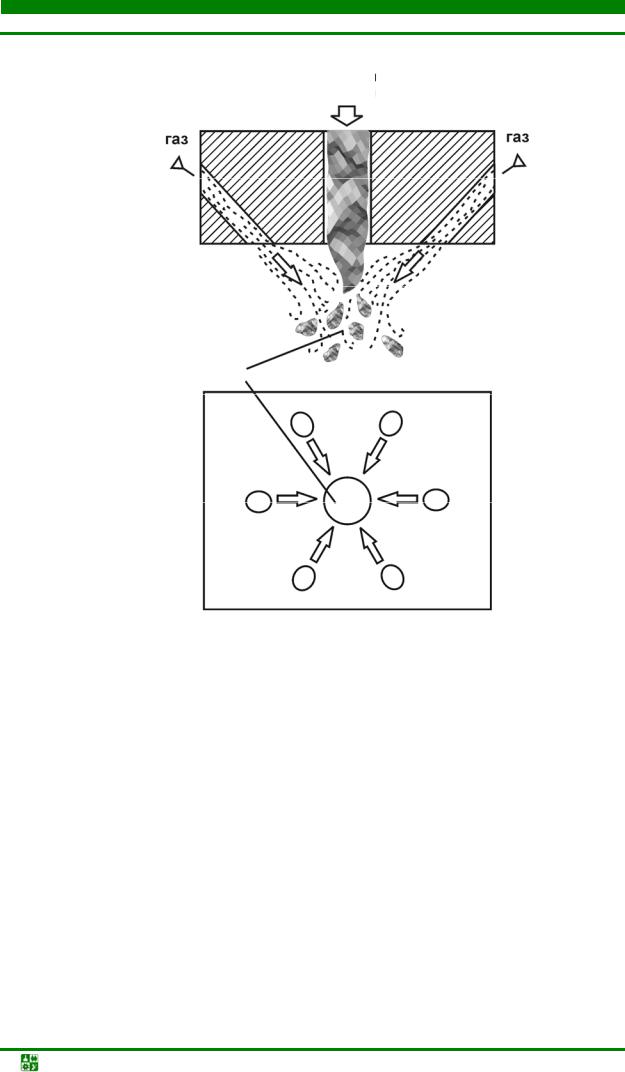
ГЛАВА 9.ПОЛУЧЕНИЕ ЗАГОТОВОК ДЕТАЛЕЙ МАШИН ИЗ НЕМЕТАЛЛИЧЕСКИХ И КОМПОЗИЦИОННЫХ МАТЕРИАЛОВ
9.1. Порошковая металлургия
Жидкий
металл
Газ |
|
Газ |
Фокус
распыления
Рис. 9.2. Распыление жидкого сплава инертным газом
Одним из распространенных способов распыления для многотоннажного получения порошков быстрорежущих сталей является диспергирование газом (аргоном, гелием или азотом). Схема с вертикальным расположением форсунки, где на струю расплавленного металла под углами 60° направлены потоки подогретого газа с дозвуковой и сверхзвуковой скоростью, представлена на рис. 9.2.
Полученные порошки подвергаются восстановительному отжигу. Механические способы получения порошков, основанные на измельче-
нии твердых тел, часто совмещают с приготовлением смесей порошков. Из методов измельчения наибольшее распространение получили:
•обработка металлов резанием с образованием мелкой стружки или
опилок;
•измельчение металлов в паровых, вихревых, центробежных, молотковых и других мельницах.
