
МУ-РГР-Детали машин
.pdf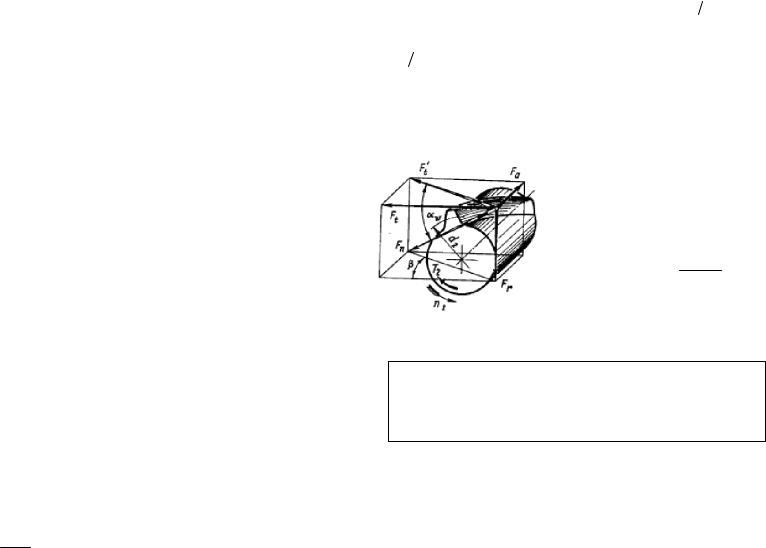
лах β = 8 ... 20°. Если при расчетах угол наклона зуба выходит за пределы указанного диапазона, то необходимо изменить значение модуля и заново произвестирасчет по формулам (16) – (18).
Определение чисел зубьев колеса и шестерни
Число зубьев шестерни рассчитывается по формуле:
z |
= |
zs |
|
≥ z |
min |
. |
( 19 ) |
|
|||||||
1 |
|
u +1 |
|
|
|
||
|
|
|
|
|
|
Значение z1 округляют в ближайшую сторону до целого. Полученное число зубьев должно быть больше допускаемого минимального количества зубьев:
-дляпрямозубых колес zmin = 17;
-длякосозубых ишевронныхколес zmin = 17cos3β . Число зубьев колеса определяется по формуле:
z2 = zs − z1 . |
( 20 ) |
Определение фактического передаточного числа
Фактическое передаточное число определяется исходя из фактических чисел зубьев колеса и шестерни:
|
z2 |
|
|
u = |
|
. |
( 21 ) |
z |
|||
1 |
|
|
Найденное фактическое передаточное число обязательно проверяется на отклонение от заданного (исходного u):
∆u = |
uф − u |
100 |
≤ 4% . |
( 22 ) |
|
u |
|||||
|
|
|
Если отклонение превышает 4 %, необходимо изменить число зубьев ведомого колеса или модуль передачи и повторить проверку.
3.Расчет геометрических параметров зубчатых колес
Делительные диаметры зубчатых колес определяются по формуле (точностьвычислениядовторогознакапослезапятой):
mz |
(мм), |
( 23 ) |
d = cos β |
где z – число зубьев соответствующего колеса.
Диаметрокружностивершинзубьев: dа = d + 2m мм. ( 24 ) Диаметрыокружностейвпадинзубьев: df = d – 2,5m мм.
21
Шестерня должна выполняется несколько большей ширины, чем ко-
лесо. Ширину шестерни b1 принимают из соотношения b1 |
b2 (табл. 3): |
|||
|
|
|
|
Таблица3 |
Приb2 мм |
до 30 |
св. 30 до 50 |
св. 50 до 80 |
св. 80 до 100 |
b1 b2 |
1,1 |
1,08 |
1,06 |
1,05 |
Этап 2. Выполнение проверочного расчета
1. Определение сил в зацеплении
Действующую под нагрузкой в зацеплении силу раскладывают на три составляющие силы (рис. 2):
|
2T 103 |
|
– окружная F = |
2 |
, Н, ( 25 ) |
|
||
t |
d2 |
|
|
|
– радиальная Fr = Ft tgα , Н , ( 26 ) cos β
– осевая Fa = Ft tgβ , Н. ( 27 )
Рис. 2. Силы в зацеплении косозубых колес
ПРИМЕР.
Для рассматриваемой передачи:
-окружная сила Ft = 2 103 339,1/234,32 = 2898,6 Н;
-радиальная сила Fr = 2898,6 tg20°/cos9,1° = 1068,3 Н;
-осевая сила Fa = 2898,6 tg9,1° = 462,7 Н.
