
Детали машин / Konspekty_lekcii / Конспекты лекций / Лекция 25. Основные принципы и правила конструирования
.pdfЛекция 25
ОСНОВНЫЕ ПРИНЦИПЫ И ПРАВИЛА КОНСТРУИРОВАНИЯ
План лекции
1.Прочность и жесткость деталей.
2.Точность взаимного положения деталей.
3.Другие методы и принципы конструирования.
4.Особенности конструкции деталей при различных способах изготовления. 4.1. Механически обрабатываемые детали.
4.2. Особенности конструкции литых деталей.
1. Прочность и жесткость деталей
Прочная и жесткая деталь при эксплуатации не должна разрушаться и подвергаться недопустимым упругим и пластическим деформациям. Примерами опасных деформаций являются большие прогибы и перекосы валов с зубчатыми колесами при действии сил, образование ямок на дорожках подшипников качения от действия нагрузок
Условия прочности для сечения, в котором под действием сил возникают лишь нормальные напряжения, следующие:
- в расчетах общего машиностроения по допускаемым напряжениям σmax ≤
[σ]RN = σIimд/[n] или по запасам прочности п = σlimД/σmах ≥ [п], где [σ]RN, δlimД
допускаемые и предельные, нормальные напряжения; п, [п] фактический и допускаемый коэффициенты запаса прочности;
-при расчетах ЛА по разрушающим напряжениям Fp = Fэf, σр=Fp /А, η = σB/σp
≥1, где Fp, Fэ расчетные и эксплуатационные нагрузки, f коэффициент безопасности (f ≥ 1,3), η коэффициент запаса прочности по разрушающим напряжениям, А площадь поперечного сечения. Для касательных напряжений формулы аналогичны, но в них нужно заменить σ на τ.
Самый простой способ повышения прочности и жесткости детали заключается
вувеличении размеров опасных сечений или замене материала на более качественный. Обычно такое решение приводит к увеличению массы, габаритов и стоимости. Однако цель конструктора и состоит в отыскании способов обеспечения прочности при минимальном увеличении массы. Эти способы и являются предметом изучения.
Прочность узлов и деталей. Конструирование прочных узлов и деталей минимальной массы сводится к выбору рациональной схемы конструкции, формы, размеров и материала деталей. Возможно использование и упрочнения материала. Минимальная масса конструкции обеспечивается следующими способами:
-создание изделия с рациональной конструктивно-силовой схемой.
Например, грунтозаборное устройство I корабля, совершающего посадку на Венеру, сходном варианте имело трубчатый корпус шнека, который крепился кронштейнами
1

к двум различным элементам конструкции: кронштейны 2, 3 к ферме Ф, а кронштейн 1 к приборному отсеку П (рис. 25.1, а). При испытаниях было установлено, что в момент посадки при перегрузке около 400 g шнек заклинивало. Внесенные изменения позволили получить более рациональную конструктивносиловую схему (рис.25.1, б) корпус шнека стал крепиться на едином кронштейне К, что уменьшило деформацию и обеспечило надежную работу.
Рис.25.1
Для получения конструкций минимальной массы необходимо предусмотреть
передачу силы по кратчайшему пути (рис. 25.2).
Рис. 25.2
2

Это осуществляется тогда, когда конструкция подвергается растяжению, сжатию, сдвигу, но не изгибу. На рис. 25.2, а изображена неудачная конструкция качалки, плечи которой работают на изгиб. В измененной конструкции (рис. 25.2, б) этот недостаток устранен, так как дополнительная полка передает нагрузки по кратчайшему пути и работает на растяжение, а напряжения от изгиба значительно меньше. На рис. 25.2, в также показана неудачная конструкция, а на рис. 25.2, г рациональная. В конструкциях предпочтительнее использовать двухопорные балки,
ане консольные, так как максимальный изгибающий момент у них в 4 раза больше;
-конструирование балки минимальной массы. Форма детали должна быть
согласована с напряженно-деформированным состоянием (НДС), т. е. где нагрузка там и материал, отсутствует нагрузка нет материала. Форма такой детали определяется двумя условиями:
- выбором рациональной формы сечения. Для балки, нагруженной изгибающим моментом, рациональным сечением является двутавр или полый прямоугольник. Это связано с тем, что нормальные напряжения в сечении распределяются неравномерно (рис. 25.3). Они имеют максимальное значение в крайних точках сечения и снижаются до нуля у нейтральной оси.
