
ОТМ
.pdf
Задача 1.14. Определить число годных деталей, исправимого и неисправимого брака при обработке на токарном полуавтомате партии валов 450 шт. диаметром 40−0,16 мм,
если среднее квадратическое отклонение s и см = d − dcp , (см рис. 1.1), вычисленные
по результатам измерений пробных валиков, имею значения, приведенные в табл. 1.5. s = 0, 03 мм, см = −0, 02 мм.
Рисунок 1.1
Решение
Интервал рассеяния размеров обрабатываемых валов относительно выборочного среднего (в предположении, что их распределение подчиняется закону Гаусса)
Dd = ±ks = ±3×0, 03 = ±0, 09
Из расположения поля рассеяния фактических размеров валов по отношению к полю допуска, очевидно, что часть размеров валов (область размеров F2) ,будут выходить за допустимый наибольший размер рис. 1.1.
Вся площадь под кривой распределения (полагаем, что она подчиняется закону Гаусса) равна 1, половина ее – 0,5.
Тогда
|
|
|
1 |
z |
|
z2 |
|
F |
= 0, 5 − F = 0,5 − |
|
∫0 |
e 2 dz = 0, 5Ф(z) |
|||
|
|
||||||
|
|
||||||
2 |
1 |
|
2π |
|
|
|
|
|
|
|
|
|
|
Ф(z) - функция Лапласа.
Величина z = |
в рассматриваемом случае |
|||
|
s |
|
||
|
|
dср |
= dнб − T / 2 = 40 − 0, 08 = 39,92 мм, |
|
|
|
|
= |
см + dср = −0, 02 + 39, 92 = 39,90 мм, |
|
d |

2 = dнб − d = 40 − 39, 90 = 0,1 ,
z = 2 = |
0,1 |
= 3, 3 |
|
||
s |
0, 03 |
Тогда,
Ф(z) = Ф(3,3) = 0, 4995
F2 = 0, 5 − Ф(z) = 0,5 − 0, 4995 = 0, 01
Таким образом, 1% деталей (5 шт.) будут бракованными, брак исправим.
Задача 1.24. Определить методом полной взаимозаменяемости допуск, верхнее отклонения на операционный размер (табл. 1.10).
Рисунок 1.2.
A1 = 22−0,21
A2 = 54+0,19
Решение
Составим размерную цепь (в качестве замыкающего звена может быть конструкторский размер или припуск). Строим цепь, приняв за замыкающее звено конструкторский размер А2 (рис. 1.3). Здесь А2 – замыкающее звено, А3 и А1 – увеличивающие составляющие звенья.
Рисунок 1.3.

Запишем уравнение размерной цепи
А2=А1+А3
Из этого уравнения найдем номинальное значение операционного размера
А3=А2-А1=54-22=32мм
И его среднее отклонение
ЕсрА3=ЕсрА2-ЕсрА1= 0,095 – 0,105=-0,01
= ESA1+ EIA1 = 0 + (−0, 21) = − ЕсрА1 0,105
2 |
2 |
|
||
ЕсрА2 = |
ESA2 + EIA2 |
= |
0,19 + 0 |
= 0, 095 |
|
|
|||
2 |
2 |
|
ES – верхнее предельное отклонение
EI – нижнее предельное отклонение
Запишем уравнение допусков для размерной цепи (допуск замыкающего звена равен сумме допусков составляющих звеньев).
ТА2=ТА3+ТА1
Отсюда допуск операционного размера равен
ТА3=ТА2-ТА1=0,19-(-0,21)=0,4
Расчетный допуск операционного размера равен ТА3=0,4 мм
Верхнее предельное отклонение операционного размера
ESA3= ЕсрА3+0,5*ТА3=-0,01+0,5*0,4=0,19
EIA3= ЕсрА3-0,5*ТА3=-0,01 -0,5*0,4=-0,21
Расчетное значение операционного размера равно:
А3= 32+−0,190,21
Задача 1.65. Определить исполнительный размер цилиндрического установочного пальца d, обеспечивающий заданную точность выполнения размера А1 при фрезеровании поверхностей втулки (см. рис. 1.5). Исходные данные приведены в табл. 1.
