
Типовые детали
.pdf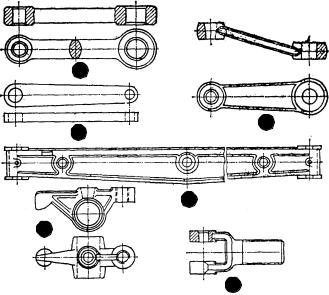
2.3. Технология обработки деталей класса “Некруглые стержни”
2.3.1. Общиесведенияодеталяхкласса“Некруглые стержни”
К деталям данного класса относятся рычаги, вилки, шатуны, тяги, коромысла, прихваты, балансиры и др. подобные детали (рис. 2.10).
Технологические задачи, решаемые при обработке деталей этого класса, следующие: 1) достижение параллельности и перпендикулярности осей отверстий в заданных пределах;
2)достижение перпендикулярности торцов к осям отверстий;
3)получение точных отверстий и точных расстояний между ними. Основные технические условия при изготовлении рычагов
(кроме шатунов) следующие:
–допуск на расстояние между осями главных отверстий – 0,1-0,2 мм;
–непараллельность осей отверстий – 0,03-0,05 на длине 200 мм;
–неперпендикулярность торцов бобышек и оси отверстия – 0,03-0,04 мм на радиусе 50 мм;
а
в
б
г
д
е
Рис. 2.10. Детали класса “Некруглые стержни”:
а– горячештампованный рычаг; б – холодноштампованный рычаг;
в– литой рычаг; г – балка; д – коромысло толкателя; е – вилка
103
– точность отверстий под пальцы – 6-9-й квалитет;
– шероховатость отверстий – Ra = 1,25-0,32 мкм. Материалы для деталей этого класса: серый чугун марки СЧ18,
СЧ24, для ненагруженных рычагов чугун СЧ12, ковкий чугун КЧ3712, КЧ35-10, стальное литье марки 35Л, алюминиевые сплавы, прокат стали 45 и др. материалы.
Заготовки – преимущественно отливки и штамповки; для крупных деталей – поковки; для некоторых простых по конфигурации деталей – листовой прокат (рис. 2.10, б).
Технологические базы: на первой операции – торцы головок и наружные цилиндрические поверхности головок либо тело стержня; на последующих операциях – обработанные торцы бобышек и отверстия либо дополнительные поверхности (центровые отверстия, площадки).
2.3.2. Технологическиепроцессыобработкидеталей класса“Некруглыестержни”
2.3.2.1. Технологическийпроцессобработкипростого рычага
Простой рычаг (рис. 2.10, а) обрабатывают по следующему маршруту (заготовка – штамповка из стали 45):
–фрезерование базовых бобышек;
–сверление, зенкерование, снятие фасок, черновое и чистовое развертывание отверстий, подрезание торцов бобышек облицовочным зенкером с направлением по отверстию;
–подрезание торцов бобышек с другой стороны облицовочным зенкером с направлением по отверстию, снятие фасок;
–снятие наружных фасок (при надобности).
Фрезерование базовых бобышек обычно производят на горизонтально-фрезерном станке одновременно с двух сторон двумя фрезами. Обработка отверстий и торцов бобышек в зависимости от серийности производства может производиться на одно- и многошпиндельных сверлильных станках и на сверлильных станках с ЧПУ.
Существует ряд других вариантов процесса обработки плоских торцовых поверхностей: 1) бобышки обжимают под прессом, после этого выполняют плоское шлифование; 2) осуществляют обдирочное шлифование торцов бобышек, затем – чистовое плоское шлифование.
При обработке отверстий выполняют: 1) сверление, а затем протягивание или 2) сверление, зенкерование, прошивание.
104
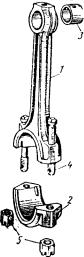
Если конструкцией рычага предусмотрена постановка втулок в отверстия головок, то отверстия запрессованных втулок развертывают, а затем дорнуют или растачивают.
2.3.2.2. Технологический процесс обработки шатуна
Шатуны являются звеньями шатунно-кривошипных механизмов, главным образом поршневых двигателей внутреннего сгорания и компрессоров. В качестве материалов для шатунов используют стали 40, 45 с HB 210…255 и легированные стали 45Г2, 18ХНМА, 40ХНМ и др. с НВ 177…255, а также высокопрочные чугуны и титановые сплавы.
