
ТПАП
.pdf
51
Рис. 7. Схема лущения чурака Скорость резания является величиной переменной, т.к. число оборотов
чурака постоянно, а диаметр чурака в процессе лущения уменьшается. Чурак зажимают между шпинделями станка путем их осевого перемещения. Вращательное движение шпиндели получают от электродвигателя. Нож крепится на суппорте, движение которого осуществляется с помощью механизма подачи. Максимальная длина обрабатываемого чурака (ширина ленты шпона) зависит от расстояния между зажимными кулачками. У современных станков оно в пределах 500 - 5000 мм. Наибольший диаметр обрабатываемых чураков зависит от высоты центров шпинделей над станиной. В современных станках оно составляет 400 – 2000 мм.
После разлущивания чурака остается отход в виде цилиндра, называемый карандашом. Диаметр карандаша зависит от диаметра зажимных кулачков. Для уменьшения диаметра карандаша кулачки делают телескопическими. В начале процесса лущения чурак зажимают наружными кулачками, имеющими диаметр 100 – 110 мм, а затем в конце процесса зажим осуществляют внутренними кулачками диаметром 55 – 65 мм.
Толщина шпона представляет собой величину подачи ножа на один оборот шпинделя. В последних моделях станков диапазон толщины может находиться в пределах 0,05 – 5 мм.
52
При свободном резании древесины на левой стороне шпона, обращенной к чураку, возникают трещины и неровности:
Для их ликвидации применяют обжим шпона с помощью прижимной линейки, которая устанавливается так, чтобы создаваемое ей давление было направлено через режущую кромку ножа. При этом зазор между ножом и линейкой должен быть не меньше расчетной толщины шпона. Степень обжима можно определить по формуле:
|
= |
S−S0 |
100% , |
(19) |
|
|
|||
|
|
S |
|
|
|
0 |
|
|
|
где |
S – расчетная толщина шпона, мм; |
|
||
|
S0 – расстояние между ножом и прижимной линейкой, мм. |
Для обеспечения требуемого качества шпона степень обжима должна
быть выдержана в пределах 10 – 30 % в зависимости от породы древесины, толщины шпона и температуры чурака.
При разлущивании чурака выделяют четыре зоны (рис. 8).
1 – зона рванины, являющаяся следствием неправильной формы чура-
ка;
2 - зона длинных кусков, являющаяся следствием неправильной установки чурака между шпинделями станков;
3 – зона полноформатного шпона;
4 – зона карандаша.
Объем древесины в каждой зоне может быть охарактеризован следующими цифрами: зона рванины 20 – 23 %; зона длинных кусков 4 – 5 %; зона полноформатного шпона 57 – 59 %; зона карандаша 15 – 17 %.
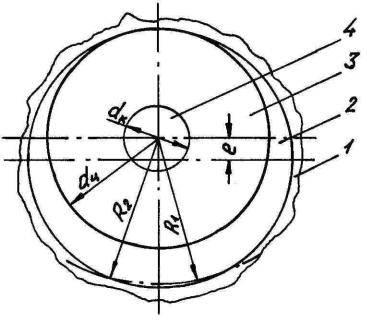
53
Рис. 8. Зоны лущения чурака В случае лущения чурака на станке, оборудованном центровочным
устройством, полезный выход может быть определен по формуле:
|
q = |
πlч |
(Кв2dч2 − dк2 ), |
(20) |
||
|
|
|||||
|
|
|
4 |
|
|
|
где |
dч – диаметр чурака, м; |
|
||||
|
dк – диаметр карандаша, м; |
|
||||
|
lч – длина чурака, м; |
|
||||
|
Кв – коэффициент выхода сырого шпона из чурака. |
|
||||
|
Объем чурака, оставшегося после лущения, определяется по формуле: |
|||||
|
qк = |
πd |
2 |
|
||
|
4 |
к lч , м |
(21) |
|||
|
|
|
|
|
Объем рванины из одного чурака определяется по формуле: Q=qч-qш.п.-qк, (22)
где qч– объем чурака, м3.
