
АПП курсовик / 5551 АПП / Курсовой проект / Обработка на станках с ЧПУ / Токарные станки / Технологическая подготовка токарных станков с ЧПУ
.pdf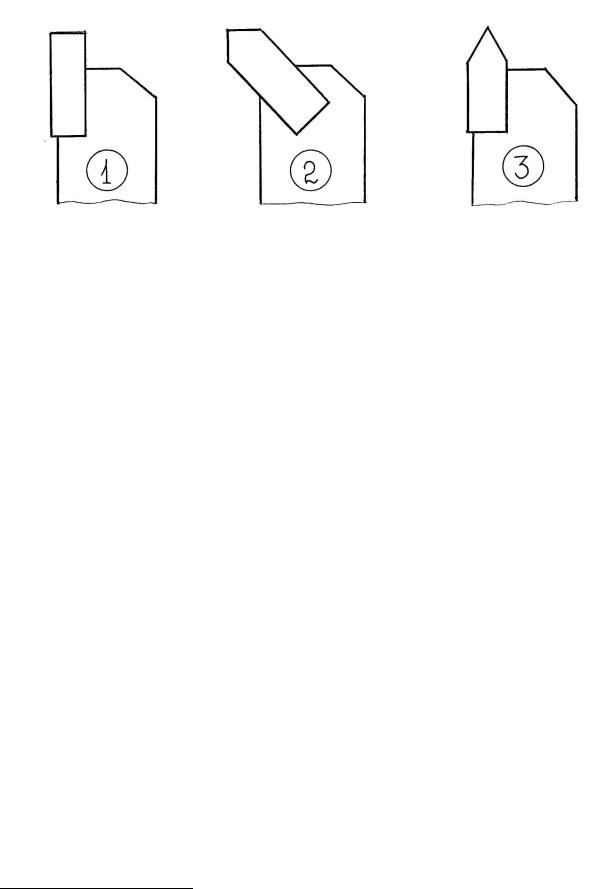
Рис. 2.23. Резцы для обработки дополнительных поверхностей
При обработке прямоугольных канавок ширину резца выбирают по самой узкой канавке, которую обрабатывают за один рабочих ход. Более широкие канавки точат за несколько ходов. При этом возможны два варианта обработки:
-без перекрытия (рис. 2.24, а);
-с перекрытием (рис. 2.24, б).
В первом варианте после каждого рабочего хода резец выводится из канавки и смещается по оси Z на величину B , равную ширине резца H . Однако, в местах стыков рабочих ходов на дне канавки возможны дефекты обработки в виде нарушения шероховатости или небольших обечаек.
Во втором варианте резец работает по всей ширине только на первом ходе. Остальные ходы делают с перекрытием lп = 1 − 2 мм. При этом повы-
шается качество обработки и улучшаются условия работы резца.
Перед выводом резца из канавки после каждого рабочего хода рекомендуется выдерживать паузу (на 1-2 с) для зачистки дна канавки. Если этого не делать, то на дне канавки образуется заусенец с толщиной, равной величине подачи на один оборот шпинделя.
