
ТКМ Часть 1 (2)
.pdf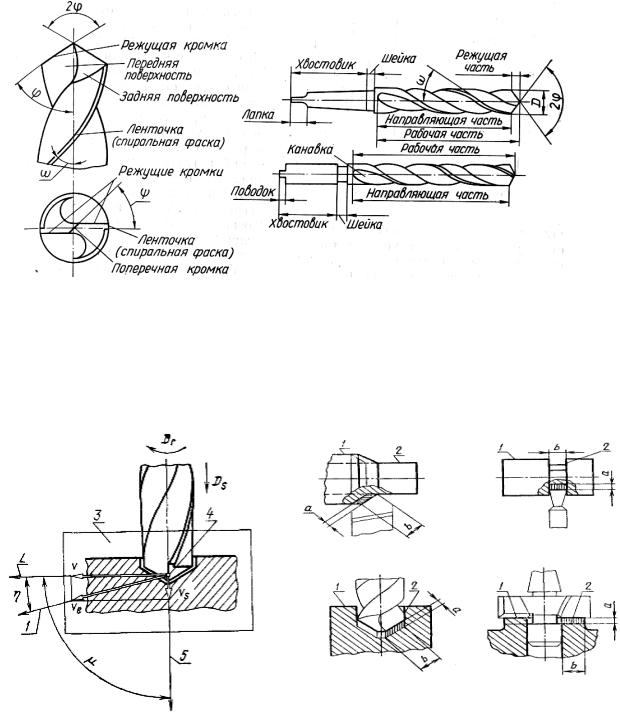
Рис. 2.2. Элементы конструкции спирального сверла Элементы движений в процессе резания при сверлении представлены на
рис. 2.3. Главным движением резания Dг при сверлении является вращательное движение сверла, а движением подачи Ds – поступательное перемещение сверла в направлении оси просверливаемого отверстия (см. рис. 2.3, а).
а б
1 – направление скорости результирующего движения резания Ve; 2 – направление скорости главного движения резания V; 3 – рабочая плоскость Ps; 4 – рассматриваемая точка главной режущей кромки; 5 – направление скорости движения подачи Vs; – угол скорости резания между направлениями скорости главного движения резания V и результирующей скорости резания Vе; Dг – главное движение резания; Ds – движение подачи; a – толщина срезаемого слоя; b – ширина срезаемого слоя
Рис. 2.3. Движения в процессе сверления (а) и элементы срезаемого слоя (б)
21

Элементы рабочей части сверла показаны на рисунках 2.2 и 2.4. Направляющая часть имеет две винтовые канавки 1 для вывода стружки, которые делят рабочую часть сверла на два зуба. На поверхности 2 расположена ленточка 3, которая служит для направления сверла при резании и уменьшения трения его о стенки обрабатываемого отверстия. На режущей части сверла располагаются главные режущие кромки К, которые непосредственно участвуют в процессе резания, а также поперечная режущая кромка Кп, необходимая в начальный момент для врезания инструмента в сплошной материал заготовки. Передней поверхностью Aγ зуба сверла является криволинейная поверхность канавки, по которой сходит стружка, главной задней поверхностью Aα – спинка зуба, а вспомогательной задней поверхностью – поверхность ленточки.
