
metod416
.pdf
ным диаметрам. Диаметр образца, у которого в центре твердость соответствует твердости полумартенситной зоны, и будет критическим диаметром. Этот метод рекомендуется применять для углеродистых сталей, прокаливаемость которых определяется в небольших сечениях (до 25-30 мм).
Для более глубоко прокаливающихся легированных сталей используют метод торцовой закалки. Прокаливаемость определяют на стандартных образцах диаметром 25 мм и длиной 100 мм. После нагрева в печи образец быстро переносят в установку, где он охлаждается струёй воды под определенным напором только с торца (рисунок 8.7).
Рисунок 8.7 - Схема охлаждения образца при определении прокаливаемости стали методом торцовой закалки
Температура воды должна быть в пределах от 10 до 25 °С. На поверхности образца не допускаются обезуглероженный слой и окалина. Образцы под закалку для предохранения от окисления и обезуглероживания нагревают в печи с контролируемой атмосферой. Если нагревают в печи без контролируемой атмосферы, образец помещают в стальной стакан с крышкой. Торец образца, предназначенный для охлаждения, ставят на графитовую или угольную пластину.
Скорость охлаждения образца в разных точках по его длине будет различной. У закаливаемого торца скорость охлаждения соответствует скорости охлаждения в воде (1000 °С/с), а у головки образца - скорости охлаждения на воздухе (3-4 °С/с). Остальные участки поверхности образца охлаждаются с промежуточной скоростью. После охлаждения измеряют твердость на приборе по методу Роквелла по длине образца и строят кривую изменения твердости в зависимости от расстояния от закаливаемого торца. При помощи номограммы, разработанной М.Е.Блантером, можно определить критический диаметр изделия.
8.3 Порядок выполнения работы
Работа выполняется двумя подгруппами студентов. Одна подгруппа получает образец из углеродистой стали 40, другая - из легированной стали
40Х.
101

8.3.1Определить температуру нагрева под закалку соответственно мар-
ки стали.
8.3.2Образцы поместить в муфельную печь, нагреть до температуры закалки и выдержать для прогрева по сечению в течение 20 мин.
8.3.3Нагретый образец быстро установить в установку и открыть кран подачи воды. Время от момента извлечения образца из печи до начала охлаждения его струей вода не должно превышать 5 с. Образец должен нахо-
диться под струей воды до полного охлаждения (не менее
10мин).
8.3.4Подготовить образец для измерения твёрдости. По длине закаленного образца сошлифовать слой на глубину 0,2-0,3 мм.
8.3.5На образовавшейся площадке измерить твердость HRC, с шагом
3мм до твёрдости немного меньшей твёрдости полумартенситной зоны.
8.3.6На основании полученных опытных данных построить кривые прокаливаемости в координатах "Твёрдость - расстояние от торца " (рисунок
8.6).
Рисунок 8.6 - Схема определения расстояния от торца до полумартенситной зоны
8.3.7На построенных кривых, зная твёрдость полумартенситной зоны для данной стали, определить глубину прокаливаемости.
8.3.8Используя номограмму М.Е.Блантера, определить искомый кри-
тический диаметр Дкр при охлаждении в трёх средах (вода, масло, воздух). Для определения критического диаметра пользуются шкалой, по-
мещённой в верхней части номограммы, которая характеризует расстояние от закаленного торца до полумартенситной зоны. По опытным данным, полученным при выполнении работы, на указанной шкале нужно найти расстояние до полумартенситной зоны. От найденной точки опустить перпендикуляр до шкалы "идеальное охлаждение". От точки пересечения провести влево горизонтальную линию до пересечения с линией, соответствующей заданной охлаждающей среде (вода), опустить перпендикуляр до шкалы "форма тела" (цилиндр, куб, шар, параллелепипед). В точке пересечения линии с этой шкалой находим ответ: диаметр изделия в мм, имеющий в середине полумартенситную структуру.
102
8.4 Содержание отчёта
8.4.1Цель работы.
8.4.2Определения прокаливаемости, критического диаметра. Значение прокаливаемости в практике термической обработки.
8.4.3Методика проведения испытаний для определения прокаливаемости методом торцовой закалки.
8.4.4Таблица замеров твёрдости по длине образца
Таблица 8.I
Порядок |
Расстояние от охлаждаемого |
Твёрдость HRC |
|
номера |
торца, мм |
сталь 40 |
сталь 40Х |
1 |
1,5 |
|
|
2 |
3 |
|
|
3 |
6 |
|
|
4 |
9 |
|
|
5 |
12 |
|
|
8.4.5Кривые распределения твердости в координатах "твёрдость - расстояние от закаленного торца".
8.4.6Результаты экспериментальной части работы в виде таблицы 8.2.