Последний ход режется на всю ширину резца только в том случае, если ширина канавки L кратна ширине резца H
51
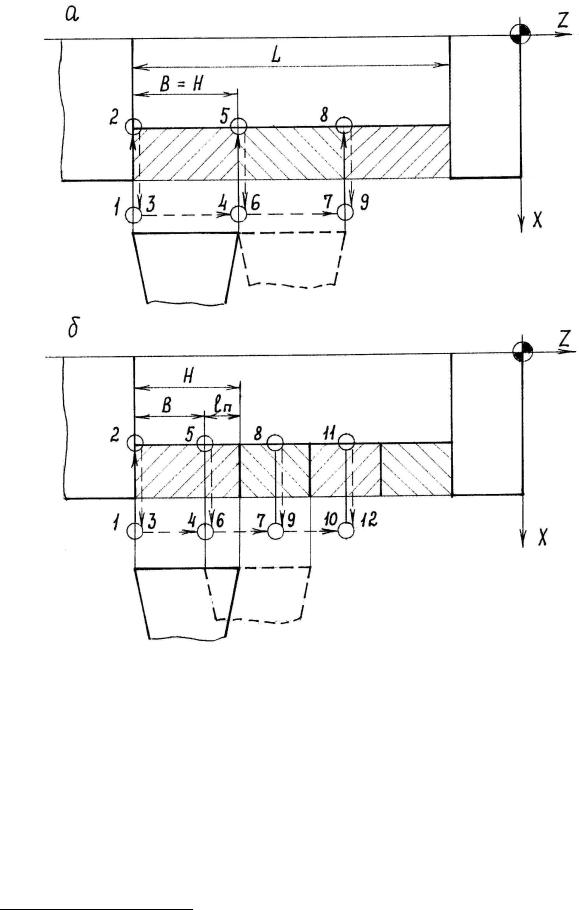
Рис. 2.24. Обработка прямоугольной канавки за несколько ходов: а – без перекрытия; в – с перекрытием
При повышенных требованиях к точности и шероховатости рекомендуется выполнять чистовую обработку профиля канавки, оставляя для этого припуск t = 0,2 − 0,5 мм (рис. 2.25). Обработка производится за два встреч-
ных хода (1-2-3 и 5-6-7) с перекрытием lп .
Обработка за один ход по всему контуру канавки недопустима по условиям работы канавочного резца
52
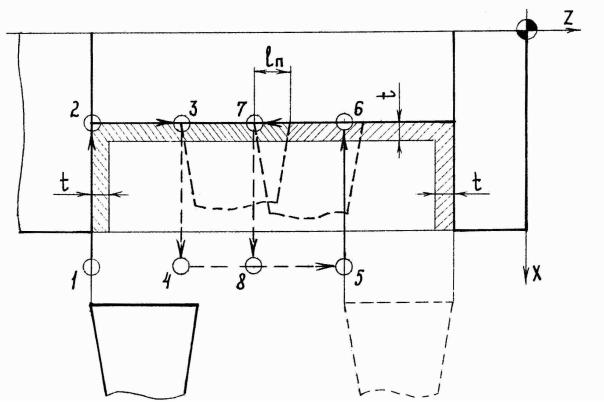
Рис. 2.25. Чистовая обработка профиля канавки
На токарных станках с ЧПУ появляется возможность обрабатывать прямоугольным резцами канавки другой формы. Обработка выполняется в два этапа. Сначала прорезается центральная зона прямоугольной формы. Затем обрабатывают боковые участки с подачей по направлению ко дну канавки. На рис. 2.26 показаны примеры обработки канавок со скошенными и закругленными краями при условии, что ширина боковых зон lб не превышает ширины резца H . Траектория резца содержит здесь три рабочих хода:
-прорезка центральной зоны (1-2);
-обработка правого края (4-5-6);
-обработка левого края (8-9-10).
53
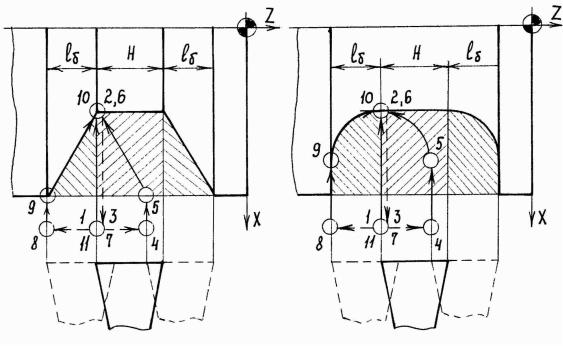
Рис. 2.26. Обработка канавок различной формы прямоугольными резцами
Некоторые характерные примеры обработки канавок представлены на рис. 2.27:
1.Канавки с фасками под стопорные и уплотнительные кольца (рис. 2.27, а). Здесь рекомендуется оставлять припуск t под чистовую обработку краев канавки, совмещая ее с обработкой фасок.
2.Канавки под шкивы и сальниковые уплотнения (рис. 2.27, б). Здесь, зачастую, ширина боковой зоны lб превышает ширину резца H . Поэтому края канавки приходится обрабатывать за несколько ходов.
