
2
.pdf
Определение основного времени в этом случае производится по формуле
t |
o |
|
lo |
|
lвр |
lп |
z i |
(4.11) |
|
S |
о |
n |
q |
||||||
|
|
|
|
||||||
|
|
|
|
ф |
|
|
|
где 10 — длина нарезаемых шлицев в мм; lвр — величина врезания в мм;
lвр (1,1...1,2) |
h(Dф h) |
(4.12) |
h — высота шлица в мм;
Dф — диаметр червячной фрезы в мм; lп — величина перебега, равная 2...5 мм; z — число нарезаемых шлицев;
i — число ходов (обычно i = 1);
S0 — подача фрезы в мм на один оборот нарезаемого вала; n — частота вращения фрезы, мин-1;
q —число заходов червячной фрезы.
При центрировании втулки (или зубчатого колеса) по внутреннему диаметру шлицев вала как червячная, так и дисковая фреза должна иметь «усики», вырезающие канавки в основания шлица, чтобы не было заедания во внутренних углах; эти канавки необходимы также при шлифовании по боковым сторонам и внутреннему диаметру.
4.3.2 Выбор вспомогательного, дополнительного и подготовительно-заключительного времени
Вспомогательное время на установку и снятие деталей в зависимости от веса и характера установки деталей приведено в таблице 4.17 (для ремонтных мастерских общего назначения) и таблице 4.20 (для специализированных ремонтных предприятий и заводов).
Вспомогательное время, связанное с проходом, приведено в таблице 4.18 (для мастерских общего назначения) и таблице 4.21 (для специализированных ремонтных предприятий и заводов).
Дополнительное время рассчитывают по формуле 2.7 Подготовительно-заключительное время для мастерских общего назначения берут из таблицы
4.19, для специализированных ремонтных предприятий и заводов — из таблицы 4.22.
Таблица 4.17. Вспомогательное время на установку и снятие детали (для мастерских общего назначения), мин
|
|
Вес детали не более, |
кг |
|
|||
Установка |
|
|
|
|
|
|
|
|
|
|
|
|
|
|
|
|
|
|
|
|
|
|
|
|
1 |
3 |
5 |
10 |
|
20 |
30 |
В центрах |
0,2 |
0,5 |
0.6 |
0,7 |
|
1,0 |
1,4 |
|
|
|
|
|
|
|
|
В трехкулачковом патроне |
0,1 |
0,2 |
0,3 |
0,4 |
|
0,6 |
— |
В тисках с простой выверкой |
0,3 |
0,6 |
0,7 |
0,8 |
|
1,0 |
— |
В тисках с выверкой средней |
0,4 |
0,9 |
1,2 |
1,5 |
|
2,0 |
— |
сложности |
|
||||||
|
|
|
|
|
|
|
|
На призмах |
0,6 |
1,0 |
1,3 |
1,6 |
|
2,1 |
2,4 |
На столе с простой выверкой |
0,7 |
0,9 |
1,2 |
1,5 |
|
1,8 |
2,2 |
|
|
|
|
|
|
|
|
На столе с выверкой средней |
1,0 |
1,2 |
1,5 |
1,8 |
|
2,2 |
3,0 |
сложности |
|
||||||
|
|
|
|
|
|
|
51
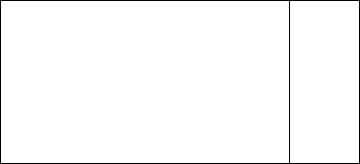
Таблица 4.18. Вспомогательное время, связанное с проходом (для мастерских общего назначения)
Наименование проходов |
Время на один |
|
проход, мин |
||
|
||
Обработка плоскостей на первый проход с двумя пробными |
1,4 |
|
стружками |
||
|
||
Обработка плоскостей на первый проход с одной |
10 |
|
пробной стружкой |
||
|
||
Обработка плоскостей на последующие проходы |
0,3 |
|
Обработка пазов на первый проход с одной проб- |
1,0 |
|
ной стружкой |
||
|
||
Обработка пазов на последующие проходы |
0,4 |
Примечание. При фрезеровании партии одинаковых деталей время на первый проход принимают только для первой детали, а для остальных деталей считают, как на последующие.
