
KR1
.pdf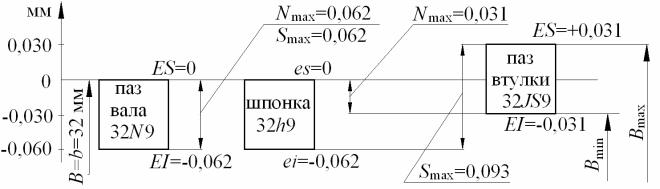
По найденным значениям отклонений чертим схему расположения полей допусков (рисунок 4.3) и проводим анализ этих посадок (см. таблицу
4.2).
Рисунок 4.3 – Схема расположения полей допусков посадок шпонки с пазом вала и с пазом втулки
Таблица 4.2 – Анализ посадки шпонки в паз вала и паз втулки
Наименование |
Паз вала |
|
Шпонка |
|
Паз втулки |
|||
Обозначение поля допуска |
32N9 |
|
|
32h9 |
|
|
32JS9 |
|
Верхнее отклонение, мкм |
ES = 0 |
|
es = 0 |
|
ES = +31 |
|||
Нижнее отклонение, мкм |
EI = -62 |
|
ei = -62 |
|
EI = -31 |
|||
Наибольший |
предельный |
|
|
|
|
|
|
|
размер, мм |
|
Bв. max = 32,000 |
|
bшп. max = 32,000 |
Bвт.max = 32,031 |
|||
Наименьший |
предельный |
|
|
|
|
|
|
|
размер, мм |
|
Bв. min = 31,938 |
|
bшп. min = 31,938 |
Bвт.min = 31,969 |
|||
Допуск размера, мм |
TBв = Bв. max – |
|
Tbшп = bшп.max – |
TBвт = Bвт. max – |
||||
– Bв.min= 0,062 |
|
– b шп. min = 0,062 |
– Bвт.min= 0,062 |
|||||
|
|
|
||||||
Наибольший натяг, мм |
Nmax = bшп. max – Bв.min = 0,062 |
|
|
|||||
|
|
|
Nmax = bшп.max – |
Bвт.min = 0,031 |
||||
|
|
|
|
|
||||
Наибольший зазор, мм |
Smax = Bв.max – bшп.min = 0,062 |
|
|
|||||
|
|
|
|
|
|
|
||
|
|
|
Smax = Bвт. max – |
bшп. min = 0,093 |
||||
|
|
|
|
|
||||
Допуск посадки, мм |
TN ( S ) = TB |
+ Tb |
= Nmax + Smax = 0,124 |
|
||||
â |
øò |
|
|
|
|
|
||
|
|
|
TN ( S ) = TB |
+ Tb |
= Nmax + Smax = 0,124 |
|||
|
|
|
|
|
||||
|
|
|
|
|
âò |
øò |
|
17
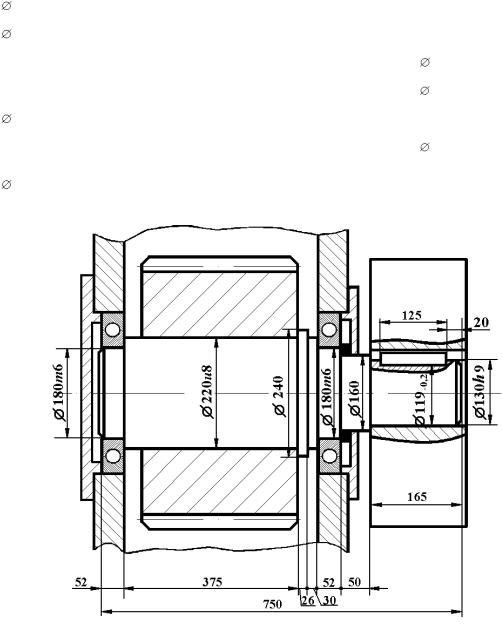
5 НАЗНАЧЕНИЕ РАЗМЕРОВ ВАЛА. ЗАДАЧА 5
Используя заданные по варианту размеры (см. данные заданий 2, 3 и 4), назначить недостающие осевые и диаметральные размеры ступеней вала, исходя из особенностей конструкции (рисунок 2. 1).