3.Канавки, сопряженные с торцовой поверхностью (рис. 2.27, в). При предварительной обработке контурным резцом здесь рекомендуется оставлять припуск t = 0,5 −1 мм на торец под кана-
вочный резец.
4.Угловые канавки под шлифовальный круг (рис. 2.27, г). В отличие от прямоугольных резцов рабочая подача здесь всегда идет
54
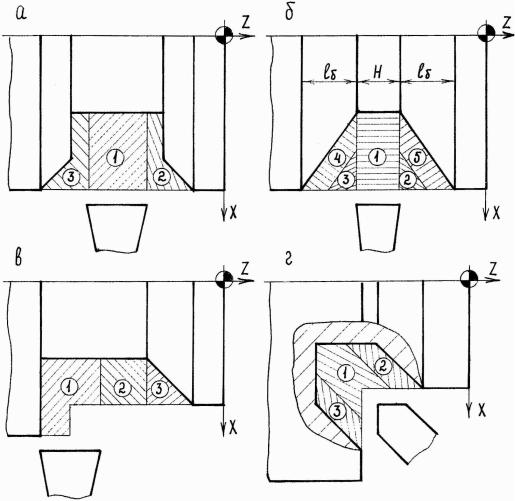
по обеим осям (как правило, под углом 45°). Узкие канавки обрабатывают за один рабочий ход, а более широкие канавки точат за три рабочих хода «в разгонку» (от центра канавки).
5.
Рис. 2.27. Примеры обработки типовых канавок: а – под стопорные и уплотнительные кольца; б – под шкивы и сальниковые уплотнения; в - сопрягаемых с торцем; г – под выход шлифовального круга
Нарезание резьб производят с помощью резьбовых резцов, форма которых соответствует профилю резьбы. В большинстве случаев резьбу нарезают за несколько ходов по схеме «петля», постепенно углубляясь в заготовку до получения нужной высоты профиля резьбы (рис. 2.28).
55
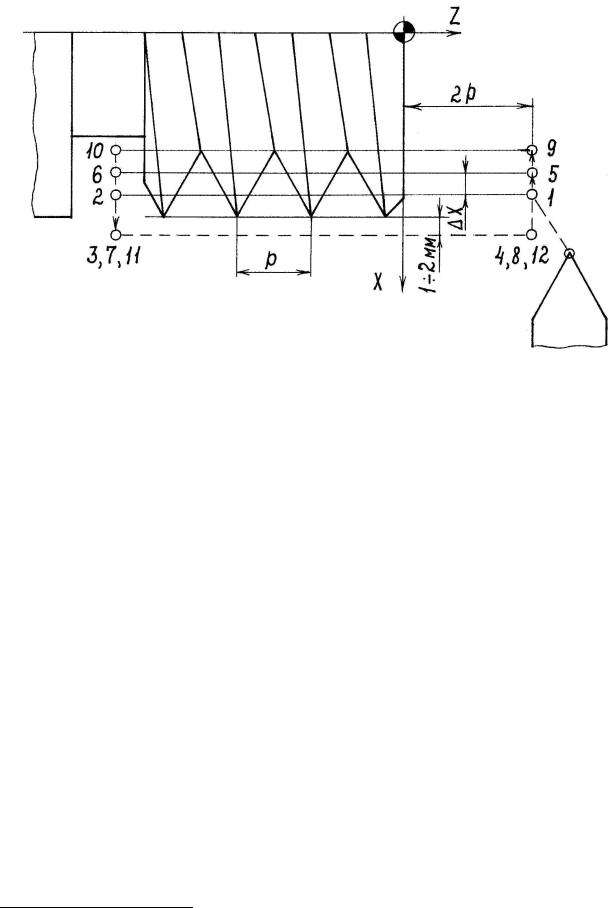
Рис. 2.28. Нарезание резьбы резцом по схеме петля
Точное попадание в нитку резьбы обеспечивается на станках с ЧПУ с помощью специального датчика резьбонарезания, который выдает сигнал на начало очередного рабочего хода в определенном угловом положении шпинделя. Для разгона привода подачи по оси Z начало цикла резьбонарез-
ния сдвигают от начала резьбы на величину двойного шага резьбы. Для цилиндрических резьб нарезание производится продольными ходами, а для конических резьб – под соответствующим углом к оси Z. Возврат на быстром ходу в начало цикла по оси Z выполняется на одном и том же уровне, отстоящем от заготовки на 1 – 2 мм. Для выхода резца предусматривают зарезьбовую канавку. Если такая канавка отсутствует, то резьбу делают со сбегом, для чего на последнем витке резец плавно отводят по оси X.