Рис. 25.3
Для выравнивания напряжений необходимо удалить материал из наименее нагруженных мест и сосредоточить его в более нагруженных участках
сечения, т. е. используется принцип ф о р м а и р а з м е р ы д е т а л и |
д о л ж н ы |
с о о т в е т с т в о в а т ь н а г р у з к е . При переходе от прямоугольного |
сечения к |
двутавровому (рис. 25.3, б) или к полому прямоугольнику (рис. 25.3, в) для обеспечения равного момента сопротивления при одинаковой ширине b нужно несколько увеличить высоту у нового сечения, погонная масса которого уменьшается. Так, при η = h/Н1 = 0,5, H1/H = 1,07, К = 0,53 (К = G1/G коэффициент совершенства по массе, G, G1 погонные массы балки прямоугольного сечения и двутавра или полого прямоугольника). У облегченных балок необходимо предусмотреть стенки для восприятия перерезывающих сил. Аналогично у вала, нагруженного изгибающим и крутящим моментами, рациональным является кольцевое, а не сплошное круглое сечение. При увеличении внутреннего диаметра кольцевого сечения возможен п е р е х о д к равномерному р а с п р е д е л е н и ю напряжения. Проиллюстрируем это на примере вала, нагруженного изгибающим Ми и крутящим Т моментами. У сплошного вала
3
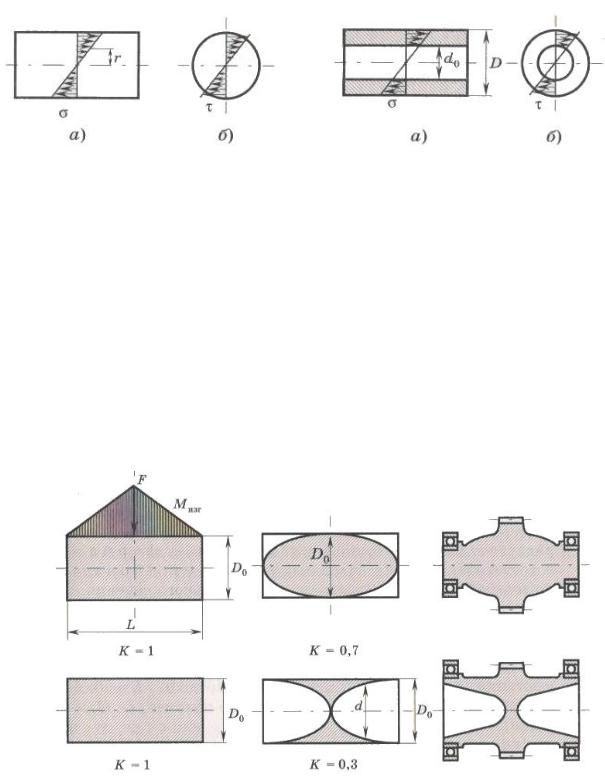
нормальные σи и касательные τ напряжения распределяются неравномерно (рис.25.4), напряжения меняются пропорционально радиусу r:
σи = Mиr/Jи; τ = Tr/Jр,
где r расстояние от нейтральной оси.
При наличии у вала отверстия напряжения распределяются более равномерно (рис. 25.5), при d0 → D, σ = const, τ = const (переход к тонкостенным конструкциям).
