
KR1
.pdf9 НАЗНАЧЕНИЕ ДОПУСКОВ ФОРМЫ И РАСПОЛОЖЕНИЯ ПОВЕРХНОСТЕЙ ВАЛА. ЗАДАЧА 9
По ГОСТ 24643-81 назначить допуски формы и расположения поверхностей вала под подшипники, зубчатое колесо, шкив, сальниковое уплотнение, шпонку, определяющих качество работы механизма. Принять уровень относительной геометрической точности – А.
Используя ГОСТ 2.308-79* указать эти допуски на эскизе вала. Пояснить содержание назначенных отклонений формы и расположения.
Назначение допусков формы и расположения зависит от конструктивных и технологических требований к элементам вала. Схема установки вала в рассматриваемом механизме приведена на рисунке 2.1. Рабочая ось вала – ось, проходящая через середины посадочных поверхностей подшипников качения. Поэтому в качестве базы для назначения допусков расположения используется поверхности двух шеек вала ø180 m6 под подшипники, обозначенные на рисунке 9.1 через АВ.
Относительно этой базы назначаются допуски радиального биения посадочных поверхностей под подшипники, под зубчатое колесо, шкив и под сальниковое уплотнение. Допуски торцового биения, определяющие качество работы подшипников, назначаются для заплечиков вала. Ограничение торцового биения буртика вала ø240 необходимо для обеспечения норм контакта соприкасающегося с ним зубчатого колеса. При установлении требований к форме посадочных поверхностей для подшипников качения рекомендуется использовать отклонения от круглости и от профиля продольного сечения. Для обеспечения симметричности шпоночного паза относительно оси вала и равномерности контакта рабочих поверхностей паза вала и шпонки допуск симметричности принимается равным 0,05 мм.
Допуски торцового биения заплечиков вала, влияющих на точность положения внутреннего кольца подшипника следует принять по таблице
9.1 [2, 5, 8]
Таблица 9.1 – |
Допуск торцового биения |
|
||||
|
|
|
|
|||
Интервал номи- |
Допуск торцового биения заплечика вала, не более, мкм |
|||||
нальных размеров |
|
Класс точности подшипника |
|
|||
валов, мм |
нормальный (0) |
|
6 |
|
5 |
|
св. 18 |
до 30 |
21 |
|
13 |
|
8 |
св. 30 |
до 50 |
25 |
|
16 |
|
10 |
св. 50 |
до 80 |
30 |
|
19 |
|
12 |
св. 80 |
до 120 |
35 |
|
22 |
|
14 |
св. 120 до 180 |
40 |
|
25 |
|
16 |
Допуск торцового биения буртика вала TCA для обеспечения норм контакта зубьев в передаче и нормальной работы подшипников рекомендуется принимать равным (см. [3]):
27

ТСА = |
Fβ |
× dσ |
= |
0,045 × 240 |
= 0,0104 |
мм = 10,4 мкм, |
|
3 |
× L |
3 × 345 |
|||||
|
|
|
|
где Fβ – допуск на погрешность направления зуба. Для нашего зубчатого
колеса со степенью точности изготовления 8-В (m = 10, B = 345 мм) согласно ГОСТ 1643-81 Fβ = 45 мкм = 0,045 мм;
dσ – диаметр буртика, dσ = 240 мм;
L – ширина зубчатого колеса, L = 345 мм. Принимаем ТСА = 10 мкм.
Допуск радиального биения поверхности вала под сальниковое уплотнение принимается в пределах от 0,04 до 0,02 мм при частотах враще-
ния от 1000 до 3000 об/мин [3].
Используя изложенные выше рекомендации, а также данные таблиц 21-23, часть 2 (ГОСТ 24643-81) сведём полученные результаты в таблицу
9.2.
