
Технол.станкостр.Метод.указ.к лаб.раб
.pdf11
ставляет всего 0,5...1 % от общего числа травм на производстве. Однако доля со смертельным исходом от электротравм составляет 20...40 %, в основном при обслуживании электроустановок с напряжением 127...380 В.
Электрический ток оказывает на тело человека сложное воздействие, являющееся совокупностью термического (нагрев тканей и биологических сред), электролитического (разложение крови и плазмы) и биологического (раздражение и возбуждение нервных волокон) воздействий. Наиболее сложным является биологическое воздействие, свойственное только живым организмам. Различают местные электротравмы и электрические удары. Приблизительно 55 % травм имеют смешанный характер.
Электробезопасность обеспечивается соответствующей конструкцией электроустановок; применением технических способов и средств электрозащиты технологического оборудования; организационными и техническими мероприятиями (ГОСТ 12.1.030-81).
Наиболее распространены защитное заземление и зануление. Защитным заземлением (ГОСТ 12.1.030-81) называется преднаме-
ренное электрическое соединение с землей или ее эквивалентом металлических нетоковедущих частей, которые могут оказаться под напряжением.
Занулением (ГОСТ 12.1.030-81) называется преднамеренное электрическое соединение с нулевым защитным проводником металлических нетоковедущих частей, которые могут оказаться под напряжением.
Организационные и технические мероприятия по обеспечению элек-
тробезопасности (ГОСТ 12.1.019-79), в основном, заключаются в соответствующем обучении, инструктаже и допуске к работе лиц, прошедших медицинское освидетельствование; выполнении ряда технических мер при проведении работ с отключением напряжения в действующих станках или вблизи них (снятие с предохранителей, отсоединение концов питающих линий; установка ограждений и знаков безопасности; проверка наличия заземлений и т. п.); соблюдении особых требований при работах на токоведущих частях, находящихся под напряжением, или вблизи них (выполнение работ по наряду не менее чем двумя лицами, организация надзора за проведением работ, применение электрозащитных средств и т. п.).
Спасение жизни человека, пораженного электрическим током, во многом зависит от быстроты и правильности действий лиц, оказывающих помощь. Прежде всего, нужно как можно быстрее освободить пострадавшего от действия электрического тока. При освобождении человека от напряжения до 1000 В можно воспользоваться канатом, палкой, доской или другим сухим предметом, не проводящим ток. Можно оттянуть пострадавшего за сухую одежду. Для изоляции рук лучше всего воспользоваться диэлектрическими перчатками, а при их отсутствии необходимо обмотать руку любой сухой материей. Рекомендуется при этом действовать одной рукой. Меры доврачебной помощи после освобождения пострадавшего зависят от его состояния.
12
Экология при работе на станках
Экология – раздел биологии, изучающий взаимоотношения человека, животных, растений, микроорганизмов между собой и с окружающей средой.
К загрязнениям окружающей среды относят результаты жизнедеятельности человека, отрицательно воздействующие на самого человека, полезные для него организмы и ресурсы неживой природы. Изучением этого занимается социальная экология.
Развитие промышленности, освоение более эффективных технологических процессов с целью повышения производительности труда привело к увеличению всевозможных производственных отходов, вызывающих загрязнение окружающей среды. Технологические процессы являются также источниками шума и вибрации.
В машиностроении источником загрязнения воздушного бассейна являются разнообразные пыли – взвешенные в воздухе частицы твердых веществ.
Производственными сточными водами называются воды, использованные промышленным предприятием и подлежащие очистке. К ним относятся: эмульсии, не растворимые в воде жидкости (например, масла), взвешенные в виде мелких капелек, и суспензии – взвеси твердых частиц, размеры которых могут достигать нескольких миллиметров.
Производственные сточные воды подразделяются на условно чистые (оборотные) и грязные. Оборотные воды используют для охлаждения технологического оборудования, компрессоров и т. д. Эти воды охлаждают в заводских прудах или градирнях, очищают от механических загрязнений и масел и затем, добавив небольшое количество свежей воды, возвращают в производство. Грязные сточные воды являются специфичными для каждого вида производства.
