
2
.pdfПодача — величина перемещения сверла вдоль оси за один его оборот (или за один оборот детали при сверлении на токарном станке) в мм/об.
Величина подачи при сверлении зависит от заданной чистоты и точности обработки, обрабатываемого материала, прочности сверла и жесткости системы «станок — инструмент — деталь».
Скорость резания при сверлении представляет собой окружную скорость сверла относительно заготовки (детали).
Величина скорости резания зависит от обрабатываемого материала, диаметра и материала сверла, подачи, глубины сверления и охлаждения.
Рекомендуемые технологически допустимые величины подач приведены в таблицах 3.1 (для сверления), 3.2 (для рассверливания), 3.3 (для зенкерования) и 3.4 (для развертывания). Подачи выбирают по обрабатываемому материалу и диаметр режущего инструмента.
Таблица 3.1. Подачи при сверлении спиральными сверлами, мм/об.
|
Диаметр |
|
|
Обрабатываемый материал |
|
||
|
|
сталь σв не |
сталь |
сталь σв |
чугун НВ |
|
|
|
сверла не |
|
чугун НВ |
||||
|
|
более |
σв=910-1100 |
более |
не более |
||
|
более, мм |
|
свыше 170 |
||||
|
|
900 МПа |
МПа |
1100 МПа |
170, бронза |
||
|
|
|
|
||||
|
|
|
|
|
|
|
|
6 |
|
0,15 |
0.11 |
0,09 |
0,38 |
0,22 |
|
8 |
|
0,18 |
0,14 |
0,11 |
0,45 |
0,27 |
|
10 |
|
0,22 |
0,16 |
0,13 |
0,50 |
0,30 |
|
12 |
|
0,26 |
0,19 |
0,16 |
0,50 |
0,30 |
|
14 |
|
0,22 |
0,16 |
0.13 |
0,40 |
0,24 |
|
16 |
|
0,19 |
0,14 |
0,11 |
0,35 |
0,21 |
|
18 |
|
0,15 |
0,11 |
0,09 |
0,30 |
0,18 |
|
20 |
|
0.14 |
0,10 |
0,08 |
0,25 |
0,15 |
|
22 |
|
0,13 |
0,09 |
0,08 |
0.23 |
0,14 |
|
24 |
|
0,11 |
0,08 |
0,07 |
0,21 |
0,12 |
|
26 |
|
0,10 |
0,07 |
0,06 |
0.19 |
0,11 |
|
28 |
|
0,09 |
0,07 |
0,06 |
0,17 |
0,10 |
|
30 |
|
0,08 |
0,06 |
0,05 |
0,16 |
0,10 |
|
35 |
|
0,07 |
0,05 |
0,04 |
0.14 |
0,09 |
|
40 |
|
0.06 |
0,04 |
0,03 |
0,12 |
0,07 |
Таблица 3.2. Подачи при рассверливании спиральными сверлами мм /об
Диаметр |
|
Диаметр |
Обрабатываемый материал |
|
|
||
сверла |
не |
рассверли |
сталь σв |
сталь |
|
чугун НВ |
|
более, мм |
|
ваемоего |
не |
σв=91 - |
сталь σв |
не более |
чугун НВ |
|
|
отверстия |
более |
1100 |
более |
170, |
свыше 170 |
|
|
не более, |
1100 МПа |
||||
|
|
900 МПа |
МПа |
бронза |
|
||
|
|
мм |
|
|
|
|
|
25 |
|
10 |
0,40 |
0,30 |
0,25 |
0,70 |
0,60 |
|
|
15 |
0,40 |
0.30 |
0,25 |
0,70 |
0.60 |
|
|
10 |
0,45 |
0,30 |
6,28 |
0,90 |
0.60 |
30 |
|
15 |
0,45 |
0,40 |
0,30 |
0,90 |
0.60 |
|
|
20 |
0,45 |
0,10 |
0,30 |
0,90 |
0.70 |
40 |
|
15 |
0,30 |
0,20 |
0,I6 |
1,00 |
0,80 |
|
|
20 |
0,50 |
0,30 |
0.25 |
1,00 |
0,80 |
|
|
30 |
|
0.45 |
0,38 |
1,00 |
0,80 |
|
|
20 |
0.20 |
0,15 |
0.I2 |
0,65 |
0,40 |
50 |
|
30 |
0,45 |
0,25 |
0.20 |
1,20 |
0,80 |
|
|
40 |
0.65 |
0,50 |
0.45 |
1.20 |
0.80 |
Таблица 3.3. Подачи при зенкеровании, мм/об
Диаметр |
|
Обрабатываемый материал |
|
|
|
зенкера |
не |
|
|
|
|
более, мм |
|
сталь σв до |
сталь σв более |
чугун НВ до |
чугун НВ |
|
|
1100 МПа |
1100 МПа |
200, бронза |
свыше 200 |
15 |
|
0,5 |
0,4 |
0,7 |
0,5 |
20 |
|
0,6 |
0,46 |
0,9 |
0,6 |
25 |
|
0,7 |
0,5 |
1,0 |
0,7 |
30 |
|
0,8 |
0,6 |
1,1 |
0,8 |
35 |
|
0,9 |
0,6 |
1,2 |
0,9 |
40 |
|
0,9 |
0,7 |
1,4 |
1.0 |
50 |
|
1,0 |
0,8 |
1,6 |
1,2 |
31
Таблица 3.4. Подачи при развертывании, мм/oб
Диаметр |
Обрабатываемый материал |
|
|
|
отверстия |
сталь σв до |
сталь σв более |
чугун. НВ |
чугун НВ |
не более, мм |
800 МПа |
800 МПа |
не более 200, |
свыше 200 |
|
|
|
бронза |
|
5 |
0,4 |
0,3 |
0,9 |
0,6 |
10 |
0,65 |
0,5 |
1,7 |
1,4 |
15 |
0,9 |
0,8 |
1.9 |
1,6 |
20 |
1,1 |
0,9 |
2,0 |
1,7 |
25 |
1,2 |
1,0 |
2,2 |
1,9 |
30 |
1,4 |
1,1 |
2,4 |
2,0 |
40 |
1,6 |
1,3 |
2,6 |
2,2 |
50 |
1,9 |
1,5 |
2,7 |
2,6 |
60 |
2,1 |
1,7 |
2,9 |
2,8 |
80 |
2,4 |
1,9 |
3,4 |
3,2 |
Скорости резания при сверлении в сплошном материале определяют по диаметру сверла и принятой подаче (табл. 3.5), скорости резания при рассверливании — по диаметру сверла, диаметру рассверливаемого отверстия и принятой подаче табл. 3.6.
