
- •4. Электромагнитное порошковое сцепление
- •5.2. Особенности конструкций сцеплений с периферийными пружинами
- •5.5. Сцепление с автоматической компенсацией износа накладок
- •2 Мс Jдв Jn ωм
- •4 G b4 ƒ
- •7.4. Рычаги выключения сцепления
- •7.5. Кожух сцепления
- •7.6. Картер сцепления
- •I. Решение для случая постоянной работы автомобиля с прицепом:
- •II. Решение для случая эксплуатации одиночного автомобиля:
7.4. Рычаги выключения сцепления
Рычаги выключения сцепления изготавливают из ковкого чугуна или малоуглеродистой стали и обычно устанавливают на игольчатых подшипниках с целью уменьшения трения и повышения КПД привода сцепления.
Наибольшему изнашиванию подвержены внутренние концы рычагов. Для предотвращения изнашивания к рычагам может прикрепляться упорное кольцо, в которое упирается выжимной подшипник муфты выключения сцепления. На рычаги действует изгибающий момент от силы Р, которая приложена к внутренним концам рычагов (рисунок 7.11). Этот момент вызывает напряжения изгиба в опасном сечении рычага:
Рпр.в ƒ ℓ σи = ────── ≤ [σ]и , е zр Wизг
где Рпр.в – суммарная сила от нажимных пружин при выключенном сцеплении (Рпр.в = 1,2 P∑); ℓ –
расстояние до опасного сечения; е и ƒ – плечи рычага; zр – число рычагов; Wизг – момент сопротивления изгибу одного рычага.
Для рычагов из стали допускаемое напряжение изгиба [σ]и = 140…160 МПа, из ковкого чугуна – [σ]и = 60…80 МПа.
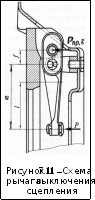
7.5. Кожух сцепления
Кожух сцепления должен иметь достаточную жесткость, его штампуют из малоуглеродистых сталей марок 08 или 10, толщиной листа 2,5…5,0 мм. Для отвода теплоты от нагретых деталей сцепления в кожухе делают специальные вырезы и окна, которые обеспечивают интенсивность циркуляции воздуха. Кожух центрируется с маховиком двигателя с помощью установочных штифтов, центрирующим бортиком на маховике или болтами, которыми прикрепляется к маховику.
7.6. Картер сцепления
Картер сцепления устанавливается и закрепляется на заднем торце блока цилиндров двигателя. У сцеплений грузовых автомобилей он отливается из чугуна, у сцеплений легковых автомобилей – из алюминиевого сплава. Он имеет замкнутую колоколообразную форму, существенно повышающую его жесткость, что обеспечивает в эксплуатации соосность коленчатого вала двигателя и первичного вала коробки передач. В картере выполняют вентиляционные окна, которые закрываются металлическими сетками. Окна обеспечивают циркуляцию воздуха внутри картера и отвод теплоты от рабочих поверхностей деталей сцепления.
8. Привод сцепления
Привод сцепления предназначен для осуществления связи между педалью управления и муфтой выключения сцепления. К нему предъявляются следующие требования: удобство и легкость управления, высокий КПД (минимальные потери на трение), наличие следящего действия, безотказность и долговечность, простота в обслуживании.
Для удобства и легкости управления ГОСТ 21398 устанавливает:
допускаемое усилие на педаль при полном выключении сцепления [Рп] = 147 Н – для легковых автомобилей и грузовых автомобилей с усилителем и 245 Н – для грузовых автомобилей без усилителя;
допускаемый полный ход педали управления при выключении сцепления [Sп] = 150 мм для легковых и 180 мм – для грузовых автомобилей.
Полный ход педали управления складывается из свободного ее хода (до начала сжатия рабочих пружин, когда устраняются зазоры в приводе с учетом допустимого износа фрикционных накладок) и рабочего хода (до полного выключения сцепления). Свободный ход педали управления в основном определяется зазором (δ) между выжимным подшипником муфты выключения 2 и концами рычагов выключения сцепления 1 (рисунки 8.1, а и б), между выжимным подшипником 4 и муфтой нажимных рычагов 5 (рисунок 8.1, г), либо между пятой 3 рычагов выключения и упорным подпятником 4 (рисунок
8.1, в).