Технология конструкционных материалов. Учебное пособие |
-258- |
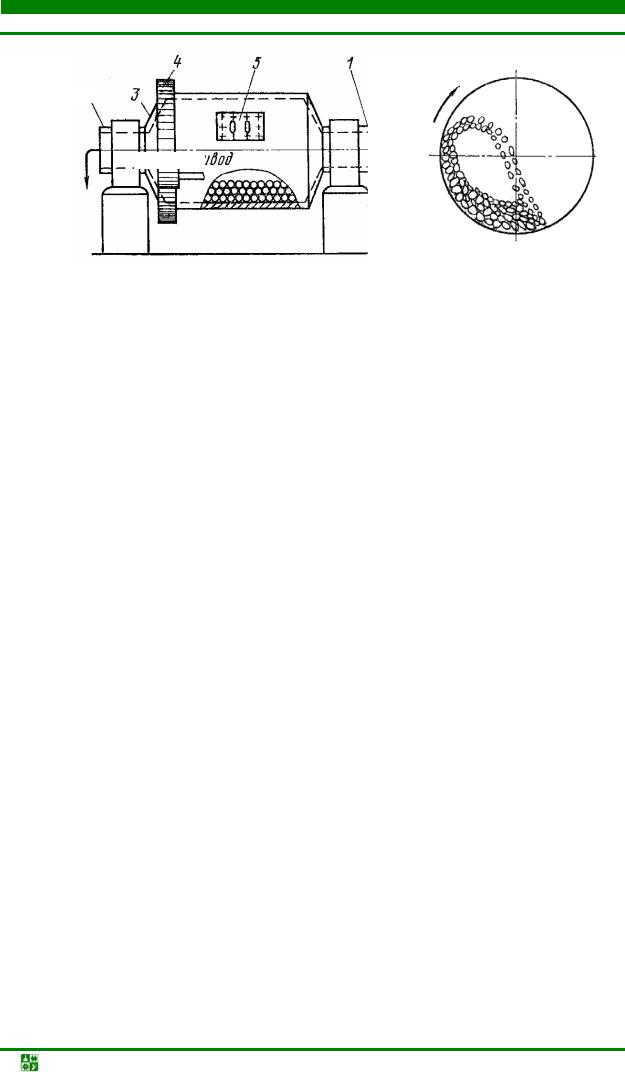
ГЛАВА 9.ПОЛУЧЕНИЕ ЗАГОТОВОК ДЕТАЛЕЙ МАШИН ИЗ НЕМЕТАЛЛИЧЕСКИХ И КОМПОЗИЦИОННЫХ МАТЕРИАЛОВ
9.1. Порошковая металлургия
4 |
|
5 |
|
1 |
|
|
|
|
|
|
|
|
|
|
2 3
Привод
а |
б |
|
Рис. 9.3. Барабанная шаровая мельница: а – схема устройства; б – схема перемещения размольных тел и измельчаемого материала
Одним из наиболее распространенных видов размольного оборудования являются барабанные мельницы. В простейшем конструктивном варианте такая мельница представляет собой вращающийся вокруг горизонтальной оси барабан, внутри которого находится измельчаемый материал и мелющие тела (рис. 9.3, а). Мелющие тела чаще всего имеют форму шара и изготовлены из стали.
Процессы, происходящие в рабочем объеме барабанных мельниц, сводятся к следующему: мелющие тела поднимаются на некоторую высоту в направлении вращения барабана, до тех пор пока угол подъема не превысит угол естественного откоса, после чего шары скатываются или падают вниз и измельчают материал, истирая и раздалбливая его.
Измельчение может быть мокрым и сухим. Считается, что мокрое измельчениеболееэффективно и улучшает экологическиехарактеристики оборудования.
9.1.2. Формообразованиезаготовок
Прессование изделий из порошков начинается с приготовления смеси и включает предварительный отжиг, сортировку порошка по размерам частиц и смешение порошков разного состава.
Предварительный отжиг порошка способствует восстановлению оксидов и снимает наклеп, возникающий при механическом измельчении исходного материала.
В металлические порошки вводят технологические присадочные материалы различного назначения: пластификаторы (парафин, стеарин, олеиновая кислота и др.), облегчающие процесс прессования и способствующие получению заготовок высокого качества; легкоплавкие материалы, улучшающие процесс спекания; летучие вещества, обеспечивающие получение заданной пористости.