Заготовки шатунов автомобильных и тракторных двигателей получают в закрытых штампах на молотах и кривошипных прессах, используется и поперечно-винтовой прокат. Заготовки шатунов, как правило, получают цельными, а в процессе обработки крышку отрезают.
На рис. 2.11 показаны детали входящие в комплект шатуна. Крышку 2 – отъемную часть кривошипной головки – базируют
по плоскости разъема тела шатуна 1 и закрепляют презонными болтами 4 с гайками 5 или посредством уступов в месте стыка крышки с телом шатуна.
В кривошипные головки шатунов для снижения трения скольжения и упрощения ремонта шатунов устанавливают вкладыши с антифрикционным покрытием.
Технические требования на шатуны:
–отверстие под запрессовываемую втулку и отверстие в ней под поршневой палец должны быть изготовлены по посадкам Н7-Н8, для повышения точности сопряжения поршневого пальца шатуны сортируют на группы по диаметру отверстия втулок с интервалом 2,5 мкм;
–шероховатость поверхности отверстия втулки
Ra = 0,63-1,25 мкм;
–отверстия под вкладыши в кривошипных головках изготавливают по посадкам Н6-Н7 с шероховатостью Ra = 0,63-1,25 мкм;
Рис. 2.11. Детали шатуна:
1 – тело; 2 – крышка; 3 – втулка; 4 – болты; 5 – гайки
105
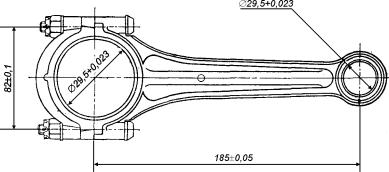
–допуск соосности отверстия запрессованной втулки с отверстием в кривошипной головке не более 0,04-0,05 мм на длине 100 мм, допуск параллельности этих осей 0,02-0,04 мм на длине 100 мм;
–отклонения межосевого расстояния ±(0,03-0,1) мм;
–допуск перпендикулярности торцов кривошипной головки
коси отверстия не более 0,005-0,01 мм на длине 100 мм;
–отверстия под призонные болты изготавливают по посадке Н9. При изготовлении шатунов на первой операции обрабатывают
торцы головок, базируя заготовку по противолежащим торцам – установочной базе и наружной поверхности, используемой в качестве направляющей и опорной баз. Обработанные торцы головок служат установочной базой для последующих операций. Для создания комплекта технологических баз протягивают площадки на весовых бобышках заготовок шатунов и боковых поверхностей поршневой и кривошипной головок, а также опорные площадки под головки болтов и гаек.
На рис. 2.12 показан шатун автомобильного двигателя, а в таблице 2.6 приведен типовой техпроцесс обработки в поточной линии.
В крупносерийном и массовом производстве обработку шатунов выполняют частично на отдельных автоматических линиях (по 2-4 операции в одной линии).
Шатуны контролируются после каждой операции и после полной обработки. Диаметры отверстий в головках шатунов проверяются предельными пробками-калибрами, индикаторными приборами, пневматическими пробками.
Рис. 2.12. Шатун автомобильного двигателя
106
107
Таблица 2.6. Типовой процесс обработки шатунов в поточной линии.
