
2
.pdfТаблица 2.17. Скорость резания при отрезке и прорезке углеродистой конструкционной стали σВ= 650 МПа (резец из стали Р9 без охлаждения)
Подача S не |
|
0,06 |
0,08 |
0,10 |
0,15 |
0,20 |
0,25 |
0,30 |
0,40 |
0,50 |
более, мм/об |
|
|
|
|
|
|
|
|
|
|
Скорость |
резания |
44 |
37 |
32 |
25 |
21 |
18 |
16 |
13 |
12 |
V, м/мин |
|
|
|
|
|
|
|
|
|
|
Таблица 2.18. Скорость резания при отрезке и прорезке углеродистой конструкционной σВ=650МПа (резец из стали Т15К6 без охлаждения)
Подача S |
не |
0,08 |
0,10 |
0,15 |
0,20 |
0,25 |
0,30 |
0,40 |
0,50 |
более, мм/об |
|
|
|
|
|
|
|
|
|
Скорость |
|
179 |
160 |
107 |
87 |
73 |
62 |
50 |
41 |
резания |
V, |
|
|
|
|
|
|
|
|
м/мин |
|
|
|
|
|
|
|
|
|
Выбранная из таблицы 2.17 или 2.18 скорость резания должна быть пересчитана на поправочные коэффициенты в зависимости от измененных условий эксплуатации (табл. 2.5, 2.6, 2.7, 2.8, 2.9 и 2.19).
Таблица 2.19. Поправочные коэффициенты на скорость резания в зависимости от отношения конечного диаметра обработки к начальному d2/d1 при отрезке деталей с отверстиями
Материал |
режущей |
части |
Отношение d2/d1 |
|
|
|
резца |
|
|
|
|
|
|
|
|
1.0 |
0,5-0,6 |
0,7—0,8 |
больше 0,8 |
|
|
|
|
||||
Сталь |
быстрорежущая |
1,0 |
0,96 |
0,92 |
0,88 |
|
Твердый сплав |
|
1,0 |
0,97 |
0,90 |
0,84 |
Примечание. d2—диаметр отверстия (конечный диаметр заготовки, или детали); d1-наружный (начальный) диаметр заготовки (детали).
2.2.5 Сверление и рассверливание отверстий
Значительное место при выполнении токарных работ занимает обработка отверстий. Различают заготовки с отверстиями, выполненными при отливке, ковке или штамповке, и заготовки без предварительно подготовленных отверстий.
Обработку отверстий в заготовках, не имеющих предварительно подготовленных отверстий, всегда начинают со сверления. Отверстия большого диаметра обычно обрабатывают двумя сверлами: сначала сверлят, принимая диаметр первого сверла равным примерно половине диаметра обрабатываемого отверстия, а затем рассверливают под необходимый размер.
Сверление и рассверливание на токарных станках в большинстве случаев служит подготовкой отверстия для последующей его обработки растачиванием или развертыванием.
Режим резания при сверлении и рассверливании на токарных станках выбирают по таблицам 3.1
и 3.2.
2.2.6 Нарезание резьбы
При нарезании резьбы на токарно-винторезных станках в ремонтных предприятиях применяют резьбовые резцы, метчики и плашки.
Нарезание наружном и внутренней резьб резцами характеризуется высокой точностью, хорошей чистотой поверхности резьбы, но малой производительностью.
Резьба образуется в результате вращения нарезаемой детали и осевого перемещения резца (продольная подача). За один оборот обрабатываемой детали резец перемещается на величину шага резьбы.
Основными элементами режима при нарезаний резьбы резцами являются скорость и число проходов. Подачу при этом выбирают по шагу резьбы.