Промышленные твердые отходы делятся на токсичные и нетоксичные. Основная масса твердых отходов машиностроения нетоксична (металлическая стружка, окалина, зола, отходы дерева, резина, различный мусор). К токсичным твердым отходам относят шламы, образующиеся при работе гальванических цехов и травильных участков.
Промышленный шум большой интенсивности поражает органы слуха и оказывает общее отрицательное воздействие на организм человека (повышает утомляемость, количество брака, травматизм, рассеивает внимание, снижает производительность, приводит к хроническим заболеваниям).
Совокупность технических и организационных мероприятий, позволяющих свести к минимуму или исключить загрязнение окружающей среды и его вредное влияние, называют методами охраны окружающей сре-
ды от загрязнения отходами производства. Различают пассивные и ак-
тивные методы борьбы с загрязнением окружающей среды.
13
Кпассивным относят методы, не связанные с непосредственным воздействием на источники загрязнения, это рациональное размещение источников загрязнения, локализация загрязнений и их очистка перед выбросом в окружающую среду.
Кактивным относят методы, связанные с совершенствованием существующих и разработкой новых технологических процессов, оборудования
иоснастки в целях снижения уровня загрязнения окружающей среды или его исключения.
Задачи охраны окружающей среды успешнее решаются активными методами и им уделяют больше организационного и правового внимания.
Порядок выполнения и обеспечения безопасности
Китоговым занятиям допускаются студенты, имеющие полный комплект технологической документации, разработанной на занятиях. Студенты приступают к выполнению практических действий на металлорежущих станках только в присутствии преподавателя и учебного мастера (техника, лаборанта).
Ксамостоятельной работе на станках допускаются только студенты, имеющие квалификационный разряд и прошедшие инструктаж по охране труда согласно инструкции по работе на металлорежущем оборудовании.
Наладку и настройку станка на обработку детали студенты выполняют самостоятельно в соответствии с технологическими картами под наблюдением преподавателя и учебного мастера. Студентам запрещается производить пробные пуски станка самостоятельно (без разрешения преподавателя или учебного мастера) при их наладке и настройке.
Контрольные вопросы
1Какие факторы воздействуют на труд станочника?
2Какие факторы влияют на формирование условий труда?
3Что такое охрана труда рабочего-станочника?
4Что такое гигиена труда рабочего-станочника?
5Как влияет вибрация на условия работы станочника?
6Что называется рабочим местом станочника?
7Расскажите о планировке рабочего места станочника.
8Чем оснащается рабочее место станочника?
9Какие мероприятия проводятся при обслуживании рабочего места?
10Что такое пожарная безопасность?
11Как и когда проводится противопожарный инструктаж?
12Какие меры по предупреждению пожара вы знаете?
13Как обеспечивается электробезопасность на производстве?
14Назовите технические средства защиты металлорежущих станков.
14
15Расскажите об экологии как о науке.
16Какие виды загрязнений возникают в машиностроении?
17Какое влияние на человека оказывает промышленный шум?
18Расскажите о методах охраны окружающей среды от загрязнений отходами производства.
Лабораторная работа № 1. Технология сборки. Сборка узла станка в лабораторных условиях
Цель работы: совершенствование практических навыков студентов в составлении схем сборки, станков, приспособлений и узлов.
Порядок выполнения
В соответствии с представленным чертежом узла, видом производства разработать схему сборки, назначить необходимые технические требования на сборку исходя из метода достижения точности замыкающего звена при сборке (ГОСТ 23887-79, ГОСТ 16319-80, ГОСТ 14.320-81, полной взаимозаменяемости, неполной взаимозаменяемости, групповой взаимозаменяемости, пригонки, регулирования, сборки с компенсирующими материалами), выбрать вид и организационную форму сборки.
Оформление отчета
В состав отчета входят: эскиз или ксерокопия чертежа выданного узла, схема сборки, обоснование выбранного метода достижения точности замыкающего звена и рекомендации по виду и организационной форме сборки.
Лабораторная работа № 2. Технология изготовления валов, стаканов, втулок
Цель работы: приобретение практических навыков студентами в настройке и наладке токарных, шлифовальных и фрезерных станков для обработки деталей типа тела вращения с L > 3D.
