
Детали машин / Konspekty_lekcii / Конспекты лекций / Лекция 24. Основные принципы и правила конструирования
.pdfЛекция 24
ОСНОВНЫЕ ПРИНЦИПЫ И ПРАВИЛА КОНСТРУИРОВАНИЯ
План лекции
1.Общие концепции при конструировании.
2.Стандартизация и унификация.
3.Принцип агрегатности.
4.Устранение подгонки.
5.Устранение и уменьшение изгиба.
6.Принцип самоустанавливаемости.
7.Бомбинирование.
1.Общие концепции при конструировании
Во избежание ошибок при создании конкретных конструкций необходимо познакомиться с азбукой конструирования. Такой подход позволит в дальнейшем создавать не только типовые, но и самые разнообразные совершенные изделия.
Вначале рассмотрим общие концепции при конструировании, в основе которых лежат эксплуатационные, производственно-технологичес- кие, экономические и эргономические требования. Затем перейдем к знакомству с принципами и правилами конструирования и примерами их конструктивных решений.
Конструкция изделия должна максимально удовлетворять потребности пользователя при низкой цене иметь высокое качество. Технические характеристики должны находиться на уровне мировых достижений и иметь резерв развития.
При конструировании механизмов узлов и деталей должны выполняться следующие мероприятия:
- выбор рациональной схемы конструкции и ее элементов, например, использование вместо развернутой схемы соосной или замена передачи скольжения винт гайка на роликовинтовую передачу (РВП). Создание машин нового поколения на базе мехатроники, когда механические системы сочетаются с электронными;
-обеспечение показателей, записанных в техническом задании (ТЗ), определяющих назначение, технические и экономические характеристики объекта такие, как производительность, мощность, скорость движения, стоимость и другие параметры, которые должны превышать соответствующие параметры существующих изделий;
-повышение надежности и ресурса. Изделие в течение заданного времени должно выполнять свои функции, сохраняя эксплутационные показатели. У детали надежность определяется прочностью, жесткостью и стойко-
1
стью к воздействиям вибрации, износа, температуры, давления, влажности и др. В зависимости от назначения и условий эксплуатации требования могут быть различными, например, при воздействии вибрации на резьбовые детали они должны стопориться;
-уменьшение материалоемкости. Это условие выполняется при создании компактных конструкций и изготовлении деталей из материала с высокой удельной прочностью, включая металлы, биметаллы, неметаллы и композиты, выборе размеров и формы детали, обеспечивающей выравнивание напряжений. Возможно также упрочнение материала различными методами (термическими, химико-термическими, физическим воздействием высоких энергий и др.), использование заготовок, максимально приближенных к окончательной форме детали, получаемых при больших сериях литьем, штамповкой, сваркой и другими высокопроизводительными способами;
-малое энергопотребление и высокая износостойкость при эксплуатации, что реализуется при минимальных потерях на трение и высоком КПД, например уменьшением потерь путем использования в передачах подшипников качения вместо подшипников скольжения;
-обоснованное назначение точности и шероховатости деталей и обеспечение их взаимозаменяемости, использование стандартизации и унификации деталей и их элементов;
-исключение попадания грязи, пыли и влаги на подвижные детали изделий, что достигается созданием герметичных корпусов, кожухов, уплотнений и других элементов конструкций, а также нанесением антикоррозионных покрытий на ряд поверхностей, особенно наружных. В результате такими мероприятиями устраняется коррозия, а в узлах, трения уменьшается износ;
-включение элементов (лючков, регулировочных устройств) для обеспечения технического обслуживания, ремонта и контроля;
-создание безопасности и комфорта оператору или исключение его присутствия (автоматизация процесса), устранение вредного воздействия на человека и окружающую среду;
-учет производственно-технологических требований
Рассмотрев общие концепции, перейдем к более подробному изучению основ конструирования.
2. Стандартизация и унификация
Использование стандартизации и унификации деталей и узлов улучшает качество изделий, делает конструкцию более технологичной, а ее производство экономичным.