Исходя из приведённых в задачах 2, 3, 4 диаметральных размеров ступеней вала, назначаем недостающие размеры. Данные сведены в таблице 5.1 и показаны на рисунке 5.1.
Таблица 5.1 – Размеры вала
Диаметр |
Заданные размеры |
Конструктивно назначенные |
||
ступени, мм |
сопрягаемых деталей, мм |
размеры ступеней вала, мм |
|
|
180 |
Ширина подшипника В = 52 |
Ширина ступени |
52 |
|
220 |
Ширина зубчатого колеса |
Ширина ступени с учётом места под |
||
L = 345 |
съёмник для левого подшипника 375 |
|||
|
||||
– |
Буртик – упор для зубчатого колеса |
Назначаем: 240; ширина |
26 |
|
– |
Ступень для съёмника перед пра- |
Назначаем: 220; ширина |
30 |
|
вым подшипником |
||||
|
|
|
||
180 |
Ширина подшипника В = 52 |
Ширина ступени |
52 |
|
– |
Ступень под крышку с сальниковым |
Назначаем: 160; ширина |
50 |
|
|
уплотнением |
|
|
|
130 |
Ширина шкива b = 170 |
Ступень под шкив на 5 мм |
|
|
короче |
165 |
|||
|
|
|||
|
|
Общая длина вала 750 мм |
|
Рисунок 5.1 - Эскиз вала с назначенными размерами
18

6 РАЗМЕРНЫЕ ЦЕПИ. ЗАДАЧА 6
При обработке вала с размерами, установленными в задаче 5, необходимо обеспечить отклонения размера между опорами под подшипник по двенадцатому квалитету (h12). Для этого необходимо:
1.Составить схему размерной цепи.
2.Решить прямую задачу (задачу синтеза) размерной цепи с помощью метода полной взаимозаменяемости. При этом:
-проверить замкнутость размерной цепи;
-определить допуски составляющих звеньев с использованием метода равной точности;
-назначить одно из звеньев увязывающим для последующей корректировки несоответствия между расчётным коэффициентом точности и принимаемым стандартным;
-определить отклонения составляющих звеньев и произвести проверку правильности решения.
Для нормальной работы редуктора необходимо при обработке вала
выдержать размер между опорами под подшипники А = 431h12 = 431-0,630
(см. рисунки 5.1 и 6.1):
Рисунок 6.1 - Эскиз вала с размерами вдоль оси
19
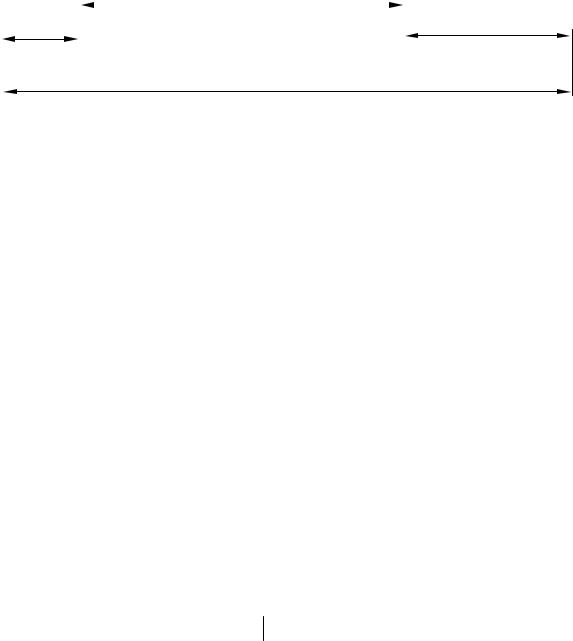
Для соблюдения этого размера с заданными отклонениями требуется правильно задать допуски размеров А1 = 750 мм, А2 = 267 мм, А3 = 52 мм, образующих вместе с размером А = 431 мм замкнутую размерную цепь.
