
Химсопрмат
.pdfПреимущества протекторной защиты заключаются в простоте, эффективности, высоком уровне рентабельности. Недостатки – в нестабильности защитного тока в процессе эксплуатации (за счет частичной пассивации протектора), малом сроке службы протектора.
7.2.3. Использование вторичных алюминиевых сплавов в качестве протекторов
Преимуществами протекторной защиты являются простота монтажа и отсутствие внешнего источника тока. Однако основным недостатком протекторной защиты является безвозвратная потеря материала протектора [41], что адекватно экономическим потерям, которые следует минимизировать.
Чистые металлы и их сплавы отличаются высокой стоимостью,
но имеется много отработанных изделий, из которых можно получить вторичные алюминиевые сплавы с примесями. Значительный практи-
ческий интерес представляет их использование для изготовления протекторов, что позволит снизить себестоимость протекторов и ра-
ционально использовать материалы.
Проведены исследования свойств вторичных алюминиевых спла-
вов с целью определения их электрохимических и коррозионных ха-
рактеристик, возможности их использования для изготовления про-
текторов путем простого переплава или с введением модификаторов
иобласти их применения.
Вкачестве образцов проводились испытания вторичных алюми-
ниевых сплавов, приближенных по своим химическим составам к маркам АМг, АВ, АК-8 и сплавов на основе Al–Cu–Si.
Химический состав исследуемых образцов представлен в табл. 7.3.
Пластовые воды по своему химическому составу разнообразны и могут иметь различное содержание отдельных компонентов [43]. На основании анализа подтоварных вод Самарской и Оренбургской областей был выбран модельный раствор, состав которого отвечает тео-
339
ретическим рекомендациям и наиболее близок к химическому составу подтоварных вод. Состав модельного раствора: 98,6% – NaCl; 0,28% – ион Ca2+; 0,012% – ион Mg2+; 0,524% – ион SO24 .
Таблица 7.3
Химический состав вторичных алюминиевых сплавов
№ об- |
|
Содержание основных элементов, % (основ. Al) |
Примечание |
|||||||
разца |
|
|
|
|
|
|
|
|
|
|
Cu |
|
Si |
Mg |
Mn |
Ti |
Fe |
Zn |
Be |
||
|
|
|||||||||
|
|
|
|
|
|
|
|
|
|
|
2 |
0,8 |
|
0,6 |
1,52 |
0,26 |
0,02 |
0,4 |
- |
- |
Марка АВ |
|
|
|
|
|
|
|
|
|
|
|
3 |
0,75 |
|
0,62 |
0,32 |
0,15 |
0,02 |
0,41 |
- |
- |
|
|
|
|||||||||
|
|
|
|
|
|
|
|
|
|
|
5 |
2,3 |
|
0,71 |
0,75 |
0,33 |
0,03 |
0,69 |
- |
- |
Марка АК-8 |
|
|
|
|
|
|
|
|
|
|
|
1 |
0,84 |
|
0,63 |
1,9 |
0,74 |
- |
0,5 |
0,2 |
- |
Марка |
|
|
|
|
|
|
|
|
|
|
|
8 |
1,05 |
|
2,5 |
0,1 |
0,15 |
0,02 |
0,58 |
- |
- |
|
|
Al–Cu–Si |
|||||||||
|
|
|
|
|
|
|
|
|
|
|
11 |
1,18 |
|
2,54 |
0,12 |
0,1 |
0,02 |
0,52 |
- |
- |
|
|
|
|||||||||
|
|
|
|
|
|
|
|
|
|
|
05 |
- |
|
- |
4 |
0,09 |
- |
0,45 |
- |
0,0002 |
|
|
|
|
|
|
|
|
|
|
|
|
06 |
- |
|
- |
4,15 |
0,09 |
- |
0,47 |
- |
0,0002 |
|
|
|
|
|
|
|
|
|
|
|
Марка |
07 |
- |
|
- |
3,8 |
0,09 |
- |
0,49 |
- |
0,0002 |
|
|
|
|
|
|
|
|
|
|
|
АМг |
08 |
- |
|
- |
3,9 |
0,09 |
- |
0,6 |
- |
0,0002 |
|
|
|
|
|
|
|
|
|
|
|
|
09 |
- |
|
- |
3,95 |
0,09 |
- |
0,42 |
- |
0,0002 |
|
|
|
|
|
|
|
|
|
|
|
|
12 |
- |
|
- |
3,9 |
0,19 |
- |
0,45 |
- |
0,0002 |
|
|
|
|
|
|
|
|
|
|
|
|
Исследуемые образцы выдерживались в модельном растворе с минерализацией от 20 до 200 г/л, периодически производилось их взвешивание, по этим данным определены весовые показатели скорости саморастворения, т. е., фактически, скорости их коррозии. Зависимости весовых показателей скорости саморастворения от минерализации воды представлены на рис. 7.21 и 7.22.
