
ТСМ I
.pdfТехнологии получения шлакопортландцемента:
1.Изготовление клинкера
2.Подготовка гранулированного шлака
3.Совместный помол клинкера, шлака и гипса.
Гранулированный шлак нужно сушить до влажности 1-2% (сушильные барабаны),температура сушки не выше 700 ОС, что исключает процесс рекристаллизации шлака. (Рекристаллизация - рост кристаллов, укрепление кристаллов).
Обычный шлакопортландцемент измельчают до остатка на сите №088 (7-9%), что соответствует удельной поверхности около 3000 см2/г.
Гипс в ШПЦ служит не только регулятором сроков схватывания, но и активизатором твердения шлака. Замедляя схватывания клинкера, он в то же время ускоряет схватывания шлака. Увеличение количества гипса с 2% до 4- 5% вызывает рост прочности ШПЦ во все сроки твердения.
Твердение ШПЦ - является более сложным, т.к. участвуют два компонента. Вначале происходит гидратация клинкера, при этом раствор насыщается ионами Са2+, ОН-, SO42-, что и создает условия для щелочной и сульфатной активизации шлакового стекла. Поскольку часть Са(ОН)2 поглощается силикатом, концентрация его снижается, что способствует переходу возникших при гидратации высокоосновных соединений в низкоосновные. В составе новообразований - гидросиликаты, низко - высокосульфатные ГСАК, а также ГАК и гидрогелинит 2СаО∙ Al2O3∙ SiO2∙ 8Н2О. содержание Са(ОН)2 ниже чем в ПЦ.
101
РАЗДЕЛ №8 ТЕХНОЛОГИЯ ИЗДЕЛИЙ НА ОСНОВЕ МИНЕРАЛЬНЫХ ВЯЖУЩИХ ВЕЩЕСТВ
Технология производства бетонов
Бетон – искусственный каменный материал, получаемый в результате затвердевания рационально подобранной, тщательно перемешанной и хорошо уплотненной бетонной смеси, состоящей из вяжущего вещества, воды и заполнителей.
Строительный материал в котором бетон и стальная арматура, соединенные взаимным сцеплением, работают под нагрузкой как единое монолитное тело, принято называть железобетоном, а конструкции из такого бетона – железобетонными.
В современном строительстве бетон и железобетон – основные материалы для строительства промышленных, гражданских, сельскохозяйственных, гидротехнических сооружений, устройства покрытий дорог и аэродромов.
Классификация бетонов
1. По структуре различают:
-бетоны плотной структуры, у данных бетонов пространство между зернами заполнителя занято затвердевшим вяжущим практически полностью.
-крупнопористые бетоны, у которых пространство между зернами крупного заполнителя занято мелким заполнителем и затвердевшим вяжущим не полностью.
-поризованные бетоны, в которых затвердевшее вяжущее поризовано пенно- и газообразователями, воздухововлекающими добавками.
-ячеистые бетоны, структура которых представлена искусственно созданными ячейками, заменяющими зерна заполнителей.
2. По объемной массе бетоны разделяют:
-особо тяжелые с объемной массой более 2500 кг/м3 (применяются для специальных сооружений).
-тяжелые 2200 – 2500 кг/м3.
-облегченные с объемной массой 1800 – 2200 кг/м3 (для несущих конструкций).
-легкие с объемной массой 500-1800 кг/м3.
-особо легкие с объемной массой до 500 кг/м3.
3. По виду вяжущего:
-цементные.
-силикатные (на известково-кремнеземистом вяжущем).
-гипсовые (на основе высокообжиговых и низкообжиговых вяжущих веществ).
102
-на смешанных вяжущих (известково-цементных, известковошлаковых).
-специальные вяжущие (органические и неорганические).
4. По виду заполнителей:
-на плотных заполнителях (для тяжелых бетонов).
-на пористых заполнителях (для легких и облегченных бетонов).
-на специальных заполнителях, удовлетворяющих специальным требованиям.
5. По зерновому составу заполнителей:
-крупнозернистые, с крупным и мелким заполнителем;
-мелкозернистые, только с мелким заполнителем.
6. По условиям твердения:
-естественного твердения (преимущественно для монолитных конструкций и в летних условиях для сборных конструкций, изготовляемых на полигонах);
-подвергнутые тепловой обработке при атмосферном давлении (преимущественно для сборных конструкций из тяжелых и легких цементных бетонов);
-подвергнутых автоклавной обработке (в конструкциях заводского изготовления из силикатных, ячеистых и мелкозернистых бетонов).
