
- •1. TABLE OF CONTENTS
- •2. BASIC MANUFACTURING
- •2.1 INTRODUCTION
- •2.2 PRACTICE PROBLEMS
- •3. MANUFACTURING COST ESTIMATING
- •3.1 COSTS ESTIMATES
- •3.2 COGS (COST OF GOODS SOLD)
- •3.3 VALUE ENGINEERING
- •3.4 REFERENCES
- •4. BASIC CUTTING TOOLS
- •4.1 CUTTING SPEEDS, FEEDS, TOOLS AND TIMES
- •4.2 HIGH SPEED MACHINING
- •4.3 REFERENCES
- •5. CUTTING THEORY
- •5.1 CHIP FORMATION
- •5.2 THE MECHANISM OF CUTTING
- •5.2.1 Force Calculations
- •5.2.1.1 - Force Calculations
- •5.2.1.2 - Merchant’s Force Circle With Drafting (Optional)
- •5.3 POWER CONSUMED IN CUTTING
- •5.4 PRACTICE QUESTIONS
- •5.5 TEMPERATURES IN CUTTING
- •5.6 TOOL WEAR
- •5.7 CUTTING TOOL MATERIALS
- •5.7.1 A Short List of Tool Materials
- •5.8 TOOL LIFE
- •5.8.1 The Economics of Metal Cutting
- •5.9 REFERENCES
- •5.10 PRACTICE PROBLEMS
- •6. SAWS
- •6.1 SPEEDS AND FEEDS
- •6.2 PRACTICE PROBLEMS
- •7. DRILLING
- •7.1 TYPES OF DRILL PRESSES
- •7.2 TYPICAL DRILL PRESS OPERATIONS
- •7.3 TYPICAL DRILL BITS
- •7.3.1 Reamers
- •7.3.2 Boring
- •7.3.3 Taps
- •7.4 DRILLING PROCESS PARAMETERS
- •7.4.1 The mrr For Drilling
- •7.5 PRACTICE PROBLEMS
- •8. LATHES
- •8.1 INTRODUCTION
- •8.2 OPERATIONS ON A LATHE
- •8.2.1 Machine tools
- •8.2.1.1 - Production Machines
- •8.3 LATHE TOOLBITS
- •8.3.1 Thread Cutting On A Lathe
- •8.3.2 Cutting Tapers
- •8.3.3 Turning Tapers on Lathes
- •8.4 FEEDS AND SPEEDS
- •8.4.1 The mrr for Turning
- •8.4.2 Process Planning for Turning
- •8.5 PRACTICE PROBLEMS
- •9. MILLING
- •9.1 INTRODUCTION
- •9.1.1 Types of Milling Operations
- •9.1.1.1 - Arbor Milling
- •9.1.2 Milling Cutters
- •9.1.3 Milling Cutting Mechanism
- •9.1.3.1 - Up-Cut Milling
- •9.1.3.2 - Down-Cut Milling
- •9.2 FEEDS AND SPEEDS
- •9.2.1 The mrr for Milling
- •9.2.2 Process Planning for Prismatic Parts
- •9.2.3 Indexing
- •9.3 PRACTICE PROBLEMS
- •10. GRINDING
- •10.1 OPERATIONS
- •10.2 MACHINE TYPES
- •10.2.1 Surface
- •10.2.2 Center
- •10.2.3 Centerless
- •10.2.4 Internal
- •10.3 GRINDING WHEELS
- •10.3.1 Operation Parameters
- •10.4 PRACTICE PROBLEMS
- •11. SURFACES
- •11.1 MEASURES OF ROUGHNESS
- •11.2 METHODS OF MEASURING SURFACE ROUGHNESS
- •11.2.1 Observation Methods
- •11.2.2 Stylus Equipment
- •11.2.3 Specifications on Drawings
- •11.3 OTHER SYSTEMS
- •11.4 PRACTICE PROBLEMS
- •11.4.0.1 - Roundness Testing
- •11.4.0.1.1 - Intrinsic Roundness Testing
- •11.4.0.1.2 - Extrinsic Roundness Testing
