
ОТМ
.pdfV = |
Cv |
× Kv |
T m ×t x × Sy |
По табл. 17 стр. 269 [27] определим значение коэффициента и показатели степеней.
Cv =340,
x = 0,15,
y = 0,45,
m = 0,2
T – стойкость инструмента (резца) 90 мин. Без переточки.
Kv = Kmv × Knv × Kuv
где:
Kmv - коэффициент, учитывающий физико-механические свойства обрабатываемого материала.
|
|
|
750 |
nv |
||
Kmv |
= KГ |
× |
|
|
= 0, 75 |
|
σ в |
||||||
|
|
|
|
|
По табл. 2 стр. 262 [27] определяем значение коэффициента K Г и
показатели степени nv; K Г =1,0; nv = 1
По табл. 5 стр. 263 [27] определяем коэффициент, Knv учитывающий влияние состояния поверхности заготовки. Knv =0,8
По табл. 6 стр. 263 [27] определяем коэффициент, Kuv учитывающий влияние инструментального материала на скорость резания. Kuv =1
|
|
|
Kv |
= 0, 75 ×0,8 ×1 = 0, 6 |
|
|||||
|
340 |
|
|
|
|
|||||
|
V = |
|
|
|
×0, 6 |
= 113,3 |
м/мин. |
|||
|
900,2 ×10,15 ×0, 60,45 |
|||||||||
4. |
Определяем число оборотов шпинделя. |
|
|
|||||||
|
n = |
1000 ×V |
= |
1000 ×113,3 |
= 360, 5об / мин |
|||||
|
|
|
||||||||
|
|
π × Dз |
3,14 ×90 |
|
|
|
||||
|
nпас = 400об / мин |
|
|
|
|
|
|
|||
5. |
Определяем действительную скорость. |
|
|
Vд |
= π × D × n = |
3,14 ×90 × |
400 |
= 94, 2м / мин |
1000 |
|
|||
|
1000 |
|
|
6. Определяем силу резания.
Pz = 10 ×Cp ×t x × S y ×V n × K p
По табл. 22 стр. 273 [27] определяем поправочный коэффициент и показатели степеней.
Cp =300
x = 1
y = 0,75
n = -0,15
K p = Kмp × Kϕ p × Kλ p × Kγ p × Krp
По табл. 9 стр. 264 [27] определяем:
K мp - коэффициент, учитывающий влияние качества обрабатываемого
материала на силовые зависимости.
|
σ в |
n |
1000 |
0,75 |
||||
K мp |
= |
|
|
= |
|
|
= 0,8 |
|
750 |
750 |
|||||||
|
|
|
|
|
|
Определяем коэффициенты, учитывающие влияние геометрических параметров режущей части инструмента на силы резания.
Kϕ p = 0,89
Kγ p = 1,1
Krp 0,87
Kλ p = 1, 0
K p |
= 0,8 ×0,89 ×1,1×1, 0 ×0,87 = 0, 68 |
||
R = |
10 ×300 ×301 ×0, 60,75 ×0, 68 |
= 2021Н × м |
|
|
|||
z |
1260,15 |
|
7. Определяем мощность резания по формуле:
N рез |
= |
|
Rz ×Vд |
= |
2021×94, 2 |
= 3,11кВт |
|
|
|
||||
|
1020 ×60 |
1020 ×60 |
|
|||
Nст |
= Nдв ×η = 10 ×0, 75 = 7,5кВт |
N рез < Nст 3,11<7,5
8. Определяем основное время операции:
T = |
Lpx |
= |
320 |
= 0, 57 мин |
|
|
|||
o |
n × s 800 ×0, 7 |
|
||
|
|
Расчет норм времени
1. Определяем основное время операции:
n
To = ∑To
i=1
To = 4, 42мин
2. Определяем вспомогательное время операции:
Tв = tуст + tпер + tизм + tдоп ,
где tуст - вспомогательное время на установку и снятие детали, определяем на стр. 33
[6]; tпер - вспомогательное время, связанное с переходом [6]; tизм - вспомогательное время, затрачиваемое на измерение обработанных поверхностей при включении станка [6]; tдоп - вспомогательное время на переключение скоростей и подач.