-
в)
Рисунок 8.1 – Схемы конструк
г)
ций муфт выключения сцеплений:
– рычаг выключения сцепления;
– выжимной подшипник муфты выключения сцепления; 3 – пята
рычагов выключения сцепления;
4 – упорный подпятник; δ – зазор
– упругий нажимной рычаг;
– нажимной диск; 3 – опорный фланец ;
4 – выжимной подшипник муфты выключения сцепления; 5 – муфта нажимных рычагов; δ – зазор
Приводы бывают механические, гидравлические и электрические (электропневматические и электрогидравлические), а также автоматические и неавтоматические.
Механический привод (см. рисунок П.5) наиболее простой по конструкции, дешевый и достаточно безотказный в работе, однако имеет низкий КПД, плохо приспособлен к дистанционному управлению, передает вибрации от двигателя на педаль управления, а также при нем затруднены герметизация кузова (кабины) автомобиля и обеспечение плавности включения сцепления. В настоящее время механический привод применяется редко, за исключением его разновидности – тросового привода (рисунок 8.2), который находит все большее распространение на легковых автомобилях. Тросовый привод имеет минимальную массу, приспособлен к дистанционному управлению, позволяет герметизировать кузов, прост в эксплуатации, обеспечивает близкую к характеристикам гидравлического привода плавность включения сцепления. Новая технология изготовления оболочки троса, покрытой полимерными материалами изнутри и снаружи, обеспечивает малый коэффициент трения и высокий КПД.
-
Рисунок 8.2 – Схема тросового привода управления сцеплением
Гидравлический привод (рисунки 8.3 и 8.4) приспособлен к дистанционному управлению сцеплением, имеет высокий КПД, обеспечивает герметизацию кузова (кабины) автомобиля и хорошие условия размещения педали управления, которая делается подвесной.
Гидропривод позволяет ограничить скорость перемещения нажимного диска даже при резком включении сцепления, что дает возможность снизить динамические нагрузки в трансмиссии. Однако гидропривод сложнее по конструкции и в обслуживании, менее надежен в работе, более дорогостоящий и требует бóльших затрат в эксплуатации.
а) |
б) |
Рисунок 8.3 – Схемы гидравлических приводов управления сцеплением: а – непосредственное воздействие на муфту выключения сцепления; б – воздействие на муфту выключения сцепления через рабочий цилиндр и рычаг выключения сцепления (классическая схема) |
Гидравлический привод (рисунок 8.4) состоит из подвесной педали 1, главного цилиндра 3 с расширительным бачком 6 и рабочего цилиндра 8.
Подвешенная на пальце педаль 1 снабжена возвратной и усилительной пружинами. Усилительная пружина, соединенная через крючок с верхним плечом педали, уменьшает усилие на педаль при выключении сцепления.
Исходное положение педали фиксируется ограничителем хода педали.
В главном цилиндре 3 установлен рабочий поршень 5 и поршень толкателя 4 с упорным гнездом. В выточке поршня сделаны перепускные отверстия и поставлен кольцевой плавающий клапан. Поршни отжимаются пружиной до упора в стопорное кольцо корпуса главного цилиндра. В торец корпуса ввернута пробка. В углубление гнезда поршня толкателя 4 входит конец толкателя 2, образуя между ними зазор 0,1…0,5 мм, необходимый для гарантированного возвращения рабочего поршня в исходное положение.
Толкатель 2 соединен с педалью 1 управления сцеплением.
Полость цилиндра сообщается через компенсационное и перепускное отверстия со штуцером, закрепленным в корпусе стопорной шайбой. Штуцер соединен шлангом с бачком 6. Полости главного 3 и рабочего 8 цилиндров соединены трубопроводом 7.
-
Рисунок 8.4 – Схема гидравлического привода сцепления (типа ВАЗ-2101): 1 – педаль; 2 – толкатель; 3 – главный цилиндр; 4 – поршень толкателя; 5 – поршень главного цилиндра; 6 – бачок; 7 – трубопровод; 8 – рабочий цилиндр; 9 – поршень; 10 – пружина; 11 – вилка; 12 – опора вилки; 13 – муфта выключения сцепления с выжимным подшипником
Рабочий цилиндр 8 закреплен на картере сцепления. В цилиндре перемещается поршень 9, уплотненный двумя резиновыми кольцами. В цилиндр ввернут вентиль для прокачки гидросистемы. В углубление поршня входит шток, соединенный с концом рычага выключающей вилки 11 сцепления регулировочной гайкой с шаровой опорой, застопоренной контргайкой. Шток закрыт защитным резиновым чехлом.
