
metod416
.pdf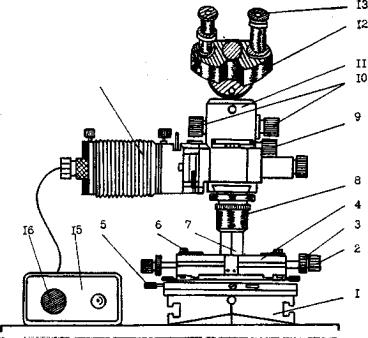
знавания микроструктуры имеет правильный выбор состава электролита, электрического режима и продолжительности травления.
1.6 Устройство металлографического микроскопа ММУ-3
Микроскоп металлографический упрощенный ММУ-3 состоит из оптической, осветительной и механической систем (рисунок 1.2).
Рабочие параметры любого микроскопа определяются его оптической системой. Основные элементы оптической системы – объектив и окуляр (рисунок 1.2).
14
1 - основание; 2 - рукоятка продольного перемещения столика; 3 - рукоятка поперечного перемещения столика; 4 - столик; 5 - винт; 6 - пружинные клеммы; 7 - колонка: 8 - объектив; 9 - рукоятка грубой наводки; 10 - рукоятка точной наводки;
11 - тубус; 12 - бинокулярная насадка; 13 - окуляры; 14 –осветитель; 15 - блок питания; 16 - рукоятка регулирования накала лампы.
Рисунок 1.2 - Металлографический микроскоп ММУ-3
Объектив 8 представляет собой систему линз, установленных в общей оправе и обращенных к рассматриваемому объекту. Основное назначение объектива - создание действительного увеличенного изображения в плоскости объекта окуляра. Оптические характеристики объектива (фокусное расстояние F и числовая апертура) обозначены на его оправе.
Окуляр 13 представляет собой систему линз, установленных в одной оправе и обращённых к глазу наблюдателя. Окуляр даёт мнимое изображе-
11
ние, увеличивая изображение, полученное объективом. Значение собственного увеличения (кратность) окуляра нанесено на его оправе.
Осветительная система состоит из осветителя, линз, светофильтров и диафрагм. Питание лампы осуществляется через блок питания. Рукоятка 16 служит для регулировки накала лампы.
Механическая система у микроскопа имеет штатив, тубус 11 и предметный столик. Микрошлиф устанавливается на предметный столик 4, который перемещается в двух взаимно-перпендикулярных плоскостях с помощью винтов 2 и 3 (рисунок 1.2).
Это позволяет перемещать шлиф на нужное расстояние и просматривать микроструктуры в различных участках без изменения фокусного расстояния
Для получения чёткого изображения микроструктуры шлифа вращением рукоятки 9 производят приблизительное фокусирование. Вращением рукоятки 10 производят микрометрическую фокусировку. Увеличение микроскопа подбирают путём комбинации объективов и окуляров, перемножая их собственные увеличения или пользуясь таблицей 1.1.
Таблица 1.1 - Увеличения микроскопа ММУ-3
Объективы |
|
|
Окуляры |
|
|
|
|
|
|
|
|
|
|
10 |
х |
12,5 |
х |
15 |
х |
|
|
|
|
|
|||
|
|
|
|
|||
F = 25мм, А = |
80 |
100 |
120 |
|||
0,17 |
|
|
|
|
|
|
F = 10мм, А = |
200 |
250 |
300 |
|||
0,40 |
|
|
|
|
|
|
F = 6,3 мм, А |
317 |
396 |
476 |
|||
= 0,65 |
|
|
|
|
|
|
1.7 Порядок выполнения работы
1.7.1Ознакомьтесь с руководством.
1.7.2Определите характер излома полученных образцов, зарисуйте и опишите виды изломов.
1.7.3Изучите устройство микроскопа ММУ-3, пользуясь настоящим руководством. При изучении микроскопа необходимо найти объектив, окуляр, осветитель, научиться пользоваться рукоятками грубой и точной наводки на фокус.
1.7.4Определите общее увеличение микроскопа. Для этого:
1) выпишите характеристики оптической системы микроскопа (на оправке объектива нанесены фокусное расстояние и апертурное число, на оправке окуляра - кратность его увеличения);
12
2) по таблице найдите общее увеличение микроскопа (для установленных на микроскопе объективе и окуляра).
1.7.5Рассмотрите микрошлифы в микроскоп до травления и зарисуйте обнаруженные неметаллические включения, а для чугуна – графит.
1.7.6Зарисуйте микроструктуру стали и чугуна, выявленную травлением, и дайте пояснения к ней.
