
Методички / Конструирование деталей машин
.pdfТаблица 26. Фундаментные болты
|
Длина плиты L, мм |
≤ 500 |
500…700 |
700…1000 |
1000…1200 |
|
|
|
|
|
|
|
Диаметр фундамент- |
14 |
16 |
20 |
24 |
|
ных болтов d, мм |
|
|
|
|
|
Число болтов z |
4 |
4 |
6 |
8 |
|
|
|
|
|
|
Размеры фланцев основания плиты (рис. 46) принимают: |
|
||||
|
ширину b = (2,5…3,5) δ; |
|
|
(47) |
|
|
толщину t = 1,5 δ. |
|
|
|
(48) |
Размеры бобышек (рис. 46) принимают: |
|
|
|||
|
толщину горизонтальной полки δ1 = 1,5 δ; |
|
(49) |
||
|
высоту h = (2,5…3,5)d; |
|
|
(50) |
ширину, размеры под болты и цековку из условия размещения болтов -
по табл. 8.
Сварные рамы (рис. 47) проектируют с учётом основных принципов конструи-
рования литых плит. Рама состоит из швеллеров, которые располагают полками наружу для удобства сборки. Высоту швеллера назначают по высоте Н – формула
(45). Нижнюю поверхность рамы не обрабатывают. Для установки узлов проекти-
руют платики толщиной 5…6 мм, которые приваривают к раме и обрабатывают по
Rz20. Основные элементы рамы приведены на рис. 45.
Раму удобно конструировать из двух продольно расположенных швеллеров и трёх-четырёх поперечных, приваренных к продольным. Узлы к раме крепят бол-
тами. На внутреннюю поверхность полки приваривают плоские или косые шайбы по ГОСТ 10906. Под гайки фундаментных болтов проектируют бобышки. Если позволяет компоновка узлов на раме, фундаментные болты пропускают сквозь обе полки и гайку опирают о верхнюю полку.
Рамы и плиты располагают на бетонном полу. Для покрытия полов применяют высококачественные марки бетона. Толщина слоя бетона – 30…40 мм. Фунда-
ментные болты для крепления рам отличаются друг от друга формой закладных концов [8]. Диаметр фундаментной скважины зависит от диаметра болта: D =
(5…7) d. Глубина заложения болтов в фундаменте h1 = (12…15) d. Фундаментные

А |
B |
Б |
|
|
Б |
|
L |
А |
H |
|
|
Рис. 47. Рама сварная |
|
болты и их крепления к фундаменту показаны на рис. 44 и 45. |
10. МУФТЫ
Сборочные единицы, собранные на раме, соединяют муфтами или передачами.
Муфты предназначены прежде всего для соединения валов и передачи крутящего момента. В большинстве конструкций решаются и другие задачи. Из многообра-
зия классов муфт в механических приводах используют механические муфты.
Несмотря на расположение узлов на общем основании (раме или плите) глухие

муфты (втулочные, фланцевые) в приводах не используют из-за высоких требова-
ний к соосности валов. Менее высокие требования по соосности предъявляют муф-
там, частично компенсирующим несоосность. К компенсирующим муфтам отно-
сятся зубчатые, шарнирные (муфта Кардана) и кулачково-дисковые (муфта Ольд-
гема). Широко используются упругие муфты.
Упругие муфты обладают определёнными компенсирующими свойствами, но их основное назначение – смягчать динамические нагрузки и выводить систему из состояния резонанса. При малых и средних вращающих моментах ( Т < 10000 Н·м)
применяют муфты с неметаллическими упругими элементами, например, резино-
выми или войлочными кольцами, при больших моментах используют муфты с ме-
таллическими упругими элементами.