Схема размерной цепи представлена на рисунке 6.2.
|
А3 = 52 |
|
А = 431-0,630 |
|
А2 = 267 |
|
|
|
|||
|
|
Замыкающее звено |
|
||
|
|||||
|
Увязывающее звено |
|
|
|
|
|
|
|
А1 = 750 |
|
|
|
|
|
|
|
|
Рисунок 6.2 - Схема размерной цепи
Звенья А1, А2, А3 – составляющие, звено А – замыкающее. Производим проверку замкнутости размерной цепи, мм:
|
|
m−1 |
+ ξ3 A3 , |
|
|
|
A = ∑ξ j × Aj = ξ1 A1 + ξ2 A2 |
(6.1) |
|
|
|
j =1 |
|
|
где Аj – |
|
номинальные размеры составляющих звеньев; |
|
|
m-1 |
– общее число составляющих звеньев без замыкающего; |
|
||
ξ j |
– |
передаточные отношения составляющих звеньев: ξ = +1 для со- |
||
|
|
ставляющих увеличивающих, ξ = -1 – |
для составляющих умень- |
|
|
|
шающих звеньев. |
|
|
A = +1× 750 -1× 267 -1×52 = 431 мм
Метод полной взаимозаменяемости обеспечивает сборку узла без пригонки, сортировки, индивидуального подбора или регулировки – при любом сочетании размеров деталей значения размера замыкающего звена не выходят за установленные пределы.
В основе расчета методом полной взаимозаменяемости лежит форму-
ла:
|
TA = ∑m−1 [ξ j |
|
×TAj ], |
(6.2) |
|
|
|||
|
j=1 |
|
|
|
где TA |
– допуск замыкающего звена. В нашем случае для А |
= 431h12 |
||
|
TA = A max - A min = 630 мкм = 0,63 мм; |
|
||
ξ j – |
передаточные отношения составляющих звеньев; |
|
||
ТАj – |
допуски составляющих звеньев. |
|
20

Принимаем для расчета допусков составляющих звеньев метод равной точности: допуски составляющих звеньев имеют одинаковую точность, то есть один коэффициент точности kср:
ТАj = kср · ij , |
(6.3) |
где i = 0,453D + 0,001D – единица допуска составляющих звеньев для размеров до 500 мм;
i = 0,004 D + 2,1 – единица допуска составляющих звеньев для разме-
ров свыше 500 мм,
где D – среднее геометрическое граничных значений интервала, попадает размер составляющего звена, мм:
D = Dmin × Dmax .
Тогда
в который
(6.4)
TA |
= ∑m−1 [ |
ξ j |
|
× kcpij ]; |
(6.5) |
|||||
|
||||||||||
|
|
j=1 |
|
|
|
|
|
|
||
kcp |
= |
TA |
×ij ]. |
(6.6) |
||||||
m∑−1[ |
|
ξ j |
|
|
||||||
|
|
|||||||||
|
|
j=1 |
|
|
|
|
|
|
|
Значения единицы допуска для составляющих звеньев:
|
|
мм; i1 = 0,004 |
|
|
|
|
|
|
|
|
|
|
+ 2,1 = 4,9397; |
|
|
|
|
|
|||||||||||||
А1 |
= 750 |
630 ×800 |
|
|
|
|
|||||||||||||||||||||||||
|
|
|
|
|
|
|
|
|
|
|
|
|
|
|
|
|
|
|
|
|
|
|
|
|
|
|
|
|
|
|
|
|
|
мм; i2 = 0,45 × 3 |
|
|
|
|
|
|
|
|
|
|
|
+ 0,001× |
|
|
|
|
= 3,2281; |
||||||||||||
А2 |
= 267 |
250 ×315 |
250 × 315 |
||||||||||||||||||||||||||||
|
= 52 мм; i3 = 0,45 × 3 |
|
|
|
|
|
|
|
|
|
+ 0,001× |
|
|
|
|
|
= 1,8543. |
|
|||||||||||||
А3 |
50 ×80 |
50 ×80 |
|||||||||||||||||||||||||||||
|
|
kcp = |
|
|
|
|
|
630 |
|
|
|
|
|
|
|
|
|
= |
630 |
= 62,86 |
|||||||||||
|
|
|
+1 |
|
× 4,9397 + |
|
-1 |
|
×3,2281+ |
|
-1 |
|
×1,8543 |
|
|||||||||||||||||
|
|
|
|
|
|
|
|
|
10,0221 |
По данным ГОСТ 25346-89 ближайшее меньшее значение коэффициента точности (таблица 6.1) к полученному kср = 62,86 будет для 9-го квалитета. Оно равно 40 (IT9 = 40i).