Таблица 3.5. Скорость резания (м/мин) и частота вращения (мин-1) при сверлении углеродистой конструционной стали σв = 650 МПа
Диаметр |
|
|
|
|
Подача S не более мм/об |
|
|
|
|
|||
сверла |
|
|
|
|
|
|
|
|
||||
|
|
|
|
|
|
|
|
|
|
|
||
не |
|
|
|
|
|
|
|
|
|
|
|
|
более, |
0,05 |
0,07 |
0,08 |
0,09 |
0,10 |
0,12 |
0,15 |
0,18 |
0,20 |
0,25 |
0,30 |
|
мм |
|
|
|
|
|
|
|
|
|
|
|
|
5 |
50/ |
39/ |
36/ |
33/ |
31/ |
28/ |
23/ |
20/ |
19/ |
- |
- |
|
3154 |
2501 |
2266 |
2090 |
1940 |
1708 |
1454 |
1285 |
1200 |
||||
|
|
|
||||||||||
8 |
- |
|
39/ |
36/ |
33/ |
29/ |
25/ |
22/ |
21/ |
19/ |
17/ |
|
|
1540 |
1430 |
1320 |
1165 |
990 |
878 |
815 |
764 |
664 |
|||
|
|
|
||||||||||
10 |
- |
|
42/ |
39/ |
36/ |
32/ |
27/ |
24/ |
22/ |
20/ |
18/ |
|
|
1350 |
1248 |
1154 |
1016 |
865 |
767 |
712 |
637 |
582 |
|||
|
|
|
||||||||||
12 |
- |
|
|
|
39/ |
34/ |
29/ |
26/ |
24/ |
22/ |
20/ |
|
|
|
|
1035 |
910 |
775 |
688 |
638 |
575 |
523 |
|||
|
|
|
|
|
||||||||
16 |
- |
|
|
|
|
37/ |
32/ |
28/ |
26/ |
23/ |
21/ |
|
|
|
|
|
740 |
628 |
558 |
518 |
464 |
424 |
|||
|
|
|
|
|
|
|||||||
20 |
- |
|
|
|
|
37/ |
32/ |
28/ |
26/ |
23/ |
21/ |
|
|
|
|
|
596 |
506 |
450 |
418 |
374 |
342 |
|||
|
|
|
|
|
|
|||||||
24 |
- |
|
|
|
|
40/ |
34/ |
30/ |
28/ |
25/ |
23/ |
|
|
|
|
|
535 |
455 |
404 |
375 |
336 |
306 |
|||
|
|
|
|
|
|
|||||||
30 |
- |
|
|
|
|
|
|
30/ |
28/ |
25/ |
23/ |
|
|
|
|
|
|
|
319 |
296 |
268 |
244 |
|||
|
|
|
|
|
|
|
|
Таблица 3.6. Скорость резания (м/мин) и частота вращения (мин-1) при рассверливании углеродистой конструкционной стали σв = 650МПа
Диаметр |
Диаметр |
|
Подача S не более мм/об |
|
||||
сверла не |
рассверливаемоего |
0,2 |
|
0,3 |
0,4 |
0,6 |
|
0,8 |
более, мм |
отверстия, мм |
|
|
|||||
|
|
|
|
|
|
|
||
|
10 |
33/ |
|
28/ |
24/ |
19/ |
|
16/ |
|
425 |
|
349 |
302 |
246 |
|
208 |
|
25 |
|
|
|
|||||
15 |
36/ |
|
29/ |
26/ |
21/ |
|
18/ |
|
|
|
|
||||||
|
356 |
|
276 |
325 |
265 |
|
230 |
|
|
|
|
|
|||||
|
10 |
33/ |
|
27/ |
23/ |
19/ |
|
16/ |
|
350 |
|
284 |
245 |
201 |
|
175 |
|
|
|
|
|
|||||
30 |
15 |
35/ |
|
28/ |
25/ |
20/ |
|
17/ |
370 |
|
300 |
255 |
212 |
|
182 |
||
|
|
|
|
|||||
|
20 |
38/ |
|
31/ |
27/ |
22/ |
|
19/ |
|
400 |
|
380 |
282 |
230 |
|
200 |
|
|
|
|
|
|||||
|
15 |
30/ |
|
25/ |
22/ |
18/ |
|
15/ |
|
244 |
|
197 |
172 |
140 |
|
124 |
|
|
|
|
|
|||||
40 |
20 |
32/ |
|
26/ |
25/ |
19/ |
|
16/ |
255 |
|
207 |
180 |
147 |
|
124 |
||
|
|
|
|
|||||
|
30 |
36/ |
|
29/ |
26/ |
21/ |
|
18/ |
|
290 |
|
238 |
205 |
167 |
|
146 |
|
|
|
|
|
|||||
|
20 |
29/ |
|
23/ |
21/ |
17/ |
|
15/ |
|
187 |
|
152 |
132 |
108 |
|
95 |
|
|
|
|
|
|||||
50 |
30 |
32/ |
|
26/ |
23/ |
18/ |
|
16/ |
204 |
|
166 |
144 |
117 |
|
101 |
||
|
|
|
|
|||||
|
40 |
37/ |
|
30/ |
26/ |
21/ |
|
18/ |
|
234 |
|
192 |
166 |
135 |
|
116 |
|
|
|
|
|
32
Скорость резания при зенкеровании определяют по диаметру зенкера и подаче (табл. 3.7), при развертывании — по диаметру развертки и принятой подаче (табл. 92).
