
Типовые детали
.pdf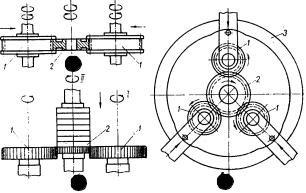
как правило, двусторонними головками, а с малым количеством – односторонними.
2.5.5. Накатываниеизакруглениезубьевзубчатыхколос
Накатывание в 15-20 раз производительнее зубонарезания и, кроме того, отходы металла составляют всего 4-5% от веса заготовки. Зубья модулем до 1 мм обычно накатываются в холодном состоянии, а более 1 мм – горячим или комбинированным способом.
Горячее накатывание производится на специальном прокатном стане с нагревом заготовок токами высокой частоты до 1000-1100°С.
Поштучное накатывание (рис. 2.39, а) осуществляется путем постепенного вдавливания вращающихся валков 1 во вращающуюся заготовку 2.
Сближение валков производится с помощью ходовых винтов. Валки вращаются с реверсированием по автоматическому циклу, передавая вращательное движение заготовке. После выключения подачи валки совершают еще несколько оборотов для калибровки зубьев.
При накатывании нескольких заготовок сразу (рис. 2 39, б) рабочими движениями являются синхронизированные вращения I
иII валков 1 и заготовок 2 и осевое перемещение пакета заготовок относительно валков (сверху вниз). Межосевое расстояние валков
ипакета заготовок постоянно.
а
бв
Рис. 2.39. Накатывание зубчатых профилей:
а – штучное; б– пакетное; в– калибрование зубьев методом холодного накатывания
133
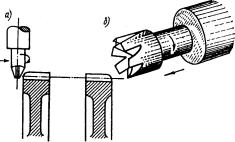
Производительность стана для штучных заготовок (рис. 2.39, а) 240-300 колес в час (m = 1,5-3 мм), а для пакетного 250-350 деталей в час (m = 2-5 мм). Производительность зубофрезерования для тех же колес 7-8 штук в час. По методу горячего накатывания достигается 8-9-я степени точности зубьев.
Калибрование зубьев на втором станке производится методом бесцентрового холодного пластического деформирования (рис. 2.39, в). Инструментом служат три накатника 1, расположенные под углом 120° и сидящие свободно на своих осях. Накатники приводятся во вращение заготовкой 2. Радиальная подача накатников осуществляется поворотом центрирующего кольца 3, имеющего эксцентричные участки. При этом шпиндели накатников перемещаются в радиальном направлении до упоров. По методу горяче-холодного накатывания достигается 7-8-я степень точности.
Вмашиностроении применяется накатывание и конических колес с прямыми и криволинейными зубьями с модулем до 10 мм и диаметром до 300 мм.
Применение накатывания помимо значительного снижения времени обработки и расхода материала, повышает срок службы зубчатых колес благодаря упрочнению зубьев пластическим деформированием.
У зубчатых колес, предназначенных для коробок передач и других зубчатых колес, переключающихся на ходу, для облегчения включения производится закругление торца зубьев на специальных зубозакругляющих станках при помощи пальцевых фрез методом копирования (рис. 2.40).
Впроцессе работы пальцевая фреза вращается и одновременно перемещается по дуге с возвратно-поступательным движением, огибая кромку зуба обрабатываемого колеса, которая периодически отводится в осевом направлении, поворачивается вокруг оси на один зуб и подводится к фрезе. Время обработки каждого зуба 1-3 с.
зубьев цилиндрических колес:
фрезой; б– пустотелойфрезой
134
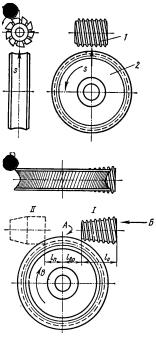
Большая производительность достигается при закруглении зубьев пустотелой фрезой (рис. 2.40, б).
