
книги / Принципы технологии основного органического и нефтехимического синтеза.-1
.pdfвая выход ацетальдегида по этилену на уровне 92—95 %. Конверсии за один про ход для двух вариантов реализованных в промышленном масштабе отличаются. Так, если для однореакторного варианта характерна конверсия этилена за один проход 30—50 %, то для двухреакторного — 100 %. Казалось бы, что второй ва риант предпочтительнее. Однако высокие конверсии достигаются за счет двух (вместо одного) дорогостоящих реакторов. Кроме того, двухреакторный вари ант требует обеспечения циркуляции каталитического раствора между реакци онными аппаратами, а следовательно, капитальных затрат на коррозионностой кие насосные устройства, трубопроводы, запорную аппаратуру и т.п. С другой стороны, воднореакторном варианте используется более дорогой окислитель — технический кислород. Все это в совокупности приводит к конкурентоспособ ности двух рассмотренных технических решений.
В рамках технологии окисления этилена в ацетальдегид используют прин цип рециркуляции. В целом, в обоих случаях использование рециклов направ лено на полное использование исходного сырья. Но если в однореакторном ва рианте это просматривается непосредственно — рецикл этилена, то рецикл по катализаторному раствору в двухреакторном варианте обеспечивает работоспо собность реакторной подсистемы в целом и, следовательно, именно его приме нение позволяет достигать стопроцентной конверсии этилена за один проход.
Применение принципа полноты выделения продуктов из реакционной сме си в рассматриваемых технологиях реализуется как получение в виде продукто вой фракции кротонового альдегида с концентрацией, соответствующей азео тропному составу с водой. Отвод тепла за счет испарения продуктов реакции и воды катализаторного раствора не позволяет из-за низкого потенциала в полной мере использовать его для технологических целей. Как правило, степень его ути лизации составляет не более 30 %. В то же время этот показатель может быть уве личен, если поддерживать в теплообменниках-конденсаторах по холодной сто роне достаточно высокое давление и затем направлять подогретую воду (не пар) на питание котлов утилизаторов других технологических подсистем.
С точки зрения создания аппаратов и технологических линий большой еди ничной мощности можно отметить, что, с одной стороны, как и для большин ства гомогенно-каталитических процессов создание аппаратов большой еди ничной мощности затруднено из-за проблем организации контакта газа и жид кости при больших диаметрах аппаратов, сдругой стороны, создание технологическихлиний большой единичной мощности возможно, поскольку работающие параллельно реакторы могут питать единую систему разделения.
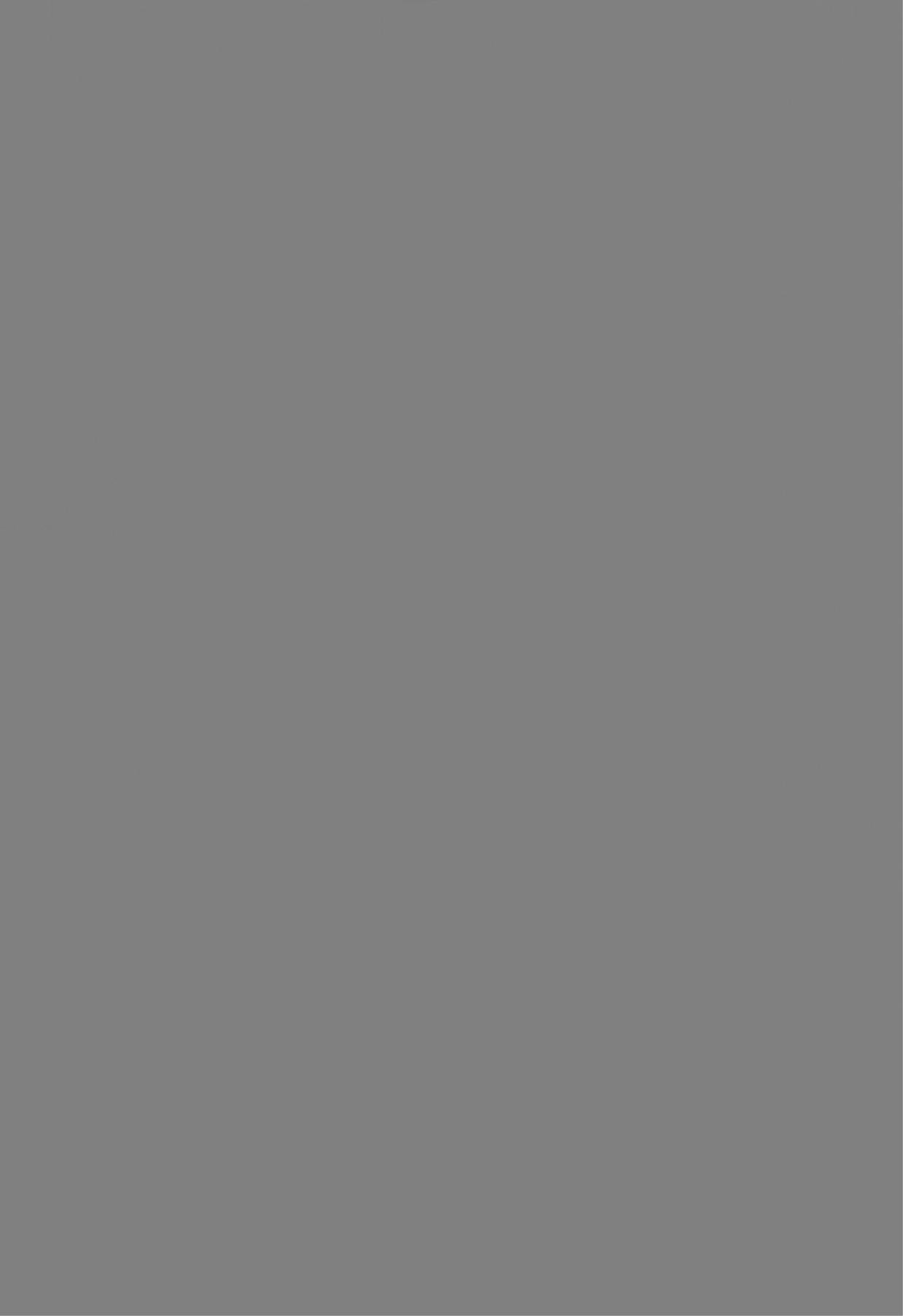