Пока педаль не нажата, муфта выключения сцепления 13 удерживается оттяжной пружиной 10 в исходном положении, обеспечивая между выжимным подшипником и фрикционным кольцом упорного фланца выключения сцепления зазор 2 мм, необходимый для компенсации износа фрикционных накладок в процессе эксплуатации автомобиля.
При нажатии на педаль 1 рычаг вилки 11 с помощью гидропривода поворачивается и перемещает вперед муфту 13, которая через выжимной подшипник воздействует на упорный фланец выключения сцепления и лепестки диафрагменной пружины. При отпускании педали сцепление вновь включается. В случае быстрого отпускания педали и быстрого перемещения поршня 5 в главном цилиндре в исходное положение его кольцевой клапан, смещаясь вперед, открывает перепускные отверстия в головке поршня, и жидкость через них проходит в нагнетательную полость цилиндра, устраняя возникающее в ней разряжение.
В рассматриваемом приводе регулируют полный ход педали сцепления (140 мм), который определяет необходимую величину хода толкателя главного цилиндра, и свободный ход (20…30 мм), который необходим для выбора зазоров между концом толкателя 2 и гнездом поршня толкателя 4 и между выжимным подшипником муфты 13 и упорным фланцем выключения сцепления (если зазор имеется). При недостаточном ходе толкателя главного цилиндра или большом зазоре между выжимным подшипником и упорным фланцем сцепление не будет полностью выключаться, что затруднит переключение передач (сцепление «ведет»). При отсутствии зазора между выжимным подшипником и упорным фланцем сцепление будет неполностью включаться, что приведет к постоянному его буксованию. Полный ход педали регулируют винтом ограничителя хода педали, а свободный ход – изменением положения регулировочной гайки штока рабочего цилиндра.
Для облегчения управления сцеплением (уменьшения усилия на педаль управления) в приводах при необходимости применяют механические усилители в виде сервопружин (см. рисунок 8.4), которые уменьшают усилие выключения сцепления на 20…40 %, а также пневматические (см. рисунок П.5) или гидропневматические (см. рисунок П.6) усилители. Приводы сцепления с пневматическими и гидропневматическими усилителями, в которых
механические элементы (тяги, рычаги, штанги) или гидравлические магистрали выполняют только функции управления, называют пневмомеханическими (см. приложение 5) или гидропневматическими (см. приложение 6), соответственно. Порядок расчета привода управления сцеплением следующий:
Определяют рабочий ход нажимного диска при выключении сцепления (из расчета диафрагменной пружины):
hраб = (2∆н + ω) zд ,
где ∆н – зазор для новых накладок между поверхностями трения при полностью выключенном сцеплении; ω – осевая деформация ведомого диска; zд – число ведомых дисков.
Задают величину зазора ∆у между концами рычагов и муфтой (выжимным подшипником) выключения сцепления (рисунок 8.5):
∆у = 2…4 мм.
По мере износа накладок этот зазор уменьшается, поэтому в процессе эксплуатации его необходимо поддерживать для обеспечения полного включения сцепления.
Определяют передаточное число привода iпр.м и ход педали управления Sп Для механического привода (рисунок 8.5, а)
c2 b2 a2 iпр м = — — — c1 b1 a1 (обычно iпр.м = 30…45, a2 / a1 = 3,8…5,5);
Sп.м = hраб iпр + ∆у (с2 / с1) (b2 / b1),
где hраб iпр – определяет величину рабочего отхода нажимного диска,
∆у (с2 / с1) · (b2 / b1) – определяет выборку зазора ∆у. Для гидравлического привода (рисунок 8.5, б)
c2 b2 a2 (d2)2 iпр г = — — — ——
c1 b1 a1 (d1)2
(обычно d2 / d1 = 1,0);
Sп.г = hраб iпр.г + ∆у (с2 / с1) (b2 / b1) (d2 / d1)2.
Если полученный ход педали Sп.м или Sп.г не превышает [Sп], то переходят к следующему пункту расчета, иначе – изменяют передаточное число.
