
ТКМ Часть 1 (2)
.pdfдлиной l1 – наибольшим расстоянием от вершины резца 4 до границы ослабления державки 2 гнездом под режущую пластину 3;
размерами режущей пластины 3 – толщиной s, длиной l и шириной b. Резание осуществляется лезвием рабочей части резца, которое образуется
врезультате пересечения двух сопрягающихся поверхностей:
передней А – поверхности лезвия, контактирующей в процессе резания со срезаемым слоем и стружкой (по данной поверхности сходит стружка);
главной задней А – поверхности лезвия, контактирующей с поверхностью резания R на обрабатываемой заготовке.
Вспомогательной задней поверхностью головки резца называется поверхность лезвия, контактирующая с обработанной поверхностью заготовки.
Сопрягаясь, передняя А и задняя А поверхности лезвия образуют: главную режущую кромку К, формирующую большую сторону сечения
срезаемого слоя (срезает с заготовки основную часть припуска); вспомогательную режущую кромку К1, формирующую меньшую сторону
сечения срезаемого слоя (зачищает остаточные гребешки на обработанной поверхности, оставленные главной режущей кромкой К).
Острота главной режущей кромки К характеризуется радиусом округления , который изменяется от одного до нескольких десятков микрометров и зависит от свойств инструментального материала и качества заточки и доводки лезвия, по мере изнашивания которого увеличивается.
Пересечение режущих кромок К и К1 образует вершину резца 4 (см. рис. 1.5), где rв – радиус скругления при вершине резца.
1.1.4. Геометрические параметры резца (ГОСТ 25762-83)
Положение элементов рабочей части резца в пространстве определяется системой угловых размеров, которые называются геометрическими параметрами и могут быть измерены в статической, кинематической и инструментальной прямоугольных системах координат.
Статическая система координат имеет начало в рассматриваемой точке k на режущей кромке и ориентирована относительно направления скорости главного движения резания V (см. рис. 1.4 и 1.6).
11

Кинематическая система координат ориентирована относительно направления результирующей скорости резания Vе.
Инструментальная система координат ориентирована относительно элементов режущего инструмента, принятых за базу. Для токарных резцов такими элементами являются продольная и поперечная оси, опорная поверхность.
В качестве исходных баз для измерения углов в статической и кинематической системах координат используются следующие координатные плоскости, следы которых показаны на рис. 1.6 и 1.7:
основная плоскость Рv – проведенная через рассматриваемую точку k на режущей кромке перпендикулярно вектору скорости главного движения резания V в статической системе координат (Рvс) или перпендикулярно направлению результирующей скорости резания Vе в кинематической системе (Рvк);
главная Рn и вспомогательная плоскости резания, касательные к по-
верхности резания в рассматриваемых точках k и k1 на главной и вспомогательной режущих кромках, соответственно, и перпендикулярные к основной плоскости Рv (см. рис. 1.7). В статической плоскости резания Рnc расположен вектор скорости главного движения резания V, проходящий через точку k, а в кинематической Рnк – вектор результирующей скорости резания Ve;
η Рnc
Ve V
n, об/мин |
|
|
|
|
Рvк |
|
|
Рvс |
Рvс |
η |
|
γк |
|||
|
|
||
Рvк |
|
γс |
|
|
αс |
|
|
|
αк |
|
|
Рnc |
Рnк |
|
Рис. 1.6. Системы координат и координатные плоскости при точении канавки, отрезании и подрезании торца (в проекции на рабочую плоскость Рs)
12

рабочая плоскость Рs – проведенная через рассматриваемую точку k, в которой расположены направления скоростей главного движения резания V и движения подачи Vs, перпендикулярно основной плоскости Рv и параллельно вектору подачи S (см. рис. 1.7).
Поскольку углы, определяющие положение поверхностей лезвия в пространстве, являются двугранными, они измеряются в разрезах рабочей части резца секущими плоскостями, проведенными перпендикулярно к ребру угла, которым является режущая кромка. Главная секущая плоскость Р проводится перпендикулярно линии пересечения основной плоскости Рv и главной плоскости резания Рn в рассматриваемой точке k главной режущей кромки. Аналогично проводится вспомогательная секущая плоскость через рассматриваемую точку k1 на вспомогательной режущей кромке (см. рис. 1.7).