- •11.4.0.1.3 - Practice Problems
- •11.5 PRACTICE PROBLEMS
- •35. METROLOGY
- •35.1 INTRODUCTION
- •35.1.1 The Role of Metrology
- •35.2 DEFINITIONS
- •35.3 STANDARDS
- •35.3.1 Scales
- •35.3.2 Calipers
- •35.3.3 Transfer Gauges
- •35.4 INSTRUMENTS
- •35.4.1 Vernier Scales
- •35.4.2 Micrometer Scales
- •35.4.2.1 - The Principle of Magnification
- •35.4.2.2 - The Principle of Alignment
- •35.4.3 Dial Indicators
- •35.4.4 The Tool Makers Microscope
- •35.4.5 Metrology Summary
- •35.5 PRACTICE PROBLEMS
- •35.5.0.1 - Interferometry (REWORK)
- •35.5.0.1.1 - Light Waves and Interference
- •35.5.0.1.2 - Optical Flats
- •35.5.0.1.3 - Interpreting Interference Patterns
- •35.5.0.1.4 - Types of Interferometers
- •35.5.0.2 - Laser Measurements of Relative Distance
- •35.5.0.2.1 - Practice Problems
- •35.6 GAUGE BLOCKS
- •35.6.1 Manufacturing Gauge Blocks
- •35.6.2 Compensating for Temperature Variations
- •35.6.2.1 - References
- •35.6.3 Testing For Known Dimensions With Standards
- •35.6.3.1 - References
- •35.6.4 Odd Topics
- •35.6.5 Practice Problems
- •35.6.6 Limit (GO & NO GO) Gauges
- •35.6.6.1 - Basic Concepts
- •35.6.6.2 - GO & NO GO Gauges Using Gauge Blocks
- •35.6.6.3 - Taylor’s Theory for Limit Gauge Design
- •35.6.6.4.1 - Sample Problems
- •35.6.7 Sine Bars
- •35.6.7.1 - Sine Bar Limitations
- •35.6.7.1.1 - Practice Problems
- •35.6.8 Comparators
- •35.6.8.1 - Mechanical Comparators
- •35.6.8.2 - Mechanical and Optical Comparators
- •35.6.8.3 - Optical Comparators
- •35.6.8.4 - Pneumatic Comparators
- •35.6.9 Autocollimators
- •35.6.10 Level Gauges
- •35.6.10.1 - Clinometer
- •35.6.10.2 - The Brookes Level Comparator
- •35.6.11 The Angle Dekkor
- •35.7 MEASURING APARATUS
- •35.7.1 Reference Planes
- •35.7.1.1 - Granite Surface Plates
- •35.7.1.2 - Cast Iron Surface Plates
- •35.7.2 Squares
- •35.7.2.1 - Coordinate Measureing Machines
- •35.7.2.2 - Practice Problems
- •AM:35.7.3 Coordinate Measuring Machines (CMM)
- •36. ASSEMBLY
- •36.1 THE BASICS OF FITS
- •36.1.1 Clearance Fits
- •36.1.2 Transitional Fits
- •36.1.3 Interference Fits
- •36.2 C.S.A. B97-1 1963 LIMITS AND FITS(REWORK)
- •36.3 CSA MODIFIED FITS
- •36.4 CSA LIMITS AND FITS
- •36.5 THE I.S.O. SYSTEM
- •36.6 PRACTICE PROBLEMS
- •42. WELDING/SOLDERING/BRAZING
- •42.1 ADHESIVE BONDING
- •42.2 ARC WELDING
- •42.3 GAS WELDING
- •42.4 SOLDERING AND BRAZING
- •42.5 TITANIUM WELDING