Таблица 6.1 – |
Значения коэффициента точности |
|
|
|
|
|
||||||||
|
|
|
|
|
|
|
|
|
|
|
|
|
|
|
Квалитет |
|
5 |
6 |
7 |
8 |
9 |
10 |
11 |
12 |
13 |
14 |
15 |
16 |
17 |
Обозначение |
|
IT5 |
IT6 |
IT7 |
IT8 |
IT9 |
IT10 |
IT11 |
IT12 |
IT13 |
IT14 |
IT15 |
IT16 |
IT17 |
допуска |
|
|
|
|
|
|
|
|
|
|
|
|
|
|
Формула |
|
7i |
10i |
16i |
25i |
40i |
64i |
100i |
160i |
250i |
400i |
640i |
1000i |
1600i |
допуска |
|
|||||||||||||
|
|
|
|
|
|
|
|
|
|
|
|
|
|
|
Коэффициент |
|
7 |
10 |
16 |
25 |
40 |
64 |
100 |
160 |
250 |
400 |
640 |
1000 |
1600 |
точности |
|
|
|
|
|
|
|
|
|
|
|
|
|
|
21

Назначаем по таблице 4, часть 2 (ГОСТ 25346-89) допуски составляющих звеньев А1 = 750 мм и А2 = 267 мм по 9-му квалитету:
ТА1 = 0,200 мм; TA2 = 0,130 мм.
Звено А3 выбираем увязывающим.
Сумма допусков составляющих звеньев без увязывающего
m−2 [ TA ] TA TA 0,200 0,130 0,330 TA 0,630 , (6.7)
∑ ξ j × j = 1 + 2 = + = < = мм
j=1
что меньше допуска замыкающего звена. Их разница равна допуску увязывающего звена:
|
|
|
1 |
|
m−2 |
|
|
|
|
TAувяз = |
|
× TA - ∑[ξ j |
×TAj ] = 0,630 - 0,330 = 0,300 мм. (6.8) |
||||
ξ увяз |
||||||||
|
|
|
|
j=1 |
|
|
||
Отклонения составляющих звеньев (EsAj – верхнее, EiAj – |
нижнее, |
|||||||
EcAj = |
EsAj + EiAj |
– среднее) |
назначаем как отклонения основного отвер- |
|||||
|
||||||||
2 |
|
|
|
|
|
|
||
стия или вала – в тело детали: |
|
|
|
|||||
для звена А1 (750h9) – |
в минус: EsA1 = 0; EiA1 = -200; EcA1 = -100 мкм; |
|||||||
для звена А2 (267H9) – |
в плюс: EsA2 = +130; ЕiА2 = 0; EcA2 = +65 мкм; |
|||||||
для звена А (431h12) задано: EsА = 0; EiА = -630; EcА = -315 мкм. |
||||||||
Поле допуска увязывающего звена должно располагаться так, чтобы |
||||||||
выполнялось равенство: |
|
|
|
|
||||
|
|
|
|
|
m−1 |
m−2 |
|
|
|
|
|
EcA = ∑[ξ j × EcAj ]= ∑ξ j EcAj + ξ увяз EcAувяз , |
(6.9) |
||||
|
|
|
|
|
j=1 |
j=1 |
|
где EcA – среднее отклонение замыкающего звена, мкм; EcAj – среднее отклонение составляющих звеньев, мкм; EcAувяз – среднее отклонение увязывающего звена, мкм.