Положение резца по отношению к нитке резьбы в начале очередного рабочего хода определяется схемой врезания. Здесь можно выделить пять основных вариантов (рис. 2.29):
Если этого не сделать, то первые витки будут нарезаны с нарушением шага резьбы P
56
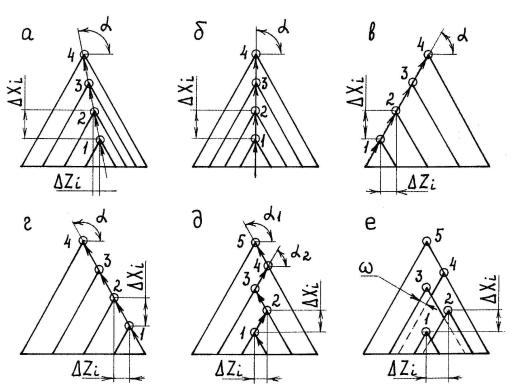
1.Врезание под углом;
2.Радиальное врезание;
3.Боковое врезание;
4.Врезание по зигзагу;
5.Врезание по зигзагу с зазором.
Рис.2.29. Схемы врезания в начало хода: а – под углом; б – радиальное; в – боковое; г – по зигзагу; д – по зигзагу с зазором
Первая схема представляет собой общий случай смещения резца под некоторым углом α к винтовой поверхности. Ее модификациями являются схемы с радиальным или боковым врезанием. Врезание по зигзагу предполагает попеременное смещение резца то в одном, то в другом направлении. Разновидностью этой схемы является врезание по зигзагу с зазором.
В первых двух схемах резание производится обеими режущими кромками резца. Стружка имеет в сечении жесткую V-образную форму, что обуславливает плохой стружкоотвод.
57
При боковом врезании условия стружкообразования лучше. Однако, здесь происходит неравномерный износ резца, поскольку резание производится одной и той же режущей кромкой.
Врезание по зигзагу обеспечивает хорошее стружкообразование и равномерный износ резца, поскольку режущие кромки чередуются. При врезании по зигзагу с зазором ε исключается трение ненагруженной кромки резца, что повышает его стойкость.
Величину радиального врезания X определяют делением высоты профиля на рекомендуемое число рабочих ходов [7, 8, 20]. На практике эту величину выбирают в пределах X =0,2–0,4 мм. Для обеспечения постоянства площади сечения стружки рекомендуется уменьшать значение X на каждом ходе по закону геометрической прогрессии [7, 10].
Следует отметить, что выбор той или иной схемы врезания во многом предопределен наличием соответствующей подпрограммы резьбонарезания. Например, в стандартном цикле L01 «Резьба» для устройства ЧПУ 2Р22 реализовано врезание по зигзагу с чистовым ходом обеими кромками [3].
Перед нарезанием резьбы предварительно протачивают поверхность выступов контурным резцом (наружный диаметр для валов и внутренний диаметр для отверстий). При этом следует учитывать, что в процессе резьбонарезания происходит выдавливание металла из впадин, которое приводит к изменению первоначального диаметра выступов (до 6-7% от шага резьбы). Диаметры стержней и отверстий под нарезание резьбы с учетом выдавливания приводятся в нормативной литературе (ГОСТ 19258-73, ГОСТ 19257-73 и др.). Если для нарезания резьбы используется пластина с полным профилем, то эффект выдавливания не учитывают. Но при предварительной обработке диаметра выступов оставляют припуск (0,2–0,5 мм) на его калибровку резьбовым резцом.