2. Проверка зубьев колес по напряжениям изгиба
Расчетное напряжение изгиба σF в зубьях колеса (σF2) определяется по формуле:
σF 2 = |
K Fα K Fβ K FvYβYFS 2 Ft |
, Н/мм2 |
( 28 ) |
|
b2m |
||||
|
|
|
где KFα − коэффициент, учитывающий влияние погрешностей изготовления шестерни и колеса. Для колес нормальной точности (7-я степень точности по ГОСТ 1643-81) значения коэффициента принимают:
- для прямозубых KFα = 1,0,
22
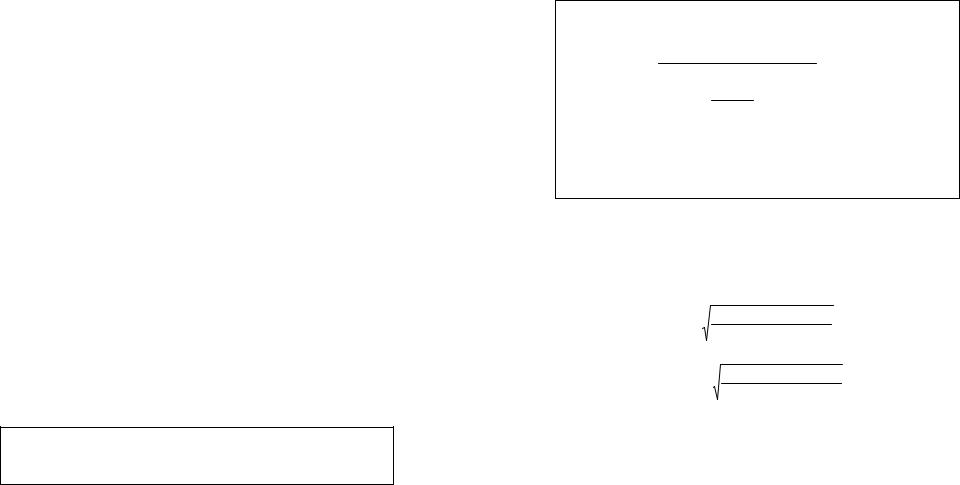
- для косозубых KFα = 0,81;
KFβ − коэффициент, учитывающий неравномерность распределения нагрузки по длине контактной линии. При вариантах термообработки I и II (см. приложение 13) и окружной скорости колеса v < 15 м/с зубья колес полностью прирабатываются, поэтому коэффици-
ент KFβ = 1,0;
KFv − коэффициент, учитывающий внутреннюю динамическую нагрузку и зависящий от степени точности, окружной скорости и твердости поверхности зубьев колеса. При вариантах термообработки I и II (см. приложение 13), окружной скорости колеса v < 15 м/с и нормальной точности исполнения коэффициент принимают:
-для прямозубых KFv = 1,4,
-для косозубых KFv = 1,2;
Yβ − коэффициент, учитывающий наклон зуба колеса. Определяется по формуле:
Yβ =1− |
|
β |
; |
( 29 ) |
|
100 |
|||||
|
|
YFS − коэффициент, учитывающий форму зуба и концентрацию напряжений, в зависимости от числа зубьев z. Для косозубых колес – в зависимости от эквивалентного числа зубьев zv = z ⁄ cos3β. Рекомендуемые значения приведены в табл. 4.
Таблица 4
|
z илиzv |
17 |
20 |
25 |
30 |
40 |
50 |
60 |
80 |
|
|
YFS |
4,28 |
4,09 |
3,90 |
3,80 |
3,70 |
3,66 |
3,62 |
3,60 |
|
|
|
|
|
|
|
|
|
|
|
|
|
|
|
|
|
|
|
|
|
|
|
ПРИМЕР.
Для рассматриваемой передачи при z1 = 26 и z2 = 132 значения коэффициентов – для шестерни YFS1 = 3,9, а для колеса YFS2 = 3,6.
Расчетное напряжение изгиба в зубьях шестерни определяется по формуле:
σ |
F1 |
= σF 2YFS1 |
, Н/мм2 . |
( 30 ) |
|
YFS 2 |
|
|
|
|
|
|
|
Расчетные значения напряжений могут отклоняться от допускаемых:
σF ≤1,1[σ]F . |
( 31 ) |
23
ПРИМЕР.
Для рассматриваемой передачи расчетные напряжения изгиба в зубьях колеса будут равны:
σF 2 = 0,81 1,0 1,2 0,912 3,6 2898,6 = 94,1 Н/мм2 . 56 1,75
В зубьях шестерни: σF1 = 94,1 3,9 = 102,0 Н/мм2 .
3,6
Проверка по допустимым изгибным напряжениям:
σF1= 102,0 Н/мм2 < [σ]F = 255 Н/мм2 ,
σF2= 94,1 Н/мм2 < [σ]F = 255 Н/мм2 .
Следовательно, зубья шестерни и колеса выдержат изгибные нагрузки, предусмотренные для данной передачи.
3. Проверка зубьев по контактным напряжениям
Расчетное контактное напряжение в зацеплении определяется по формуле:
•для прямозубых колес
уH = 436 |
K Hб K Hв K Hv Ft (uф +1) |
2 |
( 32 ) |
d2b2 |
, Н/мм , |
||
|
|
|
•для косозубых колес
уH = 376 |
K Hб K Hв K Hv Ft (uф +1) |
2 |
( 33 ) |
d2b2 |
, Н/мм , |
||
|
|
|
где KHα − коэффициент, учитывающий распределение нагрузки между зубьями, принимают:
-для прямозубых колес KHα = 1,0 ,
-для косозубых колес KHα = 1,1 ;
KHβ – коэффициент неравномерности распределения нагрузки по длине контактной линии KHβ = 1,0;
KHv – коэффициент, учитывающий внутреннюю динамику нагружения, принимают при твердости зубьев менее 350 НВ:
-для прямозубых колес KHv = 1,2 ,
- для косозубых колес KHv = 1,1.
Полученное расчетное контактное напряжение должно находиться в
интервале: |
|
σН = (0,85 ... 1,05)[σ]Н |
( 34 ) |
При несоблюдении этого условия изменяют b2 и производят перерасчет b1 , а затем повторяют проверку по формуле (34).
24
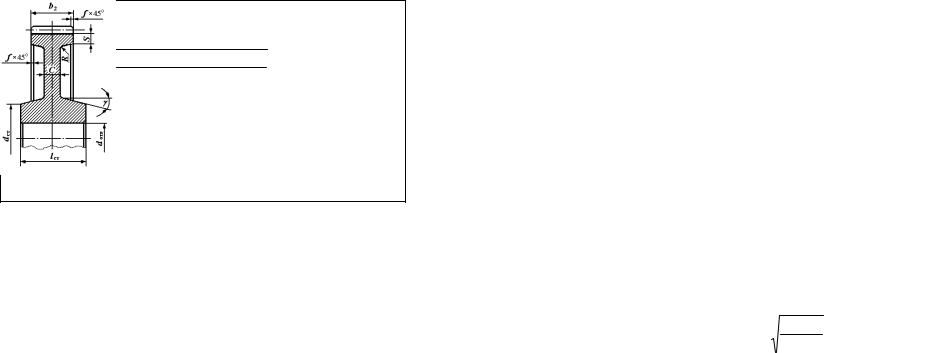
ПРИМЕР.