1.8 Содержание отчёта
1.8.1Цель работы.
1.8.2Описать излом одного образца.
1.8.3Перечислить дефекты выявляемые макроанализом.
1.8.4Описать порядок работы на микроскопе. Кратко описать методику приготовления микрошлифа.
1.8.5Зарисовать микроструктуру образцов стали и чугуна.
1.9Контрольные вопросы
1.9.1Каковы основные методы исследования строения металлов и сплавов? Дайте определение макроанализа, макрошлифа.
1.9.2Какие дефекты металла и особенности его структуры позволяет выявить макроанализ?
1.9.3Какие бывают виды изломов и как они различаются?
1.9.4Назовите дефекты сварных соединений.
1.9.5Дайте определение микроанализа, микрошлифа.
1.9.6Как приготовить микрошлиф? Для чего производят травление?
1.9.7Устройство и работа микроскопа ММУ-3.
1.9.8Назначение травителей.
13
2 Лабораторная работа № 2
Испытание металлов на твёрдость
2.1 Цель работы
Ознакомиться с основными методами определения твердости металлов и сплавов, приобрести навыки измерения твердости на различных приборах.
2.2 Общие сведения
Большинство методов определения твердости основано на принципе вдавливания. Вдавливаются стальной шарик или алмазный наконечник (конус или четырехгранная пирамида).
Твердость – это свойство поверхностного слоя материала оказывать сопротивление упругой и пластической деформации при местных контактных воздействиях со стороны другого, более твердого и не получающего остаточной деформации тела (индентора) установленной формы и размеров. Однако такое определение не является общим, т. к. существуют и другие методы определения твердости, основанные не на принципе вдавливания, а на принципе царапания, маятниковом методе, методе упругой отдачи, динамическом методе и др.
Твердость имеет большое практическое значение, так как характеризует многие рабочие свойства металлов и сплавов, например, износостойкость, режущие свойства и др. Поэтому сложные и требующие времени испытания на растяжение, ударную вязкость и т. д. часто заменяют испытаниями на твердость, которые выполняются значительно быстрее и не требуют больших затрат. Твердость связана определенным соотношением с пределом прочности при растяжении σв.
Испытание на твердость может производиться непосредственно на детали без ее разрушения. Поэтому оно широко применяется не только для изучения свойств металла, но и как метод контроля качества металла в готовых изделиях.
В зависимости от формы индентора (шарик, конус, пирамида) и измеряемой величины (отношение нагрузки к площади полученного отпечатка) различают три метода определения твердости материала: определение твердости по Бринеллю, по Роквеллу, по Виккерсу.
14
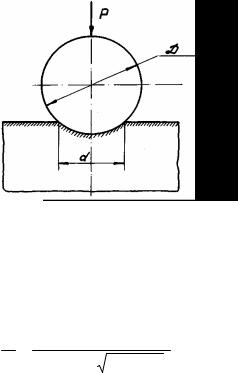
2.3Основные методы определения твердости
2.3.1Метод Бринелля
При измерении твердости по Бринеллю в испытуемый образец вдавливают индентор в виде стального закаленного шарика диаметром D под нагрузкой P, приложенной в течение определенного времени твердость измеряют на приборах ТШ-2 или ТП-2. После снятия нагрузки на поверхности металла образуется отпечаток в виде сферической лунки диаметром d (рису-
нок 2.1).
Рисунок 2.1 - Схема измерения твердости по методу Бринелля
Число твердости по Бринеллю НВ (МПа) определяется отношением приложенной нагрузки P (МН) к площади поверхности сферического отпечатка F (м2):
HB = |
P |
= |
2 P |
, |
(2.1) |
|
F |
|
πD (D − D2 − d 2 ) |
|
|
где D – диаметр вдавливаемого шарика, м; d – диаметр отпечатка, м;
Число твердости по Бринеллю по ГОСТ 9012-59 записывают без единиц измерения. На практике при измерении твердости расчет по указанной формуле не проводят, а используют таблицы. Необходимо отметить, что определение твердости по методу Бринелля допускается для сталей, твердость которых не более 450 НВ, цветных металлов с твердостью не более 200 НВ.
Между пределом прочности σв, МПа, и числом твердости HB, МПа, различных металлов существует следующая приближенная зависимость:
σв = k · HB,
где k – коэффициент.
