
2
.pdf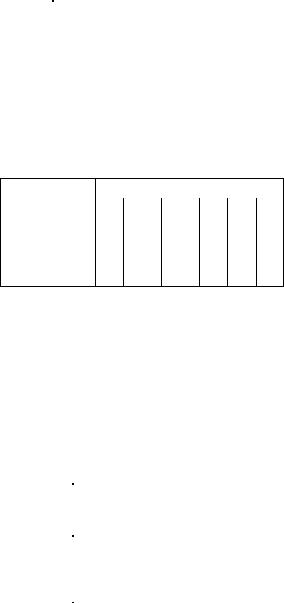
Таблица 4.2. Подачи при обработке плоскостей торцовыми фрезами мм/об
Диаметр фрезы, мм |
Количество |
|
Черновая обработка |
|
Получистовая обработка |
||
|
глубина резания t не более, мм |
|
|||||
зубьев фрезы |
|
|
|||||
|
3 |
5 |
|
8 |
2 |
4 |
|
|
|
|
|||||
|
|
|
Сталь |
|
|
|
|
|
|
|
|
|
|
|
|
60 |
16 |
1,6-0,96 |
1,28—0,8 |
|
— |
0,64—1,00 |
0,80—1,20 |
10 |
1,5—0,80 |
1,2-0,6 |
|
— |
0,48-0,80 |
0,54—0,96 |
|
|
|
||||||
75 |
18 |
1,8—1,08 |
1,44—0,9 |
|
1,0—0,5 |
0,80—1,20 |
0,96—1,44 |
10 |
1,5—0,80 |
1,2—0,6 |
|
|
0,48—0,80 |
0,54—0,96 |
|
|
|
|
|||||
90 |
20 |
2,0—1,20 |
1,6—1,0 |
|
1,2—0,6 |
0,96—1,44 |
1,2—1,60 |
12 |
1,8—0,96 |
1,44—0,72 |
|
— |
0,54—0,96 |
0,64—1,00 |
|
|
|
||||||
110 |
12 |
1,8—0,96 |
1,44-0,72 |
|
1,2-0,6 |
0,54—0,60 |
0,64—1,00 |
Таблица 4.3. Скорость резания (м/мин) и частота вращения (мин-1) при фрезеровании плоскостей из углеродистой конструкционной стали σв=650 МПа цилиндрическими фрезами (фреза из стали Р9; с охлаждением)
|
диаметр фрезы, мм |
Количеств о зубьев фрезы |
Ширина фрезы, мм |
Подача S не более, мм/об |
|
Глубина фрезерования не более, мм |
|||||||
|
|
|
|
|
|
|
|
|
|||||
|
|
3 |
|
5 |
|
8 |
|||||||
|
|
|
|
|
|
|
|
|
|||||
v |
|
n |
v |
|
n |
v |
n |
||||||
|
|
|
|
|
|
|
|
||||||
|
|
|
|
|
|
|
|
|
|
|
|
|
|
|
|
|
|
|
1,28 |
46 |
|
245 |
39 |
|
207 |
33 |
180 |
|
|
|
|
|
|
|
|||||||
|
60 |
|
16—8 |
50 |
0,80 |
49 |
|
256 |
44 |
|
222 |
36 |
192 |
|
|
0,40 |
55 |
|
285 |
48 |
|
250 |
41 |
216 |
|||
|
|
|
|
|
|
|
|||||||
|
|
|
|
|
0,32 |
59 |
|
314 |
51 |
|
274 |
44 |
234 |
|
|
|
|
|
1,44 |
49 |
|
205 |
42 |
|
177 |
36 |
154 |
|
|
|
|
|
|
|
|||||||
|
75 |
|
18-8 |
60 |
0,90 |
52 |
|
223 |
44 |
|
190 |
39 |
164 |
|
|
0,54 |
69 |
|
250 |
51 |
|
216 |
43 |
185 |
|||
|
|
|
|
|
|
|
|||||||
|
|
|
|
|
0,32 |
64 |
|
274 |
55 |
|
234 |
48 |
202 |
|
|
|
|
|
1,60 |
52 |
|
182 |
44 |
|
157 |
39 |
136 |
|
|
|
|
|
|
|
|||||||
|
90 |
|
20—8 |
70 |
1,00 |
56 |
|
198 |
48 |
|
170 |
42 |
143 |
|
|
0,60 |
63 |
|
223 |
54 |
|
187 |
47 |
165 |
|||
|
|
|
|
|
|
|
|||||||
|
|
|
|
|
0,40 |
68 |
|
240 |
57 |
|
205 |
50 |
180 |
Таблица 4.4. Поправочные коэффициенты kM на скорость резания (частоту вращения) при фрезеровании различных марок стали
Сталь |
Предел прочности σв, МПа |
|
|
|||
|
|
|
|
|
|
|
|
410- |
510- |
610- |
710- |
810- |
910- |
|
500 |
600 |
700 |
800 |
900 |
1000 |
Углеродистая |
0,9 |
1,2 |
1,0 |
0,9 |
0,8 |
0,5 |
конструкционная |
|
|
|
|
|
|
Хромоникелёиая |
1,4 |
1,2 |
0,9 |
0,8 |
0,7 |
0,3 |
Углеродистая |
|
|
|
|
|
|
инструментальная |
- |
- |
0,6 |
0,5 |
0,4 |
- |
Таблица 4.5. Скорость резания (м/мин) и частота вращения (мин-1) при фрезеровании плоскостей из углеродистой конструкционной стали σв=650 МПа - торцевыми фрезами (фреза из стали Р9; с охлаждением)
|
диаметр фрезы, мм |
Колич ество зубьев фрезы |
Подач а S не |
более, |
мм/об |
|
Глубина фрезерования не более, мм |
|
|
|||||
|
|
|
|
|||||||||||
|
3 |
|
5 |
|
|
8 |
||||||||
|
v |
n |
v |
|
n |
v |
|
n |
||||||
|
|
|
|
|
|
|
|
|
||||||
|
|
|
|
|
|
|
|
|
|
|
|
|
|
|
|
|
|
|
1,28 |
|
|
45,5 |
242 |
43,0 |
|
228 |
|
|
|
|
|
|
|
|
|
|
|
|
|
|||||
|
60 |
|
10-16 |
0,80 |
|
|
49,6 |
262 |
47,2 |
|
250 |
— |
|
— |
|
|
0,48 |
|
|
55,3 |
293 |
52,4 |
|
278' |
— |
|
— |
||
|
|
|
|
|
|
|
|
|||||||
|
|
|
|
0,32 |
|
|
60,0 |
318 |
56,6 |
|
302 |
— |
|
— |
|
|
|
|
1,44 |
|
|
46,5 |
197 |
43,6 |
|
186 |
— |
|
— |
|
|
|
|
|
|
|
|
|||||||
|
75 |
|
10-18 |
0,90 |
|
|
50,6 |
214 |
48,2 |
|
210 |
— |
|
— |
|
|
0,54 |
|
|
56,5 |
240 |
53,4 |
|
226 |
— |
|
— |
||
|
|
|
|
|
|
|
|
|||||||
|
|
|
|
0,36 |
|
|
61,0 |
260 |
59,0 |
|
250 |
— |
|
— |
