
Химсопрмат
.pdfТогда при заданной концентрации среды будет существовать верхнее критическое напряжение крв , выше которого (область I) v vадс vкр , т. е. долговечность материала в агрессивной среде и на воздухе одинакова. В области средних напряжений (область II) роль vадс и vхим становится решающей, и долговечность резко снижается под действием среды. При малых напряжениях (область III) снова изменяется вид зависимости; это вызвано, очевидно, тем, что ско-
рость процесса термофлуктуационного накопления повреждений стремится к нулю.
Долговечность в области II хорошо описывается уравнением
|
' |
|
' |
U' |
' |
|
|
|
|
|
|
|
|
exp |
0 |
|
C |
, |
(6.17) |
|
0 |
|
RT |
||||||
|
|
|
|
|
|
|
|
где ' , 0' , U0' , ' – те же параметры, что и в уравнении С.Н. Журкова,
характеризующие температурно-силовую зависимость долговечности в агрессивной среде;
C– концентрация агрессивной среды;
– коэффициент.
Решение уравнений (6.15) и (6.17) относительно напряжения дает зависимость для определения расчетного сопротивления конструкци-
онных неметаллических материалов:
|
|
|
1 |
|
|
|
c |
|
|
на воздухе |
|
|
RT |
|
|
; |
|||
дл |
|
|
|
||||||
U0 |
0 |
|
|||||||
|
|
|
|
|
|
|
|
|
1 |
|
|
|
|
' |
|
|
|
в агрессивной среде ' |
|
U' |
RT ln |
c |
C |
, |
||||
|
|
' |
||||||||
дл |
|
|
' |
0 |
|
|
|
|
||
|
|
|
|
|
|
0 |
|
|
где c , c' – срок службы конструкции.
299
Данные уравнения позволяют проводить выбор расчетного сопротивления для создания изделий с требуемым уровнем надежности.
Совместное решение уравнений (6.15) и (6.17) позволяет устано-
вить значение напряжения крв (см. рис. 6.10), при котором наблюда-
ется отклонение температурно-силовой зависимости долговечности в среде от соответствующего значения на воздухе:
в |
|
U0 U0' |
|
ln 0 ln 0' |
RT |
|
RTC. |
(6.18) |
' |
' |
|
||||||
кр |
|
|
|
' |
|
Вид нагружения учитывается величиной структурночувствительного параметра, а масштабный фактор – показателем однородности материала.
Долговечность при циклическом нагружении обычно меньше, чем при статическом. При знакопеременных нагрузках долговечность меньше, чем при одностороннем циклическом нагружении. С увеличением частоты циклов долговечность уменьшается. Усталостные свойства характеризуются чаще всего числом циклов до разрушения или определяются по снижению какой-либо характеристики после заданного времени воздействия циклической нагрузки.
Особо опасным эффектом от совместного воздействия на полимерный материал агрессивной среды и механических напряжений является коррозионное растрескивание, которое может происходить как за счет уже имеющихся в конструкции трещинообразных дефектов, так и за счет дефектов, возникающих при непосредственном контакте агрессивной среды с напряженным полимером. Этот вид разрушения может наблюдаться даже в инактивных средах, которые на ненапряженный полимер практически не действуют.
Трещиностойкость полимерных материалов в агрессивных средах оценивается по времени до появления микротрещин на поверхности образца и по напряжению растрескивания при постоянной деформации или других режимах нагружения. В настоящее время для
300
описания растрескивания полимерных материалов стали успешно применяться методы линейной механики разрушения.
6.5. Прогнозирование работоспособности
оборудования из неметаллов и долговечности
полимерных покрытий
Применение полимерных материалов в технике защиты от корро-
зии является одним из эффективных мероприятий, направленных на повышение надежности изделий, снижение их материалоемкости и, в
конечном итоге, на уменьшение коррозионных потерь. Применение полимерных материалов развивается по двум самостоятельным на-
правлениям [23]:
1) защита металлических конструкций полимерными (в том чис-
ле лакокрасочными) покрытиями; 2) создание изделий из коррозионно-стойких конструкционных
материалов на полимерной основе.