№ |
Операция |
Оборудование |
Технологические базы |
|
оп. |
||||
|
|
|
||
|
|
|
|
|
1. |
Фрезерная. Фрезерование торцов головок |
Карусельно-фрезерный или 2-х сторонний |
Торцы попеременно или |
|
|
|
продольно-фрезерный станок |
наружные поверхности головок |
|
2. |
Плоскошлифовальная. Шлифование торцов головок |
Плоскошлифовальный станок |
Торцы попеременно |
|
3. |
Протяжная. Протягивание базовых площадок на головках |
Протяжный специальный станок |
Торцы головок |
|
4. |
Расточная. Растачивание отверстия в малой головке |
Сверлильный специальный станок |
Торцы головок |
|
5. |
Фрезерная. Фрезерование мест под болты и гайки на большой головкеГоризонтально-фрезерный станок |
Торцы головок и малое |
||
|
|
|
отверстие |
|
6. |
Фрезерная. Разрезание большой головки |
Горизонтально-фрезерный станок |
Торцы головок и малое |
|
|
|
|
отверстие |
|
7. |
Протяжная. Протягивание плоскостей стыка шатуна и крышки |
Протяжный вертикальный станок |
Торцы и боковые поверхности |
|
8. |
Плоскошлифовальная. Шлифование плоскостей стыка шатуна и |
Плоскошлифовальный специальный станок |
Торцы и малое отверстие |
|
|
крышки |
|
|
|
9. |
Агрегатная. Сверление, растачивание и развертывание отверстий |
Специальный агрегатный станок |
Торцы и малое отверстие |
|
|
под болты в большой головке и крышке |
|
|
|
10. |
Сверлильная. Зенкование фасок в отверстиях под болты в большой |
Вертикально-сверлильный станок |
Стыковые поверхности |
|
|
головке и крышке |
|
|
|
11. |
Сверлильная. Подрезание облицовочным зенкером мест под болты и |
Вертикально-сверлильный станок |
Стыковые поверхности |
|
|
гайки в шатуне и крышке |
|
|
|
12. |
Сборочная. Сборка шатуна и крышки |
Верстак |
- |
|
13. |
Расточная. Черновое растачивание отверстия в большой головке |
Специализированный сверлильный станок |
Малое отверстие и торцы |
|
14. |
Вертикально-сверлильная. Зенкование фасок в отверстии большой |
Вертикально-сверлильный станок |
Торцы |
|
|
головки |
|
|
|
15. |
Плоскошлифовальная. Шлифование торцов большой головки |
Плоскошлифовальный станок |
Торцы попеременно |
|
16. |
Расточная. Чистовое растачивание отверстий в обеих головках |
Специальный расточной станок |
Торцы и базовая площадка |
|
17. |
Гидропрессовая. Прессование втулки в малую головку |
Гидропресс |
Торцы и базовая площадка |
|
18. |
Расточная. Тонкое растачивание отверстий в обеих головках |
Алмазно-расточный станок |
Торцы и базовая площадка |
|
19. |
Хонинговальная. Хонингование отверстия в большой головке |
Хонинговальный станок |
Торцы и базовая площадка |
|
20. |
Контрольная |
Контрольный стол |
- |
|
21. |
Подгоночная. Подгонка по массе большой головки |
Фрезерно-контрольный автомат |
Отверстие в малой головке |
|
22. |
Разборочная. Разборка шатуна и зачистка заусенцев |
Верстак |
- |
|
23. |
Сборочная. Сборка шатуна с крышкой и вкладышем |
Верстак |
- |
|
|
|
|
|
Расстояние между осями отверстий в деталях, отклонения от параллельности, перпендикулярности и положения осей отверстий измеряются так же, как и в корпусных деталях (см. п. 2.1.4).
Литература: [1-3, 7]
2.4. Технология обработки деталей класса “Полые цилиндры”
2.4.1. Общиесведенияодеталяхкласса“Полые цилиндры”
К данному классу относятся: втулки, гильзы, поршни, стаканы, барабаны, ступицы колес и т.п. детали, имеющие внутренние цилиндрические поверхности, а наружные – цилиндрическую или другую форму.
Главные технологические задачи при изготовлении деталей – это достижение концентричности внутренних и наружных поверхностей и перпендикулярности торцов к оси. Эти задачи решаются тремя способами: 1) обработкой поверхностей с одной установки заготовки; 2) обработкой сначала отверстия, а затем наружной поверхности при установке детали по отверстию; 3) обработкой сначала наружной поверхности, затем отверстия при установке детали по наружной поверхности.
Таблица 2.7. Технические условия на изготовление полых цилиндров.
Условия |
Допустимые отклонения |
|
Точность диаметров |
6-9-й квалитет |
|
Шероховатость внутренних поверхностей для |
1,25-0,32 |
мкм |
отверстий 7-9-го квалитета |
|
|
То же в деталях гидравлических систем |
0,32-0,08 |
мкм |
Шероховатость наружной поверхности при |
2,5-0,63 мкм |
|
посадках 7-9-го квалитета |
|
|
Радиальное биение наружной поверхности |
0,01-0,03 |
мм |
Торцевое биение (при соприкосновении торца с |
0,015-0,020 мм на радиусе 50 мм |
|
вращающейся деталью) |
|
|
Некруглость и отклонения профиля продольного |
В пределах поля допуска |
|
сечения (конусность, седлообразность и пр.) |
|
|
То же для точных деталей (7-й квалитет) |
В пределах половины поля |
|
|
допуска |
|
|
|
|
108
Материалы для полых цилиндров применяют самые разнообразные: чугун, сталь, бронзу, латунь, специальные сплавы, биметалл и металлокерамику в зависимости от назначения и условий работы детали в изделии.