Порядок выполнения
Исходя из требований чертежа, программы выпуска и в соответствии с разработанной технологической документацией подобрать необходимую технологическую оснастку (приспособления, вспомогательные, режущие и мерительные инструменты) для обработки различных поверхностей вала на токарном и фрезерном станках. Определить порядок базирования и закрепления на станке приспособления, вспомогательного и режущего инст-
15
рументов, а также метод обеспечения размера статической настройки технологической системы для получения заданного размера на детали после обработки и способы подстройки. Обосновать способ получения и базирования заготовки на станке. Определить порядок настройки кинематических цепей станков (привода главного движения и привода подач) на обеспечение оптимальных режимов согласно разработанным технологическим картам. Закрепить заготовку на станке и произвести обработку под наблюдением учебного мастера (техника, лаборанта). Текущий контроль обработанных поверхностей детали выполнять между технологическими операциями и переходами. Окончательный контроль детали произвести при помощи имеющихся технических средств измерений.
Оформление отчета
При выполнении отчета необходимо отобразить: эскиз детали, все необходимые технологические расчеты, приложить комплект технологической документации, заключение о годности обработанной детали. Все расчеты и эскизы выполняются в отдельной ученической тетради. Технологический процесс оформляется на стандартных бланках ЕСТД или на бланках, расчерченных в тетради. Эскизы и схемы выполняются в произвольном масштабе с использованием чертежных принадлежностей. В случае получения бракованной детали приводится анализ причин появления брака и методы их устранения.
Технологический процесс изготовления вала
Разработка технологического процесса изготовления вала включает следующие этапы:
–выбор метода получения заготовки;
–подготовка технологических баз (обработка торцов и сверление центровых отверстий);
–черновая токарная обработка;
–чистовая токарная обработка; фрезерование шлицев (при наличии шлицевого венца на валу);
–фрезерование шпоночных пазов, лысок, уступов и других элементов;
–сверление отверстий, зенкование фасок, нарезание резьбы;
–термическая обработка;
–шлифование поверхностей вала.
Заготовки валов в зависимости от их формы и объема выпуска получают одним из следующих методов:
–отрезкой из круглого проката;
–штамповкой на кривошипных горячештамповочных прессах;
–штамповкой на горизонтально-ковочных машинах.

16
Токарная обработка валов в крупносерийном и массовом производствах выполняется, как правило, на многорезцовых токарных полуавтоматах или гидрокопировальных токарных полуавтоматах. В серийном производстве токарная обработка валов может быть выполнена на универсальных токарных станках или токарных станках с ЧПУ.
На занятиях каждый студент получает индивидуальное задание (чертеж вала).
Примеры оформления технологических документов приведены на рисунках А.1…А.3.
1 Чертеж детали. В соответствии со своим вариантом в отчете вычерчивается чертеж вала. Вариант задается преподавателем. Чертеж выполняется на развороте ученической тетради или отдельном листе, вклеенном в тетрадь. Механические характеристики марок стали приведены в таблице Б.1.
2 Выбор заготовки. Все детали, на которые разрабатываются технологические процессы, студенты изготавливают в лабораторных условиях по одной штуке. Заготовками для всех вариантов валов является горячекатаный круглый прокат (ГОСТ 2590-71). Сортамент, размеры и допускаемые отклонения горячекатаного проката приведены в таблице Б.2.
В зависимости от наибольшего диаметра вала и количества рабочих ходов, необходимых для его обработки, выбирается диаметр заготовки из проката.
Длина заготовки определяется по длине вала с учетом припусков на обработку торцов. Предельные отклонения на длину заготовки зависят от способа резки проката и приведены в таблице Б.3. В отчете вычерчивается эскиз заготовки. Внутри заготовки тонкими линиями изображается контур детали. Размеры заготовки (длина и диаметр) проставляются с предельными отклонениями. Пример эскиза заготовки приведен на рисунке 1.