Материалы для производства бетонов
Вяжущие вещества (материалы). В качестве вяжущих используют цементы, строитльная известь, гипс и др. Среди цементов наиболее часто применяют портландцемент, реже глиноземистый, расширяющийся и другие цементы.
При производстве сборного железобетона рекомендуется применять высокомарочные быстротвердеющие цементы, что позволяет сократить их расход и время изготовления изделий. Повышенная активность цемента эффективно используется только в бетонах сравнительно высокой прочности (более 20 МПа).
Для приготовления тяжелых и легких бетонов в зависимости от их проектной прочности рекомендуется использовать цементы следующих марок.
Марка |
100-150 |
200-250 |
300 |
400 |
500-800 |
тяжелого |
|
|
|
|
|
бетона |
|
|
|
|
|
Марка цемента |
300 |
400 |
400БТЦ |
500 |
600БТЦ |
Марка легкого |
До 35 |
50-150 |
200 |
250 |
300 |
бетона |
|
|
|
|
|
Марка цемента |
300 |
400 |
400БТЦ |
500БТЦ |
500-600 |
103
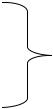
Известь применяют как гашенную (гидратную), так и негашеную. При изготовлении силикатных бетонов автоклавного твердения необходимо использовать известь с содержанием МgО не более 5%.
Для изготовления гипсовых и гипсобетонных изделий в зависимости от их назначения вяжущими могут служить низкообжиговые гипсовые, водостойкие гипсоцементные-пуццолановые, а также высокообжиговые гипсовые вяжущие.
Заполнители. Заполнитель составляет основную часть (около 75-85%) массы бетона. Мелким заполнителем является песок, представляющий собой смесь зерен крупностью 0,14-5 мм и объемной массой более 1200 кг/м3. Качество песка, используемого в бетоне, определяется его минералогическим, зерновым составом, а также содержанием примесей. Зерновой состав песка имеет особо важное значение для получения бетона заданной марки и долговечности при минемальном расходе цемента. В зависимости от зернового состава пески разделяют на крупные, средние, мелкие и очень мелкие. Основной характеристикой песка является модуль крупности песка Мкр.
|
А2,5 + А1,25 + А0,63 +А0,315 + А0,16 |
Мкр= |
--------------------------------------------------------; |
|
100 |
2,5 – П
1,25 – П+Р
0,63 – П+Р+О Мкр=∑Аi/100. 0,315 - П+Р+О+Л 0,16 - П+Р+О+Л+Д
Модуль крупности: крупный песок более 2,5; средний 2,0-2,5; очень мелкий 1,0-1,5.
В бетонах применяют пески с модулем крупности 2,1-3,25. Качество бетона ухудшается при наличии в песке примесей. Поэтому содержание пылевидных, глинистых и илистых частиц, препятствующих сцеплению заполнителя с цементным камнем должно быть не более 3, а в дробленом 4- 5%, в том числе глины не более 0,5%. Содержание данных примесей снижается промыванием песка в специальных машинах-пескомойках.
Все что больше 5 мм – это крупный заполнитель. Гравий – это природный материал, щебень – это дробленый материал. Так как доля крупного заполнителя в бетоне очень велика, то необходимо соблюдать определенные требования к щебню и гравию.
Щебень – это материал, получаемый в результате дробления твердых горных пород на куски размером 5-70 мм. В отличие от щебня зерна гравия имеют окатанную форму, поэтому он хуже сцепляется с цементом и бетон на гравии дает меньшую прочность, чем на щебне.
104
Прочность гравия и щебня (при сжатии), должна быть в 1,5 раза больше марки бетона, если марка бетона меньше 300, и в 2 раза, если марка бетона выше 300. Морозостойкость заполнителя должна быть не ниже морозостойкости бетона. Содержание илистых и глинистых примесей в гравии не более 1%, в щебне 1-3%. Желательно, чтобы форма зерен щебня была близка к кубической.
Крупный щебень и гравий благодаря меньшей их суммарной поверхности требуют меньше цементного теста для покрытия зерен однородным слоем. Увеличение крупности заполнителя с 10 до 20 мм уменьшает расход цемента примерно на 10%. Рекомендуется использовать фракционный заполнитель, состоящий из нескольких фракций (мм): 5-10, 1020, 20-40, 50-70.
Заполнители для легких бетонов. Служат природные и искусственные сыпучие пористые с объемной массой не более 1200 кг/м3 при крупности зерен до 5 мм (песок) и не более 1000 кг/м3 при крупности зерен 5-40 мм (щебень, гравий).
