
АПП курсовик / 5551 АПП / Курсовой проект / Обработка на станках с ЧПУ / Наладка и эксплуатация станков с ЧПУ
.pdfсложности. Поэтому на многих предприятиях используют другие формы КН/П, позволяющие более полно отразить особенности современных станков. Представляется целесообразным разработка единой формы КН/П, которая бы позволила подробно описать технологию наладки по переходам (по аналогии с описанием технологической операции в ОК).
Для правильной установки приспособлений наладчик должен хорошо представлять их конструкцию и способы сопряжения со станком, которые широко представлены в [13]. Особая ответственность лежит на наладчике в том случае, если технология обработки и УП разрабатываются непосредственно на рабочем месте. В этом случае выбор приспособления осуществляет сам наладчик, руководствуясь типовым комплектом принадлежностей к станку. Наиболее сложной задачей является компоновка элементов приспособления непосредственно на столе станка или координатной плите (или угольнике), что характерно для единичного и мелкосерийного производства. Повышенной сложностью обладает также установка механизированных и автоматизированных приспособлений, поскольку кроме базирования и закрепления приспособления здесь необходимо обеспечить его правильную стыковку с силовыми приводами станка и устройствами автоматики.
Иногда требуется доработка элементов приспособления непосредственно на станке (например, растачивание отверстия для юстировки измерительной головки, обработка отверстия под установочный палец для токарных станков с осью C и др.).
На токарных станках часто применяют патроны с незакаленными ("сырыми") кулачками, которые предварительно растачивают под нужный диаметр зажима. Такой способ позволяет уменьшить погрешность расположения базовых и обрабатываемых поверхностей до 0,015 - 0,030 мм для патронов нормальной точности. Расточку кулачков выполняют следующим образом [14]:
11
-прикрепляют незакаленные кулачки к основным, выдерживая примерно равные расстояния от рабочих поверхностей до оси шпинделя;
-зажимают основными кулачками или нерабочими поверхностями незакаленных кулачков жесткий диск (для выборки зазоров в механизме патрона);
-растачивают рабочие поверхности незакаленных кулачков в размер заготовки, а также обрабатывают их торцовые поверхности.
Растачивание кулачков можно выполнять по специальной программе [29]. Рекомендуемая форма незакаленных кулачков представлена в [12]. Вместо жесткого диска допускается использование универсальной накладной шайбы [15], с помощью которой можно растачивать кулачки под разные диаметры зажима.
В некоторых случаях (особенно при высоких требованиях к точности обработки) требуется выверить расположение приспособления относительно рабочих органов станка. Различают два вида выверки:
-выверка по линейным размерам;
-угловая выверка.
Для токарных станков выверку по линейным размерам не применяют, поскольку приспособление здесь может занять единственное положение относительно станка.
Для станков сверлильно-фрезерно-расточной группы выверка по линейным размерам не нужна, если обеспечено полное базирование приспособления на столе станка. Такое базирование можно обеспечить следующими схемами установки [1, 13]:
-по продольному и поперечному пазу с помощью трех шпонок;
-по центральному отверстию и продольному пазу с помощью пальца
ишпонки (или двух пальцев);
-в координатный угол, образованный двумя планками или тремя опорами;
12

- по двум отверстиям (при наличии сетки координатно-фиксирующих отверстий) с помощью цилиндрического и ромбического пальцев.
"Традиционная" схема установки фрезерных приспособлений по продольному пазу с помощью двух шпонок не обеспечивает полного базирования. Если смещение X0 задано в карте наладки, то здесь требуется выверка по координате X. Для этой цели, обычно, применяют метод касания с помощью калиброванной оправки известного диаметра d (рис. 1.4).
Рис.1.4. Выверка приспособления по координате Х с помощью калиброванной оправки
Оправку закрепляют в шпинделе, а приспособление устанавливают на столе станка в произвольном положении по оси Х. Пользуясь индикацией текущего положения, отрабатывают мерное перемещение по оси X относительно нуля станка М в точку с координатой
ХС = Х0 + d/2,
где Х0 - смещение нуля программы W относительно нуля станка М.
13

После этого приспособление передвигают вдоль стола до касания базирующей поверхности с оправкой, совмещая тем самым вершину координатного угла F с нулем программы W.