2.5.6. Нарезаниезубьевчервячныхколесичервяков
При нарезании зубьев червячных колес на зубофрезерных станках ось фрезы устанавливается перпендикулярно оси колеса и точно по центру его ширины. Нарезать зубья можно способом радиальной подачи, тангенциальной подачи или комбинированным способом.
При способе радиальной подачи (рис. 2.41, а) фреза 1 и колесо 2 вращается таким образом, чтобы за один оборот фрезы колесо повернулось на число зубьев, равное числу заходов червяка.
Суппорт с фрезой стоят на месте, стол с колесом совершает горизонтальную подачу S на глубину зуба в радиальном направлении. а В зубофрезерных станках, предназначенных для нарезания колес большого диаметра, горизонтальная подача осуществляется стойкой, несущей суппорт
с фрезой.
Способ радиальной подачи применяется в основном для нарезания червячных зубчатых колес однозаходных и реже – двухзаходных.
Нарезание зубьев червячных колес
бспособом тангенциальной подачи фрезы осуществляется на зубофрезерных станках, имеющих тангенциальный суппорт (рис. 2.41, б). Нарезание зубчатого венца заканчивается, когда все зубья фрезы перейдут за ось колеса. При нарезании способом тангенциальной подачи получается более правильный профиль зубьев, но фреза дороже цилиндрической. Этот способ применяется в основном для нарезания червячных зубчатых колес к многозаходным червякам.
Рис. 2.41. Зубонарезание червячных колес червячными фрезами:
а – способом радиальной подачи; б – способомтангенциальной подачи;
I-II – соответственно начальное и конечное положение фрезы
135
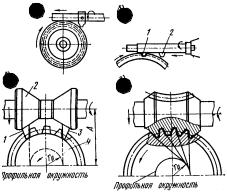
|
а |
б |
В единичном произ- |
|
|
водстве при отсутствии |
|
|
|
|
|
|
|
|
фрез нарезание червячных |
|
|
|
колес осуществляется ком- |
в |
|
г |
бинированным способом |
|
последовательно двумя рез- |
||
|
|
||
|
|
|
|
|
|
|
цами, закрепленными в оп- |
|
|
|
равке – черновым и чисто- |
|
|
|
вым (рис. 2.42, а). |
|
|
|
Черновой резец уже |
|
|
|
чистового примерно на |
|
|
|
0,5 мм и врезается на тре- |
Рис. 2.42. Зубонарезание червячных зуб- |
буемую глубину с радиаль- |
||
|
|
чатых колес: |
ной подачей. Чистовой ре- |
|
|
а– однимрезцом; б– двумярезцами; |
зец изготавливается точно |
|
|
в – двумя резцами глобоидного |
по профилю впадины и до- |
|
|
колеса; г – червячной фрезой |
резает зуб с тангенциаль- |
|
|
глобоидного колеса |
ной подачей. Часто закрепляют оба резца в одной оправке (рис. 2.42, б) на определенном расстоянии один от другого.
Нарезание зубьев червячного глобоидного колеса обычно состоит из двух операций: предварительного нарезания при радиальной подаче и чистового нарезания при круговой подаче и точно заданном межосевом расстоянии. Инструментом для предварительного и окончательного нарезания зубьев глобоидного колеса в единичном и мелкосерийном производствах являются два “летучих” резца (рис. 2.42, в). Как предварительное, так и окончательное нарезание глобоидных колес можно производить глобоидной гребенкой или глобоидной фрезой (рис. 2.42, г).
Способы нарезания червяков зависят от профиля витка. Цилиндрические червяки разделяются на следующие основные виды: архимедовы, имеющие прямолинейный профиль в осевом сечении и архимедову спираль в торцовом сечении; эвольвентные, имеющие криволинейный профиль в нормальном сечении, эвольвентный в торцовом и прямолинейный в сечении плоскостью, касательной к основному цилиндру; конвалютные, имеющие прямой профиль в нормальном к витку сечении и удлиненную эвольвенту (конвалюту) в торцовом сечении; нелинейчатые, имеющие во всех сечениях криволинейный профиль.