Ps
ψ
|
|
|
|
|
|
|
|
|
|
|
|
|
|
|
|
|
п |
|
|
Pν |
|
|
|
|
|
|
|
|
|
|
|
|
|
Ps |
|
|
|
|
|
|
|
|
|
|
|
|
|
|
|
|
|
|
||||
|
|
|
|
|
|
|
|
|
|
|
|
|
|
|
|
|
|
|
|
|
|
|
|
|
|
|
К1 |
|
|
|
|
|
|
|
|
||
|
|
|
|
|
|
|
|
|
Pτ |
|
|
|
|
|
|
|
||
|
|
|
|
|
|
|
|
φ1 |
ω |
Aγ |
|
|
|
|
||||
V |
|
|
|
|
|
|
|
|
|
|
|
Psx – Psx |
||||||
|
|
|
|
|
|
|
|
|
|
|
|
Psx |
|
|
|
Pn |
||
|
|
|
|
|
|
|
|
|
|
|
|
|
|
|
|
|
||
|
|
|
|
|
|
|
|
|
|
|
|
|
|
|
|
|
||
|
|
|
|
|
|
|
|
|
|
|
|
|
|
|
|
|
|
|
|
Pν |
|
|
|
|
|
|
|
|
|
|
Aα |
|
|
|
|
α |
|
|
|
|
|
|
|
|
|
|
|
|
x |
|
|
|||||
|
|
|
|
|
|
|
|
|
|
|
|
|
||||||
|
|
|
|
|
|
|
|
|
|
|
|
|
||||||
|
|
|
|
|
|
|
|
|
|
|
|
|
|
|||||
|
|
|
|
|
|
|
|
|
|
|
|
|
|
|
||||
|
+ |
|
Pτ – Pτ |
|
|
|
|
|
|
|||||||||
|
|
|
|
|
|
|
Ps |
|||||||||||
|
|
|
|
|
|
|||||||||||||
– |
Pν |
|
|
|
|
|
α |
|
|
|
|
|
||||||
|
|
|
|
|
|
|
|
|
|
|||||||||
|
|
γ |
|
β |
|
|
|
|
|
|
|
|
|
|||||
|
|
|
|
|
|
|
|
|
|
|
|
|
|
|
||||
|
Aγ |
|
|
|
|
|
|
|
|
2φ |
|
|
|
|
||||
|
+ |
|
|
|
|
|
|
Aα |
|
Psx |
|
|
|
Pτ |
||||
|
|
|
|
|
|
|
|
|
|
|
||||||||
|
|
|
|
|
|
|
|
|
|
|
|
|
||||||
|
Pn |
|
|
|
|
|
|
|
|
|
|
|
||||||
|
– |
|
|
Pν |
|
|
|
|
|
|
|
|||||||
|
|
|
|
|
|
|
|
|
|
|
|
|
|
Рис. 2.4. Конструкция и геометрия рабочей части спирального сверла
Конструкция и геометрия зуба сверла принципиально не отличаются от конструкции и геометрии токарного резца (см. рис. 1.2). Пересечение главной К и вспомогательной К1 режущих кромок (см. рис. 2.4) образует вершину зуба 4.
Спиральное сверло имеет ряд конструктивных особенностей:
22
передняя поверхность лезвия Aγ является винтовой, поэтому передний угол γ, измеряемый в главной секущей плоскости Рτ между касательной к передней поверхности в рассматриваемой точке режущей кромки и основной плоскостью Рv, проведенной через эту точку, уменьшается от периферии к центру, а для поперечного лезвия Кп он имеет отрицательное значение. Угол γ определяет угол наклона винтовой канавки ω. Передний угол в любой точке х на режущей кромке может быть рассчитан по формуле:
tgγx = (dx /d) tgω/sin φ, |
(2.1) |
где ω – угол наклона винтовой канавки (см. рис. 2.2), измеряемый между осью сверла и касательной к винтовой линии по наружному диаметру d; принимается от 18° для мелких сверл до 30° для более крупных;
dx – диаметр сверла в точке х.