Таблица 8.2
Марка |
|
Твёрдость |
Расстояние от |
Значение Дкр при охлаждении |
||
стали |
|
полумартен- |
торца до по- |
|
|
|
в воде |
в масле |
на |
||||
|
|
ситной зоны, |
лумартенсит- |
|
|
воздухе |
|
|
HRC |
ной зоны, мм |
|
|
|
Сталь 40 |
|
|
|
|
|
|
|
|
|
|
|
|
|
Сталь 40Х |
|
|
|
|
|
|
|
|
|
|
|
|
|
8.4.7 |
Выводы. |
|
|
|
|
8.5 Контрольныевопросы
8.5.1Что понимается под закаливаемостью и прокаливаемостью?
8.5.2Почему легированные стали имеют большую прокаливаемость при охлаждении в одной и той же среде, чем углеродистые стали?
8.5.3Что понимается под критическим диаметром?
8.5.4Как влияет охлаждающая среда на величину Дкр данной стали?
8.6.5Методы определения прокаливаемости.
8.6.6Как по номограмме определяется критический диаметр?
103

9 Лабораторная работа № 9
Химико-термическая обработка (цементация) стали *)
9.I Цель работы
9.1.1Ознакомление с принципами химико-термической обработки на примере цементации стали.
9.1.2Практическое изучение влияния термической обработки на структуру и свойства сердцевины и поверхностного слоя цементованной стали.
9.2 Общие сведения
Химико-термической обработкой (ХТО) называется тепловая обработка металлов в химически активной среде для изменения химического состава, структуры и свойств поверхностного слоя металлического изделия.
Процесс ХТО включает три элементарные стадии:
1)диссоциацию молекул газообразной среды с образованием активных
атомов;
2)адсорбцию активных атомов и их растворение в поверхностном слое металла;
3)диффузию растворенных атомов вглубь металла и образование диффузионной зоны.
Возможность данного вида химико-термической обработки и характер структуры диффузионного слоя связаны определённым образом с типом диаграммы состояния «металл – насыщающий компонент».
ХТО возможна только в тех случаях, когда диаграмма содержит высокотемпературную область значительной растворимости насыщающего компонента в металле изделия.
Основными видами ХТО сталей являются: цементация (науглероживание), азотирование, цианирование, нитроцементация (совместное насыщение азотом и углеродом), диффузионная металлизация, насыщение поверхностного слоя алюминием, хромом, кремнием, бором и др.
Цементация состоит в насыщении поверхностного слоя стальных деталей углеродом. Цель цементации - получение изделий с твердой износостойкой поверхностью в сочетании с вязкой сердцевиной. Достигается это науглероживанием поверхностного слоя изделий из низкоуглеродистых сталей, (содержащих 0,1 - 0,25 % углерода) с последующей закалкой и низким отпуском.
Среду, в которой производят цементацию, называют карбюризатором.
Восновном применяют два способа цементации: в твёрдом и газовом карбюризаторе. В качестве твёрдого карбюризатора применяют смесь древесного
*) Составлено при участии Синюхина А.В. и Шейнина Б.М.
104
угля с углекислыми солями (обычно до 20-25 % BaCO3). Цементуемые детали упаковывают попеременно с карбюризатором в контейнер (стальной ящик) и нагревают в печи до 910-930 ºС. При нагреве уголь взаимодействует с кислородом воздуха, имеющимся между частичками карбюризатора:
2С + 02 = 2СО
На поверхности деталей протекает реакция диспропорционирования:
2СО СО2 + С
Выделившийся активный углерод адсорбируется поверхностью деталей, а СО2 (в том числе образовавшийся при термическом разложении углекислых солей) взаимодействует с углем, образуя новые порции СО. Скорость цементации в твердых карбюризаторах составляет 0,1-0,15 мм.
В качестве газового карбюризатора используют получаемые в специальных генераторах контролируемые атмосферы, содержащие в определенном соотношении предельные углеводороды и некоторое количество окиси углерода.
Применяют также жидкие углеводороды (керосин, бензол и др.), каплями подаваемые в герметичное печное пространство.
Газовая цементация - более совершенный метод, чем цементация в твёрдых карбюризаторах. Она протекает значительно быстрее, так как исключается время на прогрев и охлаждение массивных контейнеров с малотеплопроводным карбюризатором. Для получения цементованного слоя 1,5 мм при газовой цементации достаточно 2-3 часов. Применяют газовую цементацию, главным образом, на заводах массового и крупносерийного производства.
Схема микроструктуры диффузионного слоя цементованной низкоуглеродистой стали представлена, в сопоставлении с диаграммой железоуглерод, на рисунке 9.1.
Часть слоя, прилежащая к поверхности детали и имеющая концентрацию углерода больше 0,8 %, имеет структуру заэвтектоидной стали: перлит, окруженный сеткой вторичного цементита. Средняя часть слоя, имеющая концентрацию, близкую к эвтектоидному, состоит из перлита. Далее вглубь слоя структура становится доэвтектоидной.