58
ЛИТЕРАТУРА
1.Аверченков В.И. Проектирование технологических процессов обработки на станках с ЧПУ. – Брянск, 1984. – 84 с.
2.Александров А.М. Обработка заготовок на токарном станке 16К20Ф3 с
УЧПУ 2Р22. – СПб.: ПИМаш, 1995. – 61 с.
3.Александров А.М. Программирование обработки для станка 16К20Ф3 с
УЧПУ 2Р22. – Л.: ЛКИ, 1990. – 44 с.
4.Александров А.М. Программирование обработки на многооперационном станке. – СПб.: ПИМаш, 1994. – 53 с.
5.Александров А.М. Технологическая подготовка станка 16К20Ф3 с
УЧПУ 2Р22. – Л.: ЛКИ, 1990. – 44 с.
6.Александров А.М., Шишов Г.А. Наладка и эксплуатация станков с ЧПУ.
– СПб.: ПИМаш, 1998. – 174 с.
7.Гжиров Р.И., Серебренницкий П.П. Программирование обработки на станках с ЧПУ: Справочник. – Л.: Машиностроение, 1990. – 588 с.
8.Дерябин А.Л., Эстерзон М.А. Технология изготовления деталей на станках с ЧПУ и в ГПС. – Учеб. пособие для машиностроит. техникумов. – М.: Машиностроение, 1983. – 304 с.
9.Евгенев Г.Б. Основы программирования обработки на станах с ЧПУ. – М.: Машиностроение, 1983. – 304 с.
10.Инструмент для станков с ЧПУ, многоцелевых станков и ГПС / И.Л. Фадюшин, Я.А. Музыкант, А.И. Мещеряков и др. – М.: Машинострое-
ние, 1990 – 272 с.
11.Каштальян И.А., Клевзович В.И. Обработка на станках с числовым программным управлением: Справ. пособие. – Минск: Выш. шк., 1989. – 271 с.
59
12.Комиссаров В.И., Леонтьев В.И. Точность, производительность и надежность в системе проектирования технологических процессов. – М.: Машиностроение, 1985. – 224 с.
13.Кузнецов Ю.И., Маслов А.Р., Байков А.Н. Оснастка для станков с ЧПУ: Справочник. – 2- е изд., перераб. и доп. - М.: Машиностроение , 1990. – 512 с.
14.Марголит Р.Б. Эксплуатация и наладка станков с программным управлением и промышленных роботов: Учеб. пособие для машиностроит. техникумов. – М.: Машиностроение, 1991. – 272 с.
15.Маталин А.А. Технология машиностроения: Учебник для машиностроительных вузов. – Л.: Машиностроение, 1985. – 496 с.
16.Обработка металлов резанием: Справочник технолога / А.А. Панов, В.В. Аникин Н.Г. Бойм и др.; Под общ. ред. А.А. Панова. – М.: Машино-
строение, 1989. – 736 с.
17.Панов Ф.С., Травин А.И. Работа на станках с программным управлени-
ем. – Л.: Лениздат, 1984. – 278 с.
18.Справочник нормировщика / А.В. Ахумов, Б.М. Генкин, Н.Ю. Иванов и
др.; Под общ. ред. А.В. Ахумова. – Л.: Машиностроение, 1986. |
– |
458 с.
19.Справочник технолога-машиностроителя. В 2-х т. / Под ред. А.Г. Косиловой и Р.К. Мещерякова. – 4- е изд., перераб. и доп. – М.: Машино-
строение, 1986. – Т. 1. – 656 с.
20.Справочник технолога-машиностроителя. В 2-х т. / Под ред. А.Г. Косиловой и Р.К. Мещерякова. – 4- е изд., перераб. и доп. – М.: Машино-
строение, 1986. – Т. 2. – 496 с.
21.Шарин Ю.С. Технологическое обеспечение станков с ЧПУ. – М.: Машиностроение, 1986. – 176 с.
60