Технология конструкционных материалов. Учебное пособие |
-259- |
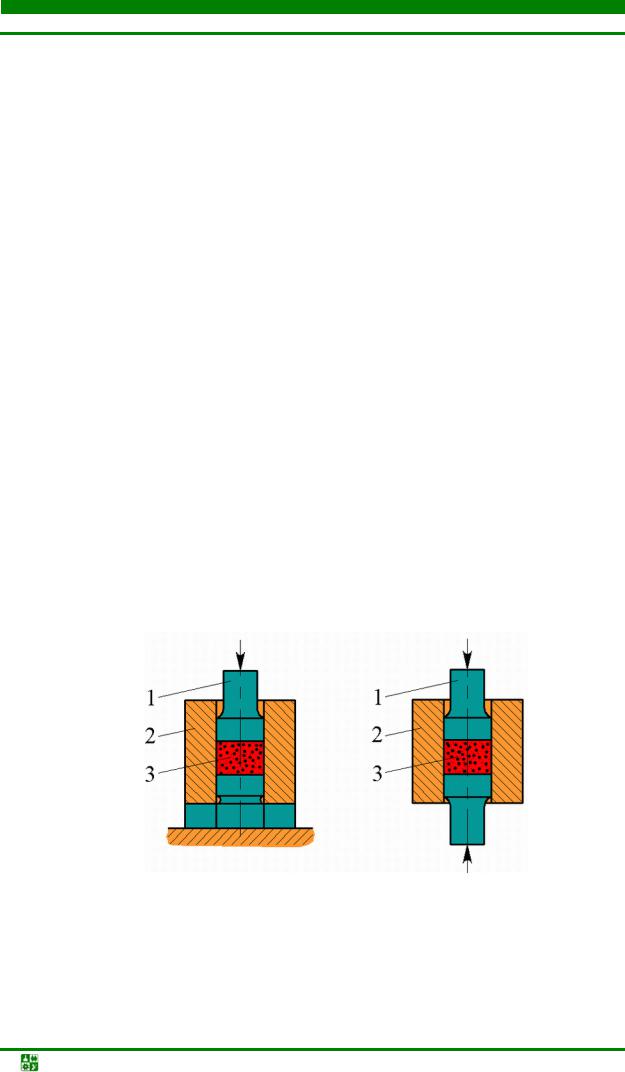
ГЛАВА 9.ПОЛУЧЕНИЕ ЗАГОТОВОК ДЕТАЛЕЙ МАШИН ИЗ НЕМЕТАЛЛИЧЕСКИХ И КОМПОЗИЦИОННЫХ МАТЕРИАЛОВ
9.1. Порошковая металлургия
Заготовки из металлических порошков получают прессованием (холодным, горячим, гидростатическим), прокаткой и др.
Холодное прессование. При холодном прессовании в закрытых прессформах (рис. 9.4, а) определенное количество подготовленного порошка 3 засыпают в пресс-форму 2 и прессуют пуансоном 1.
Порошковые металлы, в отличие от металлов, полученных традиционными методами, при деформации изменяют не только форму, но и объем. Обычно при формовании высота заготовки по отношению к высоте насыпанного порошка уменьшается в 3−4 раза и более.
Прочность получаемой заготовки обеспечивается в основном силами механического сцепления частиц порошка. С увеличением давления прессования прочность заготовки возрастает. Давление распределяется неравномерно по высоте прессуемой заготовки вследствие влияния трения порошка о стенки пресс-формы, в результате чего заготовки получаются с различной прочностью и пористостью по высоте.
В зависимости от размеров и сложности прессуемых заготовок применяют одно- и двустороннее прессование. Односторонним прессованием (рис. 9.4, а) получают заготовки простой формы с отношением высоты к диаметру меньше единицы и заготовки типа втулок с отношением наружного диаметра к толщине стенки меньше трех. Двустороннее прессование (рис. 9.4, б) применяют для формообразования заготовок сложной формы. В этом случае требуемое давление для получения равномерной плотности снижается на 30−40 %. Давление прессования зависит от требуемой плотности, формы прессуемой заготовки, вида прессуемого порошка и других факторов. Использование вибрационного прессования позволяет в десятки раз уменьшить необходимое давление.