Таблица 9.2 – Численные значения допусков
Рассматриваемая |
Наименование |
Степень точно- |
|
Числовое |
Знак услов- |
|||||
сти формы или |
|
значение |
ного обо- |
|||||||
поверхность |
допуска |
|
||||||||
расположения |
допуска, мкм |
значения |
||||||||
|
|
|
||||||||
|
|
Радиальное |
|
|
|
20 |
|
|
||
ø 180m6(++0,0400,015 ) – |
биение |
|
|
|
|
|
||||
|
|
|
|
|
|
|
||||
Круглости |
5 |
|
8 |
|
O |
|||||
под подшипники |
|
|
||||||||
Профиля про- |
|
|
|
8 |
|
|
||||
|
|
|
|
|
|
|
||||
|
|
дольного сечения |
|
|
|
|
|
|||
|
|
|
|
|
|
|
|
|
||
ø220 – диаметр |
Торцовое биение |
см. таблицу 9.1 |
40 |
|
|
|||||
заплечика |
|
|
|
|||||||
|
|
|
|
|
|
|
|
|
||
ø 220u8(++0,3300,258 ) – |
Радиальное |
7 |
|
50 |
|
|
||||
под зубчатое коле- |
|
|
|
|||||||
биение |
|
|
|
|||||||
со |
|
|
|
|
|
|
|
|
||
|
|
|
|
|
|
|
|
|
||
ø240 – диаметр |
Торцовое биение |
TCA = |
Fβ × dσ |
|
|
45 × 240 |
@ 10 |
|
||
буртика |
|
3 × L |
3 × 345 |
|
||||||
|
|
|
|
|
||||||
|
|
|
|
|
|
|
|
|
||
ø160 – под саль- |
Радиальное |
см. рекоменда- |
|
|
|
|
||||
никовое уплотне- |
40 |
|
|
|||||||
биение |
ции выше |
|
|
|||||||
ние |
|
|
|
|
|
|||||
|
|
|
|
|
|
|
|
|
||
ø 130h9(−0,100 ) – |
под |
Радиальное |
8 |
|
80 |
|
|
|||
шкив |
|
биение |
|
|
|
|||||
|
|
|
|
|
|
|
|
|||
32N 9(−0,062 ) – |
под |
Симметричности |
8 |
|
50 |
|
|
|||
шпонку |
|
|
|
|
||||||
|
|
|
|
|
|
|
|
|
В частности, для Ø180 m6 – степень точности формы или расположения – 5 ( таблица 21, часть 2). Допуски круглости и профиля продольного сечения – 8 мкм (таблица 22, часть 2). Допуск радиального биения – 20 мкм (таблица 23, часть 2). Для Ø220 u8 – степень точности формы и распо-
28
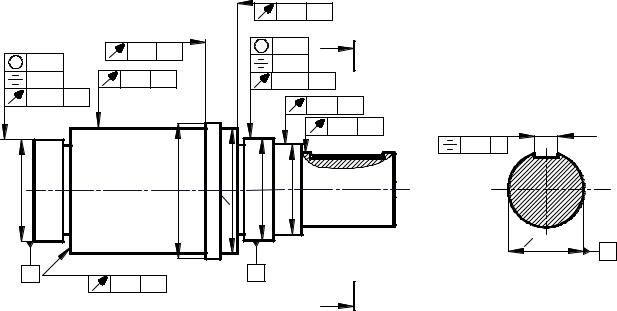
ложения – 7 ( таблица 21, часть 2). Допуск радиального биения – 50 мкм |
||||||||
(таблица 22, часть 2). Для Ø130 h9 и размера 32N9 степень точности формы |
||||||||
и расположения – 8 ( таблица 21, часть 2). Допуск радиального биения |
||||||||
Ø130 h9 – 80 |
мкм, допуск симметричности размера 32N9 – 50 |
мкм (таблица |
||||||
23, часть 2). |
|
|
|
|
|
|
|
|
На рисунке 9.1 приведены обозначения отклонений формы и распо- |
||||||||
ложения в соответствии с ГОСТ 2.308-79*. |
|
|||||||
|
|
|
|
|
|
0,04 |
АВ |
|
|
0,01 |
АВ |
|
|
0,008 |
A |
|
|
|
|
|
|
|
||||
0,008 |
|
|
0,008 |
|
|
|||
|
|
|
|
|
|
|
||
0,008 |
0,05 |
АВ |
|
|
0,020 |
АВ |
|
|
0,020 АВ |
|
|
|
|
|
|
0,04 АВ |
A-A |
|
|
|
|
|
|
|
||
|
|
|
|
|
|
|
|
|
|
|
|
|
|
|
|
0,08 АВ |
|
|
|
|
|
|
|
|
0,05 C |
|
O180m6 |
|
|
O240 |
O220 |
O180m6 |
O160 |
|
|
|
|
|
|
|
|
|
|
O130h9 |
|
|
|
|
|
|
|
|
C |
А |
0,04 |
АВ |
|
В |
|
|
|
|
|
|