136

Глобоидные червяки в осевом сечении представляют собой круговую рейку с прямолинейными боковыми сторонами.
Винтовая поверхность цилиндрических червячков в зависимости от серийности производства может быть нарезана следующими способами: профильными резцами на токарно-винторезных станках; дисковыми фрезами на универсально-фрезерных, резьбофрезерных
испециальных станках; пальцевыми фрезами на универсальнофрезерных станках; круглыми долбяками на специальных или универсальных зубофрезерных станках, оснащенных протяжным суппортом; червячными фрезами по методу обката на универсальных зубофрезерных и шлицефрезерных станках; резцовыми головками (вихревое нарезание) на токарно-винторезных станках, так же, как
ирезьбы.
При нарезании червяков на токарно-винторезных станках требуемый профиль витка обеспечивается при этом соответствующей установкой резца.
Для нарезания архимедова червяка резец с прямолинейным профилем устанавливают так, чтобы его режущие кромки лежали в осевой плоскости червяка (рис. 2.43, а).
Червяки с малым углом подъема винтовой линии нарезают двусторонним резцом. При больших углах подъема винтовой линии раздельно обрабатывают левую и правую стороны витка односторонними резцами.
При нарезании эвольвентного червяка резец с прямолинейным профилем устанавливают так, чтобы его режущие кромки расположились в плоскости, касательной к осевому цилиндру (рис. 2.43, б). Эвольвентные червяки с углом подъема витка более 5° нарезают резцами с профилем, криволинейным в осевом или нормальном сечениях.
а |
б |
в |
Рис. 2.43. Схемы нарезания резцами червяков:
а – архимедова; б – эвольвентного; в – конвалютного
137
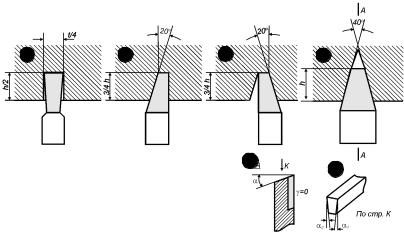
Для нарезания конвалютного червяка резец с прямолинейным профилем устанавливают так, чтобы его режущие кромки соответственно требуемым геометрическим параметрам червяка лежали в плоскости, нормальной направлению витка или направлению впадины (рис. 2.43, в).
Крупномодульные архимедовы червяки с углом трапеции 40° обычно нарезаются на токарно-винторезных станках за 4 перехода
(рис. 2.44).
На первом переходе прорезается прямоугольная канавка глубиной на половину профиля червяка, т.е. 1/2 h и шириной 1/4 шага витка (рис. 2.44, а).
На втором переходе (рис. 2.44, б) подрезается левая боковая поверхность витка до глубины 3/4 h.
На третьем переходе (рис. 2.44, в) подрезается правая боковая поверхность витка до глубины 3/4 h.
На четвертом переходе (рис. 2.44, г) производится калибровка профиля витка на полную глубину точно доведенным трапециевидным резцом с углами: γ = 0, α = 12-15° (рис. 2.44, д).
В калибровочном резце вспомогательные задние углы α 1 и α 2 различны (рис. 2.44, е). Угол α 1, совпадающий с направлением осевой подачи, принимается равным сумме углов α 2 + β , где β – угол подъема винтовой линии витка червяка; угол α 2 принимается 8-10°. Такие же требования по углам α 1 и α 2 предъявляются при нарезании мелкомодульных червяков одним резцом.
