
Записка металлорежущий инструмент
.pdf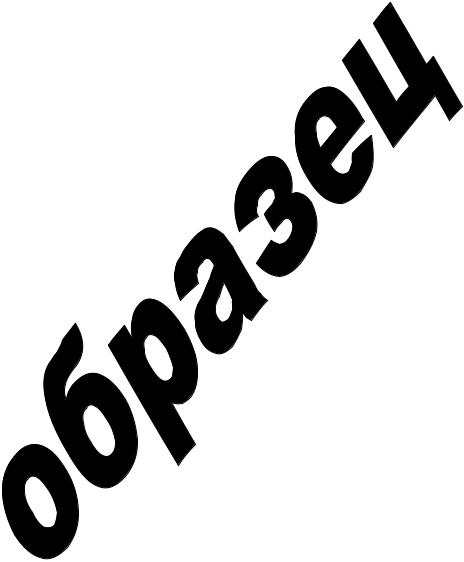
Министерство образования и науки Российской Федерации Марийский государственный технический университет Механико-машиностроительный факультет
Кафедра МиМ
Проектирование металлорежущего инструмента
Расчетно-пояснительная записка к курсовой работе по дисциплине:
«Режущий инструмент» Вариант 26
Выполнил: Студент группы ТМП-31 Кузнецов Д.А.
Проверил: Каширский В.Н.
Йошкар-Ола, 2010
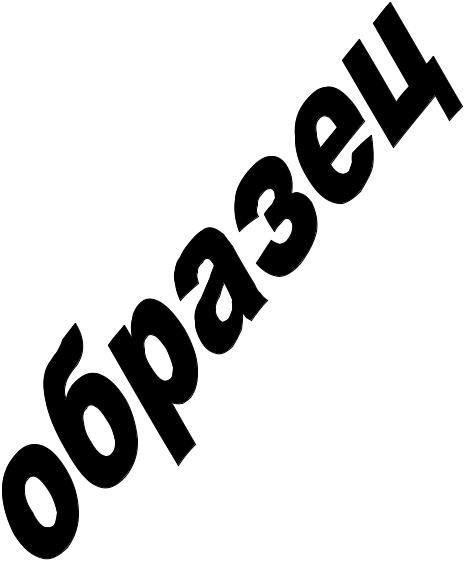
|
Оглавление: |
|
1. |
Введение |
3 |
2. |
Расчет круглого фасонного резца |
4 |
3. |
Расчет круглой протяжки прогрессивной схемы резания |
12 |
4. Список литературы |
20 |
2
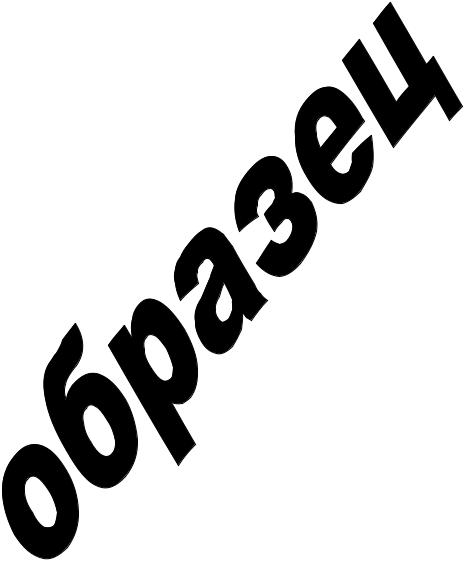
Введение
Целью курсовой работы является закрепление, углубление и обобщение теоретических знаний, полученных при изучении дисциплин «Режущий инструмент», «Резание материалов» и др., а также применение этих знаний в самостоятельной практической работе при решении конкретных производственных задач в области проектирования сложных видов инструмента, дать возможность студентам проявить свои творческие способности, как в конструировании, так и при разработке технологических процессов изготовления этих инструментов.
Курсовая работа преследует задачи научить студента:
-самостоятельно анализировать существующие конструкции режущих инструментов для обработки заданных деталей и выбирать наиболее оптимальные из них;
-разрабатывать принципиально новые конструкции инструмента и определять рациональные условия его эксплуатации;
-обоснованно для конкретных условий обработки выбирать инструментальный материал и назначать оптимальные геометрические параметры режущей части инструмента;
-грамотно рассчитывать инструмент на прочность и жесткость, определять его конструктивные параметры;
-уметь с необходимой точностью определять профиль режущих кромок
инструмента;
-профессионально выполнять рабочие чертежи инструментов, назначать технические условия на их изготовление;
-самостоятельно разрабатывать технологические процессы изготовления инструмента для различных типов производства;
-проводить анализ точности, стойкости и производительности инструмента;
-пользоваться технической литературой, каталогами, справочниками и
ГОСТами при выполнении конкретного технического задания.
