
Записка металлорежущий инструмент
.pdf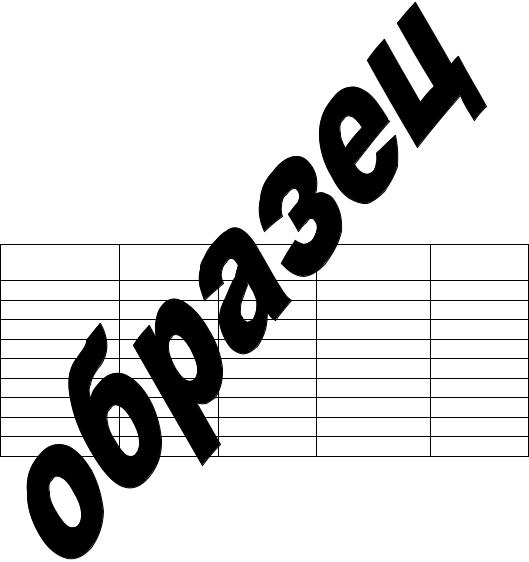
11. Исследование геометрических параметров спроектированного резца
Режущая способность инструмента определяется нормальными углами,
поэтому рассчитываем углы x и x , пересчитываем в углы N x и N x ,
расположенные в плоскостях, проходящих через узловые точки нормально к участкам режущей кромки.
Анализ передних углов x и задних углов x в узловых точках режущей
кромки резца в плоскости, перпендикулярной его оси.
№ точки |
sin γx=(r1/rx)·sin γ |
γx |
tg βx=Cx·sin ψ1/(R1-Cx·cos ψ1) |
βx |
αx=α+γ-γx+βx |
1 |
0,208 |
12,000 |
0,000 |
|
8,000 |
6 |
0,156 |
8,971 |
0,035 |
1,981 |
13,011 |
3 |
0,101 |
5,770 |
0,186 |
10,541 |
24,771 |
2,4,5 |
0,089 |
5,109 |
0,275 |
15,378 |
30,269 |
Анализ передних N |
x |
углов в узловых точках режущей кромки резца |
|||
|
|
|
|
|
|
в нормальных плоскостях |
|
|
|
||
№ узловой |
|
γx |
sin φx |
tg γNx=tg γx·sin |
γNx |
точки |
|
φx |
|||
|
|
|
|
||
1 |
|
12,000 |
0,733 |
0,156 |
8,856 |
2 |
|
5,109 |
0,733 |
0,066 |
3,750 |
2' |
|
5,109 |
1,000 |
0,089 |
5,109 |
3 |
|
5,770 |
0,000 |
0,000 |
0,000 |
4 |
|
5,109 |
1,000 |
0,089 |
5,109 |
4' |
|
5,109 |
0,000 |
0,000 |
0,000 |
5 |
|
5,109 |
0,000 |
0,000 |
0,000 |
5' |
|
5,109 |
0,805 |
0,072 |
4,117 |
6 |
|
8,971 |
0,805 |
0,127 |
7,244 |
Анализ задних Nx углов в узловых точках режущей кромки резца в
нормальных плоскостях
№ узловой точки |
αx |
sin φx |
tg αNx=tg |
αNx |
|
αx·sin φx |
|||||
|
|
|
|
||
1 |
8,000 |
0,733 |
0,103 |
5,882 |
|
2 |
30,269 |
0,733 |
0,428 |
23,163 |
|
2' |
30,269 |
1,000 |
0,584 |
30,269 |
|
3 |
24,771 |
0,000 |
0,000 |
0,000 |
|
4 |
30,269 |
1,000 |
0,584 |
30,269 |
|
4' |
30,269 |
0,000 |
0,000 |
0,000 |
|
5 |
30,269 |
0,000 |
0,000 |
0,000 |
|
5' |
30,269 |
0,805 |
0,470 |