Определяют максимальное усилие на педаль управления:
Рп max = Рmax / iпр ηпр ,
где Рmax – максимальная сила, действующая на нажимной диск (определяют из расчета фрикционных накладок и нажимных пружин. Для диафрагменного сцепления Рmax = Рпр max); ηпр – КПД привода. Для механического привода ηпр = 0,5…0,8, для гидравлического – ηпр = 0,8…0,9.
Если Рп max > [Рп], необходимо ставить усилитель.
Определяют параметры усилителя.
Для примера, рассмотрим пневмоусилитель (рисунок 8.5, в). Так как водитель должен быть способен выключить сцепление и при неработающей пневмосистеме, то схема привода такая же, как и без пневмоусилителя. За расчетную принимаем максимальную силу, действующую на нажимной диск. В этом случае последовательность расчета должна быть следующей:
Вычисляют необходимую силу на штоке пневмоусилителя:
Рmax
Ршт = ———————— ,
(b2 / b1) (a2 / a1) ηсц
где ηсц = 0,9…0,95 – КПД механизма сцепления.
Определяют максимальную допускаемую силу, передаваемую на шток через гидросистему:
[Ргс] = [Рп] (с2 / с1) (d2 / d1)2,
где [Рп] = 147 Н.
Рассчитывают максимальную необходимую силу, развиваемую в цилиндре пневмоусилителя и передаваемую на шток:
Рц max = Ршт – [Ргс] + Рпр ,
где Рпр – максимальная сила, развиваемая пружиной возврата пневмоусилителя.
Вычисляют диаметр цилиндра пневмоусилителя
0 , 5 d3 = 2 (Рц max / π pw) ,
где pw – давление в ресивере (обычно pw = 0,65…0,75 МПа).
|
Рисунок 8.5 – Схемы механического (а), гидравлического (б) и гидравлического с пневмоусилителем (в) приводов сцеплений |
Следует отметить, что существенное значение для работы привода сцепления имеет время опорожнения цилиндра пневмоусилителя, которое напрямую связано со временем сжатия фрикционных накладок. Время истечения воздуха из пневмоусилителя должно составлять 0,4…0,5 с. При этом коэффициент динамичности
I kдин = Р∑ / Р∑ ≈ 1,0,
I
где Р∑ – максимальная сила сжатия фрикционных накладок.
При отсутствии пневмоусилителя время сжатия фрикционных накладок может сокращаться до 0,03 с, что вызывает увеличение kдин до 1,5, т.е. приводит к возрастанию динамических нагрузок в трансмиссии. В [1] предложено дополнительно определять и оценивать величину работы, совершаемой водителем при управлении сцеплением (при выключении и включении сцепления):
(Рпр + Рпр. в) (ƒв – ƒ)
Аус = ————————— ,
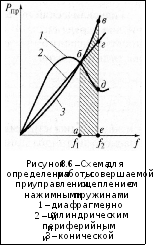
2 ηпр
где Рпр и Рпр.в – усилия нажимных пружин при включенном и выключенном положении сцепления; ƒ и ƒв – деформация пружин при включенном и выключенном положении сцепления; ηпр – КПД привода сцепления.
Работа Аус не должна превышать 25
Дж для легковых автомобилей и 30 Дж – для грузовых автомобилей и автобусов.
Схема для определения работы, совершаемой водителем при управлении сцеплением, приведена на рисунке 8.6. На схеме точка б соответствует включенному
сцеплению, а точки в, г и д –
выключенному.
Работа, совершаемая водителем при управлении сцеплением, соответствует заштрихованным площадям следующих фигур: абде – для сцепления с диафрагменной пружиной, абге – для сцепления с цилиндрическими периферийными пружинами, абве – для сцепления с конической пружиной.
На рисунке 8.6 видно, что наименьшая работа затрачивается водителем при управлении сцеплением с диафрагменной пружиной.
9. Тенденции развития систем управления сцеплениями
На большегрузных грузовых автомобилях и автопоездах сцепление передает значительный крутящий момент, поэтому на них применяют системы управления сцеплением с пневматическими или гидропневматическими усилителями. Эти системы относятся к классу автоматизированных. На их базе создаются системы полуавтоматического управления, где автоматизируется лишь процесс переключения передач [4].
