
Химсопрмат
.pdf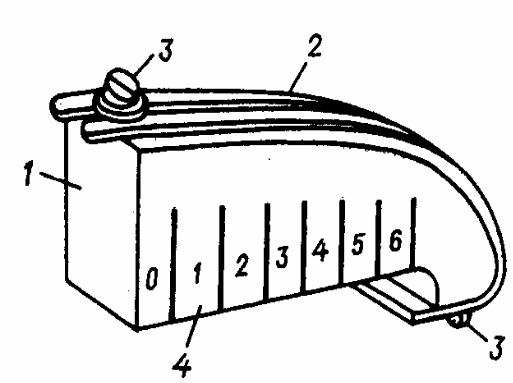
Модуль упругости при растяжении определяется как отношение приращения напряжения к соответствующему приращению относи-
тельного удлинения. Модуль упругости наиболее жестких пластмасс в 5-10 раз ниже, чем металлов. Модуль упругости при изгибе опреде-
ляется по ГОСТ 9558.
Твердость пластмасс определяют методом вдавливания стального шарика в поверхность образца по ГОСТ 4670.
Коррозионные испытания образцов пластмасс в напряженно-
деформированном состоянии проводят с помощью приспособления,
имеющего образующую эллиптической формы (рис. 6.2) [22, 23].
Рис. 6.2. Приспособление для создания напряженно-деформированного состояния пластмасс:
1 – эллипс; 2 – прижимная планка; 3 – винты; 4 – шкала отсчета по ГОСТ 12020
Приспособление изготавливается из материала, стойкого к воздействию агрессивной среды, по размерам, зависящим от модуля упругости материала.
279
Для испытаний применяют образцы материала в форме полосок шириной 20 мм и толщиной 1-2 мм, длина равна длине эллиптической поверхности приспособления. Образец закрепляют на этой поверхности и погружают в сосуд с коррозионной средой.
После испытаний под микроскопом определяют длину участка растрескивания и вычисляют деформацию растрескивания по формуле
|
|
b |
a2 b2 |
|
2 |
|
3 |
|
|||
|
|
z |
2 |
|
|||||||
ТР |
|
|
|
1 |
|
|
|
, |
|||
a |
2 |
a |
4 |
||||||||
|
|
|
|
|
|
|
|
|
|
где a – длина большой полуоси эллипса приспособления для испытаний;
b– длина малой полуоси эллипса;
– толщина образца;
z – длина участка растрескивания.
Для получения более корректных данных об изменении механических свойств неметаллических материалов во времени широкое применение находят методы длительных испытаний в условиях, приближенных к условиям эксплуатации. Испытания проводят с использованием различных приспособлений, позволяющих создать механические нагрузки, повышенную или пониженную температуру, контакт с агрессивной средой и др. [23].
Наибольшую количественную информацию о кинетике процесса разрушения можно получить при испытаниях с постоянным растягивающим напряжением (для эластически и пластически деформируемых материалов) или с постоянной нагрузкой (чаще используется для жестких высокопрочных пластмасс). При проведении испытаний в агрессивных средах установку герметизируют.
Испытания неметаллических материалов на растяжение могут проводиться с использованием приспособления (рис. 6.3) с электрической регистрационно-измерительной системой [22].
Установка состоит из нагрузочных секций, монтируемых на верхней и нижней опорных плитах. Обе опорные плиты укреплены на
280
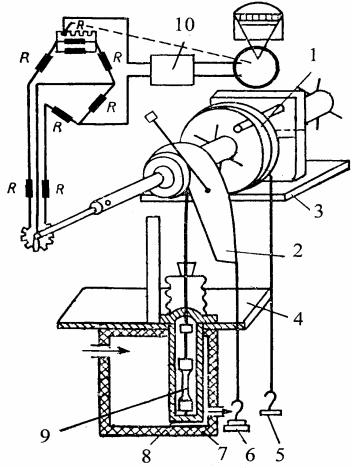
штанге, при этом образуется единая жесткая конструкция. Для на-
блюдения за ростом трещин и кинетикой перераспределения напря-
жений в образце на установке можно смонтировать микроскоп.
Профиль фигурного рычага задается соотношением:
R0 |
1 , |
(6.4) |
|
||
R |
|
где R0 – начальный радиус кривизны рычага;
R– текущий радиус;
– относительное удлинение образца.
Рис. 6.3. Схема установки для коррозионных испытаний при растяжении:
1 – диск нагрузочный; 2 – рычаг фигурный; 3, 4 – плиты опорные; 5, 6 – грузы; 7 – термостат; 8 – ячейка; 9 – образец; 10 – регистратор
281
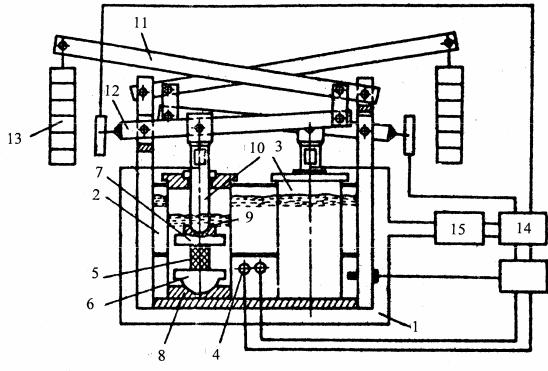
Для реализации напряжений сжатия используется приспособле-
ние, представленное на рис. 6.4 [18]. Устройство работает следую-
щим образом. Испытуемые образцы устанавливают в ячейках 3 меж-
ду шарнирами 8 и 9 и штампами 6 и 7. Затем ячейки с образцами 5
устанавливают в термостате 2. Соединяют штампы 7 через направ-
ляющие 10 с пластинами 12, а на пластинах 11 укрепляют грузы 13.