|
|
|
|
|||
Рисунок 9.1 – |
|
|
|
|
|
A |
|
|
Обозначение отклонений формы и расположения |
||||||||
|
|
|
|
|
поверхностей |
|
||
10 НАЗНАЧЕНИЕ ПАРАМЕТРОВ ШЕРОХОВАТОСТИ |
||||||||
|
ПОВЕРХНОСТЕЙ ВАЛА. ЗАДАЧА 10 |
|
Назначить требования к шероховатости (ГОСТ 2789-73*) поверхностей вала, исходя из нормального уровня относительной геометрической точности А. Используя ГОСТ 2.309-79* указать назначенные параметры шероховатости поверхностей на эскизе вала. Пояснить содержание назначенных параметров шероховатости.
Основные параметры и числовые значения шероховатости регламентированы стандартом ГОСТ 2789-73*.
В соответствии с рекомендациями минимальные требования к шероховатости поверхности в виде предела допустимых значений среднего арифметического отклонения неровностей профиля Ra или высоты неровностей профиля по десяти точкам Rz устанавливаются в зависимости от допуска размера и формы. Параметр Ra считается предпочтительным потому, что он более точно отражает отклонения профиля (определяется по
29
большему числу точек). Параметр Rz используют, если контроль Ra затруднен.
Числовые значения параметров шероховатости назначаются по связи с допуском размера (формы). Например, при допуске формы 60% от допуска размера Т (относительная геометрическая точность А):
Ra ≤ 0,05T ; |
Rz ≤ 0,2T |
(10.1) |
Полученные значения Ra |
или Rz округляются до ближайшего мень- |
шего стандартного числа по ГОСТ 2789-73* или в нормативных документах приводятся необходимые рекомендации. Для некоторых наиболее характерных видов сопряжений информация приведена в литературе (табли-
цы 10.1 и 10.2).
Таблица 10.1 - Рекомендуемые значения параметра Ra
Характеристика поверхности |
Ra , мкм |
Посадочные поверхности подшипников скольжения |
0,4…0,8 |
Поверхности деталей под посадки с натягом |
0,8…1,6 |
Поверхности валов под уплотнения |
0,2…0,4 полировать |
Таблица 10.2 - Рекомендуемые значения параметра Ra для поверхностей под подшипники качения
Посадочная |
Номинальный |
Значение параметра Ra , |
мкм, не более |
|||
|
Класс точности подшипника |
|||||
поверхность |
размер, мм |
нормальный |
6 и 5 |
|
4 |
|
|
|
(0) |
|
|
||
|
|
|
|
|
|
|
Валов |
До 80 |
1,25 |
|
0,63 |
|
0,32 |
Свыше 80 до 500 |
2,5 |
|
1,25 |
|
0,63 |
|
|
|
|
||||
Отверстий |
До 80 |
1,25 |
|
0,63 |
|
0,63 |
корпусов |
Свыше 80 до 500 |
2,5 |
|
1,25 |
|
1,25 |
Опорных торцов |
До 80 |
2,5 |
|
1,25 |
|
1,25 |
заплечиков валов |
|
|
|
|
|
|
Свыше 80 до 500 |
2,5 |
|
2,5 |
|
2,5 |
|
и корпусов |
|
|
|
|
|
|
При шлифовании поверхностей под подшипники качения канавки для выхода круга принять по таблице 10.3 (ГОСТ 8820-69).