Для рассматриваемой передачи расчетные контактные напряжения в зацеплении будут равны:
σ Н = 376 |
1,1 1,0 1,1 2898,6 (5,29 +1) = 479,6 Н/мм2 . |
|
234,32 56 |
Проверка нахождения напряжений в допускаемом диапазоне:
σ H |
= |
479,6 = 0,93 , |
[σ] |
513 |
|
H |
|
|
0,85[σ]Н < (σН = 479,6) < 1,05[σ]Н .
Следовательно, напряжения, возникающие в передаче при заданной нагрузке, обеспечивают ее работоспособность.
Результаты расчетов сводятся в итоговую таблицу (табл. 5).
|
|
|
|
|
|
|
Таблица 5 |
|
Сводные данные расчета параметров зубчатой передачи |
||||||
|
(пример заполнения итоговой таблицы) |
|
|||||
№ |
Обозначение |
Значение |
|
№ |
Обозначение |
Значение |
|
параметра |
параметра |
|
параметра |
параметра |
|||
1 |
aw , (мм) |
140,0 |
|
12 |
da1 |
, (мм) |
49,58 |
2 |
b1 , (мм) |
59 |
|
13 |
da2 |
, (мм) |
237,42 |
3 |
b2 , (мм) |
56 |
|
14 |
df1 |
, (мм) |
41,7 |
4 |
m , (мм) |
1,75 |
|
15 |
df2 |
, (мм) |
229,55 |
5 |
β , (град) |
9,1° |
|
16 |
Ft , (Н) |
2898,8 |
|
6 |
z1 |
26 |
|
17 |
Fr , (Н) |
1068,4 |
|
7 |
z2 |
132 |
|
18 |
Fa , (Н) |
462,7 |
|
8 |
uф |
5,08 |
|
19 |
σF1 , (Н/мм2) |
102,0 |
|
9 |
∆ |
– 4,0 |
|
20 |
σF ⁄[σ]F |
0,4 |
|
|
u , % |
|
|
|
|
||
10 |
d1 , (мм) |
46,08 |
|
21 |
σН , (Н/мм2) |
479,6 |
|
11 |
d2 , (мм) |
233,92 |
|
22 |
σН ⁄[σ]Н |
0,93 |
25
Этап 3. Разработка конструкции зубчатого колеса
Конструкцию зубчатого колеса выбирают в зависимости от его размеров и способа получения заготовки [2, с. 261 … 262]. Наиболее целесообразный способ получения заготовок зубчатых
колес диаметром более 200 мм – |
|
|||
штамповка. |
После |
механической |
|
|
обработки такое колесо имеет соот- |
|
|||
ветствующую форму (рис. 3). |
|
|||
Диаметр |
посадочного |
отверстия |
|
|
колеса dотв равен диаметру вала в |
|
|||
месте установки колеса. Поэтому |
|
|||
необходимо знать диаметр той сту- |
|
|||
пени вала редуктора dвала, на которой |
|
|||
устанавливается данное |
зубчатое |
|
||
колесо. Диаметр вала определяется |
|
|||
прочностными характеристиками его |
|
|||
материала, |
зависит |
от |
величины |
Рис. 3. Форма зубчатого |
вращающего момента, |
передаваемо- |
колеса |
||
го от колеса на вал, и рассчитывает- |
|
ся по формуле [1, с. 312]: |
|
|
|
dвала =103 |
Мк |
, мм, |
( 35 ) |
|
0,2[τ]к |
|
где Мк – крутящий момент (Нм) на валу, в данном случае равный вращающему моменту на колесе, т.е. Мк = Т2.
[τ]к – допускаемое напряжение на кручение для участка вала в месте установки зубчатого колеса. Для валов из конструкционной стали марки 45 (наиболее характерной для валов редукторов общего назначения) принимают [1, с. 312]:
•для концевых участков валов [τ]к = 20 … 28 Н/мм2;
•для диаметров в месте посадки колес [τ]к = 14…20 Н/мм2.
Полученное значение диаметра вала округляют до стандартного из
ряда R40 (см. приложение 4) ) и принимают: dотв = dвала. Диаметр ступицы зубчатого колеса принимают равным:
dст = (1,5 … 1,7)dотв , мм. |
( 36 ) |
Длину ступицы на предварительном этапе проектирования принимают равной:
lст = b2 , мм.
26
Для уменьшения массы и экономии металла зубчатые колеса делают с более тонким диском. Рекомендуется C = 0,3b2 .
Следует обратить внимание, что любая штампованная заготовка в соответствующих местах имеет штамповочные уклоны под углом γ ≥ 7° и с радиусом сопряжения R ≥ 6 мм, которые остаются на детали в местах, не подвергаемых механической обработке.
На торцах зубчатого венца, торцах ступицы и углах обода выполняют фаски f = 2×45°.
Ширину торцов зубчатого венца S принимают равной: |
|
S = 2,25m + 0,05b2 , мм. |
(37) |
Расчетные размеры dст , lст , C и S необходимо округлить до целого числа.
На чертеже зубчатого колеса обязательно должны быть указаны все его размеры и приведена таблица с параметрами зацепления. Пример оформления чертежа см. приложение 10.
Следует обратить внимание, что размер посадочного отверстия зубчатого колеса определялся исходя из диаметра сопряженной ступени вала. Следовательно, окончательный диметр посадочного отверстия будет определяться после расчета размеров той ступени вала, на которой предполагается устанавливать данное колесо.
27
Расчетно-графическая работа № 3
Проектный и проверочный расчеты вала редуктора. Расчет шпоночных соединений
Вал в редукторе предназначен для передачи вращающего момента вдоль своей оси, для поддержания расположенных на нем деталей и восприятия действующих на них сил. При работе вал испытывает, как правило, изгиб и кручение. Поэтому при определении геометрических размеров вала учитывают прочностные характеристики материала вала и допускаемые им напряжения.