Сталь с твердостью HB:
1200 – 1750 …………………………σв ≈ 3,4·HB
15

1750 – 4500………………………….σв ≈ 3,5·HB
Медь, латунь, бронза:
отожженная……………………….…σв ≈ 5,5·HB наклепанная………………………….σв ≈ 4,0·HB
Алюминий и алюминиевые сплавы с твердостью
HB = 200 – 450……………………….σd ≈3,3-3,6·HB
Дуралюмин:
отожженный………………………...σв ≈ 3,6·HB
после закалки и старения………..…σв ≈ 3,5·HB
2.3.2 Прибор ТШ-2 для испытания металлов на твердость по методу Бринелля
Прибор ТШ-2 (рисунок 2.2) предназначается для измерения твердости по методу вдавливания стального шарика в соответствии с методикой ГОСТ 9012-59.
|
|
|
а) |
|
б) |
а – общий вид; |
б – схема; |
1 – станина прибора; 2 – подвеска с грузами; 3 – шаровой индентор; 4 – ограничитель; 5 – сменный стол; 6 – винт; 7 – маховик; 8 – пусковая кнопка; 9 – сигнальная лампа
Рисунок 2.2 - Прибор ТШ-2
При испытаниях на твердость применяют шарики диаметром 10; 5 или 2,5 мм в зависимости от толщины испытуемого материала.
Механизмы прибора (механизмы привода, подъема стола, подъема рычажного устройства, реверсирования, нагружения) смонтированы на литой чугунной станине 1.
16
Механизм нагружения состоит из подвески с грузами 2, которые через систему рычагов создают необходимые испытательные нагрузки на шаровом инденторе 3.
Механизм привода, состоящий из электродвигателя и червячного редуктора, обеспечивают работу механизма нагружения и возврата его в исходное состояние. Работа прибора протекает в автоматическом цикле.
Механизм подъема стола состоит из сменного стола 5, винта 6 и маховика 7. Включение прибора осуществляется пусковой кнопкой 8.
Перед проведением испытания следует, в зависимости от твердости материала, выбрать величину испытательной нагрузки и соответствующий индентор (таблица 2.1).
Таблица 2.1 - Ориентировочные параметры испытаний
|
|
Твёрдость по |
Минимальная |
|
|
||||||||||
|
|
Бринеллю, |
Диаметр |
Нагрузка, H |
|||||||||||
Материал |
|
|
|
|
HB |
толщина испы- |
шарика, |
||||||||
|
|
|
|
|
|
МПа |
|
туемого образ- |
мм |
(кгс) |
|||||
|
|
|
|
|
|
ца, мм |
|
||||||||
|
|
|
|
(кгс/ мм2 ) |
|
|
|||||||||
1 |
|
|
|
|
|
2 |
|
|
|
|
3 |
4 |
5 |
||
Черные |
метал- |
1370 − 4410 |
6 - 3 |
10 |
29420 (3000) |
||||||||||
4 - 2 |
5 |
7355 (750) |
|||||||||||||
лы |
|
|
(140 − 450) |
|
|||||||||||
|
|
менее 2 |
2,5 |
1840 (187,5) |
|||||||||||
|
|
|
|
|
|
|
|
|
|
|
|
||||
Черные |
метал- |
< |
|
1370 |
|
|
|
|
более 6 |
10 |
9807 (1000) |
||||
лы |
|
(140) |
|
|
|
|
6 - 3 |
5 |
2452 (250) |
||||||
Цветные метал- |
|
|
|
|
|
1270 |
|
|
|
|
6 - 3 |
10 |
29420 (3000) |
||
лы и сплавы |
> |
|
|
|
|
||||||||||
|
|
|
|
4 - 2 |
5 |
7355 (750) |
|||||||||
(медь, латунь |
(130) |
|
|
|
|
||||||||||
|
|
|
|
|
|
|
|
менее 2 |
2,5 |
1840 (187,5) |
|||||
бронза и т.д.) |
|
|
|
|
|
|
|
|
|
|
|||||
|
|
|
|
|
|
|
|
|
|
|
|
|
|||
Цветные ме- |
|
|
340 −1270 |
|
|
|
|
||||||||
таллы и сплавы |
|
|
9 – 3 |
10 |
9807 (1000) |
||||||||||
(медь, латунь |
|
|
(35 −130) |
6 - 3 |
5 |
(250) |
|||||||||
бронза и т.д.) |
|
|
|
|
|
|
|
|
|
|
|
|
|
||
Цветные металлы |
|
|
|
|
|
|
|
|
|
|
|
|
|
||
и сплавы (алюми- |
|
|
|
78 − 340 |
|
более 6 |
10 |
2452 (250) |
|||||||
ниевые, подшип- |
|
|
|
||||||||||||
|
|
|
(8 − 35) |
||||||||||||
никовые сплавы и |
|
|
|
|
|
|
|||||||||
т.д.) |
|
|
|
|
|
|
|
|
|
|
|
|
|
|
Для шарика диаметром 10 мм при стандартном испытании применяют нагрузку 29420 H (3000 кгс).