Стандартизация это регламентирование типоразмеров и конструкций применяемых машиностроительных деталей, узлов, агрегатов. Стандартизация ускоряет проектирование, облегчает изготовление, эксплуатацию и ремонт машин и механизмов и при целесообразной конструкции деталей спо-
2
собствует увеличению надежности машин. Например, имеются стандарты на резьбу, модули зубчатых колес, что позволяет для их изготовления применять стандартный инструмент. Использование стандартных деталей и изделий позволяет наладить их массовое производство, что обеспечивает высокое качество.
В зависимости от сферы действия предусматриваются следующие категории стандартов: государственные (ГОСТ), отраслевые (ОСТ) и стандарты предприятий (объединений) (СТП).
ГОСТы устанавливают требования преимущественно к продукции массового и крупносерийного производства широкого и межотраслевого применения, например ряды нормальных линейных размеров, модули зубчатых передач, допуски и посадки, размеры и допуски резьбы и др.
ОСТы устанавливают требования к специфической для отрасли продукции, технической оснастке, инструменту. ОСТы разрабатывают также для ограничения числа, например, типоразмеров крепежных деталей, полей допусков и посадок. В авиации используется ОСТ1.
СТП распространяются на нормы, правила, методы, составные части изделий. Они применяются только на данном предприятии (объединении).
Унификация это приведение объектов одинакового функционального назначения к единообразию по установленному признаку и рациональное сокращение числа этих объектов на основе данных об их эффективной применяемости. Унификация состоит в многократном применении в конструкции одних и тех же элементов и деталей. Это наиболее распространенная и эффективная форма улучшения технологичности изделий.
Унификация конструктивных элементов.
Конструктивные элементы – линейные размеры, углы, конусы, канавки, рифления, резьбы, шлицевые и шпоночные соединения и пр.
Согласно определению унификации элементы, выявляющиеся в процессе компоновки изделия, следует многократно использовать для всей конструкции, усредняя расчетные параметры и добиваясь максимального сокращения номенклатуры этих элементов.
Унификации в первую очередь подлежат посадочные размеры соединения (по номинальным размерам, типу посадок и квалитету), резьбы (по диа-
метру, шагу и квалитету), шлицевые и шпоночные соединения, крепежные детали. Целесообразно сокращать номенклатуру материалов, виды отделочных операций, гальванических покрытий, типы сварки, форму сварных швов.
На рис. 24.1,а-в приведен пример компонования вала с насадной деталью, опертой в бронзовой втулке. В конструкции а выбор посадочных диаметров не продуман. Правильно назначен основной посадочный размер (диаметр опорной шейки) из числа нормальных (ø 50). Далее допущены ошибки. С целью уменьшения расхода бронзы конструктор принимает толщину стенок втулки равной 3,5 мм, вследствие чего получается нестандартный размер наружного диаметра втулки (ø 57). Стремясь увеличить прочность вала в насадном соединении, конструктор уменьшает диаметр вала по
3

отношению к диаметру шейки на 2 мм на сторону, в результате чего получается нестандартный диаметр ø 46, который приводит к размеру резьбы М45 под затяжную гайку.
Вкомпоновке на основе нормальных размеров (конструкция б) наружный диаметр втулки 60 мм, диаметр насадного соединения 45 мм. Отсюда следует размер резьбы М42. Однако стандартизация размеров в данном случае приводит к некоторому снижению прочности вала и увеличению массы бронзовой втулки. В более рациональной конструкции в диаметр шейки 55 мм, наружный диаметр втулки 60 мм, диаметр насадного соединения 50 мм.
Вконструкции г допущен значительный разнобой в размерах посадочных диаметров, резьб, шпонок и модулей зуба. В рациональной конструкции
дсокращено число посадочных размеров, унифицированы шпонки и модули зубьев (m = 4). Необходимая прочность зуба малых зубчатых колес достигнута увеличением их длины. Итоги унификации представлены в таблице 24.1. В общей сложности номенклатура элементов сокращена с 16 до 7 наименований.
