
SPR / Лекция_1
.pdf
17
Первые промышленные установки для вакуумирования металла в камере
(рисунок 1.10) были введены в эксплуатацию в начале 50-х годов.
Рисунок 1.10– Схема процесса вакууми-
рования стали в камере:
1 – вакуумная камера; 2 – вакуумпровод к вакуумным насосам; 3 – крышка ваку-
умной камеры; 4 – бункер для ввода раскислителей и легирующих; 5 – уст-
ройство для отбора проб металла и за-
мера температуры; 6 – гляделка; 7 – за-
щитный экран; 8 – сталеразливочный ковш; 9 – подача аргона
В 50-х – 60-х годах широкому распространению порционного вакуумиро-
вания способствовали такие его преимущества, как отсутствие потребности в аргоне и наличие лишь одного погружаемого в металл патрубка, который мож-
но было расположить в стороне от стопорного устройства сталеразливочного ковша. Однако, со временем они потеряли свое значение по мере роста доступ-
ности аргона и перехода к использованию ковшей с шиберными затворами.
Кроме того, эффективная дегазация металла в камерах порционного вакууми-
рования достигалась только при обработке кипящей и полуспокойной стали. По мере ужесточения требований к содержанию серы в стали для повышения эф-
фективности десульфурации началось широкое использование раскисления стали алюминием. В этих условиях эффективная дегазация металла в камерах порционного вакуумирования достигалась только при подаче в патрубок арго-
на.
Поэтому из более чем 100 установок такого типа, построенных в 20 стра-
18
нах мира к 1984 г., к 2002 г. в эксплуатации оставалось лишь 11.
В настоящее время установки циркуляционного вакуумирования эксплуа-
тируются преимущественно в кислородно-конвертерных цехах. К их преиму-
ществам можно отнести прежде всего малую длительность обработки, а также высокое усвоение легирующих при подаче их в вакууме на свободную от шлака поверхность металла и отсутствие необходимости в большой высоте свободно-
го борта ковша, которая требуется при обработке металла в камере.
Вакуумирование металла в камерах обычно используется в электростале-
плавильных цехах.
Для производства стали с низким и ультранизким содержанием углерода установки вакуумирования были оснащены оборудованием для продувки ме-
талла кислородом в вакууме (процессы VD-OB, RH-KTB и др.). Это позволило использовать их также и для химического нагрева обрабатываемого металла.
Известны также способы вакуумирования стали в ковше с одновремен-
ным электродуговым нагревом. Примером может служить показанный на ри-
сунке 1.11 способ VAD.
1.3Организация производства стали различного назначения в современных сталеплавильных цехах
Современные способы внепечной обработки стали позволяют решать следующие задачи:
∙выравнивание химического состава и температуры стали в объеме ковша;
∙корректировка химического состава стали подачей ферросплавов в строго заданных количествах;
∙удаление водорода, азота и, если требуется, углерода;
∙десульфурация металла;
∙получение температуры направляемого на разливку металла на опти-
мальном уровне;
∙высокая чистота стали по оксидным и сульфидным включениям;
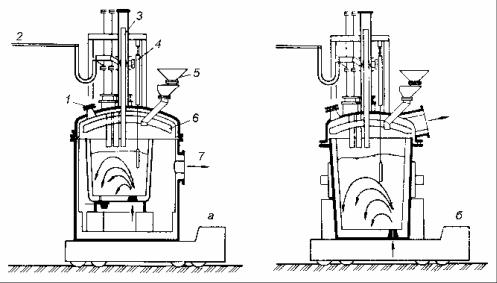
19
∙ получение металла с постоянными свойствами от плавки к плавке;
Рисунок 1.11 – Схемы установок VAD, размещенных на тележке:
а – размещение ковша в отдельной вакуумной камере; б – дегазация и нагрев металла непосредственно в сталеразливочном ковше; 1 – гляделка; 2 – подвод тока; 3 – графитовые электроды, установленные вакуумплотно; 4 - пробоотбор-
ник; 5 – бункер для подачи раскислителей и легирующих; 6 – защитный экран; 7 – вакуумпровод к вакуумному насосу
∙корректировка химического состава ковшевого шлака;
∙изменение состава и формы неметаллических включений в стали;
∙удаление примесей цветных металлов;
∙повышение производительности сталеплавильных агрегатов и улучшение технико-экономических показателей их работы.
В связи с этим в современных кислородно-конвертерных и электростале-
плавильных цехах в основных сталеплавильных агрегатах выплавляют базовый расплав (полупродукт), содержащий 0,04 – 0,08% углерода, необходимую кон-
центрацию фосфора и нагретый до заданной температуры. При этом необходи-
мое содержание цветных металлов обычно обеспечивается использованием в шихте металлизованного сырья и чугуна. Доводка базового расплава по хими-
ческому составу и температуре выполняется в ковше.
Основные рекомендации по организации производства стали различного
20
назначения представлены в таблице 1.1.
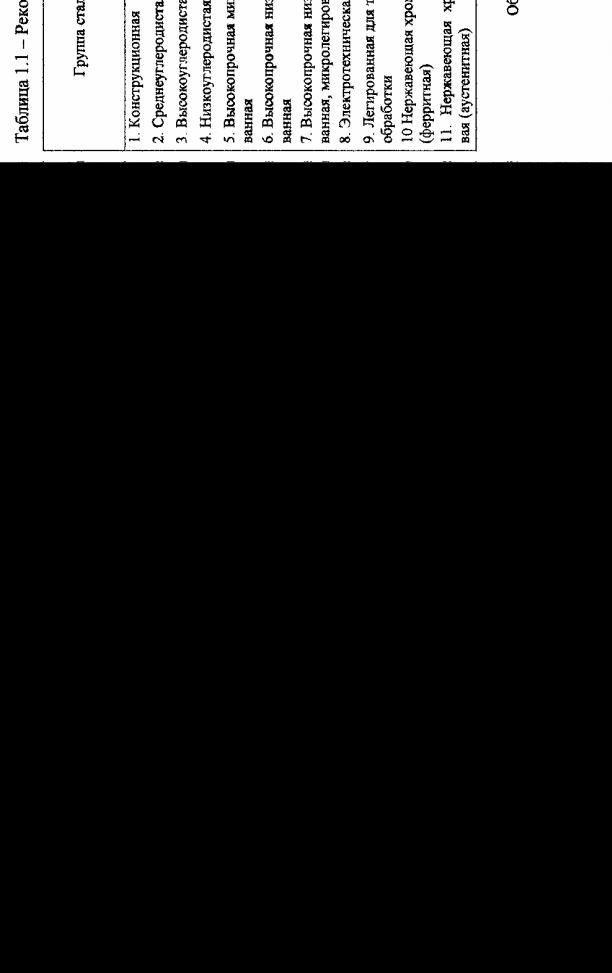
21