Таблица 4.19. Подготовительно-заключительное время (для мастерских общего назначения)
Способ установки |
Время, |
|
мин |
На столе с креплением болтами |
12 |
В тисках |
16 |
В центрах с делительной головкой |
19 |
На угольнике |
12 |
Установка одной фрезы |
12 |
Таблица 4.20. Вспомогательное время на установку и снятие детали (для специализированных ремонтных предприятий и заводов), мин
Способ установки |
Характер |
Вес детали не более, кг |
|
|
|
|
|
|||
|
выверки |
1 |
3 |
5 |
8 |
12 |
20 |
50 |
120 |
200 |
На столе с креплением болтами и |
Простая |
1,0 |
1,2 |
1.4 |
1.6 |
1,9 |
2,2 |
3,9 |
4,9 |
5,4 |
планками |
Сложная |
1,6 |
1.9 |
2,0 |
2,2 |
2,5 |
2,9 |
6,0 |
7,0 |
8,9 |
На угольнике с креплениями болтами |
Простая |
0,9 |
1,1 |
1.3 |
1.5 |
1,7 |
2.1 |
5,5 |
— |
— |
и планками |
Без выверки |
0,7 |
0,3 |
1,0 |
1,1 |
1.2 |
1,3 |
— |
|
|
В тисках с винтовым зажимом |
Простая |
0,4 |
0,5 |
0.5 |
0,6 |
0,6 |
— |
— |
— |
— |
|
Без выварки |
0,2 |
0.2 |
0,3 |
0,3 |
0,3 |
|
|
|
|
|
|
|
|
|
|
|
|
|
|
|
В тисках с пневматическим зажимом |
Простая |
0,4 |
0,4 |
0,5 |
0,5 |
0,6 |
0,7 |
0,9 |
— |
— |
|
Без выверки |
0,2 |
0.2 |
0,2 |
0,3 |
0,3 |
|
|
|
|
В центрах |
Простая |
0,25 |
0,26 |
0,34 |
0,43 |
0,48 |
0,55 |
— |
— |
— |
|
Сложная |
0,35 |
0,44 |
0,55 |
0,60 |
0,75 |
0,85 |
|
|
|
|
|
|
|
|
|
|
|
|
|
|
На оправке |
Простая |
0,46 |
0,49 |
0,60 |
0,65 |
0,75 |
0,85 |
— |
— |
— |
|
Сложная |
0,65 |
0,75 |
0,85 |
0,95 |
1,10 |
1,20 |
|
|
|
В самоцеатрирующем патроне |
— |
0,18 |
0,19 |
0,22 |
0,26 |
0,32 |
0,39 |
— |
— |
— |
В цанговом патроне |
— |
— |
0,40 |
0,45 |
0,5 |
0,6 |
— |
— |
— |
— |
Таблица 4.21. Вспомогательное время, связанное с проходом (для специализированных ремонтных предприятий и заводов
Наименование проходов |
Время |
на |
|
один |
проход, |
|
мин |
|
Обработка плоскостей на первый проход с двумя |
1,0 |
|
пробными стружками |
|
|
Обработка плоскостей на первый проход с одной |
0,7 |
|
пробной стружкой |
|
|
Обработка плоскостей на последующие проходы |
0,1 |
|
|
|
|
Обработка пазов на первый проход с одной |
0,8 |
|
пробной стружкой |
|
|
Обработка пазов на последующие проходы |
0,2 |
|
Таблица 4.22. Подготовительно-заключительное время: (для специализированных ремонтных предприятий и заводов)
Способ установки |
Время, мин |
|
|
На столе с креплением болтами и планками |
24 |
В тисках |
22 |
В центрах |
28 |
В самоцентрирующем патроне |
16 |
В приспособлении |
27 |
Установка фрезы |
2 |
52
5 РАСЧЕТ РЕЖИМОВ РЕЗАНИЯ И НОРМЫ ВРЕМЕНИ ПРИ ШЛИФОВАЛЬНЫХ РАБОТАХ
5.1 Общие сведения
Шлифование является основным методом чистовой, отделочной обработки металлов, при которой добиваются высокой степени чистоты поверхности и точности обработки. Такие результаты возможны благодаря тому, что шлифовальным кругом можно снимать очень тонкий слой металла, равный тысячным долям миллиметра.
