
830
.pdfводой, с помощью разбрызгивания крыльчаткой, распыливания форсунками или используя капиллярные свойства пористых материалов (эффект фитиля). Недостаток этих конструкций – низкая их эффективность в связи с тем, что снижение температуры воздуха происходит за счет увеличения его влажности.
Третий способ. Оборудование системами вентиляции с ротационным пылеотделением, которая позволяет поддерживать требуемую чистоту воздуха, удаляет теплоизбытки и создает необходимое избыточное давление в кабине для исключения инфильтрации загрязненного наружного воздуха. Следует учесть, что химических фильтров отечественные системы фильтрации вентиляционного воздуха для кабин мобильных машин вообще не имеют.
Таким образом, для решения проблемы безопасности выполнения работ, повышения эффективности и производительности труда механизаторов, необходимо понимать, что все решения требуют вложения средств. И все же такие затраты оправдывают себя, так как речь идет о самом главном – здоровье работников АПК.
Литература:
1. Исламиев Р.Р. Современное состояние и стратегия развития АПК Пермского края / Р.Р. Исламиев // Современное состояние и стратегия развития АПК Пермского края / г. Пермь, 2001вып. 28 (245) – с. 72-76.
2. Лысенко М.В. Экономика, математика и информатика [Текст] / М.В. Лысенко // Оптимизация технического потенциала сельскохозяйственных организаций. 2013г. Вып. - №2. С. 32-36.
3. Сельскохозяйственная продукция [Электронный ресурс]:– режим доступа свободный: http://www.claas.ru/
УДК 593.3
Р.А. Боговеев - студент 2 курса; Д.А. Соломенников - студент 2 курса;
В.А. Елтышев - научный руководитель, доктор техн. наук, профессор, ФГБОУ ВО Пермский ГАТУ, г. Пермь, Россия
ПРОЕКТИРОВОЧНЫЙ РАСЧЕТ КОНСОЛЬНОЙ БАЛКИ НА ПРОЧНОСТЬ ПРИ ИЗГИБЕ
Аннотация. Проведен проектировочный расчет консольной балки круглого поперечного сечения на прочность. Построены эпюры поперечных сил и изгибающих моментов. Определен необходимый диаметр балки.
Ключевые слова: изгиб, балка, метод сечений, прочность.
Постановка задачи: требуется определить диаметр сечения консольной балки d из условия прочности. Расчетная схема балки приведена на рисунке 1а.
Исходные данные: М = 8 кН м ; Р = 8 кН; q = 8 кН/м; а = 1 м; b = 1,2 м; [σ]=100 МПа.
Решение. Из уравнений равновесия определяем реакции в опоре балки А
(рис. 1б)
MА |
0 ; mA |
|
q b a |
||
|
|
|
b |
M P (2 a b) 0 , |
|
|
|
|
|
||
2 |
|
131
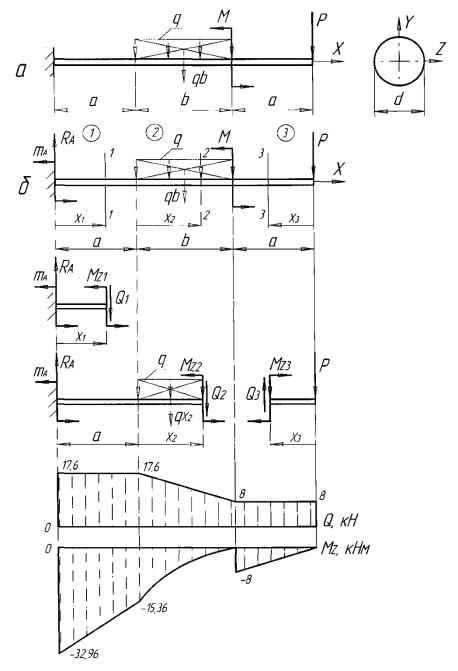
|
|
b |
|
|
mA |
q b a |
|
|
M P (2 a b) , |
|
||||
|
|
2 |
|
|
|
|
1,2 |
|
|
|
|
||
mA |
8 1,2 1 |
|
|
|
|
8 8 (2 1 1,2) |
32,96 |
кН м . |
|
2 |
|||||||||
|
|
|
|
|
|
|
Y 0 ; RА P q b 0 , RА P q b ,
RА 8 81,2 17,6 кН.