При нарезании крепежной метрической и трапециидальной резьбы резцами из быстрорежущей стали число проходов в зависимости от шага резьбы и обрабатываемого материала выбирают по таблице 2.20
21
Таблица 2.21. Число проходов при нарезании резьбы резцами из быстрорежущей стали
Тип резьбы |
Шаг |
Наружная резьба |
Внутренняя резьба |
||||
|
резьбы |
|
|
|
|
|
|
|
обрабатываемый материал |
|
|
||||
|
|
|
|
|
|
|
|
|
|
углеродистая сталь |
легированна я сталь |
чугун, бронза, латунь |
углеродистая сталь |
легированна я сталь |
чугун, бронза, латунь |
|
|
|
|
|
|
|
|
Крепежная метрическая |
1,5 |
6 |
8 |
6 |
8 |
10 |
8 |
|
2 |
9 |
11 |
8 |
11 |
11 |
9 |
|
2,5 |
9 |
11 |
9 |
11 |
14 |
10 |
|
3 |
9 |
11 |
9 |
11 |
14 |
10 |
|
4 |
11 . |
13 |
10 |
13 |
17 |
И |
|
5 |
12 |
16 |
11 |
15 |
19 |
12 |
|
6 |
13 |
17 |
11 |
17 |
22 |
13 |
Трапецеидальная |
4 |
17 |
20 |
14 |
20 |
24 |
16 |
|
6 |
21 |
24 |
16 |
24 |
29 |
18 |
|
8 |
23 |
27 |
18 |
27 |
32 |
21 |
|
10 |
28 |
34 |
22 |
33 |
40 |
27 |
|
12 |
31 |
37 |
25 |
37 |
44 |
29 |
|
16 |
38 |
45 |
30 |
45 |
53 |
38 |
При нарезании резьбы резцами, оснащенными пластинками из твердого сплава (Т15К6 — для стали и ВК6— для чугуна), число проходов определяют по таблице 2.21.
Числа проходов, указанные в таблицах 2.20 и 2.21, даны из условий нарезания крепежной метрической резьбы по 3-му классу точности и трапецеидальной резьбы средней точности. При нарезании резьбы крепежной по 2-му классу точности и точной трапецеидальной резьбы, кроме указанного в таблице числа проходов, необходимо ввести три-четыре зачистных прохода.
Число проходов для нарезания трапецеидальной резьбы в таблицах 2.20 и 2.21 даны из расчета нарезания однозаходной резьбы. При нарезании двух- и многозаходных резьб указанные числа проходов увеличивают на один-два прохода для каждого захода.
Скорость резания выбирают в зависимости от шага резьбы, вида резьбы, обрабатываемого материала и материала режущей части резца. В таблице 2.22 приведены значения скорости резания при нарезании резьбы резцами из быстрорежущей стали, в таблице 2.23 — резцами, оснащенными пластинками из твердого сплава.
Таблица 2.21. Число проходов при нарезании резьбы резцами, оснащенными пластинками из твердого сплава
Тип резьбы |
Шаг |
Наружная резьба |
Внутренняя резьба |
||||
|
резьбы |
|
|
|
|
|
|
|
обрабатываемый материал |
|
|
||||
|
|
|
|
|
|
|
|
|
|
углеродистая сталь |
легирован ная сталь |
чугун, бронза, латунь |
углеродис тая сталь |
легирован ная сталь |
чугун, бронза, латунь |
|
|
|
|
|
|
|
|
Крепежная метрическая |
1,5 |
4 |
5 |
- |
5 |
6 |
- |
|
2 |
4 |
5 |
4 |
5 |
6 |
5 |
|
2,5 |
5 |
7 |
5 |
6 |
8 |
6 |
|
3 |
5 |
7 |
5 |
6 |
8 |
6 |
|
4 |
6 |
8 |
6 |
7 |
9 |
7 |
|
5 |
7 |
9 |
6 |
8 |
10 |
7 |
|
6 |
8 |
10 |
7 |
9 |
11 |
8 |
Трапецеидальная |
4 |
9 |
12 |
6 |
12 |
15 |
8 |
|
6 |
12 |
15 |
7 |
15 |
18 |
11 |
|
8 |
15 |
19 |
8 |
19 |
23 |
13 |
|
10 |
18 |
24 |
12 |
24 |
30 |
15 |
|
12 |
20 |
26 |
14 |
26 |
32 |
17 |
|
16 |
24 |
31 |
16 |
31 |
37 |
21 |
22
Таблица 2.22. Скорость резания (м/мин) при нарезании резьбы (резец из быстрорежущей стали Р9; с охлаждением)
|
|
|
Обрабатываемый материал |
|||
|
|
|
|
|
|
|
Тип резьбы |
Шаг |
сталь |
чугун |
|||
резьбы |
|
|
|
|
|
|
наружная |
|
внутрен- |
наружная |
внутрен- |
||
|
|
|||||
|
|
|
||||
|
|
|
|
няя |
|
няя |
|
1,5 |
8,4 |
|
6,8 |
6,8 |
5,5 |
|
2 |
8,4 |
|
6,8 |
6,8 |
5,5 |
Метрическая |
2,5 |
8,4 |
|
6,3 |
6.8 |
5,5 |
3 |
7,2 |
|
5,7 |
5,7 |
4,6 |
|
крепежная |
|
|||||
4 |
6,3 |
|
5,6 |
5,2 |
4,2 |
|
|
|
|||||
|
о |
5,6 |
|
4,5 |
4,5 |
3,6 |
|
6 |
5,2 |
|
4 |
4,0 |
3.4 |
|
4 |
17 |
|
14 |
— |
11 |
|
6 |
14 |
|
1! |
— |
9 |
Трапецеидальная |
8 |
12 |
|
10 |
— |
8 |
10 |
12 |
|
9 |
— |
7 |
|
|
|
|||||
|
12 |
11 |
|
8 |
— |
7 |
|
16 |
10 |
|
8 |
— |
б |
При нарезании резьбы на стальных деталях резцами из быстрорежущей стали нужно обязательно применять охлаждающе-смазывающую жидкость.