|
|
|
|
2,00 |
|
|
45,0 |
158 |
42.5 |
|
150 |
39,1 |
|
138 |
|
90 |
|
12-20 |
1,60 |
|
|
47,0 |
167 |
44,6 |
|
157 |
41,0 |
|
145 |
|
|
1,00 |
|
|
51,5 |
1.83 |
48,8 |
|
173 |
45,0 |
|
159 |
||
|
|
|
|
|
|
|
|
|||||||
|
|
|
|
0.60 |
|
|
57,2 |
205 |
54,4 |
|
193 |
49,8 |
|
176' |
|
|
|
|
2,20 |
|
|
45,0 |
130 |
42,5 |
|
124 |
39,2 |
|
!12 |
|
|
|
12-20 |
1,73 |
|
|
47,0 |
136 |
44,6 |
|
129 |
41,0 |
|
118 |
|
110 |
|
1,10 |
|
|
51,5 |
150 |
49,0 |
|
142 |
45,0 |
|
130 |
|
|
|
|
|
0.66 |
|
|
57,2 |
165 |
54,5 |
|
153 |
49,8 |
|
144 |
|
|
|
|
0,44 |
|
|
62.0 |
180 |
59.0 |
|
170 |
54,0 |
|
156 |
41
Таблица 4.6. Поправочные коэффициенты kM на скорость резания (частоту вращения) при фрезеровании серого чугуна различной твердости
Твердость |
|
|
|
|
НВ |
120—140 |
141 — 180 |
181 -220 |
221-260 |
Коэффициент kм |
0,7 |
0,6 |
0,5 |
0,4 |
Примечание. Для серого чугуна поправочные коэффициенты даны в отношении углеродистой конструкционнойстали σв=650 МПа.
Таблица 4.7. Поправочные коэффициенты kx на скорость резания (частоту вращения) при фрезеровании в зависимости от характера заготовки и состояния ее поверхности
Материа |
Чистые |
Отливка, |
Прокат |
л |
отливка, |
загрязненная |
горячекатаный |
|
поковка |
включениями |
|
|
|
(сварочная корка) |
|
Сталь |
0,80 |
0,7 |
0,9 |
Чугун |
0,75 |
0,5 |
- |
Бронза |
0,90 |
0,7 |
- |
Таблица 4.8 .Поправочные коэффициенты kмр на скорость резания (частоту вращения) при фрезеровании в зависимости от марки стали фрезы
Марка стали фрезы |
Коэффициент kмр |
|
|
У10 и У12 |
0,5 |
9ХС |
0.6 |
4.2.2 Фрезерование пазов и уступов.
Прямоугольные пазы и уступы фрезеруют дисковыми или концевыми фрезами.
Ширину фрезерования устанавливают в соответствии с условиями на обработку и в связи с этим выбирают фрезу.
Шириной, равной ширине паза, а при обработке уступа — несколько больше ширины фрезеруемой поверхности.
Глубину резания определяют, исходя из припуска на обработку.
При фрезеровании пазов и уступов дисковыми фрезами подачу на оборот фрезы берут из таблицы 4.9 в зависимости от принятой глубины резания, диаметра и количества зубьев фрезы и ширины паза.
Таблица 4.9. Подачи при обработке пазов и уступов дисковыми фрезами, мм/об
Диаметр |
Количест- |
|
Глубина резания t не более, мм |
|||
фрезы, |
во |
Ширина |
|
|
|
|
зубьев |
паза, мм |
5 |
10 |
15 |
||
мм |
||||||
фрезы |
|
|||||
|
|
|
|
|
||
|
|
|
|
|
|
|
60 |
16 |
6-12 |
1.28-0,80 |
0,96-0,48 |
0,80—0,48 |
|
|
|
|
|
|
|
|
75 |
18 |
10-20 |
0,44—0,90 |
1,08—0,54 |
0,90-0.54 |
|
12 |
1,44—0,96 |
1,20-0,72 |
0,96-0,60 |
|||
|
|
|||||
90 |
20 |
10-20 |
1,60-1,00 |
1,20-0,60 |
1,00-0,60 |
|
12 |
1,44-0,96 |
1,20-0,72 |
0,96—0,60 |
|||
|
|
|||||
110 |
22 |
12-24 |
2,20—1,10 |
1,76-0,88 |
1,32—0,66 |
|
14 |
1,68-1,12 |
1,40-0,70 |
1,12-0,56 |
|||
|
|
Втаблице 4.10 приведены значения подач при обработке пазов и уступов концевыми фрезами в зависимости от глубины паза (уступа), диаметра и количества зубьев фрезы и обрабатываемого материала.
Скорость резания и частота вращения при обработке пазов и уступов дисковыми фрезами берут из таблицы 4.11 в зависимости от принятой глубины резания, подачи и диаметра фрезы.
Втаблице 4.12 приведены значения скорости резания и числа оборотов при обработке пазов и уступов концевыми фрезами. Скорость резания и частота вращения определяют в зависимости от принятой глубины резания, диаметра и количества зубьев фрезы и принятой подачи.
Выбранные из таблиц 4.11 и 4.12 значения скорости резания а числа оборотов должны быть пересчитаны на поправочные коэффициенты если условия обработки отличаются от табличных.
42
Поправочные коэффициенты даны в таблицах 4.4, 4.6, 4.7 и 4.8.