Рисунок 1 – Эскиз заготовки вала
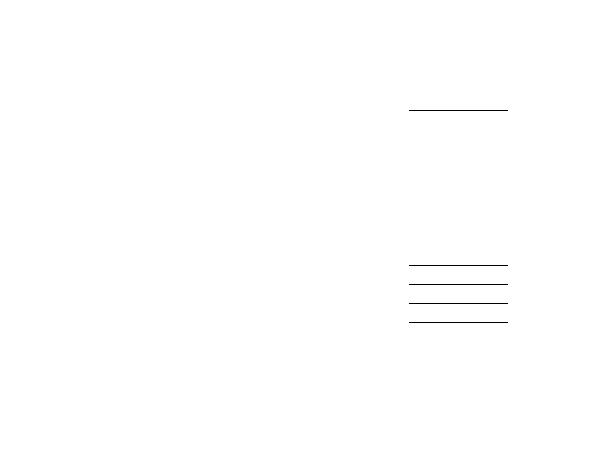
17
3 Маршрутный техпроцесс. Маршрутный техпроцесс разрабатывается с учетом наличного парка станков лаборатории, в состав которого входят: токарно-винторезный, вертикально-фрезерный, радиальносверлильный, вертикально-сверлильный, зубофрезерный, зубодолбежный, зубострогальный и кругло-шлифовальный станки. Предварительно каждый студент намечает план обработки детали, т. е. последовательность обработки поверхностей, и определяет необходимость черновой, чистовой и отделочной обработки для всех поверхностей, руководствуясь рекомендациями, изложенными в таблице 1.
Таблица 1 – Точность и шероховатость поверхности при различных видах обработки
Вид обработки |
Ra, мкм |
Квалитет |
Обтачивание наружных поверхностей: |
|
|
обдирочное |
100...25 |
17...15 |
черновое (однократное) |
12,5...6,3 |
14...12 |
чистовое |
3,2...1,6 |
9...7 |
тонкое (алмазное) |
0,8...0,4 |
6 |
Растачивание внутренних поверхностей: |
|
|
черновое (однократное) |
25…12,5 |
14...12 |
чистовое |
3,2...1,6 |
9...8 |
тонкое (алмазное) |
0,8...0,4 |
7…6 |
Шлифование: |
|
|
чистовое |
1,6...0,8 |
8...6 |
получистовое |
6,3…3,2 |
11…8 |
тонкое |
0,4...0,2 |
5 |
Сверление и рассверливание |
25...12,5 |
14...12 |
Зенкерование (после сверления) |
6,3...3,2 |
11...10 |
Фрезерование концевой фрезой (однократное) |
25...6,3 |
14...12 |
На основании этого плана составляется маршрутный техпроцесс и оформляется в виде таблицы 2. Таблицу целесообразно разместить на развороте тетради.
Таблица 2 – Маршрутный техпроцесс вала
Наименование операции |
Модель |
Режущий инструмент |
Технологическая база |
|
и содержание переходов |
станка |
|
|
|
1 |
|
2 |
3 |
4 |
05 Токарная |
|
16К20 |
|
|
Установ А |
|
|
|
|
Подрезка торца |
|
Резец проходной |
Наружная поверхность |
|
Сверление |
центрового |
|
Сверло центровочное |
Наружная поверхность |
отверстия |
|
|
|
|
Установ Б |
|
|
|
|
Подрезка торца |
|
Резец проходной |
Наружная поверхность |
|
Сверление |
центрового |
|
Сверло центровочное |
Наружная поверхность |
отверстия |
|
|
|
|
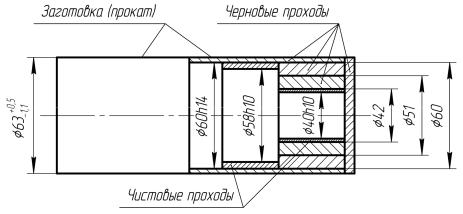
18
Окончание таблицы 2
|
1 |
|
2 |
3 |
4 |
Установ В |
|
|
|
|
|
Черновое |
точение |
по- |
|
Резец проходной |
Центровые отверстия |
верхностей 30, 50 |
|
|
Резец проходной |
Центровые отверстия |
|
Чистовое |
точение |
по- |
|
||
верхностей 30 |
|
|
|
|
4 Расчет режимов резания для токарных операций. Расчет режи-
мов резания начинается с записи всех исходных данных, которые целесообразно располагать в следующей последовательности. При наличии нескольких переходов в операции исходные данные записываются для каждого перехода:
–наименование и номер операции;
–наименование и модель станка;
–марка и свойства обрабатываемого материала (бв, НВ);
–наименование и марка материала режущего инструмента;
–содержание перехода.
4.1 Определение глубины резания. При обработке поверхности за один рабочий ход глубина резания принимается равной припуску, т. е. t = Z.