Рис. 25.4 |
Рис.25.5 |
При растяжении сжатии балок сечение может быть произвольным, если силы приложены в центре жесткости;
- созданием равнопрочной по длине балки (п = const). Рассмотрим вал круглого сечения, нагруженный посередине силой F (рис. 25.6, а). Переходя от вала постоянного сечения к равнопрочному, полученному путем изменения наружного диаметра (рис. 25.6, б), получаем уменьшение массы примерно на 30%. При использовании равнопрочного вала, в котором выбрано рациональное (кольцевое) сечение, изменяется также размер отверстия (рис. 25.6, б), масса уменьшается примерно на 70%, К характеристика относительной массы вала (отношение массы равнопрочного вала к массе вала с постоянным, сплошным сечением). В равнопрочной конструкции вероятность разрушения всех элементов одинакова. На рис.25.6, в показаны реализации таких валов;
Рис. 25.6
4

-уменьшение нагрузки. Снижение нагрузок на детали реализуется увеличением числа элементов, передающих силы и моменты, например заменой однопоточной схемы у планетарного редуктора на многопоточную с несколькими сателлитами, что приводит к снижению нагрузок на зубья, массы
игабаритов;
-применение композиционных материалов. Детали из композиционного материала (КМ) можно придать свойства, согласованные с действующими нагрузками (где больше нагрузка, там в материале матрицы больше высокопрочных волокон, направленных вдоль действующих сил);
-уменьшение концентрации напряжений. Это важно для увеличения прочности и долговечности при циклическом нагружении. Снижение концентрации напряжений можно выполнить двумя способами: конструк-
тивным и технологическим. В первом случае рекомендуется не делать резких переходов формы (галтели с малым радиусом, пазы под шпонки и т. п.) и скачков нагрузки от сосредоточенных сил, прессовых посадок и др. При технологическом способе прочность детали увеличивается за счет создания в поверхностном слое остаточных напряжений сжатия и/или повышения прочности поверхностного слоя. Это осуществляется дробеструйной обработкой, обкаткой роликами, химикотермическими способами (цементация, азотирование), методами физического воздействия высокой энергией (лазерная, ионно-плазменная обработка) и др.;
-упрочнение материала детали в наиболее напряженных местах.
Упрочнение выполняется теми же технологическими способами, как и при уменьшении концентрации напряжений (предыдущий вариант). Например, рабочую поверхность зуба колеса делают более твердой по сравнению с сердцевиной. В результате зуб выдерживает большие контактные напряжения, а пластичная сердцевина не дает ему разрушаться при изгибе. Такое мероприятие позволяет снизить массу в 2 раза и более;
-удаление материала в малонагружен-
ных участках. На рис.25.7 показано, как нужно изменить форму детали для уменьшения ее массы (конструкции рис. 257, а заменить на более рациональные конструкции рис.25.7, б). В улучшенных конструкциях у зубчатого колеса в малонагруженном диске, соединяющем ступицу с ободом, сделаны дополнительные проточки, а в консольно расположенной на валу шестерне расточено отверстие в центре, где напряжения малы.
Жесткость деталей и узлов. Жесткость определяет способность детали сопротивляться деформации при нагружении. Наряду с деталя-
ми, где деформация ограничена, а жесткость Рис.25.7 должна быть достаточно высокой (валы, балки), имеются элементы с регламентированной и/или малой жесткостью (пружины,
5
сильфоны, гибкие колеса волновых передач). Для обеспечения необходимой жесткости балок целесообразно использовать рациональные сечения, выбранные из условия прочности. Такие сечения также будут иметь минимальную массу, а равнопрочная конструкция минимальную жесткость.
Н е л ь з я д о п у с к а т ь п о т е р ю о б щ е й и местн о й ус т о й ч и в о с т и . Общая устойчивость балки, нагруженной сжимающими силами, связана с жесткостью. Действующая сила должна быть меньше критической силы, которая определяется по формуле Эйлера:
Fкр= π2 EJи /(µl)2
При конструировании длинных стержней, которые могут потерять общую устойчивость, следует иметь в виду, что их рациональным сечением, обеспечивающим минимальную массу, будет кольцевое, которое имеет максимальное значение отношения момента инерции сечения к погонной массе, поэтому в конструкциях используются детали, состоящие из труб.