Рис. 24.1. Унификация элементов конструкции
4

Таблица 24.1
Унификация элементов зубчатого перебора
Элементы |
Исходящая конструкция |
Число |
Унифицированная конструкция |
Число |
|
Элементы |
Исходящая конструкция |
Число |
Унифицированная конструкция |
Число |
|
|
|
|
|
|
|
|
|
|
|
|
40 Н7/js6 |
1 |
|
|
|
|
|
1 |
|
|
|
45 H7/f7 |
1 |
|
|
|
Резьбы |
М 39 |
|
М 39 |
2 |
|
46 H7/h6 |
1 |
|
|
|
|
М 48 |
2 |
|
|
|
48 H7/h6 |
1 |
40 Н7/js6 |
2 |
|
|
|
|
|
|
|
|
Шпонки |
8 |
2 |
|
3 |
||||
Диаметры |
50 H7/h6 |
1 |
45 H7/f7 |
2 |
|
|
||||
|
(б мм) |
10 |
3 |
10 |
|
|||||
и посадки |
|
|
|
|
|
|
||||
|
|
|
|
|
|
|
|
|
|
|
|
50 H7/js6 |
1 |
50 H7/h6 |
1 |
|
|
|
|
|
|
|
|
|
4 |
1 |
|
|
||||
|
55 H7/f7 |
1 |
55 H7/r6 |
2 |
|
Модули |
|
|
|
|
|
55 H7/r6 |
1 |
|
|
|
зубьев |
4,5 |
1 |
4 |
3 |
|
|
|
|
|
|
|
5 |
1 |
|
|
|
65 H7/r6 |
1 |
|
|
|
|
|
|
|
|
|
|
|
Всего одинаковых |
16 |
-- |
7 |
-- |
|||
|
|
|
элементов |
|
|
|
|
|
||
|
|
|
|
|
|
|
|
|
|
|
В качестве примера унификации размеров под ключ приведем узел регулирования редукционного клапана рис. 24.2. в конструкции а применены три размера (1-3), в унифицированной конструкции б - один размер (4).
Рис.24.2. Узел регулирования редукционного клапана
5
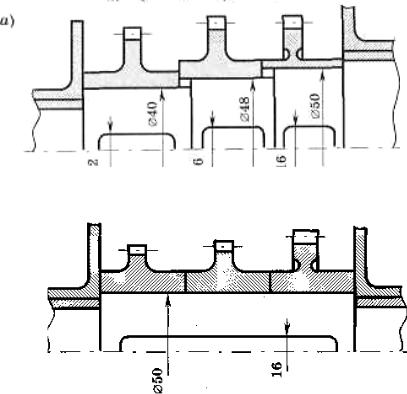
Стандартизация изделий, их составных частей и деталей дает наибольший эффект при сочетании с унификацией. В результате этих мероприятий сокращается номенклатура стандартного рабочего и мерительного инструмента, что особенно при использовании сложного инструмента (фрез, метчиков: плашек и др.) стоимость которых значительно увеличивается при индивидуальном производстве нестандартных образцов.
На рис. 24.3 приведен пример конструкции до (а) и после (б) унификации (т модуль). Она включает переход к единой шпонке и единому модулю для всех зубчатых колес, что сокращает количество необходимого для изготовления инструмента.
m = 5 |
m=4,5 |
m = 4 |
б)
m = 4 |
m = 4 |
m = 4 |
Рис. 24.3. Унификация группы зубчатых колес
Унификация деталей. Следует добиваться максимальной унификации оригинальных деталей. Особенно это важно для трудоемких и многократно повторяющихся деталей.
Конвейерная цепь (рис. 24.4, а) составлена из звеньев двух типов. В рациональной конструкции б звенья унифицированы. Стяжной хомут (в) состоит из двух трудоемких деталей. Соединение промежуточной серьгой (г) позволяет сделать половины хомута одинаковыми.
На рис. 24.4, д и е приведен пример унификации штамповок в узле составного шкива, на рис. 24.4, з и ж – в конструкции цилиндрического штампованного резервуара.