Таблица 4.10. Подачи ври обработке пазов и уступов концевыми фразами, мм/об
Диаметр |
Количество |
|
Глубина паза (уступа) не более, мм |
|
|||
фрезы, |
|
|
|
|
|
||
мм |
зубьев фрезы |
5 |
10 |
15 |
20 |
30 |
|
|
|||||||
|
|
|
|
|
|
|
|
|
|
|
Сталь |
|
|
|
|
|
|
|
|
|
|
|
|
8 |
5 |
0,05—0,10 |
0,04—0,08 |
— |
— |
— |
|
10 |
5 |
0,08—0,13 |
0,06—0,10 |
0,05—0,08 |
— |
— |
|
16 |
3 |
0,11—0,15 |
0,09—0,12 |
0,06—0,09 |
— |
— |
|
5 |
0,10—0,20 |
0,08—0,13 |
0,06—0,10 |
— |
— |
||
|
|||||||
20 |
3 |
— |
0.15—0,24 |
0,12—0,18 |
0.08—0,15 |
— |
|
5 |
— |
0,20—0,30 |
0,15—0,25 |
0,10—0,20 |
— |
||
|
|||||||
25 |
3 |
— |
0,18—0,36 |
0,18—0,30 |
0,12—0,18 |
0,08—0,15 |
|
5 |
— |
0,30—0,50 |
0,25—0,40 |
0,20—0,30 |
0,10—0,20 |
||
|
|||||||
32 |
4 |
— |
0,28—0.48 |
0.24—0,40 |
0,20—0,32 |
0,16—0,24 |
|
6 |
|
0,42—0,60 |
0,36—0,54 |
0,24—0,36 |
0,18—0,30 |
||
|
|
4.2.3 Отрезные работы
Для отрезных работ применяют тонкие дисковые фрезы, которые называют отрезными. Глубину резания при работе отрезными фрезами принимают в пределах от 6 до 30 мм.
Подачу определяют по таблице 4.13 в зависимости от обрабатываемого материала, диаметра, количества зубьев и ширины фрезы и принятой глубины резания.
Скорость резания определяют по таблице 4.14 в зависимости от принятой глубины резания, диаметра, количеству зубьев и ширины фрезы и принятой подачи.
При измененных условиях эксплуатации взятые из таблицы 4.14 значения скорости резания и числа оборотов должны быть пересчитаны на поправочные коэффициенты (см. табл. 4.4, 4.6, 4.7 и 4.8).
Таблица 4.11. Скорость резания м/мин и частота вращения (мин-1) при фрезеровании пазов и уступов в углеродистой конструкционной стали σв=650 МПа дисковыми фрезами (фреза из стали Р9; с охлаждением)
диаметр фрезы, мм |
Подача S не более, мм/об |
|
|
|
Глубина паза (уступа) неболее, мм |
|
|
|
|||||||
|
|
|
|
|
|
|
|
|
|
|
|
|
|
||
|
5 |
|
10 |
|
15 |
|
|
|
20 |
||||||
|
|
|
|
|
|
|
|
||||||||
|
|
|
|
|
|
|
|
|
|
|
|
|
|
|
|
|
1,28 |
48 |
|
253 |
|
38 |
|
205 |
34 |
|
181 |
|
|
|
|
60 |
0,80 |
51 |
|
272 |
|
41 |
|
221 |
36 |
|
196 |
|
— |
|
— |
0.42 |
58 |
|
305 |
|
47 |
|
248 |
41 |
|
220 |
|
— |
|
— |
|
|
|
|
|
|
|
|
|||||||||
|
0,32 |
62 |
|
331 |
|
50 |
|
269 |
55 |
|
238 |
|
— |
|
— |
|
1,44 |
49 |
|
207 |
|
39 |
|
!59 |
35 |
|
149 |
|
32 |
|
137 |
75 |
0,90 |
52 |
|
225 |
|
42 |
|
182 |
37 |
|
161 |
|
35 |
|
147 |
0,54 |
59 |
|
250 |
|
43 |
|
204 |
42 |
|
180 |
|
38 |
|
165 |
|
|
|
|
|
|
|
|
|||||||||
|
0,35 |
64 |
|
272 |
|
52 |
|
221 |
46 |
|
196 |
|
41 |
|
179 |
|
1,60 |
50 |
|
177 |
|
39 |
|
144 |
36 |
|
127 |
|
33 |
|
116 |
90 |
1,00 |
53 |
|
190 |
|
43 |
|
154 |
38 |
|
127 |
|
35 |
|
125 |
0,60 |
60 |
|
213 |
|
49 |
|
173 |
42 |
|
153 |
|
39 |
|
140 |
|
|
|
|
|
|
|
|
|||||||||
|
0,40 |
05 |
|
231 |
|
52 |
|
188 |
47 |
|
166 |
|
42 |
|
153 |
|
1,70 |
52 |
|
146 |
|
40 |
|
119 |
36 |
|
106 |
|
33 |
|
100 |
110 |
1.10 |
54 |
|
158 |
|
43 |
|
129 |
38 |
|
114 |
|
36 |
|
104 |
0,66 |
61 |
|
177 |
|
50 |
|
144 |
43 |
|
128 |
|
39 |
|
116 |
|
|
|
|
|
|
|
|
|||||||||
|
0,11 |
66 |
|
124 |
|
53 |
|
156 |
48 |
|
138 |
|
43 |
|
127 |
43
Таблица 4.12. Скорость резания и частота вращения при фрезеровании пазов и уступов в углеродистой конструкционной стили σв=650МПа концевыми фрезами (фреза из стали Р9; с охлаждением)
|
Количест- |
Подача S |
Глубина паза (уступа) не более, мм |
|
|
|
|
|
|
||||
диаметр |
|
|
|
|
|
|
|
|
|
|
|||
во зубьев |
не более, |
5 |
|
10 |
|
15 |
|
20 |
|
30 |
|
||
фрезы, мм |
фрезы |
мм/об |
|
|
|
|
|
|
|
|
|
|
|
v |
