
- •4. Электромагнитное порошковое сцепление
- •5.2. Особенности конструкций сцеплений с периферийными пружинами
- •5.5. Сцепление с автоматической компенсацией износа накладок
- •2 Мс Jдв Jn ωм
- •4 G b4 ƒ
- •7.4. Рычаги выключения сцепления
- •7.5. Кожух сцепления
- •7.6. Картер сцепления
- •I. Решение для случая постоянной работы автомобиля с прицепом:
- •II. Решение для случая эксплуатации одиночного автомобиля:
МИНИСТЕРСТВО ОБРАЗОВАНИЯ И НАУКИ РОССИЙСКОЙ ФЕДЕРАЦИИ
МОСКОВСКИЙ ГОСУДАРСТВЕННЫЙ
ТЕХНИЧЕСКИЙ УНИВЕРСИТЕТ «МАМИ»
А.В. Острецов
П.А. Красавин
В.В. Воронин
АВТОМОБИЛЬНЫЕ СЦЕПЛЕНИЯ
Учебное пособие
Допущено УМО вузов РФ по образованию в области транспортных машин и транспортно-технологических комплексов в качестве
учебного пособия для студентов, обучающихся по специальности
«Автомобиле - и тракторостроение»
Москва – 2011
УДК 629.113 – 578
Острецов А.В., Красавин П.А., Воронин В.В. Автомобильные сцепления:
Учебное пособие по дисциплинам «Конструкция автомобиля и трактора» и «Конструирование и расчет автомобиля» для студентов вузов, обучающихся по специальности 190201 «Автомобиле - и тракторостроение». – М.: МГТУ «МАМИ», 2011. – 99 с.
В учебном пособии изложены особенности конструкций автомобильных сцеплений, их приводов и стандартного двухмассового маховика. Даны классификация сцеплений и предъявляемые к ним требования. Приведены порядок расчета сцепления в целом и отдельных его деталей, а также примеры выбора параметров диафрагменной нажимной пружины и определения размеров фрикционных накладок ведомого диска. Даны тенденции развития систем управления сцеплением.
Рецензенты: Зав. кафедрой «Колесные и гусеничные машины» МГТУ «МАМИ», Засл. деятель науки РФ, д-р техн. наук, проф. ШАРИПОВ В.М.; Начальник отдела тяжёлых наземных комплексов НПЦ СМ МГТУ им. Н.Э.
Баумана, д-р техн. наук, проф. БЕЛОУСОВ Б.Н.
© ОСТРЕЦОВ А.В., КРАСАВИН П.А., ВОРОНИН В.В., 2011
© Издательство МГТУ «МАМИ», 2011
Содержание
Введение ............................................................................................................. 5
Классификация сцеплений ......................................................................... 8
Требования, предъявляемые к сцеплениям .......................................... 10
Гидравлическое сцепление (гидромуфта) ............................................... 11
Электромагнитное порошковое сцепление .............................................. 14
Конструкции фрикционных сцеплений ..………………………............ 16
Сцепление с диафрагменной нажимной пружиной ...………..........… 16
Особенности конструкций сцеплений с периферийными пружи- нами и центральной конической пружиной ...……………….................... 24
Полуцентробежное фрикционное сцепление ...................................... 27
Центробежное фрикционное сцепление .............................................. 29 5.5. Сцепление с автоматической компенсацией износа накладок
ведомого диска (система XTend) ............................................................... 31
Расчет сцепления ...……………………………………………….…….... 34
Определение расчетного момента трения сцепления ...….…........... 34 6.2. Определение работы Aб буксования сцепления, удельной рабо- ты Aуд буксования и температуры t0 деталей сцепления в процессе буксования ...…………………………………....................…................. 36
Конструирование и расчет деталей фрикционных сцеплений ……. 43
Нажимной и средний ведущие диски ...………………………......... 43
Ведомые диски ...……………………………………………..……... 44
Пружины ...………………………………………………………..…. 53
Рычаги выключения сцепления ...……………………………….…. 63
Кожух сцепления ......………………………………………….......... 63
Картер сцепления ..…………………………………………….…..... 64
Привод сцепления ...……………………………….....……………..….... 64
Тенденции развития систем управления сцеплениями ...….........…. 75