Наиболее распространённая упругая муфта – втулочно-пальцевая, сокращённо МУВП (рис. 48). Полумуфты несимметричны. В одной из них закреплены метал-
лические пальцы, на которые надеваются резиновые кольца. Другая полумуфта имеет ответные цилиндрические отверстия.
|
lв |
|
п |
|
d |
d |
0 |
D |
Рис. 48. Муфта упругая втулочно-пальцевая Компенсирующие способности муфты невелики. Допускается осевое смещение
l в пределах до половины монтажного зазора (до 4 мм), радиальное смещение r = 0,2…0,6 мм; угловое смещение α = 1º, однако такие смещения могут вызывать быстрый износ колец. Размеры муфт выбирают по ГОСТ 21424 [8]. В специфика-
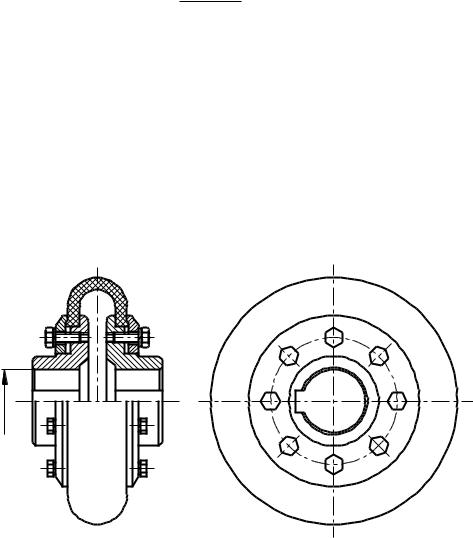
ции муфту обозначают по типу: «Муфта 1000-50-1 ГОСТ 21424-93» [8], где основ-
ные параметры [Т]= 1000 Н·м, d = 50 мм. Для проверки прочности пальцы рассчи-
тывают на изгиб, а резину – по давлению (смятию) по формуле:
2T |
|
|
p zD0 lв dп |
[ p] 2МПа, |
(51) |
где z – число пальцев; D0 – диаметр расположения центров отверстий; lв – длина рабочей поверхности втулки; dп – диаметр пальца.
Упругая муфта с торообразной оболочкой (рис. 49) обладает хорошими ком-
пенсирующими свойствами. Упругая оболочка позволяет осевое смещение l =
4…6 мм, радиальное смещение r = 2…6 мм; угловое смещение α = 2º. Кроме то-
го, она обладает большой крутильной податливостью (угол закручивания до 5º).
Такие достоинства определяют широкие области применения.
d
Рис. 49. Муфта упругая с торообразной оболочкой
Размеры муфт выбирают по ГОСТ 20884 [8]. В спецификации муфту обознача-
ют по типу: «Муфта 2000-1-63-1 ГОСТ 20884-93» [8], где основные параметры [Т]
= 2000 Н·м, d = 63 мм. Расчёты на прочность стандартных муфт не выполняют,
правильность выбора проверяют по условию: |
|
|
|
Tр = T·K1·K2 ≤ [Т], |
(52) |
где коэффициенты: |
|
|
K1 |
– ответственности передачи; K1 = 1…1,8; |
|
K2 |
– режима работы; K2 = 1,15…3. |
|
В зубчатых муфтах компенсирующая способность достигается созданием за-

зоров и подвижностью жёстких зубьев. Муфта состоит из двух одинаковых полу-
муфт с наружными эвольвентными зубьями и обоймы с внутренними зубьями
(рис. 50). Для создания подвижности во всех направлениях и снижения концентра-
ции нагрузки наружные зубья делают сферическими по вершинам и бочкообраз-
ными. Величины допускаемых смещений ограничиваются угловым смещением обоймы относительно оси валов.
d
Рис. 50. Муфта зубчатая
Муфты допускают радиальное смещение r = 1,5…6,5 мм (при отсутствии угло-
вого смещения) и угловое смещение α = 1,5º (при отсутствии радиального), однако максимальных значений следует избегать по причине повышенного износа зубьев.
Возможно также осевое смещение l за счёт осевых зазоров между деталями. Зуб-
чатую муфту применяют при значительных нагрузках. Размеры муфт выбирают по ГОСТ 5006 [8]. В спецификации муфту обозначают по типу: «Муфта 1- 10000-100-
1 ГОСТ 5006-94», где основные параметры [Т]= 10000 Н·м, d = 100 мм. Правиль-
ность выбора проверяют по условию (52).