3

1.Расчет круглого фасонного резца
1.Задание. Рассчитать и сконструировать круглый фасонный резец для наружного обтачивания фасонной детали, изготавливаемой из прутка.
Материал заготовки – сталь 40Х с в 850 МПа, НВ 230-280.
Условия:
1)деталь изготавливается из пруткового материала;
2)диаметр прутка принимается немного больше максимального размера фасонного профиля детали;
3)заготовку обрабатывают с проточкой канавки под отрезание;
Эскиз детали
L=80мм; d1=40мм; d2=70мм; d3=30мм; l1=10мм; l2=17мм; l3=25мм; r=4мм.
4

2. Выбор инструментального материала |
|
|
|
Для изготовления резца принимаем быстрорежущую сталь Р6М5Ф3 [табл.1.5, |
|||
стр. 16, 4]. Некоторые физико-механические свойства стали Р6М5Ф3: |
|||
плотность 8,15 г/см3; твердость |
HB 269 ; |
после термообработки и 3300...3500 |
|
МПа; HRCэ 65...66 , 625 С [табл.1.4, стр. 14, 4]. |
|
||
3. Подготовка расчётных размеров детали для проектирования |
|||
-0,06 |
(-0,019) |
|
-0,05 |
40 |
70h6 |
|
30 |
|
|
|
1 |
|
|
|
|
6 |
|
|
|
5 |
|
4 |
3 |
|
|
||
10-0,1 |
|
R4 |
2 |
|
17-0,1 |
||
|
|
|
|
|
|
|
25-0,1 |
|
80 |
|
|
На профиле детали обозначаем характерные узловые точки 1, 2, 3, 4, 5, 6. По чертежным диаметрам детали (d1=40-0,06мм; d2=70-0,019мм; d3=30-0,05мм ) определяем соответствующие им расчетные диаметры в характерных точках.
Т.к. допуск по профилю расположен несимметрично, расчетные размеры профиля детали не совпадают с номинальными, т.е.:
d1=40-0,06/2=39,97мм; d2=70-0,019/2=69,991мм; d3=30-0,05/2=29,975мм.
Итак, расчетные размеры узловых точек профиля детали, полученные исходя из исполнительных размеров детали, следующие:
r1=19,985мм; r2=34,996мм; r3=14,988мм; l1=10мм; l2=17мм; l3=25мм.
5
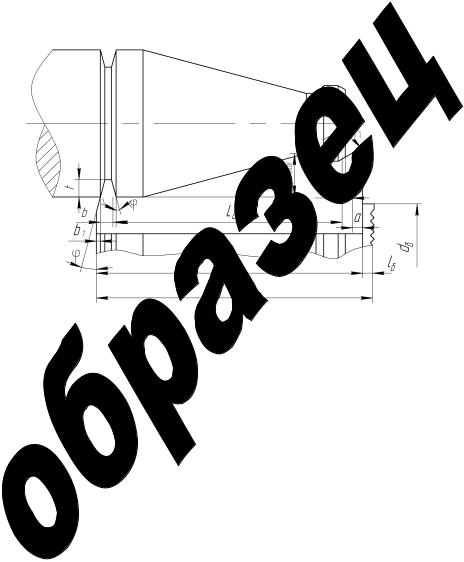
4. Выбор положения базовой линии
Базовую линию проводим через базовую точку 1, лежащую на минимальном радиусе детали rmin= r3 = 14,988мм и располагаем ее параллельно оси детали
ирезца.
5.Расчёт ширины резца
Рис. 3.13. Дополнительные режущие кромки фасонных резцов при
обработке деталей из прутка
При изготовлении детали из пруткового материала ширина резца :
Lp lд 2b1 b a , [стр. 63, 3]
где lä – длина детали, lä = 80 мм; b1 – величина перекрытия торца детали, b1
= 1 мм; b – ширина лезвия под отрезку детали, b = 5 мм; a – ширина дополнительного упрочняющего лезвия, a = 2 мм.