Термостат 2 заполняют теплоносителем и поддерживают определен-
ную температуру.
Рис. 6.4. Устройство для коррозионных испытаний образцов под нагрузкой:
1 – станина, 2 – термостат, 3 – ячейка, 4 – нагреватель, 5 – образец, 6, 7 – штампы, 8, 9 – шарниры, 10 – направляющая, 11, 12 – пластины, 13 – груз, 14 – регистратор, 15 – тензостанция
Таким образом, образцы 5 подвергаются одновременному воз-
действию температуры, агрессивной среды и сжимающей нагрузки.
За счет периодического изменения массы грузов возможно создание малоцикловой нагрузки.
282
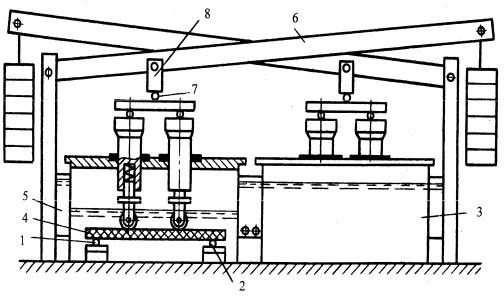
Имеется аналогичное приспособление для испытаний образцов конструкционных материалов в агрессивной среде в условиях чисто-
го изгиба. Схема устройства приведена на рис. 6.5 [19].
Приспособление содержит две цилиндрические опоры в виде ро-
ликов 1 и 2 и один или несколько нажимных подпружиненных эле-
мента. В ячейку 3 устанавливают плиты с полусферическими опора-
ми, на которых размещают ролики. Поверх роликов 1 и 2 устанавли-
вают образец 4 и размещают ячейки в термостате 5. Элементы конст-
рукции соединяют шарнирами и с помощью грузов через рычаги 6,
направляющие 8 и ролики 7 создают усилия на образцах. Наличие подпружиненных элементов обеспечивает плавное приложение на-
грузки к образцу, необходимое ее распределение и поддерживает ее постоянной в процессе испытаний.
Рис. 6.5. Приспособление для испытаний образцов материалов на чистый изгиб в агрессивной среде:
1, 2, 7 – ролики, 3 – ячейка, 4 – образец, 5 – термостат, 6 – рычаг, 8 – направляющая
Обязательному коррозионному контролю подлежат полимерные и лакокрасочные покрытия, применяемые для защиты от агрессивных сред и атмосферной коррозии. Основные характеристики, опреде-
283
ляющие защитные свойства лакокрасочных покрытий: сплошность, проницаемость (как быстро компоненты агрессивной среды проникают через пленку), химическая стойкость, адгезия к защищаемой поверхности, ударная прочность, твердость и эластичность.
Для определения сплошности покрытий используют высокочастотные или электроконтактные дефектоскопы. Наличие дефекта в пленке определяется по звуковому сигналу или стрелочному индикатору.
В настоящее время существует три группы методов определения коэффициентов диффузии и проницаемости компонентов агрессивных сред [23]:
методы, основанные на измерении проницаемости;
методы, основанные на измерении физико-химических свойств полимеров;
методы, основанные на регистрации положения движущейся границы вещества в полимере.
Определение диффузионных параметров методом проницаемости основано на регистрации количества вещества, переносимого за единицу времени через единицу площади полимерной пленки. Значение коэффициента диффузии может быть найдено двумя способами.
Первый способ базируется на данных по проницаемости и растворимости вещества в полимере. Коэффициент диффузии рассчитывается по формуле, полученной из первого закона Фика [22, 23, 34]:
D |
dcp |
|
V |
|
|
|
|
|
, |
(6.5) |
|
dt |
|
||||
|
|
c0 F |
|
где V – объем ячейки, в которой регистрируется вещество;
– толщина пленки полимера; F – площадь пленки полимера; t – время;
284

c0 и cp – концентрации вещества в поверхностном слое полиме-
ра со стороны раствора вещества постоянной концентрации и со сто-
роны измеряемого раствора соответственно.
Второй способ основан на знании времени запаздывания, т. е.
времени, в течение которого вещество не может быть зарегистриро-
вано в камере с измеряемым раствором.
Определение диффузионных параметров с помощью методов, ос-
нованных на измерении физико-химических свойств, заключается в прямом или косвенном фиксировании количества компонентов агрес-
сивной среды в материале.