Характеристики других соединительных муфт приведены в пособии [8].
11.ЧЕРТЕЖИ ДЕТАЛЕЙ
11.1.Общие положения
Правильно разработанные и хорошо оформленные рабочие чертежи деталей имеют большое значение для производства. Они в совокупности с техническими
требованиями содержат все необходимые данные, определяющие форму, размеры,
допуски, материал, термическую обработку, отделку и другие сведения, необходи-
мые для изготовления и контроля деталей.
Детали, представляющие собой тела вращения (валы, червяки, стаканы, зубча-
тые и червячные колёса и т.д.), принято изображать на чертежах так, чтобы их оси вращения были параллельны основной надписи, т.е. в соответствии с установкой на станке. Для удобства чтения чертежа деталь следует располагать на чертеже вправо стороной, на которой производят наибольшее число операций. При простановке размеров должны соблюдаться правила, регламентированные ЕСКД.
1) Количество размеров на чертеже должно быть достаточным для изготовления и контроля детали; при отсутствии какого-либо размера деталь невозможно изгото-
вить.
2)Каждый размер следует приводить на чертеже только один раз: на основных проекциях, в технических требованиях и др..
3)На каждом чертеже проставляют габаритные размеры по трём координатным осям.
4)Размеры, относящиеся к одному конструктивному элементу, следует группиро-
вать в одном месте.
5) Все размеры детали должны быть проставлены с предельными отклонениями,
иначе они становятся неопределёнными для производства; предельные отклонения приводят в одном из трех вариантов: в миллиметрах, в буквенно-цифровом выра-
жении (типа H7, р6 и т.п.), в комбинации обоих вариантов, иногда в технических требованиях.
6)Все размеры детали должны соответствовать ГОСТ 6636 (прил. Г).
7)Размеры фасок и канавок не включают в общую размерную цепочку размеров;
канавки следует выносить и показывать их форму и размеры в масштабе увеличе-
ния.
8) Мелкие элементы разрешается увеличивать с отклонением от масштаба, ана-
логично разрешается увеличивать конусы и уклоны при их малых величинах.
9) Проставлять размеры в виде замкнутой цепочки не допускается, кроме случая,
когда один из размеров справочный.
10)На чертежах деталей проставляют допуски формы и расположения поверхно-
стей, шероховатость поверхностей, при необходимости указывают термическую обработку, отделку и т.п.
11)При большом количестве допусков формы их целесообразно концентрировать в одном месте чертежа, размеры – в другом.
12)При выполнении чертежей литых деталей необходимо указать формовочные уклоны, радиусы скруглений и др.
13)При выполнении чертежей сварных деталей (по сути сборочных единиц) необ-
ходимо приводить обозначения швов и их количество; допускается не указывать стыки между деталями и штриховать элементы соединения в одну сторону.
14)При выполнении чертежей корпуса и крышки необходимо указывать в квадрат-
ных скобках размеры в совместной обработке.
Основные способы простановки размеров: цепной, координатный и комбиниро-
ванный. Цепной способ обеспечивает точность расположения каждого последую-
щего элемента относительно предыдущего. Однако точность расположения эле-
ментов относительно общей базы, например, торца вала, последовательно умень-
шается. Цепной метод применяют, например, для простановки размеров межосе-
вых расстояний на чертежах корпусов и крышек редукторов.
При координатном способе размеры проставляют от одной базы (например,
торца вала). Этим обеспечивается точность расстояний всех элементов от базы, но снижается точность расстояний между самими элементами. Комбинированный спо-
соб состоит из цепного и координатного способов. Выбор рационального способа определяется конструктивными и технологическими требованиями.
Технические требования располагают над основной надписью, а при недостатке места – левее основной надписи. Их записывают в следующем порядке:
1.Требования к материалу, заготовке, термической обработке, например, «260…285НВ».
2.Указания о размерах. Примеры: «*Размеры для справок»; «Неуказанные радиусы R3»; «Формовочные уклоны 5º».
3.Неуказанные предельные отклонения размеров, например, «H14, h14, ±
IT14/2».
