
Типовые детали
.pdf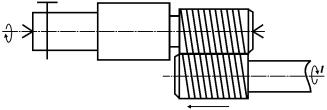
2)метод внешнего касания, когда деталь расположена вне окружности описываемой резцами (рис 1.36, в).
Вначале обработки ширина срезаемого слоя непрерывно возрастает, пока резцы не врежутся на полную глубину резания (заштрихованная площадь АВСД на рис. 1.36, г). В дальнейшем формировании резьбы участвуют обе режущие кромки, срезающие стружку одинаковой формы (рис. 1.36, д). Так как резцы соприкасаются
сдеталью только на части окружности, то они мало нагреваются. Отношение диаметра окружности вращения резцов к диаметру
нарезаемой резьбы принимается от 1,4 до 1,6 при методе внутреннего касания.
Метод внешнего касания используется при нарезании наружных резьб большого диаметра и внутренних резьб диаметром более 40 мм. Для внутренних резьб отношение диаметров расположения резцов и резьбы принимают в пределах 0,6-07.
При вихревом нарезании достигается 4-6-я степень точности резьбы с шероховатостью поверхности Ra = 5-2,5 мкм.
Производительность вихревого метода высокая, так как нарезание резьбы осуществляется за один рабочий ход; метод особо эффективен при нарезании длинных резьб.
Наружные резьбы нарезают также плашками, самораскрывающимися резьбонарезными головками, гребенками, фрезами (дисковыми и групповыми).
На рис. 1.37 показана схема фрезерования резьбы групповой фрезой.
Фрезерование групповой (гребенчатой) фрезой применяется в серийном и массовом производстве для получения коротких резьб с мелким шагом.
Групповая фреза устанавливается параллельно оси детали, поэтому резьбу с большим наклоном нарезать нельзя. За 0,2 оборота детали фреза врезается на глубину резьбы, а за последующий один
Рис. 1.37. Схема фрезерования резьбы групповой фрезой
53
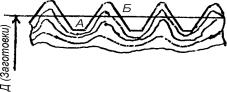
оборот детали фреза перемещается вдоль оси на величину шага и оформляет полный профиль резьбы.
Внутренние резьбы нарезают резцами, метчиками, групповыми фрезами, метчиками-накатниками, литьем с последующим калиброванием.
Наиболее распространенным способом является нарезание резьбы метчиками на различных станках: токарных, сверлильных, расточных, резьбонарезных, гайконарезных, револьверных, агрегатных, многоцелевых станках с ЧПУ.
1.5.2. Накатываниерезьбирифлений
Накатывание резьб применяется в крупносерийном и массовом производстве при изготовлении, главным образом, крепежных резьб.
Формирование резьбы при накатывании происходит за счет выдавливания некоторого объема металла из впадин А и образования выступов Б (рис 1. 38).
Металл детали должен обладать пластичностью с относительным удлинением от 8 до 24% и твердостью HRC < 33.
Пластические деформации сжатия при накатывании резьбы упрочняют поверхностный слой.
Предел прочности при растяжении деталей с накатанной резьбой на 20%, усталостная прочность на 25%, а износостойкость на 50% выше, чем у деталей с нарезанной резьбой.
Накатанная резьба имеет гладкую и чистую поверхность, дает экономию материала, так как диаметр заготовки выбирается приблизительно равным среднему диаметру резьбы.
Резьбонакатный инструмент имеет значительно большую стойкость, чем любые резьбонарезные инструменты.
Основные схемы накатывания резьбы изображены на рис. 1.39 При накатывании резьбы плоскими плашками (рис 1.39, а) одна плашка неподвижна, а подвижная плашка установлена на ползуне, совершающим возвратно-поступательное движение. Рабочая поверхность плашек имеет прямолинейную резьбу (развертку резьбы винта) с параметрами, соответствующими накатываемой резьбе.
Рис. 1.38. Перераспределение материала при накатывании резьбы
54
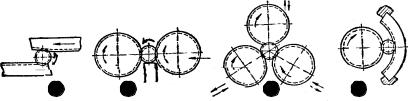
а |
б |
в |
г |
Рис. 1.39. Схемы накатывания резьб:
а– плоскими плашками; б – двумя роликами; в – тремя роликами;
г– круглым роликом и сектором
Резьбонакатные станки с плоскими плашками имеют загрузочное устройство и работают в автоматическом режиме с высокой производительностью (120-150 двойных ходов ползуна в минуту). На этих станках можно накатывать резьбу диаметром от 2 до 25 мм и длиной до 125 мм. Плоскими плашками большей частью накатывают болты, винты и шурупы.