Список литературы ....................................................................................... 82
Приложение 1. Двухдисковое сцепление с периферийными пружинами ... 83 Приложение 2. Определение размеров фрикционных накладок для одно-
дискового сцепления автомобиля КамАЗ-4310 (6х6) ................................... 84 Приложение 3. Особенности конструкции стандартного двухмассового
маховика ............................................................................................................ 87
Приложение 4. Выбор параметров диафрагменной нажимной пружины вдавливаемого типа для однодискового сцепления автомобиля КамАЗ-
4310 (6х6) .......................................................................................................... 92
Приложение 5. Механический привод управления сцеплением с пневма-
тическим усилителем (пневмомеханический привод) ................................... 94
Приложение 6. Гидропневматический привод управления сцеплением …. 97
Введение
Сцепление предназначено для кратковременного разобщения коленчатого вала двигателя от трансмиссии и последующего их соединения, необходимого для осуществления плавного трогания автомобиля с места и переключения передач во время движения. Сцепление также служит для предохранения трансмиссии и двигателя автомобиля от перегрузок инерционными моментами.
Первые автомобили были оборудованы ленточными сцеплениями, в которых металлическая лента охватывала снаружи металлический барабан. Их особенность состояла в том, что в обычном положении они были постоянно выключены и включались путем перемещения рычага в определенное положение. Основным их недостатком была необходимость в использовании сложных регулировочных узлов, компенсирующих изнашивание рабочих поверхностей.
Появившиеся в дальнейшем конусные сцепления были постоянно включенными (рисунок 1). Маховик двигателя 2, являвшийся ведущим элементом сцепления, крепился к фланцу коленчатого вала и имел изнутри коническую поверхность. Соответствующую наружную коническую поверхность имел конус 9, являвшийся вместе с кожухом сцепления 7 ведомым элементом, который перемещался в осевом направлении по шлицам первичного вала коробки передач. Во включенном (рабочем) положении конус 9 с фрикционной накладкой 10 удерживались усилием пружины 8. Сцепление выключалось, когда водитель нажимал педаль сцепления 4 и через рычаг 5 и муфту выключения сцепления 3 сжимал пружину 8.
В конусных сцеплениях угол между поверхностью трения и осью конуса составлял 150. В последних конструкциях фрикционные накладки применялись из фрикционных материалов с асбестовой основой.
Главным недостатком конусных сцеплений был большой момент инерции ведомого элемента, в результате чего он долго вращался после выключения сцепления, затрудняя переключение передач.
Рисунок 1 – Конусное сцепление:
1 – фланец коленчатого вала; 2 – маховик; 3 – муфта выключения сцепления; 4 – педаль сцепления; 5 – рычаг выключения сцепления; 6 – вал сцепления; 7 – кожух сцепления; 8 – пружина; 9 – конус сцепления; 10 – фрикционная накладка
На смену конусным сцеплениям пришли многодисковые сцепления, работающие в масляной ванне. Они состояли из чередующихся стальных и бронзовых дисков, закрепленных на шлицах с ведомым и ведущим барабанами,
т.е. имели большое число поверхностей трения и обеспечивали высокую плавность включения. Однако ведомый барабан с многочисленными ведомыми дисками обладал большим моментом инерции, что в значительной степени затрудняло переключение передач. Кроме того, при отрицательных температурах окружающего воздуха масло густело, ведущие и ведомые диски слипались, и сцепление не выключалось. В дальнейшем такие сцепления нашли широкое применение в качестве дисковых фрикционных элементов управления в планетарных коробках передач, а также в качестве многодисковых муфт.