4.Указания о контрольных параметрах зубчатых колёс по типу: «Комплекс показателей точности устанавливается изготовителем по ГОСТ 1643-81».
5.Обработку по размерам в квадратных скобках производить совместно с дет.
поз. 3.
6.Детали применять совместно.
Впоследних двух пунктах показана запись для элементов, обрабатываемых совместно (например, подшипниковые расточки корпуса и крышки редуктора).
Восновной надписи материалы приводят с указанием стандартов: стали обык-
новенного качества (например, Ст5, Ст6) – по ГОСТ 380-88, стали углеродистые качественные (35, 45) – по ГОСТ 1050-88, стали легированные (40Х, 30ХГС) – по ГОСТ 4543-88, чугун серый (СЧ15, СЧ20) – по ГОСТ 1412-85, чугун ковкий (КЧ
30-6) – по ГОСТ 1215-79.
Вопросы конструирования изложены в достаточном количестве учебных посо-
бий и справочников [2, 3, 8, 11]. Требования к рабочим чертежам также приведены в СТО [12].
11.2. Чертежи валов
Пример рабочего чертежа ступенчатого вала приведен на рис. 51. Вал имеет простую конструктивную форму, поэтому выполнена одна проекция, дополненная выносными изображениями элементов и сечениями, разгружающими основное изображение. Упорный бурт для шестерни, увеличивающий размер заготовки, от-
сутствует, так как принято центрирование по цилиндру, когда длина ступицы больше диаметра. Вал имеет ступени, предназначенные для упора полумуфты и подшипников. Торцы снабжены фасками, галтелями или кольцевыми канавками.
Шпоночные пазы спроектированы вдоль оси симметрии на одной стороне вала. В целях унификации приняты шпонки одинакового сечения. Проекции пазов с полукруглыми торцами соответствуют их изготовлению пальцевой фрезой. Такая форма обеспечивает хорошую устойчивость шпонки в пазу. При такой технологии изготовления боковые поверхности паза, являющимися рабочими, имеют доста-
точно высокий класс шероховатости (Ra = 3,2 мкм). Нерабочая поверхность осно-

вала ступенчатого чертёж Рабочий .51 .Рис
|
|
|
|
|
|
|
|
|
|
Ra 5 ( |
) |
|
|
|
|
|
318 |
|
|
|
|
|
|
|
|
|
|
120 |
|
|
|
138 |
|
|
|
|
|
|
A |
|
|
|
|
|
|
|
|
|
|
|
|
|
|
|
Б |
|
|
|
|
|
10 |
28 |
6 |
80 |
0,5x45° |
|
|
|
|
|
|
|
|
|
15 |
96 |
|
|
|
||||
|
a |
|
|
|
E |
|
|
|
|
||
|
R |
|
2,5 |
|
|
|
80 |
6 |
|
|
|
|
|
Ж 65s6 |
В |
|
Ж 55h10 |
|
|
||||
|
|
|
|
Ra 10 |
|
|
|||||
|
|
|
a |
|
|
|
|
||||
|
1,5x45° |
|
|
Б |
Г |
|
|
||||
|
|
R |
|
|
|
||||||
Ra 1,25 |
4 фаски |
|
|
|
Ra 3,2 |
|
|
|
|||
|
|
|
|
|
|
|
|||||
55k6 |
|
|
|
|
Ж 60 |
|
|
|
50h6 |
|
|
Ж |
|
|
|
|
|
|
|
|
Ж |
|
|
|
|
|
|
|
|
55k6 |
|
Ra 0,32 |
2,5x45° |
|
|
|
A |
Д |
|
|
|
|
|
|
|
||
|
|
|
В |
Ra 1,25 |
|
|
|
|
|||
|
|
|
|
|
|
|
|
|
|||
|
|
|
|
|
Ж |
Г |
|
|
|
||
|
|
|
|
|
|
|
|
|
|
||
|
|
|
|
|
|
|
|
|
|
|
|
|
|
|
|
|
|
|
Ra 2,5 |
|
|
|
|
10 |
B-B |
|
10 |
Г-Г |
|
|
|
|
|
|
|
a |
|
|
a |
|
|
|
|
|
|
|
|
R |
|
|
R |
|
Д (4:1); |
Е (4:1) |
|
|
|
|
|
|
|
|
|
|
|
|
|
|