- •42.5.1 Practice Problems
- •42.6 PLASTIC WELDING
- •42.7 EXPLOSIVE WELDING
- •42.7.1 Practice Problems
- •43. AESTHETIC FINISHING
- •43.1 CLEANING AND DEGREASING
- •43.2 PAINTING
- •43.2.1 Powder Coating
- •43.3 COATINGS
- •43.4 MARKING
- •43.4.1 Laser Marking
- •43.5 PRACTICE PROBLEMS
- •44. METALLURGICAL TREATMENTS
- •44.1 HEAT TREATING
- •44.2 ION NITRIDING
- •44.3 PRACTICE PROBLEMS
- •45. CASTING
- •45.1 SAND CASTING
- •45.1.1 Molds
- •45.1.2 Sands
- •45.2 SINGLE USE MOLD TECHNIQUES
- •45.2.1 Shell Mold Casting
- •45.2.2 Lost Foam Casting (Expandable Pattern)
- •45.2.3 Plaster Mold Casting
- •45.2.4 Ceramic Mold Casting
- •45.2.5 Investment Casting
- •45.3 MULTIPLE USE MOLD TECHNIQUES
- •45.3.1 Vacuum Casting
- •45.3.2 Permanent Mold Casting
- •45.3.2.1 - Slush Casting
- •45.3.2.2 - Pressure Casting
- •45.3.2.3 - Die Casting
- •45.3.3 Centrifugal Casting
- •45.3.4 Casting/Forming Combinations
- •45.3.4.1 - Squeeze Casting
- •45.3.4.2 - Semisolid Metal Forming
- •45.3.5 Single Crystal Casting
- •45.4 OTHER TOPICS
- •45.4.1 Furnaces
- •45.4.2 Inspection of Casting
- •45.5 Design of Castings
- •45.6 REFERENECES
- •45.7 PRACTICE PROBLEMS
- •46. MOLDING
- •46.1 REACTION INJECTION MOLDING (RIM)
- •46.1.1 References
- •46.2 INJECTION MOLDING
- •46.2.1 Hydraulic Pumps/Systems
- •46.2.2 Molds
- •46.2.3 Materials
- •46.2.4 Glossary
- •46.3 EXTRUSION
- •46.4 PRACTICE PROBLEMS
- •47. ROLLING AND BENDING
- •47.1 BASIC THEORY
- •47.2 SHEET ROLLING
- •47.3 SHAPE ROLLING
- •47.4 BENDING
- •48. SHEET METAL FABRICATION
- •48.1 SHEET METAL PROPERTIES
- •48.2 SHEARING
- •48.2.1 Progressive and Transfer Dies
- •48.2.2 DRAWING
- •48.3 DEEP DRAWING
- •48.4 SPINNING
- •48.5 MAGNETIC PULSE FORMING
- •48.6 HYDROFORMING
- •48.7 SUPERPLASTIC FORMING
- •48.7.1 Diffusion Bonding
- •48.8 PRACTICE PROBLEMS
- •49. FORGING (to be expanded)
- •49.1 PROCESSES
- •49.1.1 Open-Die
- •49.1.2 Impression/Closed Die
- •49.1.3 Heading
- •49.1.4 Rotary Swaging
- •50. EXTRUSION AND DRAWING
- •50.1 DIE EXTRUSION
- •50.1.1 Hot Extrusion
- •50.1.2 Cold Extrusion
- •50.2 HYDROSTATIC EXTRUSION
- •50.3 DRAWING
- •50.4 EQUIPMENT
- •50.5 PRACTICE PROBLEMS
- •51. ELECTROFORMING
- •51.1 PRACTICE PROBLEMS
- •52. COMPOSITE MANUFACTURING
- •52.1 FIBER REINFORCED PLASTICS (FRP)
- •52.2 COMPOSITE MANUFACTURING
- •52.2.1 Manual Layup
- •52.2.2 Automated Tape Lamination
- •52.2.3 Cutting of Composites