Повышение жесткости возможно путем:
- использования материала с более высоким модулем упругости (например, вместо алюминиевых сплавов Е = 0,72 • 105 МПа бериллиевых Е = 1,35 • 105, который имеет более высокую удельную жесткость Е/ ) или композиционных материалов;
-замены деформации изгиба на растяжение сжатие;
-использования ребер или перегородок;
-увеличения площади контакта;
-увеличения жесткости наиболее податливого сжатию элемента (например, упругой прокладки) и др.
2.Точность взаимного положения деталей
Точность деталей и их взаимного положения определяется назначенными допусками и посадками. Рассмотрим лишь общие подходы к точности положения деталей. В конструкции должны быть предусмотрены элементы, обеспечивающие заданную точность относительного расположения ее частей центрирующие, фиксирующие, компенсирующие и другие части. Они должны иметь простую конструкцию и свободный подход для режущего и мерительного инструментов.
Базирование деталей. Базирование придание детали требуемого положения относительно выбранной системы координат. Поверхность, ось, точка, принадлежащие детали и используемые для базирования, называются базами.
Погрешностью базирования называют отклонение фактически полученного положения детали от требуемого. Чаще всего базирование производят по плоским и цилиндрическим поверхностям деталей и их комбинациям. Вследствие погрешностей формы сопрягаемых поверхностей и некоторых других факторов при соединений возможны перекосы на валах, особенно при установке узких деталей. В случае малого отношения длины сопряжения к диаметру l/d < 0,8 для повышения точности базирования деталь прижимают к торцу буртика вала, т. е. базируют по торцу. Детали с отношением l/d ≥ 0,8 базируют по цилиндрической поверхности (рис. 25.8).
6
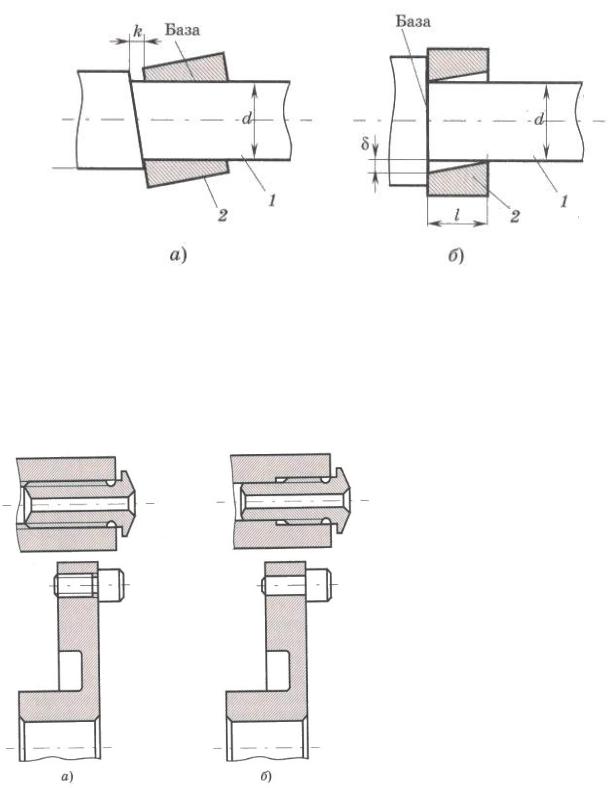
Рис. 25.8
На рис. 25.8, а радиальный зазор между валом 1 и отверстием в детали 2 (ступицы колеса, втулки и т. д.), определяющий погрешность центрирования, должен быть мал. Между торцами детали 2 и буртиком вала образуется клиновый зазор k (l/d > 0,8, основная база цилиндр), а на рис. 25.8, б радиальный зазор δ достаточно велик, деталь 2 своим торцом полностью прилегает к буртику вала (l/d < 0,8, основная база торец).