25,171 |
|
6 |
13,011 |
0,805 |
0,186 |
10,540 |
11

2.Расчет круглой протяжки прогрессивной схемы резания Исходные данные:
Длина протяжки не более1500 мм
Производство крупносерийное
Отверстие под протягивание подготовлено сверлом
Диаметр обрабатываемого отверстия d=50Н8
Диаметр отверстия под протягивание d0=48,7 мм
Длина протягивания Lд=100мм
Тяговое усилие протяжного станка Q=40 тс (392,3 кН)
Наибольший ход каретки протяжного станка Lст=1600 мм
Обрабатываемый материал ст. 30 НВ=179
12
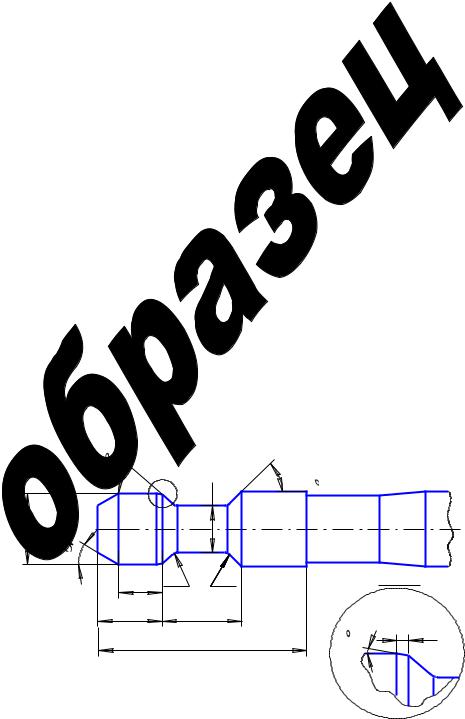
1.Устанавливаем группу обрабатываемости по табл. 5.1 сталь с твердостью НВ= 179 относится к I-й группе обрабатываемости.
2.Устанавливаем группу качества протянутой поверхности. Согласно табл. 5.2 обработанная поверхность с полем допуска по 8-му квалитету (D = 50Н8 мм) относится к 2-й группе качества.
3.Определяем по формуле (5.4) припуск на протягивание
4.Необходимые технические данные протяжного станка: Q = 392,3 кН,
lст = 1600 мм.
5.Выбираем материал режущей части протяжки по табл. 5.6. Для I-й
группы обрабатываемости и крупносерийного типа производства: Р6М5.
6.В качестве материала хвостовика принимаем сталь 40Х с твердостью после термообработки HRCЭ 42…56.
Диаметр хвостовика:
Dхв= D0 – 0,5 = 48,7 – 0,5 = 48,2 мм. [3,156]
7.По ГОСТ 4044-70 принимаем размеры круглого хвостовика протяжки
(табл. 5.7):
Dхв= 45е8 мм; dхв= 34с11 мм; с = 1,5; Lхв= 160 мм; l2 = 32 мм; l3 = 32 мм; l4 = 20 мм; r1 = 0,5 мм; r2 = 2,5 мм; α = 30º; Fхв= 907,9 мм2.
|
1 |
|
5 |
5 |
|
|
4 |
|
|
|
|
4 |
|
dхв |
|
Dхв |
|
|
|
l4 |
r1 |
r2 |
1 |
l2 |
|
l3 |
с |
|
|
Lxв |
|
|
|
0 |
|
|
|
|
|
|
|
|
1 |
13
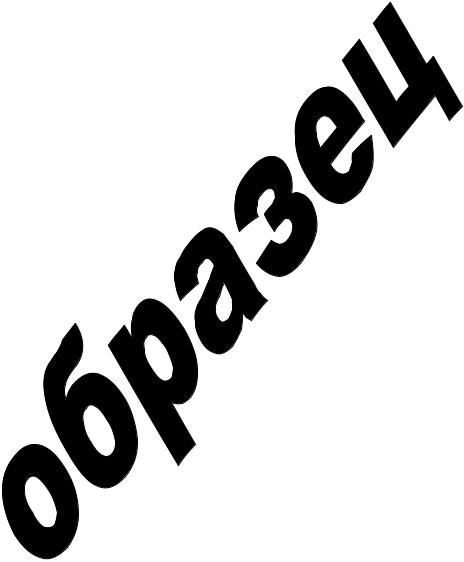
8. Сила, допустимая прочностью хвостовика, рассчитывается по формуле
(5.5):
Pхв р хв Fхв 250 907,9 226,975 кН,
где [σр]хв=250 МПа.