На свободные поверхности вала шероховатость, как правило, назначается Rz 20 и указывается на чертеже или эскизе в правом верхнем углу зна-
ком (рис. 10.1).
Используя приведенные выше рекомендации рассчитаем или назначим числовые значения параметров шероховатости поверхностей вала и сведём их в таблицу 10.4, учитывая при этом стандартные значения параметров Ra и Rz – таблица 24, часть 2 (ГОСТ 2789-73*).
30

Таблица 10.3 – Канавки для выхода шлифовального круга
|
|
|
|
|
|
|
d , мм |
h, мм |
b, мм |
c, мм |
r, мм |
r1 , мм |
|
|
|
|
|
|
|
|
Св. 10 |
до 50 |
0,3 |
3 |
0,5 |
1,0 |
0,5 |
Св. 50 |
до 100 |
0,5 |
5 |
1,0 |
1,6 |
0,5 |
Св. 100 |
0,5 |
8 |
1,0 |
2,0 |
1,0 |
Рисунок 10.1 – Обозначение шероховатости свободных поверхностей
Таблица 10.4 - Принятые значения параметров шероховатости
|
|
До- |
Расчетное |
Рекомендуемое |
Принятое |
|
|
|
|
|
|
|
Рассматриваемая |
значение |
нормативными |
значение |
Обозначение |
||||||||
пуск, |
парамет- |
документами |
по |
|
|
|
по |
|||||
поверхность |
Т, |
ра, мкм |
|
|
|
|||||||
значение Ra, |
ГОСТ2789, |
ГОСТ 2.309.79* |
||||||||||
|
|
мкм |
Ra = |
мкм |
мкм |
|
|
|
|
|
|
|
|
|
|
0,05T |
|
|
|
|
|
|
|
||
|
|
|
|
|
|
|
|
|
|
|
|
|
ø 180m6(++0,0400,015 ) – |
30 |
1,5 |
2,5 |
1,25 |
|
|
|
|
|
|
|
|
|
Ra1,25 |
|||||||||||
под подшипники |
|
|||||||||||
|
|
|
|
|
|
|
|
|
|
|
||
ø220 – |
диаметр |
– |
– |
2,5 |
2,5 |
|
|
|
|
|
|
|
|
|
Ra2,5 |
||||||||||
заплечика |
|
|
||||||||||
|
|
|
|
|
|
|
|
|
|
|
||
ø 220u8(++0,3300,258 ) – |
72 |
3,6 |
1,6 |
1,6 |
|
|
|
|
|
|
|
|
|
|
Ra1,6 |
||||||||||
под зубчатое колесо |
|
|
||||||||||
|
|
|
|
|
|
|
|
|
|
|
||
ø240 – |
диаметр |
– |
– |
2,5 |
2,5 |
|
|
|
|
|
|
|
|
|
Ra2,5 |
||||||||||
буртика |
|
|
||||||||||
|
|
|
|
|
|
|
|
|
|
|
||
ø160 – |
под сальнико- |
– |
– |
0,4 |
0,4 |
|
|
|
|
|
|
|
вое уплотнение |
полировать |
|
|
|
|
|
|
|
||||
|
|
|
|
|
|
|
|
|
|
|||
ø 130h9(−0,100 ) – под |
100 |
5 |
– |
5 |
|
|
|
|
|
|
|
|
|
|
|
Ra5 |
|||||||||
шкив |
|
|
|
|
||||||||
|
|
|
|
|
|
|
|
|
|
|
|
|
32N 9(−0,062 ) – |
62 |
3,1 |
– |
2,5 |
|
|
|
|
|
|
|
|
|
|
Ra2,5 |
||||||||||
под шпонку |
|
|
||||||||||
|
|
|
|
|
|
|
|
|
|
|
31
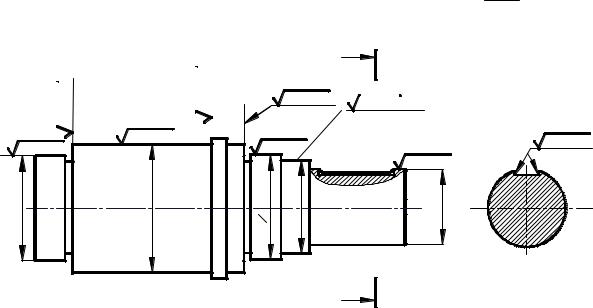
На рисунке 10.2 приведены обозначения параметров шероховатости в соответствии с ГОСТ 2.309-79* (свободные поверхности - Rz20 ).