Рисунок – Расчетная схема консольной балки, эпюры поперечной силы и изгибающего момента
132

Рассчитываем и строим эпюры поперечных сил и изгибающих моментов по участкам.
Участок 1; 0 x1 a
Q1 RA 0 ,
Q1 RA 17,6 кН.
МZ1 mA RA x1 0 ,
МZ1 mA RA x1 ,
МZ1 X1 0 mA 32,96 кН м ,
МZ1 X1 a mA RA a 32,96 17,6 1 15,36 кН м .
Участок 2; 0 x2 |
b |
|
|
|
|
|
|
|
|
|||||||||||||
|
|
|
|
|
|
|
|
|
|
|
Q2 RA q x2 0 , |
|
|
|
||||||||
|
|
|
|
|
|
|
|
|
|
|
|
|
Q2 RA q x2 , |
|
|
|
||||||
|
|
|
|
|
|
|
|
|
|
|
Q2 |
|
X2 0 RA 17,6 кН, |
|
|
|
||||||
|
|
|
|
|
|
|
|
|
|
|
|
|
|
|
||||||||
|
|
|
|
|
|
|
Q2 |
|
X2 b RA q b 17,6 8 1,2 8 кН. |
|
||||||||||||
|
|
|
|
|
|
|
|
|
||||||||||||||
|
|
|
|
|
|
|
МZ2 mA RA (a x2 ) q |
x22 |
0 |
, |
|
|
||||||||||
|
|
|
|
|
|
|
|
|
|
|||||||||||||
|
|
|
|
|
|
|
|
|
|
|
|
|
|
|
2 |
|
|
|
|
|
|
|
|
|
|
|
|
|
|
|
|
МZ2 mA R A |
(a x2 ) q |
x22 |
, |
|
|
|
|||||||
|
|
|
|
|
|
|
|
|
|
|
|
|
||||||||||
|
|
|
|
|
|
|
|
|
|
|
|
|
|
|
2 |
|
|
|
|
|||
|
|
|
МZ2 |
|
X2 0 |
mA RA a 32,96 17,6 1 15,36 кН м , |
|
|||||||||||||||
|
|
|
|
|
||||||||||||||||||
М |
|
|
m |
|
R |
|
(a b) q |
b2 |
32,96 17,6 (1 1,2) 8 |
1,22 |
0 |
|||||||||||
Z2 |
X2 b |
A |
A |
|
|
|||||||||||||||||
|
|
|
|
|
|
|
2 |
|
|
|
|
|
2 |
|
||||||||
|
|
|
|
|
|
|
|
|
|
|
|
|
|
|
|
|
кН м .
Участок 3; 0 x3 a
Q3 P 0 ,
Q3 P 8 кН.
МZ3 P x3 0 ,
МZ3 P x3 ,
МZ3 X3 0 0 ,
МZ3 X3 a P a 8 1 8 кН м .
Определяем диаметр сечения консольной балки d из условия прочности [1, 2]
133
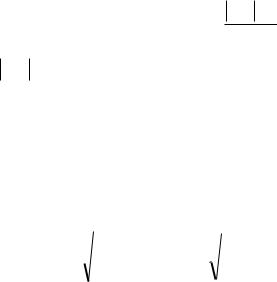
σmax MZ max [σ] ,
WZ
где МZ max – изгибающий момент в опасном сечении балки, который
|
|
= |
|
МZ1 |
|
= 32,96 кН м = 32,96 106 |
Н мм . |
|
определяем по эпюре, |
МZ |
max |
|
|
||||
|
|
|
|
|
|
|
|
WZ – осевой момент сопротивления круглого сечения балки, мм3 , который равен
|
|
|
|
|
|
W |
π d3 |
, |
|
|
||
|
|
|
|
|
|
|
|
|
||||
|
|
|
|
|
|
|
Z |
32 |
|
|
|
|
|
|
|
|
|
|
|
|
|
|
|
|
|
|
|
|
|
|
|
|
|
|
|
|
||
|
|
32 |
МZ |
|
|
|
|
32 32,96 106 |
||||
d 3 |
|
|
max |
= 3 |
|
|
|
|
|
149,76 мм. |
||
π [σ ] |
|
|
|
|
||||||||
|
|
|
|
|
|
π 100 |
С учетом неравенства округляем диаметр сечения балки до стандартного d = 150 мм.