Центрирование деталей.
Работоспособность проектируемого изделия во многом определяется необходимой соосностью деталей и узлов, входящих в изделие, т. е. требуемой точностью центрирования. Соосность характеризуется величиной смещения номинально совпадающих осей цилиндрических поверхностей. Выбор расположения этих поверхностей определяет допуск соосности. При обеспечении требуемой соосности надо принимать во внимание то, что резьбовые соединения не обеспечивают правильного центрирования из-за
биения среднего диаметра и зазоров в резьбе. В качестве центрирующих поверхностей в таких случаях, как правило, используются цилиндрические или
соосные с резьбой гладкие цилиндрические пояски.
На рис. 25.9, а базой является резьба, что не обеспечивает необходимой точности положения оси пальца и подшипника. В правильных конструктивных решениях (рис.25.9, б) палец запрессован в водило и базой является цилиндрическая поверхность, а у подшипника сделан цилиндрический поясок.
7

Необходимо также избегать фиксации детали по нескольким поверхностям, так как это усложняет изготовление и сборку. Например, фиксировать призматическую шпонку следует только по рабочим граням, предусмотрев по торцам К, а также между верхней плоскостью шпонки и пазом под шпонку в ступице зазоры Т и З (рис. 25.10, а). Неправильные конструкции изображены на рис. 25.10, б, где отсутствует зазор Т у торцевой поверхности К и фиксация шпонки выполняется по всем граням.
Рис. 25.10
Аналогично у втулки (рис. 25.11) и пальца (рис.25.12) в одной из двух цилиндрических поверхностей также нужно делать зазор. Центрирование по двум поверхностям обычно усложняет изготовление и сборку, увеличивает стоимость и не улучшает конструкцию. На рис. 25.11, а центрирование втулки, а на рис.25.12, а пальца выполняется по двум цилиндрическим поверхностям 1 и 2, что неоправданно. Правильные конструкции приведены на рис. 25.11, б, в и рис. 25.12, б, в, где предусмотрены зазоры s, а на рис. 25.11, в верхняя часть (буртик) выступает наружу. Отметим, что на рис. 25.11, а неправильно произведена фиксация втулки вдоль оси опора по двум поверхностям 3 и 4. На рис. 25.11, б это устранено введением зазора s, а на рис. 25.11, в увеличением отверстия, расположенного ниже втулки.
Рис. 25.11 |
Рис. 25.12 |
Фиксация детали на плоскости. Фиксация детали на плоскости, например крышки на основании корпуса (рис. 25.13), может осуществляться с помощью двух, а иногда и более штифтов. Более двух штифтов устанавливают, когда они не только
8

фиксируют деталь, но и передают большие силы, действующие в плоскости стыка. Силы, перпендикулярные к плоскости стыка, воспринимаются винтами (шпильками). Не рекомендуется плоскость стыка делать ступенчатой, так как это усложняет его изготовление и герметизацию.
Рис.25.13
Наиболее технологична конструкция, в которой используется метод полной взаимозаменяемости. Однако наряду с ним иногда приходится использовать методы компенсации (введением компенсатора) или пригонки (один из размеров подгоняется при сборке). Метод пригонки используется лишь в индивидуальном производстве.