задний угол сверла α переменный, измеряемый в осевом сечении плоскостью Рsх, – угол между касательной к главной задней поверхности Aα сверла, проходящей через некоторую точку х, лежащую на главной режущей кромке К,
иплоскостью, проведенной через эту точку перпендикулярно оси сверла. Сверло затачивается по главной задней поверхности таким образом, чтобы угол заострения β в каждой точке режущей кромки был примерно одинаковым, т. е. задний угол от периферии к центру увеличивается. В связи с этим принимаемый на периферии задний угол α = 6 – 8° доходит у оси сверла до 25°;
вспомогательная задняя поверхность лезвия цилиндрическая (поверхность ленточки), поэтому вспомогательный задний угол α1 равен нулю;
главные задние поверхности зубьев при пересечении образуют поперечную режущую кромку Кп (см. рис. 2.4). Угол наклона поперечной режущей кромки ψ измеряется между проекциями поперечной и главной режущих кромок на плоскость, перпендикулярную оси сверла, при этом ψ = 50 – 55°;
вспомогательный угол в плане φ1 (см. рис. 2.4) обеспечивается за счет изготовления рабочей части сверла с обратной конусностью, т. е. сверла диаметром свыше 18 мм уменьшают по диаметру на 0,05 – 0,12 мм на каждые 100 мм длины рабочей части от поперечной режущей кромки к хвостовику. В результате этого уменьшается трение направляющей части сверла о стенки обработанного отверстия;
23
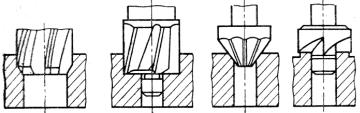
угол при вершине сверла 2φ оказывает большое влияние на процесс сверления и зависит от свойств обрабатываемого материала. Для стандартных сверл угол 2φ принимается равным 116 – 118°. Если сверла используются для обработки заготовок из твердых или хрупких материалов, то угол при вершине должен быть в пределах 130 – 140°, если они применяются для сверления мягких и вязких материалов или не жестко закрепленных листовых изделий – угол при вершине затачивается в пределах от 90 до 110°.
2.1.2. Зенкеры
Зенкер – многолезвийный режущий инструмент для предварительной или окончательной обработки просверленных, штампованных или отлитых отверстий с целью получения качества поверхности, соответствующего 10-му и 11му квалитетам точности, и шероховатости Ra до 6,3 мкм. Зенкеры подразделя-
ются: по назначению – на цилин- |
|
||
дрические для обработки цилин- |
|
||
дрических отверстий, |
конические |
|
|
для обработки конических отвер- |
|
||
стий и |
получения |
конических |
|
углублений под головки винтов и |
Рис. 2.5. Типы зенкеров |
||
шурупов, |
торцевые для получе- |
|
ния цилиндрических углублений и обработки торцевых поверхностей на выступах корпусных деталей (рис. 2.5); по конструкции – на цельные, насадные, сборные.
Конструкция зенкера схожа с конструкцией сверла. Припуск на зенкерование составляет 0,5 – 5,0 мм на диаметр и срезается режущей частью, которая не имеет поперечной режущей кромки, поскольку зенкер не предназначен для обработки отверстий в сплошном материале. Вспомогательные режущие кромки располагаются на ленточках калибрующей части. Количество зубьев зенкера составляет 2 – 4 (рис. 2.6).
24
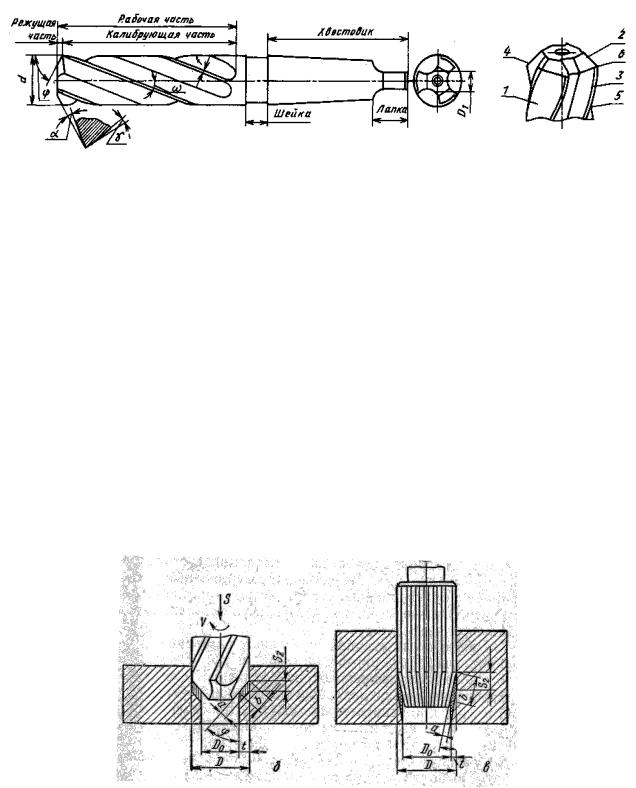
а |
б |
α – главный задний угол; γ – передний угол; φ – главный угол в плане; ω – наклона винтовой канавки; f – ширина ленточки; 1 – вспомогательная задняя поверхность; 2 – главная задняя поверхность; 3 – ленточка; 4 – главная режущая
кромка; 5 – вспомогательная режущая кромка; 6 – вершина зуба зенкера Рис. 2.6. Конструктивные элементы (а) и элементы рабочей части (б) цельного
цилиндрического зенкера
2.1.3. Развертки
Развертка – многолезвийный инструмент, предназначенный для предварительной и окончательной обработки цилиндрических и конических отверстий с квалитетом точности поверхности от 6-го до 10-го и шероховатостью Ra, равной 0,32 – 1,25 мкм, после их зенкерования (рис. 2.7).