Выход шпона выражается в % от объема чурака:
p = |
qш |
100% . |
(23) |
|
|||
|
qч |
|
Кусковой шпон, образующийся в начальной стадии лущения, используется для изготовления малоформатной фанеры или серединок полноформатной. Минимальная длина отбираемых кусков 0,8,м, минимальная ширина
54
– 0,13 м. Правильная организация отбора кусков увеличивает выход шпона
на 4 – 4,5 %.
В настоящее время наиболее широко применяются лущильные станкимарки ЛУ 17-4; ЛУ 17-10 (Россия); SF 2350 (Италия); Токио Плитвуд МК
(Япония).
Шпон, получаемый при разлущивании чурака, имеет вид ленты, ширина которой равна длине чурака, а длина зависит от диаметра чурака и толщи-
ны шпона.
На выходе из лущильного станка лента шпона разрезается на отдель-
ные ленты, ширина которых определяется из выражения: |
|
В=Вф+ о+ у, |
(24) |
где Вф – ширина готового листа фанеры, мм;
0 – припуск на обрезку (75-80) мм;
у – припуск на усушку в зависимости от породы древесины и размера листа, мм.
Раскрой ленты осуществляется на ножницах различных типов (НФ-18; НФ-1803), снабженных устройством для укладки листов шпона в стопу. Как правило, лущильный станок и ножницы встраиваются в полуавтоматическую поточную линию: лущение – рубка – укладка шпона (ЛУР 17-3 состоит из ЛУ 17-4 и НФ 18-3).
4.3.5. Сушка шпона
При склеивании шпон должен иметь влажность 6-12 %. Поэтому шпон подвергают сушке сразу же после выхода из лущильного отделения.
В связи с малой толщиной шпона, напряжения, возникающие в нем, незначительны. Значит сушку можно осуществлять по более жестким режимам, чем пиломатериалы.
Существует 3 способа сушки шпона: кондуктивный, конвективный и кондуктивно-конвективный.
55
При кондуктивном – тепло передается высушиваемому материалу в результате его соприкосновения с нагретым телом. Этот способ используется в так называемых «дыхательных» прессах. Они периодически размыкались для выхода пара. В настоящее время практически не используются.
При конвективном способе передача тепла осуществляется посредством агента сушки: горячий воздух или топочный газ. Этот способ используется в ленточных сушилках (камера, в которой циркулирует воздух). Шпон перемещается по проволочным лентам специального плетения, которым сообщается движение от специального привода. Температура агента сушки 60120 оС; скорость движения воздуха 0,9-1,1 м/с; продолжительность сушки 2090 мин.
При кондуктивно-конвективном способе сушки передача тепла осуществляется сразу 2-мя способами. На этом способе работают роликовые сушилки. Это камеры, внутри которых в несколько рядов по высоте располагаются ролики.
В зависимости от вида агента сушки и направления его циркуляции различают:
•паровые роликовые сушилки с продольной противоточной циркуляцией;
•паровые роликовые сушилки с поперечной циркуляцией;
•газовые роликовые сушилки с прямоточной циркуляцией.
Продолжительность сушки зависит от температуры агента сушки, скорости циркуляции, толщины шпона, породы древесины, начальной и конечной влажности шпона. Обычно температура агента сушки у паровых сушилок 80-150, у газовых -160-300 о С; скорость движения воздуха 1,7-2,5 м/с; продолжительность сушки 3-15 мин.
Производительность роликовых и ленточных сушилок определяется по формуле:
A = |
m n L b S T |
KП KЗ KВ м3/смену, |
(25) |
|
|||
|
1000Z1 |
|
56
где m – число листов шпона на 1 этаж; n – число этажей;
L – полная рабочая длина сушилки, м; b – ширина сухого листа шпона;
S – толщина шпона, мм;
T – время работы сушилки в мин;
Кп – коэффициент, учитывающий переход от сушки шпона одного вида к другому. Кп = 0,9 – 1;
Кз – коэффициент заполнения сушилки по длине; Кз = 0,96 – 0,98; Кв – коэффициент использования рабочего времени;
Z1 – продолжительность прохождения шпона через сушилку, мин. После сушки шпон сортируется.