Таблица 2.23. Скорость резания (м/мин) при нарезании резьбы резцами, оснащенными пластинками из твердого сплава Т16К6 и ВК6 (без охлаждения)
|
|
|
Обрабатываемый материал |
|||
Тип резьбы |
Шаг |
сталь |
чугун |
|||
резьбы |
наружная |
|
Внутрен- |
наружная |
внутрен- |
|
|
|
|||||
|
|
|
|
няя |
|
няя |
|
1,5 |
34 |
|
30 |
12 |
10,6 |
|
2 |
32 |
|
28 |
12 |
10,6 |
Метрическая |
2,5 |
31 |
|
26 |
13 |
11,2 |
3 |
30 |
|
25 |
14 |
12,2 |
|
крепежная |
|
|||||
4 |
29 |
|
24 |
14 |
12,2 |
|
|
|
|||||
|
о |
29 |
|
24 |
15 |
13 |
|
6 |
63 |
|
— |
— |
21 |
|
4 |
60 |
|
— |
— |
22 |
|
6 |
58 |
|
— |
— |
23 |
Трапецеидальная |
8 |
57 |
|
— |
— |
25 |
10 |
55 |
|
— |
— |
27 |
|
|
12 |
53 |
|
— |
— |
29 |
|
16 |
52 |
|
— |
— |
31 |
|
|
51 |
|
— |
— |
33 |
При нарезании резьбы метчиками или плашками скорость резания выбирают по таблице 2.24 в зависимости от диаметра резьбы и обрабатываемого материала.
Таблица 2.24. Скорость резания (м/мин) при нарезании резьбы метчиками или плашками (с охлаждением)
Обраба- |
Режущий |
|
|
|
Диаметр резьбы не более, мм |
|
|
|||||
тывамый |
|
|
|
|
|
|
|
|
|
|
|
|
инструмент |
6 |
8 |
10 |
|
12 |
16 |
20 |
24 |
|
30 |
36 |
|
материал |
|
|
||||||||||
Сталь |
Метчик |
6,5 |
7,5 |
8,0 |
|
9,0 |
11,0 |
12,0 |
13,0 |
|
14,5 |
16,0 |
|
Плашка |
2,5 |
2,6 |
2,8 |
|
3,0 |
3,4 |
3,5 |
3,6 |
|
3,8 |
4,0 |
Чугун |
Метчик |
4,5 |
5,2 |
5,8 |
|
6,3 |
7,7 |
8,5 |
8,9 |
|
10,0 |
11,2 |
|
|
|
|
|
|
|
|
|
|
|
|
|
Процесс нарезания резьбы машинным метчиком выполняется обычно одним метчиком и в редких случаях комплектом из двух метчиков. Для нарезания наружной резьбы применяется одна плашка.
23
2.2.7 Обработка конических поверхностей
В ремонтных предприятиях наряду с цилиндрическими поверхностями обрабатывают детали в виде наружных конусов или конусных отверстий.
Для получения конических поверхностей на токарном станке могут быть применены следующие способы:
- поворотом верхней части суппорта;
-поперечным смещением корпуса задней бабки;
-при помощи конусной линейки;
-при помощи широкого резца.
При обработке конических поверхностей порядок выбора режима резания такой же, как и при продольном наружном точении и растачивании.
2.3 Расчет нормы времени
2.3.1 Расчет основного времени
После окончательного установления режима резания основное (машинное) время можно
вычислить по формуле: |
|
|||||
t |
o |
|
L i |
|
(2.4) |
|
n S |
||||||
|
|
|
где L — расчетная длина обрабатываемой поверхности с учетом врезания и перебега, мм; i — число проходов;
n — частота вращения шпинделя (детали) в мин-1; S — подача, мм/об.