n |
v |
n |
v |
n |
v |
n |
v |
n |
||||
|
|||||||||||||
|
|
|
|
|
|
|
|
|
|
|
|
|
|
|
|
0,03 |
- |
- |
126 |
5000 |
— |
— |
— |
— |
— |
— |
|
8 |
5 |
0,04 |
110 |
4350 |
103 |
4100 |
— |
— |
— |
— |
— |
— |
|
0,05 |
99 |
3950 |
92 |
3650 |
— |
— |
— |
— |
— |
— |
|||
|
|
||||||||||||
|
|
0,10 |
70 |
2800 |
65 |
2600 |
— |
— |
— |
— |
— |
— |
|
|
|
0,04 |
- |
_- |
102 |
3250 |
97 |
3100 |
— |
— |
— |
— |
|
|
|
|
|
|
|
|
|
|
|
|
|
|
|
10 |
5 |
0.05 |
98 |
3100 |
91 |
2900 |
82 |
2750 |
— |
— |
— |
— |
|
|
|
|
|
|
|
|
|
|
|
|
|||
0,10 |
69 |
2200 |
64 |
2050 |
62 |
1980 |
— |
— |
— |
— |
|||
|
|
||||||||||||
|
|
|
|
|
|
|
|
|
|
|
|
|
|
|
|
0.15 |
56 |
1780 |
— |
— |
— |
— |
— |
— |
— |
— |
|
|
|
|
|
|
|
|
|
|
|
|
|
|
|
|
|
0.03 |
87 |
1730 |
81 |
1610 |
78 |
1550 |
— |
— |
— |
— |
|
|
|
|
|
|
|
|
|
|
|
|
|
|
|
|
|
0,06 |
61 |
1220 |
60 |
1200 |
58 |
1160 |
— |
—. |
— |
— |
|
16 |
3-5 |
|
|
|
|
|
|
|
|
|
|
|
|
0,12 |
53 |
1060 |
57 |
11.30 |
55 |
1100 |
— |
— |
— |
— |
|||
|
|
0,18 |
46 |
920 |
50 |
990 |
48 |
950 |
— |
— |
— |
— |
|
|
|
|
|
|
|
|
|
|
|
|
|
|
|
|
|
0,20 |
44 |
860 |
47 |
940 |
— |
— |
— |
— |
— |
— |
|
|
|
0,06 |
|
|
46 |
730 |
44 |
700 |
43 |
680 |
— |
— |
|
|
|
0,09 |
— |
— |
42 |
670 |
41 |
640 |
40 |
630 |
— |
— |
|
20 |
3—5 |
0,12. |
— |
— |
40 |
640 |
39 |
610 |
37 |
590 |
— |
— |
|
0,18 |
— |
— |
35 |
550 |
33 |
520 |
32 |
510 |
— |
— |
|||
|
|
||||||||||||
|
|
0,24 |
— |
— |
33 |
520 |
31 |
4S5 |
— |
— |
— |
— |
|
|
|
|
|
|
|
|
|
|
|
|
|
|
|
|
|
0,30 |
— |
— |
30 |
480 |
— |
— |
— |
— |
— |
— |
|
|
|
|
|
|
|
|
|
|
|
|
|
|
|
|
|
0,06 |
— |
__ |
42 |
530 |
40 |
510 |
— |
495 |
38 |
480 |
|
|
|
0,09 |
— |
— |
40 |
500 |
38 |
485 |
37 |
470 |
36 |
450 |
|
|
|
|
|
|
|
|
|
|
|
|
|
|
|
|
|
0,12 |
— |
— |
34 |
435 |
33 |
415 |
32 |
405 |
31 |
390 |
|
|
|
|
|
|
|
|
|
|
|
|
|
|
|
25 |
3—5 |
0,18 |
— |
— |
32 |
405 |
31 |
395 |
30 |
380 |
29 |
370 |
|
|
|
|
|
|
|
|
|
|
|
|
|||
0,24 |
— |
— |
30 |
375 |
29 |
360 |
— |
— |
— |
— |
|||
|
|
||||||||||||
|
|
|
|
|
|
|
|
|
|
|
|
|
|
|
|
0,36 |
— |
— |
28 |
355 |
27 |
345 |
— |
— |
— |
— |
|
|
|
|
|
|
|
|
|
|
|
|
|
|
|
|
|
0,40 |
— |
— |
24 |
305 |
— |
— |
— |
— |
— |
— |
|
|
|
|
|
|
|
|
|
|
|
|
|
|
|
|
|
0,60 |
— |
- |
23 |
290 |
— |
— |
— |
— |
— |
— |
|
|
|
|
|
|
|
|
|
|
|
|
|
|
|
|
|
0,12 |
— |
— |
29 |
235 |
28 |
275 |
27 |
265 |
26 |
255 |
|
|
|
0,16 |
— |
— |
28 |
275 |
26 |
260 |
25 |
255 |
24 |
245 |
|
32 |
4—6 |
0,24 |
— |
— |
25 |
250 |
24 |
240 |
23 |
230 |
— |
— |
|
0.36 |
— |
— |
24 |
'240 |
23 |
230 |
22 |
220 |
— |
— |
|||
|
|
||||||||||||
|
|
0,48 |
— |
— |
20 |
200 |
19 |
193 |
— |
— |
— |
— |
|
|
|
|
|
|
|
|
|
|
|
|
|
|
|
|
|
0,72 |
— |
— |
19 |
192 |
18 |
185 |
— |
— |
— |
— |
|
|
|
|
|
|
|
|
|
|
|
|
|
|
Таблица 4.13. Подачи при работе отрезными фрезами, мм/об
Диаметр фрезы, |
Количество |
Ширина |
|
|
Глубина резания не более, мм |
|
||
мм |
зубьев |
фрезы, мм |
6 |
|
10 |
15 |
20 |
30 |
|
|
|
|
|||||
|
|
|
|
|
|
|
|
|
|
|
|
|
Сталь |
|
|
|
|
|
|
|
|
|
|
|
|
|
60 |
36 |
1 |
0,54—0,72 |
|
0,36—0,72 |
— |
— |
— |
30 |
2 |
0.45—0,75 |
|
0,30-0,60 |
— |
— |
— |
|
|
|
|||||||
75 |
36 |
1 |
0.54—0,72 |
|
0,36—0,72 |
— |
— |
— |
2 |
0,54—0.90 |
|
0,36-0,72 |
0,36—0,72 |
- |
- |
||
|
|
|
||||||
|
30 |
3 |
0,60—0,90 |
|
0,45—0,75 |
0,36—0,72 |
|
|
110 |
50 |
1,5 |
1,00-1,25 |
|
0,75—1,00 |
0,50—1,00 |
0,50—1,00 |
0,50—0,75 |
|
|
|
|
|
|
|
|
|
40 |
2 |
1.25—1,50 |
|
1,00—1,25 |
1,00—1,25 |
0,75—1,25 |
0,75—1,00 |
|
|
|
|||||||
|
3 |
0,80—1,20 |
|
0,80—1,20 |
0,80—1,00 |
0.60—0,80 |