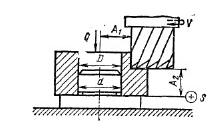
При выборе поля допуска вала в качестве исполнительного размера установочного пальца следует помнить, что установка заготовки с зазором менее 10 мкм несколько усложняется.
Рисунок 1.5.
Вариант |
Диаметр |
Точность |
Допустимый |
Заданная |
|
отверстия |
метода |
износ |
точность |
|
заготовки D,мм |
обработки, ω , |
установочного |
размера А1, мм |
|
|
мкм |
Пальца Tизн , |
|
|
|
|
мкм |
|
|
|
|
|
|
10 |
50+0,062 |
120 |
20 |
80 ± 0,150 |
|
|
|
|
|
Решение
Анализ схемы установки втулки показывает, что погрешность базирования для размера А1 будет равна зазору в сопряжении отверстия заготовки D с установочным пальцем d. Поэтому исполнительный размер диаметра установочного пальца определяется из условия обеспечения заданной точности выполнения размера А1
TA1 = ε yA1 + ω
Принимая погрешности закрепления ε3 ,и положения заготовки ε пз по отношению к размеру А1 равными нулю, ε3 = εпз = 0 , точность выполняемого размера определяется равенством:
TA1 = εδ A1 + ω ,
где εδ A1 погрешность базирования для размера А1 равна максимальному зазору в сопряжении отверстия заготовки с установочным пальцем
εδ A1 = Smax = TD + Smin + Td
Таким образом:
TA1 = TD + Smin + Td + ω
откуда
Smin + Td = TA1 - (TD + ω) = 0, 3 - (0, 062 + 0,12) = 0,118 мм
Из таблиц ГОСТ 25347-82 подбираем поле допуска вала так, чтобы соблюдалось условие Smin + Td ³ ei .
Для валов диаметром 50 мм, отклонения, мкм, приведены ниже:
|
g6 |
f7 |
e8 |
d9 |
d11 |
|
|
|
|
|
|
es |
-9 |
-25 |
-50 |
-80 |
-80 |
|
|
|
|
|
|
ei |
-25 |
-50 |
-89 |
-142 |
-240 |
|
|
|
|
|
|
Очевидно, что указанному условию удовлетворяют поля допусков валов g6, f7 и e8; поля допусков валов d9 и d11 не удовлетворяют принятому условию, так как абсолютная величина ei больше полученной расчетной (Smin + Td)=0,118мм.
Таким образом, в качестве исполнительных размеров установочных пальцев могут быть приняты:
d = 50g6 ( −−0,0090,025 ) , d = 50 f 7 ( −−0,0250,050 ) , d = 50e8( −−0,0500,089 ) мм.
Приняв поле допуска на изготовление установочного пальца в соответствии с точностью по 6-му квалитету g6, выполним проверочный расчет и определим ожидаемую точность размера А1.
TA1 = TD + Smin + Td + ω = 0, 062 + 0, 009 + 0, 016 + 0, 012 = 0, 207 мм
При заданном допуске на размер А1, TA1 = 0,3 мм принятое поле допуска
установочного пальца d = 50g6 ( −−0,0090,025
0,093мм.
) мм обеспечивает некоторый запас точности в
Задача 1.87. На консольно-фрезерном станке производится чистовое торцовое фрезерование партии N заготовок (табл. 2). Заготовки, предварительно обработанные с точностью h13, устанавливаются на опорные пластины приспособления с пневматическим зажимом. Для условий обработки, соответствующих вариантов 2 – 6 , определить суммарную погрешность размера h после выполнения операции при
υ =150 м/мин и sz=0,04 мм/зуб. Настройка фрезы также производятся по габариту с контролем положения металлическим щупом толщиной 3 мм.

Таблица 2
Рисунок 1.6.
Решение
1. Определим погрешность установки заготовки ε y .