Таблица 3.7. Скорость резания (м/мин) и частота вращения (мин-1) при зенкеровании углеродистой конструкционной стали σв=650 МПа (зенкер из стали Р9; с охлаждением)
Диаметр |
|
|
|
|
Подача S не более мм/об |
|
|
|
|
||||
зенкера, |
|
|
|
|
|
|
|
|
|||||
мм не |
|
|
|
|
|
|
|
|
|
|
|
|
|
более |
|
|
|
|
|
|
|
|
|
|
|
|
|
0,2 |
0,3 |
0,4 |
0,5 |
0,6 |
0,7 |
0,8 |
0,9 |
1,0 |
1,2 |
1,4 |
1,6 |
||
|
|||||||||||||
|
|
|
|
|
|
|
|
|
|
|
|
|
|
15 |
41,6/ |
34/ |
29,4/ |
26,3/ |
24/ |
22,2/ |
- |
- |
- |
- |
- |
- |
|
883 |
721 |
624 |
588 |
510 |
472 |
||||||||
|
|
|
|
|
|
|
|||||||
|
|
|
|
|
|
|
|
|
|
|
|
|
|
20 |
- |
38/ |
32,1/ |
28,7/ |
26,2/ |
24,2/ |
22,7/ |
21,4/ |
20,3/ |
- |
- |
- |
|
604 |
510 |
456 |
417 |
386 |
361 |
340 |
323 |
||||||
|
|
|
|
|
|||||||||
|
|
|
|
|
|
|
|
|
|
|
|
|
|
25 |
- |
29,7/ |
25,7/ |
23,0/ |
21/ |
19,4/ |
18,2/ |
17,1/ |
16,2/ |
14,8/ |
- |
- |
|
378 |
327 |
292 |
267 |
247 |
231 |
218 |
207 |
189 |
|||||
|
|
|
|
||||||||||
|
|
|
|
|
|
|
|
|
|
|
|
|
|
30 |
- |
- |
27,1/ |
24,3/ |
22,1/ |
20,5/ |
19,2/ |
18,1/ |
17,2/ |
15,6/ |
14,5/ |
- |
|
288 |
257 |
235 |
218 |
204 |
192 |
182 |
166 |
154 |
|||||
|
|
|
|
||||||||||
|
|
|
|
|
|
|
|
|
|
|
|
|
|
35 |
- |
- |
25,2/ |
22,5/ |
20,5/ |
19/ |
17,8/ |
16,8/ |
15,9/ |
14,5/ |
13,4/ |
12,6/ |
|
299 |
205 |
187 |
173 |
162 |
153 |
145 |
132 |
122 |
114 |
||||
|
|
|
|||||||||||
|
|
|
|
|
|
|
|
|
|
|
|
|
|
40 |
- |
- |
24,7/ |
22,1/ |
20,2/ |
18,7/ |
17,5/ |
16,5/ |
15,6/ |
14,3/ |
13,2/ |
12,3/ |
|
197 |
176 |
161 |
149 |
139 |
131 |
124 |
114 |
105 |
98 |
||||
|
|
|
|||||||||||
|
|
|
|
|
|
|
|
|
|
|
|
|
|
50 |
- |
- |
- |
19,7/ |
18/ |
16,7/ |
15,6/ |
14,0/ |
12,7/ |
11,8/ |
11/ |
10,1/ |
|
157 |
143 |
133 |
124 |
111 |
101 |
94 |
88 |
82 |
|||||
|
|
|
|
||||||||||
|
|
|
|
|
|
|
|
|
|
|
|
|
Таблица 3.8. Скорость резания (м/мин) и частота вращения (мин-1) при развертывании углеродистой конструкционной стали σв=650 МПа (развертки из стали Р9; с охлаждением)
Подача, |
|
|
Диаметр развертки не более мм/об |
|
|
|
|||||
мм не |
|
|
|
|
|
||||||
|
|
|
|
|
|
|
|
|
|
|
|
более |
5 |
10 |
15 |
20 |
25 |
30 |
40 |
|
50 |
60 |
80 |
|
|
|
|
|
|
|
|
|
|
|
|
0,5 |
24/ |
21,6/ |
17,4/ |
18,2/ |
16,6/ |
- |
- |
|
- |
- |
- |
1528 |
689 |
371 |
290 |
211 |
|
||||||
|
|
|
|
|
|
|
|||||
|
|
|
|
|
|
|
|
|
|
|
|
0,6 |
21,3/ |
19,2/ |
15,3/ |
16,1/ |
14,8/ |
- |
- |
|
- |
- |
- |
1357 |
613 |
326 |
258 |
188 |
|
||||||
|
|
|
|
|
|
|
|||||
|
|
|
|
|
|
|
|
|
|
|
|
0,7 |
19,3/ |
17,4/ |
14,1/ |
14,7/ |