9. Диаметр шейки:
Dш= Dхв – (0,3…0,5) = 45 – 0,5 = 44,5 мм.
10.Длина переходного конуса (табл. 5.8): Lпк = 20 мм, так как D=50 мм.
12. Диаметр передней направляющей Dпн принимают равным D0 min с
полем допуска е8:
Dпн= D0 min = 48,7e8 мм.
Длина передней направляющей зависит от D и l: при l/D 1,5, имеем l/D = 100/50 = 2 1,5 Lпн= 0,75l = 0,75*100 мм=75 мм.
13. Расстояние от торца протяжки до первого зуба по формуле (5.6):
L1 l1 l2 l3 l 25 ; [3,159]
где l1 = 160 мм (Dхв= 45 мм); l2 = 25 мм; l3 = 40 мм; l = 100 мм;
Подставляя в формулу (5.6) цифровые данные, получим
L1 = 160 + 25 + 40 + 100 + 25 = 350 мм.
14. Определяем диаметр и длину задней направляющей (табл. 5.9):
Dзн = Dmin с полем допуска f7. При диаметре протягиваемого отверстия D = 50Н8 имеем Dmin = 50 мм, следовательно Dзн = 50f7 мм; длина задней направляющей Lзн = 40 мм, так как l = 100 мм.
15.Выбираем прогрессивную схему резания.
16.Назначаем геометрические параметры зубьев протяжки.
Передний угол любого инструмента зависит от обрабатываемого
материала. По табл. 5.10 для обработки стали, относящейся к I-й группе обрабатываемости, принимаем:
для черновых и переходных зубьев |
; |
для чистовых и калибрующих зубьев |
; |
|
14 |
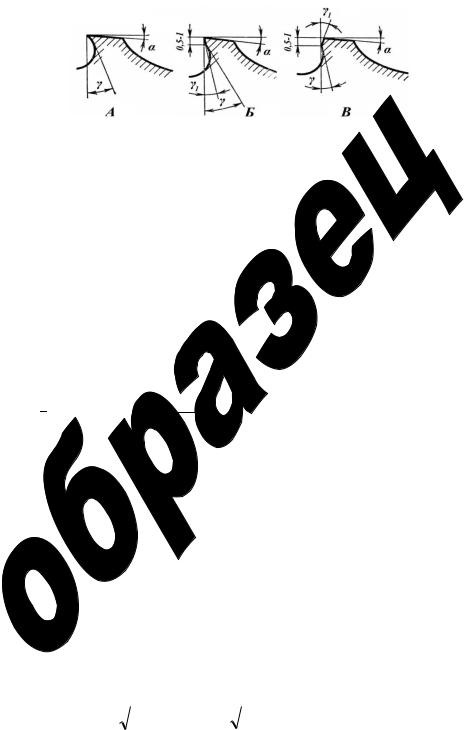
Форма заточки передней поверхности - А.
Рис.5.10. Формы заточки по передней поверхности зуба:
По табл. 5.11 выбираем задние углы для режущих и переходных зубьев круглой протяжки, для отверстий 8-го квалитета - α = 3º ± 30′. Для чистовых
зубьев всех типов протяжек α = 2º ± 30′, а для калибрующих α = 1º ± 30′.
17. Выбираем скорость резания при протягивании сталиа I-й группы
обрабатываемости. По табл. 5.12 при массовом типе производства
Vр = 9 м/мин.