Исходные данные для расчета вала:
схема расположения зубчатых колес относительно опор в редукторе;
наружный диаметр ведомогозубчатого колеса da2 , мм; ширина обода ведомогозубчатого колеса b2 , мм; уголнаклоназубьевколесаβ, град;
вращающий моментнаколесеT2 , Нм; частотавращенияколесап2., мин–1 .
Исходные данные для расчета вала были получены при выполнении РГР № 1 и РГР № 2. Схема расположения зубчатых колес относительно опор в редукторе представлена на кинематической схеме индивидуального заданиякрасчетно-графическимработам.
Требуется произвести проектный расчет вала второй ступени редуктора:
рассчитатьдиаметрвыходногоконцавала; определитьколичествоступенейвала, ихдлиныидиаметры;
уточнить размеры посадочного диаметра зубчатого колеса и диаметраступицы; определитьразмерыдискаиободазубчатогоколеса;
подобрать подшипники, обеспечивающие работоспособность передачи; выполнитьчертежвторойступениредуктора.
Расчет конструктивных параметров вала проводится поэтапно: Этап 1. Выбор материала для изготовления вала.
Этап 2. Определение необходимого количества ступеней вала и их назначения.
Этап 3. Определение диаметров каждой ступени вала. Этап 4. Определение длины каждой ступени вала.
28
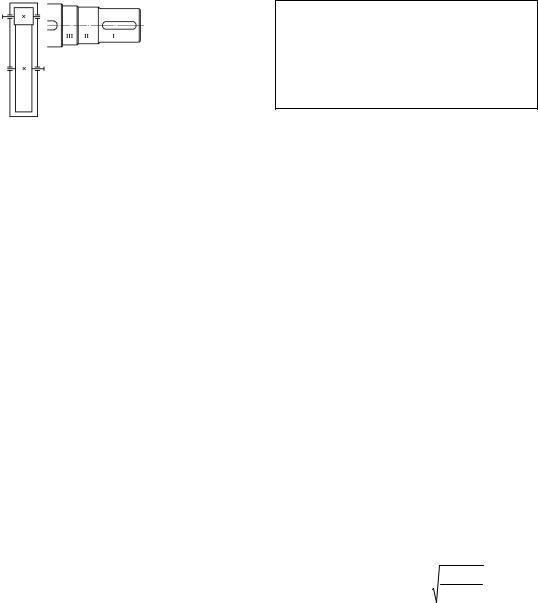
Этап 5. Разработка конструкции вала второй ступени редуктора с установленными на нем элементами.
Этап 1. Выбор материала для изготовления вала
Материалы валов и осей должны хорошо обрабатываться, быть прочными и иметь высокий модуль упругости.
Этим требованиям наиболее полно удовлетворяют углеродистые и легированные стали, из которых преимущественно изготавливают валы и оси. Для валов и осей с упрочняющей термообработкой применяют стали 45, 40Х.
Для изготовления валов редукторов общего назначения целесообразно выбрать сталь 45.
Этап 2. Определение необходимого количества ступеней вала и их назначения
Исходя из кинематической схемы (см. чертеж редуктора в индивидуальном задании на РГР) и знаний об условиях расположения деталей на валах составляют схему расположения элементов на валу.
Анализ кинематической схемы данного редуктора (рис.4) показывает, что ведомый вал должен иметь ступенчатую форму. На одной ступени располагается зубчатое колесо, две ступени предназначаются
для установки подшипников, еще одна ступень (вы- |
|
ходной конец вала) предназначена для присоедине- |
|
ния следующей передачи или вала рабочей маши- |
|
ны. Кроме этого необходимо предусмотреть фикса- |
|
цию зубчатого колеса в осевом направлении и уп- |
|
лотнительное устройство для защиты подшипника |
|
со стороны выходного конца вала. |
|
Рекомендуется для удобства перед проектиро- |
|
ванием вала вычертить его эскиз, пронумеровать |
Рис. 4. Схема |
все ступени римскими цифрами, начиная с выход- |
|
ного конца вала, и дать подробное описание их на- |
редуктора |
значения. |
|
Ведомый вал рассматриваемого в примере редуктора (рис. 5) ступенчатый и имеет шесть ступеней следующего назначения (см. прототип редуктора в индивидуальном задании к РГР):
29
ПРИМЕР.
Рис.5. Эскиз ведомого вала редуктора
•ступень I – выходной конец вала, предназначенный для присоединения других элементов привода, необходимых для передачи вращающего момента исполнительному органу соответствующей машины (в данном примере на ступени I установлена упругая втулоч- но-пальцевая муфта);
•ступень II – предназначена для установки манжетного уплотнения;
•ступень III – опорная часть вала, предназначенная для установки подшипника;
•ступень IV – предназначена для установки зубчатого колеса;
•ступень V – буртик, который обеспечивает заданное осевое положение зубчатого колеса на валу относительно опор;
•ступень VI – опорная часть вала, предназначенная для установки второго подшипника.
Этап 3. Определение диаметров каждой ступени вала
Размеры диаметров ступенчатого вала зависят от вида установленных на этот вал деталей и во многом определяются последовательностью их установки. Определение диаметров ступеней вала начинают с выходного конца вала, постепенно переходя к последующим ступеням.