Ra2,5
|
Ra1,6 |
|
Ra1,25 |
O180m6 |
O220u8 |
Ra2,5
A
Ra2,5 |
Полировать |
|
Ra0,4 |
||
|
Ra1,25 |
|
O180m6 |
O160 |
Ra5 |
O130h9 |
A-A
Ra2,5
A
Рисунок 10.2 – Обозначение параметров шероховатости поверхностей вала
11 АНАЛИЗ ТОЧНОСТИ РЕЗЬБОВОГО СОЕДИНЕНИЯ. ЗАДАЧА 11
1.Привести эскизы резьбового соединения с обозначением посадки и отдельно деталей соединения с обозначением их полей допусков.
2.Пояснить содержание условных обозначений.
3.По ГОСТ 8724-2002 определить номинальные размеры параметров резьбы, показав их на эскизе.
4.Установить предельные отклонения диаметров резьбы по ГОСТ 160932004, их предельные размеры и допуски. Определить зазоры по среднему диаметру.
5.Построить в масштабе 100:1 схему расположения полей допусков, указав предельные размеры диаметров резьбы и зазоры по среднему диаметру.
Проанализируем точность резьбового соединения М24-7Н/6g-45. На рисунке 11.1 приведены эскизы резьбового соединения и отдельно полей допусков деталей соединения.
Условное обозначение указывает, что резьба метрическая (угол профиля α = 60º), с крупным шагом, диаметром 24 мм, длиной свинчивания 45 мм.
7H/6g – обозначение посадки резьбового соединения;
7Н – поле допуска среднего и внутреннего диаметров резьбы гайки; 6g – поле допуска среднего и наружного диаметров резьбы болта;
32
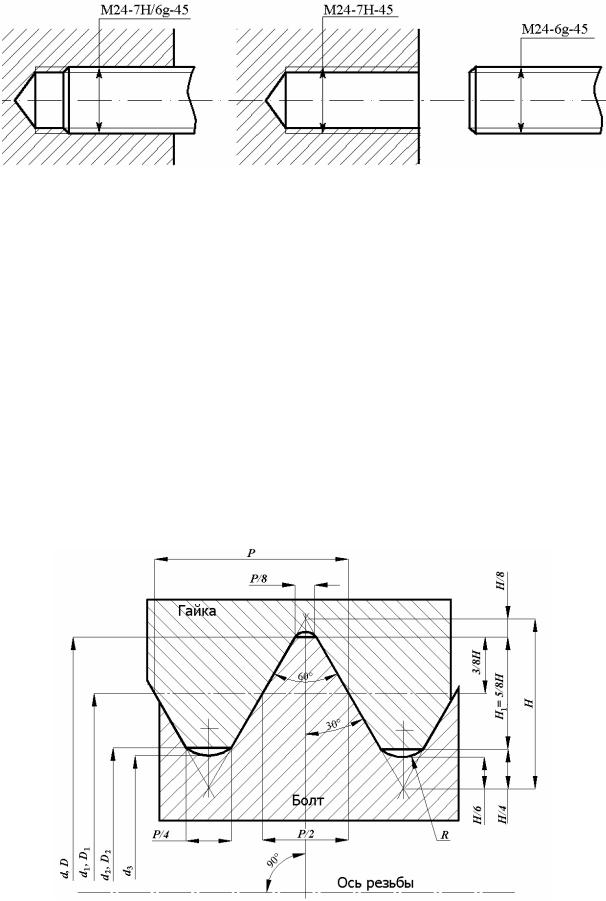
Рисунок 11.1 - Обозначение посадки и полей допусков резьбового соединения
7, 6 – степени точности, определяющие соответственно допуски диаметров резьбы гайки и болта;
Н, g - основные отклонения соответственно диаметров резьбы гайки и болта.