0,40—0,60 |
|
|
|
|
||||||
150-200 |
60 |
2 |
— |
|
— |
1,20—1,50 |
0,90—1,20 |
0,60—0,90 |
50 |
3 |
|
|
|
1,06—1,50 |
0,75—1,25 |
0,75-1,00 |
|
|
|
|
|
44
Таблица 4.14. Скорость резания и частота вращения при отрезании конструкционной углеродистой стали σв=650МПа (фреза из стали Р9; с охлаждением)
|
|
Ширина |
Подачи |
|
|
|
|
|
|
|
|
Глубина резания не более, мм |
|
|
|
|
|
|
|||||||
Диаметр |
Количество |
Soб не |
|
|
|
|
|
|
|
|
|
|
|
|
|
|
|
|
|
|
|
|
|
|
|
Фрезы, мл: |
зубьев |
фрезы, |
более, |
|
6 |
10 |
|
15 |
|
|
|
20 |
|
|
30 |
||||||||||
|
|
мм |
м/мин |
|
|
|
|
|
|
|
|
|
|
|
|
|
|
|
|
|
|
|
|
|
|
|
|
v |
|
|
n |
|
v |
|
|
n |
|
v |
|
|
n |
v |
|
|
n |
v |
|
n |
|||
|
|
|
|
|
|
|
|
|
|
|
|
|
|
||||||||||||
|
|
|
|
|
|
|
|
|
|
|
|
|
|
|
|||||||||||
|
|
|
|
|
|
|
|
|
|
|
|
|
|
|
|
|
|
|
|
|
|
|
|
|
|
|
|
|
0,30 |
75 |
|
400 |
65 |
|
|
345 |
- |
|
|
_ |
|
— |
|
|
— |
— |
|
— |
|||
|
|
|
|
|
|
|
|
|
|
|
|
|
|
|
|
|
|
|
|
|
|
|
|
|
|
|
|
|
0,40 |
70 |
|
370 |
60 |
|
|
320 |
|
— |
|
|
— |
— |
|
|
— |
— |
|
— |
|||
|
|
|
|
|
|
|
|
|
|
|
|
|
|
|
|
|
|
|
|
|
|
|
|
|
|
60 |
30—36 |
1—2 |
0,45 |
66 |
|
350 |
57 |
|
|
300 |
|
— |
|
|
— |
— |
|
|
— |
— |
|
— |
|||
|
|
|
0,60 |
52 |
|
275 |
45 |
|
|
235 |
|
— |
|
|
— |
— |
|
|
— |
— |
|
— |
|||
|
|
|
0,72 |
48 |
|
255 |
41 |
|
|
220 |
|
— |
|
|
— |
— |
|
|
— |
— |
|
— |
|||
|
|
|
0,90 |
45 |
|
240 |
39 |
|
|
210 |
|
— |
|
|
— |
— |
|
|
|
— |
|
|
|||
|
|
|
|
|
|
|
|
|
|
|
|
|
|
|
|
|
|
|
|
|
|
|
|
|
|
|
|
|
0,30 |
74 |
|
315 |
|
63 |
|
|
270 |
|
56 |
|
|
240 |
|
— |
|
|
— |
— |
|
— |
|
|
|
|
0.36 |
67 |
|
285 |
|
58 |
|
|
245 |
|
52 |
|
|
220 |
|
— |
|
|
— |
__ |
|
— |
|
|
|
|
|
|
|
|
|
|
|
|
|
|
|
|
|
|
|
|
|
|
|
|
|
|
|
|
|
|
0,45 |
65 |
|
275 |
|
56 |
|
|
240 |
|
50 |
|
|
210 |
|
— |
|
|
— |
— |
|
— |
|
|
|
|
|
|
|
|
|
|
|
|
|
|
|
|
|
|
|
|
|
|
|
|
|
|
|
75 |
30—36 |
1,5—3 |
0,54 |
64 |
|
270 |
|
55 |
|
|
235 |
|
49 |
|
|
210 |
|
— |
|
|
— |
— |
|
— |
|
|
|
|
|
|
|
|
|
|
|
|
|
|
|
|
|
|
|
|
|
|
|
|
|||
0,60 |
60 |
|
|
255 |
|
52 |
|
|
220 |
|
46 |
|
|
195 |
|
— |
|
|
— |
— |
|
— |
|||
|
|
|
|
|
|
|
|
|
|
|
|
|
|
||||||||||||
|
|
|
|
|
|
|
|
|
|
|
|
|
|
|
|
|
|
|
|
|
|
|
|
|
|
|
|
|
0,72 |
59 |
|
250 |
|
51 |
|
|
215 |
|
45 |
|
|
192 |
|
— |
|
|
— |
— |
|
— |
|
|
|
|
|
|
|
|
|
|
|
|
|
|
|
|
|
|
|
|
|
|
|
|
|
|
|
|
|
|
0,90 |
57 |
|
240 |
|
49 |
|
|
210 |
|
43 |
|
|
182 |
|
— |
|
|
— |
—. |
|
— |
|
|
|
|
|
|
|
|
|
|
|
|
|
|
|
|
|
|
|
|
|
|
|
|
|
|
|
|
|
|
1,10 |
53 |
|
225 |
|
44 |
|
|
187 |
|
40 |
|
|
170 |
|
— |
|
|
— |
— |
|
— |
|
|
|
|
|
|
|
|
|
|
|
|
|
|
|
|
|
|
|
|
|
|
|
||||
|
|
|
0.60 |
61 |
|
177 |
|
53 |
|
|
154 |
|
47 |
|
|
136 |
|
43 |
|
124 |
— |
|
— |
||
|
|
|
0,75 |
58 |
|
168 |
|
51 |
|
|
148 |
|
45 |
|
|
129 |
|
41 |
|
119 |
— |
|
— |
||
110 |
40—50 |
2—3 |
0.85 |
54 |
|
157 |
|
46 |
|
|
133 |
|
41 |
|
|
119 |
|
38 |
|
109 |
— |
|
— |
||
1.00 |
50 |
|
|
145 |
|
43 |
|
|
124 |
|
23 |
|
|
110 |
|
33 |
|
101 |
— |
|
— |
||||
|
|
|
|
|
|
|
|
|
|
|
|
|
|||||||||||||
|
|
|
1.20 |
48 |
|
|
139 |
|
41 |
|
|
119 |
|
36 |
|
|
104 |
|
33 |
|
96 |
— |
|
— |
|
|
|
|
1.50 |
44 |
|
|
128 |
|
38 |
|
|
110 |
|
34 |
|
|
97 |
|
31 |
|
90 |
— |
|
— |
|
|
|
|
|
|
|
|
|
|
|
|
|
|
|
|
|
|
|
|
|
|
|
||||
|
|
|
0.75 |
— |
|
|
|
|
|
|
|
|
|
43 |
|
|
90 |
|
39 |
|
33 |
35 |
|
73 |
|
|
|
|
0,90 |
— |
|
|
— |
|
— |
|
— |
|
41 |
|
|
86 |
|
37 |
|
79 |
33 |
|
70 |
||
150 |
50—60 |
2-4 |
1,00 |
|
|
|
|
|
|
|
|
|
|
37 |
|
|
79 |
|
34 |
|
72 |
30 |
|
64 |
|
1.20 |
— |
|
|
— |
|
— |
|
— |
|
35 |
|
|
75 |
|