Рассчитаем положение середины поля допуска увязывающего зве-
на:
|
|
1 |
|
|
|
m−2 |
|
|
|
1 |
|
EcAувяз |
= |
|
|
EcA - ∑[ξ j |
× EcAj |
] = |
|
|
(EcA - (ξ1 EcA1 + ξ2 EcA2 )); (6.10) |
||
|
|
ξ |
|
||||||||
|
|
ξ увяз |
|
j =1 |
|
|
увяз |
|
|||
EcA |
= |
1 |
×(- 315 - [(+1)×(-100) + (-1)×(+ 65)]) = +150 мкм. |
||||||||
|
|||||||||||
|
|
увяз |
|
|
-1 |
|
|
|
|
|
|
|
|
|
|
|
|
|
|
|
|
Предельные отклонения увязывающего звена Аувяз будут равны:
EsAувяз = EcAувяз + TAувяз/2 = + 150 + (300/2) = + 300 мкм;
22
EiAувяз = EcAувяз – TA увяз/2 = + 150 – (300/2) = 0 мкм.
Результаты расчетов удобно представить в виде таблицы (таблица 6.2):
Таблица 6.2 – Результаты расчетов методом полной взаимозаменяемости
Номиналь- |
Допуск |
Верхнее |
|
Нижнее |
|
Середина |
|
Переда- |
Произве- |
|
|
|
точное |
дение |
|||||
ный размер |
размера |
отклонение |
отклоне- |
|
поля допус- |
||||
|
отноше- |
ξ Аj· ЕсАj |
|||||||
звена Аj, |
ТАj, |
EsAj, |
|
ние EiAj, |
|
ка ЕсАj, |
|
||
|
|
|
ние звена |
(со зна- |
|||||
мм |
мкм |
мкм |
|
мкм |
|
мкм |
|
||
|
|
|
ξ Аj |
ком), мкм |
|||||
|
|
|
|
|
|
|
|
||
431h12 |
630 |
0 |
|
-630 |
|
-315 |
|
|
|
А1 = 750h9 |
200 |
0 |
|
-200 |
|
-100 |
|
+1 |
-100 |
А2 = 267H9 |
130 |
+130 |
|
0 |
|
+65 |
|
-1 |
-65 |
Аувяз = 52 |
300 |
+300 |
|
0 |
|
+150 |
|
-1 |
-150 |
Проверка правильности выполненных расчётов: |
|
|
|||||||
|
n |
m−1 |
|
|
|
|
= 0 − (0 + 0) = 0 ; |
||
EsA = ∑ EsAjyв − ∑ EiAjyм = EsA1 − EiA2 − EiA3 |
|||||||||
|
1 |
n+1 |
|
|
|
|
|
|
|
|
|
n |
|
m−1 |
= EiA1 − EsA2 |
− EsA3 = |
|
||
|
EiA |
= ∑ EiAjyв |
− |
∑ EsAjyм |
|
||||
|
|
1 |
|
n+1 |
|
|
|
|
|
= −200 − (+130 + 300) = −630 мкм,
где EsAjув, EiAjув – отклонения составляющих увеличивающих звеньев, мкм; EsAjум, EiAjум – отклонения составляющих уменьшающих звеньев, мкм.
7 НАЗНАЧЕНИЕ ПОЛЕЙ ДОПУСКОВ ОСЕВЫХ И ДИАМЕТРАЛЬНЫХ РАЗМЕРОВ ВАЛА. ЗАДАЧА 7
Используя данные задач 2, 3, 4, 5, 6 выбрать метод простановки размеров и указать на эскизе полученные поля допусков осевых и диаметральных размеров вала.
Размеры вала (исходя из конструктивных особенностей рассматриваемого узла) получены в разделе 5. При оформлении рабочего чертежа вала (простановка размеров, отклонений и т.д.) следует учитывать особенности технологии изготовления рассматриваемой детали, сборки и измерения. Осевые размеры валов подобной конструкции формируются за два установа или за две операции (закрепление за левую часть при обработке правой и наоборот). Требуемая точность отдельных диаметральных размеров обеспечивается на соответствующих переходах.
При выборе метода простановки, получения (технология) и измерения размеров (цепной, координатный, комбинированный) следует учитывать их особенности.