λ
γ1 |
δ1 |
α1 |
β1
α
β γ
δ
k
k1
φ |
φ1 |
ε
Рис. 1.7. Координатные плоскости и геометрические параметры лезвия прямого проходного правого резца в статической системе координат при точении цилиндрической заготовки
13
В главной секущей плоскости P измеряют:
главный задний угол – двугранный угол между главной задней поверхностью лезвия А (или касательной к ней) и главной плоскостью резания Рn;
главный передний угол – двугранный угол между передней поверхностью лезвия А (или касательной к ней) и основной плоскостью Рv; если передняя поверхность А располагается выше основной плоскости Рv, то угол отрицателен (иногда на передней поверхности делают фаску f размерами от 0,1 до 1,0 мм с отрицательным передним углом).
главный угол заострения – двугранный угол между передней А и главной задней А поверхностями лезвия (или касательными к ним, если эти поверхности криволинейны);
угол резания – двугранный угол между передней поверхностью А лезвия и главной плоскостью резания Рn, причем = + .
Аналогичным образом измеряются углы 1, 1, 1, 1 во вспомогательной секущей плоскости (см. рис. 1.7).
В основной плоскости Рv измеряют:
главный угол в плане – угол между главной плоскостью резания Рn и рабочей плоскостью Рs, проведенными через точку k на режущей кромке;
вспомогательный угол в плане 1 – угол между вспомогательной плоскостью резания и рабочей плоскостью Рs, проведенными через точку k1;
угол в плане при вершине резца – угол между главной К и вспомогательной К1 режущими кромками.
В главной плоскости резания Рn измеряется угол наклона главной режущей кромки – угол между главной режущей кромкой К и основной плоскостью Рv. Угол считается положительным, если все точки главной режущей кромки располагаются выше вершины резца. Для угла 1 условия определения знаков изменяются на противоположные.
Между углами, измеряемыми в основной плоскости, существуют следующие зависимости:
+ + 90 ; |
(1.1) |
= 90 – ( + ); |
(1.2) |
14 |
|
+ + 1 = 180 . |
(1.3) |
В кинематической системе координат углы резца могут быть определены при известных статических углах по следующим формулам (см. рис. 1.6):
к = c – ; |
(1.4) |
к = c + , |
(1.5) |
где – угол скорости резания между направлениями скорости главного движения резания V и результирующей скорости резания Vе,
= arctg(Sо/D), |
(1.6) |
где Sо – подача на оборот заготовки, мм/об;
D – диаметр обрабатываемой поверхности.
К геометрическим параметрам срезаемого слоя металла относятся толщина срезаемого слоя a и ширина срезаемого слоя b (см. рис. 1.7).
Воспроизвести заданные на чертеже углы, измеряемые в нормальных сечениях, на заточных станках невозможно. Заточные станки позволяют выставить углы только в продольном и поперечном сечениях резца, перпендикулярных к основной (опорной, проходящей через подошву резца) плоскости. Углы в этих сечениях связаны между собой соотношениями:
tgпр = tg cos tg sin ; |
(1.7) |
tgп = tg sin tg cos ; |
(1.8) |
tgпр = tg /cos ; |
(1.9) |
tgп = tg /sin . |
(1.10) |
В формулах (1.7) и (1.8) верхние знаки применяют для положительных значений , нижние – для отрицательных.
На угловые параметры резца влияет погрешность его установки на станке. Выдержать указанные на чертеже углы возможно, если вершину резца установить строго по высоте и перпендикулярно линии центров станка (по оси вращения заготовки). Если известна погрешность установки резца h относительно высоты центров станка, то фактические углы α и γ определяют по формулам:
15
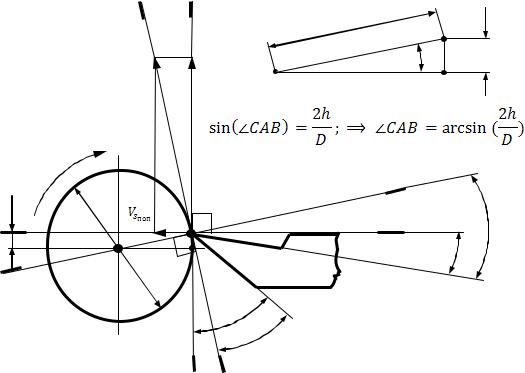
ф = с arcsin(2h/D); |
(1.11) |
ф = с arcsin(2h/D). |
(1.12) |
Знаки «+» или «–» определяют по расчетной схеме.
Расчетная схема определения фактических углов резца с учетом погрешности его установки на станке приведена на рис. 1.8.