а |
б |
V – главное движение резания; S – движение подачи; D – начальный диаметр; D0 – конечный диаметр; t – глубина резания; φ – главный угол в плане; a – толщина срезаемого слоя; b – ширина срезаемого слоя; S1 – величина подачи при зенкеровании; S2 – величина подачи при развертывании
25
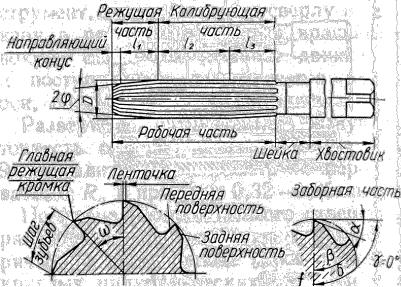
Рис. 2.7. Операции зенкерования (а) и развертывания (б) отверстия Развертка по конструкции аналогична зенкеру (рис. 2.8), так как процесс
развертывания, как видно из рис. 2.7, принципиально не отличается от процесса зенкерования. Основными конструктивными элементами цилиндрической развертки являются центрирующая часть с направляющим конусом и углом φ = 45°, режущая и калибрующая части, шейка и хвостовик.
l1 – участок срезающий припуск; l2 – цилиндрический участок; l3 – участок с обратной конусностью; ω – угол раствора соседних зубьев развертки
Рис. 2.8. Конструктивные элементы цилиндрической развертки
Шаг зубьев развертки выполняется неравномерным для уменьшения вибрации в процессе резания и величины огранки отверстия.
Высокое качество обработки объясняется большим количеством зубьев (от 6 до 16) и малым припуском на обработку: 0,1 – 0,4 мм на диаметр при черновом и 0,05 – 0,2 мм – при чистовом развертывании. Развертки различают: по конструкции хвостовика – с коническим и цилиндрическим хвостовиком; по способу крепления – хвостовые и насадные; по способу применения – машинные и ручные.
2.2.Порядок выполнения работы
1)Изучить конструкцию и назначение сверл, зенкеров, разверток.
26

2)Измерить конструктивные параметры спирального сверла: d, 2φ, φ1, ω, ψ, длину главных режущих кромок К и поперечной режущей кромки Кп.
3)Вычислить передний угол γ в нескольких точках главной режущей кромки К и построить график изменения переднего угла по ее длине.
4)В соответствии с заданием (см. табл. 2.1) выполнить эскизы технологических переходов при обработке отверстия с заданной точностью. Порядок обработки отверстий наиболее распространенных размеров (при длине отверстия не более пяти диаметров) указан в табл. 2.2, где С – сверление; РС – рассверливание; З – зенкерование; Р – развертывание.
2.3.Содержание отчета
1)Краткое описание конструкции и назначения сверл, зенкеров и развер-
ток.
2)Эскиз рабочей части спирального сверла с сечениями и видами, достаточными для обозначения всех линейных и угловых параметров, с расшифровкой обозначений и указанием материала режущей части и хвостовика.
3)Результаты измерений параметров спирального сверла, график изменения переднего угла γ сверла по длине главной режущей кромки К.