Аналогичный прием используют для выверки базирующих элементов приспособления по двум координатам (рис. 1.5). Здесь заготовка устанавливается в координатный угол, образованный тремя регулируемыми опорами 1, 2 и 3. Смещения Х0, Y0 нуля программы W относительно нуля станка М определены в карте наладке. Сначала наладчик отрабатывает мерное перемещение ХС = Х0 + d/2 и регулирует опору 1 до соприкосновения с оправкой. Затем отрабатывается мерное перемещение YС = Y0 + d/2 и выполняется регулировка опор 2 и 3.
Рис.1.5. Выверка приспособления по координатам Х, Y с помощью калиброванной оправки
Выверка приспособления по двум координатам, зачастую, необходима для горизонтальных станков с поворотным столом (рис. 1.6). Здесь необходимо обеспечить точное расположение приспособления относительно
14
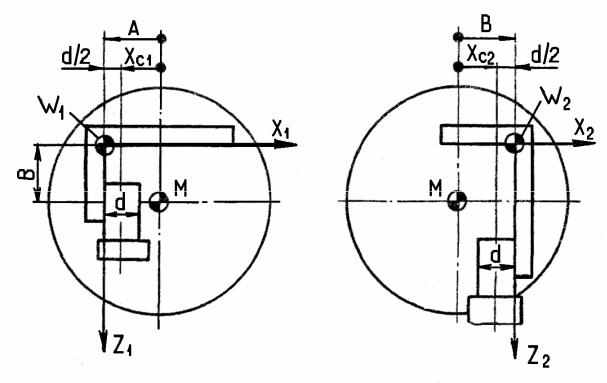
оси вращения стола М, выдерживая размеры А и В. Выверку производят в два этапа. Сначала отрабатывают мерное перемещение ХС1 = А + d/2 и выверяют размер А. Далее поворачивают стол на 90°, отрабатывают мерное перемещение ХС2 = В - d/2 и выверяют размер В.
Рис.1.6. Выверка приспособления на поворотном столе по координатам Х, Z с помощью калиброванной оправки
Угловая выверка приспособлений необходима для станков сверлиль- но-фрезерно-расточной группы независимо от схемы установки на столе станка.
Из-за конструктивных зазоров между посадочными элементами приспособления и станка неизбежно возникает угловая погрешность расположения приспособления, которая недопустима при повышенных требованиях к точности обработки. В этом случае для угловой выверки, чаще всего, применяют индикаторные оправки, которые устанавливают в шпинделе станка (рис.1.7).
15

Рис.1.7. Угловая выверка приспособления с помощью индикаторной оправки: а - для вертикального станка; б - для горизонтального станка с поворотным столом
Наконечник индикатора вводят в соприкосновение с направляющей базой приспособления. Затем добиваются такого углового положения приспособления, в котором при перемещении оправки вдоль направляющей базы показания индикатора не изменяются.
Для вертикальных станков угловое положение приспособления можно изменять в пределах зазоров между посадочными элементами приспособления и станка (рис. 1.7, а).
Для горизонтальных станков с поворотным столом правильного углового положения можно добиться путем поворота стола по координате В
(рис.1.7,б).
При токарной обработке угловая выверка может потребоваться только для станков с программируемым поворотом шпинделя (по оси С).
Следует отметить, что для современных станков с ЧПУ, как правило, ограничиваются угловой выверкой, а выверку по линейным размерам заменяют размерной привязкой приспособления (см. раздел 2).
16

Установку инструментов выполняют в соответствии с картой наладки, где перечислены все режущие и вспомогательные инструменты с указанием позиций инструментального магазина и необходимых наладочных размеров. В зависимости от формы организации труда и других производственных условий сборка инструментальных блоков производится либо на участке комплектации, либо самим наладчиком непосредственно на рабочем месте. При подборе инструментов, используя принципы групповой технологии, стараются в максимальной степени сохранить "старый" инструментальный комплект, который уже установлен на станке.
В станках с автоматической сменой инструмента применяют две системы его поиска (рис. 1.8):
-с кодированием номера инструмента;
-с кодированием номера гнезда инструментального магазина. Наиболее современным и перспективным способом кодирования ин-
струмента является применение электронных кодовых датчиков. Например, в системе инструментального обеспечения Coroplan шведского концерна Sandvic [8] применен кодовый датчик в виде миниатюрной вставки, которую закрепляют в гнезде инструментального блока (рис. 1.8, а).
Рис.1.8.Способы кодирования номера инструмента:
а - с помощью электронного датчика; б - с помощью кодовых колец
17
Емкость памяти датчика позволяет хранить не только номер инструмента, но и другие данные: размеры инструмента, заданную стойкость, режимы резания, время работы и др. Запись и считывание информации производится с помощью специальных головок, которыми оснащают станок и измерительную машину. Такая система обладает широкими возможностями, но требует соответствующего оборудования и высокого уровня организации производства.