Для заданных условий по [26, с 43] ε y = 40мкм.
2. Определим погрешность настройки фрезы на размер согласно [26, с 70]:
DH = (K p Dp )2 + ( Kи Dизм )2 =
(1, 73×10)2 + (1× 20)2 = 26, 5мкм
где K p и Kи - коэффициенты, учитывающие отклонения закона распределения величин Dp и Dизм от нормального, Dp - погрешность регулирования фрезы по эталону с контролем металлическим щупом [26, с. 71];
Dизм - допускаемая предельная погрешность измерения размера 45h10 |
[26, с. 72]. |
|||||||||||||||||
3. Определим размерный износ инструмента при фрезеровании |
|
|
||||||||||||||||
|
100 |
|
|
lД BN |
|
100 |
|
|
300 ×100 × 40 |
|
||||||||
Dит.фр = uот.фр × Lфр = 1+ |
|
|
u0 |
|
|
|
|
= 1+ |
|
|
|
×14 |
|
|
|
|
|
= 25мкм |
|
B |
10 |
6 |
sz z |
100 |
10 |
6 |
×0, 04 |
×12 |
|||||||||
|
|
|
|
|
|
|
|
|
u0 - относительный износ при точении [26, с. 74].
4.Определим погрешность Dy . Поле рассеяния размера 45h10 под действием упругих деформаций зависит от колебания составляющей силы резания Px при изменении величины снимаемого припуска и податливости системы шпиндель – стол. В соответствии с [26, с. 32] для 6Р12 станка (ширина стала 320 мм) податливость технологической системы может быть определена как:
|
|
|
|
W = |
y |
= |
|
500 |
|
|
= 40мкм / кН |
||||||||||
|
|
|
|
12, 25 |
|||||||||||||||||
|
|
|
|
|
|
|
Px |
|
|
|
|
|
|
||||||||
Приняв Px: Pz=0.5 [27, c. 292] согласно [27, с. 282] |
определим |
||||||||||||||||||||
|
|
|
Px |
= 0,5Pz |
= 0,5 |
Cp ×t x × Szy × Bn × z |
|||||||||||||||
|
|
|
|
|
Dq × nw |
|
|
||||||||||||||
Учитывая, что n = |
1000 ×υ |
= |
1000 ×150 |
= 319мин−1 |
и приняв коэффициент и |
||||||||||||||||
|
3,14 ×150 |
||||||||||||||||||||
|
π × D |
|
|
|
|
|
|
|
|
|
|
||||||||||
|
|
фр |
|
|
|
|
|
|
|
|
|
|
|
|
|
|
|
|
|
||
показатели степени по [27, с. 291], определяем |
Px max |
и Px min : |
|||||||||||||||||||
|
P |
= |
8, 25 ×1, 21 ×0, 040,75 ×1001,1 ×12 |
= 0, 44кН . |
|||||||||||||||||
|
|
|
|
|
|||||||||||||||||
|
x min |
|
|
|
1501,3 ×3190,2 |
|
|
|
|
||||||||||||
Так как показатель при t равен 1,0, то |
|
|
|
|
|
||||||||||||||||
|
P |
= |
tmax |
P |
|
|
|
= |
1, 6 |
×0, 44 = 0,59kH . |
|||||||||||
|
|
|
|
|
|
||||||||||||||||
|
|
x max |
|
|
|
|
x min |
1, 2 |
|
|
|
|
|
||||||||
|
|
|
|
|
|
tmin |
|
|
|
|
|
|
|
|
Тогда
Dy = W (Px max - Px min ) = 40 ×(0, 59 - 0, 44) = 6мкм.
5.Погрешность, вызванная геометрическими неточностями фрезерного станка нормальной точности, представляет собой отклонение от параллельности верхней поверхности основанию на длине 300 мм, и согласно [26, с. 59]

∑Dст = 25мкм .
6.Погрешность ∑ т = от температурных деформаций системы принимаем в размере 10% от суммы остальных погрешностей:
∑т = 0,1(40 + 26, 5 + 25 + 6 + 25) = 12 мкм.