Одними из критериев, определяющих практическую пригодность протекторных сплавов, являются достаточно отрицательный потенциал и незначительное саморастворение [41]. Известно, что содержание таких элементов, как Mg, Mn, Cu, Fe, может оказывать различное влияние как на скорость саморастворения [39,40], так и на величину потенциала.
340
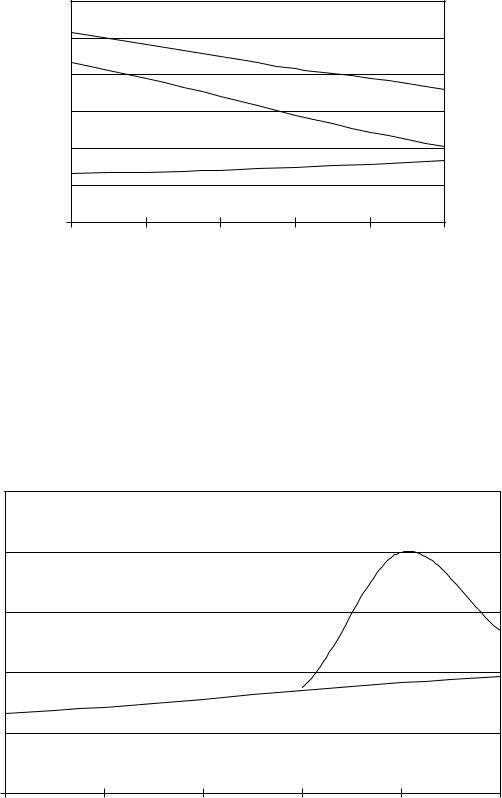
скорости |
|
0,018 |
|
|
|
|
|
час) |
0,015 |
|
|
2 |
|
|
|
0,012 |
|
|
|
|
|||
Весовой коэффициент |
коррозии, г/(см2∙ |
|
|
|
|
|
|
0,009 |
|
|
3 |
|
|
||
|
|
|
|
|
|||
0,006 |
|
1 |
|
|
|
||
|
|
|
|
|
|||
0,003 |
|
|
|
|
|
||
0 |
|
|
|
|
|
||
|
|
|
|
|
|
|
|
|
|
20 |
40 |
60 |
80 |
140 |
200 |
|
|
|
|
Концентрация раствора, г/л |
|
|
|
|
Рис. 7.21*. Зависимость весового коэффициента скорости |
|
||||
|
|
саморастворения образцов от минерализации раствора: |
|
||||
|
1 – образцы, приближенные к марке АВ; 2 – образец, приближенный |
|
|||||
|
|
к марке АК–8; 3 – образцы на основе сплава Al–Cu–Si |
|
||||
|
|
* – Результаты получены при участии Бестужевского М.В. |
|
||||
, |
|
0,015 |
|
|
|
|
|
коррозии |
|
0,012 |
|
|
|
|
|
|
|
|
|
|
|
|
|
скорости |
|
|
|
|
05, 06 |
|
|
час) |
0,009 |
|
|
|
|
|
|
|
|
|
|
|
|
||
коэффициент |
г/(см2∙ |
0,006 |
|
|
|
|
|
0,003 |
|
07, 08, 09, 12 |
|
|
|
||
Весовой |
|
|
|
|
|
|
|
|
0 |
|
|
|
|
|
|
|
|
|
|
|
|
|
|
|
|
20 |
40 |
60 |
80 |
140 |
200 |
|
|
|
|
Концентрация раствора, г/л |
|
|
Рис. 7.22*. Зависимость весового коэффициента скорости саморастворения образцов, приближенных к марке АМг, от минерализации раствора
341
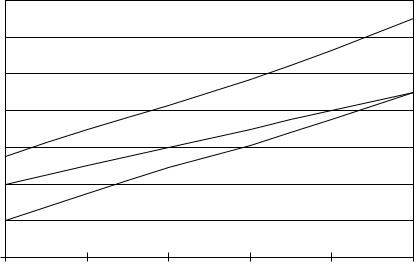
Результаты экспериментов демонстрируют определенные различия в скорости саморастворения. Из изучаемых групп образцов низкую скорость саморастворения показали образцы, химический состав которых приближен к маркам АВ и АМг. Такое поведение образцов можно объяснить отсутствием или низким содержанием в их составе вредных примесей меди и железа, а также наличием в сплавах АМг высокого содержания магния.