- •52.2.4 Vacuum Bags
- •52.2.5 Autoclaves
- •52.2.6 Filament Winding
- •52.2.7 Pultrusion
- •52.2.8 Resin-Transfer Molding (RTM)
- •52.2.9 GENERAL INFORMATION
- •52.2.10 REFERENCES
- •52.2.11 PRACTICE PROBLEMS
- •53. POWDERED METALLURGY
- •53.1 PRACTICE PROBLEMS
- •54. ABRASIVE JET MACHINING (AJM)
- •54.1 REFERENCES
- •54.2 PRACTICE PROBLEMS
- •55. HIGH PRESSURE JET CUTTING
- •56. ABRASIVE WATERJET CUTTING (AWJ)
- •57. ULTRA SONIC MACHINING (USM)
- •57.1 REFERENCES
- •57.1.1 General Questions
- •58. ELECTRIC DISCHARGE MACHINING (EDM)
- •58.1 WIRE EDM
- •58.2 PRACTICE PROBLEMS
- •58.3 REFERENCES
- •59. ELECTROCHEMICAL MACHINING (ECM)
- •59.1 REFERENCES
- •59.2 PRACTICE PROBLEMS
- •60. ELECTRON BEAM MACHINING
- •60.1 REFERENCES
- •60.2 PRACTICE PROBLEMS
- •61. ION IMPLANTATION
- •61.1 THIN LAYER DEPOSITION
- •61.2 PRACTICE PROBLEMS
- •62. ELECTROSTATIC SPRAYING
- •62.1 ELECTROSTATIC ATOMIZATION METHOD
- •62.2 PRACTICE PROBLEMS
- •63. AIR-PLASMA CUTTING
- •63.1 REFERENCES
- •63.2 PRACTICE PROBLEMS
- •64. LASER CUTTING
- •64.1 LASERS
- •64.1.1 References
- •64.2 LASER CUTTING
- •64.2.1 References
- •64.3 PRACTICE PROBLEMS
- •65. RAPID PROTOTYPING
- •65.1 STL FILE FORMAT
- •65.2 STEREOLITHOGRAPHY
- •65.2.1 Supports
- •65.2.2 Processing
- •65.2.3 References
- •65.3 BONDED POWDERS
- •65.4 SELECTIVE LASER SINTERING (SLS)
- •65.5 SOLID GROUND CURING (SGC)
- •65.6 FUSED DEPOSITION MODELLING (FDM)
- •65.7 LAMINATE OBJECT MODELING (LOM)
- •65.8 DIRECT SHELL PRODUCTION CASTING (DSPC)
- •65.9 BALLISTIC PARTICLE MANUFACTURING (BPM)
- •65.9.1 Sanders Prototype
- •65.9.2 Design Controlled Automated Fabrication (DESCAF)
- •65.10 COMPARISONS
- •65.10.1 References
- •65.11 AKNOWLEDGEMENTS
- •65.12 REFERENCES
- •65.13 PRACTICE PROBLEMS
- •66. PROCESS PLANNING
- •66.1 TECHNOLOGY DRIVEN FEATURES
- •66.2 MOST SIGNIFICANT FEATURE FIRST
- •66.3 DATABASE METHODS
- •66.4 MANUFACTURING VOLUMES
- •66.5 STANDARD PARTS
- •66.6 PRACTICE PROBLEMS
- •66.6.1 Case Study Problems
- •66.6.1.1 - Case 1
- •66.7 REFERENCES
page 438
65.5 SOLID GROUND CURING (SGC)
•Basic Process,
1.A computer program preprocesses a part so that it is in sliced layers.
2.A plate (glass?) is charged selectively and coated with a back powder. This process is much like photocopying.The result is a photographic mask of clear and opaque areas for a single slice of the part.
3.A thin layer of photopolymer is spread in a part vat.