Наиболее простой вариант полуавтоматического управления сцеплением – пневмомеханический привод 6 (рисунок 9.1) с пневмоусилителем 7 и дополнительным трехлинейным двухпозиционным электромагнитным клапаном 5, подключенным к атмосферному выходу распределительного клапана 4.
Команды на выключение и включение сцепления подает электронный блок (на схеме не показан). Так, чтобы выключить сцепление, блок подает электропитание на обмотку клапана 5, в результате чего открывается доступ воздуха из ресивера к распределительному клапану 4, а от него – в рабочую полость исполнительного цилиндра. Сцепление выключается. Чтобы включить сцепление, блок обесточивает обмотку клапана 5, благодаря чему рабочая полость исполнительного цилиндра по линии «клапан 4 – клапан 5» соединяется с атмосферой.
В системе сохранена возможность непосредственного управления сцеплением педалью 1. В этом случае темп его выключения и включения задает водитель. Кроме того, в схеме предусмотрена «скользящая» вилка 3, обеспечивающая независимую работу привода как при трогании автомобиля (автопоезда) с места, так и в процессе переключения передач.
Рисунок 9.1 – Схема полуавтоматического пневмомеханического привода сцепления:
1 – педаль управления сцеплением; 2 – система рычагов и тяг; 3 – «скользящая» вилка;
4 – распределительный клапан; 5 – двухпозиционный электромагнитный клапан;
6 – пневмомеханический привод; 7 – пневмоусилитель; 8 – исполнительный цилиндр сцепления
Гидропневматический привод (рисунок 9.2) по конструкции более сложный. В таком приводе для переключения передач должно изменяться давление в управляющей гидравлической магистрали 6, поэтому шток подпедального цилиндра 1 педали управления сцеплением 2 выполнен скользящим.
В другой схеме (рисунок 9.3) в управляющую магистраль пневмоусилителя 5 устанавливается гидропневмоцилиндр 1 релейного действия, который управляется электромагнитным клапаном 3. В этом случае не требуется доработка подпедального цилиндра 6, упрощается механизм передачи усилия от педали управления к пневмоусилителю и повышается КПД привода.
Приведенные схемы полуавтоматического управления сцеплением достаточно просты и позволяют с минимальными затратами дооборудовать обычный (неавтоматический) привод сцепления. С точки зрения функциональных возможностей они одинаковы. Однако пневмомеханический привод (см. рисунок 9.1) проще: во-первых, в нем нет сопряжений гидравлических и пневматических магистралей, что упрощает схему; вовторых, в режиме переключения передач непосредственная подача давления в рабочую полость исполнительного цилиндра исключает работу распределительного клапана 4, что упрощает предварительную настройку системы и снижает влияние работы клапана на переходный процесс переключения передач (педаль управления сцеплением в такой системе используется только при трогании автомобиля с места).
Рисунок 9.2 – Схема полуавтоматического гидропневматического привода сцепления:
1 – подпедальный цилиндр; 2 – педаль управления; 3 – двухпозиционный электромагнитный клапан; 4 – гидропневматический привод; 5 – пневмоусилитель; 6 – управляющая гидравлическая магистраль
Полуавтоматические системы с гидропневматическим приводом целесообразны для сочлененных транспортных средств, у которых двигатель расположен в задней части второго звена. В этом случае привод сцепления упрощается и повышается его КПД, снижается инерционность работы привода, связанная с деформацией тяг значительной длины и трением на осях вращения рычагов, а также трудоемкость его технического обслуживания, связанная с необходимостью периодического регулирования. Однако эти системы не лишены недостатков, связанных с большим числом подвижных механических элементов, трущихся пар и пружин гидропневмоаппаратов, а также значительными дроссельными потерями.
Рисунок 9.3 – Схема полуавтоматического гидропневматического привода сцепления: 1 – гидропневматический привод; 2 – педаль управления; 3 – гидропневмоусилитель релейного действия; 4 – электромагнитный клапан; 5 – пневмоусилитель; 6 – цилиндр подпедальный |
Рисунок 9.4 – Схема электропневматического привода сцепления: 2 – клапан впуска; 3 – клапан выпуска; 4 – подпедальный датчик; 5 – педаль управления; 6 – исполнительный цилиндр; 7 – датчик обратной связи; I и II (а и в) – входные (выходные) сигналы электронного блока управления |
В связи с этим, в последнее время находят все большее распространение системы управления сцеплением, базирующиеся на электроприводе. В таких системах сведено к минимуму число входящих в них гидропневмоаппаратов и существенно упрощена схема дистанционного управления сцеплением, что позволяет достичь малой инерционности систем управления.