1. Определение диаметра I-й ступени
Диаметр выходного конца ведомого вала является основной характеристикой редуктора, так как эта часть обеспечивает требуемый вращающий момент и полезную мощность редуктора. Диаметр выходного конца ведомого вала предварительно определяется расчетным путем по формуле (35), уже используемой ранее:
|
М |
d ≥103 |
0,2[τк]к . |
30
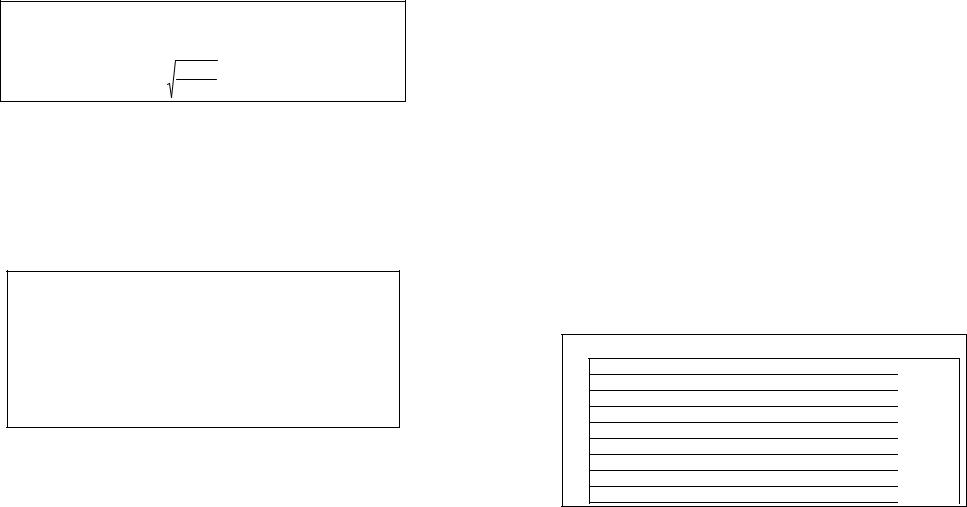
Следует обратить внимание, что при расчете выходного конца вала, имеющего меньший диаметр, чем остальные ступени вала, допускаемое напряжение на кручение принимается большим, чем при расчете других диаметров вала.
ПРИМЕР.
При Т2 = 339,1 Н м и допускаемом напряжении на кручение для стали 45 после улучшения [τ]к = 25 Н/мм2 :
d =103 339,1 = 40,8 мм. 0,2 25
Следует обратить внимание, что для окончательного определения диаметра выходного конца вала необходимо рассмотреть конструктивный элемент, который в этом месте установлен (см. индивидуальное задание к РГР), так как различные элементы могут иметь определенные стандартами конструктивные ограничения. Это в первую очередь относится к упругим муфтам, которые в зависимости от передаваемого вращающего момента имеют вполне определенные геометрические параметры [2, с. 346 … 348]. В этом случае диаметр выходного конца вала должен быть равен диаметру отверстия, устанавливаемому на нем стандартного элемента.
ПРИМЕР.
На выходном конце вала, расчетный диаметр которого равен dI = = 40,8 мм, должна быть установлена упругая втулочно-пальцевая муфта (МУВП), передающая вращающий момент Т2 = 339,1 Н м. Для этих условий по ГОСТ 21424-93 [2, с. 346] следует выбрать муфты, которые могут передать момент до 500 Н м. Таких муфт две – с диаметром 40 мм и 45 мм. Посадочный диаметр муфты не может быть менее рассчитанного выходного конца вала, поэтому выбираем муфту с посадочным диаметром 45 мм и соответственно диаметр выходного конца вала также будет равен dI = 45 мм.
2. Определение диаметра II-й ступени вала
Так как вторая ступень вала предназначена для установки манжетного уплотнения, которым оснащается крышки подшипника, диаметр этого участка вала должен быть несколько большим, чем у ступени I, чтобы уплотнение при монтаже легко прошло через ступень I,
т.е. dII > dI .
31
Прежде чем определять параметры ступени II, необходимо выбрать уплотнение, которое обеспечит достаточную герметичность подшипника на выходе вала из редуктора. По ГОСТ 8752-79 [2, с. 320] выбираем для уплотнения резиновую армированную манжету с внутренним диаметром посадки на вал dупл и с максимальной шириной h1 . Для рассматриваемого примера dупл = 48 мм, h1 = 10 мм.
Диаметр ступени II вала будет равен внутреннему диаметру уплотнения dII = dупл .
3.Определение диаметра III-й ступени вала, выбор подшипника и проставочного кольца
Третья ступень является опорным участком вала и предназначена для установки подшипника и проставочного кольца.
Для удобства установки подшипника диаметр ступени III должен быть несколько больше диаметра ступени II , т.е. dIII > dII.
Для редукторов, передающих мощность менее 5 кВт, следует выбирать подшипники легкой серии.
При выборе типа подшипника следует обратить внимание на наличие (или отсутствие) силы, действующей вдоль оси вала. Такая сила всегда присутствует, если на валу установлено косозубое колесо.
При наличии осевой силы рекомендуется выбирать роликовый ра- диально-упорный подшипник. При отсутствии осевой силы – шариковый радиальный однорядный подшипник [2, с. 540 … 545].
Выбранные параметры подшипника должны быть представлены в виде таблицы.
ПРИМЕР.
Подшипник роликовый конический однорядный
Обозначение |
7210 |
Внутренний диаметр d , мм |
50 |
Наружный диаметр D , мм |
90 |
Ширина внутреннего кольца В , мм |
21 |
Монтажная высота подшипника Tmax , мм |
21,75 |
Радиус фаски r , мм |
2 |
Базовая динамическая грузоподъемность Cr , кН |
56,0 |
Базовая статическая грузоподъемность C0r , кН |
40,0 |
Для удобства посадки подшипника на вал на торце третьей ступени должна быть предусмотрена фаска под углом 45о.
32
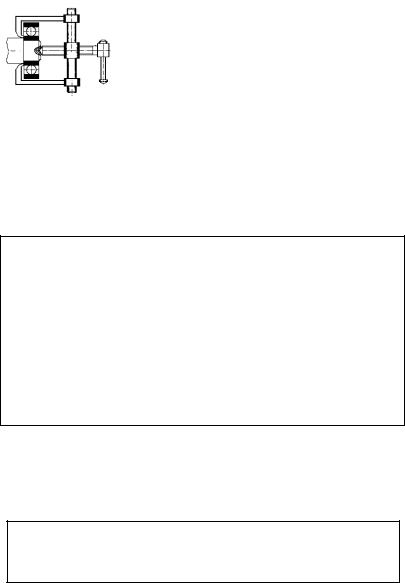
На этой ступени кроме подшипника размещается также проставочное кольцо, устанавливаемое между подшипником и зубчатым колесом.