32 |
|
68 |
28 |
|
60 |
|||||
|
|
|
|
|
|
|
|
|
|
|
|
|
|||||||||||||
|
|
|
1,50 |
|
|
|
|
|
|
|
|
|
|
32 |
|
|
68 |
|
30 |
|
64 |
26 |
|
55 |
|
|
|
|
1.80 |
|
|
|
|
|
|
|
|
|
|
30 |
|
|
64 |
|
26 |
|
55. |
24 |
|
50 |
|
|
|
|
|
|
|
|
|
|
|
|
|
|
|
|
|
|
|
|
|
||||||
|
|
|
0,75 |
— |
|
|
— |
|
— |
|
— |
|
46 |
|
|
72 |
|
42 |
|
67 |
37 |
|
59 |
||
|
|
|
|
|
|
|
|
|
|
|
|
|
|
|
|
|
|
|
|
|
|
|
|
||
|
|
|
0,90 |
— |
|
|
— |
|
— |
|
— |
|
43 |
|
|
68 |
|
39 |
|
62 |
35 |
|
53 |
||
200 |
50-60 |
3—5 |
1,00. |
— |
|
|
— |
|
— |
|
— |
|
42 |
|
|
67 |
|
38 |
|
60 |
34 |
|
52 |
||
1.20 |
|
|
|
|
|
|
|
|
|
|
40 |
|
|
64 |
|
37 |
|
58 |
32 |
|
51 |
||||
|
|
|
|
|
|
|
|
|
|
|
|
|
|
|
|
|
|
||||||||
|
|
|
1.50 |
|
|
|
|
|
|
|
|
|
|
39 |
|
|
60 |
|
36 |
|
56 |
30 |
|
47 |
|
|
|
|
1,80 |
— |
|
|
— |
|
— |
|
— |
|
37 |
|
|
58 |
|
34 |
|
53 |
28 |
|
45 |
||
|
|
|
|
|
|
|
|
|
|
|
|
|
|
|
|
|
|
|
|
|
|
|
|
|
|
45
4.3 Расчет нормы времени
4.3.1 Расчет основного времени
Расчет нормы времени приведен в разделе 1.
Основное время при фрезеровании рассчитывают по формуле:
t |
o |
|
L i |
(4.3) |
|
n Sоб |
|||||
|
|
|
где L — длина фрезеруемой поверхности с учетом врезания и перебега, мм; i — число проходов;
So6 - подача на один оборот фрезы, мм/об; n — частота вращения, мин-1.
Длину фрезерования определяют по формуле (2.6). Значения величин врезания и перебега приведены в таблицах 4.15 и 4.16.
Таблица 4.15. Величины врезания и перебега при фрезеровании цилиндрическими и дисковыми фрезами.
|
|
|
|
Перебег фрезы у2, м |
|
|
|
|
|||
Глубина |
|
|
|
|
|
|
|
|
|
|
|
2 |
2 |
2,5 |
2,5 |
3 |
3 |
3,5 |
|
3,5 |
4 |
||
резання |
|
|
|
диаметр фрезы, мм |
|
|
|
|
|||
не более, |
|
|
|
|
|
|
|
|
|
|
|
40 |
50 |
60 |
75 |
|
90 |
110 |
130 |
|
150 |
200 |
|
мм |
|
|
|||||||||
|
|
|
|
|
|
|
|
|
|
|
|
|
|
|
|
врезание фрезы у1, мм |
|
|
|
|
|||
|
|
|
|
|
|
|
|
|
|
|
|
1 |
6,6 |
7,0 |
7,7 |
8,6 |
|
9,4 |
10,5 |
11,4 |
|
12,2 |
14,1 |
2 |
8,7 |
9,8 |
10,8 |
12,1 |
|
13,3 |
J4.7 |
16,0 |
|
17,2 |
19,3 |
3 |
10,5 |
11,9 |
13,1 |
14,7 |
|
16,2 |
17,9 |
19,5 |
|
21,0 |
24,3 |
4 |
12,0 |
13,6 |
15,0 |
16,9 |
|
18,6 |
20,6 |
22,5 |
|
24,2 |
28,0 |
5 |
13,2 |
15,0 |
16,6 |
18,7 |
|
20,6 |
22,9 |
25,0 |
|
26,9 |
31,2 |
6 |
14,3 |
16,2 |
18,2 |
20,4 |
|
22,5 |
25,0 |
27,3 |
|
29,4 |
34,4 |
7 |
15,2 |
17,3 |
19,3 |
21,8 |
|
24,1 |
26,9 |
29,4 |
|
31,6 |
36,8 |
8 |
16,0 |
18,3 |
20,4 |
23,2 |
|
25,6 |
28,6 |
31,2 |
|
33,7 |
39,2 |
9 |
16,7 |
19,2 |
21,4 |
24,2 |
|
27,0 |
30,2 |
33,0 |
|
35,6 |
41,6 |
10 |
17,3 |
20,0 |
22,4 |
25,5 |
|
28,3 |
31,6 |
34,7 |
|
37,4 |
43,6 |
12 |
— |
21,4 |
24,0 |
27,5 |
|
30,6 |
34,3 |
37,7 |
|
40,7 |
44,6 |
14 |
— |
— |
25,4 |
29,2 |
|
32,7 |
36,7 |
40,3 |
|
43,6 |
51,4 |
16 |
— |
— |
— |
30,7 |
|
34,4 |
38,7 |
42,7 |
|
46,6 |
54,4 |
18 |
— |
— |
— |
32,2 |
|
36,0 |
40,7 |
45,0 |
|
48,8 |
57,2 |
20 |
— |
— |
— |
— |
|
37,4 |
42,2 |
47,0 |
|
51,0 |
60.0 |
25 |
— |
— |
— |
— |
|
— |
50,0 |
55,0 |
|
60,0 |
65,0 |
30 |
— |
— |
— |
— |
|
— |
— |
60,0 |
|
65,0 |
70,0 |
|
|
|
|
|
|
|
|
|
|
|
|
Таблица 4.16. Величины врезания и перебега при фрезеровании торцовыми и концевыми фрезами, мм
Ширина |
|
|
|
Диаметр фрезы не более, мм |
|
|
|
||||
фрезерова- |
|
|
|
|
|
|
|||||
|
|
|
|
|
|
|
|
|
|
|
|
ния не |
|
|
|
|
|
|
|
|
|
|
|
16 |
20 |
25 |
|
32 |
40 |
50 |
60 |
75 |
90 |
110 |
|
более, мм |
|
||||||||||
|
|
|
|
|
|
|
|
|
|
|
|
10 |
3 |
3 |
3 |
|
3 |
— |
— |
— |
— |
— |
— |
15 |
— |
4 |
4 |
|
4 |
4 |
4 |
4 |
4 |
— |
— |
20 |
— |
— |
6 |
|
5 |
4 |
4 |
4 |
4 |
4 |
— |
14 |
