
ТПАП
.pdf71
шины по конструкции (виду рабочего органа) делятся на дисковые и барабанные.
Наибольшее распространение получили дисковые рубительные машины. В них на вращающиеся в вертикальной, горизонтальной или наклонной плоскости диска под постоянным углом наклона к поверхности расположены режущие ножи. Наиболее распространенными марками рубительных машин являются: ДУ-2А; ДШ-4, ФРГ-1200НВ 1100S и т.д.
Для производства плит плоского прессования рекомендуется фракция стружки 40/5, т.е. щепа, проходящая через сито с размерами ячеек 40х40 мм и остающаяся на сите с размером 5х5 мм.
Полученная на рубительных машинах щепа различна по фракционному составу и подвергается сортировке, где удаляется мелочь, выделяется кондиционная фракция и отделяются крупные частицы, которые возвращаются для повторного измельчения.
Для сортировки щепы применяются в основном плоские сортирующие устройства. Рабочей частью его является сито с отверстиями определённых размеров круглого или квадратного сечения. Сита устанавливают в подвижной коробке и совершают качательные движения. Марки: СЩ-1М; СЩ-120
Таким образом, производится ударное измельчение древесины. Ударное измельчение не обеспечивает получения древесных частиц за-
данной толщины. Эта задача решается путём измельчения древесины резанием на стружечных станках. Также резанием получают стружку из круглых лесоматериалов, после её разделки на метровые чураки. Основным типом оборудования для этой операции являются стружечные станки с ножевым валом марок ДС-6; ДС-8.
На станках с ножевым валом и дисковых станках получаем плоскую стружку для всех слоёв плит.
Длинномерная древесина перерабатывается в стружку без предварительной разделки по длине на станках немецкой фирмы “Хомбак” типа Z- 130-55. Щепа и мелкие кусковые отходы перерабатываются в стружку на
72
центробежных стружечных станках ДС-5; ДС-7, а также фирмы “Пальман” и “Майер”.
Рабочим органов этих станков является ножевой барабан и крыльчатка, которые расположены на одной оси в корпусе и вращаются в противоположные стороны.
Центробежные станки изготавливают игольчатую резаную стружку, неравномерную по толщине, которая используется только для внутреннего слоя плит, или для наружного слоя после специальной дополнительной обработки.
Вторичное (повторное) измельчение стружки.
Размеры стружки, получаемые при первичном измельчении резанием, не отвечают требованиям производства ДСП по ширине, а при ударном измельчении и по толщине. Поэтому в технологическом процессе производства плит предусмотрено вторичное измельчение древесных частиц.
Для вторичного измельчения стружки используют молотковые, лопостные и зубчато-ситовые дробилки, в которых измельчение происходит ударом или размолом.
Молотковые дробилки ДМ-7. Измельчение стружки осуществляется билами. Молотковая дробилка представляет собой ротор, состоящий из дисков, на которых установлено 150 пластин-молотков.
Из лопастных дробилок отметим отечественную модель ДМ-3, немецкие – фирмы “Кондукс”.
Указанные выше дробилки обеспечивают измельчение стружки по длине и ширине. Но с резким увеличением объёма производства облицованных ДСтП возросли требования к размерам и качеству стружки наружных слоёв. Поэтому возникла необходимость дополнительного измельчения стружки ещё и по толщине.
Для этого отечественная промышленность выпускает дробилку ДМ-8, при разработке которой за основу был принят стружечный станок ДС-7.
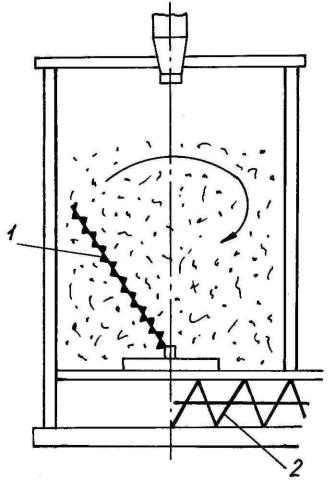
73
Транспортировка щепы и стружки в цехи осуществляется на ленточных, скребковых и винтовых конвейерах, а также пневмотранспортными устройствами.