Различают полную и эффективную толщину цементованного слоя. Эффективная толщина соответствует сумме заэвтектоидной, эвтектоидной и половине доэвтектоидной зоны. Обычно она равна 0,5-1,8 мм и в исключительных случаях, при больших контактных нагрузках на цементованную поверхность, может достигать 6 мм. При заданной температуре толщина слоя определяется длительностью цементации. Обычно содержание углерода в поверхностном слое составляет от 0,8 до 1,1 %.
105
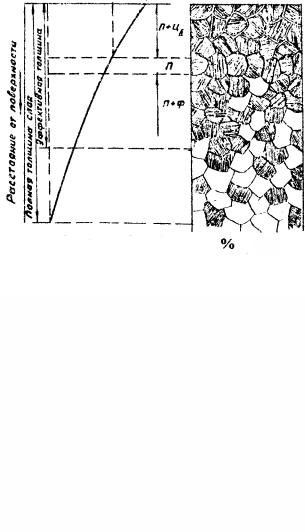
Рисунок 9.1 – Схема микроструктуры диффузионного слоя в сопоставлении с диаграммой железо-углерод
Для получения заданного комплекса механических свойств цементованные изделия подвергают термической обработке.
Для получения в деталях ответственного назначения мелкозернистой структуры, как на поверхности, так и в сердцевине, их подвергают сложной термической обработке, состоящей из двух последовательных закалок и низкого отпуска. При первой закалке, проводимой от температуры, на 30-50 градусов превышающей для цементуемой стали температуру Ас3, происходит перекристаллизация сердцевины, что обеспечивает получение мелкозернистого аустеинта и продуктов его распада. При второй закалке нагрев проводят до температуры Ас1 + (30-50)º. Образовавшийся в поверхностном слое в результате первой закалки мартенсит отпускается с выделением глобулярных карбидов. После второй закалки структура поверхности состоит из высокоуглеродистого мартенсита и глобулярных карбидных частиц, увеличивающих её твёрдость. При этом также обеспечивается мелкое зерно в поверхностном слое.
106
Окончательной операцией термической обработки является низкий отпуск, проводимый при температуре 160-200 °С.
Детали менее ответственного назначения могут подвергаться более простой термической обработке, состоящей из одной закалки и низкого отпуска.
После цементации природно-мелкозернистой стали и содержании углерода в поверхностном слое около 0,8 % однократная закалка дает вполне удовлетворительные свойства, как в сердцевине, так и в цементованном слое деталей. При цементации таких сталей в газовом карбюризаторе целесообразно закалку вести непосредственно с цементационного нагрева.
Структура сердцевины зависит от легированности стали. В деталях из нелегированной стали сердцевина после термообработки состоит из феррит- но-перлитной смеси или из сорбита. В изделиях из легированных сталей сердцевина в зависимости от количества легирующих элементов может состоять из троостита, бейнита или низкоуглеродистого мартенсита.
Во всех случаях из-за низкого содержания углерода сердцевина имеет достаточную вязкость.
9.3 Приборы и оборудование
При выполнении лабораторной работы используются: 1) металлографический микроскоп ММУ-3 или МИМ-7;
2)твердомеры ТП и ТК-2;
3)шлифовально-полировальный станок "НЕРИС";
4)электропечь муфельная с приборами теплового контроля;
5)закалочная ёмкость с водой.
9.4 Порядок выполнения работы
9.4.1Ознакомьтесь со всеми разделами руководства.
9.4.2Изучите влияние термической обработки на твердость сердцевины и поверхностного слоя цементованной стали. Для этого:
I) получите у лаборанта образцы цементованной и нецементованной стали одной и той же марки;
2) на шлифовальном диске станка "НЕРИС" подготовьте поверхность образцов для измерения твёрдости;
3) измерьте твёрдость каждого из образцов на твердомере типа ТП по методу Бринелля. Результаты измерения твердости занесите в таблицу (тип таблицы представлен таблицей 9.1). Следует иметь в виду, что при небольших размерах образцов нецементованный образец по своим свойствам примерно соответствует сердцевине цементованного образца;
107
Таблица 9.1 - Твёрдость цементованных образцов до и после термообработки
№ |
|
|
Твердость НВ |
||
Марка стали |
Участок образца |
|
|
||
до термообра- |
после термо- |
||||
п/п |
|||||
|
|
|
ботки |
обработки |
|
|
|
Поверхностный |
|
|
|
|
|
слой |
|
|
|
|
|
|
|
|
|
|
|
Сердцевина |
|
|
|
|
|
|
|
|
4) проведите закалку каждого из образцов. Температура нагрева под закалку – 820 °С. Охлаждаемая среда - вода. Время выдержки образцов в электропечи определите по таблице 9.2;
Таблица 9.2 - Ориентировочные нормы нагрева стали при термической обработке в лабораторных электрических печах
|
|
Форма изделия |
||
|
|
|
|
|
Температура нагрева, ºС |
круг |
|
пластина |
|
|
|
|
||
Продолжительность нагрева, мин |
||||
|
||||
|
|
|
|
|
|
на 1 мм диаметра |
|
на 1 мм толщины |
|
|
|
|
|
|
800 |
1,0 |
|
2,0 |
|
|
|
|
|
|
900 |
0,8 |
|
1,6 |
|
|
|
|
|
|
1000 |
0,4 |
|
0,8 |
|
|
|
|
|
5)на шлифовальном диске станка "НЕРИС" подготовьте поверхность закаленных образцов для измерения твёрдости;
6)измерьте твердость образцов на приборе ТК-2 (индентор - алмазный конус, нагрузка - 150 кг). Полученную твердость HRC переведите по таблице «Соотношение между числами твёрдости HRC, HRA, НВ, HV в твёрдость по Бринеллю». Результаты занесите в таблицу 9.1
9.4.3. Изучите структуру диффузионного слоя цементованных образцов до термообработки и после нее.