Устранение пригонки (подгонки). Использование пригонки затрудняет изготовление конструкций, и ее нужно по возможности исключать, что особенно важно в крупносерийном и массовом производствах. Точность замыкающего звена
вместо пригонки (метод пригонки) может обеспечиваться |
за |
счет |
введения |
|
к о м п е н с а т о р а |
(метод |
регулиров- |
||
ки). |
|
|
|
|
На |
рис. |
25.14 |
показаны |
|
активный (ЗА) и пассивный (ЗП) |
||||
замки, установленные на стыковочных |
||||
шпангоутах космического |
аппарата. |
|||
Крюк активного замка закреплен и |
||||
перемещается под действием пальца, |
||||
соединенного с крюком в точке Оэ. |
||||
Палец |
эксцентрично |
закреплен на |
|
барабане Б, вращающемся вокруг оси |
|
Об. На барабане закреплен трос Т, |
|
который приводит его во вращение. |
|
Трос соединяет группу замков, ко- |
|
торые приводятся в движение от |
Рис. 25.14 |
одного редуктора. Пассивный замок |
|
|
|
состоит из крюка, имеющего гайку Г |
для регулировки зазора между замками, которая через тарельчатые пружины П, являющиеся компенсаторами, передает нагрузки на стыковочный шпангоут. При соединении крюков активного и массивного замков возможна ситуация, когда на
9
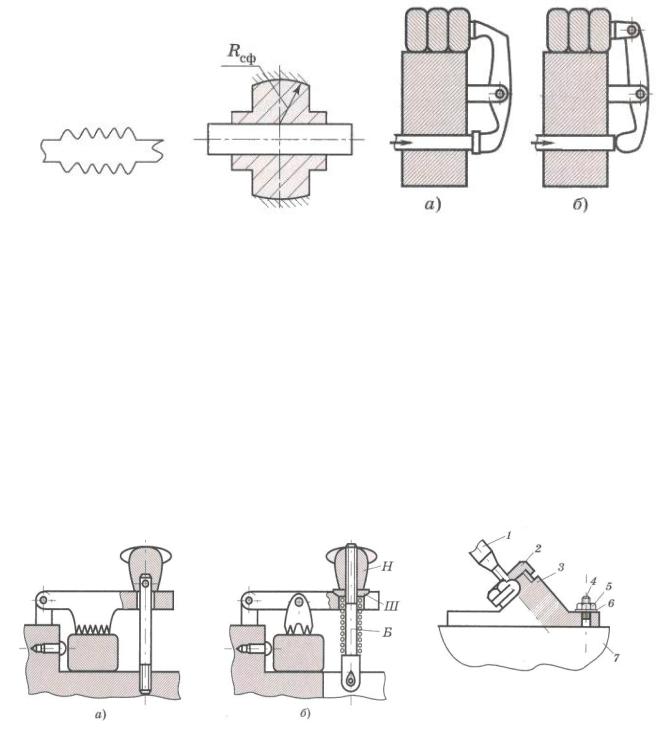
одних замках люфт отсутствует, а на других наблюдается зазор. Тогда движение крюков будет продолжаться и за счет перемещения компенсатора зазор устраняется во всех соединениях, что обеспечивает жесткое и надежное соединение стыковочных шпангоутов КА.
Рис.25.15 |
Рис.25.16 |
Рис.25.17 |
В гидросистемах в качестве компенсаторов используются сильфоны (рис. 25.15), которые хорошо деформируются, так как имеют меньшую, чем у трубопровода, жесткость.
Компенсаторы в виде регулировочных колец используются в схеме установки подшипников враспор, что позволяет создать необходимый зазор для обеспечения удлинения вала при изменении, температуры.
Разновидностью использования компенсаторов можно считать применение м е т о д а с а м о у с т а н а в л и в а е м о сти. Для этого в конструкцию вводят подвижные детали, компенсирующие неточности. Например, у подшипника добавляется шаровая опора, устраняющая перекос опоры вала (рис. 25.16). Узлы, приведенные на рис. 25.17, а и 25.18, а, не обеспечивают необходимое крепление заготовки.
Рис. 25.19
Рис.25.18
Введение самоустанавливающихся звеньев позволяет надежно закрепить детали (рис. 25.17, б, 25.18, б). Такие рычажные системы используются в стеклоочистителях автомобилей. В конструкции на рис. 25.18, б под накидной гайкой Н подложена сферическая шайба Ш, разгружающая откидной болт Б от изгибающего момента.
Для компенсации углового перемещения относительно двух перпендикулярных
10