В машиностроении широкое применение получило накатывание резьбы роликами с радиальной, продольной и тангенциальной подачей. Накатывание резьбы с радиальной подачей производится одним, двумя и тремя роликами.
Накатывание резьбы диаметром от 5 до 25 мм одним роликом применяется на токарных и револьверных станках и токарных автоматах.
Наибольшее распространение получил способ накатывания резьбы двумя роликами (рис. 1.39, б). Заготовку помещают на направляющей планке. Оба ролика вращаются в одну сторону, причем один из роликов получает радиальную подачу.
Реже накатывают резьбу тремя роликами (рис. 1.39, в). Радиальная подача в этом случае дается одновременно всем трем роликам. Центрирование заготовки производится самими роликами без дополнительных опор.
Скорость вращения роликов принимается от 12 до 100 м/мин в зависимости от диаметра резьбы, точности ее и материала заготовки. При накатке роликами можно получить резьбу высокой точности.
На (рис. 1.39, г) показана схема многоцикличного планетарного резьбонакатного автомата с одной неподвижной плашкой в виде сектора и вращающимся роликом. Заготовки в зону накатки подаются периодически так, что в процессе обработки находится одновременно несколько заготовок. Производительность такого автомата достигает 300-400 деталей в минуту.
55
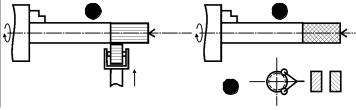
Для накатывания резьбы с тангенциальной подачей заготовок в вертикальном направлении применяют два затылованные ролика с одним секторным вырезом для выхода детали из зоны накатки.
Накатывание резьбы с продольной подачей заготовки производится роликами с винтовыми витками (оси роликов параллельны оси заготовки) или роликами с кольцевыми витками, при этом угол наклона роликов должен быть равным углу подъема винтовой линии накатываемой резьбы детали.
Накатные ролики должны быть изготовлены с средним диаметром, числом заходов, длиной хода резьбы кратно тем же параметрам накатываемой резьбы.
Накатывание внутренней резьбы диаметром от 3 до 30 мм производят метчиками-накатниками в зависимости от соотношения длины резьбы l и диаметра d: для мягких сталей – l/d < 3, для цветных сплавов – l/d < 8. При этом достигается шероховатость поверхности
Ra = 1,25-0,63 мкм.
Накатывание резьб в отверстиях диаметром от 20 до 100 мм производится одним роликом, а при диаметре более 100 мм предварительно прорезают резьбу, а затем накатывают головкой с тремя роликами.
Накатывание рифлений производят на наружных цилиндрических поверхностях рукояток различных измерительных инструментов, круглых гаек, на поверхностях валов под напрессовку листов ротора электродвигателей и др. Накатка бывает прямой (рис. 1.40, а) и перекрестной (рис. 1.40, б).
При накатывании рифлений державку с одним или двумя роликами прижимают к вращающейся детали, зубчики ролика вдавливаются в материал детали и образуют на ее поверхности накатку. Для получения достаточной глубины накатки надо вести накатывание за 2-3 рабочих хода.
а |
б |
в
Рис. 1.40. Схема накатывания прямой накатки (а); перекрестная накатка (б); ролики для накатывания перекрестной накатки (в)
56

Перекрестную накатку (рис. 1.40, б, в) осуществляют двумя роликами с зубцами различного направления. Ролики изготавливают из ст. ХВГ с твердостью HRC 62-64.
При накатывании рифлений назначают следующие режимы: скорость вращения детали – 10-25 м/мин (для стали), 25-100 м/мин (для цветных сплавов); осевая подача ролика – 1-1,5 мм/об. дет. (для стали), 2-2,5 мм/об. дет. (для цветных сплавов).
Во время накатывания рабочие поверхности роликов следует хорошо смазывать веретенным или машинным маслом.
1.5.3. Шлифованиерезьб
Шлифование резьбы применяется при изготовлении резьбонарезного инструмента, резьбовых калибров, накатных роликов, точных винтов и др. деталей с точной резьбой.
Шлифование резьбы производят на резьбошлифовальных станках однониточными или многониточными кругами.
Шлифование однониточным кругом 1 (рис. 1.41, а) осуществляется при продольном перемещении детали 2 и вращательном движении круга и детали. Однониточные круги правят одним или двумя алмазами при помощи специального приспособления (рис. 1.41, б: 1
– шлифовальный круг, 2 – державка с алмазом).
Периодическая поперечная подача перед каждым рабочим ходом и быстрый отвод круга от детали в конце хода производятся путем радиального перемещения шлифовальной бабки, или посредством качательного движения стола вокруг горизонтальной оси, параллельной направлению продольной подачи. Однониточный круг устанавливается под углом, равным углу подъема винтовой линии резьбы на среднем диаметре.
