
АПП курсовик / 5551 АПП / Курсовой проект / Обработка на станках с ЧПУ / Наладка и эксплуатация станков с ЧПУ
.pdfдоставку и замену всех необходимых элементов производственного процесса: приспособлений и инструмента, заготовок, технологической документации, программоносителей, масла для смазки и гидросистем, охлаждающей жидкости др. Особое значение эта проблема приобретает в условиях гибких производственных систем (ГПС).
Важную роль играет рациональная расстановка оборудования. Практика показала, что наибольший эффект станки с ЧПУ дают при их концентрации на отдельных участках (10 - 15 станков) или в целых цехах, которые обслуживает постоянная группа специалистов из технологов, программистов, наладчиков и ремонтников [19, 21].
На участке станков с ЧПУ иногда устанавливают несколько обычных станков для выполнения таких операций, где использование станков с ЧПУ нерентабельно (например, для обдирки заготовок и подготовки технологических баз). Участок станков с ЧПУ должен иметь свое отделение для подготовки инструмента, где производятся его дефектация и заточка, сборка инструментальных блоков, измерение корректируемых размеров и предварительная настройка. Станочные приспособления также желательно хранить в пределах участка или в непосредственной близости от него.
С точки зрения организации транспортно-складского хозяйства, наиболее приемлемым является автоматизированный стеллажный склад со штабеллером. Особый эффект здесь дает применение ЭВМ для управления складом и учета хранящихся грузов. Планировка рабочих мест должна обеспечивать удобство и безопасность работы, а также возможность многостаночного обслуживания. Примеры рациональной организации рабочих мест для различных станков с ЧПУ представлены в [14, 21]
Для эксплуатации станков с ЧПУ привлекают специалистов различных профессий, среди которых можно выделить два основных профиля: технологический и ремонтный. К специалистам технологического профиля относят наладчиков и операторов, которые осуществляют подготовку и
31
выполнение технологических операций. Специалисты ремонтного профиля обеспечивают работоспособность станков с ЧПУ путем технического обслуживания (ТО) и ремонтов.
Граница между этими двумя направлениями, в известном смысле, носит условный характер. Например, ежедневное ТО и некоторые виды профилактических работ выполняют операторы и наладчики. С другой стороны, в технологической наладке станков с ЧПУ могут участвовать представители ремонтных служб. Таким образом, эффективная эксплуатация, оборудования с ЧПУ требует совместной работы специалистов обоих профилей.
На практике установлено, что наиболее рациональной формой организации труда специалистов по обслуживанию станков с ЧПУ является создание комплексных бригад. Состав таких бригад может быть различным в зависимости от характера решаемых задач.
Для повседневной эксплуатации станков с ЧПУ образуют бригады из наладчиков, и операторов, за которыми закрепляют определенную группу станков и номенклатуру деталей. В помощь этим бригадам ремонтные службы выделяют постоянных представителей. Эффективность работы бригад обеспечивается рядом организационно-технических мероприятий: образованием архива эталонных программ; ведением учета работы УП; предотвращением возможности брака при отказе станка; устранением неисправностей УЧПУ путем замены блоков (из полного комплекта на пять станков) и др.
Техническое обслуживание и ремонт станков с ЧПУ выполняют комплексные бригады, в состав которых включают специалистов по всем системам станка: механиков, электриков, гидравликов и наладчиков УЧПУ. Рекомендуется создавать такие бригады не по территориальному признаку, а по видам обслуживаемых станков [33]. Техническое обслуживание и текущий ремонт, как правило, производится ремонтной бригадой цеха или
32
участка. Средний, капитальный и аварийные ремонты осуществляются централизованно заводскими службами (иногда с привлечением специалистов сервисных организаций). Правила проведения ТО и ремонтов для станков с ЧПУ подробно изложены в [14]. Эффективной работе ремонтных служб способствуют некоторые организационно-технические мероприятия, оснащение специальными стендами для проверок, испытаний и ремонта; применение тестирующих программ; ведение оперативных журналов; анализ причин отказов и др.
Ежедневное ТО проводится наладчиками и операторами. В ходе обслуживания проверяют: работоспособность отдельных узлов и станка в целом; уровень вибраций; температуру подшипников; показания манометров гидросистемы; уровень масла по маслоуказателям; отсутствие ударов в механизмах; плавность перемещения рабочих органов и отсутствие рывков при реверсировании; отсутствие утечек из гидросистемы; индикацию и сигнализацию органов управления; исправность зажимных устройств и средств защиты и др. Оператор должен ежедневно чистить станок, убирать стружку и смазывать механизмы.