Основное время при нарезании резьбы метчиками или плашками рассчитывают по формуле:
t |
o |
|
1,8 L |
(2.5) |
|
n S |
|||||
|
|
|
где 1,8 — коэффициент, которым учитывается разность скоростей прямого и обратного хода режущего инструмента.
В случае нарезания резьбы последовательно несколькими метчиками основное (машинное) время следует умножить нa число проходов (число метчиков).
Расчетную длину обрабатываемой поверхности определяет по формуле
L l y |
(2.6) |
где l — длина обрабатываемой поверхности детали, мм у — величина врезания и перебега, мм.
Длину обрабатываемой поверхности (l) в направлении подачи определяют по чертежу детали. При наружном продольном точении и растачивании l равняется длине обрабатываемой поверхности; при поперечном точении, подрезке и отрезке сплошного сечения (рис. 2.2) — половине диаметра детали, а при отрезке и подрезке торца пустотелых деталей — полуразности наружного и внутреннего диаметров. Величины врезания перебега при токарной обработке резцами приведены в таблице 2.25.
Величины врезания и перебега при нарезании резьбы метчиками и плашками приведены в таблице 2.26 (величинами врезания и перебега учтена длина заборной части).
24
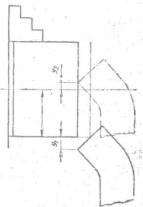
Рис. 2.1. Длина обрабатываемой поверхности при поперечном точении.
Таблица 2.25. Величина врезания и перебега при токарной обработке резцами, мм
Наименование резцов |
|
|
Глубина резания не более, мм |
|
|
|||||||
|
|
|
|
|
|
|
|
|
|
|
|
|
1 |
2 |
|
3 |
|
4 |
5 |
|
6 |
|
8 |
10 |
|
|
|
|
|
|
||||||||
|
|
|
|
|
|
|
|
|
|
|
|
|
Проходные и |
2 |
4 |
|
5 |
|
6 |
7 |
|
8 |
|
11 |
13 |
расточнын |
|
|
|
|
||||||||
|
|
|
|
|
|
|
|
|
|
|
|
|
Подрезные и отрезные |
|
|
|
|
|
от 2 до 5 |
|
|
|
|
||
Резьбовые |
|
|
|
|
2...3 шага резьбы |
|
|
|
|
Таблица 2.26. Величина врезания и перебега при нарезании резьбы метчиками и плашками
Наименование инструмента |
Шаг резьбы не более мм |
|
|
||||
|
|
|
|
|
|
|
|
|
1.5 |
2 |
2.5 |
3 |
4 |
5 |
6 |
Комплект из одного метчика |
14 |
18 |
23 |
27 |
36 |
45 |
54 |
Комплект из двух метчиков |
6 |
8 |
10 |
12 |
16 |
20 |
26 |
Плашка |
4 |
6 |
8 |
10 |
14 |
18 |
22 |
|
|
|
|
|
|
|
|
Величину врезания и перебега при сверлении и рассверливании на токарных станках следует выбирать из таблицы 3.14.
При проточке фасок и галтелей работу выполняют с ручной переменной подачей и без изменения числа оборотов предыдущего или последующего перехода. В связи с этим режимы резания при этих видах обработки не регламентируются и в нормативах на них показывают основное время.
Основное время на снятие фасок с деталей и их зацентровку приводится в таблицах 2.27 и 2.28.
Таблица 2.27. Основное время (мин) на снятие фасок под углом 45 и 30°
Диаметр |
|
|
|
|
Диаметр |
Ширина фаски |
||
обрабатывае- |
Ширина фаски не более, мм |
обрабатывае- |
||||||
не более. |
||||||||
мой |
|
|
|
|
мой |
|||
|
|
|
|
|
|
|||
детали не |
|
|
|
|
детали не |
|
|
|
1 |
2 |
3 |
5 |
3 |
5 |
|||
более, мм |
более, мм |
|||||||
|
|
|
|
|
|
|||
20 |
0,05 |
0,10 |
0,13 |
— |
180 |
0,94 |
1,20 |
|
40 |
0,10 |
0,23 |
0,27 |
— |
200 |
— |
1,28 |
|
60 |
0,14 |
0,27 |
0,36 |
0,50 |
210 |
— |
1,36 |
|
80 |
0,16 |
0,36 |
0,48 |
0,70 |
220 |
_ |
1,42 |
|
100 |
— |
0,48 |
0,60 |
0,80 |
240 |
— |
1,51 |
|
120 |
— |
0,58 |
0,68 |
0,87 |
260 |
__ |
1,65 |
|
140 |
— |
0,62 |
0,75 |
1,00 |
280 |
— |
1,84 |
|
160 |
— |
— |
0,82 |
1,13 |
300 |
— |
2,00 |
Таблица 2.28. Основное время на зацентровку деталей
Диаметр обрабатываемой |
10 |
40 |
80 |
120 |
180 |
детали не более, мм |
|
|
|
|
|
|
|
|
|
|
|
Диаметр сверла, мм |
2 |
3 |
4 |
5 |
6 |
Глубина сверления, мм |
5 |
7 |
10 |
13 |
15 |
Время, мин |
0,07 |
0,08 |
0,09 |
0,10 |
0,13 |
25
2.3.2 Выбор вспомогательного, дополнительного и подготовительно-заключительного времени
Вспомогательное время при токарной обработке (как и при выполнении всех видов работ на металлорежущих станках) бывает двух видов: вспомогательное время на установку и снятие детали и вспомогательное время, связанное с проходом.