6
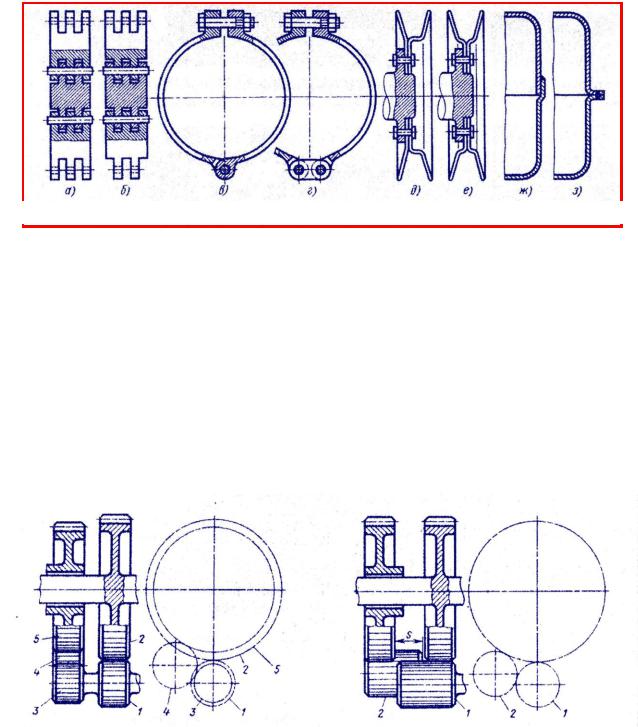
Рис. 24.4. Унификация деталей
Нередко унификацияУнификациядостигается лишьдеталейв результате. целенаправленной проработки, требующей оригинальных решений. В редукторе с двумя концентрическими валами, вращающимися с одинаковой частотой, но в противоположные стороны (рис. 24.5), на приводном валу посажены два зубчатых колеса, одно из которых 1 сцепляется с колесом 2 редуктора, второе 3 – через промежуточное колесо 4 с колесом 5. Узел имеет колеса четырех наименований (1 – 4; 2, 3, 5). Многодетальность и сложность конструкции вызваны необходимостью предупредить заедание зубьев колес 3 за зубья колеса 5. Для этого потребовалось уменьшить диаметр колеса 3 и соответственно (для сохранения передаточного числа) уменьшить диаметр колеса 5.
|
|
а) |
б) |
Рис. 24.5. Схема редуктора (а) до унификации и после унификации (б)
В оригинальном решении (рис. 24.5, б), существенно упрощающем конструкцию, шестерня 1 приводного вала зацепляется с одной стороны с правым колесом редуктора, а с другой стороны – с шестерней 2 привода. Число наименований колес сокращено до двух; малые и большие колеса редуктора попарно одинаковы. Для этого понадобилось только расставить
7
большие колеса редуктора на расстояние s, достаточное для сцепления малых колес.
Унификация позволяет увеличить серийность и тем самым снизить стоимость изготовления деталей. Она облегчит обслуживание и ремонт за счет уменьшения номенклатуры инструмента и запасных частей. Унификация упрощает процесс конструирования.
Унификацию применяют в ущерб равнопрочности. Например, если в редукторе использовать подшипники одного вида и размера, то диаметры отдельных валов окажутся завышенными, окажется также и долговечность отдельных подшипников. Равнопрочность может быть обеспечена при одинаковых одних параметрах и варьировании других. Например, при одинаковом модуле и диаметре зубчатого колеса изменяют его ширину, округляя до регламентированного значения.
3. Принцип агрегатности (блочности)
Целесообразно конструировать узлы в виде независимых агрегатов, отдельно собираемых, регулируемых, подвергаемых обкатке, контрольным испытаниям и устанавливаемых в отработанном виде на машину. Последовательно проведенное агрегатирование позволяет осуществить параллельную и независимую сборку узлов машин, упрощает монтаж, ускоряет доводку опытных образцов, облегчает использование на новых машинах отработанных и проверенных в эксплуатации конструкций и упрощает ремонт, позволяя комплектно заменить износившиеся узлы новыми.
Агрегатирование иногда усложняет конструкцию, но, в конечном счете всегда дает большой выигрыш в общей стоимости изготовления машин, надежности и удобстве эксплуатации. Примеры агрегатирования мелких узлов приведены на рис. 24.6 а – ж.
Вконструкции а редукционный клапан установлен непосредственно в корпусе. Установка клапана в отдельной втулке (конструкция б) делает узел агрегатным. Конструкция в торцового уплотнения неудовлетворительна. При демонтаже уплотняющий диск 1 под действием пружины сходит с направляющей и пазов, фиксирующих его от вращения, и узел распадается. Неудобен и монтаж уплотнения. Введение кольцевого стопора 2 (конструкция г) придает узлу агрегатность.