18.Предварительное расчетное значение шага режущих зубьев по формуле
(5.28) |
√ |
( |
) |
|
√ |
19.Число одновременно работающих зубьев по формуле (5.29)
Zip = l / tp + 1 = 100 / (15…19) + 1= 6…8.
20.Для черновых рекомендуемая технологически допустимая подача на группу зубьев Szc для обработки стали I-й группы обрабатываемости со
скоростью резания V = 9 м/мин (табл. 5.25) |
|
|||||
|
|
Szc = 0,2 мм. |
|
|||
21.Глубина стружечной канавки |
hp для принятой подачи Szc=0,2 мм |
для |
||||
сливной стружки по формуле (5.30): |
|
|
|
|
||
|
|
|
|
|
|
|
hp 1,128 KlS zc 1,128 |
|
2,0 100 0,2 7,13 мм, |
|
|||
где K – коэффициент заполнения стружечной канавки; по табл. 5.27 при |
tp = |
15…19 и Szc 0,1 мм K = 2,0.
22.Принимаем глубину стружечной канавки h = 8 мм и для этой глубины по табл.5.14 выбираем остальные размеры стружечной канавки:
шаг черновых зубьев tчерн = 20 мм;
15

шаг чистовых и калибрующих зубьев tчист = 15 мм;
стружечная канавка: g =8 мм; r = 4 мм; R = 12 мм; Fк = 50,3 мм2.
23.Уточняем число одновременно участвующих в работе зубьев по
формуле 5.32 Zi = l / tчерн =100 / 20 = 5.
24.Подача, допустимая по размещению стружки в канавке по формуле
(5.33): Szк = Fк / Kl = 50,3 / (2,0 100) = 0,252 мм.
Обязательно должно соблюдаться условие Szc ≤ Szк:
Szc = 0,2 Szк = 0,252 ,
то есть условие размещения стружки в канавке соблюдается.
25.Тяговая сила станка с учетом его износа
Pст = 0,8Q = 0,8 392,3 = 313,840 кН.
Сила, допускаемая прочностью хвостовика по формуле (5.36)
Pхв = [σp]хв Fхв = 250 907,9 =226,975 кН;
Сила, допускаемая прочностью протяжки в опасном сечении по впадине перед первым зубом по формуле (5.37):
Pоп = [σp]им Fоп = 400 2635,7 =1054,277 кН,
где [σp]им – допустимое напряжение для инструментального материала; по табл. 5.22 [σp]им = 400 МПа.
Площадь опасного сечения по формуле (5.26)
Fоп = 0,785 π (D1 – 2 h)2 = 0,785 3,14 (48,7 – 2 8)2 = 2635,7 мм2;
где D1- диаметр первого зуба, |
D1= |
Dпн= 48,7мм. |
|
Наименьшую из этих трех |
сил |
(Pст, Pхв, Pоп) |
принимаем в качестве |
максимально допустимой силы резания |
|
Pmax = Pхв = 226,975 кН.
26.Предварительно количество зубьев в черновой секции: Zco1 = 2 – в первой секции;
в остальных секциях по формуле (5.38):
Zco Cp DSzcx Zi K Kc Ku / Pmax 6123 50 0,20,85 5 0,85 1 1/ 226975 1,46 2
, где Cp = 6123, x = 0,85 (табл. 5.28); Kγ = 0,85, Kc = 1, Ku = 1 (табл. 5.20).
16
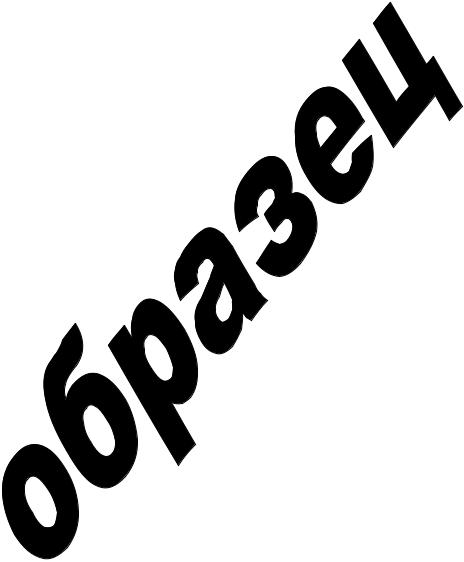
27.Определяем подачу, допустимую максимальным усилием резания по формуле (5.39) :
Szp Pmax Zco / Cp DZi K Kc Ku 1/ x (226975 2 /(6123 50 5 0,85 1 1))1/ 0,85 0,290 .