Необходимо отметить, что выбор режима резания и расчет основного времени при выполнении работ на металлорежущих станках не зависят от того, для какого типа производства они рассчитываются, будь то единичное и мелкосерийное или серийное производство.
Единичное и мелкосерийное производство характеризуется широкой номенклатурой изделий и малым количеством деталей в партии. Технология обработки деталей обусловливается применением универсальных инструментов и приспособлений, выполнением работы по образцу или по месту, а также тем, что инструмент на заданный размер устанавливают на каждую деталь путем пробных стружек и оборудование по существу налаживают при обработке каждой детали.
Всерийном производстве технология обработки деталей на металлорежущих станках характеризуется тем, что в большинстве случаев обработку проводят на станках, настроенных на первых двух-трех деталях, с использованием наряду с универсальными, более производительных приспособлений.
При этом инструмент на размер устанавливают по упорам или лимбам, а в некоторых случаях при помощи копиров или других специальны устройств. Уменьшается время на наладку станка путем использования времени, затраченного при предшествующих наладках для обработки последующих деталей.
Вкомплекс приемов, связанных с установкой и снятием делали, включено время на установку, выверку, крепление и снятие детали. Продолжительность вспомогательного времени, связанного с установкой, определяют с учетом веса детали, типа приспособления (способа, установки детали), наличия и степени сложности выверки.
Вспомогательное время на установку и снятие детали для условий ремонтных мастерских общего назначения (единичное и мелкосерийное производство) приведено в таблице 2.29, для специализированных ремонтных предприятий и заводов (серийное производство) — в таблице 2.32.
Вкомплекс приемов, связанных с проходом, включены затраты времени на установку оборотов и подач, включение и выключение вращения шпинделя и подач, взятие пробных стружек, обмеры детали, подвод и отвод резца, поворот резцедержателя, перемещение и крепление задней бабки.
Вспомогательное время, связанное с проходом, для мастерских общего назначения приведено в таблице 2.30, для специализированных ремонтных предприятий и заводов — в таблице 2.33.
Затраты вспомогательного времени, связанного с проходом, в основном зависят от размеров станка, что и учтено в таблицах.
Дополнительное время (время на техническое и организационное обслуживание рабочего места
иестественные надобности [подробно см. раздел 1]) определяют по формуле:
|
|
|
|
|
|
|
|
|
|
|
|
|
|
|
|
|
|
' |
|
|
|
|
|
|
|
|
|
|
|
|
|
|
|
|
|
|
|
' |
|
|
t |
доп |
t |
об |
t |
ф |
t |
Т.об |
t |
о.об |
t |
ф |
t |
о |
t |
в |
|
|
|
t |
о |
t |
в |
|
|
|
t |
о |
t |
в |
|
|
|
t |
о |
t |
в |
|
|
|
(2.7) |
|
|
|
|
|
|
|
||||||||||||||||||||||||||||||||||
|
|
|
|
|
|
|
|
|
100 |
|
|
|
100 |
|
|
|
100 |
|
|
|
100 |
|
|
|||||||||||||||||
|
|
|
|
|
|
|
|
|
|
|
|
|
|
|
|
|
|
|
|
|
|
|
|
|
|
|
|
|
|
|
|
|
|
Затраты подготовительно-заключительного времени в таблице 2.31 даны для условий единичного производства в зависимости от сложности выполняемой работы и размера станка. Степень сложности работы характеризуется количеством участвующих в работе инструментов, необходимостью смены крепежного приспособления.