Дальнейшим развитием многодисковых сцеплений стали сухие многодисковые сцепления. Их ведущие диски снабжены накладками из фрикционного материала, приклепанного к дискам с обеих сторон. Эти сцепления могут передавать особо большой крутящий момент при относительно небольших размерах. Однако им присущ тот же недостаток – большой момент инерции ведомых частей. Кроме того, ведомые металлические диски, расположенные между фрикционными накладками, имеют небольшую толщину (не более 4 мм), обладают низкой теплопроводностью, сильно нагреваются при буксовании сцепления, что ускоряет износ накладок, а иногда приводит к короблению дисков и нарушению чистоты выключения сцепления.
Сухие однодисковые сцепления начали применяться с 1910 года и к середине 20-х годов прошлого века, благодаря присущим им преимуществам, получили всеобщее признание и практически вытеснили другие конструкции.
Классификация сцеплений
По способу передачи крутящего момента – фрикционные, гидравлические (гидромуфты) и электромагнитные порошковые.
Наибольшее распространение получили фрикционные сцепления, у которых крутящий момент от ведущих деталей, соединенных с коленчатым валом двигателя, передается на ведомые детали, соединенные с трансмиссией автомобиля, посредством сил трения. У гидравлических сцеплений (гидромуфт) связь ведущей и ведомой частей осуществляется движущимся потоком жидкости, а у электромагнитных порошковых – электромагнитным полем.
По форме поверхностей трения – дисковые, конусные и барабанные. В современных конструкциях автомобилей применяются только дисковые сцепления.
По числу ведомых дисков – одно-, двух- и многодисковые.
Двухдисковые сцепления (см. приложение 1) применяются на грузовых автомобилях. Их использование вызвано необходимостью передачи большого крутящего момента, что достигается путем увеличения площади поверхностей трения без увеличения диаметра сцепления. Они имеют относительно большие показатели массы, осевой габаритной длины и перемещения муфты выключения. Кроме того, в их конструкциях для обеспечения чистоты выключения требуется предусматривать принудительное перемещение среднего ведущего диска.
По состоянию поверхностей трения – сухие и мокрые (работают, соответственно, без смазки поверхностей трения и в масляной ванне). Одно- и двухдисковые сцепления применяются только сухими, а многодисковые, – в основном, мокрыми.
По возможности передачи крутящего момента при отсутствии внешнего управляющего воздействия – нормально замкнутые и нормально разомкнутые, причем последние применяются достаточно редко.
По способу создания давления на рабочих поверхностях сцепления – пружинные, центробежные и полуцентробежные.
В пружинных сцеплениях используются центральные диафрагменные, цилиндрические периферийно расположенные или, крайне редко, центральные конические пружины.
В центробежных и полуцентробежных сцеплениях сила сжатия пар трения полностью или частично обеспечивается за счет кинетической энергии грузиков, закрепленных на рычагах выключения сцепления. Центробежные сцепления применяются достаточно редко, что объясняется их большой стоимостью, меньшей надежностью и сложностью конструкции при реализации предохранительной функции сцепления. Полуцентробежные сцепления в настоящее время не применяются из-за присущих им недостатков (см. подраздел 5.3).
По числу силовых потоков мощности, передающихся через элементы сцепления – однопоточные, когда весь поток мощности от двигателя передается в трансмиссию, и двухпоточные, когда один поток мощности от двигателя передается в трансмиссию, а другой – на привод вала отбора мощности, или, когда мощность от двигателя передается в трансмиссию двумя параллельными потоками.
По способу управления:
сцепления с принудительным управлением, полностью управляемые водителем;
сцепления с автоматизированным управлением, которые снабжены автоматическими устройствами, обеспечивающими, как минимум, управление процессом трогания автомобиля с места;
автоматические сцепления (гидравлические и центробежные), обладающие внутренней автоматичностью, т.е. увеличивающие передаваемый крутящий момент с ростом частоты вращения коленчатого вала двигателя.
На подавляющем большинстве автомобилей установлены постоянно замкнутые сцепления с принудительным управлением.