Tв = 0, 324 +1, 35 + 0, 24 + 0,83 = 2, 74мин
3. Находим оперативное время:
Tоп = Tо + Tв
Tоп =4,42+2,74=7,16мин
4. Определяем время на обслуживание станка:
Tобс. = 4% ×Tоп
Tобс. = 0, 04 ×7,16 = 0, 286мин
5. Находим время отдыха:
Tотд. = 4% ×Tоп
Tотд. = 0, 04 ×7,16 = 0, 286мин
6. Находим штучное время:

Tшт = To + Tв + Tобс. + Tотд.
Tшт = 4, 42 + 2, 74 + 0, 286 + 0, 286 = 7, 733мин
7. Определяем подготовительно – заключительное время на стр. 70 [6]
Тп.з.=9 мин
8. Определяем штучно – калькуляционное время:
Tш−к = Tшт + Tп.з.
n
где n партия деталей запускаемых в производство, шт.
Tш−к = 7, 733 + |
|
9 |
= 7, 74мин |
|
1000 |
||||
|
|
Из представленного расчета видно трудоемкость меньше при обработке детали на станке 16К20
2.20. Токарная обработка наружных поверхностей деталей производится на различных станках. Определить более экономичный вариант обработки по технологической себестоимости при двухсменном режиме работы. Исходные данные приведены в табл. 8.
Таблица 8.
Решение:

Решение I. При наличии на участке сравниваемых станков выбор варианта производим по технологической себестоимости обработки, уравнение (2.47). Для расчета элементов себестоимости необходимы дополнительные данные, которые определяем по [20, 27]:
|
16Б16А |
16Б16ФЗ |
Оптовая цена станка Ц, руб…… |
5450 |
24400 |
Масса станка, кг…… |
2835 |
3800 |
Размеры станка в плане, мм…… |
2505x1190 |
3360x1710 |
Площадь станка в плане, м*…… |
3,0 |
5,75 |
Установленная мощность |
|
|
электродвигателей N3, кВт…… |
11,0 |
10,0 |
Категория ремонтной сложности: |
|
|
механической части, Кн…… |
11,0 |
14 |
электрической части, К*…… |
8,5 |
26 |
Расчет элементов технологической себестоимости сведем в таблицу (см. табл. 9).
Таблица №9

Расчет себестоимости нормативным методом.
Для станка 16Б16А K мч =1.0 [27, с. 429], для станка 16Б16ФЗ принимаем K мч =4,5. При двухместном режиме работы в условиях мелкосерийного производства H0 = 31,2 коп/ч [27, с. 429],
Соп1 = 5, 64 руб.
Соп2 = 2, 74 руб.
Результаты расчетов показывают экономическую целесообразность обработки поверхностей на станке с ЧПУ при обоих условиях, в поставленных в задаче.
3.6. Установить методом полной взаимозаменяемости допуски и предельные отклонения на линейные размеры деталей (табл. 10).
Таблица №10
Решение:
Строим размерную цепь
Рисунок 1.8
Исходные данные: ε = 1+0,6 (мм).
Таблица 11. Допуски и номинальные размеры звеньев
1. Находим значения единиц допуска для составляющих звеньев:
Размер |
Квалитет |
Допуск |
Пред-ое |
Ср. откл. |
Примечание |
|
|
|
откл. |
|
|
|
|
|
|
|
|
мм |
- |
мм |
- |
мм |
- |
|
|
|
|
|
|
А1=161 |
11 |
0,58 |
h, вал |
-0,29 |
Увеличивающее |
|
|
|
|
|
|
А2=6 |
12 |
0,4 |
h, вал |
-0,2 |
Уменьшающее |
|
|
|
|
|
|
А3=149 |
11 |
0,58 |
h, вал |
-0,29 |
Уменьшающее |
|
|
|
|
|
|
А4=6 |
12 |
0,4 |
h, вал |
-0,2 |
Уменьшающее |
|
|
|
|
|
|
Решение:
2. Определяем средний коэффициент точности:
aср = TAD / Σi j = 400 / (0,58 + 0, 4 + 0,58 + 0, 4) = 204,1
Значение aср соответствует значению точности обработки 10-го квалитета.
По ГОСТ 25346-82 принимаем допуски на все составляющие звенья по 10 квалитету:
TA1 = 160мкм , TA2 = 48мкм , TA3 = 160мкм , TA4 = 160мкм .
3.Проверяем полученные результат: ΣTAj = 160 +160 + 48 + 48 = 416
Т.к. не соблюдается условие, TAD = ΣTAj принимаем допуск звена A2 по 9
квалитету TA1 = 30мкм . 4. Предельные отклонения
ESAD = 0мкм , EI AD = −400мкм
5. Назначим отклонения всех составляющих звеньев кроме A1 в “ минус”.