28.Должно соблюдаться условие (5.40): Szp ≥ Szc .
Имеем Szp = 0,290 Szc = 0,2 , т.е. условие соблюдается.
Так как соблюдаются оба условия (5.34) и (5.40), то окончательно принимаем для проектируемой протяжки максимальную допустимую подачу
Szo = Szc = 0,2 мм.
29.Распределение припуска на протягивание между черновыми,
переходными и чистовыми зубьями:
полный припуск А = 1,339 мм,
припуск на переходные зубья Ап = 0,34 мм (табл. 5.29),
припуск на чистовые зубья Ач = 0,10 мм (табл. 5.30).
Припуск на черновые зубья по формуле (5.42):
A0 = A – (An + Aч) = 1,339 – (0,34 + 0,10) = 0,899 мм.
30.Число секций черновых зубьев по формуле (5.43):
i0 = A0 / 2Szo = 0,899 / 2 0,2 =2,25 Принимаем i0 = 2. Аост=А0-2Szoio=0,899-0,8=0,099 мм
Аост/2=0,05мм<0,08мм, значит остаточный припуск прибавляем к припуску переходных зубьев: Ап = 0,34 + 0,099 = 0,439 мм
31.Число черновых зубьев протяжки по формуле (5.45):
Z0 = Zcо1+ i0 Zco= 2+2 2= 6. 32.Общее число всех зубьев протяжки по формуле (5.46):
Z Z0 Z n Zч Z к =6+6+10+6=28,
где Zn = 6 - число переходных зубьев (табл. 5.29);
Zч = 10 и Zк = 6 - число чистовых и калибрующих зубьев (табл. 5.30).
33.Длина рабочей части протяжки по формуле (5.47):
Lp L0 Ln Lч Lк t р Z0 Zn tч tк 20*12+151+90=481мм,
где tч = Lч и tк = Lк – длины чистовой и калибрующей частей протяжки.
17
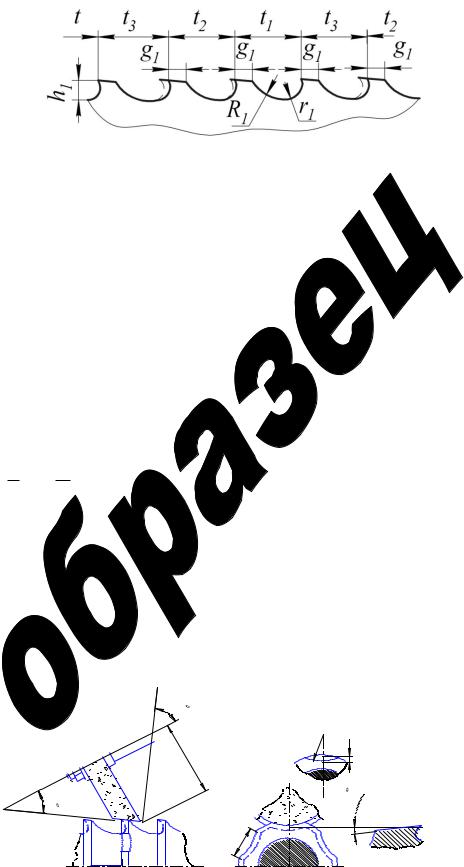
Рис.5.13. Неравномерные шаги чистовых и калибрующих зубьев протяжки
На чистовой и калибрующей частях протяжки шаги зубьев переменные t1, t2 и t3. Согласно табл. 5.17 при шаге режущих зубьев t = 20мм мы имеем t1 = 14 мм, t2 = 15 мм и t3 = 16 мм. Тогда:
Lч = tч = 3*(16+15+14)+16=151 мм.