Широкое применение полимерных материалов сдерживается не-
удачными случаями их использования, однако необходимо помнить,
что не бывает плохих материалов, а бывают некачественные изделия,
причина появления которых кроется в следующем:
в ошибочном выборе того или иного материала;
в нерациональном конструировании изделия;
в неудовлетворительной технологии изготовления;
в нарушении условий эксплуатации.
Располагая надежными методами прогнозирования работоспо-
собности объектов, можно оптимизировать выбор материалов для конкретных изделий, более рационально конструировать изделия, оп-
301
ределять целесообразные условия эксплуатации объектов из поли-
мерных материалов и материалов с защитными покрытиями, объек-
тивно оценивать срок службы и контролировать работоспособность объектов в процессе эксплуатации.
При прогнозировании осуществляется решение двух практически важных задач [22, 23]:
1) на заданный срок службы создается объект, соответствующий функциональному назначению, и устанавливаются предельно допус-
тимые изменения эксплуатационных параметров этого объекта; 2) по установленным величинам допустимых изменений эксплуа-
тационных параметров объекта оценивается срок его службы.
Первая задача прогнозирования носит активный характер, так как она решается на стадии создания объекта и направлена на обеспече-
ние его работоспособности в течение установленного срока. Вторая задача прогнозирования пассивна, она решается применительно к уже функционирующему объекту и направлена на контроль его работо-
способности.
Прогнозирование срока службы базируется на определении того,
какие свойства полимерного материала или готовой конструкции и под действием каких факторов будут изменяться во времени. Одной из важнейших задач прогнозирования является установление количе-
ственных взаимосвязей фундаментальных свойств материала с экс-
плуатационными свойствами изделия.
В настоящее время наибольшее применение находят полуэмпи-
рические методы, основанные на феноменологических подходах; при этом сложный процесс разрушения представляется в виде упрощен-
ной модели, которая достаточно подробно исследована.
В общем случае срок службы емкости, например для воды, при воздействии механических напряжений будет определяться как
302
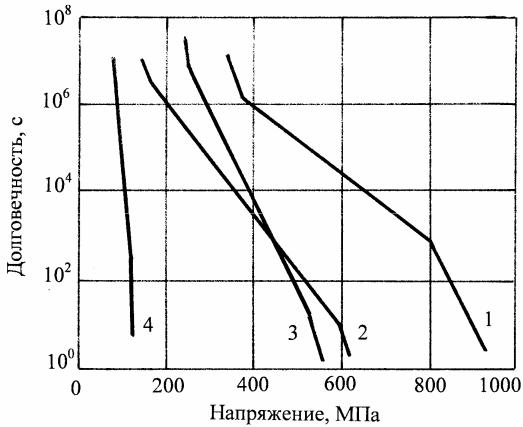
меньшее значение из двух величин: долговечности или времени
непроницаемости н . Воспользуемся экспериментальными данными
по долговечности (рис. 6.11) и параметрам переноса.
Рис. 6.11. Долговечность различных полимерных материалов:
1 – АГ-4с при изгибе в H2SO4 ; 2 – то же при растяжении; 3 – электропроводного стеклопластика при изгибе в воде; 4 – ДГ-2 при сжатии в H2SO4 при 20 С
Представленные на рис. 6.11 результаты испытаний хорошо кор-
релирут с приведенным ранее уравнением типа уравнения Журкова.
Наиболее общими характеристиками процесса разрушения являются термоактивационные параметры U0' и ' . Их применение позволяет в значительной мере отказаться от детального изучения механизма раз-
рушения материала. Представленные экспериментальные данные свидетельствуют о том, что кривые долговечности в агрессивных средах являются стадийными.
303
Определение н возможно по результатам изучения кинетики
проникновения агрессивной среды в ненапряженный и напряженный материал. Для приведенных материалов процессы переноса в нена-
пряженный материал описываются законами активированной диффу-
зии, а величины коэффициентов диффузии приведены в табл. 6.3.