Литература
1.Миролюбов И.Н. Сопротивление материалов. Пособие по решению задач.- Москва: Лань,
2014.-508с.
2.Степин П.А. Сопротивление материалов. Пособие по решению задач.- Санкт-Петербург:
Лань, 2014.-592с.
УДК 631.362
П.П. Заякин, А.А. Двоеглазов – студенты 3 курса; В.Д. Галкин - научный руководитель, д-р техн. наук, профессор;
А.Д. Галкин - научный руководитель, д-р техн. наук, профессор, ФГБОУ ВО Пермская ГАТУ, г. Пермь, Россия
ТЕНДЕНЦИИ СОВЕРШЕНСТВОВАНИЯ ЗЕРНОСУШИЛОК И ИХ ИСПОЛЬЗОВАНИЯ
Аннотация. Исследованиями Андрианова Н.М. установлено, что использование в шахтных зерносушилках перфорированных коробов обеспечивает снижение неравномерности сушки зерна и семян за счет повышения равномерности подачи теплоносителя. При этом увеличивается интенсивность сушки. Достоинством модульных колонковых зерносушилок сотового типа является возможность с ростом урожайности наращивания их производительности путем установки дополнительных модулей. Сушку зерна и семян целесообразно осуществлять по двухэтапной технологии, предусматривающей обработку зерна на высокотемпературной сушилке, отлѐжку, досушивание охлаждением на установках активного вентилирования или в бункерах.
Ключевые слова:зерносушилки, условия работы, оценки.
Одной из главных задач послеуборочной обработки зерна и семян является сокращение количественных и качественных потерь конечного продукта в процессе проведения технологических операций, начиная от приема комбайнового
134
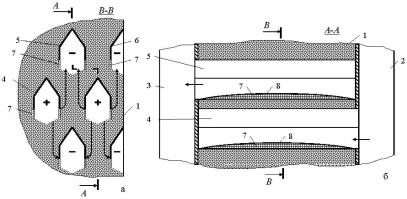
вороха и заканчивая его хранением. Среди технологических операций, направленных на снижении влажности зерна c обеспечением его дозревания основной является сушка.
В настоящее наиболее широкое применение получили зерносушилки шахтного, колонкового и карусельного типов.
Целью работы является выявление тенденций совершенствования шахтных, колонковых и карусельных зерносушилок и их использования.
Среди исследований процесса сушки в шахтных зерносушилках, заслуживают внимание работы Н.М. Андрианова, направленные на снижение неравномерности сушки и повышение производительности[1].
Им предложено установить на каждый короб со стороны подводящей камеры специальной насадки. В насадке направление движения газа изменяется с вертикального на горизонтальное, при котором VВ = 0 м/с.
Н.М. Андриановым установлено, что качественный характер изменения поля скорости по длине короба определяется аэродинамической структурой сушильной камеры.
В этой связи предложено изменить сопротивление зернового слоя вдоль короба. Оно технически реализуется применением устройства для сушилок, у которых подводящие и отводящие короба расположены в одном ряду, и применением устройства для сушилок, у которых подводящие и отводящие короба расположены в разных рядах.
Течение газа между перфорированными коробами (рис.1)
Рис.1. Устройство распределения газа в шахтной сушилке: а - поперечный разрез сушильного пространства; б - продольный разрез
осуществляется следующим образом. Через перфорированную область 7 стенок подводящего короба 4 часть газа свободно проникает в слой зерна и течет к открытой донной поверхности соответствующих отводящих коробов 5 либо полу коробов 6, расположенных в соседнем верхнем ряду. Другая часть газа через открытое дно короба 4 поступает в зерновой слой и движется по укороченному пути к перфорированной поверхности 7 соответствующих отводящих коробов либо полу коробов, расположенных в соседнем нижнем ряду. Таким образом, как для верхнего, так и для нижнего ряда отводящих коробов симметрично выполняется условие течения газа по укороченному пути. За счет укорачивания длины линий
135
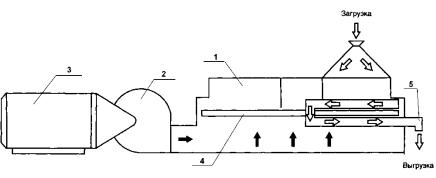
тока обеспечивается уменьшение аэродинамического сопротивления зернового слоя в соответствующей части короба и создаются условия для увеличения расхода газа.