Lк = tк = 2*(16+15+14)=90
34.Количество выкружек на прорезных черновых зубьях по формуле (5.48)
N D / Zcoв 3,14 50 / 2 8.49 9.25 .
Округляя N до ближайшего большего четного числа, получим N=10. При
этом в 1,2D 1,2
50 8,49 мм.
35.Ширина выкружки по формуле (5.51)
a0 D Zco 1 / NZco 3,14 50 2 1 /(10 2) 7,85 мм=>8мм.
36.По табл. 5.32 принимаем радиус шлифовального круга Rк= 25 мм. Тогда радиус выкружек:
3
5
Rв Rк / cos 25/ cos 35 30 мм.
5 5
|
в |
c |
R |
R |
|
к |
|
|
6= в
a
Рис.5.19. Радиусы выкружек и шлифовального круга
18

37.Число выкружек для переходных и чистовых зубьев рассчитывают по формуле (5.52)
Nч 1,45D 1,45
50 10,25=>10.
38.Ширина выкружек при D=50 мм и Nч=10 согласно данным табл. 5.33 –
ап=6,0 мм. Эти выкружки наносим на каждом переходном и чистовом зубьях,
располагая их в шахматном порядке, шлифовальным кругом радиусом Rк=25
мм (табл. 5.32).
39.По выполненным расчетам разрабатываем рабочий чертеж спроектированной цилиндрической протяжки прогрессивной схемы резания
(рис. 5.21). Технологические условия на изготовление протяжки назначаем согласно ГОСТ 28442-90.
19
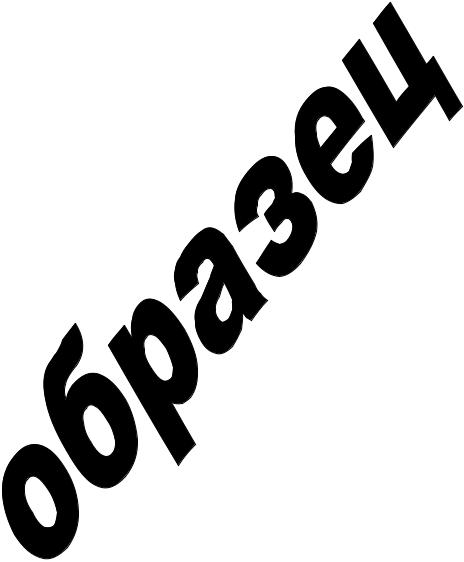
5.Список литературы
1.Проектирование металлорежущих инструментов. Метчики, развертки,
фасонные резцы: Методические указания для выполнения курсовых работ. /Сост. А.Е. Беляев, И.И. Ятманов.- Йошкар-Ола: МПИ, 1983-44с.
2.Проектирование металлорежущих инструментов. Протяжки:
Методические указания для выполнения курсовых работ. /Сост. А.Е.
Беляев, И.И. Ятманов.- Йошкар-Ола: МПИ, 1983-44с.
3.Режущий инструмент: технический альбом / сост. Е.Н.Трембач. –
Йошкар-Ола: Марийский государственный технический университет,
2008.-268с.
4.Справочник конструктора-инструментальщика / Под общ.ред.
В.И.Баранчикова. -М.:Машиностроение, 1994.-560с.
5.Справочник инструментальщика / И.А.Ординарцев, Г.В.Филиппов, А.Н.
Шевченко и др.; Под общ.ред. И.А.Ординарцева. –Л.:Машиностроение.
Ленингр.отд-ние, 1987.-846с.
6.Трембач Е.Н. и др. Резание металлов: Учебное пособие/ Е.Н.Трембач,
Г.А.Мелетьев, А.Г.Схиртладзе, Л.Н.Шобанов. – Йошкар-Ола: МарГТУ,
2005.-396с.
20