Свойства некоторых материалов |
Таблица 6.3 |
||||
|
|||||
|
|
|
|
|
|
Материал |
D 10 |
15 |
2 |
/с |
m 10 15 , |
|
, м |
м2/с∙МПа |
|||
|
|
|
|
|
|
|
|
|
|
||
АГ-4с |
0,32 |
|
0,025 |
||
ДГ-2 |
7,5 |
|
|
0,033 |
|
|
|
|
|
|
|
Электропроводный стеклопластик |
5,4 |
|
|
0,047 |
|
|
|
|
|
|
|
С помощью полученных коэффициентов время непроницаемости рассчитывается по уравнению (6.16):
|
|
|
L2 |
, |
(6.19) |
|
н |
kD |
|||||
|
|
|
|
где L – толщина.
Величина коэффициента диффузии D определяется структурой материала и природой среды, а также зависит от температуры и кон-
центрации среды. Зависимость D от температуры с достаточной для практических целей точностью описывается уравнением Аррениуса.
В области низких напряжений коэффициентD меняется незначитель-
но, и в расчетах может применяться величина, полученная для нена-
пряженных материалов. Величина коэффициента диффузии в напря-
женный материал Dн зависит от вида напряженного состояния и уровня приложенных напряжений и в первом приближении может
определяться зависимостью |
|
Dн D m кр , |
(6.20) |
304
где m – эмпирический коэффициент, зависящий от природы среды,
материала и от вида нагружения;
кр – критическое напряжение, соответствующее первому пере-
гибу кривых lg (см. рис. 6.11).
Данная методика позволяет на научной основе прогнозировать срок службы полимерной аппаратуры.
В качестве примера проведем расчет срока службы плоского днища емкости для воды из электропроводного стеклопластика толщиной 1,0 мм при действии изгибающих напряжений величиной 250 МПа. Из рис. 6.10 долговечность материала составляет 107 с,
или 0,32 года, а время непроницаемости н по данным табл. 6.3 со-
ставляет 3∙107 с, или 0,95 года. Следовательно, срок службы определяется долговечностью и составляет 0,32 года. При уровне напряжений 240 МПа долговечность составит 5∙107 с, или 1,6 года, т.е. срок службы будет определяться временем непроницаемости и составит
0,95 года.
Методология прогнозирования долговечности полимерных покрытий определяется, прежде всего, правильностью выбора критериев оценки, уровнем экстраполяции результатов лабораторных испытаний и точностью выбранных моделей.
Основное функциональное назначение защитных покрытий заключается в создании препятствия непосредственному контакту агрессивной среды с конструкционным материалом. Дополнительными функциями могут являться антиадгезионные, противоэрозионные и др.
В общем случае долговечность конструкции с защитным покры-
тием п складывается из времени непроницаемости покрытия н ,
времени воздействия проникшей среды до нарушения адгезионной прочности и целостности покрытия а , допустимого времени экс-
плуатации незащищенной конструкции к .
Слагаемое н определяется так же, как и для объекта, целиком из-
готовленного из неметаллического материала.
305
Если при оценке долговечности защитных покрытий влияние проницаемости и химической стойкости изучено достаточно полно,
то оценка роли адгезионной прочности менее ясна. Адгезионная прочность полимерных покрытий должна рассматриваться с учетом диффузии среды; при этом возможны три случая.
Для первого из них, когда диффузия через покрытие незначи-
тельна, характерно сохранение исходной адгезионной прочности в течение длительного периода, и второе слагаемое а вносит значи-
тельный вклад в долговечность покрытия. При резком уменьшении адгезионной прочности и отслаивании покрытия от подложки (второй случай) величиной а можно пренебрегать. И, наконец, когда наблю-
дается неинтенсивное снижение адгезионной прочности при воздей-
ствии на покрытие агрессивных сред, слагаемые н и к становятся сравнимыми и должны учитываться в расчетах.
Эксплуатация конструкции с поврежденным покрытием обычно не допускается или допускается кратковременно, и слагаемое к не учитывается. При необходимости величина к может быть найдена по скорости коррозии металлов.