При многопроходной обработке предварительно составляется схема обработки (рисунок 2), из которой определяется глубина резания для всех черновых (предварительных) и чистового рабочих ходов.
Рисунок 2 – Схема токарной обработки вала
После установления глубины резания для каждого рабочего хода определяется подача S.
4.2 Определение подачи. Величина подачи зависит от марки обрабатываемого материала, марки материала режущего инструмента, жесткости технологической системы, прочности пластинки твердого сплава и дер-
19
жавки резца, вида обработки (черновое или чистовое точение). При черновом точении подача определяется но формуле
S0 = Sтабл Кms , |
(1) |
где Sтабл – табличное значение подачи;
Kms – коэффициент, зависящий от свойства обрабатываемого ма-
териала.
Значения Sтабл и Kms приведены в таблицах Б.4…Б.5.
Найденное значение S0 корректируется и окончательно принимается по паспорту станка.
4.3 Пример расчета подачи для черновой обработки поверхности диаметром 50 мм (заготовка имеет диаметр 58 мм). Марка материала детали – сталь 40Х (σв = 980 МПа). Материал режущей пластинки резца – твердый сплав марки Т5К10. Глубина резания t = 4 мм.
По таблице Б.4 находим рекомендуемые значения подачSтабл = 0,4...0,8 мм/об. По таблице Б.5 находим поправочный коэффициент Кms = 1,25. Тогда
S0 =0,6 1,25 =0,75.
По паспорту токарно-винторезного станка 16К20 принимаем ближайшую меньшую подачу S0 = 0,7 мм/об.
Для чистовой токарной обработки подачи принимаются по таблице Б.6 в зависимости от шероховатости обрабатываемой поверхности и радиуса при вершине резца. Поправочный коэффициент Kms определяется по таблице Б.7.
Подачи при прорезании канавок, пазов и отрезании заготовок (деталей) принимаются по таблице Б.8.
4.4 Расчёт скорости резания. При расчёте скорости в качестве расчётного диаметра принимается наибольший диаметр заготовки. Скорость резания рассчитывается по формуле
Vр =Vтабл K1 K2 K3, |
(2) |
где Vтабл – табличное значение скорости, м/с;
К1 – коэффициент, зависящий от обрабатываемого материала; К2 – коэффициент, зависящий от стойкости и марки твёрдого
сплава;
К3 – коэффициент, зависящий от вида обработки.
20
Значение Vтабл , м/с, и коэффициента К1 приведены в табли-
цах Б.9…Б.11. Коэффициенты К2 и К3, в лабораторных условиях принимаются равными 1,0 при наружном точении. При растачивании отверстий К2 = 1, К3 = 0,85. По расчетному значению скорости Vp, м/с, определяется расчетная частота вращения шпинделя пр, мин-1, по формуле
np = |
60000 Vp |
, |
(3) |
|
|||
|
π D |
|
где D – наибольший диаметр заготовки, мм.
Действительная частота вращения шпинделя nд принимается по паспорту станка, по которому рассчитывается действительная скорость резания Vд , м/с, по формуле
V = π D nд . |
(4) |
д |
60000 |
|
4.5 Пример расчёта скорости резания. В примере расчёта подачи
(см. подпункт 4.3) была определена подача S0 = 0,7 мм/об при обработке
заготовки диаметром 58 мм из стали 40Х (σв = 980 МПа, НВmax217). Глубина резания t = 4 мм. По таблице Б.9 находим значение скорости
Vтабл = 1,58 м/с, при этом поправочный коэффициент К1 = 0,9 (таблица Б.11). Тогда вычисляем расчётное значение скорости
Vp =1,58 0,9 =1,42.
Расчетная частота вращения шпинделя
np = |
60000 1,42 |
= 468. |
|
3,14 58 |
|
По паспорту станка 16К20 принимаем действительную частоту вращения шпинделя пд = 400 мин-1. Тогда действительная скорость резания
Vд = 3,14 58 400 =1,21. 60000
4.6 Сверление центровых отверстий. Центровые отверстия явля-
ются искусственными технологическими базами. Поэтому их размеры и формы определяет технолог в процессе разработки технологического процесса. Центровые отверстия обрабатываются центровочными сверлами,