Функции управления в такой схеме (см. рисунок 9.4) переданы электронному блоку управления, который по сигналам датчиков I и II вырабатывает наиболее рациональный закон управления сцеплением (выходные сигналы а и в). За пневмоаппаратурой остаются лишь силовые функции: клапаны 2 впуска и клапаны 3 выпуска подают или выпускают воздух из рабочей полости исполнительного цилиндра 6. При наличии электропневматического привода управления сцеплением водитель, воздействуя на педаль подачи топлива, задает скоростной режим движения автопоезда, а все функции по управлению сцеплением, выбору и переключению передач выполняет автоматика. Управление автопоездом становится двухпедальным. Одновременно повышается и долговечность самого сцепления, потому что оно всегда включается по наиболее рациональному закону управления.
Дальнейшим развитием систем управления сцеплением являются микропроцессорные системы автоматического управления сцеплением, которые позволяют полностью отказаться от педали управления. Как правило, они представляют собой составные части более общих систем – управления трансмиссией или силовой установкой автомобиля.
Система автоматического управления сцеплением состоит из измерительноинформационного блока, блока преобразования информации, электронного блока управления (ЭБУ), усилительного устройства, исполнительного механизма сцепления, устройства отображения информации и блока питания. Блок преобразования информации и усилительное устройство образуют устройство сопряжения.
Измерительно-информационный блок предназначен для выдачи информации о скорости движения автомобиля, положении педали подачи топлива, состоянии исполнительного механизма сцепления (датчик положения штока исполнительного цилиндра сцепления – датчик обратной связи), коробки передач (концевые выключатели передач), двигателя (датчик частоты вращения коленчатого вала). Работу автомобиля в целом этот блок отражает по датчику угловой скорости вторичного вала коробки передач.
Полученная от датчиков информация (сигналы) проходит блок преобразования информации, который обрабатывает сигналы и приводит их к удобному для работы ЭБУ виду. Задача ЭБУ – формирование требуемого закона изменения момента трения сцепления, а также контроль величины рассогласования рассчитанного параметра регулирования и параметра, фиксируемого датчиком обратной связи.
Далее ЭБУ выдает сигналы в усилительное устройство, откуда они идут в исполнительные механизмы (приводы) управления двигателем, коробкой передач и сцеплением. При этом гидравлические или пневматические исполнительные механизмы сцепления и коробки передач в процессе трогания автомобиля с места, движения с низкой скоростью при буксующем сцеплении, а также при переключении передач работают синхронно.
Функции по индикации режимов работы ЭБУ и состоянию системы автоматического управления сцеплением возложены на устройство отображения информации.
Блок питания имеет устройство стабилизации выходного напряжения, что необходимо для устойчивой работы всей системы при эксплуатации автомобиля.
Типичная для систем электрогидравлического автоматического и дистанционного управления сцеплением схема (рисунок 9.5), разработанная фирмой «Isuzu Motors», включает исполнительный механизм, который управляется быстродействующими электромагнитными клапанами впуска (1 и 2) и выпуска (3 и 4). Различия сводятся к типу, числу и размерам условных проходных сечений электромагнитных клапанов, которые могут быть двухлинейными двухпозиционными, двухлинейными трехпозиционными и трехлинейными трехпозиционными.
Варианты управления сцеплением следующие:
клапаны 3 и 4 закрыты, клапан 2 открыт, жидкость под давлением подается в рабочую полость исполнительного цилиндра 5, выключая сцепление;
клапаны 2, 3 и 4 закрыты, цилиндр 5 удерживает буксующее сцепление в заданном промежуточном положении;
клапан 2 закрыт, клапаны 3 и 4 открыты – сцепление включено.
Темп включения сцепления задается за счет импульсного способа подачи электропитания на обмотки клапанов 3 и 4, которые, открываясь и закрываясь с большой частотой, обеспечивают плавное включение сцепления, не допуская значительных колебаний давления в рабочей полости исполнительного цилиндра 5.
Как работает система
автоматического управления сцеплением можно рассмотреть на примере самого сложного из режимов – трогания автомобиля с места.