Требования, предъявляемые к сцеплениям
Сцепление представляет собой самостоятельный механизм, к конструкции которого помимо общетехнических требований (простота конструкции, большой срок службы, малая масса, низкая трудоемкость технического обслуживания) предъявляются следующие специальные требования:
надежная передача крутящего момента от ведущих деталей сцепления к ведомым его деталям в любых условиях эксплуатации автомобиля;
возможность передачи крутящего момента в обратном направлении (от ведущих колес автомобиля к двигателю) при работающем или неработающем двигателе, что необходимо для торможения автомобиля двигателем, а также пуска двигателя буксированием автомобиля;
чистота выключения, т.е. быстрое (менее чем за 0,25 с) и полное разобщение поверхностей трения;
плавность включения (достигается обеспечением осевой и тангенциальной податливости ведомого диска);
возможность длительной работы со скольжением (буксованием), т.е. кинематическим рассогласованием между частотами вращения ведущих и ведомых элементов сцепления, которое необходимо для осуществления плавного трогания автомобиля с места, а также тонкого регулирования его скорости при маневрировании;
минимальный момент инерции ведомых элементов (необходим для быстрого снижения частоты вращения первичного вала коробки передач при переключении передач);
нормальный тепловой режим работы;
уравновешенность вращающихся масс (необходима для уменьшения динамических нагрузок в деталях сцепления при больших частотах вращения коленчатого вала двигателя);
предохранение трансмиссии и двигателя автомобиля от перегрузок инерционным крутящим моментом;
безотказность в работе;
легкость и удобство управления (оценивается усилием на педали управления и величиной ее хода при выключении сцепления).
Гидравлическое сцепление (гидромуфта)
В гидромуфте (рисунок 3.1) ведущее (насосное) колесо 3 вместе с корпусом 2 связано с коленчатым валом двигателя, а ведомое (турбинное) 1 – с трансмиссией. Колеса имеют форму тора, между наружной 5 и внутренней 6 частями которого расположены плоские радиальные лопатки 4. Корпус примерно на 90 % заполнен рабочей жидкостью – турбинным маслом малой вязкости. Турбинное колесо расположено предельно близко к насосному колесу.
При вращении насосного колеса кинетическая энергия жидкости, находящейся между его лопатками и движущейся под действием центробежных сил к периферии, передается турбинному колесу. Пройдя по его межлопаточным каналам, жидкость вновь попадает в насосное колесо. При достижении определенной частоты вращения турбинного колеса кинетической энергии становится достаточно для того, чтобы автомобиль тронулся с места. При дальнейшем повышении частоты вращения коленчатого вала двигателя оба колеса гидромуфты начинают вращаться практически с одинаковой скоростью.
Если угловые скорости вращения насосного ωн и турбинного ωт колес равны, то отсутствует движение рабочей жидкости, так как центробежные силы, развиваемые жидкостью в межлопаточном пространстве колес, взаимно уравновешиваются. Следовательно, для обеспечения работы гидромуфты необходимо соблюдать неравенство ωн ≠ ωт . Это означает, что при работе гидромуфты турбинное колесо всегда проскальзывает относительно насосного. При трогании автомобиля с места, когда угловая скорость турбинного колеса ωт = 0, проскальзывание будет наибольшим (100 %), а при установившейся работе оно составляет 2…3 % .
Рисунок 3.1 – Схема гидромуфты:
1 – турбинное колесо; 2 – корпус; 3 – насосное колесо; 4 – лопатки; 5 – наружная часть тора; 6 – внутренняя часть тора; 7 – клапаны заполнения; 8 – радиатор; 9 – клапан насоса предохранительный; 10 – насос; 11 – бак; 12 – клапаны опорожнения
Скольжение S определяется по формуле
S = (ωн – ωт) / ωн .
Характерным для гидромуфты является то, что она не изменяет величину крутящего момента при его передаче от двигателя к трансмиссии, т.е. Мн = Мт , где Мн = Мт – крутящие моменты на насосном и турбинном колесах,
соответственно.