Природные пористые заполнители – это щебень и песок из пемзы, вулканического туфа, пористых известняков, известковых туфов. Искусственные пористые заполнители – изготавливают специально, и это прежде всего керамзит (гравий и песок), аглопорит (щебень, песок). Керамзитовый гравий и песок (зерна округлой формы) получают путем вспучивания в процессе обжига гранул из легкоплавкой глины. Аглопоритовый щебень и песок изготавливают спеканием глинистой породы и отходов от добычи, переработки и сжигания каменных углей на агломерационной решетке с последующим дроблением. Прочность пористых заполнителей колеблется в широких пределах 0,4-20 МПа, объемная масса 400-1400 кг/м3, водопоглащению 15-45%.
Добавки для бетонов подразделяют по основному эффекту действия на:
-регулирующие реологические свойства бетонных смесей (пластифицирующие, стабилизирующие, водоудерживающие).
-регулирующие схватывание и твердение (ускорители и замедлители схватывания).
-регулирующие пористость бетона (воздухововлекающие, газообразующие, пено-образующие, уплотняющие).
На практике добавки чаще классифицируют по достигаемому технологическому эффекту:
Пластифицирующие добавки – это добавки снижающие поверхностное натяжение воды и ослабляющие связи водяных оболочек с зернами песка и цемента. В результате этого бетонные смеси приобретают повышенную подвижность , разжижаются и пластифицируются. Это дает возможность снизить расход цемента и воды на 5-20% и при равной подвижности смеси получить бетон повышенной прочности. Количество добавок 0,1-0,3% от массы цемента – СДБ, полифосфаты натрия и т.д.
105
Суперпластификаторы – они позволяют получать текучую бетонную смесь и укладывать ее без принудительного уплотнения (лигносульфонаты0.
Воздухововлекающие добавки – они способствуют вовлечению воздуха в бетонную смесь при интенсивном ее перемешивании и образованию мелких сферических пор. Такие поры, размещаясь на поверхности зерен цемента и заполнителя, играют роль смазки, повышающей подвижность и пластичность смеси, что позволяет уменьшить количество воды в бетонной смеси примерно на 3-5 кг/м3 бетона на каждый процент вовлеченного воздуха. Вовлеченный воздух снижает водоотделение, облегчает укладку бетона, уменьшает расслаиваемость смеси в процессе транспортирования. Однако вовлеченный воздух может вызвать некоторое снижение прочности бетона. Воздухововлекающие добавки вводят в бетонные смеси в количестве 0,02-0,1% от массы цемента. Это синтетические смолы, пенообразователи, смола нейтрализованная воздухововлекающая и др.
Ускорители твердения бетонов – добавки хлорида кальция, хлорида натрия, нитрата кальция, карбоната калия в количестве до 3% от массы цемента. Эти ускорители могут вызвать коррозию арматуры и появления высолов на поверхности бетонов.
Арматура. Для армирования бетонов применяют главным образом стальную арматуру из углеродистых и низколегированных сталей.
Стальную арматуру классифицируют:
-Гладкая круглая
-Круглая периодического профиля
-Высокопрочная проволока периодического профиля
-Двухпроволочная прядь.
Основные свойства бетонов
Прочность при сжатии. Это основной показатель механических свойств бетона положен в основу деления бетона на марки. Маркой бетона по прочности при сжатии называется предел прочности (кгс/см2) образца испытуемого бетона, имеющего форму куба с длиной ребра 150 мм, качественно уплотненного, твердевшего в нормальных условиях при температуре около 200С и испытанного в возрасте 28 сут. Для тяжелых бетонов установлены марки от М100 до М800.
М100-М200 – для сооружений с невысоким расчетным напряжением, например для фундаментов и др.
М200-М300 – для обычных железобетонных конструкций в промышленном и гражданском строительстве.
М300 – М500 – для предварительно напряженных конструкций.
М600 – М800 - в некоторых специальных конструкциях и инженерных сооружениях.
Качество бетона характеризуют также его классом по прочности (индекс В). Это нормируемое значение унифицированного ряда показателей
106
качества бетона по прочности, принимаемое с гарантируемой обеспеченностью. Установлены следующие классы бетона по прочности на сжатие:
-для тяжелого и мелкозернистого бетона В3,5-В60;
-для напрягающего В20-В60;
-для легкого В2,5-В40;
-для ячеистого В1-В12,5;
-для поризованного В2,5-В7,5.