Для бесперебойной и надёжной работы всех агрегатов на определённых стадиях необходимы запасы технологической щепы и стружки.
Хранение запасов щепы может быть в кучах на открытых складах или вертикальных бункерах типа ДБО.
Схема вертикального бункера для щепы представлена на рис.9.
Рис.9. Бункер для хранения щепы.1 – ворошитель, 2 – винтовой разгрузчик
Для хранения межоперационных запасов стружки устанавливают горизонтальные бункера с дозирующими устройствами.
Это бункера с вертикальными стенками и подвижным дном марки ДБД-1. Горизонтальные бункера более сложны по конструкции, имеют
74
меньшую ёмкость, поэтому здесь может использоваться и вертикальный бункер ДБО-60 (если позволяют габариты стружечного цеха).
Сушка стружки. Влажность стружки оказывает решающее влияние на процесс прессования ДСтП. Высокая влажность повышает расход тепла на превращение воды в пар и увеличивает продолжительность прессования, также приводит к образованию пузырей или разрыву плит при размыкании пресса. При низкой влажности стружки, последняя поглощает значительное количество связующего, что приводит к снижению прочности плит.
Рекомендуемая влажность стружки в трёхслойных плитах 5-12% для наружных слоёв и 3-5 % для внутреннего слоя.
Для сушки стружки используется отечественные сушилки завода “Прогресс” или импортные “Бютнер” и “Бизон”.
Существуют кондуктивные (контактные) и конвективные сушилки. При кондуктивной сушке тепло передаётся непосредственно от нагре-
того тела, недостаток истирание стружки при перемешивании, достоинство низкий удельный расход тепла.
Конвективные сушилки могут быть с механическим и пневматическим перемешиванием стружки. В этих сушилках древесные частицы высушиваются во взвешенном состоянии в потоке газовоздушной смеси при температуре 200-600оС на входе в барабан и 90-100оС на выходе. Для увеличения производительности сушилок их дополняют циклонно-спиральными приставками, в которых на входе при t=600-800оС удаляется свободная влага.
Сортировка стружки. Устройства для сортирования стружки делятся на механические и пневматические.
Механическая сортировка осуществляется в закрытом коробе с помощью сит, расположенных под углом 4-6о к горизонтальной плоскости и совершающих плоскопараллельное качающее движение в горизонтальной плоскости.
В пневмосепараторах древесные частицы сортируются в воздушном потоке. Схема пневмосепаратора представлена на рис. 10.
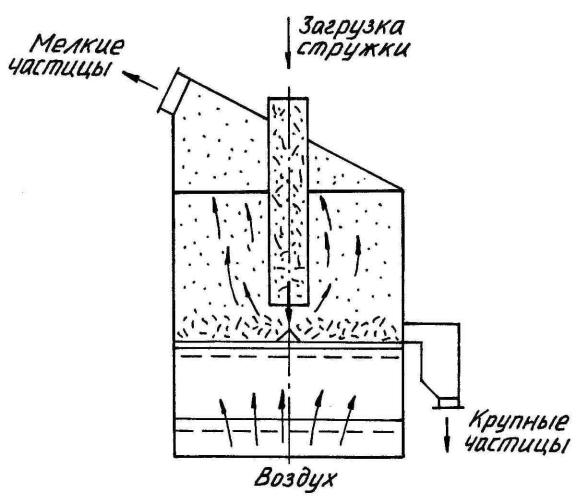
75
Рис. 10. Схема пневмосепаратора Сухая стружка складируется в бункерахи затем дозировано подается к
смесителю.
В качестве связующего, обычно, используют карбамидоформальдегидную смолу и отвердитель – хлористый аммоний. Количество отвердителя соответствует 0,7 – 1% от массы жидкого рабочего раствора связующего.
Для качественного распыления связующего его вязкость должна составлять 13 – 22 с по вискозиметру ВЗ – 246. Приготовление рабочего раствора осуществляется путем добавления воды. При этом концентрация связующего снижается до 50 – 55. Снизить вязкость можно также путем нагревания смолы до температуры 30 – 35о С.