Н.М. Андриановым экспериментально подтверждено (рис.3), что выполнение коробов с перфорацией позволяет изменить аэродинамическую структуру зерносушильной камеры, обеспечивая повышение равномерности и интенсивности сушки зерна.
Колонковые зерносушилки, по сравнению с шахтными, допускают большие удельные подачи теплоносителя, что обеспечивает повышение их производительности. Эти зерносушилки более пригодны для сушки высоковлажного, засоренного зернового вороха [3].
ВПермском крае ООО «Техноград» разработал и выпускает модульные колонковые зерносушилки сотового типа серии «СоСС», производительностью до 40 т/ч. Камеры сушилок состоят из блоков ромбической формы, стенки которых выполнены из перфорированного оцинкованного листа. Теплоноситель нагнетается внутрь этих ромбов.
При сушке в камерах организовано перемещение материала от стенок внутреннего ромба верхнего блока к наружным стенкам нижнего и далее наоборот, что способствует повышению равномерности сушки семян - по температуре нагрева и влажности. Предусмотрена рециркуляция теплоносителя из нижних блоков сушилки и зоны охлаждения, а также возможность использования охладительной камеры в качестве сушильной.
Вкарусельных зерносушилках (Рис.2) [3] реализована схема сушки материала в противотоке с теплоносителем. В этих сушилках зерно высушивается во вращающейся цилиндрической камере (платформе) диаметром до 6 м и толщине слоя материала около 0,5 м. Камера имеет перфорированное днище из пробивных решет, под которое нагнетается теплоноситель. Материал из нижнего слоя удаляется с помощью выгрузного шнека, а сверху добавляется слой исходного материала.
Теория и практика показали, что сушку целесообразно осуществлять по двухэтапной технологии. Технология предусматривает сушку зерна на высокотемпературной сушилке, отлѐжку, досушивание охлаждением на установках активного вентилирования или в бункерах.
Рис. 2. Технологическая схема сушилки: 1 – камера сушильная; 2 – вентилятор; 3
– топочный блок; 4 – платформа поворотная; 5 – разгрузочное устройство
136
Теория и практика показали, что сушку целесообразно осуществлять по двухэтапной технологии. Технология предусматривает сушку зерна на высокотемпературной сушилке, отлѐжку, досушивание охлаждением на установках активного вентилирования или в бункерах.
При медленном охлаждении эта технология позволяет использовать для испарения влаги теплоту, аккумулированную зерном, в большей степени, чем при быстром охлаждении в охладительной зоне сушилки.
В этом случае отлѐжка зерна необходима для выравнивания влаги в зерновках, распределение которой в конце процесса сушки неравномерно.
В результате повышается интенсивность испарения влаги из нагретого зерна, которая в немалой степени определяется совпадением градиентов термо- и влагопроводности.
Использование технологии позволяет существенно снизить энергозатраты на сушку благодаря рациональному использованию теплоты, повысить производительность зерносушилок, сократить потери теплоты с отработавшим теплоносителем, кроме того, сохранить и улучшить качество зерна.
Эффективным способом снижения энергозатратности процесса сушки – применение, наряду с основным (жидким) топливом, использование твердого, например, дров.
Выводы
1.Исследованиями Андрианова Н.М. установлено, что использование в шахтных зерносушилках перфорированных коробов обеспечивает снижение неравномерности сушки зерна и семян за счет повышения равномерности подачи теплоносителя. При этом увеличивается интенсивность сушки.