LP = 80 + 2 + 5 + 2 = 89 мм.
Общая ширина резца L0 Lp lá ,
где lá – ширина буртика с рифлениями, lá = 5 мм
L0 = 89 + 5 = 94 мм.
6
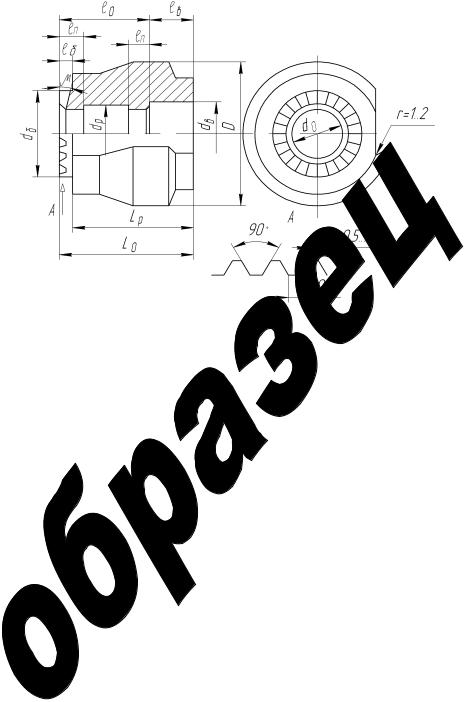
6. Расчёт диаметра посадочного отверстия
Рис. 3.14. Конструктивное оформление посадочного отверстия и
буртика с рифлениями
Диаметр посадочного отверстия:
d0 0,6Lp0,33Pz0,38 ,
где Pz – сила резания, Pz PóäLp ; Póä – удельная сила резания в даН, зависящая
от подачи при фасонном точении. Рекомендуемая для LP = 89 мм и d=70 мм подача S = 0,025…0,05 мм/об [табл.3.3, 3]. Принимаем S = 0,03 мм/об, для которой Póä = 15 даН [табл.3.2, 3]. Тогда
Pz PóäLp = 15 89 = 1335 даН,
d0 0,6Lp 0,33Pz 0,38 0,6 890,33 13350,38 40.7 мм.
Из стандартного ряда принимаем d0=40 мм.
Конструктивные элементы посадочного отверстия:
dв 1,5d0 1,5 40 60мм
lв (0,25...0,5)L0 (0,25...0,5) 94 23,5...47 мм; Принимаем lв=30
ширина шлифованной части отверстия lП 0,25(L0 lв ) 0,25(94 30) 16 мм;
диаметр расточки d p d0 2 42 мм.
7
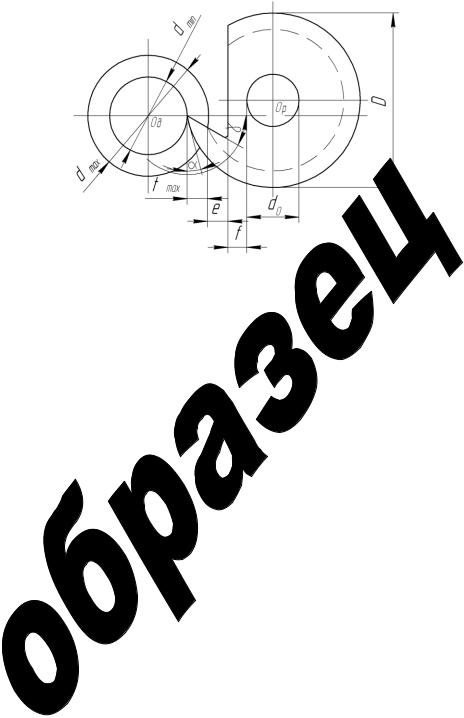
7. Определение наружного диаметра резца
Рис. 3.15. Определение наружного диаметра круглого резца
Наружный диаметр резца
D 2( tmax e f d0 / 2 ), [стр. 67, 3]
где tmax – глубина профиля детали;
tmax rmax rmin 34,996 14,988 20,008 мм;
e 5 мм– размер, обеспечивающий достаточное пространство для схода и размещения стружки;
f 0,25d0 0,25 40 10 мм f – толщина стенки резца.
Тогда D 2(20,008 5 10 20) 110,016 мм.
Принимаем из нормального ряда D 110 мм.