23
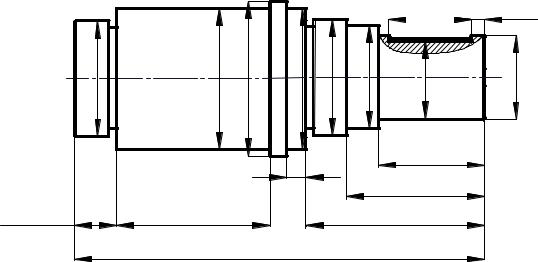
ЦЕПНОЙ МЕТОД – каждый последующий размер измеряется вслед за ранее полученным; связывающая их общая поверхность используется как база (технологическая и измерительная). Погрешности одного размера зависят от погрешностей других размеров, его образующих.
КООРДИНАТНЫЙ МЕТОД – все размеры получаются и измеряются от одной базы (в данном случае от торца вала); при этом погрешность одного размера не влияет на погрешность других размеров.
КОМБИНИРОВАННЫЙ МЕТОД использует особенности первого и второго методов.
На рисунке 7.1 приведена простановка размеров на рабочем чертеже вала с использованием комбинированного метода.
Для обработки левой части (после обработки правой) вал поворачивают на 180°, т.е. происходит смена технологических баз для формирования размеров как вдоль оси, так и диаметральных.
O180m6 |
O220u8 |
O240 |
52 +0,3 |
375 |
|
|
|
|
|
|
125H15 |
20 |
O220 |
O180m6 |
O160 |
-0,2 |
O130h9 |
119 |
||||
|
|
|
165 |
|
30 |
|
215 |
|
|
|
|
|
|
|
|
|
|
267H 9 |
|
|
750h9 |
|
|
|
Рисунок 7.1 – Эскиз вала с указанием полей допусков осевых и диаметральных размеров
Обеспечение при обработке точности размеров 52+0,3 , 267H9 и 750h9 обеспечит точность размера 431h12, определяющего качество сборки. Точность этих размеров принята на основе расчета размерной цепи. Так как для обработки левой части вала размер 431h12 не нужен, на чертеже приводим необходимый для обработки свободный размер 375 мм. Для всех свободных размеров отклонения принимаем по "среднему" классу точности ГОСТ 25670-83, что соответствует 14-му квалитету по ГОСТ 25347-82.
Отклонения диаметральных размеров назначаем исходя из результатов расчетов, полученных в разделах 2-4. Так как предельные отклонения следует назначать для всех диаметральных размеров, проставляемых на чертеже, включая не влияющие на качество сборки и несопрягаемые, их также принимаем по "среднему" классу точности ГОСТ 25670-83.
24
На чертеже это должно быть оговорено общей записью в технических требованиях типа:
Неуказанные отклонения размеров:
отверстий – Н14; валов – h14; остальных – ± IT14/2.
8 ВЫБОР ИЗМЕРИТЕЛЬНЫХ СРЕДСТВ ДЛЯ КОНТРОЛЯ РАЗМЕРОВ ВАЛА ПОД ПОСАДКУ С НАТЯГОМ. ЗАДАЧА 8
1.Определить допускаемую погрешность измерения и рекомендуемые средства измерения вала под посадку с натягом (ГОСТ 8.051-81).
2.Охарактеризовать выбранное измерительное средство: наименование, ГОСТ, цена деления шкалы, диапазон измерений, погрешность измерения, температурный режим, вариант использования (РД 50-98-86).
Допускаемые погрешности измерений назначаются в зависимости от допусков и номинальных размеров измеряемых изделий.
В ГОСТ 8.051-81 приведены установленные значения допускаемых погрешностей измерения для квалитетов IT2 – IT18 по ГОСТ 25346-89. Допускаемые погрешности измерения, установленные стандартом, включают не только погрешности измерительных средств, но и погрешности от других источников (таких, как погрешность от базирования, температурных деформаций и т.д.).
Допускаемые погрешности измерения нормированы вне зависимости от способа измерения размеров при приёмочном контроле.