Проставочное кольцо служит для:
•осевой фиксации зубчатого колеса на
валу; |
|
Рис. 6. Схема снятия |
|
• обеспечения удобства снятия подшип- |
|||
ника с помощью съемника (рис. 6). |
подшипника с вала с |
||
помощью съемника |
|||
Для |
обеспечения достаточного зазора |
||
между |
колесом и подшипником ширину |
|
проставочного кольца следует выполнять в пределах bпк = 5 … 7 мм. Высоту торца кольца целесообразно принять примерно равной по-
ловине высоты опорного торца внутреннего кольца подшипника, которую можно определить из данных, приведенных в приложении 12.
ПРИМЕР.
На третьей ступени вала установлен подшипник 7210 с внутренним диаметром d = 50 мм и наружным диаметром D = 90 мм. Высота опорного торца внутреннего кольца этого подшипника:
S = 0,5 [0,48(D +d) −d ]= 0,24 140 −25 =8,6 мм.
Высоту опорного торца проставочного кольца следует принять равной:
hпк ≈ 0,5S ≈ 4,5 мм.
Проставочное кольцо должно иметь следующие параметры:
-внутренний диаметр dпк = 51 мм;
-наружный диаметр Dпк = 59 мм;
-ширина bпк = 7 мм.
4.Определение диаметра IV-й ступени вала
Четвертая ступень – предназначена для установки зубчатого колеса. Диаметр этой ступени должен быть несколько больше предыдущей и обязательно соответствовать ряду нормальных линейных размеров.
ПРИМЕР.
Для рассматриваемого примера диаметр третьей ступени вала
был равен dIII = 50 мм. Поэтому принимаем из ряда Ra40 (см. приложение 4) диаметр четвертой ступени dIV = 53 мм.
Следует обратить внимание, что диаметр четвертой ступени вала следует согласовать с ранее полученным посадочным диаметром зубчатого колеса, который был определен предварительно при выполне-
33
нии РГР №2 (для рассматриваемого примера предварительное значение диаметра посадочного отверстия колеса было равно dотв = 50 мм). Известно, что сопряженные диаметры должны быть равны, поэтому принимаем dотв = dIV . Соответственно будет изменена и величина диаметра ступицы колеса.
5. Определение диаметра V-й ступени вала
Пятая ступень вала – это буртик, который обеспечивает заданное осевое положение зубчатого колеса на валу относительно опор. Наружный диаметр буртика целесообразно делать равным наружному диаметру проставочного кольца, т.е.:
dV = Dпк
6. Определение диаметра VI-й ступени вала
Ступень VI предназначена для установки второго подшипника. Обычно на валу редуктора с обеих его сторон устанавливают одинаковые подшипники. Поэтому диаметр VI-ой ступени вала будет таким же, как и диаметр его третьей ступени.
dVI = dIII .
Этап 4. Определение длины каждой ступени вала
Длины почти всех ступеней вала назначаются из конструктивных соображений. Исключение составляют участки, предназначенные для размещения деталей, передающих вращающий момент. В рассматриваемом примере это четвертая ступень, где установлено зубчатое колесо, и первая ступень, т.е. выходной конец вала.
1. Определение длины IV-й ступени вала
Прежде чем определять длину четвертой ступени вала следует определить присоединительные размеры зубчатого колеса и его конструктивные размеры. Предварительно длина ступицы была принята из
условия lст = b2.
Окончательную длину ступицы зубчатого колеса определяют исходя из размеров шпонки, которая должна передавать вращающий момент от колеса к валу.
Наиболее простым конструктивным решением шпоночного соединения являются призматические шпонки [2, с. 251]. Призматическая шпонка представляет собой стальной брусок прямоугольного сечения. Размеры сечения (bшп х hшп) определяются по стандарту (ГОСТ 23360-
34

78) исходя из диаметра вала в месте ее расположения (см. приложение 12). Длина шпонки lшп рассчитывается исходя из величины передаваемого вращающего момента. Выбранные параметры шпоночного паза должны обеспечивать прочность шпонки на смятие:
σ |
|
= |
2 103 Мк |
|
≤[σ] |
; |
( 38 ) |
|
|
|
|
||||||
|
см |
|
d(h |
−t )l |
|
см |
|
|
|
|
|
шп |
1 |
p |
|
|
где Мк – крутящий момент (Нм) на валу, в данном случае равный вращающему моменту на колесе, т.е Мк = Т2 ;
d – диаметр вала в месте установки шпонки (в данном случае dIV); t1 – глубина шпоночного паза на валу;
[σ]см – допускаемое напряжение смятия (для шпонок из стали 45 при-
нимают [σ]см = 150 Н/мм2 ); lр – рабочая длина шпонки.
Минимально допустимая рабочая длина шпонки определится из условия отсутствия смятия по формуле:
l p ≥ |
2 103 |
Мк |
; |
( 39 ) |
|
d(hшп − t1 )[σ]см |
|||||
|
|
|
Полученный результат округляют до целого числа в большую сторону. Полная длина шпонки определится по формуле:
lшп = lр + bшп . |
( 40 ) |
Расчетную длину шпонки увеличивают до ближайшего стандартного размера (см. приложение 12).
ПРИМЕР. Для рассматриваемого редуктора при dIV = 53 мм ширина шпоночного паза по ГОСТ 23360-78 составит b = 16 мм, высота шпонки h = 14 мм, глубина паза на валу t1 = 9 мм:
l p ≥ |
2 103 |
339,1 |
= 20,5 мм. |
||
53 (14 |
−9) 150 |
||||
|
|
Полная длина шпонки составит:
lшп = lр + bшп = 20,5 +16 = 36,5 мм.
Согласно стандартному ряду размеров, длину шпонки назначаем lшп = 40 мм.