2.Достоинством модульных колонковых зерносушилок сотового типа является возможность с ростом урожайности наращивания их производительности путем установки дополнительных модулей.
3.Сушку зерна и семян целесообразно осуществлять по двухэтапной технологии, предусматривающей обработку зерна на высокотемпературной сушилке, отлѐжку, досушивание охлаждением на установках активного вентилирования или в бункерах.
Литература
1.Андрианов, Н.М. Повышение эффективности процесса сушки путем совершенствования рабочих органов, системы контроля и управления зерновых сушилок. Автореферат дисс. д-ра техн. наук. С.-Пб. Пушкин, С.Пб. ГАУ. - 40с.
2.Галкин, А.Д., Галкин В.Д. Повышение эффективности работы колонковой зерносушилки сотового типа. /А.Д. Галкин, В.Д. Галкин. Материалы Первой Международной научнопрактической конференции «Научно-технологическое развитие, моделирование, управление и решения для автоматизации деятельности сельскохозяйственных товаропроизводителей региона», 22 марта 2017 г. – Пермь: ИПЦ «Прокростъ», 2017.С.38-42.
3.Зерносушилки колонкового и карусельного типов и методы повышения эффективности их работы. /В.Д. Галкин, А.Д. Галкин, А.В. Голубкович др. – Пермь: Пермская ГСХА, 2010. – 111 с.
137
УДК631.363.285
А.В. Костицин – аспирант; В.Д. Галкин - научный руководитель, д-р техн. наук, профессор,
ФГБОУ ВО Пермский ГАТУ, г. Пермь, Россия
ПЛУНЖЕРНЫЙ ОТЖИМ СЕМЯН РАПСА
Аннотация. При отжиме масла семян рапса используется шнековая или плужерная экструзия. В статье рассматривается влияние изменения давления от времени в процессе плунжерной экструзии. Опытным путем установлено, что плунжерный отжим семян рапса отличается от плунжерного отжима экструдата рапса по характеру нарастания давления и релаксации.
Ключевые слова: рапс, экструдирование, отжим масла, моделирование,
пресс
Впоследние годы одной из востребованных культур для сельхозпроизводителей является рапс. Производство и переработка которого, по-прежнему, имеет большой потенциал как для обеспечения внутренних потребностей, так и удовлетворения спроса внешнего рынка.
Россия является страной, агроклиматические условия которой в полной мере позволяют развернуть широкомасштабное производство масличного рапсового сырья. На сегодняшний день, рапс вызывает значительный интерес, потому что продукты его переработки могут обеспечить население энергетическими продуктами питания (масло), топливом (биодизель), а животноводство – кормовым белком (шрот/жмых).
Врапсе удачно сочетаются высокая потенциальная урожайность семян (3,0-4,0 и более тонн с гектара) и высокое содержание масла (45-48 %) и белка
(22-25 %).
Одно из предназначений рапса – это масло, являющееся наиболее употребляемым в мире растительным маслом, таким же , как подсолнечное и оливковое ,спектр применения которого очень широк. Также его используют в качестве исходного материала при химическом синтезе и применяют в виде смазочных средств, но самое перспективное применение рапсового масла – для производства биотоплива. Рапсовое масло занимает третье место по уровню мирового производства и потребления после пальмового и соевого.