13,4/ |
- |
- |
|
- |
- |
- |
1223 |
553 |
299 |
232 |
170 |
|
||||||
|
|
|
|
|
|
|
|||||
|
|
|
|
|
|
|
|
|
|
|
|
0,8 |
17,6/ |
15,9/ |
12,9/ |
13,5/ |
12,2/ |
12,9/ |
12,1/ |
|
11,7/ |
10,7/ |
9,8/ |
1123 |
614 |
273 |
213 |
156 |
137 |
96 |
|
73 |
56 |
39 |
|
|
|
||||||||||
|
|
|
|
|
|
|
|
|
|
|
|
1,0 |
- |
13,8/ |
11,6/ |
11,6/ |
10,6/ |
11,2/ |
10,4/ |
|
9,9/ |
9,2/ |
8,5/ |
439 |
236 |
184 |
135 |
119 |
81 |
|
63 |
49 |
34 |
||
|
|
|
|||||||||
|
|
|
|
|
|
|
|
|
|
|
|
1,2 |
- |
12,3/ |
9,9/ |
10,3/ |
9,4/ |
9,9/ |
9,1/ |
|
8,8/ |
8,2/ |
7,5/ |
391 |
209 |
164 |
118 |
105 |
73 |
|
56 |
43 |
30 |
||
|
|
|
|||||||||
|
|
|
|
|
|
|
|
|
|
|
|
1,4 |
- |
- |
9,2/ |
9,3/ |
8,5/ |
8,9/ |
8,4/ |
|
8,0/ |
7,4/ |
6,8/ |
195 |
148 |
109 |
95 |
67 |
|
51 |
39 |
27 |
|||
|
|
|
|
||||||||
|
|
|
|
|
|
|
|
|
|
|
|
1,6 |
- |
- |
8,2/ |
8,6/ |
7,8/ |
8,2/ |
7,5/ |
|
7,3/ |
6,8/ |
6,2/ |
173 |
137 |
99 |
87 |
60 |
|
46 |
36 |
25 |
|||
|
|
|
|
||||||||
|
|
|
|
|
|
|
|
|
|
|
|
1,8 |
- |
- |
7,7/ |
7,9/ |
7,2/ |
7,6/ |
7,2/ |
|
6,7/ |
6,3/ |
5,8/ |
162 |
126 |
92 |
81 |
56 |
|
43 |
33 |
23 |
|||
|
|
|
|
||||||||
|
|
|
|
|
|
|
|
|
|
|
|
2,0 |
- |
- |
7,1/ |
7,4/ |
6,7/ |
7,1/ |
6,7/ |
|
6,3/ |
5,9/ |
5,4/ |
150 |
119 |
85 |
75 |
53 |
|
40 |
31 |
22 |
|||
|
|
|
|
||||||||
|
|
|
|
|
|
|
|
|
|
|
|
2,2 |
- |
- |
- |
- |
6,2/ |
6,6/ |
6,2/ |
|
5,9/ |
5,5/ |
5,1/ |
79 |
69 |
49 |
|
38 |
29 |
20 |
|||||
|
|
|
|
|
|
||||||
|
|
|
|
|
|
|
|
|
|
|
|
2,5 |
- |
- |
- |
- |
5,9/ |
6,2/ |
5,7/ |
|
5,4/ |
5,1/ |
4,7/ |
76 |
66 |
45 |
|
35 |
27 |
19 |
|||||
|
|
|
|
|
|
||||||
|
|
|
|
|
|
|
|
|
|
|
|
3,0 |
- |
- |
- |
- |
- |
5,4/ |
5,1/ |
|
4,8/ |
4,5/ |
4,1/ |
57 |
41 |
|
31 |
24 |
17 |
||||||
|
|
|
|
|
|
|
|||||
|
|
|
|
|
|
|
|
|
|
|
|
3,5 |
- |
- |
- |
- |
- |
5,1/ |
4,7/ |
|
4,4/ |
4,1/ |
3,8/ |
54 |
37 |
|
28 |
22 |
15 |
||||||
|
|
|
|
|
|
|
|||||
|
|
|
|
|
|
|
|
|
|
|
|
4,0 |
- |
- |
- |
- |
- |
4,6/ |
4,2/ |
|
4,0/ |
3,7/ |
3,4/ |
49 |
33 |
|
26 |
20 |
14 |
||||||
|
|
|
|
|
|
|
|||||
|
|
|
|
|
|
|
|
|
|
|
|
33
В указанных таблицах приводятся и значения чисел оборотов сверла, соответствующие выбранным скоростям резания.
Скорости резания и числа оборотов, указанные в таблицах 3.5, 3.6, 3.7 и 3.8, необходимо умножать на поправочные коэффициенты в зависимости от условий обработки (при обработке металла других марок и временного сопротивления, при использовании режущего инструмента другой марки, при охлаждении).
Значения поправочных коэффициентов приведены в таблицах 3.9, 3.10, 3.11 и 3.12.