После определения длины шпонки на четвертой ступени вала необходимо проверить, позволяет ли ступица зубчатого колеса установить шпонку такой длины. Если длина ступицы меньше длины шпонки, то длину ступицы увеличивают, перекрывая длину шпонки на 2 … 3 мм с каждой стороны:
lст = lшп + (2…3) 2 , мм. |
( 41 ) |
35
После уточнения длины ступицы длину четвертой ступени вала
определяют по формуле (42): |
|
lIV = lст – 1, мм. |
(42) |
2. Определение длины V-й ступени
Пятая ступень вала – это буртик, который обеспечивает заданное осевое положение зубчатого колеса на валу относительно опор и корпуса редуктора. Такое же назначение имеет и проставочное кольцо, расположенное на третьей ступени вала.
Поэтому длина пятой ступени будет равна: lV = bпк .
3. Определение длины VI-й ступени
Шестая ступень вала предназначена для установки подшипника и должна обеспечивать надежное расположение подшипника по всей его ширине. Поэтому длину шестой ступени следует принять на 1…2 мм больше ширины внутреннего кольца устанавливаемого подшипника.
Для удобства посадки подшипника на вал на торце шестой ступени должна быть предусмотрена фаска 1х45о.
4. Определение длины III-й ступени
Третья ступень вала предназначена для установки подшипника и проставочного кольца. Следует обратить внимание, что для гарантированного размещения этих деталей длина ступени вала должна быть на 1…2 мм больше их суммарной длины.
5. Определение длины II-й ступени
Длину второй ступени для удобства установки уплотнения с последующим закреплением крышкой можно принять равной удвоенной ширине уплотнения: lII = 2 h1.
Переход с диаметра первой ступени на диаметр второй ступени выполняют в виде галтели с радиусом:
r = dII −dI . 2
6. Определение длины I-й ступени
Длина первой ступени вала определяется исходя из длины детали, которая должна быть установлена на этой ступени (полумуфта, звездочка, шкив и т.п.). Так как длина этих деталей может быть различна
36
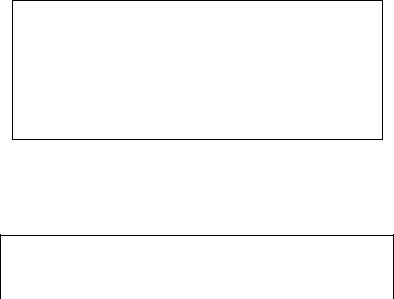
[см. 2, с.346 … 347; 232; 206], предварительно длину первой ступени определяют исходя из размеров шпонки. Если длина устанавливаемой детали не стандартизована, длина этого участка вала принимается по ГОСТ 12080-66 (приложение 12).
Длина шпонки на этом участке вала определяется так же, как и для четвертой ступени по формулам (39) и (40). После получения значения полной длины шпонки ее проверяют на соответствие стандартному размеру (приложение 13).
Шпоночный паз располагается вдоль ступени, не доходя до ее концов на 2…3 мм. Поэтому предварительная длина первой ступени вала будет равна:
lI = lшп + 2 (2 … 3) мм. |
(43) |
Найденную расчетным путем длину первой ступени уточняют, приводя в соответствие с длиной устанавливаемой детали (lдет ). При этом соблюдается условие:
lI = lдет+ (2 … 3) мм. |
(44) |
Окончательная длина первой ступени принимается в соответствии с ГОСТ 12080-66 (см. приложение 8).
ПРИМЕР.
Расчетная длина шпоночного паза на первой ступени составляет 45 мм, поэтому длина первой ступени не может быть менее 50 мм. Следует также учесть, что на выходном конце вала установлена полумуфта, длина которой по стандарту составляет 56 мм. Длина первой ступени должна обеспечивать размещение данной полумуфты. Окончательная длина первой ступени при диаметре 45 мм принимается по стандарту равной 82 мм.
7. Принятые размеры вала
Для разработки чертежа конструкции вала второй ступени редуктора с расположенными на нем элементами рекомендуется свести результаты расчетов в единую (сводную) таблицу.
ПРИМЕР
Ступень |
I |
II |
III |
IV |
V |
VI |
Полная |
Диаметр, мм |
45 |
48 |
50 |
53 |
59 |
50 |
длина вала |
Длина, мм |
82 |
20 |
31 |
55 |
7 |
24 |
219 |
|
|
|
37 |
|
|
|
|
Этап 5. Разработка конструкции вала второй ступени редуктора с установленными на нем элементами
Графическая часть работы выполняется на чертежной бумаге или на миллиметровой бумаге формата А4 или А3 со стандартными полями и штампом. Все элементы чертежа выполняются карандашом с использованием чертежных инструментов.
Чертеж второй (тихоходной) ступени редуктора должен включать в себя выходной вал редуктора в масштабе 1:1 (или 1:2) с установленными на нем элементами (см. приложение 14):
•зубчатое колесо:
•подшипники;
•проставочное кольцо.
Для лучшего отображения конструктивных особенностей деталей зубчатое колесо, подшипники и проставочное кольцо должны быть показаны в разрезе. Так же должен быть представлен разрез шпоночного участка выходного конца вала.
При вычерчивании подшипников следует обратить внимание, что размеры всех деталей подшипника взаимосвязаны (приложение 11).
На чертеже обязательно должны быть указаны размеры диаметров и длин ступеней вала, а также полная длина вала. В сечении вала следует указать размеры шпоночного паза.