В этом режиме водитель, воздействуя на педаль подачи топлива, увеличивает частоту вращения коленчатого вала двигателя. Получив данный сигнал, блок управления дает команду на повышение длительности импульсов, проходящих через обмотки электромагнитных клапанов 3 и 4. В результате возрастает общая продолжительность открытого их состояния, и момент, передаваемый сцеплением, плавно нарастает, а автомобиль столь же плавно разгоняется. В момент, когда клапаны закрываются, сцепление полностью включается.
Реализацию закона управления сцеплением обеспечивают три программы:
первая – программа информационных параметров, необходимых для режимов переключения передач, плавного трогания с места и выдержки момента сцепления на заданном уровне при парковке автомобиля;
вторая – программа параметров импульсного регулирования электроклапанов, работающая на основе анализа информации, полученной с датчика обратной связи положения штока исполнительного цилиндра 5; - третья – программа, активизирующая клапаны 1, 2, 3 и 4.
Список литературы
Вахламов В.К. Автомобили: Конструкция и элементы расчета: учебник для студ. вузов. – М.: Изд. центр «Академия», 2008. – 480 с.
Вишняков Н.Н., Вахламов В.К., Нарбут А.Н. и др. Автомобиль. – М.: Машиностроение, 1976. – 296 с.
Двухмассовый маховик: Технологические решения. Диагностика неисправностей. Руководство компании «LuK», 2007. – 27 с.
Захарик Ю.М., Руктешель О.С., Ракомсин А.П. и др. Системы управления сцеплением. Тенденции развития // Автомобильная промышленность, 2003, № 1. С.13-15.
Иванов А.М., Солнцев А.Н., Гаевский В.В. и др. Основы конструкции автомобиля. – М.: ООО «Книжное издательство «За рулем», 2005. – 336 с.
Лукин П.П., Гаспарянц Г.А., Родионов В.Ф. Конструирование и расчет автомобиля. – М.: Машиностроение, 1984. – 376 с.
Проектирование полноприводных колесных машин: Учебник для вузов: В 3 т. Т.2 / Б.А. Афанасьев, Л.Ф. Жеглов, В.Н. Зузов и др.; Под ред. А.А.
Полунгяна. – М.: Изд-во МГТУ им. Н.Э.Баумана, – 2008. – 528 с.
Шарипов В.М. Конструирование и расчет тракторов: Учебник для студентов вузов. – М.: Машиностроение, 2009. – 752 с.
Приложение 1
Двухдисковое сцепление с периферийными пружинами
Рисунок П.1 – Двухдисковое сцепление с периферийными пружинами:
1, 22 – ведомые диски; 2 – средний ведущий диск; 4 – нажимной диск; 5 – вилка выключения сцепления; 6 – рычаг выключения сцепления; 10 – выжимной подшипник; 11 – оттяжная пружина; 12 – муфта выключения сцепления; 13 – вилка выключения сцепления; 14 – упорное кольцо; 16 – нажимная пружина; 17 – кожух сцепления;
18 – теплоизолирующая прокладка; 20 – картер сцепления; 21 – маховик; 23 – первичный вал
КП; 25 – пружина демпфера крутильных колебаний; 26 – фрикционное кольцо демпфера; 27 – механизм регулирования среднего ведущего диска
Приложение 2
Определение размеров фрикционных накладок для однодискового сцепления автомобиля КамАЗ-4310 (6х6)
Исходные данные. Полная масса автомобиля mа = 14940 кг; полная масса прицепа mпр = 7000 кг; ДВС – КамАЗ-740, дизельный; крутящий момент двигателя Ме mах = 650 Нм при nе М = 1600 мин–1; Nе mах = 155 кВт при nе N = 2600 мин–1; размер шин 1200х400–533; радиус качения rк = 0,582 м; передаточные числа: 1-й и 2-й передач в КП iк1 = 7,82 и iк2 = 4,03, высшей передачи в РК iрк в = 0,917, главной передачи iо = 7,22; КПД трансмиссии ηтр = 0,8; коэффициент сопротивления качению ψ = 0,03 (для сухой грунтовой дороги в удовлетворительном состоянии); коэффициент, характеризующий тип двигателя, h = 0,724; число ведомых дисков сцепления zд = 1 (число поверхностей трения z = 2).