Взубчатой передаче д, монтируемой на станине 7 и в крышке 8, к описанным выше дефектам неагрегатированных конструкции присоединяется затруднительность введения валика промежуточного перебора 9 в опору крышки. При снятии крышки передача распадается. Проверить правильность зацепления зубчатых колес невозможно.
Вагрегатированной конструкции е опоры зубчатых колес установлены
вдиафрагме 10; передача приводится торсионом 11. Наиболее целесообразна конструкция ж, где опоры расположены в кронштейне 12, привернутом к крышке на лапах 13, что обеспечивает удобную сборку и обзор.
8
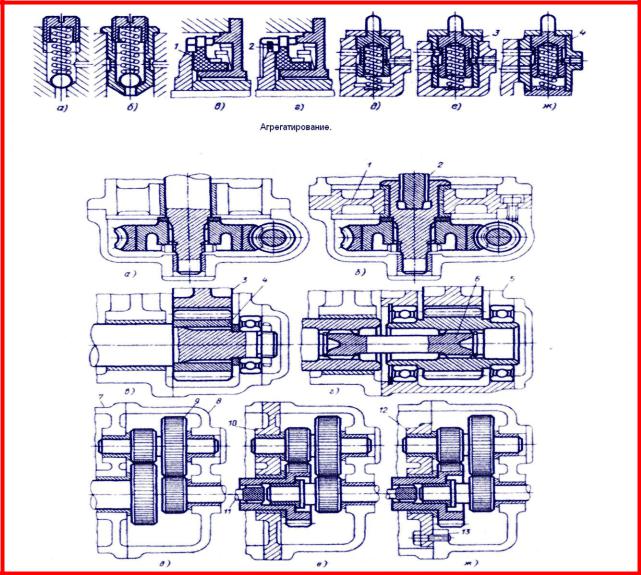
Рис. 24.6. Примеры агрегатирования
4. Устранение подгонки
Необходимо избегать установки и подгонки узлов и деталей по месту. Подгонка, особенно сопровождаемая операциями слесарной или станочной обработки, снижает производительность сборки и лишает конструкцию взаимозаменяемости.
Пример установки по месту приведен на рис. 24.7, а и б. Зубчатое колесо устанавливают на валу по сцепляющемуся с ним зубчатому колесу, после чего положение фиксируют врезным винтом (а) или штифтом (б). При этом требуется обработка по месту дрелями и ручными развертками. Неизбежно попадание стружки в агрегат. После обработки приходится его разбирать, промывать и снова собирать. Разметка при сборке с последующей передачей на станочную обработку еще более усложняет сборку. Более технологична
9

фиксация зубчатого колеса кольцевыми стопорами, устанавливаемыми в заранее проделанной канавке на валу (в).
Пример При установке подшипника в корпусе по месту (г) однажды найденное правильное положение сбивается при каждой разборке, вследствие чего требуется новая регулировка. Фиксация подшипника контрольными штифтами (д) требует механической обработки при сборке. Правильное решение – центрирование подшипника по отверстию в корпусе (е), заранее выполненному с точностью, обеспечивающей правильную работу механизма.
Рис. 24.7. Устранение подгонки
5. Устранение и уменьшение изгиба
Во всех случаях, когда допускает конструкция, изгиб следует заменять более выгодными видами деформации – растяжением, сжатием или сдвигом. Целесообразно применение стержневых или близких к ним систем, элементы которых работают преимущественно на растяжение - сжатие. Если изгибное нагружение неизбежно, то следует уменьшать плечо изгибающих сил и увеличивать моменты сопротивления на опасных участках. Особенно это важно при консольном нагружении, наиболее невыгодном по прочности и жесткости.
Плечи углового рычага испытывают изгиб от действия сил, приложенных на крайних точках (рис. 24.8). Введение таврового ребра между концами рычага ликвидирует изгиб.
Вузле 3 установки ролика на станине лапа крепления подвергается изгибу. Несколько лучше конструкция 4 с усиливающими ребрами. Наиболее рационально установить ролик непосредственно под стенкой , работающей в данном случае на сжатие (конструкция 5).
Вконструкции 6 шарикового подпятника опорная кольцевая полка подвергается изгибу под действием рабочей нагрузки. В улучшенной конструкции 7 полка усилена ребрами. В конструкции 8 сила передается непосред-
10