A2 = 6, 0−0,030 , A3 = 149−0,160 , A4 = 6, 0−0,048 ;
6. Отклонения размера A1
ES (es)AD = ΣES (es)Aj − ΣEI (ei)Ak
O = ESA4 − (30 − 48 −160); ESA4 = 238мкм

−400 = EI A4 − 0 ; EI A4 = 400мкм
7. Проверка
TAD = 400мкм , ΣTAj = 160 + 30 + 48 +162 = 400мкм
Допуск замыкающего звена равен сумме составляющих звеньев.
3.8. Установить методом неполной взаимозаменяемости допуски и предельные отклонения на линейные размеры деталей (см. рис. 1.9), если А1 = 80 мм, А2 = 120 мм. Остальные данные см. табл. 10
Таблица 10
Рисунок 1.9
Решение:
Составим схему размерной цепи (рис. 1.10);
Рисунок 1.10
Определим номинальный размер звена А3.
A = (−1) A1 + A2 + (−1) A3 ;
0 = −80 +120 − A3 ; A3 = 40мм
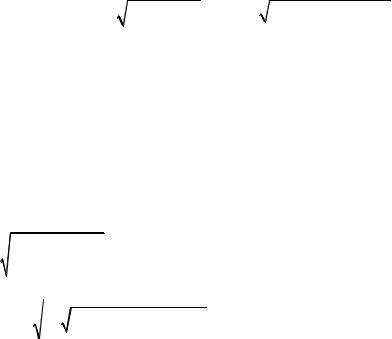
Находим средний квалитет составляющих звеньев.
P = 0,01%, следовательно t = 3,89;
Рассеяние линейных размеров деталей подчиняется нормальному закону (λА2 = 1 / 9) |
||||||||||||||
|
|
|
|
|
|
|
|
|
|
|
|
|
|
ш |
ac |
= |
|
|
TA |
|
|
= |
|
|
200 |
|
= 47,899. |
||
|
|
|
|
|
|
|
|
|
|
|
||||
f |
|
|
|
|
|
|
3,89 |
|
|
|
||||
|
|
× iA2 |
+ iA2 |
+ iA2 |
× 1,82 + 2,172 +1,562 |
|
|
|||||||
|
|
3 |
3 |
|
|
|||||||||
|
|
1 |
2 |
3 |
|
|
|
|
|
|
|
|||
|
|
|
|
|
|
|
|
|
|
|
Принимаем выполнение размеров деталей с точностью по 9 квалитету и назначаем предельные отклонения на размеры:
A1 = 80−0,074
A2 = 120+0,087
Допуск на размер A3 определим из уравнения:
|
m |
|
|
|
|
|
||||
TA |
= t × ∑×ξA2 ×λA2 ×TA2 ; |
|
|
|||||||
|
1 |
|
1 |
1 |
|
|
||||
|
1 |
|
|
|
|
|
|
|
|
|
|
|
|
|
|
|
|
|
|
||
|
|
|
1 |
|
|
|
|
|
||
0, 2 |
= 3,89 × |
|
× |
|
0, 0742 + T 2 |
+ 0, 0872 ; |
||||
|
||||||||||
|
9 |
|
|
|
A |
|
|
|||
|
|
|
|
3 |
|
|
||||
|
|
|
|
|
|
|
|
|
||
TA |
= 0, 06мм |
|
|
|
|
|
||||
3 |
|
|
|
|
|
|
|
|
|
Находим координату середины поля допуска на размер A3 :
EcA = (-1)EcA1 + EcA2 + (-1)EcA3 ;
0,1 = -(-0, 037) + 0, 0435 - EcA3 ;
EcA3 = 0,106
Тогда верхние и нижние отклонения
EsA = EcA + |
1 |
T |
|
= 0,106 + |
|
0, 06 |
= 0,136мм; |
||||
|
|
|
|
|
|||||||
3 |
3 |
2 |
A |
2 |
|
|
|||||
|
|
|
3 |
|
|
||||||
|
|
|
|
|
|
|
|
|
|
|
|
EiA = EcA - |
1 |
T |
|
= 0,106 - |
0, 06 |
= 0, 076мм. |
|||||
|
|
|
|||||||||
3 |
3 |
2 |
|
A |
2 |
|
|
||||
|
|
|
|
3 |
|
|
|||||
|
|
|
|
|
|
|
|
|
|
|