В связи с этим, мощности на насосном и турбинном колесах не равны:
Nн = Мн ωн ; Nт = Мт ωт .
Таким образом, КПД гидромуфты
ηгм = Nт / Nн = ωт / ωн , а скольжение S = 1 – ηгм .
На рисунке 3.2 представлена внешняя характеристика гидромуфты. Это экспериментальная характеристика зависимости крутящего момента М, передаваемого гидромуфтой, ее КПД ηгм и скольжения S от отношения ωт / ωн при постоянной угловой скорости ωн вращения насосного колеса.
КПД гидромуфты не может быть равным единице, так как при равенстве угловых скоростей вращения насосного и турбинного колес гидромуфта не может передавать крутящий момент. Максимальный КПД гидромуфты составляет 0,97.
Гидромуфта по сравнению с фрикционным сцеплением имеет следующие
преимущества:
обеспечивает плавное трогание
автомобиля с места;
снижает динамические нагрузки в трансмиссии автомобиля и крутильные колебания двигателя в 1,5…4,0 раза на переходных режимах [8];
повышает устойчивость работы двигателя при низких скоростях движения (в пробках), так как допускает длительную
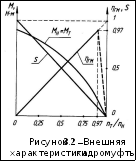
работу с большой пробуксовкой насосного и турбинного колес;
не требует регулировки в эксплуатации, так как детали гидромуфты практически не изнашиваются;
облегчает управление автомобилем;
повышает проходимость автомобиля.
Однако гидромуфта в качестве самостоятельного агрегата, выполняющего функции сцепления, не используется, так как при переключении передач для обеспечения выключения необходима система ее опорожнения, а для обеспечения включения – система заполнения. Эти системы (см. рисунок 3.1) включают клапаны опорожнения 12, бак 11, насос питания 10 с предохранительным клапаном 9, клапаны заполнения 7 и радиатор 8 для охлаждения жидкости [2]. Поэтому гидромуфта может применяться только вместе с обычным фрикционным сцеплением, которое устанавливается за ней последовательно и служит лишь для переключения передач. Это повышает сложность, металлоемкость и стоимость трансмиссии.
Кроме того, вследствие скольжения гидромуфты и нагрева рабочей жидкости снижается КПД передачи и увеличивается расход топлива.
4. Электромагнитное порошковое сцепление
Электромагнитное порошковое сцепление (рисунок 4.1) постоянно выключено и относится к сцеплениям с автоматизированным управлением, у которых педаль сцепления отсутствует. Оно получило некоторое распространение на автомобилях особо малого и малого классов. Сцепление состоит из трех основных частей: ведущей части 1, которой является маховик с прикрепленными к нему болтами магнитопроводами; присоединенного к картеру сцепления неподвижного корпуса 2 с запрессованным в него магнитопроводом с обмоткой возбуждения 3, и ведомой части 4 из немагнитного материала, передающей крутящий момент на первичный вал коробки передач. Части сцепления (магнитопровды) разделены воздушными зазорами А, Б и В. При отсутствии тока в обмотке возбуждения 3 между ведущей и ведомой частями сцепления силовой связи нет и сцепление выключено.
Когда к обмотке возбуждения подводится электрический ток, вокруг нее возникает замкнутый кольцевой магнитный поток, показанный стрелками. Магнитный поток проходит через зазоры А, Б и В, в результате чего силовое взаимодействие элементов сцепления ничтожно мало, но оно возрастает во много раз, если зазоры заполнить специальным ферромагнитным порошком, обладающим высокими магнитными свойствами. Этим порошком заполнен
зазор А между ведущей и ведомой частями сцепления.
