
umm_465
.pdf
l2
l1
Рис. 5.5 Поперечное смещение колеса при вкатывании на рельс
С
αн |
F |
|
F С
Рис. 5.6 Угол набегания αн при вкатывании колеса на рельс
Если αн 0, то Lвк стремится к бесконечности и вероятность схода мала.
Чаще всего случаи схода порожних грузовых вагонов происходят на перегонах из-за вкатывания колеса на рельс на определенных участках железных дорог, имеющих кривые малого радиуса.
Анализ обстоятельств случаев схода показывает, что сходоопасными являются направления порожних вагонопотоков, в большинстве случаев сходы происходят летом, в сухую погоду при скорости движения 60 – 70 км/ч. Среди
50
вагонов, сошедших первыми, преобладают короткобазные вагоны бункерного типа и цистерны.
Установлены характерные неисправности сошедших первыми вагонов:
-нарушение требований к зазорам в скользунах;
-неисправности узла пятник – подпятник;
-завышение и разгрузка фрикционных клиньев в сочетании со сверхнормативным зазором в скользунах;
-непараллельность осей колесных пар в тележке.
В большинстве случаев локомотивная бригада не может своевременно обнаружить сход вагона и с сошедшей колесной парой или тележкой поезд следует до въезда на стрелочный перевод станции, что приводит к тяжелым последствиям схода, большому материальному ущербу и к длительному перерыву
вдвижении поездов.
Вцелом результаты анализа свидетельствуют о необходимости и возможности предотвращения случаев схода подвижного состава путем своевременного обнаружения вагонов, имеющих высокую вероятность схода. Устойчивость от схода колеса с рельса определяется следующими параметрами:
-боковой (рамной) силой;
-перераспределением нагрузки на колеса колесной пары;
-коэффициентом трения между колесом и рельсом;
-углом набегания колеса на рельс (углом атаки);
-углом наклона рабочей части гребня (подрезом гребня).
Эти параметры зависят от технического состояния пути и подвижного состава, скорости движения, режима ведения поезда, наличия смазки рельсов и гребней колес подвижного состава. Техническое состояние ходовых частей вагонов, сошедших первыми, свидетельствует о том, что имеющиеся неисправности ходовых частей приводили к повышению амплитуды колебаний боковой качки вагона, а следовательно, к появлению боковых рамных сил, перераспределению нагрузки на колеса колесной пары и к увеличению угла набегания колеса на рельс.
Наблюдения за работой вагонов, имеющих различные углы набегания колеса на рельс (перекоса оси колесной пары) показали, что «плохие вагоны» с углами перекоса более 5 мрад поступали в текущий ремонт по ремонту ходовых частей в 3,6 раза чаще, чем в среднем по сети дорог, и в 14 раз чаще, чем «хорошие вагоны» с углами перекоса не более 2 мрад. Аналогичное положение наблюдается и со случаями схода вагонов, которые до этого неоднократно поступали в текущий ремонт из-за отказа ходовой части, а в некоторых случаях даже из-за предыдущего схода.
Известны технические средства, позволяющие контролировать параметры ходовых частей вагонов в поездах, а также устройства автоматического обнаружения схода колесной пары. С целью предотвращения случаев схода вагонов сходоопасные направления железных дорог оборудуются техническими средствами контроля ходовых частей грузовых вагонов и датчиками своевременного обнаружения случаев схода колесной пары. В систему контроля должны входить: аппаратура автоматического обнаружения неисправностей ваго-
51
нов, снижающих коэффициент устойчивости колеса от схода, аппаратура автоматического обнаружения схода колесной пары с системой оперативного сообщения локомотивной бригаде, посты безопасности, инструктивнотехнологические документы.
Поставленная цель достигается путем решения комплекса задач:
-определение предельных параметров, определяющих вероятность схода колесной пары: амплитуды колебаний боковой качки, перераспределения нагрузки на колеса колесной пары, угла набегания колеса на рельс;
-разработка средств контроля данных параметров на базе ДИСК-2;
-оборудование сходоопасных направлений подсистемами ДИСК-2-С, обнаруживающими вагоны, имеющие большую вероятность схода, – «сходоопасные вагоны»;
-организация работы с вагонами на ПТО, расположенном перед сходоопасным направлением.