Количество связующего для наружных слоев составляет 13 – 15%, для внутренних – 9 – 11% от массы абсолютно сухой стружки.
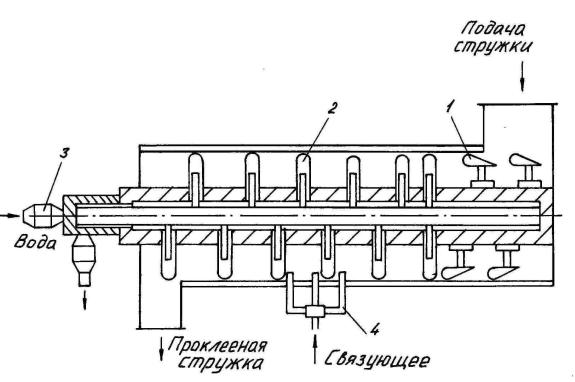
76
Смешивание стружки со связующим происходит в смесителях рис.11. Сегодня наиболее распространенными являются малогабаритные скоростные смесители с безвоздушным распылением связующего ( марки ДСМ – 5), что позволяет исключать применение пневматических форсунок, так как они постоянно засоряются клеем.
Рис. 11. Схема скоростного смесителя: 1 – захватывающие лопасти; 2 – перемешивающие лопасти; 3 – устройство для ввода воды в полый вал; 4 – сопла подачи связующего
Операции главного конвейера. Проклеенную (осмоленную) древесную стружку необходимо превратить в ковер или плоский пакет. Это первая операция главного конвейера, схема которого представлена на рис.12.
Формирующие машины предназначены для дозирования и равномерной насыпки осмоленной стружки на движущиеся поддоны. Для формирования многослойных плит последовательно устанавливается несколько машин марок ДФ – 1, ДФ – 6.

77
Рис. 12. Схема главного конвейера: 1 – цепные конвейеры; 2 - формирующие машины; 3 – холодный пресс; 4 – контрольные весы; 5 – горячий пресс; 6 – отделитель плит от поддонов; 7 – камера охлаждения поддонов
Подпрессовка стружечного пакета выполняется для уменьшения его толщины и придания транспортной устойчивости при движении по конвейеру. Выполняется эта операция в холодных одноэтажных гидравлических прессах ПР-5. Загрузка и выгрузка пакетов в пресс автоматическая. Режимы холодного подпрессовывания: давление плит пресса 1,5 МПа, продолжительность выдержки 4 секунды.
Уплотненный пакет поступает на контрольные весы для контроля массы плиты. Масса пакета обуславливает требуемую плотность готовой плиты и ее физико-механические показатели.
Наиболее ответственная операция технологического процесса производства ДСтП – горячее прессование. Головное оборудование – горячие многоэтажные пресса периодического действия типа ПР – 6 с загрузочноразгрузочной этажеркой. Загрузка всех пакетов производится одновременно с помощью автоматического загрузчика. Одновременное смыкание плит пресса обеспечивается симультанным механизмом. Заданная толщина плит обеспечивается дистанционными прокладками, прикрепленным к плитам
78
пресса. Выгрузка плит осуществляется специальными захватами, которые одновременно вытаскивают поддоны с готовыми плитами на разгрузочную этажерку. Далее плиты последовательно выгружаются на конвейер и отделяются от металлических поддонов.
Основными параметрами режима прессования, определяющими качество плит и производительность пресса, являются: температура прессования, давление и продолжительность прессования. Температуру прессования обычно принимают 160-180о С в многоэтажных и 180-220о С в одноэтажных прессах. Давление прессования зависит от плотности плиты, породы древесины, влажности стружки и др. факторов. В процессе прессования оно остается постоянным и равно 2,3 – 2,7 – 3,3 МПа, а уменьшается ступенчато или плавно. Продолжительность прессования зависит от типа плиты, ее плотности и толщины, температуры прессования, влажности осмоленной стружки. Рекомендуется устанавливать продолжительность прессования в пределах от 0,2 до 0,52 мин на 1 мм толщины готовой плиты. – продолжительность вспомогательных операций
Производительность горячего пресса определяет производительность всего завода по производству ДСтП и определяется по формуле
П = |
60nlbδК |
м3/час, |
(31) |
||
τ +τ |
всп |
||||
|
|
|
|||
|
|
|
|
где n – число этажей пресса; l – длина ЛСтП, м;
b –ширина ДСтП, м;
δ – толщина плиты, м;
К– коэффициент использования главного конвейера (К=0,85-0,90); τ- продолжительность прессования , мин;
τвсп – продолжительность вспомогательных операций, мин; (τвсп=1,5-
2,0мин).