Рапсовый шрот (жмых), полученный после отжима из семян масла, является высокобелковым кормом, содержащим до 43 % протеина, хорошо сбалансированного по аминокислотному составу. В жмыхе в отличие от шрота более высокое содержание жира и следовательно, повышенный уровень обменной энергии.[1]
Экструзионный отжим через зеерную камеру, которая представляет собой часть корпуса экструдера, является одним из способов получения растительного масла. Камера представляет собой набор тонких продольных стальных пластин с малыми зазорами , которые препятствуют проникновению отжатой масличной культуры, но свободно пропускают масло. (рисунок 1)
138
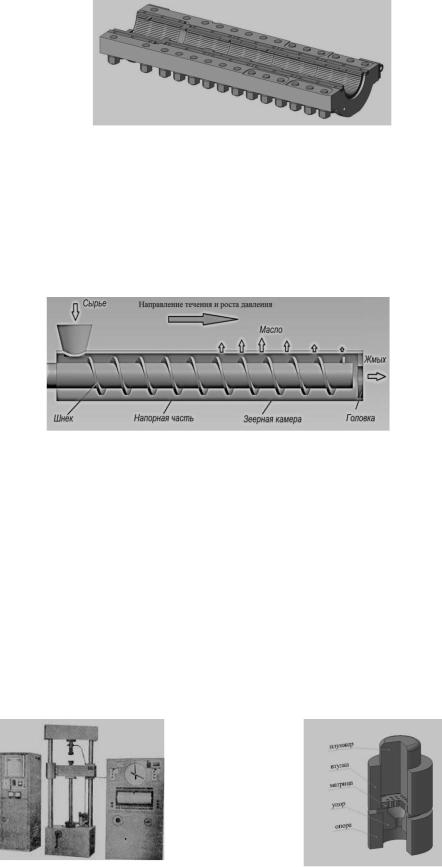
Рисунок 1-Зеерная камера Вращаясь внутри корпуса экструдера, шнек продвигает сырьѐ в направле-
нии к головке, гидродинамическое сопротивление которой создает встречный перепад давления по длине. Происходит фильтрация масла через пластически деформируемую пористую смесь и отжим масла за пределы канала экструдера через зеерную камеру.в результате появляется радиальный перепад давления в канале шнека (рисунок 2). [2]
Рисунок 2 – Схема движения сырья и отжимаемого масла в экструдере Через зазоры между пластинами в зеерной камере происходит отделение
масла от сырья, стекающего в специальную емкость. В результате мы получаем смесь жмыха и масла. После чего необходима дополнительная очистка масла.
Также существует метод плунжерной экструзии масла. Он позволяет более чѐтко регулировать параметры. А затем , полученные результаты можно будет перенести на шнековую экструзию.
Цель работы: выявить зависимость изменения интенсивности отжима масла от изменения уровня давления по времени.
Оборудование и методика эксперимента. Для экспериментов использовалась разрывная машина УМЭ-10 (рисунок 3), притертый плунжер с матрицей , опора и сетка (рисунок 4), рапс урожая 2017 года, весы аналитические . [4].
Рисунок 3-Разрывная машина УМЭ-10 |
Рисунок 4-Приспособления для плун- |
|
жерной экструзии |
|
139 |

Методика. Рапс помещали в цилиндрическую замкнутую полость между поршнем, который создаѐт давление, и проницаемым для жидкости дном с сеткой , и задавали исследуемый уровень давления. Создавали циклические силовые нагружения образцов, используя выбранный уровень давления для выключения. Для создания давления использовали разрывную машину в режиме «сжатие». В ходе эксперимента регистрировали изменение давления во времени и время снижения давления на цикле разгрузки, и объем отжатой жидкости.
Один цикл опыта состоял из этапа поджатия, на котором происходит перемещение поршня и рост давления, и этапа релаксации, на котором поршень остается неподвижным, а давление в образце снижалось в результате отжима масла.[3]
Провели эксперименты по отжиму масла с различными нагрузками и скоростями нагружения, согласно таблице 1.
|
|
Таблица 1 |
|
План эксперимента |
|
|
|
|
№ опыта |
Усилие, кг |
Скорость , мм/мин |
1 |
2000 |
0,1 |
2 |
2000 |
0,5 |
3 |
2000 |
1,0 |
4 |
3000 |
0,1 |
5 |
3000 |
0,5 |
6 |
3000 |
1,0 |
7 |
4000 |
0,1 |
8 |
4000 |
0,5 |
9 |
4000 |
1,0 |
10 |
5000 |
0,5 |
11 |
5000 |
1,0 |
Результаты. Получены графики зависимости времени нагружения и релаксации от усилия, фрагмент которых приведен на рисунке 5, 6).
Диаграмма: Время - Усилия Скорость 0.1 мм/мин
Усилия, кг
2500
2000
1500
1000
500
0
0 |
1000 |
2000 |
3000 |
4000 |
5000 |
|
|
|
Время, сек |
|
|
Усилия, кг
Рисунок 5- Зависимость изменения усилия от времени: 2000кг-0,1 мм/мин
140