Из таблиц 25 и 26, часть 2 (ГОСТ 24705-81, ГОСТ 8724-2002) выпи-
сываем номинальные размеры наружного D (d), внутреннего D1 (d1) и среднего D2 (d2) диаметров резьбы, шага резьбы Р, исходной высоты профиля Н, а также угла профиля α для резьбы с номинальным диаметром 24 и крупным шагом:
D = d = 24,000; D1 = d1 = 20,752; D2 = d2 = 22,051; Р = 3,0; Н = 0,8667P = 2,600; α = 60°.
На рисунке 11.2 показаны основные параметры анализируемой резь-
бы.
Рисунок 11.2 - Профиль и основные размеры метрической резьбы
33
По таблицам 28 и 29, часть 2 (ГОСТ 16093-2004) устанавливаем предельные отклонения диаметров резьбы, сопрягаемых на посадках с зазо-
ром, мкм: |
|
Для гайки М24-7Н : |
Для болта М24-6g : |
ESD ≈ +H/10; EID = 0; |
esd = -48; eid = -423; |
ESD2 = 335; EID2 = 0; |
esd2 = -48; eid2 = -248; |
ESD1 = 630; EID1 = 0. |
esd1 = -48; eid1 ≈ -H/8. |
Предельные размеры и допуски средних диаметров резьбы болта и |
|
гайки, мм: |
|
D2max = 22,051 + 0,335 = 22,386; |
d2max = 22,051 – 0,048 = 22,003; |
D2min = 22,051 + 0 = 22,051; |
d2min = 22,051 – 0,248 = 21,803; |
TD2 = D2max – D 2min = 0,335; |
Td2 = d2max – d 2min = 0,200. |
Для других диаметров резьбы расчет предельных размеров аналоги- |
|
чен. |
|
Для внутреннего диаметра: |
|
D1max = 20,752 + 0,630 = 21,382; |
d1max = 20,752 – 0,048 = 20,704; |
D1min = 20,752 + 0 = 20,752; |
d1min = 20,752 – 0,325 = 20,427; |
TD1 = D1max – D 1min = 0,630; |
Td1 = d1max – d 1min = 0,277. |
Для наружного диаметра: |
|
Dmax = 24,000 + 0,260 = 24,260; dmax = 24,000 – 0,048 = 23,952; |
|
Dmin = 24,000 + 0 = 24,000; |
dmin = 24,000 – 0,423 = 23,577; |
TD = Dmax – D min = 0,260; |
Td = dmax – d min = 0,375. |
Отклонения шага и половины угла профиля, влияющие на взаимозаменяемость, учитываются допуском на средний диаметр.
Зазоры в соединении по среднему диаметру, мм:
S2max = D2max – d 2min = 22,386 – 21,803 = 0,583;
S2min = D2min – d 2max = 22,051 – 22,003 = 0,048.
Зазоры в соединении по наружному и внутреннему диаметрам, мм:
Smax = Dmax – d min = 24,260 – 23,577 = 0,683; Smin = Dmin – d max = 24,000 – 23,952 = 0,048.
S1max = D1max – d 1min = 21,382 – 20,427 = 0,955;
S1min = D1min – d 1max = 20,752 – 20,704 = 0,048.
На рисунке 11.3 показано расположение полей допусков диаметров резьбы, предельные размеры и зазоры.
В отличие от схем расположения полей допусков гладких соединений для схемы расположения полей допусков резьбового соединения условно принимается соосное расположение резьбы болта и гайки, поэтому на схеме откладываются половины значений отклонений (рисунок 11.3).