Вопросы для самоподготовки
1.Виды обеспечения технического диагностирования вагона;
2.Какие виды параметров составляют рабочее диагностическое пространство?
3.Что относится к структурным параметрам вагона?
4.Назовите основные функции, выполняемые воздухораспределителем.
5.Приведите примеры производственных и эксплуатационных отказов
вагона.
6.В каких случаях используют характеристики «параметр потока отказов» и «интенсивность отказов»?
7.Дайте классификацию последствиям отказов вагона.
8.Что необходимо диагностировать для предотвращения случаев столкновения поездов по вине вагонного хозяйства?
9.По каким диагностическим признакам можно определить вероятность схода вагона?
52
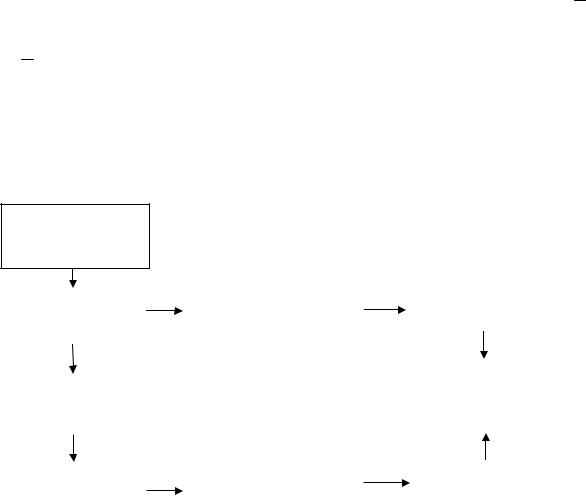
6. ДИАГНОСТИЧЕСКИЕ ПРИЗНАКИ ТЕХНИЧЕСКОГО СОСТОЯНИЯ ВАГОНА
6.1. Общие положения
Задача диагностирования вагона заключается в обработке значений выходных параметров и их соответствия определенной оценке. С целью обоснованного выбора совокупности диагностических показателей В, достаточной для решения задачи по оценке состояния технического объекта, необходимо упорядочить множество диагностических показателей, характеризующих его состояние, т. е. выстроить по порядку, определяемому выбранными критериями.
Диагностическая модель объекта любого типа содержит в явном виде множество Bп (Bп = {b п i } , i =1,2,K, N ) - прямых показателей ( Bп B ), ха-
рактеризующих состояние объекта. Они могут входить в диагностическую модель в виде аргументов или коэффициентов алгебраических и дифференциальных уравнений и других величин, непосредственно присутствующих в модели. В большинстве случаев в связи с технической сложностью или невозможностью, а также с учетом экономической целесообразности приходится из множе-
ства Bп прямых показателей выбирать совокупность
{bпi } , i =1,2,K, m ) для их замеров и оценки в процессе диагностирования. Если Bп = Bп , то введенный порядок позволяет непосредственно разработать
алгоритм и программу диагностирования. В этом случае программа предусматривает последовательность оценки показателей bп i в порядке, определенном
P1 . Обобщенная структура выполнения анализа диагностической модели представлена на рис.6.1
ФОРМИРОВАНИЕ
МНОЖЕСТВА
Bп
|
|
|
|
|
|
ОПРЕДЕЛЕНИЕ |
|
|
|
|
|
|
|
|
|
|
ВЫБОР |
|
УСЛОВИЙ |
|
|
|
ВЫБОР МЕТОДОВ |
|
|
||||||||
|
РАБОТОСПОСОБНОСТИ |
|
|
|
|
|
|
|
|
|
|
|||||
|
|
|
|
ОЦЕНКИ Bп |
|
|
||||||||||
ПОДМНОЖЕСТВА |
|
|
|
|
|
|
||||||||||
|
И |
|
|
|
|
|
||||||||||
|
B |
п |
|
ПРИЗНАКОВ ДЕФЕКТОВ |
|
|
|
|
|
|
|
|
|
|
||
|
|
|
|
|
|
|
|
|
|
|
||||||
|
|
|
|
|
|
|
|
|
|
ПОСТРОЕНИЕ |
|
|||||
ОПРЕДЕЛЕНИЕ |
|
|
|
|
|
АЛГОРИТМА И |
|
|||||||||
РАЗНОСТИ |
|
|
|
|
|
ПРОГРАММЫ |
|
|||||||||
|
|
|
|
|
|
|
|
|
|
ДИАГНОСТИРОВАНИЯ |
|
|||||
S = B п / B п |
|
|
|
|
|
|
||||||||||
|
|
|
|
|
|
|
|
|
|
|
|
|||||
|
|
|
|
|
|
|
|
|
|
|
|
|||||
|
|
|
|
|
|
|
|
|
|
|
|
|
|
|
|
|
|
|
|
|
|
|
ОПРЕДЕЛЕНИЕ |
|
|
|
|
|
|
|
|
|
|
|
|
|
|
|
|
|
|
|
ВЫБОР МЕТОДОВ |
|
||||||
ФОРМИРОВАНИЕ |
|
УСЛОВИЙ |
|
|
|
|
||||||||||
|
|
|
|
|
|
|
|
|
|
|