Таким образом, при оценке долговечности защитных покрытий применительно к противокоррозионной защите основными критериями являются прочность и деформируемость, химическая стойкость, проницаемость и адгезионная прочность. Наиболее правильным можно считать комплексный подход с использованием нескольких критериев оценки.
6.6. Коррозионно-стойкое оборудование из неметаллических материалов
В нефтедобывающей промышленности оборудование из неметаллических материалов пока не получило достаточно широкого применения, хотя можно отметить использование винипласта, фторопласта, стеклопластиков и бипластмасс [22, 23, 33].
306
Сосуды из винипласта изготавливают путем формования отдельных элементов с последующей сваркой или склеиванием. Сварка винипласта основана на том, что при температуре 220-240 °С и небольшом давлении отдельные части из данного материала способны соединяться. Пресс-формы изготавливают из металла или дерева. При изготовлении днищ из тонких листов винипласта также применяется вакуумное формование.
Сварка может производиться с помощью газовой горелки, которой одновременно разогреваются свариваемые кромки и присадочный пруток. Кромки свариваемых листов предварительно разделываются. Качество сварных соединений проверяется в процессе сварки визуально. Качественная сварка характеризуется легким закипанием прутка и материала при их контакте [23].
Для получения хорошего качества склейки соединяемые поверхности подвергают дробеструйной обработке.
Аппараты из винипласта изготавливают диаметром до 1400 мм для работы при температуре от 0 до 40 °С. При конструировании и изготовлении аппаратов из винипласта необходимо увеличивать жесткость деталей, работающих на изгиб, особенно в местах сварки, путем приварки ребер жесткости.
Широко применяют в промышленности также насосы, вентиляторы, трубопроводы и другое оборудование из винипласта [22, 23].
Химически стойкую аппаратуру, ее детали и узлы изготавливают из фторопласта прессованием с последующим спеканием или механической обработкой на станках из спеченных полуфабрикатов. Из фторопласта производят емкостную и теплообменную аппаратуру, насосы и мешалки, отличающиеся высокой химической стойкостью.
Аппаратура из стеклопластиков находит все более широкое применение, так как обладает высокой химической стойкостью и удельной прочностью, сравнимой с металлами. В зависимости от назначения изделий из стеклопластиков и предъявляемых к ним требований применяют определенные связующие и армирующий наполнитель
[23, 33].
307
Изделия из стеклопластиков можно получать из предварительно подготовленных композиций переработкой их различными методами (прессование, формование), а также, в отличие от других материалов, при непосредственном контактировании основных составляющих этих композиций в процессе производства изделий [23]. В первом случае имеется в виду материал, который легко транспортируется и пригоден для переработки в изделия в течение строго регламентируемого периода (например, фенолоформальдегидный стеклопластик АГ-4с), а во втором – только компоненты (синтетическая смола, отвердитель, пластификатор, армирующий наполнитель и др.), образующие стеклопластик в виде изделия в процессе его производства.
Процесс производства изделий из стеклопластиков сводится к послойному нанесению на форму стекловолокнистого материала, одновременно пропитываемого связующим. В качестве стеклонаполнителей применяют ткани различного плетения (полотняного, диагонального, саржевого и т. п.), нетканые материалы (стекломаты) или нити и жгуты. От вида армирующего наполнителя и способа его укладки зависит прочность получаемого материала [33].
Можно получать крупногабаритные изделия с применением несложной и дешевой оснастки и сравнительно простой технологии.
При ручном способе изготовления крупногабаритной емкостной аппаратуры обычно применяют стеклоткань, стеклохолст и стеклоро-
гожку, раскроенные на заготовки. Заготовки погружают в ванну со связующим, укладывают на форму с перекрытием стыков на 20-25 мм и прикатывают роликом. Связующее можно наносить на заготовки из пульверизатора. Этот процесс возможен только для тех связующих,
которые могут отверждаться при нормальной температуре в течение периода, необходимого и достаточного для формования изделия.
Процесс формования изделий из стеклохолстов аналогичен про-
цессу получения изделий из стеклотканей. Стекломаты можно укла-
дывать в форму также несколькими слоями с обязательной послойной пропиткой связующим.
308