Таблица 3.9. Поправочные коэффициенты на скорость резания (частоту вращения) при сверлении различных марок стали (kM)
Сталь |
Предел прочности сталь σв МПа |
|
|
|||
|
410- |
510- |
610- |
710- |
810- |
910- |
|
500 |
600 |
700 |
800 |
900 |
1000 |
Углеродистая |
0,1 |
1,2 |
1,0 |
0,9 |
0,8 |
- |
конструкционная |
|
|
|
|
|
|
Хромоникилевая |
1,3 |
1,1 |
0,9 |
0,8 |
0,7 |
0,6 |
Углеродистая |
|
|
|
|
|
|
инструментальная |
- |
- |
0,6 |
0,5 |
0,4 |
0,4 |
Таблица 3.10. Поправочные коэффициенты на скорость резания (частоту вращения) при сверлении серого чугуна различной твердости (kм)
|
Твердость НВ |
|
120-140 |
|
141—560 |
161 —180 |
181-200 |
201-260 |
|
|
|
|
|||
|
коэффициент kм |
|
1,0 |
|
|
0,3 |
|
0.7 |
0,6 |
|
0,5 |
|
для серого |
чугуна даны |
в отношении |
|
Примечание: |
Поправочные |
коэффициенты kм |
||||||||||||
|
углеродистой конструкционной стили σв=650 МПа. |
|
|
|
|||||||||||
|
Таблиц 3.11 |
Поправочные коэффициенты |
на скорость |
резания ори |
сверлении в |
зависимости от |
|||||||||
|
материала инструмента kмр |
|
|
|
|
|
|
|
|
|
|||||
|
Марка стали инструмента |
|
Коэффициент kмр |
|
|
|
|
|
|
|
|||||
|
|
|
|
|
|
|
|
|
|
|
|
|
|
|
|
|
У10 У12 |
|
|
|
0,5 |
|
|
|
|
|
|
|
|
|
|
|
9ХС |
|
|
|
0,6 |
|
|
|
|
|
|
|
|
|
|
|
Таблица 3.12 Поправочные коэффициенты на скорость резания при сверлении в зависимости |
||||||||||||||
|
от применения охлаждения kох |
|
|
|
|
|
|
|
|||||||
|
|
|
|
|
|
|
|
|
|
|
|
|
|||
|
Материал |
Обработка |
|
|
Коэффициент |
|
|
|
|
|
|
|
|||
|
|
|
|
|
|
|
kОХ |
|
|
|
|
|
|
|
|
|
Сталь |
Без охлаждения |
1,00 |
|
|
|
|
|
|
|
|
||||
|
С охлаждением |
1,25 |
|
|
|
|
|
|
|
|
|||||
|
|
|
|
|
|
|
|
|
|
||||||
|
Чугун |
|
|
|
|
|
|
|
|
|
|||||
|
Охлаждение не применяется |
|
|
|
|
|
|
|
Необходимо помнить, что при обработке отверстий различают нормальную длину обработки (нормальное сверление, нормальное зенкерование и т.д.) и глубокое сверление, глубокое зенкерование и т.д.
Под нормальной длиной обработки понимают длину отверстия, не превышающую трех диаметров. Если длина отверстия больше трех диаметров, условия работы инструмента ухудшаются: увеличивается трение ленточек инструмента о стенки отверстия, затрудняется подвод охлаждающей жидкости к месту резания, что вызывает перегрев инструмента. Поэтому при установлении режима резания (скорости и числа оборотов) вводят поправочные коэффициенты в зависимости от длины отверстия, которые приведены в таблице 3.13.
Поправочные коэффициент на скорость резания зависимости при сверлении в зависимости от глубины отверстия kот
Таблица 3.13
Глубина отверстия в диаметрах сверла |
3D |
4D |
5D |
6D |
7D |
10D |
Коэффициент kот |
1.00 |
0.85 |
0.75 |
0.70 |
0.6 |
0.50 |
34
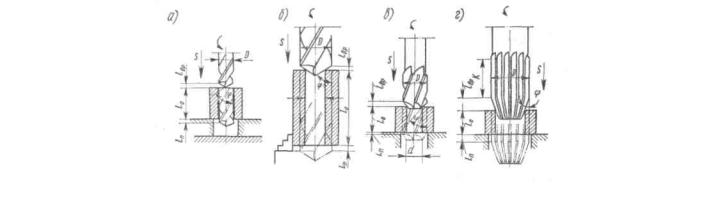
3.3 Расчет норм времени
3.3.1 Расчет основного времени
Расчет нормы времени приведен в разделе 1.
Основное время для обработки отверстий сверлом, зенкером, разверткой, цековкой и подрезным ножом
Основное время для обработки отверстий сверлом, зенкером, разверткой, цековкой и подрезным ножом определяется по формуле
t |
o |
|
L i |
(3.3) |
|
n S |
|||||
|
|
|
При сверлении, зенкеровании и развертывании длина прохода инструмента слагается из длины обрабатываемого отверстия, длины врезания и длины перебега инструмента. Для этих видов работ
формула основного времени может быть выражена следующим образом: |
|
||||
to |
lo lвр lп |
i |
(3.4) |
||
|
|
|
|||
|
|
n S |
|
||
где l0 — длина обрабатываемого отверстия в мм; |
|
||||
lвр — длина врезания в мм; |
|
||||
lп — длина перебега сверла в мм (рис. 3.3, а). |
|
||||
Длина врезания lвр при сверлении определяется по формуле 3.5 или по таблице 3.14 |
|
||||
lвр |
D d |
ctg (1...3) |
(3.5) |
||
|
|||||
2 |
|
|
|
где D — диаметр сверла в мм;
d — длина поперечной режущей кромки сверла в мм; φ— главный угол в плане сверла в град.
Величина врезания и перебега определяется по таблице 3.14 в зависимости от характера работы и диаметра инструмента.