38
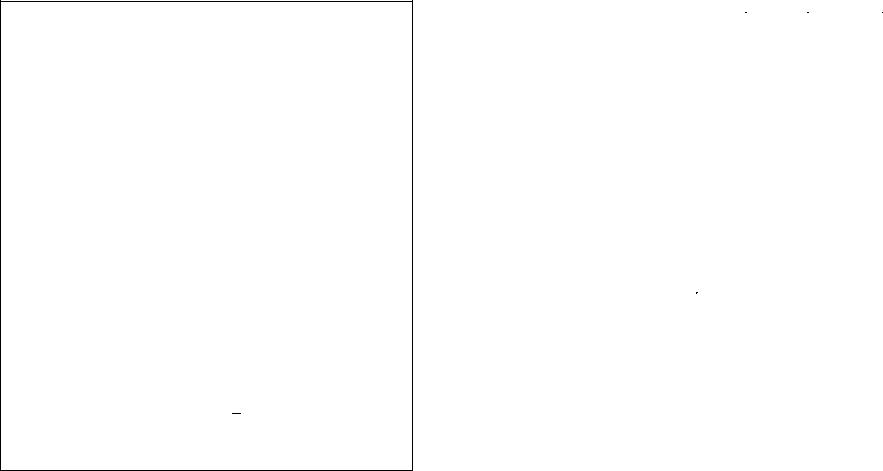
ПРИЛОЖЕНИЯ
Приложение 1
Форма титульного листа
МОСКОВСКИЙ ГОСУДАРСТВЕННЫЙ УНИВЕРСИТЕТ ПРИКЛАДНОЙ БИОТЕХНОЛОГИИ
Кафедра "Детали машин и теория механизмов"
Расчетно-графическая работа № ___
___________________________________________________
Н а и м е н о в а н и е РГР
___________________________________________________
Вариант № _____
(Фамилия, имя, отчество студента ) |
|
(Подпись студента) |
|
|
|
(Факультет) |
|
(Курс, группа) |
|
|
|
(Фамилия, имя, отчество преподавателя) |
|
(Подпись преподавателя) |
|
|
|
|
|
(Дата приема) |
Москва 20
39
|
|
|
|
|
|
|
|
|
|
|
|
Приложение 2 |
||
|
|
Ориентировочные значения основных |
|
|
||||||||||
|
|
параметров механических передач |
|
|
||||||||||
|
|
|
|
|
|
|
|
|
|
|
Передаточное число |
|||
|
|
Элемент привода |
|
|
КПД |
|
предельно |
рекомендуемое |
||||||
|
|
|
|
|
допустимое, |
максимально |
||||||||
|
|
|
|
|
|
|
|
|
|
uдоп |
допустимое, umax |
|||
Передача зубчатая цилиндри- |
|
|
|
|
|
|
|
|
|
|
||||
ческая закрытая (без учета |
|
0,96...0,97 |
|
|
≤ 8 |
6,3 |
|
|||||||
подшипников) |
|
|
|
|
|
|
|
|
|
|
|
|
||
Передача цепная (открытая) |
|
0,90... 0,93 |
|
≤ 10 |
6 |
|
|
|||||||
|
|
|
|
|
|
|
|
|
|
|
|
|
|
|
Передача ременная (трением) |
|
0,94...0,96 |
|
|
≤ 8 |
4 |
|
|
||||||
|
|
|
|
|
|
|
|
|
|
|
|
|
|
|
Муфта соединительная |
|
|
0,98 |
|
|
|
− |
− |
|
|
||||
|
|
|
|
|
|
|
|
|
|
|
|
|
|
|
Подшипники качения |
|
|
0,99 |
|
|
|
− |
− |
|
|
||||
(однапара) |
|
|
|
|
|
|
|
|
|
|
||||
|
|
|
|
|
|
|
|
|
|
|
|
|||
|
|
|
|
|
|
|
|
|
|
|
|
Приложение 3 |
||
|
|
Технические данные двигателей серии АИР |
||||||||||||
|
Мощ- |
|
Синхронная частота вращения, мин –1 |
|
|
|||||||||
|
3000 |
1500 |
|
1000 |
750 |
|
||||||||
|
ность, |
|
Асинхр. |
|
Асинхр. |
|
|
|
|
Асинхр. |
|
Асинхр. |
|
|
|
кВт |
Тип |
частота, |
Тип |
частота, |
Тип |
частота, |
Тип |
частота, |
|
||||
|
|
|
мин – 1 |
|
мин – 1 |
|
|
|
|
мин – 1 |
|
мин –1 |
|
|
|
0,55 |
– |
– |
71А4 |
1357 |
|
71В6 |
|
915 |
– |
– |
|
||
|
|
|
|
|
|
|
|
|
|
|
|
|
||
|
0,75 |
71А2 |
2820 |
71В4 |
1350 |
|
80А6 |
|
920 |
90LA8 |
705 |
|
||
|
|
|
|
|
|
|
|
|
|
|
|
|
||
|
1,1 |
71B2 |
2805 |
80A4 |
1395 |
|
80В6 |
|
920 |
90LB8 |
715 |
|
||
|
|
|
|
|
|
|
|
|
|
|
|
|
||
|
1,5 |
80A2 |
2850 |
80B4 |
1395 |
|
90L6 |
|
925 |
100L8 |
702 |
|
||
|
|
|
|
|
|
|
|
|
|
|
|
|
||
|
2,2 |
80B2 |
2850 |
90L4 |
1395 |
|
100L6 |
|
945 |
112MA8 |
709 |
|
||
|
|
|
|
|
|
|
|
|
|
|
|
|
||
|
3 |
90L2 |
2850 |
100S4 |
1410 |
|
112MA6 |
|
950 |
112MB8 |
709 |
|
||
|
|
|
|
|
|
|
|
|
|
|
|
|
|
|
|
4 |
100S2 |
2850 |
100L4 |
|
I410 |
|
112MB6 |
|
950 |
132S8 |
716 |
|
|
|
|
|
|
|
|
|
|
|
|
|
|
|
||
|
5,5 |
100L2 |
2850 |
112M4 |
1432 |
|
132S6 |
|
960 |
132M8 |
712 |
|
||
|
|
|
|
|
|
|
|
|
|
|
|
|
||
|
7,5 |
112M2 |
2895 |
132S4 |
1440 |
|
132M6 |
|
960 |
160S8 |
727 |
|
||
|
|
|
|
|
|
|
|
|
|
|
|
|
||
|
11 |
132M2 |
2910 |
132M4 |
1447 |
|
160S6 |
|
970 |
160M8 |
727 |
|
||
|
|
|
|
|
|
|
|
|
|
|
|
|
|
|
Примечание: Пример обозначения двигателя: "Двигатель АИР100L2 ТУ 16–525.564–84"
40