||||||
МНОЖЕСТВА |
|
РАБОТОСПОСОБНОСТИ |
|
|
|
ОЦЕНКИ Bк |
|
|||||||||
Bк |
|
И |
|
|
|
|
|
|
|
|
|
|
||||
|
ПРИЗНАКОВ ДЕФЕКТОВ |
|
|
|
|
|
|
|
|
|
|
|||||
|
|
|
|
|
|
|
|
|
|
|
|
|
|
|
|
|
Рис.6.1 Обобщенная структура выполнения анализа диагностической модели
53

Если |
|
п Bп и |
|
|
≠Bп , то определяется разность S = Bп − |
|
п и выбирается под- |
|
B |
B |
|||||||
п |
B |
|||||||
множество Bк (Bк |
= {bк j } , j =1,2,K, n ) косвенных показателей. При этом |
мощность множества Bк должна быть такой, чтобы полностью компенсировать
неоцениваемые прямые показатели, т. е. разность S.
Практически невозможно создать такой диагностический комплекс, который обеспечил бы контроль всех возможных нарушений технического состояния вагона. В связи с этим необходимо оценить возможность комплексной оценки технического состояния вагона имеющимися и разрабатываемыми средствами автоматизации контроля и технического диагностирования, определить направление их развития.
6.2. Диагностическая модель грузового вагона
С целью определения элементов конструкции вагона, по которым можно выделить диагностические признаки, характеризующие надежность работы вагона в целом, исследована взаимосвязь между различными неисправностями.
Проведено натурное обследование более тысячи вагонов, поступивших в текущий ремонт, а также вагонов, у которых были показания от устройств автоматического контроля перегрева букс (ДИСК2-Б), неровностей на поверхности катания (ДИСК2-К), устройства контроля подреза гребня колеса, аппаратуры диагностирования упряжного устройства (АДУ), устройства контроля угла набегания колеса на рельс (УНКР).
В ходе обследования вагона, забракованного по неисправности одного из узлов, который будем именовать «системой А», например по неисправности поглощающего аппарата А1, выявлялись неисправности других узлов, «систем», например, трещина корпуса автосцепки А2, рамы вагона Q1, литых деталей тележки Т2, которые могли быть причиной или следствием неисправности системы А, выявленной при техническом обслуживании (осмотре) вагона на ПТО.
По данным обследования определялась условная вероятность наличия на вагоне неисправности j (например состояние системы Вj) в случае выявления на нем i-й неисправности другой системы Аi:
P(B j / Ai )= N (B j Ai ) ,
N(Ai )
где N(ВjАi) – количество вагонов, отказавших по i-й неисправности системы А и имеющих j-ю неисправность системы В;
N(Аi) - общее количество вагонов, отказавших по i-й неисправности системы А.
На вагоне, отцепленном в ремонт по неисправности i, другая неисправность j может быть в следующих случаях:
-случайное совпадение двух неисправностей на одном вагоне;
-неисправность i является причиной появления неисправности j;
54

-неисправность j является причиной появления неисправности i;
-обе неисправности i и j являются следствием других неисправностей
или нарушений технического состояния вагона.
В табл. 6.1 и 6.2 представлены значения условных вероятностей различных неисправностей ходовых частей, автосцепки, кузова и рамы вагона.
