
SPR / Лекция_1
.pdf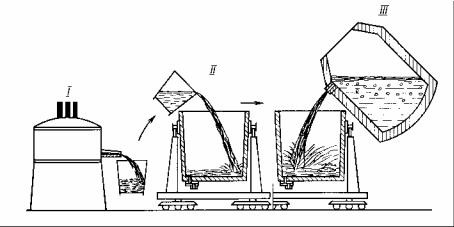
7
1 СОВРЕМЕННЫЕ ТЕХНОЛОГИИ ПРОИЗВОДСТВА СТАЛИ РАЗЛИЧНОГО НАЗНАЧЕНИЯ
Во второй половине ХХ-го столетия получили широкое распространение технологии внепечного рафинирования металла, которые позволили сущест-
венно повысить производительность сталеплавильных агрегатов и качество стали.
1.1 Внепечное рафинирование стали без использования вакуума
На отечественных металлургических предприятиях широкое промыш-
ленное использование синтетических шлаков для десульфурации стали в ков-
шах было начато в конце 50-х годов. Схема технологического процесса пред-
ставлена на рисунке 1.1.
Рисунок 1.1 – Технологическая схема обработки стали жидкими синтетически-
ми шлаками: I – дуговая электропечь для выплавки синтетического шлака; II –
заливка синтетического шлака в сталеразливочный ковш; III – выпуск стали
Выплавленный в электропечах синтетический шлак в количестве 3 – 6%
от массы стали заливают в сталеразливочный ковш, а затем в этот же ковш вы-
пускают сталь, рафинированную до заданного содержания углерода и фосфора и нагретую до необходимой температуры.
Первоначально для внепечной десульфурации стали были разработаны
8
известково-глиноземистые шлаки состава, % мас.: 50 – 55 CaO, 37 – 43 Al2O3, ≤ 7 SiO2, ≤ 7 MgO, ≤ 0,5 FeO, для выплавки которых требовались дефицитные шихтовые материалы с низким содержанием кремнезема. Впоследствии была показана возможность эффективной десульфурации стали известково-
шамотными шлаками состава, % мас.: 48 – 56 CaO, 6 – 10 MgO, 18 – 22 SiO2, 12
– 16 Al2O3, 0,5 CaF2, ≤ 0,5 FeO.
Широкое использование синтетических шлаков сдерживалось отсутстви-
ем возможности размещения в существующих сталеплавильных цехах обору-
дования для их выплавки. В связи с этим была разработана технология десуль-
фурации стали в ковше самоплавкими шлаковыми смесями состава, % мас.: 12
– 14 алюминиевый порошок или алюминиевая стружка; 21 – 24 натриевая се-
литра; 20 – флюоритовый концентрат; известь – остальное. Необходимое коли-
чество самоплавкой шлаковой смеси загружали в чугуновозный ковш и поджи-
гали. Полученный таким способом жидкий шлак переливали из чугуновозного ковша в сталеразливочный и подавали под выпуск.
Использование самоплавких шлаковых смесей существенно упростило технологию получения синтетических шлаков. Однако, после нескольких круп-
ных пожаров в отделениях подготовки смесей металлургические предприятия
СССР от их использования отказались.
В настоящее время для внепечной десульфурации стали успешно исполь-
зуют твердые шлакообразующие смеси из 10 – 30% плавикового шпата и извес-
ти, а также смеси извести с плавиковым шпатом и глиноземом. По ходу выпус-
ка плавки смесь вместе с раскислителями и легирующими загружают в ковш,
при этом плавление смеси обычно завершается в течение 1 – 2 минут.
Особенность этой технологии заключается в том, что формирование шла-
ка завершается при наполнении второй половины ковша, когда мощность пере-
мешивания стали и шлака падающей в ковш струей металла значительно уменьшается. В связи с этим десульфурирующая способность шлака использу-
ется не полностью. Поэтому после выпуска плавки целесообразно проводить дополнительное перемешивание шлака и металла продувкой в ковше аргоном.
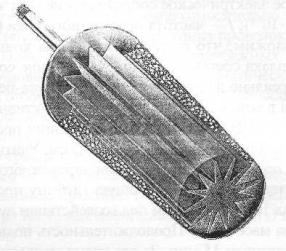
9
Широкое использование в металлургии аргона было начато в начале 60-х
годов. Продувку металла аргоном использовали для усреднения химического состава и температуры стали в объеме ковша, удаления неметаллических вклю-
чений, перемешивания металла с рафинирующим ковшевым шлаком.