Прочность на растяжение изгиб в 8-15 раз ниже прочности на сжатие. Предприятие может отпускать с завода изделия потребителю в расчете
на ее дальнейшее нарастание до проектной, называется отпускной прочностью. Отпускная прочность должна быть не менее: для изделий из тяжелых бетонов всех марок и легких бетонов более М100 – 70% от проектной марки; для изделий из легких бетонов менее М100 – 80% от проектной, для изделий из бетонов автоклавной обработки 100% проектной марки.
Технологической прочностью бетона – называют прочность, при которой можно снять изделия с поддона или с формующей установки и транспортировать его в пределах завода.
Прочность бетона зависит: активности цемента, В/Ц отношении, качества заполнителей, возраста бетона, степени уплотнения бетонной смеси, условий твердения.
Прочность бетона Rt в возрасте (t) суток можно определить по формуле:
Rt=R28 lgt/lg28
Где R28 – прочность бетона в 28-ми суточном возрасте;
Средняя прочность бетонных образцов в 1 суточном возрасте составляет 0,6-0,7 марочной прочности. У трех - месячных образцов прочность выше марочной примерно на 10-15%, а у 12 месячных на 30-40%.
1.Пористость бетона – степень заполнения его объема порами. Пористость бетона колеблется в пределах 5-15%. С увеличением пористости прочность бетона заметно снижается. Пористость бетона может быть понижена тщательным подбором зернового состава заполнителей, снижением количества воды затворения и интенсивным уплотнением бетонных смесей.
2.Трещиностойкость – является результатом напряжений и деформаций, возникающих при действии на конструкции механических нагрузок или при значительных температурных и влажностных перепадах в теле бетона. Данные факты (явления) имеют место в массивных бетонных конструкциях вследствие неравномерного их высыхания или остывания. Применение цементов с пониженной скоростью твердения и пониженным тепловыделением обеспечивают снижение трещинообразования.
3.Усадка и набухание. Бетоны при хранении на воздухе уменьшаются в объеме, а при хранении в воде набухают. Причина усадки – испарение воды
107
из бетона, продолжающееся до тех пор, пока не установиться равновесие между содержанием влаги в бетоне и окружающей среде.
4.Водопроницаемость – это свойство бетона характеризуется наименьшим значением давления воды, при котором она начинается просачиваться через бетонный образец. По этому показателю бетоны делят на маки W2 до W20, которое выдерживает давление воды соответственно от 0,2 до 2 МПа. Водонепроницаемость бетона зависит от количества и размеров открытых и сообщающихся друг с другом пор. Бетоны, имеющие в основном тонкие капиллярные поры, практически водонепроницаемы.
5.Морозостойкость. Ее оценивают числом циклов попеременного замораживания и оттаивания образцов в насыщенном водой состоянии, которое выдерживают бетонные образцы в возрасте 28 суток без снижения прочности при сжатии более 15%. Для разных видов и марок бетона число циклов попеременного замораживания и оттаивания может содержать 25, 50, 100, 150, 200, 300, 400, 500. Этот показатель называют маркой бетона по морозостойкости и обозначают F25, F50 и т.д.
Морозостойкость бетона может быть повышена введением в бетонную смесь поверхностно-активных добавок, которые уменьшают количество воды затвердения и, следовательно, объем открытых пор в затвердевшем бетоне.
5.Огнестойкость и огнеупорность. Под огнестойкостью бетонов понимают стойкость их против относительно кратковременного действия огня (например при пожаре), а под жаростойкостью – стойкость материала при эксплуатации в условиях систематического воздействия повышенных температур. Бетон является огнестойким материалом. Кратковременное действие огня не снижает прочность конструкций, так как бетон не успевает прогреться. Опасны для бетона термические удары (например, при тушении пожара водой).
Обычные бетоны пригодны для эксплуатации при систематическом его нагреве до температуры не более 2250С. Однако при специальном подборе состава бетона можно повысить его жаростойкость.
Основные технологические процессы производства бетонных и железобетонных изделий
Технологический процесс производства железобетонных изделий складывается из последовательно выполняемых операций:
-подготовка материалов;
-приготовление бетонной смеси;
-армирование железобетонных изделий;
-формование;
-тепловлажностная обработка;
-отделка лицевой поверхности изделий;
-контроль качества.
108
Подготовка материалов к приготовлению бетонной смеси
Большинство операций по подготовке исходных материалов (дробление, промывка заполнителей и др.) обычно осуществляют на горнорудных предприятиях. На заводах сборного железобетона организуется лишь их приемка, хранение необходимого запаса и в случае необходимости активация лежалых цементов и подогрев заполнителей в зимнее время.