Кондиционирование древесностружечных плит производят сразу же после горячего прессования. Эта операция производится для выравнивания внутренних напряжений в плите. Для этой цели используются камеры
79
кондиционирования с принудительной циркуляцией воздуха и охладители веерного типа.
Обрезка ДСтП по периметру для выравнивания кромок и установления прямоугольности углов производится на четырехпильных форматнообрезных агрегатах. Этот агрегат состоит из двух спаренных между собой и расположенных под углом 90о двухпильных станков.
Шлифование ДСтП производится на автоматических линиях ДЛШ50 , смонтированных на базе широколенточных шлифовальных станков ДКШ-1. Шлифование производится по пласти одновременно с двух сторон шлифовальными шкурками на первом проходе №80-40 и на втором - №3225. Далее шлифованные ДСтП укладываются пачками высотой до 1,8 м и складируются на складах.
5.Технология изделий из древесины.
5.1.Материалы для приготовления изделий из древесины можно разделить на конструкционные, облицовочные и на материалы, характерные для производства мебели для сидения и лежания. А также клей, фурнитура, стекло, зеркала, элементы декоративного оформления изделий, отделочные материалы.
Конструкционные материалы - это материалы, из которых изготавливают детали конструкций, воспринимающих нагрузку. К ним относятся древесина, древесностружечные и древесноволокнистые плиты, фанера, пластические материалы, металл.
Древесина. Ее достоинства разбирались ранее. Но древесина имеет и недостатки: анизотропность (разные механические характеристики в зависимости от направления волокон), наличие различных пороков (сучки, трещины, сердцевина, наклон волокон, сдежистость, кривизна и т.д.), размеро- и формо-изменяемость (усушка, разбухание, покоробленность), гигроскопичность, горючесть.
80
Древесностружечные плиты. Положительные свойства: сравнительно большие размеры, хорошо склеивается, обрабатывается и отделывается, примерно одинаковые физико-механические свойства по длине, ширине и толщине, гигроскопичность ниже, чем у натуральной древесины. Недостатки: формоизменяемость (покоробленность), значительная разнотолщинность, низкая шурупоудерживающая способность кромок, токсичность.
Столярные плиты применяются тогда, когда необходима высокая прочность и легкость элементов. Недостатки: сложность и трудоемкость изготовления, значительный расход массивной древесины.
Древесноволокнистые плиты. Обладают почти одинаковыми с натуральной древесиной физико-механическими свойствами (твердые древесноволокнистые плиты), характерна одинаковая прочность по всем направлениям, хорошо поддаются всем видам механической обработки.
Из них изготавливают донья ящиков и другие емкостей, задние стенки, облицовочный материал.
Фанера. Применяют для изготовления столярных плит, пустотелых щитов, задних стенок и ящиков корпусной мебели.
Облицовочные материалы:
Древесные - шпон строганный (Подробно рассматривался в разделе «Производство строганого шпона»).
Декоративные пленки на основе пропитанных бумаг. В пленках с частичной поликонденсацией смолы, смола обладает хорошей текучестью. Поэтому пленку приклеивают без применения дополнительного клея за счет собственной смолы. Такие пленки позволяют совместить две операции – облицовывание с одновременным получением отделочного покрытия. Эти пленки производятся с применением меламиноформальдегидных смол. Они применяются при изготовлении ламинированных плит. Пленки с полной поликонденсацией смолы называется листовой синтетический шпон.
Декоративный бумажно-слоистый пластик (ДБСП). В его составе до 65% бумаги. Она выполняет две функции: армирующий наполнитель, при-