— |
— |
14 |
|
8 |
6 |
5 |
5 |
5 |
5 |
— |
30 |
— |
— |
— |
12 |
8 |
7 |
6 |
6 |
6 |
— |
|
40 |
— |
— |
— |
— |
— |
12 |
10 |
8 |
7 |
7 |
|
50 |
— |
— |
— |
— |
— |
— |
16 |
12 |
10 |
9 |
|
60 |
— |
— |
— |
— |
— |
— |
— |
18 |
14 |
12 |
|
60 |
— |
— |
— |
— |
— |
— |
— |
— |
28 |
20 |
|
100 |
— |
— |
— |
— |
— |
— |
— |
— |
— |
35 |
|
120 |
— |
— |
— |
— |
— |
— |
— |
— |
— |
44 |
|
КО |
— |
— |
— |
— |
— |
— |
— |
— |
— |
60 |
|
|
|
|
|
|
|
|
|
|
|
|
|
46

Обработка шпоночных канавок.
Шпоночные канавки на валах и вообще в охватываемых деталях изготовляются для призматических и сегментных шпонок.
Шпоночные канавки для призматических шпонок могут быть закрытыми с двух сторон (глухие), закрытыми с одной стороны и сквозными.
Шпоночные канавки изготовляются различными способами в зависимости от конфигурации канавки и вала, применяемого инструмента; они выполняются на горизонтально-фрезерных или на вертикально-фрезерных станках общего назначения или специальных.
Сквозные и закрытые с одной стороны шпоночные канавки изготовляются фрезерованием дисковыми фрезами (рис. 4.2, а). Фрезерование канавки производится за один - два прохода. Этот способ наиболее производителен и обеспечивает достаточную точность ширины канавки.
Основное время при фрезеровании дисковой фрезой шпоночной канавки — сквозной и закрытой с одной стороны — определяется по формуле
t |
o |
|
lo lвр |
|
|
(4.4) |
||
Sм.пр |
||||||||
|
|
|
||||||
где l0 — длина шпоночной канавки в мм; |
|
|||||||
lвр |
|
|
|
(0.5...2) |
(4.5) |
|||
|
h(Dф h) |
DФ — диаметр фрезы в мм;
h — глубина шпоночной канавки в мм; Sм.np — продольная подача в мм/мин.
Применение этого способа ограничивает конфигурация канавок: закрытые канавки с закруглениями на концах не могут выполняться этим способом; они изготовляются концевыми фрезами с продольной подачей за один или несколько проходов (рис. 4.2, б).
а — дисковой фрезой с продольной подачей; б — концевой фрезой с продольной подачей; в — концевой фрезой с маятниковой подачей; г — концевой дисковой фрезой с вертикальной подачей
Рис. 4.2. Методы фрезерования шпоночных канавок валов.
Фрезерование концевой фрезой за один проход производится таким образом, что сначала фреза при вертикальной подаче проходит на полную глубину канавки, а потом включается продольная подача, с которой шпоночная канавка фрезеруется на полную длину. При этом способе требуется мощный станок, прочное крепление фрезы и обильное охлаждение. Вследствие того что фреза работает в основном своей периферической частью, диаметр которой после заточки несколько уменьшается, в зависимости от числа переточек фреза дает неточный размер канавки по ширине.
47
Основное время при фрезеровании шпоночной канавки, закрытой с двух сторон, за один проход определяется по формуле
to |
h (0.5...1) |
|
lo |
Dф |
(4.6) |
|
Sм.верт |
Sм.пр |
|||||
|
|
|
где h — глубина шпоночной канавки в мм; l0 — длина шпоночной канавки в мм;
Dф — диаметр фрезы, равный ширине канавки в мм; Sм.верт. — вертикальная подача в мм/мин;
Sм.np — продольная подача в мм/мин.
Для получения по ширине точных канавок применяются специальные шпоночно-фрезерные станки с «маятниковой подачей», работающие концевыми двухспиральными фрезами с лобовыми режущими кромками. При этом способе фреза врезается на 0,1—0,3 мм и фрезерует канавку на всю длину, затем опять врезается на ту же глубину, как и в предыдущем случае, и фрезерует канавку опять на всю длину, но в другом направлении (рис. 4.2, в). Отсюда и происходит определение метода — «маятниковая подача».