1 |
|
1 |
|
||
2 |
|
|
|
|
|
2 |
|
||||
|
|
|
|
|
|
|
|
|
|
|
|
3 |
|
3 |
|
||
|
|
|
|
|
|
а |
б |
Рис. 9.4. Схемы одностороннего (а) и двустороннего (б) холодного прессования: 1 − пуансон; 2 − пресс-форма; 3 − порошок
В процессе прессования частицы порошка подвергаются упругим и пластическим деформациям, в результате чего в заготовке накапливаются
Технология конструкционных материалов. Учебное пособие |
-260- |
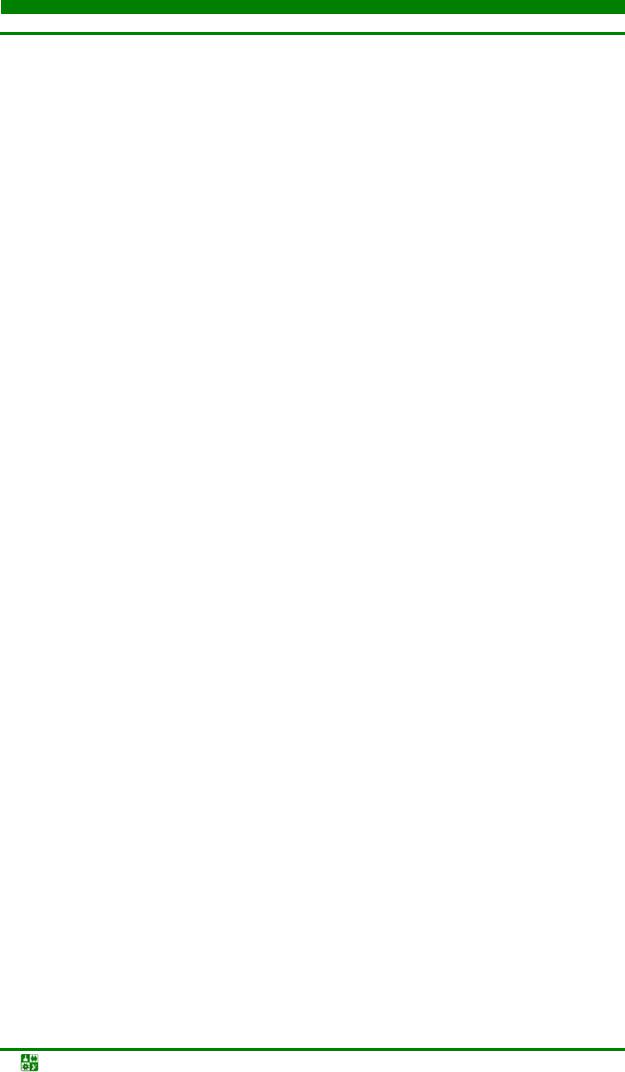
ГЛАВА 9.ПОЛУЧЕНИЕ ЗАГОТОВОК ДЕТАЛЕЙ МАШИН ИЗ НЕМЕТАЛЛИЧЕСКИХ И КОМПОЗИЦИОННЫХ МАТЕРИАЛОВ
9.1. Порошковая металлургия
значительные напряжения. После извлечения из пресс-формы заготовки, размеры ее изменяются за счет упругого последствия.
Горячее прессование. При горячем прессовании технологически совмещаются процессы формообразования и спекания заготовки. Температура горячего прессования составляет обычно 0,6–0,8 температуры плавления порошка. Благодаря нагреву пресс-формы или порошка в ней процесс уплотнения протекает гораздо интенсивнее, чем при холодном прессовании. Это позволяет значительно уменьшить необходимое давление прессования. Горячим прессованием получают материалы, характеризующиеся высокой прочностью, плотностью и однородностью структуры. Этот метод применяют для таких плохо прессуемых и плохо спекаемых композиций, как тугоплавкие металлоподобные соединения (карбиды, бориды и т. д.). Малая стойкость пресс-форм, необходимость проведения процесса в среде защитных газов ограничивают применение горячего прессования и обусловливает его использование только в тех случаях, когда другие методы порошковой металлургии не обеспечивают заданных эксплуатационных свойств.
Пресс-формы стоят дорого, поэтому изготовление прессовок в них является экономически целесообразным в условиях крупносерийного массового производства (как правило, изготовление деталей массой до 1 кг), когда стоимость пресс-форм и технического оборудования окупается.
Гидростатическое прессование применяют для получения металлокерамических заготовок, к которым не предъявляют высоких требований по точности. Сущность процесса заключается в том, что порошок 6 (рис. 9.5), заключенный в эластичную оболочку 5, подвергают равномерному и всестороннему обжатию в специальных герметизированных камерах. Отсутствие внешнего трения способствует получению заготовок равномерной плотности и снижению требуемого давления. В качестве рабочей жидкости 4 используют масло, воду, глицерин и др.