При шлифовании с поверхности детали снимают излишний слой металла при помощи специального абразивного инструмента — шлифовального круга, который представляет собой пористое тело, состоящее из большого количества мелких зерен очень твердого материала. Эти зерна соединены между собой особым веществом, которое называют связкой. Твердые материалы, из которых состоят зерна шлифовального круга, называют абразивными материалами. Выбор характеристик шлифовальных кругов для различных условий шлифования приведен в приложении 2.
Абразивные зерна шлифовального круга тверды, теплоустойчивы и своими острыми кромками выполняют роль резцов. Выступающие зерна абразивного материала при вращении круга снимают слой металла с обрабатываемой детали.
Абразивные зерна круга в процессе работы притупляются, часть их выпадает, круг постепенно теряет свою форму и режущие свойства. Для восстановления этих свойств круга необходимо периодически его править алмазами, шарошками или другими абразивными кругами.
Шлифовальные круги характеризуются величиной абразивных зерен и твердостью. Правильный выбор абразивного инструмента для обработки той или иной детали обеспечивает требуемую чистоту поверхности, максимальную производительность и наименьший расход абразивных инструментов.
При выборе круга большое значение имеет обрабатываемый материал. Как правило, очень твердые материалы следует обрабатывать более мягкими кругами, так как в таких кругах изношенные (затупленные) зерна скорее выкрашиваются, обнажая новые, острые зерна.
Материалы с низким пределом прочности, такие как чугун, мягкая сталь, бронза, рекомендуется обрабатывать твердыми кругами (из карбида кремния). Крупнозернистые круги применяют для грубого, мелкозернистые — для чистового шлифования.
В процессе шлифования в месте контакта круга с деталью возникает высокая температура (до 1500ºС), которая повышается с увеличением износа круга. Повышение температуры может вызвать деформацию изделия, прожог и трещины в обработанной поверхности. Поэтому процесс шлифования, как правило, сопровождается охлаждением обрабатываемой поверхности. Охлаждающая жидкость не только снижает температуру и повышает качество обработанной поверхности, но и удаляет абразивную и металлическую пыль из воздуха.
Струю охлаждающей жидкости следует направлять таким образом, чтобы она омывала круг и деталь и особенно обильно поступала в места соприкосновения детали с кругом.
В зависимости от обрабатываемых поверхностей и методов обработки используют различные виды шлифования.
Наружное круглое шлифование применяют при обработке наружных цилиндрических или конических поверхностей. Оно может быть выполнено способами продольной и поперечной подач, а также глубинным и бесцентровым шлифованием.
Круглое внутреннее шлифование применяют для обработки внутренних цилиндрических или конических поверхностей.
Плоское шлифование применяют для обработки плоскостей.
Наружное круглое шлифование.
В ремонтных предприятиях наибольшее применение имеют круглошлифовальные станки, основные характеристики которых приведены в приложении 1.
При наружном круглом шлифовании способом продольной подачи (рис. 5.1) шлифовальный круг имеет два движения: вращательное вокруг оси и поступательное в направлений обрабатываемой детали. Поступательное движение круга, то есть поперечная подача, осуществляется в конце продольного хода детали. Припуск на обработку при этим методе снимается за несколько проходов.