Для этого:
1)получите у лаборанта микрошлифы цементованной стали после термической обработки и без нее;
2)просмотрите структуру диффузионного слоя каждого из образцов с
108
помощью металлографического микроскопа. Определите какие структурные составляющие входят в состав слоя. Оцените как изменилась структура после термической обработки.
В связи с тем, что одновременно просматриваемый под микроскопом участок, как правило, меньше толщины диффузионного слоя, слой следует рассматривать последовательно, перемещая образец под (над) объективом микроскопа, одновременно корректируя фокусировку.
3) Зарисуйте структуру диффузионного слоя до термической обработки и после нее. Укажите какими составляющими представлены структуры.
9.5 Содержание отчета
9.5.1Цель работы.
9.5.2Краткое описание назначения и технологии цементации стали.
9.5.3Рисунки структур диффузионного слоя до и после термической
обработки.
9.5.4Таблица с результатами измерения твёрдости в соответствии с разделом 9.4.2.
9.5.5Выводы по проделанной работе.
9.6 Контрольные вопросы
9.6.1Каково назначение цементации стали?
9.6.2Как можно увеличить толщину диффузионного слоя при цемента-
ции стали?
9.6.3Какова структура диффузионного слоя, полученного в результате цементации стали?
9.6.4Какая термическая обработка проводится после цементации ста-
ли?
9.6.5Чем отличается мартенсит, полученный после закалки цементированного изделия, в сердцевинных участках от мартенсита в наружных слоях образца?
9.6.6Каким образом можно увеличить концентрацию углерода в поверхностном слое изделия при цементации?
109
10 Лабораторная работа № 10
Изучение структуры и свойств легированных сталей
10.1 Цель работы
10.1.1Ознакомиться с основами легирования. Изучить влияние легирующих элементов на структуру и свойства легированных сталей.
10.1.2Изучить маркировку и классификацию легированных сталей, научиться по марке стали определять ее химический состав.
10.1.3Приобретение навыков анализа микроструктур легированных
сталей.
10.2 Основные сведения
Легированными называют стали, в которые для изменения структуры и свойств, кроме углерода, вводят легирующие элементы. Основными легирующими элементами являются: хром, никель, вольфрам, кобальт, титан, ванадий, цирконий и другие, а также марганец и кремний при их повышенном, против обычного, содержании. В легированных сталях, также как и в конструкционных сталях, содержатся постоянные примеси: марганец, кремний, фосфор, сера и другие.
Легирование применяется в двух основных направлениях:
1)для повышения технологичности термической обработки конструкционных и инструментальных сталей (закаливаемость в масле, прокаливаемость и др.);
2)для получения сталей особого назначения, обладающих тем или иным комплексом специальных характеристик (коррозионной стойкостью, жаропрочностью, особыми магнитными свойствами и т.д.).
10.3Влияние легирующих элементов на свойства стали
Преимущества легированных сталей, а также характерные для них специальные свойства проявляются только после соответствующей термической обработки. Поэтому из легированных сталей изготовляют детали, обязательно подвергаемые термической обработке. Улучшение механических свойств обусловлено влиянием легирующих элементов на свойства феррита, дисперсность карбидной фазы, устойчивость мартенсита при отпуске, прокаливаемость, размер зерна.
Для достижения высокой прокаливаемости сталь чаще легируют более дешевыми элементами - марганцем, хромом, бором, а также более дорогими и дефицитными - никелем и молибденом.
Хром (вводят в количестве до 2 %) растворяется в феррите и цементите, оказывая благоприятное влияние на механические свойства, что предопределило его широкое применение. Способствует получению высокой
110