4.The mask is placed over the photopolymer and a UV lamp is used to expose the layer and selectively harden the polymer.
5.The photographic plate with the mask is cleaned.
6.The unhardened polymer is removed from the surface.
7.A find layer of wax is deposited and hardened.
8.The surface is milled flat for uniform thickness.
9.The process begins again at step 2 and continues until all of the layers have been added. Note: Some steps can be done concurrently for the mask and the vat (i.e., 2,5 AND 3,6,7,8) to decrease build times.
•Developed by Cubital Inc. in Israel, started in 1987.
•two commercial machines - Solider 4600 and 5600
•Uses photosensitive polymers, but these are developed using a UV light and a photopolymer
1.photopolymer is developed and hardened by a UV mask that has the pattern for one slice of the part.
2.Unhardened polymer is cleaned away and replaced with wax, that is solidified with a cooling plate.
3.the polymer/wax layer is machined to exact thickness, and coated with a new layer of polymer. (a vacuum is used to remove cut chips)
4.The process continues until done
•The masks are made using a glass plate with electrostatic powder distribution (similar to photocopiers). A slice is used to electrostatically charge a glass plate, electrostatic sensitive powder coats the charged areas, and the mask is complete. After use the glass is cleaned and reused.
•After completion the wax is melted, and the complete part remains. (the wax was used to support work and eliminate supports.)
************ Include SGC figures from pg 60 and 64
•the UV lamp is 4KW and is exposed to the polymer for a few seconds
•a resin applicator spreads the photopolymer across in thin layers
page 439
•an aerodynamic wiper is used to remove excess material to a storage reservoir. This material may be reused if not overexposed (?) thus causing a change in viscosity.
•because the toxic resins are used, exhaust fans and dark work cabinets are required.
•Advantages,
-no need for time consuming post-curing
-part complexity does not effect speed, however volume does.
-elimination of postcuring reduces internal stresses, and warping.
-jobs can be stopped, other jobs run, then the first job restarted at a later time.
-weights may be inserted at any time to alter the centre of gravity
-supports are not required
-models with moving parts can be produced because of the firm holding of work in the process.
-layers can be milled off if they are found to be in error
-many parts can be run at the same time
•disadvantages,
-overexposure of the polymer may increase the viscosity, and make it unusable, thus greatly increasing the volume of expensive polymers used.
-the resins require that light sealed chambers and toxic material handling procedures be used.
-the machine is very large
-machining is noisy
-maintenance is high, requires supervision
-very few materials available
-removal of wax after production is required
•Solider 4600 & 5600
-65 (5600) or 120 (4600) seconds per layer
-14” by 14” by 14” (4600) or 20” by 14” by 20” (5600) work vol.
-$275,000US (4600), $400,000US (5600)
-accuracy 0.1%
-has been used to produce investment casting
•A selected set of specifications for the Solider 4600 are given below,
page 440
Specification |
Details |
|
|
Work Volume |
14” by 14” by 14” |
Accuracy |
0.1% up to 0.020” max. |
Flatness |
typical 0.006” |
Resolution |
x-y 0.004”, z 0.004”-0.006” |
Smallest feature |
x-y 0.024”, z 0.006” |
Times |
preprocess 0:20-3:00 hrs., postprocess 0:30-3:00 hrs. |
Production Rate |
120 sec/layer, 35 in.**3/hr. |
Input Format |
solid formats automatically, 2D with user interaction, CT/MRI voxels, etc. |
|
|
• A selected set of specifications for the Solider 5600 are given below,
Specification |
Details |
|
|
Work Volume |
20” by 14” by 20” |
Accuracy |
0.1% up to 0.020” max. |
Flatness |
typical 0.006” |
Resolution |
x-y 0.004”, z 0.004”-0.006” |
Smallest feature |
x-y 0.024”, z 0.006” |
Times |
preprocess 0:20-3:00 hrs., postprocess 0:30-3:00 hrs. |
Production Rate |
65 sec/layer, 80 in.**3/hr. |
Input Format |
solid formats automatically, 2D with user interaction, CT/MRI voxels, etc. |
|
|
65.6 FUSED DEPOSITION MODELLING (FDM)
•Developed by Scott Crump, and Stratasys has been selling the machine since 1991.