Для станков сверлильно-фрезерно-расточной группы применяют также более простой способ кодирования номера инструмента с помощью кодовых колец (рис. 1.8, б). Эти кольца закрепляют на хвостовике оправки в определенном порядке, который соответствует номеру инструмента в двоично-десятичной системе. В процессе поиска инструмента кольца воздействуют на конечные выключатели инструментального магазина. При совпадении кода инструмента с номером, заданным в программе, выдается команда на останов вращения магазина.
В случае кодирования номера инструмента наладчик может устанавливать инструментальный комплект в магазин произвольным образом. Ответственность за правильность кодирования здесь несут работники участка комплектации. При кодировании номера гнезда магазина расстановку инструментов производят в строгом соответствии с последовательностью, установленной в управляющей программе и картой наладки. Следует отметить, что даже для современных станков чаще всего применяется второй способ.
Для станков, где смена инструмента осуществляется с помощью автооператора, необходимо обратить на правильную угловую ориентацию инструментальных блоков в магазине. Это требование обусловлено необходимостью совмещения вырезов на фланце инструментальных оправок с двумя шпонками на торце шпинделя при смене инструмента. Кроме того, некоторые способы обработки отверстий (растачивание с автоматическим
18
выводом оправки, обратное растачивание, 4-координатная интерполяция и др.) требуют определенности в угловом положении инструмента при ориентированном останове шпинделя.
Процесс установки инструментов завершается записью в соответствующие корректоры информации о фактических размерах инструментов. Обычно номера корректоров соответствуют номерам инструментов, хотя это требование и не является обязательным. Размеры инструментов измеряют на специальных приборах или определяются наладчиком непосредственно на станке (см. раздел 2).
1.4. Ввод программы и пробная обработка
Ввод управляющей программа (УП) может выполняться следующими способами:
-с внешнего носителя;
-с пульта управления УЧПУ;
-из энергонезависимой памяти УЧПУ (для зарегистрированных УП),
-по каналам связи с центральной ЭВМ (в условиях ГПС). Последние два способа применяют для ввода в оперативную память
УЧПУ только "старых" УП, уже опробованных на производстве.
Ввод УП с внешнего носителя может применяться как для "старых", так и для "новых" программ. В качестве внешнего носителя в современных УЧПУ применяют магнитофонные кассеты, дискеты, лазерные диски, флэш-карты и др. [3, 31].
Ввод УП с пульта УЧПУ применяют для "новых" программ. Введенная программа после ее редактирования может быть записана в энергонезависимую память УЧПУ или на внешний носитель. В современных УЧПУ режим ввода и редактирования допускает параллельную работу станка в автоматическом режиме по "старой" программе. Это позволяет готовить "новую" УП непосредственно на рабочем месте без простоя станка.
19
Независимо от способа ввода программы УЧПУ выполняет автоматический контроль правильности текста с точки зрения отсутствия синтаксических и семантических ошибок [26]. К таким ошибкам относят: нарушение форматов кадра и команд; использование непредусмотренных адресов; нарушение четности (в коде ISO); использование в одном кадре ортогональных G-функций и др.
Для окончательной отладки введенной УП производят пробную обработку первой заготовки партии. С целью облегчения работ по отладке УП в современных УЧПУ предусмотрена возможность активного вмешательства оператора в процесс автоматического управления. Это обеспечивается рядом специальных команд и подрежимов.
Команда "Главный кадр" (:) служит для обозначения некоторых характерных кадров УП, называемых главными. Главный кадр определяет исходное состояние УЧПУ (особенно в части G-функций) перед началом отработки фрагмента УП. Рекомендуется применять главный кадр после смены инструмента, выделяя обработку каждым инструментом в отдельную часть УП. При этом в главных кадрах записывают всю необходимую информацию для работы очередным инструментом, даже если часть этой информации была уже задана. Такой способ позволяет оператору легко возобновить отработку с произвольного инструмента без предварительного просмотра УП в поисках команд, необходимых для продолжения работы.
Команда "Пропуск кадра" (/) предназначена для выделения кадров, которые могут быть отработаны или пропущены в зависимости от положения специального переключателя на пульте управления. Этот режим полезен при отладке УП, а также в тех случаях, когда программист не может принять однозначного решения об отработке каких-либо кадров и оставляет это на усмотрение оператора.
20