Угловые параметры резца изменяются в результате образования нароста на передней поверхности, при износе поверхностей и режущих кромок лезвия в процессе резания.
|
Рnф |
|
Рnc |
0,5D |
С |
|
|
|
|
|
|
|
|
Ve |
V |
|
+h |
|
|
А |
|
||
|
|
|
|
В |
|
|
|
|
|
|
|
n, об/мин |
|
|
|
Рvф |
|
|
|
|
|
|
|
Рvс |
|
С |
|
Рvс |
γф |
|
|
|
|
||
+h |
А |
D |
В |
|
γс |
|
|
|
|||
|
|
|
|
|
|
Рvф |
|
|
αс |
|
|
|
|
|
|
|
|
|
|
|
|
αф |
|
|
|
Рnc |
Рnф |
|
|
Рис. 1.8. Расчетная схема определения фактических углов резца с учетом по- |
|||||
грешности его установки на станке (+h) по высоте центров |
|
1.1.5. Влияние геометрических параметров резца на процесс резания
Задний угол α резца обеспечивает уменьшение трения главной задней поверхности лезвия о главную поверхность резания. Оптимальное значение заднего угла α при обработке стали для черновых резцов (S > 0,3 мм/об) составляет 8 , для чистовых (S > 0,3 мм/об) – 12. Увеличение α сверх оптимального значения незначительно уменьшает трение между задней поверхностью резца и
16
поверхностью резания детали, однако за счет уменьшения угла заострения снижается прочность лезвия и ухудшаются условия теплоотвода в резец.
Передний угол γ резца в основном предназначен для уменьшения деформации стружки и обработанной поверхности, от его величины зависят значение и направление силы резания, температура, интенсивность вибрации и, следовательно, прочность и износостойкость лезвия. Увеличение угла улучшает условия стружкообразования, однако уменьшает угол заострения , что снижает прочность и износостойкость лезвия. Для обработки прочных сталей твердосплавными резцами на передней поверхности затачивается фаска шириной (0,3
– 0,5)So мм с передним углом по фаске ф, равным от –3 до –10. Для обработки мягких сталей угол равен 20 – 30 , сталей средней твердости = 12 – 15 , чугуна = 5 – 15. Чем прочнее обрабатываемый материал, тем меньше угол .
Главный угол в плане φ. С увеличением угла φ для заданных значений подачи S и глубины резания t увеличивается толщина срезаемого слоя a = Ssin и, соответственно, сила сопротивления подаче Рx, однако при этом уменьшается ширина срезаемого слоя b = t/sin и, соответственно, радиальная сила Рy, вызывающая изгиб заготовки, и увеличивается шероховатость. Для черновой обработки жестких заготовок (при l 3D) угол равен 45 – 60, для обработки нежестких деталей = 90. Чистовые резцы имеют угол , равный 0 – 3 .
Вспомогательный угол в плане 1 предусматривается для уменьшения трения вспомогательной режущей кромки об обработанную поверхность и составляет от 2 до 30 . Для чистовых резцов угол 1 равен 1 – 2. С увеличением радиуса rв при вершине резца уменьшаются углы и 1.
Угол наклона главной режущей кромки определяет направление схода стружки по передней поверхности лезвия резца. При черновой обработке положительный угол повышает прочность лезвия и отклоняет стружку в сторону обработанной поверхности, что недопустимо при чистовой обработке, так как стружка царапает предварительно обработанную поверхность и снижает ее качество. Поэтому для чистовых резцов угол имеет отрицательное значение, при котором сход стружки происходит в сторону обрабатываемой поверхности.
Образующаяся при обработке большинства сталей сливная стружка сходит в виде длинных полос или спирали и наматывается на механизмы станка, инструмент и заготовку. Это затрудняет эксплуатацию станка, может вызвать
17
травму рабочего, повреждение обработанной поверхности, поэтому для получения устойчивого стружкодробления на передней поверхности резца затачивают специальные канавки и уступы вдоль главной режущей кромки.
1.2.Порядок выполнения работы и содержание отчета
1)В соответствии с заданием, выданным преподавателем, выполнить эскиз резца с обозначением элементов конструкции и размеров: H, B, L, E, h, l1, l2, s, l (см. рис. 1.4), дать им определения, указать назначение резца и материал режущей части с его краткой характеристикой.
2)Привести схему обработки детали соответствующим резцом с указанием направлений главного движения и движения подачи, поверхностей обработки. В соответствии с заданием указать на схеме значение подачи Sо, глубины резания t, размеров поверхностей D1 и D2, толщины а и ширины b срезаемого слоя. Дать им определения.