В промышленных условиях были опробованы следующие способы про-
дувки металла аргоном: через пористые огнеупорные вставки в днище ковша;
через ложный стопор, который заканчивался огнеупорной пробкой с радиально расположенными отверстиями диаметром 0,5 – 1,0 мм; через футерованную фурму, опускаемую в металл сверху; через фурму, установленную в разливоч-
ном канале шиберного затвора.
Наибольшее распространение получили способы продувки снизу через пористую огнеупорную пробку, имеющую открытую пористость в пределах 25
– 40%, и сверху через футерованную фурму. В последние годы для продувки снизу широко используют огнеупорные блоки с направленной пористостью (в
теле огнеупора выполнены вертикальные каналы для прохождения газа диа-
метром 0,6 – 1 мм), щелевые, звездообразные (рисунок 1.2) и др.
Рисунок 1.2 – Звездообразная продувочная пробка фирмы Radex
Продувочные пробки изготавливают из качественных высокоглиноземи-
стых или основных огнеупоров – из каждого в отдельности или в разных соче-
таниях. Известно, например, использование пробок, в которых зона контакта с металлом выполнена из магнезита, а нижняя часть – из глинозема.
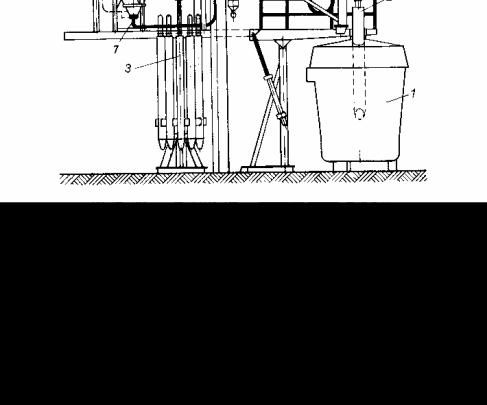
10
Для футеровки фурм обычно используют алюмосиликатные и высоко-
глиноземистые материалы, содержащие свыше 75% глинозема. В некоторых случаях используют комбинированную футеровку фурм: в зоне шлакового поя-
са устанавливают циркониевые огнеупоры, остальное – алюмосиликатные или высокоглиноземистые.
Аргон также широко использовали для инжектирования в металл порош-
кообразных материалов с целью раскисления, науглероживания, легирования,
десульфурации и дефосфорации стали. Схема установки для обработки металла порошкообразными материалами в ковше показана на рисунке 1.3.
Рисунок 1.3 – Схема установки для вдувания в металл порошкообразных мате-
риалов: 1 – ковш, накрытый крышкой; 2 – фурма; 3 – карусельная установка с запасными фурмами; 4 – расходный бункер; 5 – накопительные бункера; 6 –
пылеулавливающая установка; 7 – трубопроводы для подачи порошков от рас-
ходного бункера к фурме
Наиболее широкое распространение получили технологии внепечной де-
сульфурации стали продувкой порошкообразной известью, а также смесями из-
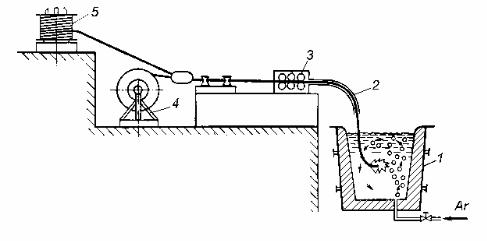
11
вести с плавиковым шпатом, алюминием, магнием и др. В 70-х годах получила широкое распространение технология внепечной десульфурации стали с ис-
пользованием продувки сплавами и соединениями кальция (карбида кальция,
силикокальция и др.).
В конце 70-х годов была разработана технология ввода порошкообразных материалов в металл с использованием порошковой проволоки, широкое при-
менение которой на отечественных предприятиях началось в 90-е годы. Схема оборудования для подачи порошковой проволоки в металл показана на рисунке
1.4.
Рисунок 1.4 – Схема ввода порошковой проволоки в сталеразливочный ковш: 1 – ковш; 2 – направляющая труба; 3 – трайб-аппарат; 4 – разматывающее уст-
ройство; 5 – бухта порошковой проволоки
В связи с увеличением объемов стали, разливаемой на МНЛЗ методом
«плавка на плавку», получили распространение установки комплексной довод-
ки стали в ковше (УДМ, LTS), которые позволяют выполнять широкий круг операций доводки металла по температуре и химическому составу, модифици-
рованию и микролегированию с использованием кусковых и порошкообразных материалов. Примером может служить УДМ в 350-т ковшах кислородно-
конвертерного цеха комбината «Азовсталь», схема которой показана на рисун-
ке 1.5.