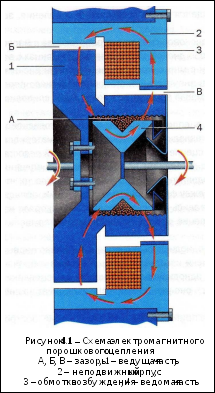
При прохождении магнитного потока через порошок его частицы притягиваются друг к другу и магнитопроводам ведущей и ведомой частей, создавая силовое взаимодействие между ними. Силовая связь зависит от силы тока в обмотке возбуждения. При малой силе тока сцепление пробуксовывает, что обеспечивает плавность трогания автомобиля. При увеличении силы тока буксование уменьшается до полной блокировки ведущих и ведомых частей и сцепление включается.
Основное достоинство
такой конструкции заключается в том, что управление сцеплением можно перенести с ножного (с педали сцепления) на ручной вариант управления.
Конструкции фрикционных сцеплений
5.1. Сцепление с диафрагменной нажимной пружиной
На рисунке 5.1 показано фрикционное однодисковое сцепление с диафрагменной нажимной пружиной. Сцепление с маховиком 2 двигателя расположено в литом картере 1, закрепленном на заднем торце блока цилиндров двигателя.
Сцепление состоит из ведущих деталей: кожуха 12, прикрепленного болтами к маховику двигателя, и нажимного диска 4, соединенного с кожухом тремя упругими пластинами 2 (рисунок 5.2) с помощью заклепок 3 и 4, и ведомых деталей: ведомого диска с фрикционными накладками и ведомого вала.
Маховик двигателя, кожух и нажимной диск вращаются с частотой коленчатого вала двигателя. Кроме того, нажимной диск за счет упругости соединительных пластин имеет возможность перемещаться в осевом направлении.
Ведомый диск расположен между нажимным диском и маховиком двигателя. Он соединен со ступицей 19 через пружинно-фрикционный демпфер (гаситель) крутильных колебаний.
У подавляющего большинства автомобилей картер коробки передач присоединяется непосредственно к картеру сцепления 1, и ступица ведомого диска соединена с первичным валом коробки передач 8 шлицевым соединением, а ведомый вал сцепления отсутствует.
Передний конец первичного вала коробки передач установлен на роликоподшипнике в выточке маховика двигателя, а задний конец – на шарикоподшипнике в картере коробки передач.
Кроме ведущих и ведомых деталей, в сцеплении выделяют группу деталей, осуществляющих его включение-выключение: диафрагменную пружину 6, муфту 10 выключения сцепления с выжимным подшипником 7 и вилку 13 выключения сцепления, и привод сцепления.
Рисунок 5.1 – Однодисковое фрикционное сцепление:
1 – картер сцепления; 2 – маховик двигателя; 3 – фрикционные накладки ведомого диска; 4 – нажимной диск; 5 – опорные кольца; 6 – диафрагменная пружина; 7 – выжимной подшипник; 8 – первичный вал коробки передач; 9 – поролоновые кольца; 10 – муфта выключения сцепления; 11 – шаровая опора вилки; 12 – кожух; 13 – вилка; 14 – шток рабочего цилиндра; 15 – соединительная пластина; 16 – рабочий цилиндр; 17 – штуцер прокачки; 18 – пружина демпфера крутильных колебаний; 19 – ступица ведомого диска
Включение сцепления осуществляется под действием силы, создаваемой нажимной пружиной (пружинами), а выключение – в результате преодоления этой силы при воздействии на педаль сцепления и через привод – на муфту выключения сцепления и пружину (пружины).
Диски сцепления сжимаются диафрагменной нажимной пружиной 6, разрезанной на лепестки (см. рисунок 5.2, поз. 1), которые выполняют функции
рычагов выключения сцепления. Она установлена между
кожухом 12 и нажимным диском 4 и зажата почти в полностью распрямленном состоянии между двумя опорными кольцами 5, закрепленными штифтами (или заклепками), расклепанными на кожухе. Наружным краем пружина опирается на выступ нажимного диска и благодаря своей упругости перемещает его в осевом
|
Рисунок 5.2 – Корзина сцепления: 1 – диафрагменная пружина; 2 – упругая пластина крепления нажимного диска к кожуху сцепления; 3 и 4 – заклепки крепления пружины к нажимному диску и кожуху |
направлении к маховику, зажимая ведомый диск с необходимым усилием.