|||
5,5+0,2 |
|
|
5,5+0,2 |
|
|
|
|
|
|
|
|
|
|
|
|
|
Ж 54 |
|
|
1. HRC 32...36. |
|
|
|
|
|
|
|
|
|
|
|
|
|
|
|
14P9 |
|
|
14P9 |
|
|
|
|
2. Неуказанные радиусы R 0,25...0,40. |
|
|
|
|
|
|
|
|
|
3. H14; h14; ±IT14/2. |
|
|
|||
|
|
|
|
|
|
|
|
|
|
||
|
|
|
|
|
45° |
|
R1,6 |
|
|
|
|
|
|
|
|
|
|
5 |
|
|
|
|
|
|
|
|
|
|
R0,5 |
|
|
|
|
|
|
|
|
|
|
|
|
|
|
|
|
|
|
T0,1 |
|
|
T0,1 |
|
|
|
|
|
ДМ.М311.09.09.01.00.14 |
||
|
|
|
|
|
|
|
Лит. |
|
|
||
|
|
|
|
|
|
|
|
Пров. |
У T |
5,7 |
1:1 |
|
|
|
|
|
|
|
|
|
|
|
|
|
|
|
|
|
|
|
|
|
Лист |
Листов 1 |
|
|
|
|
|
|
|
|
|
|
Круг |
|
|
|
|
|
|
|
|
|
|
Утв. |
|
|
|
|
|
|
|
|
|
|
|
|
Формат А2 |
|

вания паза имеет на 1…2 класса ниже. Шпоночные пазы располагают на расстоя-
нии от соседних торцов 5…10 мм.
Все осевые размеры проставлены вверху, допуски формы и отклонения поверх-
ностей показаны вверху и внизу изображения. На чертеже представлен комбиниро-
ванный способ простановки размеров. Размеры шпонок, фасок и канавок включены в размер ступени. Длина шпонки привязана к ближайшему торцу.
Показаны выносные сечения со шпоночными пазами и выносное изображение
кольцевой подточки. На выносных сечениях приведены размеры шпоночного паза с предельными отклонениями, шероховатость поверхностей и допуски параллель-
ности и симметричности рабочих граней паза [8]. Глубина паза t1 показана от дуги окружности, показанной тонкой линией на сечении, фактически от цилиндриче-
ской поверхности вала.
Все сопряжённые диаметры изображены с предельными отклонениями. Для хво-
стовиков назначают переходные посадки (k6, m6, n6), при ударных нагрузках – посадки с гарантированным натягом (p6, r6). Для шеек валов редукторов принима-
ют переходные посадки, обеспечивающие гарантированный натяг (js6, k6, m6, n6) в
сопряжении с подшипником, например, L0/k6. Зубчатые колёса напрессовывают на головки валов по сопряжениям H7/p6 (основное соединение – шпоночное) либо
H7/r6 или H7/s6 (основное соединение – прессовое). При наличии распорных вту-
лок и колец их сопрягают по h6 или h7.
Все цилиндрические поверхности вала, в том числе несопряжённые, имеют высокий класс шероховатости, так как они подвержены знакопеременным напря-
жениям. Условные обозначения шероховатости поверхностей приведены на верх-
них частях изображения вала. Сопряжённые поверхности хвостовика выполняют по Ra = 2,5…5 мкм; поверхности шеек и головки - Ra = 1,25…2,5 мкм. Торцы за-
плечиков под подшипники и зубчатые колёса обрабатывают по Ra = 2,5 мкм, торец под муфту – по Ra = 5 мкм, торцы вала – по Ra = 10 мкм.
Шероховатость обозначена знаком, аналогичным знаку радикала с указанием параметров микронеровности, по типу: Ra1,25 . Острие знака указывает на обраба-
тываемую поверхность либо на выносную линию, проведенную от этой поверхно-
сти. Знак шероховатости указывают также на линиях-выносках, на их полках, на