Последовательное выполнение большого количества операций по довод-
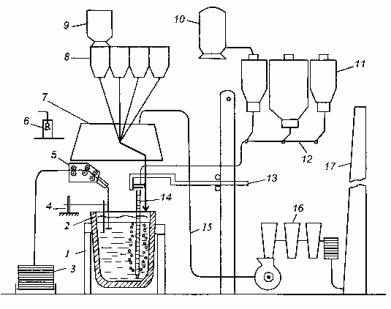
12
Рисунок 1.5 – Принципиальная схема размещения оборудования УДМ кисло-
родно-конвертерного цеха комбината «Азовсталь»:
1 – стенд; 2 – ковш; 3 – бухта алюминиевой катанки или порошковой проволо-
ки; 4 – манипулятор для отбора проб металла; 5 – трайб-аппарат; 6 – пневмо-
почта; 7 – вытяжной зонт; 8 – система бункеров-дозаторов; 9 – бадья для куско-
вых материалов; 10 – контейнер для порошков; 11 – пневматический питатель; 12 – трубопровод с переключателями потоков; 13 – подъемник фурмы; 14 –
фурма; 15 – отвод отходящих газов; 16 – газоочистка; 17 – дымовая труба
ке стали в ковше требует значительного повышения температуры металла на выпуске из сталеплавильного агрегата, что приводит к росту потерь металла,
ухудшению условий дефосфорации стали в заключительном периоде плавки,
повышению окисленности шлака и снижению стойкости футеровки сталепла-
вильного агрегата, высокой окисленности металла на выпуске, которая вызыва-
ла повышенный угар раскислителей и легирующих добавок и нестабильное их усвоение, и др.
Чтобы избежать чрезмерного перегрева стали на выпуске из сталепла-
вильного агрегата необходимо оборудование, которое позволяет осуществлять периодический нагрев металла в ковше. С этой целью в конце 60-х годов был разработан процесс ASEA-SKF, схема которого представлена на рисунке 1.6.
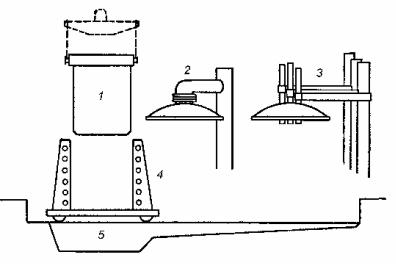
13
Рисунок 1.6 – Схема установки ASEA-SKF:
1 – ковш; 2 – участок вакуумирования; 3 – участок нагрева; 4 – металловоз с индуктором; 5 – аварийная яма
Предназначенный для рафинирования металл выпускают в ковш, кожух которого изготовлен из аустенитной (немагнитной) нержавеющей стали. Ковш имеет опорное кольцо для соединения со съемной вакуумплотной крышкой, со-
единенной с системой вакуумных насосов. При нагреве металла крышка заме-
няется сводом с тремя электродами. Как во время вакуумирования, так и при нагреве, металл в ковше перемешивается специальным индуктором системы электромагнитного перемешивания, расположенным снаружи ковша. Система подачи ферросплавов включала автоматическое взвешивающее устройство и 9
бункеров для легирующих и других добавок. Весовая чаша перемещалась вдоль бункеров. В нее набирали необходимые материалы и подавали их на ленточный конвейер для последующей подачи в металл через крышку ковша на нагрева-
тельном или вакуумном стенде.
Вначале 70-х годов оборудование для рафинирования и нагрева металла
вковше существенно упростили путем отказа от вакуумного оборудования и замены системы электромагнитного перемешивания продувкой металла арго-
ном. Таким образом появились получившие широкое распространение установ-
ки ковш-печь (УКП, LF), которые позволяют вести нагрев металла со скоро-
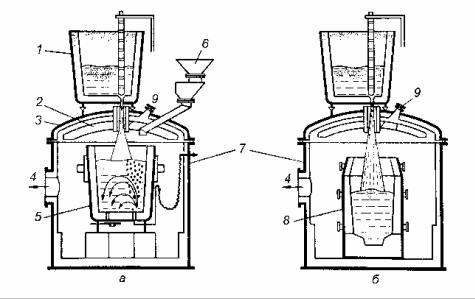
14
стью до 3 – 5оС/мин.