Муфта 10 выключения сцепления с выжимным подшипником 7 установлена на втулке, по которой может перемещаться вилкой 13 выключения сцепления, шарнирно установленной на шаровой опоре 11, закрепленной в картере сцепления. Вилка входит в выточки муфты выключения сцепления и соединяется с ней фиксирующей пружиной. Наружный конец вилки, выходящий наружу через люк картера, соединен со штоком 14 рабочего цилиндра 16 гидропривода выключения сцепления. В исходное положение механизм включения-выключения сцепления устанавливается с помощью
оттяжной пружины вилки (см. рисунок 8.4, поз. 10).
Рисунок 5.3 – Корзины сцеплений:
1 – кожух; 2 – диафрагменная пружина; 3 – упорный фланец выключения сцепления; 4 – штифты (или заклепки) крепления опорных колец диафрагменной пружины к кожуху сцепления
Вилка 13 перемещает вперед по втулке муфту 10, которая через выжимной подшипник 7 воздействует на лепестки диафрагменной пружины непосредственно (рисунок 5.3, а) или через упорный фланец выключения сцепления (рисунок 5.3, б). Как правило, упорный фланец соединяется с кожухом сцепления упругими соединительными пластинами, позволяющими фланцу перемещаться в осевом направлении (рисунок 5.4). К фланцу приклеивается фрикционное кольцо, которое обеспечивает вращение наружной обоймы выжимного подшипника при выключении сцепления.
Выжимной подшипник муфты выключения сцепления выполняют закрытым и герметичным. Смазочный материал в него закладывают при сборке.
Надежная передача крутящего момента сцеплением во включенном состоянии без пробуксовывания ведомых дисков обеспечивается достаточной силой трения между трущимися поверхностями, которая зависит от усилия, создаваемого нажимными пружинами.
В процессе эксплуатации автомобиля в результате износа фрикционных накладок нажимной диск перемещается в сторону маховика, изменяя жесткость пружин сцепления.
В сцеплениях с периферийными цилиндрическими пружинами, которые имеют линейную характеристику упругости 2 (рисунок 5.5), это приводит к снижению нажимного усилия и передаваемого момента трения вплоть до наступления пробуксовывания сцепления.
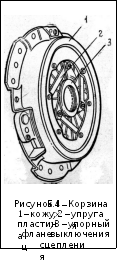
В сцеплениях с диафрагменной пружиной, которая имеет нелинейную характеристику упругости 1, нажимное усилие при износе накладок поддерживается примерно постоянным. Для выключения сцепления с диафрагменной пружиной необходимо существенно меньшее усилие, чем для сцепления с периферийными пружинами
'
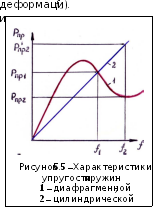
(см. на рисунке 5.5 различие в ординатах Рпр2 и Рпр2 при одинаковой
Быстрое и полное отсоединение двигателя от трансмиссии (чистота выключения сцепления) необходимо для безударного переключения передач. Это достигается получением гарантированного зазора между поверхностями трения при полностью выжатой педали сцепления, что обеспечивается принудительным отведением нажимного диска (от
ведомого) на определенное расстояние с помощью рычагов выключения или
специальных пружин. В сцеплениях с периферийными пружинами для достижения чистоты выключения число нажимных пружин должно быть кратно числу рычагов выключения, что исключает перекос нажимного диска.
Для двухдисковых сцеплений имеются специальные рычажные или пружинные устройства для принудительного перемещения среднего ведущего диска в положение, при котором оба ведомых диска будут находиться в свободном состоянии (рисунок 5.6).