Так как исследуемые материалы предполагается использовать в качестве протекторных, то наряду с весовым показателем скорости саморастворения необходимо также знать величины стационарных потенциалов, зависимости которых от минерализации воды представлены на рис. 7.23 и 7.24.
|
-0,52 |
|
|
|
|
|
|
-0,5 |
|
|
|
|
|
в.э.) |
-0,48 |
|
|
|
|
|
. |
|
|
1 |
|
|
|
В (н |
-0,46 |
|
|
|
|
|
|
|
|
|
|
||
, |
|
|
|
3 |
|
|
Потенциал |
-0,44 |
|
|
|
|
|
|
|
|
|
|
||
-0,42 |
|
|
2 |
|
|
|
|
|
|
|
|
||
|
|
|
|
|
|
|
|
-0,4 |
|
|
|
|
|
|
-0,38 |
|
|
|
|
|
|
20 |
40 |
60 |
80 |
100 |
200 |
|
|
|
Концентрация раствора, г/л |
|
|
Рис. 7.23*. Зависимость потенциалов образцов от минерализации раствора:
1 – образцы, приближенные к марке АВ; 2 – образец, приближенный к марке АК–8; 3 – образцы на основе сплава Al–Cu–Si
Наиболее отрицательным потенциалом обладают образцы, химический состав которых приближен к марке АМг. Из общего числа образцов данной марки лишь образец за номером 12 отличается менее отрицательным потенциалом, что, по-видимому, связано с содержанием в его составе марганца более 0,09%.
342
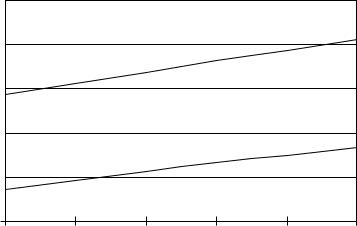
|
-0,7 |
|
|
|
|
|
э.) |
-0,66 |
|
|
|
|
|
.в. |
|
05, 06, 07, 08, |
|
|
|
|
В (н |
-0,62 |
|
|
|
|
|
, |
|
|
|
|
|
|
Потенциал |
-0,58 |
|
|
|
|
|
|
|
|
12 |
|
|
|
-0,54 |
|
|
|
|
|
|
|
-0,5 |
|
|
|
|
|
|
20 |
40 |
60 |
80 |
100 |
200 |
|
|
Концентрация раствора, г/л |
|
|
||
Рис. 7.24*. Зависимость потенциалов образцов, |
||||||
приближенных к марке АМг, от минерализации раствора |
* – Результаты получены при участии Бестужевского М.В.
Анализ полученных данных показывает, что образцы, приближенные к маркам АВ, АК-8 и сплавов на основе Al–Cu–Si, потенциалы которых находятся в интервалах значений от –0,38 до –0,52 В, не смогут обеспечить достаточной защиты конструкционных материалов, так как стандартный потенциал стали равен –0,44 В [41].
В качестве протекторных сплавов можно рекомендовать материалы, химический состав которых приближен к марке АМг. Но даже образцы данной марки ведут себя по-разному. Так, в ходе экспериментов образцы с номерами 05, 06, 09, сходные по химическому составу и практически не отличающиеся по содержанию элементов, показали разные скорости саморастворения в интервале концентраций модельного раствора 80÷200 г/л.
Скорость саморастворения образцов с номерами 05, 06 составила 0,0036÷0,012 г/(см2∙час) в отличие от образца с номером
09– 0,002÷0,0064 г/(см2∙час), см. рис. 7.22.