Коэффициент диффузии может быть найден из уравнения [23]
D 0,0494 |
x2 |
, |
(6.6) |
|
|
||||
|
|
|
где x – глубина проникновения среды;
– время, за которое произошло проникновение.
Для определения коэффициента диффузии также могут исполь-
зоваться спектральные методы, методы радиоактивных изотопов, ме-
тод электропроводности или электрохимического потенциала и дру-
гие.
Определение диффузионных параметров возможно по регистра-
ции границы вещества в материале. Скорость перемещения зоны за-
данной концентрации вдоль направления диффузии может быть рас-
считана по уравнению [23]
Xt t, |
(6.7) |
где Xt – глубина границы заданной концентрации Сx за время t;
– константа проникновения.
285
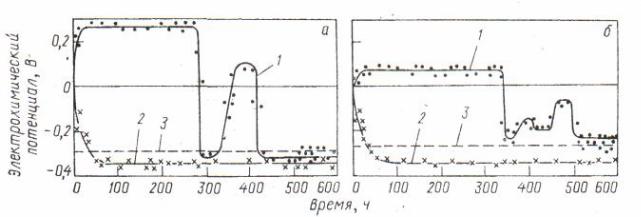
В общем случае время защитного действия покрытия складыва-
ется их нескольких составляющих [23]:
защ 1 2 3 , |
(6.8) |
где 1 – время непроницаемости покрытия, характеризующееся неста-
ционарным переносом среды в материал;
2 – время накопления среды в покрытии, характеризующееся стационарным переносом среды;
3 – время достижения недопустимых изменений на защищаемой поверхности.
Работоспособность защитного покрытия, как правило, определя-
ется первым слагаемым уравнения (6.8). В этом случае достаточно зафиксировать время контакта среды и подложки, на которую нане-
сено покрытие. Для этих целей может быть использован электрохи-
мический метод, который заключается в измерении величины потен-
циала, возникающего на межфазной границе «подложка – покрытие»
[17, 36]. При проникновении агрессивной среды через полимерное покрытие к подложке (в момент контакта) наблюдается скачкообраз-
ное изменение значения электрохимического потенциала в отрица-
тельную сторону (рис. 6.6).
Рис. 6.6. Зависимость электрохимического потенциала покрытия (1), металла (2) и покрытия с дефектом (3) от продолжительности выдержки образца в 5,0%-ном растворе серной кислоты; покрытие из смолы ПН-16 (а) и ЭД-20 (б)
286
Непостоянство электрохимического потенциала в начальный период контакта агрессивной среды с подложкой можно объяснить небольшим количеством проникшего к подложке электролита. В дальнейшем количество электролита увеличивается, повышается надежность его контактирования с подложкой, в результате этого стабилизируется значение электрохимического потенциала в системе «подложка – полимер – среда». Необходимо отметить, что момент резкого изменения электрохимического потенциала системы характеризуется изменением вида кинетической кривой сорбции. Визуальные наблюдения за состоянием поверхности подложки после извлечения образцов из раствора агрессивной среды свидетельствует о наличии следов коррозии в виде пятен. Повышения информативности этого метода можно добиться путем предварительной поляризации образца.
Для исследования лакокрасочных покрытий может использоваться импедансный метод, не оказывающий разрушающего действия на испытуемую систему. Обычно импедансным методом пользуются при исследовании неэлектропроводных покрытий, однако он применим и для электропроводных покрытий. Наиболее хорошие результаты этот метод дает при исследовании тонкослойных покрытий, для которых возможно применение простых эквивалентных схем заме-
щения (рис. 6.7) [22, 23].
Качество покрытия может быть оценено по активной составляю-
щей импеданса Ra . Для этого необходимо собрать установку, пред-
ставленную на рис. 6.8, и выполнить расчет по формуле (6.9):
|
( |
Uи |
Cos 1)2 ( |
Uи |
)2 Sin2 |
|
||||
|
|
|
|
|||||||
|
Ra |
Uш |
|
|
Uш |
|
Rш , |
(6.9) |
||
|
|
|
Uи |
Cos 1 |
|
|||||
|
|
|
|
|
|
|
|
|
||
|
|
|
|
Uш |
|
|
|
|||
где Rш |
– сопротивление шунта; |
|
|
|
||||||
Uи |
– напряжение, подаваемое с генератора сигналов; |
|
||||||||
Uш |
– падение напряжения на шунте; |
|
– угол сдвига фаз.
287

Рис. 6.7. Эквивалентные схемы, имитирующие сопротивление
иемкость покрытий:
а– свободная пленка в электролите; б, в – пленка покрытия на металле; R2 – сопротивление слоя, пропитанного средой; R1 – сопротивление слоя, не пропитанного средой; С1 – емкость, создаваемая пленкой, перегораживающей проникновение электролита; С1,2 – емкость, создаваемая пленкой после проникновения среды к металлу
Рис. 6.8. Схема экспериментальной установки:
1 – генератор звуковых сигналов; 2 – осциллограф; 3 – измерительная ячейка; 4 – цифровые вольтметры; 5 – шунтирующее сопротивление Rш
288