Гидростатическое формование металлических порошков наиболее широко применяют при изготовлении изделий и заготовок, которые в дальнейшем идут на обработку давлением. С развитием реактивной авиации и ракетной техники возникла необходимость получения крупных поковок и листов из тугоплавких металлов и их сплавов. Задача получения крупных (заготовок равномерной плотности была решена с помощью гидростатического формования.
Прокатка металлических порошков, т. е. их непрерывное формование, является одним из перспективных способов порошковой металлургии, что объясняется рядом преимуществ этого метода. Прокаткой можно получить однородные по плотности изделия большой площади, любых размеров по длине, сравнительно большие по ширине при очень малой толщине. При этом не требуется мощного прессового оборудования, как это имеет место при обычных методах формования. При прокатке порошков резко возрастают
Технология конструкционных материалов. Учебное пособие |
-261- |
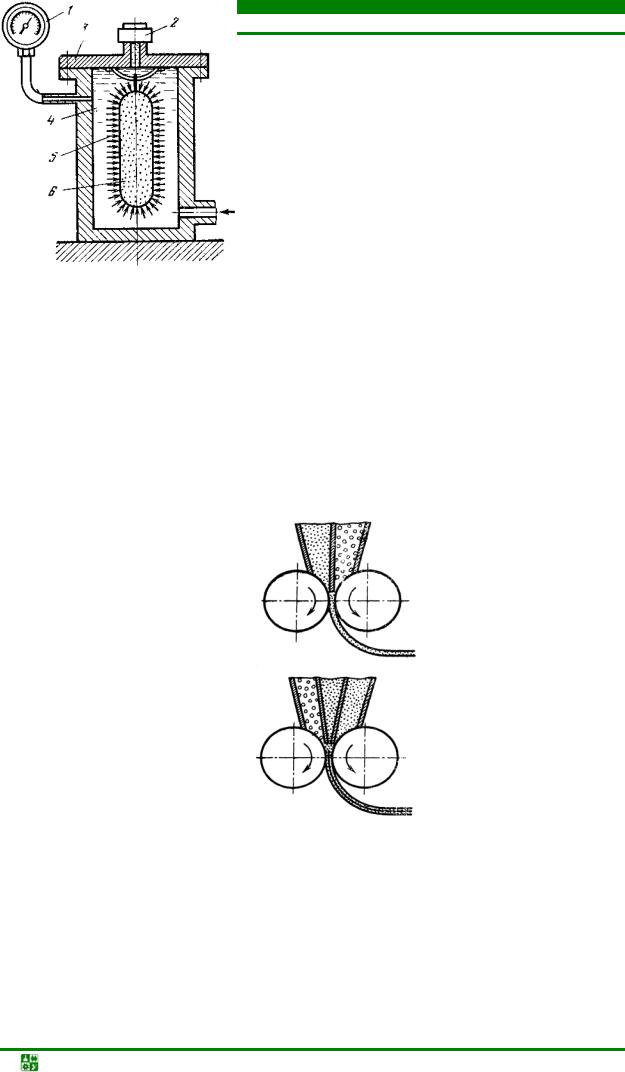
ГЛАВА 9.ПОЛУЧЕНИЕ ЗАГОТОВОК ДЕТАЛЕЙ МАШИН ИЗ НЕМЕТАЛЛИЧЕСКИХ И КОМПОЗИЦИОННЫХ МАТЕРИАЛОВ
9.1. Порошковая металлургия
производительность и экономичность процесса, поскольку не требуется больших капитальных затрат на литейные цеха и цеха горячей прокатки слитков, значительно сокращается число технологических операций и повышается выход годной продукции.
1
2
3
4
5
6
Рис. 9.5. Схема установки гидростатического формования:
1 − манометр; 2 – предохранительный клапан; 3 – крышка; 4 – жидкость; 5 – эластичная оболочка; 6 – деформируемый порошок
а
б
Рис. 9.6. Методы прокатки порошков: а – двухслойной; б – трехслойной
Метод прокатки металлических порошков (рис. 9.6) состоит в следующем. Подготовленная шихта засыпается в бункер, откуда поступает в зазор между вращающимися навстречу друг другу валками. Металлический порошок, продвигаясь в очаге деформации – области, ограниченной упорами бункера и частью поверхности валков, уплотняется и формируется в ленту. Выходя из валков, лента попадает на направляющую, откуда поступает в
Технология конструкционных материалов. Учебное пособие |
-262- |