Заготовки можно отрезать от прокатанных прутков или труб (сталь, латунь), от литых прутков небольшой длины (чугун, бронза). Можно применять штучные заготовки – литые в землю или в кокиль (чугун бронза специальные сплавы), штучные кованые (сталь) или штампованные (сталь, бронза). Кроме того, втулки можно свертывать из отрезков полосы (латунь, бронза, биметаллическая лента), прессовать из порошков (металлокерамика) и пластических масс.
Для обработки деталей из прутков диаметром до 50 мм в зависимости от типа производства применяют револьверные станки и одношпиндельные или многошпиндельные автоматы.
Детали диаметром свыше 50 мм желательно обрабатывать из цельнотянутых труб на токарных станках или многошпиндельных автоматах. Штучные заготовки можно обрабатывать на сверлильных, токарных станках, токарных полуавтоматах.
2.4.2. Технологическиепроцессыобработкиполых цилиндров
На рис. 2.13 представлены типовые схемы обработки простых втулок из прутка на револьверном станке (рис. 2.13, а) и на 6-ти шпиндельном автомате (рис. 2.13, б).
После отрезания втулки от прутка последующую операцию по снятию фаски и подрезке торца выполняют на токарном станке.
Втулки из штучных заготовок обрабатывают на сверлильных станках, прошивных прессах, протяжных, многорезцовых станках и многошпиндельных полуавтоматах.
Втулки с фланцем и буртиками обрабатывают на токарных станках – в единичном и мелкосерийном производстве, на многорезцовых токарных полуавтоматах – в серийном и крупносерийном производстве, на многошпиндельных полуавтоматах – в массовом производстве.
Шлицы в отверстиях втулок протягивают на протяжных станках или долбят на долбежном станке в поворотном приспособлении. Чистовую обработку наружной поверхности и торцов втулки выполняют на токарном станке с установкой детали на шлицевой оправке.
109
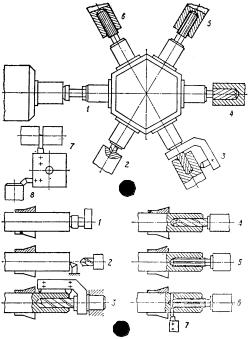
Обработка тонкостенных цилиндров высокой точности (гильз) имеет некоторые особенности. Представителями деталей этой группы могут быть тонкостенные чугунные гильзы автомобильных и тракторных двигателей, и стальные цилиндры гидросистем.
Гильзы тракторных двигателей изготавливают из чугуна. Твердость внутренней рабочей поверхности гильзы после закалки ТВЧ должна быть не ниже HRC 40, шероховатость после обработки – 0,32-0,16 мкм, овальность и конусность не более 0,02 мм, точность отверстия – 6-7-й квалитет, наружных поясков – 7-8-й квалитет с шероховатостью Ra = 1,25-0,63 мкм. Биение наружных диаметров и торцов – 0,02-0,08 мм.
После изготовления гильзы сортируют на 4-5 групп.
Заготовки чугунных гильз получают центробежным литьем или отливкой в оболочковые формы. Припуски на обработку отверстий гильз принимают 3-6 мм, для наружных поверхностей –
4-5 мм.
а
б
Рис. 2.13. Схемы обработки простых втулок:
а – на револьверном станке; б – на 6-ти шпиндельном автомате. Переходы: 1 – установка прутка до упора; 2 – подрезание торца на автомате и центрование; 3 – соответственно обточка наружной
поверхности, сверление отверстия, снятие наружной фаски;
4 – зенкерование; 5 – черновое развертывание; 6 – чистовое развертывание; 7 – отрезание детали; 8 – подрезание торца прутка на револьверном станке
110
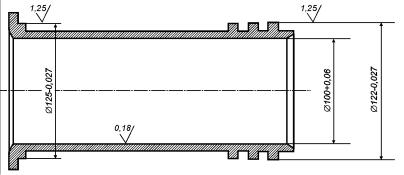
Рис. 2.14. Гильза тракторного двигателя
На рис. 2.14 показана гильза тракторного двигателя, а в таблице
2.8приведен маршрут обработки ее в поточной линии.