Для условий серийного производства затраты подготовительно-заключительного времени приведены в таблице 2.34 в зависимости от условий работы и типа станка.
В данных таблицы учтена более тщательная настройка оборудования на изготовление крупных партий детали, чем при единичном производстве, включено время на пробную обработку деталей.
Подготовительно-заключительное время устанавливают на обработку партии одинаковых деталей, и как указывалось, оно не зависит от количества деталей в партии.
26
Таблица 2.29. Вспомогательное время на установку и снятие детали, мин (для мастерских общего назначения)
Способ установки детали |
Степень выверки |
Вес детали нe более, кг |
||||
|
|
|
|
|||
3 |
8 |
10 |
свыше |
|||
|
|
10 |
||||
|
|
|
|
|
||
В центрах с хомутиком |
- |
0,3 |
0,4 |
0,5 |
0,6 |
|
В трехкулачковом |
Простая |
0,6 |
0,7 |
0,8 |
0,9 |
|
патроне |
Сложная |
1,2 |
1,4 |
1,7 |
2,2 |
|
В центрах с люнетом |
- |
0,6 |
0,7 |
0,8 |
0,9 |
|
В четырехкулаччовом |
Простая |
1,4 |
1,7 |
2,0 |
2,4 |
|
Средней сложности |
2,0 |
2,4 |
2,7 |
3,2. |
||
патроне |
||||||
Сложная |
2,8 |
3,8 |
4.2 |
5,5 |
||
|
||||||
На планшайбе |
Простая |
2.0 |
2,4 |
2,7 |
3,2 |
|
Средней сложности |
2,6 |
2,8 |
3,2 |
4,0 |
||
|
Сложная |
3,5 |
4,5 |
6,0 |
7,5 |
Таблица 2.30. Вспомогательное время, связанное с проходом, мин (для мастерских общего назначения)
|
|
|
|
|
Высота центров, мм |
||
|
|
|
|
|
|||
Наименование операции (перехода) |
150 |
|
200 |
300 |
|||
|
|
|
|
|
|
|
|
|
|
|
|
время, мин на один проход |
|||
|
|
|
|
|
|
|
|
Обточка |
или |
расточка |
по 3-му классу |
0,7 |
|
0,8 |
1,0 |
точности |
|
|
|
|
|||
|
|
|
|
|
|
|
|
Обточка |
или |
расточка |
по 4-5-му классу |
0,4 |
|
0.5 |
0,7 |
точности |
|
|
|
|
|||
|
|
|
|
|
|
|
|
Обточка |
или |
расточка |
на последующие |
0,1 |
|
0,2. |
0,3 |
проходы |
|
|
|
|
|||
|
|
|
|
|
|
|
|
Подрезка или отрезка |
|
0,1 |
|
0,2 |
0,2 |
||
Снятие фасок и радиусов |
|
0,06 |
|
0,07 |
0,08 |
||
Нарезание резьбы резцом |
|
0.03 |
|
0,04 |
0,06 |
||
Нарезание резьбы метчиком или плашкой |
0,2 |
|
0,2 |
0,2 |
|||
Сверление и центровка |
|
0,5 |
|
0,6 |
0,9 |
Таблица 2.31. Подготовительно-заключительное время при токарной обработке, мин (для условий мастерских общего назначения)
Сложность работы |
Высота центров, мм |
||
200 |
300 |
||
|
|||
Простая работа (болты, гайки, втулки) |
5 |
6 |
|
Работа средней сложности (валики, фланцы) |
10 |
11 |
|
Сложная работа (корпусные детали) |
14 |
16 |
|
|
|
|
Таблица 2.32. Вспомогательное время на установку и снятие детали, мин (для специализированных ремонтных предприятий и заводов)
Способ установки детали |
Степень |
|
Вес детали не более, кг |
|||
выверки |
3 |
|
5 |
10 |
свыше |
|
|
|
|||||
|
|
|
|
|
|
10 |
В центрах |
|
0,25 |
|
0,30 |
0,36 |
0,46 |
В центрах с люнетом |
— |
0,42 |
|
0,46 |
0,55 |
0,7 |
|
Простая |
0,19 |
|
0,22 |
0,32 |
0,39 |
|
|
|
||||
В самоцентрирующем патроне |
Средней |
|
|
|
|
|
0,44 |
|
0,50 |
0,70 |
0,9 |
||
|
сложности |
|
||||
|
|
|
|
|
|
|
|
Сложная |
1,20 |
|
1,30 |
1,80 |
2,2 |
В самоцентрирующем |
Без люнета |