4)Эскизы технологических переходов обработки отверстия в соответствии с заданным вариантом (рис. 2.9).
а |
б |
в |
г |
д |
е |
а, б – обработка отверстия диаметром 12 мм по 12-му квалитету точности; в, г, д, е – обработка отверстия диаметром 35 мм по 9-му квалитету точности Рис. 2.9. Эскизы технологических переходов обработки отверстий
27
Т а б л и ц а 2.1
Исходные данные для выполнения индивидуального задания
Номер |
Номинальный |
Квалитет |
Номер |
Номинальный |
Квалитет |
|
варианта |
диаметр, мм |
точности |
варианта |
диаметр, мм |
точности |
|
1 |
12 |
8 |
16 |
26 |
9 |
|
30 |
11 |
55 |
9 |
|||
|
|
|||||
2 |
13 |
8 |
17 |
14 |
7 |
|
32 |
12 |
38 |
11 |
|||
|
|
|||||
3 |
14 |
9 |
18 |
28 |
11 |
|
34 |
10 |
55 |
10 |
|||
|
|
|||||
4 |
15 |
7 |
19 |
19 |
10 |
|
35 |
13 |
58 |
11 |
|||
|
|
|||||
5 |
16 |
9 |
20 |
60 |
7 |
|
36 |
8 |
20 |
11 |
|||
|
|
|||||
6 |
17 |
8 |
21 |
24 |
8 |
|
38 |
10 |
62 |
10 |
|||
|
|
|||||
7 |
18 |
11 |
22 |
15 |
7 |
|
40 |
7 |
70 |
11 |
|||
|
|
|||||
8 |
19 |
9 |
23 |
22 |
9 |
|
42 |
11 |
68 |
9 |
|||
|
|
|||||
9 |
20 |
10 |
24 |
16 |
11 |
|
44 |
10 |
72 |
8 |
|||
|
|
|||||
10 |
21 |
11 |
25 |
28 |
8 |
|
45 |
10 |
78 |
13 |
|||
|
|
|||||
11 |
22 |
8 |
26 |
32 |
13 |
|
46 |
11 |
80 |
8 |
|||
|
|
|||||
12 |
23 |
10 |
27 |
17 |
8 |
|
48 |
9 |
55 |
12 |
|||
|
|
|||||
13 |
24 |
7 |
28 |
46 |
12 |
|
50 |
12 |
65 |
9 |
|||
|
|
|||||
14 |
25 |
11 |
29 |
28 |
7 |
|
50 |
8 |
58 |
11 |
|||
|
|
|||||
15 |
19 |
11 |
30 |
30 |
12 |
|
60 |
7 |
16 |
10 |
|||
|
|
Т а б л и ц а 2.2 Рекомендуемый порядок обработки отверстий в сплошном материале
Диаметр |
|
Квалитет точности допуска диаметра |
|
||
отверстия, мм |
|
|
|
|
|
12, 13 |
11 |
9, 10 |
|
7, 8 |
|
|
|
|
|
|
|
До 10 |
С |
С |
С + Р |
|
С + Р + Р |
10 – 30 |
С |
С + З |
С + З + Р |
|
С + З + Р + Р |
30 – 80 |
С + РС |
С + РС + З |
С + РС + З + Р |
С + РС + З + Р + Р |
|
|
|
|
|
|
|
28
Диаметры инструментов на эскизах проставить, используя данные табл. 2.3. Предварительное сверление при изготовлении отверстий диаметром более 30 мм выполняется сверлом диаметром 20 мм.