8. Назначение геометрических параметров лезвия резца Оптимальные значения переднего и заднего углов назначаются для базовой
точки 1, |
лежащей на уровне центра |
Oä вращения детали. При обработке |
|
стали |
800...1100МПа |
принимаем |
1 12 и 1 8 [таб.3.6, 3]. |
|
в |
|
|
Задний угол обеспечивается за счет смещения центра резца выше центра
детали на величину h |
p |
R sin 55sin 8 7,65 |
мм. |
|
1 |
|
|
|
|
|
8 |
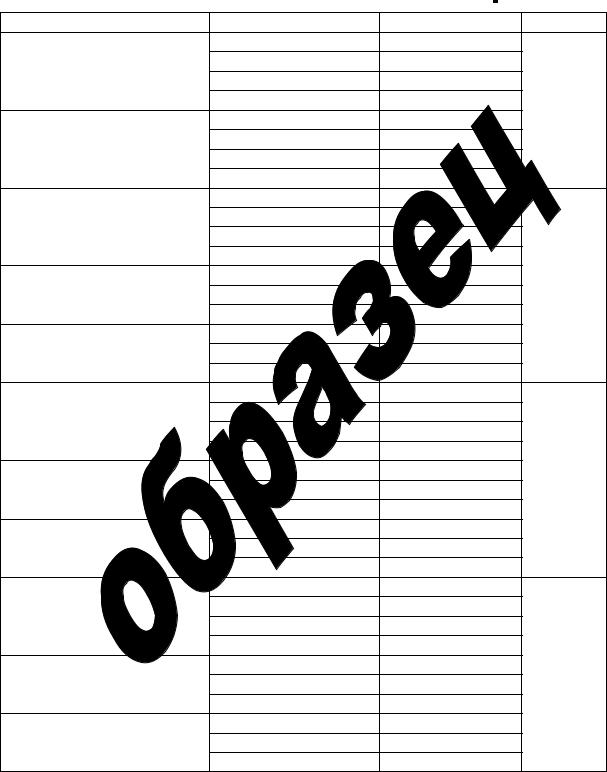
9. Расчёт профиля круглого резца в передней плоскости
Определение размеров С2 …С5 профиля в передней плоскости [таб.25,стр. 37, 3]
Расчетная формула |
Обозначение параметра |
Величина |
Точка |
|
|
r1 |
14,988 |
|
|
hu=r1·sin γ1 |
γ1 |
12,000 |
|
|
sin γ1 |
0,208 |
|
||
|
|
|||
|
hu |
3,116 |
1 |
|
|
r1 |
14,988 |
||
|
|
|||
A1=r1·cos γ1 |
γ1 |
12,000 |
|
|
cos γ1 |
0,978 |
|
||
|
|
|||
|
A1 |
14,660 |
|
|
sin γ2=hu/r2 |
hu |
3,116 |
|
|
|
r2 |
19,985 |
|
|
|
sin γ2 |
0,156 |
|
|
|
γ2 |
8,971 |
|
|
|
r2 |
19,985 |
6 |
|
A2=r2·cos γ2 |
cos γ2 |
0,988 |
||
|
||||
|
A2 |
19,741 |
|
|
|
A2 |
19,741 |
|
|
C2=A2-A1 |
A1 |
14,660 |
|
|
|
C2 |
5,080 |
|
|
|
hu |
3,116 |
|
|
sin γ3=hu/r3 |
r3 |
30,996 |
|
|
sin γ3 |
0,101 |
|
||
|
|
|||
|
γ3 |
5,770 |
|
|
|
r3 |
30,996 |
3 |
|
A3=r3·cos γ3 |
cos γ3 |
0,995 |
||
|
||||
|
A3 |
30,839 |
|
|
|
A3 |
30,839 |
|
|
C3=A3-A1 |
A1 |
14,660 |
|
|
|
C3 |
16,178 |
|
|
|
hu |
3,116 |
|
|
sin γ4=hu/r4 |
r4 |
34,996 |
|
|
sin γ4 |
0,089 |
|
||
|
|
|||
|
γ4 |
5,109 |
|
|
|
r4 |
34,996 |
2,4,5 |
|
A4=r4·cos γ4 |
cos γ4 |