а |
б |
в |
д
Рис. 2.44. Нарезание крупномодульного червяка резцами:
а – прорезным; б, в – профильными односторонними; г – профильным двусторонним
г
е
138
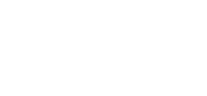
Рис. 2.45. Схема нарезания червяка дисковой фрезой
Режимы резания при черновом нарезании: V = 8-12 м/мин, глубина резания t= 0,2-0,3 мм; при чистовом V = 0,8-6 м /мин, t = 0,05-0,15 мм. После нарезания
витка производится выхаживание без радиальной подачи за 4-5 рабочих ходов. В качестве СОЖ используется мыльная эмульсия, растительные масла (хлопковое, подсолнечное, пальмовое).
При нарезании червяков резцами достигается шероховатость рабочих поверхностей витка Ra = 1,25 мкм.
Цилиндрические червяки нарезают дисковым фрезами (рис. 2.45). Для нарезания фрезу устанавливают так, чтобы ее ось вращения была наклонена на угол подъема витка червяка λ д, а средняя точка
располагалась на одной высоте с осью червяка.
Для нарезания архимедова, эвольвентного и нелинейного червяков фреза должна иметь криволинейный профиль, а для нарезания конвалютного червяка – прямолинейный.
Фрезерование дисковыми фрезами в основном применяют для чернового нарезания витков; в этом случае используют фрезы с прямолинейным профилем.
Пальцевые фрезы используют для нарезания крупномодульных червяков в мелкосерийном и единичном производстве. Фрезу устанавливают так, чтобы ее ось вращения пересекала ось червяка под углом 90°.
В крупносерийном и массовом производстве архимедовы и эвольвентные червяки нарезают круглым долбяком. При обработке червяк и долбяк вращаются (их оси вращения пересекаются под прямым углом) и одновременно долбяк перемещается вдоль оси червяка. Для червяков с углом подъема витка менее 6° используют прямозубые долбяки, при угле подъема более 6° – косозубые. Этот метод обеспечивает высокую точность обработки и большую производительность.
Червячными фрезами по методу обката нарезают эвольвентные червяки с большим углом подъема витка, для чего используют червячные фрезы с прямолинейной режущей кромкой. Этот способ обеспечивает высокую производительность, так как все витки
139
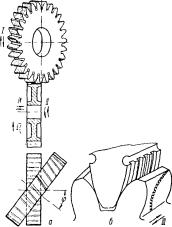
многозаходных червяков нарезают одновременно, однако получаемая при этом точность (8-9-я степени) невысока, поэтому его применяют
восновном на предварительных операциях.
2.5.7.Чистоваяотделказубьевзубчатыхколеси червяков
Окончательная чистовая отделка зубьев колес и червяков производится следующими способами: обкаткой, шевингованием, шлифованием, притиркой и приработкой.
Обкатка незакаленного зубчатого колеса осуществляется путем вращения его между тремя вращающимися закаленными шлифованными зубчатыми колесами (эталонами), точность которых достигает ±5 мкм. При обкатке исправляются небольшие погрешности формы зуба, снижается шероховатость поверхностей зубьев.
Шевингование – процесс чистовой отделки зубьев незакаленного зубчатого колеса, заключающийся в снятии (соскабливании) очень мелких волосообразных стружек, благодаря чему исправляются эксцентриситет начальной окружности, ошибка в шаге, в профиле эвольвенты и угле подъема винтовой линии.
На рис. 2.46 показана схема шевингования зубчатого колеса круглым шевером.
Шевер получает вращательное движение I (рис. 2.46, а) и вращает обрабатываемое колесо (движение II). Вращение шевера и колеса реверсируются для равномерной отделки обеих сторон зубьев.
Металл с боковой поверхности зуба снимается соединяющей последовательные точки сопряженных профилей зубьев шевера и
.46, б).
стружки по всей длине зуба колесу дополнительное продольное перемещение III.
осей шевера и колеса после каждого производится за счет радиальной
колеса.