Таблица 6.1 Условные вероятности неисправностей ходовых частей
Выявленная |
|
Условная вероятность неисправности, Р( j ) |
|
|||||
неиправность, |
|
|
|
|
|
|
|
|
i |
Износ |
|
Грение |
Ослабле- |
Пол- |
Неиспра- |
|
Тре- |
|
греб- |
|
под- |
ние тор- |
зун, К2 |
вность |
|
щина |
|
ня, К1 |
|
шип- |
цового |
|
рессор, |
|
боко- |
|
|
|
ника, В1 |
крепле- |
|
Т1 |
|
вой ра- |
|
|
|
|
ния под- |
|
|
|
мы, Т2 |
|
|
|
|
шипника, |
|
|
|
|
|
|
|
|
В2 |
|
|
|
|
Износ гребня, |
1 |
|
0,055 |
0,022 |
0,06 |
0,044, |
|
0,006 |
К1 |
|
|
|
|
|
|
|
|
Грение под- |
0,4 |
|
1 |
0,2 |
0,07 |
0,033 |
|
- |
шипника, |
|
|
|
|
|
|
|
|
В1 |
|
|
|
|
|
|
|
|
Ослабление |
0,57 |
|
- |
1 |
0,14 |
- |
|
- |
торцового кре- |
|
|
|
|
|
|
|
|
пления под- |
|
|
|
|
|
|
|
|
шипника, |
|
|
|
|
|
|
|
|
В2 |
|
|
|
|
|
|
|
|
Ползун, |
0,002 |
|
0,05 |
0,005 |
1 |
0,095 |
|
0,08 |
К2 |
|
|
|
|
|
|
|
|
|
|
|
|
|
|
|
|
|
Полагаем, что данные состояния могут возникнуть в период между техническими обслуживаниями вагона на пунктах технического обслуживания. На основании статистических данных знаем частоту отказов вагонов WBj – вероятность отказа вагона по данной неисправности в течение года. Зная годовой пробег L и длину гарантийных участков lуч , определяем вероятность обнаружения неисправности Р(Вj ) на данном вагоне при прохождении очередного
технического обслуживания |
P(Вj ) = |
WBj lуч |
. |
|
|||
|
|
L |
По данным статистического анализа отказов грузовых вагонов определена частота отказов по основным неисправностям, представленная в табл. 6.3.
55
|
|
|
|
|
|
|
|
Таблица 6.2 |
||
Условные вероятности неисправностей автосцепки, кузова и рамы |
||||||||||
|
|
|
|
|
|
|
|
|
||
Выявленная |
Условная вероятность неисправности, Р( j ) |
|||||||||
неисправность |
Трещина |
|
Неисправность |
Трещина |
|
Неисправ- |
|
|||
i |
автосцепки, |
|
поглощающего |
рамы |
|
ность |
|
|||
|
А1 |
|
аппарата, А2 |
вагона, Q1 |
|
кузова, Q2 |
|
|||
Трещина авто- |
1 |
|
0,8 |
|
- |
|
|
- |
|
|
сцепки, А1 |
|
|
|
|
|
|
|
|
|
|
Неисправность |
0,052 |
|
1 |
|
0,031 |
|
|
0,014 |
|
|
поглощающего |
|
|
|
|
|
|
|
|
|
|
аппарата, А2 |
|
|
|
|
|
|
|
|
|
|
Трещина рамы |
- |
|
0,78 |
|
1 |
|
|
- |
|
|
вагона, Q1 |
|
|
|
|
|
|
|
|
|
|
Неисправность |
- |
|
0,62 |
|
- |
|
|
1 |
|
|
Кузова, Q1 |
|
|
|
|
|
|
|
|
|
|
|
|
|
|
|
|
|
|
Таблица 6.3 |
||
|
Средняя частота отказов грузовых вагонов |
|||||||||
|
|
|
|
|
|
|||||
Вид неисправности |
|
Среднее чис- |
|
Вероятность, |
||||||
|
|
|
|
|
ло |
|
|
P(Вj) |
|
|
|
|
|
|
отказов за |
|
|
|
|
|
|
|
|
|
|
|
год, Wj |
|
|
|
|
|
Износ гребня, К1 |
|
|
|
|
0,424 |
|
0,0023 |
|
|
|
Грение, разрушение буксового подшипника, |
|
|
|
|
|
|
|
|||
В1 |
|
|
|
|
0,030 |
|
0,00017 |
|
|
|
Ослабление торцового крепления подшип- |
|
|
|
|
|
|
|
|||
ника, В2 |
|
|
|
|
0,033 |