Таблица 3.14 Величина врезания и выхода инструмента, мм
Характер работы |
Диаметр инструмента не более, мм |
|
|
|
||||||||
|
3 |
5 |
1 0 |
15 |
20 |
25 |
30 |
40 |
50 |
60 |
70 |
80 |
Сверление на проход |
2 |
2,5 |
5 |
7 |
8 |
10 |
12 |
15 |
18 |
23 |
- |
- |
Сверление в упор |
1,5 |
2 |
4 |
6 |
7 |
9 |
11 |
14 |
17 |
21 |
- |
- |
Рассверливание |
- |
- |
- |
- |
4,8 |
6 |
7,2 |
9 |
11 |
14 |
17 |
20 |
Зенкерование |
- |
- |
- |
3 |
4 |
5 |
5 |
6 |
6 |
8 |
8 |
8 |
Развертывание на проход |
- |
15 |
18 |
22 |
26 |
30 |
33 |
38 |
45 |
50 |
50 |
50 |
Развертывание в упор |
- |
2 |
2 |
2 |
2 |
3 |
3 |
4 |
4 |
5 |
5 |
5 |
Рис. 3.3. Схемы для определения длины прохода инструментов при обработке отверстий
35
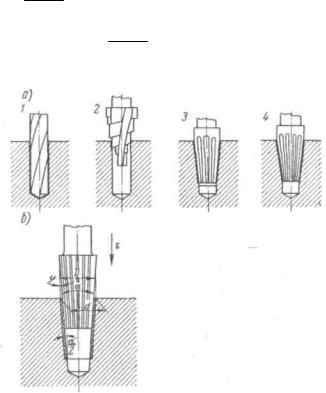
Длина врезания lвр |
при рассверливании, зенкеровании и развертывании (рис. 3.3, б, в, г) |
определяется по формуле |
|
lвр t ctg (1...3) |
(3.6) |
где t — глубина резания в мм;
φ — главный угол инструмента в плане в град.
Длина перебега инструмента lп при обработке на проход принимается равной 1...3 мм; при развертывании
lп (0,2...0,5) К , мм (рис 3.3, г), |
(3.7) |
где К — длина калибрующей части развертки. При обработке глухих отверстий lп =0.
Для точных конических отверстий применяется комплект из конических зенкеров и разверток. На рис. 3.4, а показан порядок обработки таких конических отверстий. При диаметрах больше 25
мм отверстие рекомендуется сверлить последовательно несколькими сверлами различного диаметра для образования ступенчатого отверстия, приближающегося к форме конического зенкера. После сверления 1 (рис. 3.4, а) поочередно применяются зенкер 2, черновая развертка 3 и чистовая развертка 4.
При зенкеровании и развертывании конических отверстий (рис. 3.4, б) основное время определяется по формуле
t0 |
|
l (0.5...2) |
(3.8) |
|
n s |
||||
|
|
|
где
l D d ctg
2
соответственно D d t глубина резания; 2
φ— главный угол в плане, равный половине угла при вершине конуса инструмента: α/2
Рис. 3.4. Схема обработки конического отверстия
36
3.3.2 Выбор вспомогательного, дополнительного и подготовительно-заключительного времени
Вспомогательное время определяют по следующим таблицам. В таблицах 3.15 и 3.16 соответственно приведены значения вспомогательного времени на установку и снятие, детали и связанного с проходом для условия мастерских общего назначении (мелкосерийное и единичное производство), в таблицах 3.17 и 3.18 — для условий специализированных ремонтных предприятий и заводов (серийное производство)
Таблица 3.15. Вспомогательное время на установку и снятие детали, мин (для мастерских общего назначения)
Способ установки деталей |
|
Вес детали не более, кг |
|
|
|
|
|
|
|||||||
|
|
1 |
|
3 |
5 |
|
10 |
|
18 |
30 |
50 |
|
80 |
|
|
В трехкулачковом патроне |
|
0,2 |
|
0,22 |
0,24 |
0,8 |
|
- |
- |
|
- |
|
- |
|
|
В тисках |
|
0,4 |
|
0,60 |
0,70 |
0,2 |
|
1,2 |
- |
|
- |
|
- |
|
|
На столе без крепления |
|
- |
|
0,15 |
0,18 |
1,2 |
|
0,5 |
0,5 |
2,3 |
|
2,8 |
|
||
Сбоку на угольнике |
|
- |
|
- |
1,10 |
1,2 |
|
1,7 |
2,2 |
3,8 |
|
4,5 |
|
||
Сбоку с креплением к столу |
|
- |
|
- |
1,00 |
|
|
1,6 |
2,0 |
3,6 |
|
4,3 |
|
||
Таблица 3.16. |
Вспомогательное время, |
связанное с проходом, мин (для мастерских общего |
|||||||||||||
назначения) |
|
|
|
|
|
|
|
|
|
|
|
|
|
|
|
|
|
|
|
|
|
|
|
На каждое |
|
|
|
|
|||
|
|
|
|
|
|
|
|
последующее |
|
|
|||||
|
|
|
|
|
|
|
|
отверстие |
|
|
|
|
|||
|
На первое отверстие |
того же диаметра |
|
|
|||||||||||
Условия работы |
|
|
|
|
|
|
|
при сверлении |
|
|
|||||
|
|
|
|
|
|
|
в одной или |
|
|
|
|
||||
|
|
|
|
|
|
|
|
|
|
|
|
||||
|
|
|
|
|
|
|
|
нескольких деталях |
|
||||||
|
|
для станков с наибольшим диаметром |
|
||||||||||||
|
|
|
|
|
|
сверления, мм |
|
|
|
|
|||||
|
12 |
|
25 |
|
50 |
12 |
|
25 |
|
50 |
|
||||
Сверление по разметке |
0,16 |
|
0,21 |
|
0,24 |
0,08 |
|
0,10 |
|
0,12 |
|
||||
Сверление по кондуктору |
0,14 |
|
0,18 |
|
0,20 |
0,07 |
|
0,09 |
|
0,10 |
|
||||
Рассверливание и зенкерование |
0,12 |
|
0,15 |
|
0,18 |
0,06 |
|
0,07 |
|
0,08 |
|
||||
Развертывание |
0,14 |
|
0,18 |
|
0,20 |
0,07 |
|
0,09 |
|
0,10 |
|
Дополнительное время рассчитывают по формуле 2.7 Подготовительно-заключительное время находим по таблицам 3.19 (для условий мастерских
общего назначения) и 3.20 (для специализированных ремонтных предприятий и заводов).