Цемент на заводы ЖБИ поступает в железнодорожных вагонах бункерного типа, автоцементовозах. Хорошо зарекомендовали себя железнодорожные цементовозы – цистерны грузоподъемностью 60 т, позволяющие предотвратить потери цемента от распыления и обеспечить пневматическую разгрузку его в приемные устройства на высоту 10-12 м и на расстояние по горизонтали до 50 м. Цемент и другие вяжущие вещества хранят в силосах с конусообразным днищем, в центре которого находится разгрузочное устройство. Вместительность силосов составляет 200-250 т., дтаметр 3-5 метров. Нормированный запас цемента рассчитывают на 7-10 суток.
Заполнители хранят на складах: штабельных (материалы хранят на открытых площадках); полубункерных, ограниченных стенками с двух продольных сторон, и силосных. Необходимо обеспечить раздельное хранение заполнителей по видам, размеру зерен и сортам в отдельных емкостях.
Приготовление бетонных смесей.
Основными технологическими операциями приготовления бетонной смеси являются дозирование исходных материалов и их перемешивание. Дозирование сыпучих материалов производят для бетонной смеси производят по массе (кроме пористых заполнителей, дозируемых по объему). Погрешность дозирования не должна превышать: для цемента, воды, добавок сыпучих и жидких +2%, для заполнителей +2,5%.
Дозирование материалов производят дозаторами периодического и непрерывного действия. Дозаторы цемента и заполнителей располагаются под выходными течками отсеков расходных бункеров, а дозаторы воды и добавок – на специальных опорах над смесителями. Продолжительность цикла взвешивания материала составляет 35-45 с. Дозаторы оснащают автоматическим, полуавтоматическим или ручным управлением. На современных заводах ЖБИ устанавливают, как правило, автоматические дозаторы по массе.
Основная задача перемешивания – гомогенизация составляющих смеси. Скорость и результат смешения зависит от формы и гранулометрического состава общего и каждого компонента в отдельности, количества смешиваемых компонентов, их соотношения, плотности и коэффициента трения, а также от влажности и способности к агломерации
109
отдельных частиц. При перемешивании одновременно решается ряд технологических задач. Наряду с равномерным распределением компонентов бетонной смеси необходимо максимально удалить из смеси воздух, попавший с цементом и заполнителем; раздробить комки цемента, повысить долю мелких частиц. Особенно важно обеспечить полное смачивание цемента водой.
Перемешивание осуществляется в специальных аппаратах – смесителях, конструкция которых зависит от типа смеси и требуемой производительности. Крупнозернистые смеси с заполнителем из плотных пород с подвижностью 3 см и более перемешивают в смесителях со свободным падением материалов. Для такого перемешивания служат медленно вращающиеся смесительные барабаны, на стенках которых изнутри по винтовой линии установлены корытообразные короткие лопасти. Бетоносмесители со свободным падением материалов просты по конструкции, экономичны по расходу электроэнергии и имеют длительный срок службы. Однако они обеспечивают хорошее качество перемешивания лишь достаточно подвижных бетонных смесей.
Для приготовления жестких бетонных смесей, применяемых на большинстве железобетонных заводов, необходимо использовать бетоносмесители принудительного действия. Перемешивание в них осуществляется по более сложным траекториям, что повышает однородностью смеси, а следовательно, прочность бетона и позволяет снизить расход цемента. Смесители принудительного перемешивания имеют более сложную конструкцию и в зависимости от вида перемешивания их можно разделить на три основные группы:
-неподвижные полузамкнутые барабаны корытообразной формы – лопастные, одно- и двухвальные;
-противоточные смесители, представляющие собой открытую чашу, медленно вращающуюся в направлении, противоположном вращению перемешивающихся лопаток;
-смесители турбинного типа с неподвижной чашей и лопастями, вращающимися вокрук осевого вала.
Качество перемешивания может быть повышено за счет применения вибрации, особенно при жестких бетонных смесях. Виброперемешивание активизирует вяжущее и ускоряет твердение бетона в раннем возрасте. Виброперемешивание бетонных смесей осуществляют в вибросмесителях либо за счет вибрационных импульсов, сообщаемых зернам заполнителя, либо обычными лопастями с вибрационными импульсами от вибраторов.
Транспортирование бетонной смеси к месту формования изделий должно быть максимально механизировано, а число перегрузок – сокращено до минимума. Способ транспортировки должен обеспечивать сохранность однородности и подвижности бетонной смеси. Если строительная площадка находится на значительном удалении от бетонного завода, целесообразно для
перевозки |
и |
приготовления |
бетонной |
смеси |
использовать |
110