В случае шарика меньшего диаметра необходимо сохранять постоянное соотношение нагрузки к квадрату диаметра шарика.
17

P |
= |
3000 |
= 30 |
(2.2) |
|
D2 |
100 |
||||
|
|
|
Диаметр шарика и соответствующую нагрузку следует выбирать так, чтобы диаметр отпечатка находился в пределах от 0,2 до 0,6.
Твердость испытуемого образца определяется путем измерения диаметра отпечатка при помощи микроскопа МПБ-3 (рисунок 2.3) и подсчета по формуле (2.1) или по таблицам (ГОСТ 9012-59).
1 – окуляр; 2 – сетка; 3 – установочное кольцо; 4 – тубус; 5 – колонка; 6 – объектив.
Рисунок 2.3 - Общий вид микроскопа МПБ-3
2.3.3 Метод Виккерса
При измерении твердости по Виккерсу в поверхность шлифованного материала вдавливают алмазный индентор в форме правильной четырехгранной пирамиды. Испытания проводят на приборе ТП-2. После снятия нагрузки P измеряют диагонали отпечатка в виде квадрата, оставшегося на поверхности образца (рисунок 2.4).
18
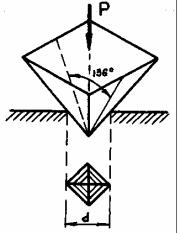
Рисунок 2.4 - Схема измерения твердости по методу Виккерса
Твердость HV (МПа) определяют как отношение нагрузки P к площади боковой поверхности F пирамидального отпечатка:
HV = |
P |
=1,854 |
P |
, |
(2.3) |
|
F |
d 2 |
|||||
|
|
|
|
где P – нагрузка, H;
d – среднее арифметическое значение длины обеих диагоналей отпечатка, мм.
На практике число твердости определяют по специальным таблицам по значению диагонали отпечатка при выбранной нагрузке.
По Виккерсу можно испытывать как мягкие, так и высокотвердые металлы, можно измерять твердость образцов толщиной до 0,3 – 0,5 мм. Метод Виккерса особенно удобен при определении твердости поверхностноупрочненных деталей, имеющих сложную конфигурацию, например, цементованных, азотированных или цианированных зубьев шестерен. Числа твердости по Виккерсу можно перевести в числа твердости по Роквеллу, а также в числа твердости по Бринеллю по таблицам (Приложение А).
Числа твердости по Виккерсу и Бринеллю имеют одинаковую размерность и для материалов с твердостью до 450 HB практически совпадают.
2.3.4 Измерение микротвердости
Методом определения микротвердости оценивают твердость отдельных структурных составляющих: отдельных зерен карбидов, металлических соединений или тонких слоев, получающихся в результате химикотермической обработки и гальванических покрытий, тонких полуфабрикатов (лент, фольги, проволоки). Для этих целей используют приборы моделей ПМТ – 3, (рисунок 2. 5), ПМТ-5.
19

1 – микровинты для перемещения предметного столика; 2 – алмазный наконечник; 3 – колонка; 4 – винт тонкой подачи;
5 – кронштейн; 6 – винт грубой подачи; 7 - окуляр; 8 – окулярный микрометр; 9 – тубус микроскопа; 10 – винты; 11 – осветитель; 12 – объектив; 13 – предметный столик; 14 - основание
Рисунок 2.5 – Прибор ПМТ-3
Определение микротвердости основано на вдавливании под нагрузкой от 0,005 H (5 гс) до 2 H (200 гс) в испытуемый образец алмазной четырехгранной пирамиды и последующем измерении диагонали отпечатка с помощью микроскопа при увеличении до 485 раз.
Поверхность исследуемого образца должна быть отполирована и подвергнута травлению. Значения микротвердости определяют по специальным таблицам (ГОСТ 9450-76) или по той же формуле (2.3), что и твердость по Виккерсу.
На рисунке 2.6 показаны отпечатки, полученные на отдельных структурных составляющих углеродистой стали, содержащей 0,4 % углерода, большой отпечаток (а) получен на мягком феррите, а отпечаток меньших размеров (б) – на твердом перлите.
20