7.Суммарная погрешность
D∑ = ε y2 + D2y + D2H + (1, 73Du )2 + (1, 73 ∑Dст )2 + (1, 73 ∑Dт )2 =
= 402 + 62 + 26, 52 + (1, 73×24)2 + (1, 73× 25)2 + (1, 73×12)2 = 72мкм
Заданная точность обеспечивается, так как IT1045 = 100 мкм > D∑ = 72 мкм.
1.108. Определить наиболее производительный метод (отделочно – упрочняющей обработки (накатывание шариковой головкой или вибронакатывание многошариковым виброустройством) направляющих станков из чугуна СЧ20 для получения требуемого значения шероховатости обрабатываемой поверхности Ra. Условия обработки приведены в табл. 3.
Таблица 3

Решение:
Из уравнения:
0,99 |
0,2 |
|
p −0,9 |
|
−0,02 |
|
Ra = 3, 43Raисх |
× Sпр |
|
|
|
× N |
|
|
|
|||||
|
|
|
10 |
|
|
Относительно продольной подачи, определяющей производительность обработки получим
|
|
5 |
p |
4,5 |
|
0,1 |
|
|
Ra |
|
× |
|
|
× N |
|
|
|
|
|||||
Sпр = 0, 02 |
|
|
10 |
|
|
|
|
|
|
Ra |
4,95 |
|
|
||
|
|
|
|
исх |
|
|
Подставив исходные данные в полученное уравнение, определим
|
|
5 |
|
500 |
4,5 |
0,1 |
|
0, 2 |
|
× |
|
|
×1 |
|
|
|
10 |
||||||
Sпр = 0, 02 |
|
|
|
|
|
= 28, 3 мм/(мин.шар). |
|
|
|
|
4,95 |
|
|
||
|
|
|
|
1 |
|
|
|
Учитывая, что обработка производится восьмишариковой головкой, получим
Sпр.м = z × Sпр = 8 × 28, 3 = 226, 4 мм/мин
Из уравнения:
1,01 |
0,29 |
p −0,72 |
|
−0,19 |
|
Ra = 8, 67Raисх |
× Sпр.м |
|
|
× N |
|
|
|
||||
|
|
10 |
|
|
Получим
Sпр = 1723 |
|
|
Ra3,48 |
|
|
||
|
|
2,48 |
|
|
|
||
|
|
|
|
исх |
|
|
|
|
|
p |
× Ra |
3,45 |
× N |
0,66 |
|
|
|
|
|
|
|
||
|
|
|
|||||
|
|
10 |
|
|
|
|
Подставив исходные данные, определяющие условия вибронакатывания, в последнее уравнение, получим
Sпр |
= 1723 |
|
|
|
13,48 |
|
|
= 4, 4 мм/мин |
500 |
|
2,48 |
|
|
||||
|
|
|
3,45 |
0,66 |
|
|||
|
|
|
|
|
×0, 2 |
|
×1 |
|
|
|
|
||||||
|
|
10 |
|
|
|
|
|
Таким образом, наиболее производительным методом отделочно-упрочняющей обработкой направляющих станков из чугуна СЧ 20, позволяющим получить Ra = 0,2 мкм, является накатывание многошариковой головкой.
2.8. Трехступенчатый вал изготавливают из горячекатаного стального проката обычной точности или стали 45. Шейку диаметром D3 обрабатывают при установке заготовки в центрах. Определить предпочтительный вариант изготовления заготовки с точки зрения экономии металла. Припуски определить расчетно-аналитическим методом.
Исходные данные в таблице 4.
Таблица 4
Вари- |
D1 |
D2 |
D3 |
L |
L1 |
L2 |
G |
ант |
мм |
мм |
мм |
мм |
мм |
мм |
кг |
|
|
|
|
|
|
|
|
10 |
50 |
75 |
60−+0,0100,010 |
350 |
70 |
85 |
8,3 |
|
|
|
|
|
|
|
|