Величина радиального припуска под шевингование для колес с модулем
Рис. 2.46. Схема шевингования зубчатого колеса круглым шевером
140
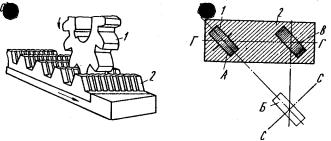
а |
б |
Рис. 2.47. Шевингование шевер-рейкой:
а – схема шевингования; б– схема скольжения шевер-рейки по зубьям зубчатого колеса
2-5 мм принимается от 0,08 до 0,25 мм. У головки и основания зуба припуск не предусматривается.
Шевинговать цилиндрические зубчатые колеса можно шеверрейками (рис. 2.47).
Впроцессе обработки стол станка с закрепленной на нем шеверрейкой имеет возвратно-поступательное движение. Как и дисковый шевер, шевер-рейка изготавливается с наклонными зубьями для
шевингования колес с прямым зубом, для обработки колес с косым зубом с углом наклона зубьев около 15° шевер-рейка может иметь прямые зубья.
Впроцессе шевингования осуществляется продольное скольжение зубьев шевер-рейки по зубьям колеса (рис. 2.47, б). Так как зубчатое колесо и шевер-рейка представляют собой как бы винтовую зубчатую пару со скрещивающимися осями, то колесо из положения
Апередвинется не в положение Б, а в положение В. В результате создается относительное скольжение зубьев колеса и шевер-рейки, определяемое отрезком между положением Б и В колеса; при этом происходит процесс снятия стружки с поверхности зуба.
После каждого хода стола колесо перемещается в вертикальном направлении вниз на 0,025-0,04 мм. В качестве СОЖ используется сульфофрезол или веретенное масло.
Шевингование применяется для отделки зубьев конических и червячных колес.
На рис. 2.48 показана схема шевингования червячного колеса шевер-червяком.
При изготовлении точных колес (5-6-й степени точности) их зубья шлифуют после термической обработки. При деформации зубьев после термической обработки более 0,05 мм и биении
141
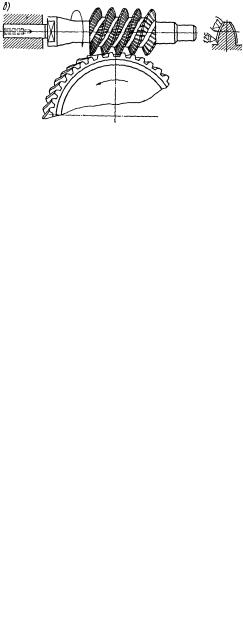
Рис. 2.48. Схема шевингования червячного колеса шевер-червяком
делительной окружности более 0,1 мм необходимо шлифовать зубья даже для достижения 7-й степени точности.
Применяют три способа шлифования зубьев: копирование, обкатка дисковыми кругами с прямолинейными боковыми сторонами, обкатка червячным кругом.
Во время обработки зубьев методом копирования (рис. 2.49) колесо неподвижно, а шлифовальный круг, вращаясь со скоростью V = 30-35 м/с, совершает возвратно-поступательное движение I вдоль оси колеса со скоростью 8-16 м/мин.
После каждого двойного хода шлифовального круга колесо поворачивается на один зуб и фиксируется в новом положении.
Профилирование круга осуществляется алмазами при помощи шаблонных пантографов.
Методом копирования могут шлифоваться зубья одновременно двумя односторонними шлифовальными кругами.
При припуске на толщину зуба 0,2-0,3 мм шлифование производится за 3-4 рабочих хода. Время обработки одного зуба методом копирования составляет 0,3-0,8 мин для колес с модулем 2-5 мм.
Недостатком метода копирования является потребность в большом количестве специальных шаблонов, делительных дисков, а также сложная переналадка станка.
Шлифование зубьев по методу обкатки производится двумя тарельчатыми кругами (или одним конусным кругом), расположенных так, что их шлифующие части образуют зуб производящей рейки того же модуля и угла зацепления, что и обрабатываемое колесо. При шлифовании двумя кругами обраба-
Рис. 2.49. Шлифование зубьев методом копирования
142