Важным резервом повышения эффективности обслуживания станков с ЧПУ является совмещение профессий. При узкой специализации наладчиков и операторов 40–50% времени простоя станка связано с ожиданием работников ремонтных служб [19]. Поэтому, желательно, чтобы наладчик знал свое оборудование в комплексе, а оператор имел о нем общее представление. В современном производстве наладчик должен иметь высшее (или по меньшей мере среднее) техническое образование, обладая знаниями и практическими навыками по технологии, программированию, механике и электронике. Квалифицированный наладчик способен выполнить все основные работы по обслуживанию станка с ЧПУ (от заточки инструмента до устранения неисправностей УЧПУ) и только при необходимости пользуется услугами ремонтных служб.
33
Следует отметить, что учебные планы вузов и техникумов не рассчитаны на подготовку таких универсальных специалистов. По этой причине многие наладчики вынуждены получать второе образование (как правило, в области вычислительной техники и электроники). Для устранения дефицита квалифицированных наладчиков представляется целесообразным переработка учебных планов и программ по технологическим специальностям с учетом требований современного производства.
При работе на станках с ЧПУ (особенно на этапе пробной обработки) необходимо строго соблюдать правила техники безопасности, которые изложены в соответствующих инструкциях и стандартах. Общими для всех станков с ЧПУ являются следующие положения [14]:
1.Перед нажатием кнопки "Пуск" удостовериться, что переключатель режимов работы УЧПУ находится в нужном положении.
2.Убедиться, что путевые кулачки предупредительных остановов и параметрические ограничители хода по каждой координате установлены в положениях, обеспечивающих безаварийную работу.
3.Проверить исправность и правильность срабатывания блокировочных устройств (конечных выключателей, предохранительных муфт).
4.Отработку "новой" УП вести в покадровом режиме. Перед отработкой очередного кадра осмыслить предстоящие действия станка и проверить возможность их безаварийного осуществления. Обратить первоочередное внимание на направление предстоящего перемещения, а затем на конечную координату и скорость движения.
5.При выполнении автоматического цикла следить, чтобы защитные кожухи ограждения были закрыты. Наблюдения вести через прозрачные экраны.
6.В случае непредусмотренных перемещений рабочих органов нажать кнопку "Стоп", а в случае возникновения аварийной ситуации, требующей остановки станка, нажать кнопку "Аварийный стоп".
34
7.При совместной наладке станка двумя лицами переключение и включение органов управления должен производить только один из участников, предупреждая другого о производимых действиях.
8.При проверке работоспособности станка не находиться в зоне действия рабочих органон.
9.Все виды ремонтных работ проводить при отключенном электропитании. Вывесить плакат "Не включать". Убедиться, что в гидросистеме отсутствует давление масла.
При установке инструментов с кодированием гнезд магазина необходимо следить за соответствием расположения инструментов карте наладки. При кодировании номера инструмента следует проверить правильность кодов по карте наладки или тексту УП. Нельзя устанавливать в магазин инструменты с габаритами и массой, превышающими допустимые значения.
Впроцессе работы необходимо контролировать состояние инструментов и своевременно заменять их по мере затупления или в случае поломки.
2.РАЗМЕРНАЯ НАСТРОЙКА СТАНКОВ С ЧПУ
2.1.Настройка станков сверлильно-фрезерно-расточной группы
Размерная настройка станков с ЧПУ состоит во взаимном согласо-
вании трех систем координат: станка, программы и инструмента. Станочная система координат используется для непосредственного
управления следящими приводами подач, т.е. все перемещения в конечном итоге отрабатываются от нуля станка.
В системе координат программы задают опорные точки траектории движения инструмента. Как правило, нуль УП совмещают с базирующими элементами приспособления или с характерной поверхностью заготовки.
Система координат инструмента необходима для того, чтобы определить положение режущих кромок инструмента относительно базовой точки инструментодержателя.
35

Системы координат для станков сверлильно-фрезерно-расточной группы (на примере вертикального станка) показана на рис. 2.1. Здесь в системе координат программы X, Y, Z (с нулем УП в точке W ) заданы координаты х, y, z опорной точки Р. Для правильного фрезерования уступа нужно сместить базовую точку инструментодержателя N (центр торца шпинделя) относительно запрограммированной точки Р на величину вылетов инструмента WX , WY , WZ.
Рис.2.1. Системы координат для станков сверлильно-фрезерно-расточной группы
Такое смещение обеспечивается командами осепараллельной коррекции G43/G44 и коррекции на радиус G41/G42. Смещения WХ, WY равны радиусу инструмента RИ, а смещение WZ - расстоянию от торца шпинделя до режущей кромки по оси Z.
36

Кроме того, для окончательного преобразования положения базовой точки N к станочной системе координат ХC, YC, ZС необходимо задать координаты X0, Y0, Z0 нуля программы W относительно нуля станка М (с помощью команд смещения нуля программы G54-G59). Таким образом, координаты базовой точки P в станочной системе будут равны
ХC = x +X0 + WX ; YC = y + Y0 + WY ; ZС = z + Z0 + WZ .
Отсюда следует, что для правильной отработки УП в общем случае наладчик должен записать в соответствующие ячейки памяти УЧПУ значения смещений нуля УП относительно нуля стенка X0, Y0, Z0 и корректоров на размеры инструмента WX , WY , WZ.