Таблица 3.17 Вспомогательное время на установку и снятие детали, мин (для специализированных ремонтных предприятий и заводов)
Способ установки детали |
Вес детали не более, кг |
|
|
|
|
|
|
|
||||||
|
|
|
|
3 |
5 |
8 |
12 |
20 |
50 |
80 |
120 |
200 |
300 |
500 |
В |
тисках |
с |
винтовым |
0,50 |
0,6 |
0,7 |
0,8 |
0,9 |
— |
— |
— |
— |
— |
— |
зажимом |
|
|
|
|
|
|
|
|
|
|
|
|
|
|
В |
тисках |
с |
0,4 |
0,5 |
0,6 |
0,7 |
0,8 |
— |
— |
— |
— |
— |
— |
|
пневматическим зажимом |
|
|
|
|
|
|
|
|
|
|
|
|||
На столе без крепления |
0,12 |
0,14 |
0,15 |
0,17 |
0,2 |
1,3 |
1,4 |
1,6 |
1,8 |
2,0 |
2,4 |
|||
На |
столе с |
креплением |
0,95 |
1,0 |
1,2 |
1,4- |
1,6 |
3,0 |
3,3 |
3,6 |
4,0 |
4,4 |
4,9 |
|
болтами и .планками |
|
|
|
|
|
|
|
|
|
|
|
|||
Сбоку стола с креплением |
1,1 |
1.3 |
1,5 |
1,8. |
2,1 |
3,5 |
— |
—. |
— |
—. |
— |
|||
болтами и планками |
|
|
|
|
|
|
|
|
|
|
|
|||
В |
самоцентрирующем |
0,18 |
0,2 |
0,24 |
0,28 |
0,39 |
— |
— |
—. |
— |
—. |
— |
||
патроне |
|
|
|
|
|
|
|
|
|
|
|
|
|
|
В кондукторе |
|
|
0,8 |
0,9 |
1,0 |
1.1 |
1,3 |
2,2 |
— |
|
— |
— |
— |
Примечание. Затраты времени для деталей весом более 20кг даны на установку с применением подъемно-транспортных приспособлений.
37
Таблица 3.18. Вспомогательное время, связанное с проходом (для специализированных ремонтных предприятии и заводов),
|
|
|
|
На каждое последующее |
|||||
|
|
|
|
|
|
отверстие |
|
||
|
На первое отверстие |
|
того же диаметра |
||||||
|
|
при сверлении |
|||||||
|
|
|
|
|
|||||
Условия работы |
|
|
|
|
в одной или |
|
|||
|
|
|
|
нескольких деталях |
|||||
|
|
|
|
|
|||||
|
|
|
|
|
|
|
|
||
|
для станков с наибольшим диаметром |
||||||||
|
|
|
сверления, мм |
|
|
|
|
||
|
|
время, мин на один проход |
|
||||||
|
12 |
25 |
50 |
|
12 |
|
25 |
|
50 |
Сверление по разметке |
0,12 |
0,14 |
0,16 |
|
0,05 |
|
0,06 |
|
0,07 |
Сверление по кондуктору |
0,10 |
0,12 |
0,13 |
|
0,04 |
|
0,05 |
|
0,06 |
Рассверливание и зенкерование |
0,08 |
0,10 |
0,12 |
|
0,03 |
|
0,04 |
|
0,05 |
Развертывание |
0,10 |
0,12 |
0,15 |
|
0,04 |
|
0,05 |
|
0,07 |
Таблица 3.19. Подготовительно-заключительное время (для мастерских общего назначения)
Способ установки детали |
Время, мин |
В трехкулачковом патроне |
4 |
В тисках |
б |
В приспособлении с креплением к столу |
8 |
На столе без крепления |
2 |
На столе с креплением |
4 |
Таблица 3.20. Подготовительно-заключительное время (для специализированных ремонтных предприятий и заводов), мин
Способ установки детали |
|
Наибольший диаметр |
||
просверливаемого отверстия, мм |
||||
|
12 |
|
25—50 |
50-75 |
На столе без крепления |
3 |
|
4 |
5 |
На столе с креплением болтами и планками |
|
|||
4 |
|
5 |
6 |
|
В тисках |
|
|||
5 |
|
6 |
7 |
|
В самоцеитрирующем патроне |
|
|||
|
|
8 |
9 |
|
В кондукторе |
|
|
||
- |
|
9 |
10 |
|
Сбоку стола с креплекием болтами и |
|
|||
- |
|
13 |
20 |
|
планками |
|
|||
|
|
|
|
38

4 РАСЧЕТ РЕЖИМОВ РЕЗАНИЯ И НОРМЫ ВРЕМЕНИ ПРИ ФРЕЗЕРНЫХ РАБОТАХ
4.1 Общие сведения
В ремонтных предприятиях фрезерные работы выполняют на горизонтально-, вертикально- и универсально-фрезерных станках, основные характеристики которых приведены в приложении 1.
Фрезерование представляет собой весьма распространенный и высокопроизводительный метод обработки металлов резанием при помощи инструмента, называемого фрезой.
Фреза является режущим инструментом с несколькими зубьями, каждый из которых представляет собой простейший резец.
Наиболее широкое применение в ремонтных предприятиях получили следующие типы фрез: цилиндрические и торцовые — для обработки плоскостей; дисковые и отрезные - для фрезерования пазов, уступов и разрезки металлов.
Главным движением при фрезеровании является вращение фрезы, движением подачи - поступательное перемещение заготовки (детали) относительно фрезы.
Фрезерование подчиняется тем же законам резания, что и токарная обработка. Однако при фрезеровании имеются свои некоторые особенности. При фрезеровании на зуб фрезы действуют переменные ударные нагрузки. Ударная нагрузка приводит к снижению стойкости зуба, а иногда и к его разрушению.