|
0,00018 |
|
|
|
Ползуны, навары, К2 |
|
|
0,205 |
|
0,0011 |
|
|
|||
Неисправность рессорного подвешивания, |
|
0,066 |
|
0,00036 |
|
|
||||
Т1 |
|
|
|
|
|
|
|
|
|
|
Неисправность литых деталей тележки, Т2 |
|
0,013 |
|
0,000071 |
|
|
||||
Трещины, изгиб автосцепки, А1 |
|
|
0,183 |
|
0,00099 |
|
|
|||
Неисправность поглощающего аппарата, А2 |
|
0,149 |
|
0,00081 |
|
|
||||
|
|
|
|
|
|
|
|
|||
Трещины рамы, Q1 |
|
|
0,085 |
|
0,00047 |
|
|
|||
Неисправности кузова (обрыв стоек, раско- |
|
|
|
|
|
|
|
|||
сов, сдвиг котлов цистерн), Q2 |
|
|
0,625 |
|
0,0034 |
|
|
|||
|
|
|
|
|
|
|
|
|
|
|
Анализируя полученные результаты и функциональную схему вагона можно сделать следующие выводы:
56
-тесная взаимосвязь между износом гребня, дефектами подшипников и рессорного подвешивания обусловлена техническим состоянием тележки – непараллельностью осей колесных пар;
-большинство случаев неисправности автосцепки, рамы и кузова вагона являются следствием неисправности поглощающего аппарата;
-отказы буксовых подшипников, рессорного подвешивания, трещины литых деталей тележек в большинстве случаев вызваны тормозными дефектами – ползунами и наварами.
На основании полученных данных определено количество информации, оценивающее степень взаимосвязи того или иного состояния систем грузового вагона, результаты представлены в табл. 6.4.
Таблица 6.4 Информативность взаимосвязанных систем грузового вагона
Выявленная |
Взаимосвязанная неисправность, |
|
|
неисправ- |
i |
P(j/i)/P(j) |
Ji(j) |
ность, j |
|
|
|
Износ гребня, |
Перегрев, разрушение буксового |
23,91 |
4,57 |
К1 |
подшипника, В1 |
|
|
|
Ослабление торцового крепления |
9,56 |
3,26 |
|
подшипника, В2 |
|
|
|
Неисправность рессорного подве- |
19,1 |
4,25 |
|
шивания, Т1 |
|
|
Ползун, навар, |
Износ гребня, К1 |
1,82 |
0,86 |
К2 |
|
|
|
|
Перегрев, разрушение буксового |
45,45 |
5,5 |
|
подшипника, В1 |
|
|
|
Ослабление торцового крепления |
4,54 |
2,18 |
|
подшипника, В2 |
|
|
|
Неисправность рессорного подве- |
86,36 |
6,43 |
|
шивания, Т1 |
|
|
|
Трещина боковой рамы, Т2 |
72,73 |
6,18 |
|
|
|
|
Неисправность |
Трещина корпуса автосцепки, А1 |
64,19 |
6,00 |
поглощающего |
|
|
|
аппарата, А2 |
Трещина рамы вагона, Q1 |
38,27 |
5,26 |
|
|
|
|
|
Неисправность кузова, Q2 |
17,28 |
4,11 |
|
|
|
|
Техническое состояние вагона может быть оценено интегральными, прямыми и косвенными диагностическими признаками.
Интегральные признаки определяются основными характеристиками вагона R и параметрами процесса функционирования F, прямые признаки опре-
57
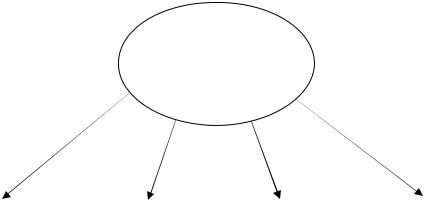
деляются структурными параметрами Е, которые включают и дефекты D, косвенные признаки определяются, в основном, вспомогательными, сопутствующими параметрами V.
Диагностическая модель грузового вагона представлена на рис. 6.2.