Сортировка может осуществляться непосредственно у сушилок, на транспортерах, перемещающих шпон к подстопным местам, а также на специально отведенных площадках.
Сортность шпона может быть повышена за счет починки. Починка заключается в вырубке из листа дефектов и вставки на их место заплаток из здоровой древесины. Заплатка должна входить с натягом в 0,1 – 0,2 мм.
Образующиеся в начале лущения куски шпона целесообразно соединять в полноформатные листы методом сращивания (гуммированной лентой, клеевой нитью).
4.5. Технология изготовления строганого шпона. Оборудование.
Строганый шпон – тонкий слой древесины красивой текстуры и цвета. Чаще всего его используют как облицовочный материал в производстве мебели и т.п.
Толщина строганого шпона зависит от породы древесины. Для рассе- янно-сосудистых лиственных пород она равна 0,4; 0,6 и 0,8 мм (бук, орех, яблоня, груша, красное и лимонное дерево); для кольцесосудистых – 0,8-1,0 мм
57
(дуб, карагач, шелковица, каштан). Шпон из древесины лиственных пород имеет толщину 0,8-1,0 мм. Вообще – от 0,4 до 1,0 мм.
Длина листов шпона от 550 мм и выше. Ширина зависит от сорта: I сорт – не менее 120 мм; II сорт – не менее 80 мм; влажность шпона 8±2 %.
Поперечный раскрой бревен на кряжи выполняется по той же технологии, что и распиловка бревен на чураки перед лущением.
Для производства строганного шпона отрезки кряжей должны быть ограничены как минимум двумя плоскими или параллельными поверхностями, являющимися базой и начальной поверхностью строгания.
Существует несколько способов продольного раскроя кряжей на ванчесы. Выбор схемы раскроя диктуется размерами сырья, породой древесины и желаемой текстурой.
Сердцевина в строганом шпоне не допускается. Заболонную древесину, имеющую светлую окраску или ненормальную окраску также удаляют.
Для разделки кряжей в продольном направлении применяют горизонтальные или вертикальные ленточные пилы и горизонтальные лесопильные рамы. Первые находят большее применение, т.к. обеспечивают большую точность реза, чистоту пропила и дают возможность распиливать кряжи больших диаметров. Также широко используются узкоспециализированные круглопильные станки фирмы «Кремона». Отличительная их особенность – возможность поворачивать кряж на любой угол вокруг продольной его оси.
Гидротермическая обработка кряжей перед строганием рассмотрена нами в разделе «Технология изготовления лущеного шпона».
Строганый шпон, как и лущеный, получают путем поперечного резания древесины в плоскости, параллельной волокнам. Обжим шпона осуществляется с помощью прижимной линейки.
Строгание шпона производят на горизонтальных, вертикальных или наклонных шпонострогальных станках.
На горизонтальных станках резание осуществляется в горизонтальной плоскости, главное рабочее возвратно-поступательное движение совершается
58
ножом, а движение подачи материалом в вертикальной плоскости во время холостого хода, на величину, равную толщине снимаемого слоя (толщине шпона).
Недостатком данного оборудования является вынужденное торможение хода суппорта перед переменой направления движения (нарушение плавного хода, износ оборудования, снижение скорости резания). Длина сырья 2-5 м; высотой до 1,2 м.
На вертикальных станках обрабатываемый материал помещается на каретке, совершающей возвратно-поступательное движение в вертикальной плоскости.
Нож устанавливают на суппорте, периодически перемещающемся в горизонтальном направлении для снятия древесины требуемой толщины. Эти станки компактны, удобен отбор шпона от станка. Но на каретке 1 можно установить только один брус.
Наклонные станки удобны при отборе листов шпона. Они менее энергоемки, имеют меньшие габариты. (Усовершенствованный вертикальный станок).