0,35 |
|
0,40 |
0,48 |
0,6 |
патроне с поджатием |
|
|
|
|
|
|
С люнетом |
0,55 |
|
0,60 |
0,70 |
0,8 |
|
задним центром |
|
|||||
В цанговом патроне |
- |
0,40 |
|
0,47 |
0,50 |
— |
В четырехкулачковом |
Простая |
0,45 |
|
0,50 |
0,60 |
0,7 |
Средней |
1,15 |
|
1,25 |
1,60 |
2,1 i |
|
патроне |
сложности |
|
||||
|
|
|
|
|
||
|
Сложная |
2,50 |
|
2,80 |
3,40 |
4,0 |
В четырехкулачковом патроне с |
— |
— |
|
— |
1,70 |
1,9 |
поджатием задним центром |
|
|||||
|
|
|
|
|
|
|
|
|
|
|
|
|
|
На гладкой или шлицевой оправке |
— |
0,30 |
|
0,36 |
0,44 |
0,5 |
|
|
|
|
|
|
|
На разжимной оправке |
— |
0,48 |
|
0,50 |
0,65 |
0,7 |
|
|
|
|
|
|
|
27
Таблица 2.33. Вспомогательное время, связанное с проходом, мин (для специализированных ремонтных предприятий и заводов).
|
|
Высота центров, мм |
||
Наименование операции (перехода) |
|
|
|
|
150 |
|
200 |
300 |
|
|
|
|
|
|
|
время, мин (на один проход) |
|||
|
|
|
|
|
Обточка или расточка по 3-му классу |
0,5 |
|
0,6 |
0,8 |
точности |
|
|||
|
|
|
|
|
Обточка или расточка по 4—5-му |
0,3 |
|
0,4 |
0,6 |
классу точности |
|
|||
|
|
|
|
|
Обточка или расточка на последующие |
0,08 |
|
0,15 |
0,20 |
проходы |
|
|
|
|
Подрезка или отрезка |
0,10 |
|
0,15 |
0,18 |
Обтачивание фасок и радиусов |
0,05 |
|
0,06 |
0,06 |
Нарезание резьбы резцом |
0,02 |
|
0,03 |
0,05 |
Нарезание резьбы метчиком или плашкой |
0,17 |
|
0,19 |
0,22 |
|
|
|
|
|
Сверление, рассверливание и центровка |
0,46 |
|
0,62 |
0,80 |
Таблица 3.34. Подготовительно-заключительное время при токарной обработке, мин (для условий специализированных ремонтных предприятий).
Условия работы |
Высота центров, мм |
|
|
|
|
|
|
|
150 |
200 |
300 |
В центрах на оправке с хомутиком |
8 |
9 |
12 |
В трехкулачховом патроне |
11 |
12 |
13 |
В трехкулачковом патроне с поджатием |
12 |
13 |
14 |
задним центром |
|
|
|
В четырехкулачковом патроне |
13 |
14 |
16 |
В четырехкулачковом патроне с поджатием |
14 |
15 |
17 |
задним центром |
|
|
|
На планшайбе с креплением болтами |
l5 |
16 |
18 |
На приспособлений, закрепленном |
17 |
18 |
21 |
на планшайбе |
|
|
|
На концевой оправке |
10 |
11 |
12 |
Прибавлять время в случае: |
|
|
|
- установки люнета |
2 |
3 |
4 |
- установки приспособления на суппорте |
20 |
20 |
23 |
|
|
|
|
- установке электрошлифовального прибора |
15 |
15 |
15 |
|
|
|
|
28
3 РАСЧЕТ РЕЖИМОВ РЕЗАНИЯ И НОРМЫ ВРЕМЕНИ ПРИ СВЕРЛИЛЬНЫХ РАБОТАХ
3.1 Общие сведения
Сверлильные станки широко применяют в ремонтных предприятиях. Конструкция сверлильных станков, их габариты и устройство обусловливаются назначением. Для сверления небольших отверстий используют сверлильные станки настольного типа. Для более крупных и разнообразных по характеру сверлильных работ применяют вертикально-сверлильные станки больших габаритов и большей мощности.
При обработке крупных и тяжелых деталей во избежание перемещения их при последовательной обработке нескольких отверстий, расположенных в одной плоскости, используют радиально сверлильные станки с поворачивающимся вокруг колонки рукавом и перемещающейся вдоль рукава сверлильной головкой.