Вкачестве предположения может быть использована гипотеза о влиянии структуры изучаемых сплавов на процесс коррозии, поскольку в некоторые образцы вводились модификаторы, обеспечи-
343
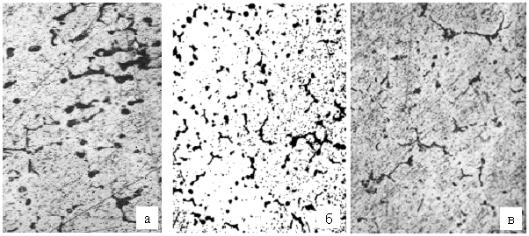
вающие однородность структуры. Микрошлифы образцов с номерами 05, 06, 09, представленные на рис. 7.25, позволяют выявить отличия в содержании включений по границам зерен.
Рис. 7.25. Микроструктура образцов (х500):
а – образец №05, б – образец №06, в – образец №09
Дальнейшее изучение поведения вторичных алюминиевых сплавов в растворах с различной минерализацией, проведение сравнения характеристик технологии литья, размеров зерен, структурных составляющих, окаймляющих границы зерен, и электрохимических характеристик образцов позволит выявить влияние химических и структурных составляющих вторичных алюминиевых сплавов на эффективность их работы в качестве протекторов.
7.2.4. Анодная защита
Анодная защита заключается в создании на поверхности защи-
щаемого металла анодной пассивирующей пленки под действием анодной поляризации от внешнего источника постоянного тока.
Анодную защиту применяют при эксплуатации оборудования, изго-
товленного из легко пассивирующихся материалов (углеродистых,
низколегированных, нержавеющих сталей, титана, высоколегирован-
ных сплавов на основе железа) в средах с хорошей электропроводно-
344
стью. Анодная защита перспективна в случае изготовления оборудо-
вания из разнородных пассивирующихся материалов, например, не-
ржавеющих сталей различного состава, сварных соединений. В табл. 7.4 представлены системы, в которых можно использовать анодную защиту.
Таблица 7.4
Некоторые среды и металлы, для которых возможно применение анодной защиты
Материал |
Агрессивная среда |
|
|
Серная кислота. |
|
|
Олеум. |
|
|
Очищенная серная кислота, содержащая органи- |
|
|
ческие вещества. |
|
|
Целлюлозные щелочные среды. |
|
Углеродистые стали |
Водные растворы аммиака. |
|
Аммиачные удобрения. |
||
|
||
|
Фосфорная кислота. |
|
|
Фосфорная и серная кислоты. |
|
|
Щавелевая кислота. |
|
|
Растворы алюминатов. |
|
|
5% NaOH и 15% Na2CO3 |
|
|
Серная кислота. |
|
|
Сульфат гидроксиламония |
|
|
Азотная кислота. |
|
|
Фосфорная кислота. |
|
|
Удобрения с хлоридом калия. |
|
|
Изобутилсерная кислота. |
|
Хромоникелевые и хромо- |
Сульфатные растворы. |
|
никельмолибденовые ста- |
Щелочи. |
|
ли |
Щелочь и кислота в процессе нейтрализации. |
|
|
Серная и азотная кислоты. |
|
|
Соляная кислота. |
|
|
Муравьиная кислота. |
|
|
Щавелевая кислота. |
|
|
Сульфаминовая кислота. |
|
|
Фосфорная кислота. |
При анодной защите потенциал активно растворяющегося метал-
ла смещают в положительную сторону до достижения устойчивого пассивного состояния (см. рис. 7.7) [10, 24]. В результате не только
345
происходит существенное (в тысячи раз) снижение скорости корро-
зии металла, но и предотвращается попадание продуктов его раство-
рения в производимый материал.
Смещение потенциала в положительную сторону можно осуще-
ствлять:
от внешнего источника тока;
введением окислителей в раствор или введением в сплав элементов, способствующих повышению эффективности протекающего на поверхности металла катодного процесса.
Анодная защита пассивирующими ингибиторами-окислителями основана на том, что в процессе их восстановления возникает ток,
достаточный для перевода металла в пассивное состояние. В качестве ингибиторов могут быть использованы соли Fe3 , нитраты, бихро-
маты и др. Применение ингибиторов позволяет защищать металл в труднодоступных местах – щелях, зазорах. Недостатком этого спосо-
ба защиты является загрязнение технологической среды [24].