Количество шпона из одного ванчеса определяется по формуле:
F = |
(D − 2H1 − H2 ) |
l b , м2, |
(26) |
S |
ср |
|
|
где D – диаметр кряжа, из которого выпиливается ванчес, взятый посереди- |
|
не его длины, мм; |
|
H1 – высота сегмента, отделяемого от ванчеса при его продольной раз- |
|
делке, мм; |
|
H2 – толщина доски, остающейся после строгания ванчеса, мм; |
|
S – толщина шпона, мм; |
|
l – длина ванчеса, м; |
|
bср – средняя ширина листов, м.
В процессе строгания листы шпона укладываются в пачку (кноль) в той последовательности, в которой они выходят из станка. Это облегчает подбор листов по текстуре при склеивании их на ребро.
59
Изготовленный шпон сушат, сортируют, прирезают и упаковывают. Для сушки используют роликовые и ленточные сушилки. Режимы
сушки более мягкие, чем у лущеного шпона: температура сушки 80-130 оС; влажность 15-25 %; продолжительность сушки 6-35 мин.
4.6. Технология изготовления фанеры. Оборудование.
Исходным материалом в производстве клееной фанеры является лущеный шпон и клеи. При изготовлении облицованной фанеры в качестве рубашек используют строганый шпон, пленки на бумажной основе и др.
Для склеивания фанеры обычно применяют карбамидоформальдегидные, фенолоформальдегидные клеи, реже казеиновые и др. клеи. Склеивание может осуществляться холодным и горячим способом. Холодный способ склеивания используется реже, т.к. снижает производительность и требует больших производственных площадей.
Технологический процесс изготовления клееной фанеры включает следующие операции: нанесение клея на шпон; сушка листов шпона, намазанных клеем; сборка пакетов; склеивание; обрезка; шлифование; сортировка; маркировка и упаковка.
4.6.1. Нанесение клея на шпон. Слой наносимого клея должен быть равномерным по толщине, непрерывным, его количество должно соответствовать норме расхода (т.к. стоимость клея в себестоимости готовой фанеры составляет до 20 %). Клей можно наносить на обе поверхности одного четного листа шпона или на одну поверхность каждого листа шпона.
Способы нанесения клея:
1. Контактный – с помощью клеевых вальцов. Поверхности вальцов резиновые, гладкие или рифленые. На клеенаносящих станках клей наносится на обе поверхности листа. Вязкость по ВЗ-460=300с; расход клея может регулироваться от 70-240 г/м2.
60
2. Облив – перемещение листа шпона через вертикальную клеевую заве-
су.
Ширина щели головки зависит от вязкости клея. А толщина наносимого слоя клея – от ширины щели головки, вязкости клея и скорости движения шпона. Давление воздуха в головке 0,1 МПа. Скорость подачи шпона 1,5- 3,3м/с.
Производительность клееналивной машины значительно выше, чем клеевых вальцов.
3.Экструзивный– выдавливание клея через цилиндрические сопла, расположенные в днище клеевой головки.
Клей распределяется по поверхности листа шпона при сжатии собранных пакетов в прессе или при пропускании через специальные вальцы.
4.Пневматическое распыление – с помощью энергии сжатого воздуха. Вытекая через сопло воздух дробит струю клея на мелкие капли. Давление воздуха 0,25-0,5 МПа; скорость воздуха близка к скорости звука. Вязкость клея по ВЗ – 4 равна 40секунд.
Этот способ применяется для нанесения клея при производстве ДСтП.
5.Механическое распыление – клей подается под большим давлением (3-6 МПа), и ему придается вращательное движение.
4.6.2.Сушка шпона, намазанного клеем. Эта операция необходима при использовании однокомпонентного клея СФЖ-3011 (фенольный). Без просушки невозможно получить сплошной непористый клеевой слой равномерной толщины. Подсушку можно заменить открытой выдержкой листов шпона в течение 1 часа.
Сушку шпона осуществляют в сушильных камерах периодического и непрерывного действия до влажности 10±2 % горячим воздухом. Режим сушки должен быть таким, чтобы отверждение клея не превышало 2 %. Температура воздуха в сушилке 80-90 oC; относительная влажность воздуха 5-