53
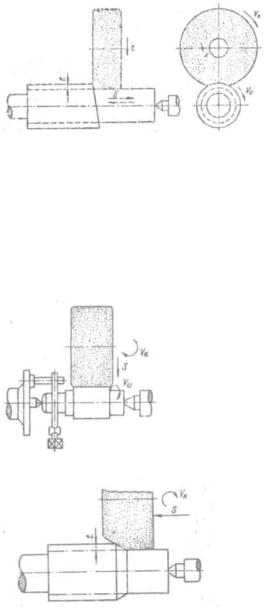
Рис. 5.1 Наружное круглое шлифование методом продольной подачи
При наружном круглом шлифовании методом поперечной подачи или методом врезания (риc. 5.2) продольное перемещение круга или заготовки отсутствует. В этом случае круг обрабатывает одновременно всю длину вращающейся детали. Круг же вращается и одновременно перемещается в поперечном направлении.
При глубинном шлифовании (рис. 5.3) круг устанавливают на полную глубину и припуск снимают за один-два прохода. В этом случае круг имеет вращательное движение и продольное перемещение, а деталь — только вращательное движение.
Рис. 5.2. Наружное круглое шлифование методом поперечной подачи.
Рис. 5.3. Метод глубинного шлифования.
5.2 Выбор режима резания при шлифовании
Под режимом круглого наружного шлифования понимают окружную скорость детали, поперечную и продольную подачи детали.
Назначение режима резания при наружном круглом шлифовании начинается с определения припуска на обработку. Припуск на обработку (на сторону) определяют по формуле:
h |
D d |
(5.1) |
|
||
2 |
|
где D — диаметр детали до шлифования, мм; d — диаметр шлифованной детали, мм.
При чистовом шлифований припуск на обработку распределяют следующим образом: 60—80% на черновое (предварительное) и 20—40% на чистовое (окончательное) шлифование.
Величину поперечного перемещения шлифовального круга по направлению к обрабатываемой детали в конце каждого хода называют глубиной шлифования или поперечной подачей. Глубина шлифования или толщина слоя металла, снимаемого за один проход шлифовального круга при круглом
54
шлифовании, колеблется в пределах от 0,005 до 0,08 мм.
Продольной подачей при круглом шлифовании называют путь, пройденный деталью за время одного оборота шлифуемой детали.
Поперечную и продольную подачу для черновой (предварительной) обработки определяют по таблицам 5.1 и 5.2, а для чистовой (окончательной) обработки — по таблице 5.3.
Tаблица 5.1. Поперечные подачи при предварительном шлифовании методом продольной подачи, мм
Обрабатываемый |
Длина, |
Диаметр шлифуемой детали не более, мм |
|||||
материал |
выраженная |
20 |
40 |
60 |
80 |
100 |
150 |
|
в диаметрах |
|
|
|
|
|
|
|
3Д |
0,020 |
0,028 0 |
0,034 |
0,039 |
0.043 |
0,052 |
Незакаленная сталь |
7Д |
0,017 |
0,033 |
0.028 |
0,032 |
0.035 |
0,042 |
|
10Д |
0,015 |
0,020 |
0,024 |
0,027 |
0,030 |
0,036 |
|
3Д |
0.015 |
0.023 |
0,030 |
0,035 |
0,040 |
0,045 |
Закаленная сталь |
7Д |
0,012 |
0,018 |
0.023 |
0,027 |
0,030 |
0,035 |
|
10Д |
0,010 |
0,015 |
0.019 |
0,022 |
0,025 |
0,030 |
Таблица 5.2. Продольные подачи в долях ширины круга β при предварительном шлифовании
Обрабатываемый материал |
Поперечная подача t не более, мм |
|
||||
|
0,01 |
0,02 |
0,03 |
0,04 |
0,06 |
0,09 |
Незакаленная сталь |
0,6 |
0,5 |
0,4 |
0,3 |
0,25 |
0,2 |
Закаленная сталь |
0,5 |
0,45 |
0,35 |
0,25 |
0,2 |
0,15 |
Таблица 5.3. Поперечные и продольные подачи при окончательном (чистовом) шлифовании незакаленной и закаленной стали
Диаметр |
|
Поперечная подача |
Продольная подача |
Окружная |
шлифуемой |
|
(глубина |
в долях ширины |
скорость детали, v |
поверхности |
не |
шлифовании), мм |
круга (Р) |
м/мин |
более, мм |
|
|
|
|
60 |
|
0,005-0,010 |
0,2-0,3 |
15-25 |
120 |
|
0,005-0,010 |
0,2-0,3 |
20-35 |
200 |
|
0,005-0,015 |
0,2-0,3 |
25-45 |
По принятой поперечной подаче определяют число проходов по формуле: |
|
|||
i |
h |
|
(5.2) |
|
t |
||||
|
|
где t — поперечная подача (глубина шлифования), мм.