0,996 |
||
|
||||
|
A4 |
34,857 |
|
|
|
A4 |
34,857 |
|
|
C4=A4-A1 |
A1 |
14,660 |
|
|
|
C4 |
20,197 |
|
9
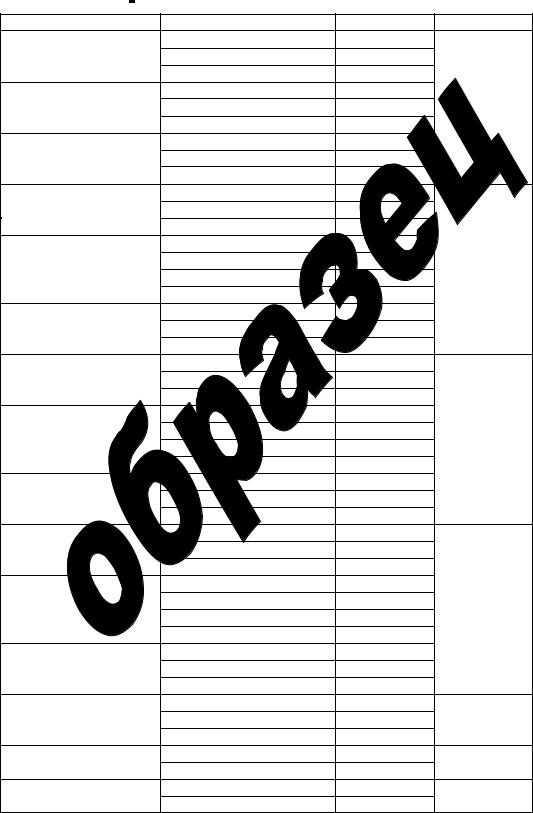
10. Расчёт профиля круглого резца в нормальной плоскости
Определение радиусов R2…R5 и размеров t2…t5 профиля резца в нормальном сечении [стр. 41, 3]
Расчетная формула |
Обозначение параметра |
Величина |
Точка |
|
|
α1 |
8,000 |
|
|
ψ1=γ1+α1 |
γ1 |
12,000 |
|
|
|
ψ1 |
20,000 |
|
|
|
R1 |
55,000 |
|
|
Hp=R1·sin ψ1 |
sin ψ1 |
0,342 |
1 |
|
|
Hp |
18,811 |
|
|
B1=R1·cos ψ1 |
R1 |
55,000 |
|
|
|
cos ψ1 |
0,940 |
|
|
|
B1 |
51,683 |
|
|
|
B1 |
51,683 |
|
|
B2=B1-C2 |
C2 |
5,080 |
|
|
|
B2 |
46,603 |
|
|
|
Hp |
18,811 |
|
|
tg ψ2=Hp/B2 |
B2 |
46,603 |
6 |
|
tg ψ2 |
0,404 |
|||
|
|
|||
|
ψ2 |
21,981 |
|
|
|
Hp |
18,811 |
|
|
R2=Hp/sin ψ2 |
sin ψ2 |
0,374 |
|
|
|
R2 |
50,256 |
|
|
|
B1 |
51,683 |
|
|
B3=B1-C3 |
C3 |
16,178 |
|
|
|
B3 |
35,505 |
|
|
|
Hp |
18,811 |
|
|
tg ψ3=Hp/B3 |
B3 |
35,505 |
3 |
|
tg ψ3 |
0,530 |
|||
|
|
|||
|
ψ3 |
27,916 |
|
|
|
Hp |
18,811 |
|
|
R3=Hp/sin ψ3 |
sin ψ3 |
0,468 |
|
|
|
R3 |
40,180 |
|
|
|
B1 |
51,683 |
|
|
B4=B1-C4 |
C4 |
20,197 |
|
|
|
B4 |
31,487 |
|
|
|
Hp |
18,811 |
|
|
tg ψ4=Hp/B4 |
B4 |
31,487 |
2,4,5 |
|
tg ψ4 |
0,597 |
|||
|
|
|||
|
ψ4 |
30,855 |
|
|
|
Hp |
18,811 |
|
|
R4=Hp/sin ψ4 |
sin ψ4 |
0,513 |
|
|
|
R4 |
36,678 |
|
|
|
R1 |
55,000 |
|
|
t2=R1-R2 |
R2 |
50,256 |
6 |
|
|
t2 |
4,744 |
|
|
t3=R1-R3 |
R3 |
40,180 |
3 |
|
t3 |
14,820 |
|||
|
|
|||
t4=R1-R4 |
R4 |
36,678 |
2,4,5 |
|
t4 |
18,322 |
|||
|
|
10