В рычажном устройстве (рисунок 5.6, а), установленном на среднем ведущем диске, винтовая цилиндрическая пружина кручения при выключении сцепления поворачивает равноплечий рычаг. Рычаг, упираясь своими концами в нажимной диск и маховик, устанавливает средний ведущий диск на одинаковом расстоянии от маховика и нажимного диска.
В пружинных устройствах между маховиком и средним ведущим диском расположены отжимные пружины. Величину необходимого перемещения S среднего диска при выключении сцепления под действием этих пружин устанавливают:
с помощью штоков, расположенных между средним диском и кожухом (рисунок 5.6, б). Штоки, выполненные заодно с шипами, закреплены гайками на среднем диске сцепления. На противоположные концы штоков надеты разрезные кольца, которыми штоки при выключении сцепления упираются в упорные планки, соединенные болтами с кожухом сцепления;
с помощью регулировочных болтов, ввернутых в кожух сцепления и застопоренных контргайками (рисунок 5.6, в).
При полностью выключенном сцеплении (полностью отведенном нажимном диске) зазор ∆н между трущимися поверхностями в однодисковых сцеплениях составляет 0,75…1,0 мм, в двухдисковых – 0,5…0,6 мм, а в многодисковых – 0,25…0,30 мм, ход нажимного диска не превышает 1,5…2,0 мм у однодисковых и 2,0…2,5 мм у двухдисковых сцеплений.
Плавность включения сцепления диктуется необходимостью снижения динамических нагрузок в трансмиссии при трогании автомобиля с места и переключении передач, что достигается постепенным отпусканием педали сцепления при включении, а также обеспечивается податливостью ведомого диска.
Рисунок 5.6 – Механизмы, обеспечивающие гарантированный зазор между поверхностями трения:
а – рычажный; б – со штоком и отжимной пружиной; в – с регулировочным болтом и отжимной пружиной; S – рабочий зазор
На плавность включения сцепления также оказывает влияние упругость элементов в механизме выключения. С этой точки зрения сцепление с диафрагменной пружиной, у которой податливые лепестки выполняют функции рычагов выключения, предпочтительнее, чем сцепление с периферийными пружинами, у которого выключение осуществляется жесткими рычагами.
Динамические нагрузки, возникающие в трансмиссии, могут быть пиковыми (единичными) и периодическими.
Пиковые нагрузки возникают при резких изменениях угловых скоростей валов трансмиссии, например при резком включении сцепления броском педали, торможении автомобиля с включенным сцеплением или движении по неровным дорогам.
При резком включении сцепления уменьшается угловая скорость коленчатого вала двигателя ωе и на трансмиссию передается повышенный крутящий момент Мс, который ее закручивает:
Мс = Мe + Је · (dωе / dt),
где Је и (dωе / dt) – соответственно, момент инерции и ускорение вращающихся частей двигателя.
Для исключения поломок в трансмиссии сцепление ограничивает пиковые нагрузки путем пробуксовывания ведомого диска.
Периодические нагрузки возникают в результате неравномерности вращения коленчатого вала двигателя и передаваемого в трансмиссию автомобиля крутящего момента, что вызывает крутильные колебания. Они могут привести к появлению резонанса – резкого повышения уровня амплитуд крутящих моментов и напряжений в деталях трансмиссии. Для снижения уровня крутильных колебаний в конструкцию ведомого диска сцепления (или маховика двигателя) включают специальные демпферы (гасители) крутильных колебаний, которые преобразуют энергию колебаний в теплоту.
Кроме того, демпферы, изменяя жесткость трансмиссии, не допускают возможности наступления резонанса в трансмиссии, выводя резонансные частоты за область рабочих частот двигателя.
Сцепления балансируют в сборе с маховиком двигателя. Допустимый дисбаланс сцепления в сборе при динамической балансировке 0,2…0,8 Н·см (в зависимости от размеров сцепления), а дисбаланс нажимного диска – 0,10… 0,25 Н·см. Балансировка нажимного диска достигается высверливанием металла по ободу, а ведомого диска – приклепыванием к нему балансировочных грузиков.