Продольная подача в таблице дана в долях ширины шлифовального круга, поэтому пересчитываем ее по формуле:
Sпр Вк |
(5.3) |
где Sпр— продольная подача, мм/об Вк— ширина шлифовального круга, мм;
β— продольная подача в долях ширины круга.
Скорость резания при шлифовании по существу является скоростью вращения шлифовального круга. При назначении скорости вращения круга должны быть учтены механические свойства обрабатываемой детали и требуемая чистота обработки. Значения окружных скоростей при шлифовании закаленных и незакаленных сталей приведены в таблицах 5.4 и 5.5.
55

Частота вращения детали определяют по формуле: |
|
n 318V |
(5.4) |
d
где v —окружная скорость детали, м/мин; d — диаметр детали, мм.
Таблица 5.4. Окружная скорость детали при шлифовании незакаленной стали, м/мин
Продольная |
Глубина |
|
Диаметр шлифуемой поверхности не более, мм |
|||||
подача в |
шлифования |
t |
20 |
40 |
60 |
80 |
100 |
150 |
долях ширины |
не более, мм |
|
|
|
|
|
|
|
круга β |
|
|
|
|
|
|
|
|
не более |
|
|
|
|
|
|
|
|
|
0,01 |
|
56 |
70 |
79 |
84 |
90 |
|
0,3 |
0,02 |
|
28 |
35 |
39 |
42 |
46 |
52 |
0,04 |
|
14 |
17 |
20 |
21 |
23 |
. 26 |
|
|
|
|||||||
|
0,06 |
|
10 |
12 |
14 |
14 |
15 |
18 |
|
0,01 |
|
42 |
52 |
59 |
65 |
69' |
77 |
0,4 |
0,02 |
|
21 . |
26 |
29 |
32 |
35 |
39 |
0,04 |
|
11 |
13 |
15 |
16 |
17 |
20 |
|
|
|
|||||||
|
0,06 |
|
7 |
8 |
10 |
11 |
12 |
13 |
|
0,01 |
|
34 |
42 |
48 |
51 |
55 |
62 |
0,5 |
0,02 |
|
17 |
2! |
24 |
25 |
28 |
31 |
0,04 |
|
9 |
11 |
12 |
13 |
14 |
15 |
|
|
|
|||||||
|
0,06 |
|
6 |
7 |
8 |
8 |
9 |
11 |
|
0,02 |
|
14 |
18 |
20 |
21 |
23 |
26 |
0.6 |
0,03 |
|
10 |
11 |
14 |
14 |
15 |
17 |
0,04 |
|
7 |
8 |
10 |
11 |
12 |
13 |
|
|
|
|||||||
|
0,06 |
|
- |
- |
7 |
7 |
8 |
8 |
|
0,02 |
|
12 |
15 |
17 |
18 |
20 |
22 |
0,7 |
0,03 |
|
8 |
10 |
11 |
13 |
14 |
15 |
0,04 |
|
- |
7 |
8 |
9 |
10 |
11 |
|
|
|
|||||||
|
0,06 |
|
- |
- |
7 |
7 |
. 8 |
9 |
Таблица. 5.5 Окружная скорость детали при шлифовании закаленной стали, м/мин
Продольная |
|
Глубина |
|
Диаметр шлифуемой поверхности не мм |
|
|||||
подача |
в долях |
|
шлифования |
|
более, |
|
|
|
|
|
ширины |
круга β |
|
t не более, мм |
|
20 |
40 |
во |
80 |
100 |
160 |
не более |
|
|
|
|
|
|
|
|
|
|
0,3 |
|
0,01 |
|
51 |
63 |
70 |
76 |
81 |
|
|
|
|
0,02 |
|
25 |
31 |
35 |
38 |
42 |
46 |
|
|
|
0,03 |
|
17 |
21 |
24 |