При массово-поточном производстве для выполнения ограниченного количества технологических операций применяют специализированные сверлильные станки. В приложении 1 приведены основные характеристики вертикально-сверлильных и радиально-сверлильных станков.
Область применения сверлильных станков не ограничивается операцией сверления отверстий. На них, особенно на универсальных станках, можно проводить дальнейшую обработку отверстий, а также ряд других технологических операций, не связанных с непосредственной обработкой отверстии.
На современных сверлильных станках могут быть выполнены следующие работы:
-сверление глухих и сквозных отверстий;
-рассверливание отверстий;
-зенкование отверстий;
-растачивание предварительно просверленных отверстий резцом, установленным на шпинделе;
-развертывание цилиндрических и конических отверстий, применяемое для получения необходимой точности и чистоты поверхности.
Впроцессе образования отверстий на сверлильных станках сверло совершает вращательное (главное) и поступательное (движение подачи) движения (при сверлении на токарных станках главное движение выполняет деталь, закрепленная в шпинделе станка, а движение подачи — сверло, закрепленное в задней бабке).
При этом режущие кромки сверла срезают тонкие слои металла у неподвижно закрепленной детали, образуя стружку, которая, завиваясь и скользя по спиральным канавкам сперла, выходит из обрабатываемого отверстия.
Сверло по сравнению с другими режущими инструментами работает в более тяжелых условиях, так как затрудняется отвод стружки и подвод охлаждающе-смазывающей жидкости.
Так, в отличие от резца сверло является не однолезвийным, а многолезвийным режущим инструментом. В процессе резания при сверлении участвуют не только два главных лезвия, но и лезвие перемычки, а также два вспомогательных лезвия, находящихся на направляющих ленточках сверла, что весьма усложняет процесс образования стружки.
Вначале обработки передняя поверхность сверла сжимает прилегающие к ней частицы металла. Затем, когда давление, создаваемое сверлом, становится большим, чем силы сцепления частиц металла, происходит отделение их от обрабатываемой поверхности и образование элементов стружки.
Наибольшее сопротивление резанию при сверлении обычно оказывает перемычка (поперечная кромка) сверла, которая увеличивается с увеличением его диаметра. Поэтому отверстия больших диаметров рекомендуется сверлить сверлом малого диаметра, а затем рассверливать их под заданный размер. В этом случае перемычка сверла не принимает участия в работе, в результате улучшаются условия резания. Например, отверстие диаметром 30 мм следует сначала сверлить сверлом 10...15мм, а затем рассверлить до окончательного размера.
Однако рассверливание отверстий с малым припуском (порядка 0,5—1 мм) не только невыгодно, но подчас и невозможно, так как направляющие ленточки сверла вблизи режущих кромок очень быстро изнашиваются, сверло начинает заклиниваться и может сломаться.
Производительность сверления в значительной степени зависит от правильности заточки сверла.
29
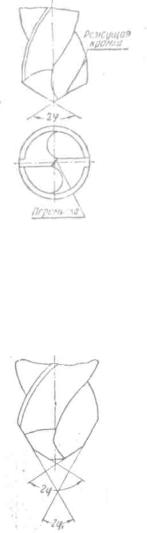
Так, угол при вершине сверла 2φ (рис. 3.1) для сверления чугуна и твердой бронзы принимают равным 116—118°, для твердых и хрупких материалов — 130—140°, для мягких и вязких материалов — 80— 90°.
Pис. 3.1. Основные элементы сверла.
Широко применяется подточка перемычки, что облегчает врезание сверла в металл; в результате этого скорость резания повышается на 10—15%.
Двойная заточка сверла (рис. 3.2) также дает возможность увеличить скорость резания в среднем на 15—25%. Это объясняется тем, что режущая кромка становится длиннее, улучшается отвод тепла и уменьшается удельная нагрузка на режущие кромки.
Рис. 3.2. Сверло с двойной заточкой.
Подточка направляющей ленточки снижает трение, что уменьшает ее износ на границе с режущей кромкой.
3.2 Выбор режима резания
Основными элементами режима резания при сверлении являются глубина, подача и скорость резания.
Глубиной резания при сверлении в сплошном материале считается половина диаметра сверла:
t |
Dсв |
(3.1) |
|
||
2 |
|
При рассверливании глубину резания определяют по формуле:
t |
Dсв d |
(3.2) |
|
||
2 |
|
где DCВ— диаметр окончательно рассверленного отверстия (сверла), мм; d — диаметр рассверливаемого отверстия, мм.
30