аб
57
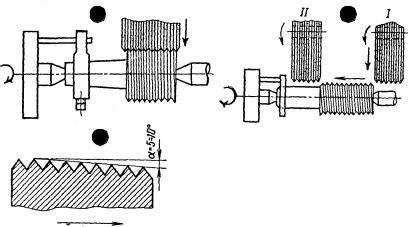
а |
б |
в
Припуски под шлифование резьбы зависят в основном от шага нарезки и находятся в основном в пределах от 0,1 до 0,2 мм. Припуск под окончательное шлифование принимается от 0,05 до 0,1 мм. Резьбы малого шага шлифуют с большой глубиной и малой окружной скоростью вращения детали. Резьбы с шагом менее 1,5 мм шлифуют за 1-3 рабочих хода при скорости вращения детали в пределах от 0,2 до 0,8 м/мин. Шлифование крупных резьб и червяков производится с малой глубиной и большой скоростью вращения детали (3-8 м/мин).
При нарезании шлифовальным кругом мелких резьб (S < 1,5 мм) в сплошном материале поперечная подача (углубление круга) на первых рабочих ходах принимается до 0,1 мм, при окончательном шлифовании – 0,03 мм на один ход. Окружные скорости детали принимаются от 0,1 до 0,3 м/мин.
Окружная скорость шлифовального круга принимается 50-60 м/с. В качестве СОЖ при резьбошлифовании используется минеральное масло.
Многониточные круги применяются преимущественно при шлифовании коротких резьб (обычно не более 40 мм) в крупносерийном и массовом производстве.
На рис. 1.42, а показана схема врезного шлифования многониточным кругом.
Ширина шлифовального круга должна быть больше длины шлифуемой резьбы на 2-4 шага. На круге делается кольцевая резьба
58
с требуемым шагом. Шлифование производится по методу врезания при продольном перемещении детали на 2-4 шага за 2-4 ее оборота.
Если длина резьбы больше ширины круга, шлифование производится при продольном передвижении детали относительно круга (рис. 1.42, б). Все нитки резьбы шлифуются последовательно всеми нитками шлифовального круга. Заправляют круг под углом α , как показано на рис. 1.42, в. Врезное многониточное резьбошлифование неизбежно приводит к искажению профиля резьбы; при продольном перемещении детали относительно круга искажение профиля получается меньшим.
Точность резьбошлифования по схемам рис. 1.41 и рис. 1.42 определяется по следующим параметрам:
а) по среднему диаметру резьбы – от ±0,005 до ±0,03 мм; б) по шагу резьбы на длине 25 мм – от ±0,002 до ±0,008 мм; в) по половине угла профиля – ±(6-10) мин.
Меньшие значения погрешностей относятся к шлифованию однониточными кругами.
Бесцентровое шлифование резьбы применяется преимущественно в массовом производстве при наличии многониточных кругов с кольцевыми канавками. Станки имеют схему обычных бесцентровошлифовальных станков.
При небольших размерах производства деталей можно шлифовать наружную и внутреннюю резьбу на токарно-винторезных станках, обладающих достаточной точностью, при помощи специальных приспособлений.
1.5.4. Методыконтролярезьбы
Контроль резьбы осуществляется по следующим основным параметрам: средний диаметр, шаг и угол профиля резьбы.
Обычно контроль среднего диаметра резьбы деталей производится предельными резьбовыми кольцами и скобами для наружной резьбы и предельными резьбовыми пробками – для внутренней резьбы. При отсутствии предельных калибров средний диаметр можно измерить резьбовым микрометром, который имеет специальные наконечники.
Средний диаметр резьбы может быть проверен методом трех проволочек. Этот метод состоит в том, что между нитками резьбы вкладывается три проволочки: две из них – с одной стороны, а третья
– с другой; расстояние между ними измеряется микрометром или оптиметром. Измерение в этом случае косвенное, и собственно средний диаметр определяют из уравнения (для метрической резьбы)
59
dcp = M - 3dnp + 0,866P + C,
где М – измеренный размер; dnp – диаметр проволочки; Р – шаг резьбы; С – суммарная поправка.
Для проверки среднего диаметра наружной резьбы применяются также резьбовые скобы с двумя парами мерительных роликов или с мерительными гребенками и приборы, измерение с помощью которых основано на принципе сравнения с эталоном.
Средний диаметр внутренней резьбы, кроме предельных резьбовых пробок, может быть измерен аналогично методу трех проволочек, только вместо проволочек используют вставки с шариковыми наконечниками.