25 |
28 |
32 |
|
|
|
0,05 |
|
10 |
12 |
14 |
16 |
17 |
18 |
|
0,4 |
|
0,01 |
|
38 |
46 |
54 |
58 |
62 |
69 |
|
|
|
0,02 |
|
20 |
24 |
27 |
30 |
31 |
35 |
|
|
|
0,03 |
|
13 |
16 |
18 |
20 |
21 |
23 |
|
|
|
0,05 |
|
6 |
8 |
9 |
10 |
10 |
11 |
|
0,6 |
|
0,01 |
|
31 |
38 |
43 |
45 |
49 |
66 |
|
|
|
0,02 |
|
16 |
20 |
21 |
23 |
25 |
28 |
|
|
|
0,03 |
|
10 |
12 |
14 |
16 |
17 |
20 |
|
|
|
0,05 |
|
6 |
8 |
9 |
10 |
10 |
11 |
|
0,6 |
|
0,02 |
|
13 |
16 |
17 |
20 |
2! |
24 |
|
|
|
0,03 |
|
9 |
10 |
12 |
13. |
14 |
16 |
|
|
|
0,04 |
|
6 |
8 |
9 |
9 |
10 |
11 |
|
|
|
0,05 |
|
5 |
6 |
8 |
8 |
9 |
10 |
|
0,7 |
|
0,02 |
|
11 |
14 |
16 |
17 |
18 |
21 |
|
|
|
0,03 |
|
7 |
8 |
10 |
11 |
13 |
16 |
|
|
|
0,04 |
|
6 |
7 |
8 |
9 |
9 |
И |
|
|
|
0,03 |
|
4 |
5 |
е |
6 |
8 |
9 |
5.3 Расчет нормы времени
5.3.1 Расчет основного времени
Расчет нормы времени приведен в разделе 1.
После установления режима резания определяют основное время для шлифования методом
56
продольной подачи по формуле:
t |
o |
|
L i |
к |
з |
(5.5) |
|
n Sпр |
|||||||
|
|
|
|
где L— длина обрабатываемой поверхности с учетом врезания и перебега камня, мм; n— числи оборотов детали в минуту;
i — число проходов;
Snp— продольная подача, мм/об;
k3— коэффициент зачистных ходов (принимают в пределах 1,2—1,7 в зависимости от требований к чистоте обработки; большее значение — для более высокого класса чистоты).
Длину обрабатываемой поверхности рассчитывают по формуле (2.6), величину врезания и перебега выбирают из таблицы 5.6,
Таблица. 5.6. Величина врезания и перебега при круглом шлифовании
Условия работы |
Величина врезания и перебега (у1+у2), |
|
мм |
Выход круга в обе стороны |
Вк +5 |
Выход круга в одну сторону |
3 |
Без выхода круга |
- Вк |
Основное время для круглого наружного шлифования с поперечной подачей круга определяется по формуле
t |
o |
|
a |
к |
(5.6) |
|
|||||
|
|
n Sпоп |
|
где Sпоп — поперечная подача на один оборот детали (глубина резания) в мм; а — припуск на сторону в мм;
n — частота вращения детали, мин-1.
5.3.2 Выбор вспомогательного, дополнительного и подготовительно-заключительного времени
Вспомогательное время на установку и снятие детали для условий ремонтных мастерских общего назначения (единичное и мелкосерийное производство) выбирают из таблицы 5.7, вспомогательное время, связанное с проходом, из таблицы 5.8.