Т а б л и ц а 2.3 Рекомендуемые диаметры промежуточных инструментов
для обработки отверстий в сплошном материале, мм
Номинальный |
|
Сверло |
|
Развертка |
||
диаметр |
|
|
|
Зенкер |
|
|
первое |
|
второе |
черновая |
чистовая |
||
отверстия, мм |
|
|
||||
|
|
|
|
|
|
|
|
|
|
|
|
|
|
1 |
2 |
|
3 |
4 |
5 |
6 |
|
|
|
|
|
|
|
12 |
10,7 |
|
– |
11,82 |
11,94 |
12 |
13 |
11,7 |
|
– |
12,82 |
12,94 |
13 |
14 |
12,7 |
|
– |
13,82 |
13,94 |
14 |
15 |
13,7 |
|
– |
14,82 |
14,94 |
15 |
16 |
14,25 |
|
– |
15,82 |
15,94 |
16 |
17 |
15,25 |
|
– |
16,82 |
16,94 |
17 |
18 |
16,25 |
|
– |
17,82 |
17,94 |
18 |
19 |
16,5 |
|
– |
18,82 |
18,93 |
19 |
20 |
17,5 |
|
– |
19,75 |
19,93 |
20 |
21 |
18,5 |
|
– |
20,75 |
20,93 |
21 |
22 |
19,5 |
|
– |
21,75 |
21,93 |
22 |
23 |
20,5 |
|
– |
22,75 |
22,93 |
23 |
24 |
21,5 |
|
– |
23,75 |
23,93 |
24 |
25 |
22,5 |
|
– |
24,75 |
24,93 |
25 |
26 |
23,5 |
|
– |
25,75 |
25,93 |
26 |
28 |
25,5 |
|
– |
27,75 |
27,93 |
28 |
30 |
20,0 |
|
27,5 |
29,75 |
29,93 |
30 |
32 |
20,0 |
|
29,0 |
31,71 |
31,92 |
32 |
34 |
20,0 |
|
31,0 |
33,71 |
33,92 |
34 |
35 |
20,0 |
|
32,0 |
34,71 |
34,92 |
35 |
36 |
20,0 |
|
33,0 |
35,71 |
35,92 |
36 |
38 |
20,0 |
|
35,0 |
37,71 |
37,92 |
38 |
40 |
20,0 |
|
37,0 |
39,71 |
39,92 |
40 |
42 |
20,0 |
|
39,0 |
41,72 |
41,92 |
42 |
44 |
20,0 |
|
41,5 |
43,71 |
43,92 |
44 |
45 |
20,0 |
|
42,0 |
44,71 |
44,92 |
45 |
|
|
|
|
|
|
|
29
Окончание табл. 2.3
1 |
2 |
3 |
4 |
5 |
6 |
|
|
|
|
|
|
46 |
20,0 |
42,8 |
45,71 |
45,92 |
46 |
50 |
20,0 |
46,0 |
49,71 |
49,92 |
50 |
48 |
20,0 |
45,0 |
47,71 |
47,92 |
48 |
52 |
20,0 |
48,0 |
51,65 |
51,91 |
52 |
55 |
20,0 |
51,0 |
54,65 |
54,91 |
55 |
58 |
20,0 |
54,0 |
57,65 |
57,91 |
58 |
62 |
20,0 |
58,0 |
61,65 |
61,91 |
62 |
65 |
20,0 |
61,0 |
64,65 |
64,91 |
65 |
68 |
20,0 |
63,0 |
67,65 |
67,91 |
68 |
70 |
20,0 |
65,0 |
69,65 |
69,91 |
70 |
72 |
20,0 |
68,0 |
71,65 |
71,91 |
72 |
75 |
20,0 |
71,0 |
74,65 |
74,91 |
75 |
78 |
20,0 |
72,0 |
77,65 |
77,91 |
78 |
80 |
20,0 |
75,0 |
79,65 |
79,91 |
80 |
|
|
|
|
|
|
2.4.Контрольные вопросы
1)Чем отличается конструкция и геометрия режущей части спирального сверла от конструкции и геометрии режущей части расточного резца?
2)Сопряжением каких поверхностей образуется поперечная режущая кромка на режущей части сверла?
3)С какой целью калибрующую (направляющую) часть осевого инструмента изготавливают с обратной конусностью?
4)Сколько и каких режущих кромок имеет спиральное сверло?
5)Какое влияние на процесс резания оказывает поперечная кромка сверла?
6)Какой из описанных выше инструментов обеспечивает наилучшие показатели качества поверхности? Чем это объясняется?
30