В конце 70-х годов были также разработаны технологии химического на-
грева металла за счет тепла, выделяющегося при окислении введенного в рас-
плав алюминия газообразным кислородом (процессы CAS-OB, IR-UT и др.).
Устройства такого типа позволяют увеличить скорость нагрева до 10 –
15оС/мин.
1.2 Внепечное вакуумирование стали
Патент на способ вакуумирования струи металла при переливе его в ус-
тановленные в вакуумной камере ковш или изложницу (рисунок 1.7) получен в
1938 г. Первые сообщения об успешной промышленной эксплуатации его отно-
сятся к 1954 г.
Рисунок 1.7 – Схема процесса вакуумирования стали при переливе:
а – из ковша в ковш; б – при отливке слитков; 1 – первый сталеразливочный ковш; 2 – защитный экран; 3 – крышка вакуумной камеры; 4 – вакуумпровод к вакуумным насосам; 5 – второй сталеразливочный ковш; 6 – бункер для рас-
кислителей и легирующих; 7 – вакуумная камера; 8 – изложница; 9 – гляделка
К 1980 г. было построено более 60 таких установок, опыт эксплуатации
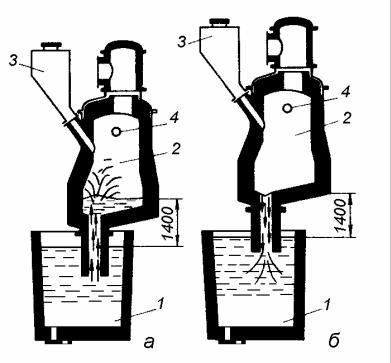
15
которых выявил ряд существенных недостатков этого способа обработки: вы-
сокие потери температуры, отсутствие возможности ввода легирующих и др.
Поэтому в настоящее время такое оборудование используется главным образом при отливке крупных кузнечных слитков.
В 1954 г. была построена первая установка порционного вакуумирования металла (DH-процесс), схема которого показана на рисунке 1.8.
Рисунок 1.8 – Схема процесса порционного вакуумирования стали:
а – камера в нижнем положении; б – камера в верхнем положении; 1 – ковш; 2 –
вакуумная камера; 3 – бункер для ввода раскислителей и легирующих; 4 – гра-
фитовый электрод для нагрева футеровки камеры
Этот процесс предусматривает вакуумную обработку порции металла в камере, к нижней части которой крепится футерованный патрубок. После по-
гружения патрубка на заданную глубину в ковш с металлом давление в камере понижают. При этом за счет разности давлений над поверхностью металла в ковше и внутри вакуумной камеры уровень металла в камере повышается при-
мерно на 1,4 м, в результате чего в камеру поступает порция металла. После этого камера перемещается вверх примерно на 0,5 м. Металл из вакуумной ка-
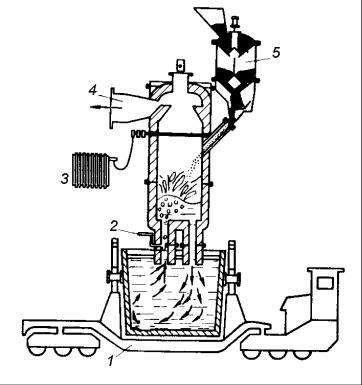
16
меры возвращается в объем ковша, после чего камера снова перемещается вниз,
заполняясь металлом. Обычно выполняется 40 – 100 циклов вакуумирования,
продолжительность каждого из которых составляет 15 – 30 с.
В 1959 г. была пущена в эксплуатацию первая установка циркуляционно-
го вакуумирования металла (RH-процесс), схема которого показана на рисунке
1.9.
Рисунок 1.9 – Схема процесса циркуляционного вакуумирования стали:
1 – тележка; 2 – подача транспортирующего газа; 3 – трансформатор; 4 – ваку-
умпровод к вакуумным насосам; 5 – бункер для раскислителей и легирующих
Камера установки циркуляционного вакуумирования оборудована двумя погружаемыми в металл патрубками, в один из которых непрерывно подается аргон. Это вызывает циркуляцию металла из ковша в вакуумную камеру и об-
ратно в ковш.
Первые исследования вакуумирования металла в камере (VD-процесс)
были выполнены в Германии в 1932 – 1935 г.г. Однако, техника того времени не позволяла понизить давление в камере ниже 4 – 7 кПа. В этих условиях зна-
чительной дегазации металла не наблюдалось.