Отклонение угла профиля, шага, диаметров резьбы измеряют также с помощью инструментальных и универсальных микроскопов. Для менее точного определения шага резьбы применяются резьбовые шаблоны. Измерение шага и угла профиля внутренней резьбы можно произвести с помощью предварительно изготовленного слепка этой резьбы.
С целью получения качественной резьбы и уменьшения объема контрольных операций, в производстве используют предварительно аттестованный резьбообразующий инструмент (резцы, фрезы, плашки, ролики и др.).
Литература[1, 5, 7]
1.6. Обработка шлицевых поверхностей и пазов
1.6.1.Обработкашлицевыхповерхностей
Вшлицевых соединениях сопряженные детали центрируются тремя способами:
1) центрированием сопрягаемой детали по наружному диаметру шлицев вала;
2) центрированием сопрягаемой детали по внутреннему диаметру шлицев вала, т.е. по дну впадин;
3) центрированием сопрягаемой детали по боковым поверхностям шлицев вала.
Форма шлицев бывает прямоугольная, эвольвентная и треугольная.
Технологический процесс изготовления шлицев валов зависит от того, какой принят способ центрирования вала с сопрягаемой
60
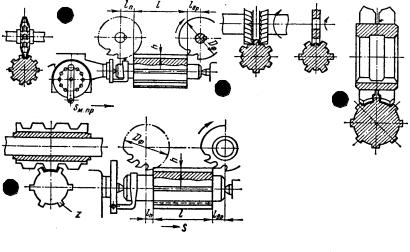
деталью. Наиболее точным является центрирование по внутреннему диаметру шлицев вала; чаще встречается центрирование по наружному диаметру (автотракторостроение, станкостроение и др.). Центрирование по боковым сторонам применяется для передачи больших крутящих моментов, при реверсировании шлицевого соединения.
Шлицы на валах и других деталях изготавливают различными способами: фрезерование, протягивание, строгание, накатывание; чистовая обработка шлиц осуществляется шлифованием.
1.6.1.1. Фрезерование, протягивание, строгание шлицев
Шлицы валов диаметром до 100 мм обычно фрезеруют за один рабочий ход, больших диаметров – за два хода. Фрезерование шлицев часто производится фрезами на горизонтально-фрезерных станках, имеющих делительные механизмы (рис. 1.43).
На рис 1.43, а показано фрезерование одной канавки шлицев дисковой фасонной фрезой на горизонтально-фрезерном станке с делительной головкой.
Фрезеровать шлицы можно способом, изображенным на рис. 1.43, б, позволяющим применять более дешевые фрезы, чем дисковые.
а
б
в
г
Рис. 1.43. Способы фрезерования шлицев валов:
а – шлицевой дисковой фрезой; б – двумя фрезами; в – двумя дисковыми специальными фрезами; г – шлицевой червячной фрезой
61
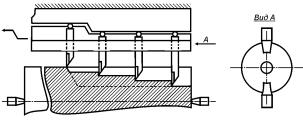
Рис. 1.44. Схема протягивания шлицев на валах
Более производительным способом является одновременное фрезерование двух шлицевых канавок двумя дисковыми фрезами специального профиля (рис. 1.43, в).
Чистовое фрезерование шлицев дисковыми фрезами производится только в случае отсутствия специального станка или инструмента, так как оно не дает достаточной точности по шагу и ширине шлицев.
Более точное фрезерование шлицев производится методом обкатки при помощи шлицевой червячной фрезы (рис. 1.43, г). Фреза помимо вращательного движения имеет продольное перемещение вдоль оси вала. Этот способ является наиболее точным и наиболее производительным.
При центрировании сопрягаемой детали по внутреннему диаметру шлицев вала как червячная, так и дисковая фреза должны иметь “усики”, вырезающие канавки в основании шлица, чтобы не было заедания во внутренних углах; эти канавки необходимы также при шлифовании по боковым сторонам и внутреннему диаметру.
Более производительными методами образования шлицев на валах являются шлицепротягивание и шлицестрогание. Шлицепротягивание производят двумя блочными протяжками (рис. 1.44) одновременно двух диаметрально противоположных впадин на валу с последующим поворотом вала на определенный угол после каждого хода протяжки.
Блок протяжки состоит из набора резцов-зубьев, которые могут независимо перемещаться в радиальном направлении. Для несквозных шлиц используется копирная линейка. Разность диаметров ступеней, при обработке валов с несквозными шлицами не должна превышать 25-30 мм.
Строгание шлицев на валах производят набором фасонных резцов, собранных в головке, их количество и профиль соответс-
62