4.2 Выбор режима резания
Основными элементами режима резания при фрезеравании являются: ширина фрезерования, глубина резания, подача и скорости резания.
Шириной фрезерования (рис. 4.1) называют ширину обрабатываемой поверхности, выраженную в миллиметрах.
Глубина резания при фрезеровании представляет собой толщину слоя металла, снимаемого с обрабатываемой детали за один проход фрезы. Глубину резания выбирают в зависимости от припуска на обработку и требуемой чистоты поверхности. При черновом фрезеровании весь припуск рекомендуется снимать за один проход (глубина резания t=3...8мм), если это допускается мощностью станка. При чистовом фрезеровании глубина резания принимается в пределах 0,5...1,5 мм.
При глубине резания свыше 3 мм рекомендуется применять фрезы с крупными зубьями, при меньшей глубине — фрезы с мелкими зубьями. При фрезеровании грубых отливок, поковок и наваренных мест, поверхность которых имеет твердую корку или окалину, глубина резания должна быть не менее 2 мм, так как зубья фрезы, работая по корке, быстро притупляются и выкрашиваются.
Подачей при фрезеровании называется перемещение обрабатываемой детали относительно фрезы, вращающейся вокруг своей оси.
При фрезеровании различают подачу на один зуб фрезы S, в мм/зуб, подачу на один оборот фрезы So6 в мм/об и минутную подачу SM в мм/мин.
Зависимость между этими подачами выражается следующими формулами:
Рис. 4.1. Ширина фрезерования. |
|
Sоб Sz z |
(4.1) |
Sм Sоб n |
(4.2) |
где t — число зубьев фрезы; |
|
n — частота вращения фрезы мин-1. |
|
|
39 |
Величина подачи существенно сказывается на производительности процесса фрезерования. Для обдирочных проходов следует выбирать подачи максимальной величины. При выборе подачи для чистового фрезерования необходимо учитывать требования к чистоте поверхности, конструкции, фрезы и жесткости системы «станок-деталь-инструмент».
При фрезеровании нежестких деталей, имеющих малые опорные поверхности, тонкие стенки и не обеспечивающих прочность закрепления, табличная величина подачи должна быть уменьшена в
1,5—2 раза.
Скоростью резания при фрезеровании считается окружная скорость фрезы, измеренная по ее наибольшему диаметру. Скорость резания при фрезеровании зависит от обрабатываемого материала, материала режущей части, диаметра фрезы, подачи, глубины резания, числа зубьев и других факторов.
4.2.1 Фрезерование плоскостей
Фрезерование плоскостей обычно проводят цилиндрическими и торцовыми фрезами.
Ширину фрезерования, как правило, устанавливают по условиям на обработку. Ширину фрезы выбирают несколько больше ширины фрезеруемой поверхности.
Глубину резания определяют, исходя из припуска на обработку и требований к чистоте обработки.
Подачу на оборот фрезы устанавливают по соответствующим таблицам. При обработке цилиндрическими фрезами подачу определяют по таблице 4.1 в зависимости от вида обработки, принятой глубины резания, диаметра и количества зубьев фрезы.
При обработке торцовыми фрезами подачу устанавливают по таблице 4.2 в зависимости от обрабатываемого материала, вида обработки, принятой глубины резания, диаметра и количества зубьев фрезы.
Скорость резания при обработке плоскостей цилиндрическими фрезами определяют по таблице 4.3 в зависимости от принятой глубины резания, подачи, диаметра, количества зубьев и ширины фрезы.
Скорость резания при обработке плоскостей торцовыми фрезами берут из таблицы 4.5 в зависимости от принятой глубины резания, подачи, диаметра и количества зубьев фрезы. В указанных таблицах приведены также и значения чисел оборотов.
Как видно из таблиц 4.3 и 4.5 скорость резания и частота вращения даны из условий обработки углеродистой конструкционной стали, которой соответствует временное сопротивление σв=650МПа. Поэтому взятые из таблиц скорости резании и числа оборотов должны быть откорректированы, если условия обработки отличаются от условий, предусмотренных таблицами. Корректирование заключается в умножении табличной скорости и числа оборотов на соответствующие коэффициенты, значения которых приведены в таблицах 4.4, 4.6, 4.7 и 4.8.
Таблица 4.1. Подачи ирн обработке плоскостей цилиндрическими фрезами, мм/об
Диаметр |
Количество |
Черновая обработка |
Получистовая обработка |
||||
|
глубина резания t не более, мм |
|
|||||
фрезы, мм |
зубьев фрезы |
|
|
||||
3 |
5 |
8 |
2 |
4 |
|||
|
|
||||||
60 |
16 |
1,28—0,64 |
0,80—0,48 |
— |
0,48—1,28 |
0,8—1,6 |
|
|
|
|
|
|
|
||
8 |
1,20—0,64 |
0,96—0,56 |
— |
0,24—0,64 |
0,4—0,8 |
||
|
|||||||
|
|
|
|
|
|
|
|
75 |
18 |
1,44—0,.72 |
0,90—0,54 |
— |
0,54—0,96 |
0,9—1,8 |
|
|
|
|
|
|
|
||
8 |
1,60—0,80 |
1,20—0,64 |
— |
0,24—0,64 |
0,4—0,8 |
||
|
|||||||
|
|
|
|
|
|
|
|
90 |
20 |
— |
1,60—1,00 |
— |
0,60-1,00 |
1,0—2,0 |
|
|
|
|
|
|
|
||
8 |
— |
1,60—0,80 |
1,20—0,64 |
0,24—0,64 |
0,4—0,8 |
||
|
|||||||
|
|
|
|
|
|
|
40