При анодной защите методом катодного легирования в сплав вводят добавки, на которых катодные реакции восстановления депо-
ляризаторов осуществляются с меньшим перенапряжением, чем на основном металле [10, 24]. Например, в сплавах титана с небольшим количеством палладия происходит селективное растворение титана, а
поверхность непрерывно обогащается палладием. Палладий выступа-
ет как протектор и пассивирует сплав. Аналогичный эффект наблю-
дается и для хромистых сталей при введении в сплав благородных металлов.
При анодной защите потенциал защищаемой конструкции сме-
щают в область, более положительную относительно потенциала коррозии (см. рис. 7.7). При этом происходит переход металла из ак-
тивного в пассивное состояние. Так, если потенциал свободной кор-
розии E1 металла располагается в активной области и соответствую-
щая ему скорость растворения равна i1, то при его смещении в поло-
346
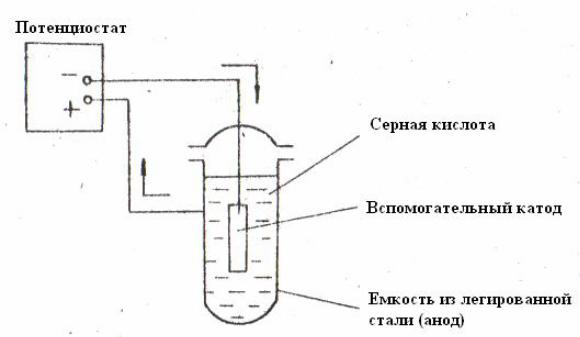
жительную сторону до значения E4 скорость растворения снижается до величины i4 [1, 24].
Установка для анодной защиты состоит из объекта защиты, като-
да, электрода сравнения и источника электрического тока (рис. 7.26) [10].
Рис. 7.26. Схема анодной защиты
Основным условием возможности применения анодной защиты является наличие протяженной области устойчивой пассивности металла при плотности тока растворения металла не более
(1,5-6,0)∙10-1А/м2.
Основным критерием, характеризующим состояние поверхности металла, является электродный потенциал. Обычно возможность применения анодной защиты для конкретного металла или сплава определяют методом снятия анодных поляризационных кривых. При этом получают следующие данные [24]:
потенциал коррозии металла в исследуемом растворе;
протяженность области устойчивой пассивности;
плотность тока в области устойчивой пассивности.
347
Эффективность защиты определяют как отношение скорости коррозии без защиты к скорости коррозии под защитой.
Существенным ограничением применения анодной защиты является вероятность возникновения локальных видов коррозии в области пассивного состояния металла [10, 16, 24]. Для предотвращения этого явления рекомендуют использовать такое значение защитного потенциала, при котором локальные виды коррозии не возникают, или вводить в раствор ингибирующие добавки. Например, анодная защита стали 12X18Н10Т в растворах хлоридов в присутствии ионов NO3
предотвращает образование питтингов и снижает скорость растворения стали в 2000 раз. В ряде случаев вследствие повышенной опасности возникновения локальных коррозионных процессов применение анодной защиты неэффективно. Резкий рост критического тока пассивации металлов с увеличением температуры агрессивных сред ограничивает применение анодной защиты в условиях повышенных температур.
При стационарном режиме работы установки величина тока поляризации, требуемого для поддержания устойчивого пассивного состояния, постоянно меняется вследствие изменения эксплуатационных параметров коррозионной среды (температуры, химического состава, условий перемешивания, скорости движения раствора и др.). Поддерживать потенциал металлоконструкции в заданных границах можно путем постоянной или периодической поляризации. В случае периодической поляризации включение и выключение тока производят либо при достижении определенного значения потенциала, либо при его отклонении на определенную величину. В обоих случаях параметры анодной защиты определяют опытным способом в лабораторных условиях.
В качестве катодов используют малорастворимые материалы, на-
пример Pt,Ta,Pb,Ni [10, 24] , платинированную латунь, высоколеги-
рованные нержавеющие стали и др. Схема расположения катодов проектируется индивидуально для каждого конкретного случая защиты.
348