Таблица 5.7. Вспомогательное время на установку и снятие детали (для мастерских общего назначения), мин
Способ |
|
|
Вес детали не более . кг |
|
|
||||
установки |
|
|
|
|
|
|
|
|
|
|
|
|
|
|
|
|
|
||
и крепления |
1 |
3 |
6 |
10 |
18 |
30 |
50 |
80 |
|
детали |
|
|
|
|
|
|
|
|
|
В центрах |
0.2 |
0,4 |
0,5 |
0,6 |
1,0 |
2,2 |
2,8 |
3,2 |
|
В трех |
0,4 |
0,6 |
0,8 |
1.0 |
1,6 |
2.5 |
3,2 |
4,0 |
|
кулачковом |
|||||||||
патроне |
|
|
|
|
|
|
|
|
|
В |
|
|
|
|
|
|
|
|
|
четырехкулач- |
0,6 |
1.0 |
1.4 |
2.0 |
2,6 |
4,0 |
5.0 |
6,0 |
|
ковом патроне |
|
|
|
|
|
|
|
|
|
В центрах |
0,5 |
0,7 |
0.8 |
0,9 |
1.2 |
2,4 |
3.0 |
3,6 |
|
с люнетом |
|||||||||
|
|
|
|
|
|
|
|
||
В центрах |
1.4 |
1,5 |
2,0 |
3,0 |
|
— |
- |
— |
|
на оправке |
|
||||||||
|
|
|
|
|
|
|
|
Для специализированных ремонтных предприятий и заводов вспомогательное время устанавливают по таблицам 5.9 и 5.10.
Дополнительное время рассчитывают по формуле 2.7
57
Подготовительно-заключительное время определяют по таблице 5.11 для мастерских общего назначения и по таблице 5.12 для специализированных ремонтных предприятий и заводов.
Таблица 5.8. Вспомогательное время, связанное с проходом (для мастерских общего назначений)
Наименование прохода |
Высота центров не более, мм |
|
|
200 |
300 |
|
время на один проход, мин |
|
Шлифование первой поверхности на одной детали |
1,00 |
1,20 |
Шлифование последующих поверхностей на одной |
|
|
детали |
0,55 |
0,70 |
На каждый последующий проход |
0,04 |
0,05 |
Tаблица 5.9. Вспомогательное время на установку и снятие детали (для специализированных ремонтных предприятий и заводов), мин
Способ установки |
Вес детали не более, кг |
|
|
|
|
||||
в крепления детали |
|
|
|
|
|
|
|
|
|
|
|
|
|
|
|
|
|
|
|
|
|
1 |
3 |
5 |
8 |
12 |
20 |
50 |
80 |
В центрах |
0,25 |
0,28 |
0,32 |
0,36 |
0,44 |
0,55 |
2,5 |
2,9 |
|
В центрах с люнетом |
— |
— |
- |
0,60 |
0.70 |
0,80 |
3,2 |
3,8 |
|
В трехкулачковом |
0,28 |
0,32 |
0,38 |
0,42 |
0,43 |
0,62 |
2,9 |
3,1 |
|
патроне |
|
|
|
|
|
|
|
|
|
В трехкулачковом |
- |
0,65 |
0,72 |
0,80 |
0,90 |
1,00 |
3,0 |
3,0 |
|
патроне с люнетом |
|
|
|
|
|
|
|
|
|
|
|
|
|
|
|
|
|
|
|
В |
четирсхкулачковом |
0,36 |
0,48 |
0,56 |
0, 68 |
0,71 |
0,90 |
1,35 |
2,0 |
патроне |
|
|
|
|
|
|
|
|
|
В |
четьрехкулачковом |
0,62 |
0,68 |
0,75 |
0,82 |
1,00 |
1,15 |
3,4 |
4,0 |
патроне люнетом |
|
|
|
|
|
|
|
|
|
|
|
|
|
|
|
|
|
|
|
Таблица 5.8. Вспомогательное время, связанное с проходом (для специализированных ремонтных предприятий и заводов)
Наименование прохода |
Высота центров не более, мм |
|
|
150 |
300 |
|
время на один проход, мин |
|
Шлифование первой поверхности на одной детали |
0,90 |
1,10 |
Шлифование последующих поверхностей на |
0,45 |
0,60 |
одной детали |
|
|
На каждый последующий проход |
0,03 |
0,04 |