Этот метод является наиболее рациональным для изготовления шпоночных канавок в серийном и массовом производствах, так как дает вполне точную канавку, обеспечивающую взаимозаменяемость в шпоночном соединении. Кроме того, поскольку фреза работает лобовой частью, она будет долговечнее, так как изнашивается не периферийная часть ее, а лобовая. Недостатком этого способа является значительно большая затрата времени на изготовление канавки по сравнению с фрезерованием за один проход и тем более с фрезерованием дисковой фрезой. Отсюда вытекает следующее:
1)метод маятниковой подачи надо применять при изготовлении канавок, требующих взаимозаменяемости;
2)фрезеровать канавки в один проход нужно в тех случаях, когда допускается пригонка шпонок по канавкам.
Основное время при фрезеровании шпоночной канавки, закрытой с двух сторон, с «маятниковой» подачей определяется по формуле
to |
h (0.5...1) |
|
lo |
Dф |
(4.7) |
|
t |
Sм.пр |
|||||
|
|
|
где l0 — длина шпоночной канавки в мм;
Dф — диаметр фрезы, равный ширине канавки в мм; Sм.np — продольная подача в мм/мин;
h— глубина шпоночной канавки в мм;
t — величина вертикального врезания на один ход фрезы в мм.
Сквозные шпоночные канавки валов можно обрабатывать на строгальных станках. Канавки на длинных валах, например на ходовом вале токарного станка, строгают на продольно-строгальном станке. Канавки на коротких валах строгают на поперечно-строгальном станке — преимущественно в индивидуальном и мелкосерийном производстве.
Шпоночные канавки под сегментные шпонки изготовляются фрезерованием с помощью концевых дисковых фрез (рис. 4.2, г).
Основное время при фрезеровании канавок под сегментные шпонки определяется по формуле
to |
|
h (0.5...1) |
(4.8) |
|
Sм.верт |
||||
|
|
|
где h — глубина шпоночной канавки в мм; Sм.верт — вертикальная подача в мм/мин.
48

Шпоночные канавки в отверстиях втулок зубчатых колес, шкивов и других деталей, надевающихся на вал со шпонкой, обрабатываются в индивидуальном и мелкосерийном производствах на долбежных станках, в крупносерийном и массовом—на протяжных станках.
Рис. 4.3. Обработка шпоночной канавки в отверстии протягиванием
На рис.4.3 показано протягивание шпоночной канавки в заготовке зубчатого колеса на горизонтально-протяжном станке. Заготовка 1 насаживается на направляющий палец 4, внутри которого имеется паз для направления протяжки 2. Когда канавка протягивается за 2—3 прохода, то под протяжку помещают подкладку 3.
Основное время при протягивании шпоночной канавки определяется по формуле
to |
|
L l |
Д |
(10...30) |
|
|
|
|
|
|
, мин |
(4.9) |
|
|
|
|
||||
|
|
1000 Vр |
|
где L—рабочая длина протяжки в мм;
lд — длина протягиваемой поверхности детали в мм; vр — скорость рабочего хода протяжки в м/мин;
i — число проходов.
Фрезерование шлицев.
В шлицевых соединениях сопряженные детали центрируются тремя способами:
1) центрированием втулки (или зубчатого колеса) по наружному диаметру шлицевых выступов
вала;
2)центрированием втулки (или зубчатого колеса) по внутреннему диаметру шлицев вала (т. е. по дну впадин);
3)центрированием втулки (или зубчатого колеса) по боковым сторонам шлицев.
Форма шлицев бывает прямоугольная, эвольвентная и треугольная.
Шлицевые соединения широко применяются в машиностроении (станкостроении, автомобиле- и тракторостроении и других отраслях) для неподвижных и подвижных посадок.
Технологический процесс изготовления шлицев валов зависит от того, какой принят способ центрирования вала и втулки. Наиболее точным является способ центрирования по внутреннему диаметру шлицев вала; он применяется, например, в станкостроительной и реже в автомобильной промышленности. Центрирование по наружному диаметру шлицевых выступов вала встречается довольно часто, этот способ применяется в тракторостроении, в автомобилестроении, а также в станкостроении и др. Центрирование по боковым сторонам шлицев применяют сравнительно редко. В автомобильной промышленности этот способ применяется для передачи больших крутящих моментов при наименьшем боковом зазоре.
Шлицы на валах и других деталях изготовляются различными способами, к числу которых относятся: фрезерование с последующим шлифованием, накатывание (шлиценакатывание), протягивание, строгание (шлицестрогание).
Наиболее распространенным способом изготовления шлицев является фрезерование. Шлицы валов небольших диаметров (до 100 мм) обычно фрезеруют за один проход, больших диаметров — за два прохода. Черновое фрезерование шлицев, в особенности больших диаметров, иногда производится фрезами на горизонтально-фрезерных станках, имеющих делительные механизмы (рис. 4.4).
49

а — шлицевой дисковой фрезой; б — двумя фрезами; в — двумя дисковыми специальными фрезами; г — шлицевой червячной фрезой
Рис. 4.4. Способы фрезерования шлицев валов.
На рис. 4.4, а показано фрезерование одной канавки шлицев дисковой фасонной фрезой. Основное время при этом определяется по формуле
to |
|
lo lвр lп |
i |
(4.10) |
|
||||
|
|
Sм.пр |
|
где l0 — длина нарезаемых шлицев в мм; lвр — величина врезания;
lвр |
h (Dф h) (1..2) |
(4.11) |
где lп — величина перебега; l = 2...5 мм; i — число шлицев;
h — высота шлица, фрезеруемого в данном проходе, в мм; Dф —диаметр фрезы в мм;
Sм.пр Sz z n— продольная минутная подача;
где Sz — подача на зуб фрезы в мм; z — число зубьев фрезы;
n — частота вращения фрезы, мин-1.
Фрезеровать шлицы можно способом, изображенным на рис. 4.4, б, позволяющим применять более дешевые фрезы, чем дисковые.
Более производительным способом является одновременное фрезерование двух шлицевых канавок двумя дисковыми фрезами специального профиля (рис. 4.4, в).
Чистовое фрезерование шлицев дисковыми фрезами производится только в случае отсутствия специального станка или инструмента, так как оно не дает достаточной точности по шагу и ширине шлицев.
Более точное фрезерование шлицев производится методом обкатки при помощи шлицевой червячной фрезы (рис. 4.4, г). Фреза помимо вращательного движения имеет продольное перемещение вдоль оси нарезаемого вала. Этот способ является наиболее точным и наиболее производительным.
50