Вкрупносерийном и массовом производстве обработку гильз выполняют на отдельно скомпонованных автоматических линиях, включающих большинство операций выше приведенного технологического процесса:
1-я линия – оп. 1 и 2; 2-я линия – оп. 6, 7, 8 и 9; 3-я линия – оп. 10-16.
Контроль гильз производится в основном по посадочным пояскам и по точности и макрогеометрии отверстия. Для контроля диаметров посадочных поясков используют многомерные микрометры с электроконтактными датчиками, скобы, универсальные микрометры, индикаторные приборы.
Для измерения и сортировки гильз по зеркалу (отверстию) используют пневморотаметры с тремя парами сопел вдоль оси отверстия. Некруглость измеряют шестимерными пневморотаметрами. Концентричность трех поясков гильзы проверяют одновременно тремя индикаторами. При шлифовании посадочных поясков и хонинговании отверстия в гильзах применяется активный контроль в процессе обработки.
Остальные детали класса “Полые цилиндры” контролируются
взависимости от вида поверхностей методами, указанными в разделе 1.
Литература:[ 2, 3]
111
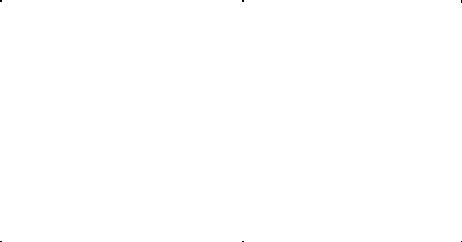
112
Таблица 2.8. Технологический процесс обработки гильз в поточной линии
№ |
Операция |
Оборудование |
Технологические базы |
|
оп. |
||||
|
|
|
||
|
|
|
|
|
1. |
Токарная. Черновое растачивание отверстий |
Токарный многошпиндельный вертикальный полуавтомат |
Наружный диаметр и левый торец |
|
2. |
Токарная. Черновое обтачивание поясков и подрезание торцов |
Токарный многорезцовый или гидрокопировальный полуавтомат |
Отверстие и торец |
|
3. |
Токарная. Получистовое обтачивание поясков и подрезание торцов |
Токарный многорезцовый или гидрокопировальный полуавтомат |
Отверстие и торец |
|
4 |
Шлифовальная. Шлифование поясков |
Бесцентровошлифовальный или круглошлифовальный станок |
Наружная поверхность или отверстие и торец |
|
5. |
Термическая |
Установка в ТВЧ |
- |
|
6. |
Токарная. Получистовое растачивание отверстия |
См. оп. 1 |
См. оп. 1 |
|
7. |
Токарная. Чистовое обтачивание поясков и подрезание буртов |
См. оп. 2 |
См. оп. 2 |
|
8. |
Токарная. Чистовое растачивание отверстия |
См. оп. 1 |
См. оп. 1 |
|
9. |
Токарная. Чистовое обтачивание конуса, поясков и фасок |
См. оп. 2 |
См. оп. 2 |
|
10. |
Хонинговальная. Предварительное хонингование отверстия |
Хонинговальный станок |
Пояски и торец |
|
11. |
Хонинговальная. Чистовое хонингование отверстия |
Хонинговальный станок |
Пояски и торец |
|
12. |
Шлифовальная. Чистовое шлифование поясков |
Круглошлифовальный станок |
Отверстие и торец |
|
13. |
Хонинговальная. окончательное (зеркальное) хонингование отверстия |
См. оп. 10 |
См. оп. 10 |
|
14. |
Моечная. Промывка деталей |
Моечная установка |
- |
|
15. |
Контрольная. Контроль и сортировка гильз на группы |
Контрольный стол |
- |
|
16. |
Консервация. Антикоррозионная обработка, консервация гильз |
Специальный стенд |
- |
|
|
|
|
|