•The concept is that material is heated and then in controlled quantities deposited directly on previous layers. Eventually layers are built up to complete the entire part.
•The materials are available on spools of 1/2 mile in length, at costs from $175(US) to $260(US). The filaments are 0.05”
•As usual the .STL file is sliced into layers, and the slices are used to drive the machine.
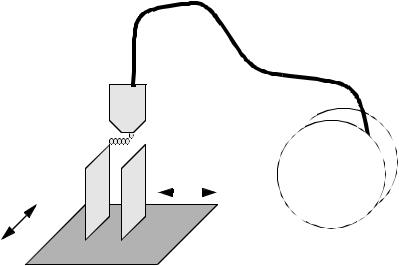
page 441
•The key to this method is an extrusion head,
-the material is fed into the head
-the material is heated until melting
-the material is then extruded from the tip in controlled quantities
-the material is wiped on the previous layer
•The extrusion head is moved about the table with an x-y positioning system to deposit material on each layer
•The platform the part is on drops when a layer is complete to allow the addition of a new layer.
heated precise volume extrusion head
|
|
|
|
|
|
x |
|
|
|
|
|
|
|
|
|
|
|
|
|
|
|
|
|
|
|
||
y |
|
|
|
|
|
|
|
|
|
spool of material |
|||
|
|
|
|
|
|
|
|
|
|||||
|
z platform |
|
|
||||||||||
|
|
|
|
|
|
|
|||||||
machine |
|
Volume |
|
$(US) |
|
|
comments |
||||||
|
|
|
|||||||||||
|
|
|
|
|
|
|
|
|
|||||
FDM 1650 |
|
10” by 10” by 10” |
|
115,000 |
|
|
|
|
|||||
FDM 2000 |
|
10” by 10” by 10” |
|
140,000 |
|
|
faster the 1650 |
||||||
FDM 8000 |
|
18” by 18” by 24” |
|
200,000 |
|
|
polyester |
||||||
Genisys |
|
8”by8”by8” |
|
50,000 |
|
|
|||||||
FDM Quantum |
|
23.6”by19.7”by23.6” |
350,000 |
|
|
5 times faster then 2000 |
• materials include
investment casting wax ABS
polyester elastomer
• slice thickness is 0.002” to 0.03”
page 442
•material changeover requires a few minutes of “flushing-out’
•Advantages,
-a good variety of materials available
-easy material change
-low maintenance costs
-thin parts produced fast
-tolerance of +/- 0.005” overall
-no supervision required
-no toxic materials
-very compact size
-low temperature operation.
•Disadvantages,
-seam line between layers
-the extrusion head must continue moving, or else material bumps up
-supports may be required
-part strength is weak perpendicular to build axis.
-more area in slices requires longer build times
-temperature fluctuations during production could lead to delamination
•selected specifications for the FDM1000 are,
Specification |
Detail |
|
|
Work Volume |
10” by 10” by 10” |
Accuracy |
0.005” |
Thickness/Width |
path width 0.010”-0.125”, thickness 0.002”-0.030” |
Head Temperature |
140°-400°F |
Materials |
Investment Casting Wax, Machinable Wax, Polyolefin and |
|
Polyamide |
Machine Dimensions |
26” by 34” by 34” |
Weight |
250 lbs. |
Input Formats |
STL, 3D surface or solid |
Computer Required |
SGI Iris |
Operating Temp. |
50-85° |
Power Supply |
110 VAC, 12A, 60Hz |
|
|
• Approximate costs are,