Для учёта влияния погрешностей измерения в ГОСТ 8.051-81 предусмотрены значения приёмочных границ, которые можно устанавливать совпадающими с нормируемыми предельными размерами проверяемого изделия.
На втором этапе выбора измерительных средств (после определения допускаемых погрешностей) необходимо установить виды измерительных средств, которые обеспечивали бы техническую возможность самого измерения (ГОСТ 4.446-86) [7]. Так измерение внутреннего диаметра ступицы зубчатого колеса можно произвести штангенциркулем, нутромером и т.д., но нельзя измерить рычажной скобой.
На третьем этапе выбора измерительного средства устанавливают значения погрешностей предполагаемых к применению измерительных средств и сопоставляют их величины с допускаемой погрешностью измерения, установленной первоначально. Такие сведения о погрешностях измерения средствами, серийно выпускаемыми специализированными заводами, приведены в ГОСТ 8.549-86.
Выбрать конкретное измерительное средство в зависимости от измеряемого размера можно по ГОСТ 8.549-86, в зависимости от допуска на изготовление и допускаемой погрешности измерения – по ГОСТ 8.051-81.
25
При этом погрешность измерительного средства должна быть меньше допускаемой погрешности измерения.
Для рассматриваемого размера 220u8 (допуск 72 мкм) по таблице 12, часть 2 (ГОСТ 8.051-81) устанавливаем допускаемую погрешность измерения: 18 мкм.
Выписываем накладные измерительные средства для размера 220 и 8 квалитета из таблицы 12, часть 2 – 4 б, 5б, 6б, рекомендуемые ГОСТ 8.54986 [8], в таблицу 8.1. Из таблиц 13-19, часть 2 в таблицу 8.1 вносим предельные погрешности средств измерения и их характеристики (4б – таблица 14, часть 2; 5б - таблица 15, часть 2; 6б – таблица 16, часть 2).
Из этого перечня инструментов (таблица 8.1) выбираем один инструмент, ориентируясь на тип производства и наличие инструментов, используя данные таблицы 20, часть 2. Выбираем микрометр гладкий МК ГОСТ 6507-90* [7]: цена деления 0,01 мм; диапазон измерений 200-225 мм; погрешность измерения 10 мкм; температурный режим – 2 º С; закреплён на стойке (изолирован от рук оператора), данные сведены в таблице 8.2.
Таблица 8.1 - Предельные погрешности средств измерения для контроля вала и их характеристики
|
|
|
Условия измерения |
|
Предельная |
||
|
|
|
|
Класс |
|
|
|
|
СИ и случаи |
Вариант |
Вид |
|
|
погрешность |
|
|
конце- |
|
Температурный |
||||
|
применения |
использо- |
контак- |
вых |
|
режим, оС |
измерения |
|
|
|
мкм |
||||
|
|
вания |
та |
мер |
|
|
|
|
|
|
|
|
|
|
|
|
Микрометр |
Изолиро- |
|
|
|
|
|
4б |
ван от рук |
- |
- |
|
2 |
10 |
|
гладкий МК |
|
||||||
|
|
оператора |
|
|
|
|
|
|
Скоба инди- |
Изолиро- |
|
|
|
|
|
5б |
ван от рук |
любой |
4 |
|
5 |
15 |
|
|
каторная |
оператора |
|
|
|
|
|
|
|
|
|
|
|
|
|
|
Микрометр |
Изолиро- |
|
|
|
|
|
6б |
рычажный |
ван от рук |
любой |
3 |
|
2 |
7 |
|
МР |
оператора |
|
|
|
|
|
Таблица 8.2 - Характеристика выбранного средства и метода измерения
|
|
Пределы |
Цена |
Погрешность |
Метод измере- |
|
Наименование |
ГОСТ |
измерения, |
деления, |
измерения, |
||
ния |
||||||
|
|
мм |
мм |
мкм |
||
|
|
|
||||
Микрометр |
ГОСТ |
200-225 |
0,01 |
10 |
Непосредствен. |
|
гладкий МК |
6507-90* |
оценки |
||||
|
|
|
26