ВАГОН
Rв |
|
Fв |
|
Ев |
|
Vв |
Показатели назна- |
|
Сопротивление |
|
Деформация |
|
Уровень шу- |
чения. |
|
Движению. |
|
Кузова. |
|
ма. |
Осность. |
|
Амплитуда и |
|
Целостность |
|
Виброакусти- |
Габарит. |
|
частота |
|
конструкций. |
|
ческие коле- |
База вагона. |
|
Колебаний. |
|
Предельный |
|
бания. |
Осевая нагрузка. |
|
Плавность хода. |
|
износ и де- |
|
Перегрев от- |
Скорость конст- |
|
Рамные силы. |
|
формация де- |
|
дельных узлов |
рукционная. |
|
Перераспреде- |
|
талей. |
|
и деталей. |
Грузоподъемность. |
|
ление нагрузки |
|
Коррозия. |
|
|
Объем кузова. |
|
по колесам. |
|
Плотность |
|
|
Нагрузка на ось. |
|
Удельная тор- |
|
тормозной |
|
|
Коэффициент та- |
|
мозная сила. |
|
системы. |
|
|
ры. |
|
|
|
Нарушение |
|
|
Тормозное нажа- |
|
|
|
габарита под- |
|
|
тие. |
|
|
|
вижного со- |
|
|
Устойчивость от |
|
|
|
става. |
|
|
схода и опрокиды- |
|
|
|
|
|
|
вания. |
|
|
|
|
|
|
|
|
|
|
|
|
|
Рис 6.2. Диагностическая модель грузового вагона
Общие характеристики Rв определяются конструкцией вагона и включают функциональное назначение вагона – показатели назначения (род груза, условия обеспечения его сохранности и др.) и основные технические характеристики (грузоподъемность, габарит, конструкционная скорость и др.)
Параметры процесса функционирования вагона Fв определяются интегральными признаками, по которым можно оценить техническое состояние вагона в целом, к ним относятся сопротивление движению, параметры колебаний, плавность хода и др.
Структурные параметры вагона Ев определяются, в основном, целостностью конструкций сборочных единиц, включая отдельный класс дефектов D.
58

Можно сказать, что параметры функционирования дают обобщенную оценку технического состояния, а структурные параметры детализируют техническое состояние вагона. Вспомогательные параметры Vв используются в качестве косвенных диагностических признаков.
Для каждого узла и сборочной единицы вагона представлены отдельные диагностические модели на рис. 6.3 – 6.7. Тот факт, что для отдельных узлов вагона количественно преобладают вспомогательные параметры, свидетельствует, во-первых, о взаимосвязи различных узлов вагона и, во-вторых, о недоступности ряда узлов и деталей для непосредственного контроля и о низком уровне контролепригодности. Особенно это относится к самым ответственным с точки зрения обеспечения безопасности движения узлам – к буксовому узлу и колесной паре.
БУКСОВЫЙ
УЗЕЛ
Rб |
|
Fб |
|
Еб |
|
Vб |
Тип подшипника. |
|
Сопротивление |
|
Целостность |
|
Перегрев корпуса |
Нагрузка на ось. |
|
качению колес- |
|
сепаратора, |
|
буксы, ступицы ко- |
Радиальный и осе- |
|
ной пары. |
|
колец, роли- |
|
леса. |
вой зазоры. |
|
Перегрев под- |
|
ков, корпуса |
|
Уровень шума. |
|
|
шипника |
|
буксы. |
|
Состояние смазки. |
|
|
|
|
Плотность |
|
Смещение корпуса |
|
|
|
|
торцевого кре- |
|
буксы относительно |
|
|
|
||||
|
|
|
|
пления. |
|
лабиринта. |
|
|
|
|
|
|
Отзвук простукива- |
|
|
|
|
|
|
ния крышки буксы. |
|
|
|
|
|
|
Виброакустические |
|
|
|
|
|
|
колебания. |
|
|
|
|
|
|
Юз, проскальзыва- |
|
|
|
|
|
|
ние колес. |
|
|
|
|
|
|
Выброс смазки через |
|
|
|
|
|
|
лабиринт. |
|
|
|
|
|
|
Искрение в зоне ла- |
|
|
|
|
|
|
биринтного кольца. |
|
|
|
|
|
|
Скольжение колеса |
|
|
|
|
|
|
по рельсу (юз). |
|
|
|
|
|
|
Состояние смазки. |
|
|
|
|
|
|
Запах. |
|
|
|
|
|
|
|
Рис 6.3. Диагностическая модель буксового узла
59