Учитывая особенности работы резьбового соединения М24-7Н/6g-45 и его точность, контроль параметров резьбы рекомендуется осуществлять резьбовыми калибрами.
34

Вид А |
|
ESD |
|
1 |
2 |
Поля допусков Поля допусков
D и d |
D2 |
и d2 |
eid |
||
|
|
|
|
||
|
|
|
|
1 |
2 |
|
|
|
|
|
|
|
2 |
|
D= |
|
|
|
|
|
|
|
|
|
|
|
|
|
|
|
ESD |
|
|
|
|
|
|
|
|
|
|
|
профиль |
|
|||
|
1 2 |
max |
|
|
|
|
|
|
|
|
|
|
|
Номинальный |
|||
|
min |
|
|
|
|
|
max |
esd |
min |
D=d |
|
|
|
|
|
||
|
|
D |
D |
|
|
|
|
|
d |
1 2 |
d |
|
|
|
|
|
|
|
2 |
|
2 |
|
2 |
d= |
|
|
|
|
|
|
|
|
|
|
|
|
=D |
|
|
esd |
|
|
|
|
|
|
|
|
|
|
|
||
2max |
2min |
2min |
eid |
2max |
|
2 |
1max |
ESD |
D= |
|
|
|
|
esd |
|
|
|
1 2 |
2 |
|
|
|
|
1 |
|
1 |
|||||||||
|
|
|
1 2 |
|
|
D |
|
1 |
1 |
|
|
|
|
1 |
|
|
1 |
D |
D |
d |
d |
|
D |
1 2 |
1min |
Поля допусков |
1min |
1 2 |
eid |
1max |
= |
||||
|
D |
||||||||||||||||
|
|
|
|
|
|
|
|
|
|
|
|
|
|
|
|||
|
Ось резьбы |
|
|
|
|
|
|
|
D |
|
D1 и d1 |
d |
|
1 2 |
d |
|
|
|
|
|
|
|
|
|
|
|
|
|
|
||||||
|
|
|
|
|
|
|
|
|
|
|
|
|
|
|
|
|
|
|
Рисунок 11.3 – |
Схема расположения полей допусков диаметров |
|
|
|||||||||||||
|
|
резьбы для посадке М24-7Н/6g-45 |
|
|
|
|
|
|
12 ХАРАКТЕРИСТИКА СХЕМЫ СЕРТИФИКАЦИИ И ДОКУМЕНТА
ОПОДТВЕРЖДЕНИИ СООТВЕТСТВИЯ. ЗАДАЧА 12
1.Опишите схему сертификации вала [1, 2] в соответствии с вариантом задания.
2.Приведите перечень пунктов, которые должна содержать декларация о соответствии (Статья 24 Закона «О техническом регулировании», п. 5).
35
В соответствии с вариантом задания схема 1 предусматривает проведение испытаний вала (типового образца продукции) в аккредитованной испытательной лаборатории (таблица 12.1).
|
Таблица 12.1 – |
Схема сертификации продукции |
|||
|
|
|
|
|
|
№ |
|
Испытание |
|
Проверка производства |
Инспекционный контроль |
схемы |
|
(системы качества) |
сертифицированной продукции |
||
|
|
||||
1 |
|
Испытание |
|
- |
- |
|
продукции |
|
|||
|
|
|
|
|
Схема 1 предназначена для ограниченного объема выпуска отечественной продукции, а также импортируемой, поставляемой по кратковременному контракту.
Для рассматриваемого вала испытания должны включать:
∙оценку механических свойств материала вала в соответствии с заданным чертежом;
∙величину осевых и диаметральных размеров и их отклонений с учетом данных чертежа;
∙значения отклонений формы и расположения поверхностей;
∙оценку параметров шероховатости поверхности;
∙величину параметров резьбового соединения.
Характеристика документа, подтверждающего соответствие (декларация о соответствии, сертификат соответствия), основывается на данных Федерального закона №184 «О техническом регулировании» или литературы [1, 2] и др.
36