Смещения нуля УП могут быть определены в карте наладки. В этом случае выполняется выверка приспособления на столе станка по линейным размерам (см. раздел 1). Однако для современных станков с ЧПУ этот способ почти не применяется. Чаще всего, положение нуля УП в станочной системе определяют непосредственно на станке с помощью соответствующих измерительных средств и показаний цифровой индикации (сохраняя при необходимости угловую выверку).
Корректируемые размеры инструмента WХ и WZ могут быть измерены на специальных приборах вне станка*. Иногда эти размеры задают в карте наладки и вместо измерения вылетов выполняют предварительную настройку инструментов. Кроме того, корректируемые размеры можно, при необходимости, определить и непосредственно на станке в режиме полуавтоматической привязки. Ниже рассмотрена методика размеров привязки приспособлений и инструментов непосредственно на станке.
* Для станков сверлильно-фрезерно-расточной группы коррекцию на радиус инструмента RИ принято обозначать символом WХ
37
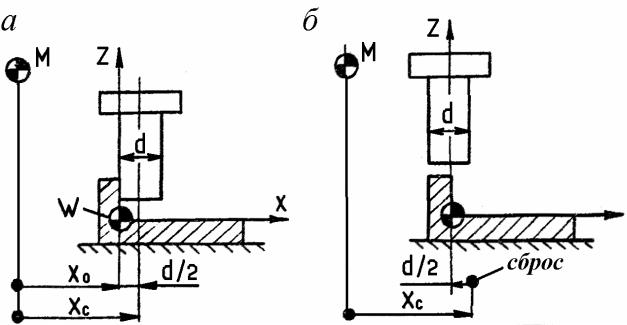
2.1.1. Настройка в плоскости XY
Для настройки станка в плоскости XY применяют следующие основные способы:
-с помощью калиброванных оправок (или мерного инструмента);
-с помощью индикаторных оправок и оптических центроискателей;
-путем пробной обработки;
-с помощью автоматической измерительной головки.
Пример использования калиброванной оправки для привязки приспособления по оси X показан на рис. 2.2. Оправку известного диаметра d устанавливают в шпиндель станка и вручную доводят до соприкосновения с базирующей поверхностью приспособления. Далее с учетом показаний цифровой индикации в станочной системе XС определяют смещение Х0 нуля программы W относительно нуля станка М (рис. 2,2, а)
Х0 = XС –d/2 .
Рис.2.2. Привязка нуля УП с помощью калиброванной оправки: а - путем ввода смещения Х0; б - путем сброса показаний цифровой индикации
38

На некоторых станках предусмотрена возможность сброса показаний цифровой индикации в нуль. В этом случае после касания шпиндель перемещают по оси X, на расстояние d/2 от точки соприкосновения, а затем обнуляют показания индикации по координате X (рис. 4.2,б). При этом величина смещения Х0 автоматически записывается в память УЧПУ.
Недостатком рассмотренного способа является относительно невысокая точность из-за субъективности определения момента касания оправки с базирующей поверхностью. На станках с ЧПУ отсутствует кинематическая связь между органами управления и рабочими органами. Поэтому момент касания оправки с базирующей поверхностью определяется визуально с некоторой погрешностью ∆Х, которая обусловлена зазором между оправкой и приспособлением (рис. 2.3, а) или упругой деформацией оправки (рис. 2.3, б). Точность настройки здесь относительно невелика и составляет 0,04-0,06 мм [18].
Рис.2.3. Погрешности привязки нуля программы с помощью калиброванной оправки: а - погрешность, обусловленная зазором между оправкой и базирующей поверхностью; б - погрешность, обусловленная деформацией оправки
39

Для повышения точности настройки между оправкой и базирующей поверхностью вставляют мерную плитку (или контрольный щуп). Точность привязки здесь повышается за счет более объективного определения момента касания по усилию страгивания плитки (рис. 2.4, а). В этом случае при расчете смещения Х0 необходимо учесть толщину плитки а
Х0 = XС –d/2 - а.
На поверхности оправки может быть предусмотрен специальный контрольный участок диаметром d1 = d – 0.06 мм (рис.2.4, б). Момент касания определяют так, чтобы пластинка щупа толщиной 0,03 мм легко проходила на контрольном участке, а пластинка щупа толщиной 0,04-0,05 мм не проходила. Иногда проходной (диаметром d1) и непроходной (диаметром d2) участки выполняют на самой оправке (рис. 2.4,в). Применение мерных плиток и контрольных щупов позволяет повысить точность на-
стройки до 0,03-0,04 мм [18].
Рис.2.4. Привязка нуля УП с помощью калиброванной оправки и мерной плитки: а- с помощью цилиндрической оправки; б – с помощью оправки с контрольным участком; в - с помощью оправки
с проходным и непроходным участками
40