Таблица 5.11. Подготовительно-заключительное время (для мастерских общего назначения), мин
Способ установки детали |
Высота центров не более, мм |
|
|
150 |
300 |
В центрах |
5 |
6 |
В трехкулачковом патроне |
8 |
9 |
Установка люнета |
4 |
5 |
Смена круга |
8 |
9 |
Замена одного кулачка |
2 |
3 |
Таблица 5.12. Подготовительно-заключительное время (для специализированных ремонтных предприятий и заводов), мин
Способ установки детали |
Высота |
центров не |
|
|
более, мм |
|
|
|
150 |
|
300 |
В центрах |
7 |
|
8 |
В самоцентрирующем патроне |
10 |
|
11 |
В самоцентрирующем патроне с люнетом |
12 |
|
14 |
В четырехкулачковом патроне |
13 |
|
15 |
В четырехкулачковом патроне с люнетом |
14 |
|
16 |
На основании полученных данных по всем операциям заполняется операционно-технологическая
карта.
Графическая часть курсовой работы оформляется на листе формата А1 с помощью компьютерной техники или карандашом с соблюдением требований ЕСКД (см. приложение 3).
В верхней части листа дается чертеж детали со всеми сечениями разрезами, размерами и указанной шероховатостью обработки. В случае разработки технологии обработки таких деталей, как зубчатое колесо, вал-шестерня, червяк и т.п. необходимо приводить их техническую характеристику в отдельной таблице. Пример заполнения технологической карты см. приложение 3.
58
ЛИТЕРАТУРА
1Справочник технолога-машиностроителя / Под ред. А.Г. Косиловой, Р.К. Мещерякова. Т. 1. М.: Машиностроение, 1985. 665 с.
2Справочник технолога-машиностроителя / Под ред. А.Г. Косиловой, Р.К. Мещерякова. Т. 2. М.:Машиностроение, 1985. 496 с.
3Горбацевич А.Ф., Шкред В.А. Курсовое проектирование по технологии машиностроения. М.:Высшая школа, 1983. 225 с.
4Никифоров А.Д., Беленький В.А., Поплавский Ю.В. Типовые технологические процессы изготовления аппаратов химических производств. М.: Машиностроение, 1979. 278 с.
5Станочные приспособления: Справочник / Под ред. Б.Н. Вардашкина, А.А. Шатилова. Т. 1. М.: Машиностроение, 1984. 591 с.
6Станочные приспособления: Справочник / Под ред. Б.Н. Вардашкина, А.А. Данилевского. Т. 2. М.: Машиностроение, 1984. 655 с.
7Обработка металлов резанием: Справочник технолога / Под ред. А.А. Панова. М.: Машиностроение, 1988. 736 с.
8Маракулин И.В. и др. Краткий справочник технолога тяжелого машиностроения. М.: Машиностроение, 1987. 464 с.
9Худобин Л.В. и др. Курсовое проектирование по технологии машиностроения. М.: Машиностроение, 1989. 288 с.
10Технико-экономическое обоснование конструкторского решения: Метод. указ. / Сост.: В.В. Быковский, А.И. Попов. Тамбов: Изд-во Тамб. гос. техн. ун-та, 2000. 24 с.
11Ткачев А.Г., Шубин И.Н. Типовые технологические процессы изготовления деталей машин. Тамбов: Изд-во Тамб. гос. техн. ун-та, 2004. 112 с.
12.В.А. Матвеев, И.И. Пустовалов Техническое нормирование ремонтных робот в сельском хозяйстве.-М.: Колос,1979.-288с.,ил.
59
ПРИЛОЖЕНИЯ
60