3)На схеме изобразить проекции координатных плоскостей Pv, Pn, , P ,
, Ps в статической системе координат и дать им определения. Построить разрезы рабочей части резца в главной и вспомогательной секущих плоскостях. Обозначить геометрические параметры резца и дать им определения, руководствуясь примером, приведенным на рис. 1.7.
4) Ознакомиться с конструкцией угломеров и методикой измерения углов резца. Замерить углы и в главной секущей плоскости, используя вертикальную шкалу угломера, которая при измерении устанавливается перпендикулярно главной режущей кромке резца (следу главной плоскости резания Pn). Замерить углы и 1 в основной плоскости, используя горизонтальную шкалу угломера. Резец при измерении прижимается боковой поверхностью державки к направляющей планке. Замерить угол наклона главной режущей кромки, используя вертикальную шкалу с указателем, имеющим измерительную плоскую поверхность. Остальные угловые параметры определить по формулам (1.1) – (1.3).
5) В соответствии с исходными данными задания построить расчетные схемы, аналогичные схемам, приведенным на рис. 1.6 и 1.8. Определить значения кинематических углов к и γк по формулам (1.4) и (1.5), главных углов пр,п, γпр и γп в продольном и поперечном сечениях по формулам (1.7) – (1.10),
18
фактических углов ф и γф при заданной погрешности установки h по формулам (1.11) и (1.12). По результатам расчетов сделать выводы о влиянии кинематики резания и погрешности установки на значения фактических углов.
1.3.Контрольные вопросы
1)По каким признакам определяют положение передней и задней поверхностей лезвия резца и его режущих кромок?
2)Как классифицируются токарные резцы по видам выполняемых работ?
3)Как и в какой координатной плоскости измеряются передний и задний углы резца, углы в плане и угол наклона режущей кромки?
4)Почему с увеличением скорости движения подачи уменьшается фактическое значение главного заднего угла?
5)С какой целью производят заточку лезвия резца по передней и задней поверхностям?
Лабораторная работа 2
ОСЕВОЙ РЕЖУЩИЙ ИНСТРУМЕНТ ДЛЯ ОБРАБОТКИ ОТВЕРСТИЙ
Ц е л ь р а б о т ы : ознакомиться с классификацией, конструкцией и назначением основных типов осевого инструмента, получить навыки в измерении их конструктивных параметров и выборе варианта технологического процесса обработки отверстия.
2.1. Краткие теоретические сведения
2.1.1. Сверла
Сверла предназначены для получения отверстий в сплошном материале, рассверливания просверленных отверстий и надсверливания углублений, они обеспечивают получение поверхности 11-го и 12-го квалитетов точности и значения ее шероховатости Rz от 20 до 80 мкм.
Различают следующие типы сверл (рис. 2.1):
19
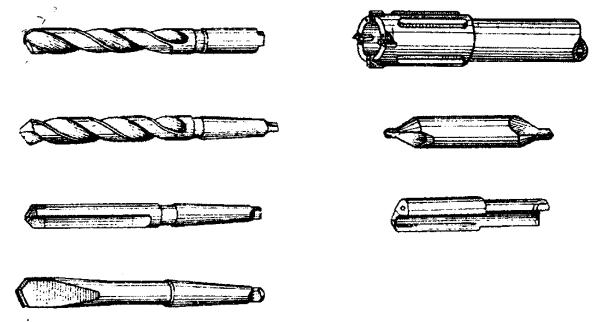
спиральные (или винтовые) цельные, составные с твердосплавными режущими пластинами с прямыми, наклонными и винтовыми стружечными канавками (см. рис. 2.1, а, б, в), являются самыми распространенными;
перовые или плоские (см. рис. 2.1, г), являются простыми по конструкции, жесткими и в основном используются для обработки дерева, пластмасс и мягких цветных металлов и сплавов;
кольцевые (рис. 2.1, д) для сверления отверстий диаметром более 80 мм;
центровочные (см. рис. 2.1, е) для получения центровых отверстий;
для глубокого сверления (пушечные, ружейные, шнековые и др.) (см.
рис. 2.1, ж).
а |
д |
б |
е |
в |
ж |
г
Рис. 2.1. Типы сверл
Спиральное сверло (рис. 2.2) состоит из рабочей части, включающей режущую и направляющую части, шейки и хвостовика с лапкой. Хвостовики сверл малого диаметра изготавливаются цилиндрическими. Лапка у сверл с коническим хвостовиком (конус Морзе) предназначена для извлечения его из отверстия шпинделя и предотвращения проворота сверла. Шейка служит для выхода шлифовального круга при шлифовании ленточек сверла.
20