
книги / Принципы технологии основного органического и нефтехимического синтеза.-1
.pdfкомпонентов и условий проведения реакции, структуры образующихся комп лексов и других факторов. Следовательно, управлять процессом можно, меняя указанные условия.
Процесс алкилирования ароматических углеводородов можно представить упрощенной схемой
Н
ArH + R -> Аг ±^->ArR+ ВН+ R к
Если принять во внимание, что промежуточный продукт обладает высокой энергией (в результате чего его концентрация достаточно мала), то можно при менить принцип стационарных концентраций и представить зависимость ско рости реакции в виде
r = d[ArR]/(h = fc,fc2[ArH]fR+][B]/OL, + fc2[B]). |
(7.1) |
Как было отмечено ранее, скорость реакции алкилирования зависит от мно гих факторов, следовательно, возможны различные предельные случаи:
1 ) распад сх-комплекса на исходные компоненты протекает значительно медленнее, чем отрыв протона; тогда Ar2[BJ 22> и величиной к-\ в знаменателе
можно пренебречь. В этом случае выражение (7.1) преобразуется в г = &i[ArH][R+], т.е. реакция имеет второй порядок и концентрация основания не влияет на ее скорость;
2)если к_х2£> £2[В], т о r'= (fcifc2/£:_i)[ArH][R+][B], т.е. реакция имеет третий
порядок и скорость реакции определяется концентрацией основания;
3)если к -1 = Аг2[В] > ки то скорость реакции описывается выражением (7.1) и
нелинейно зависит от концентрации основания;
4)если к\ ~ к-\ > &2[В ], то скорость реакции зависит от концентрации осно
вания и находящегося в избытке исходного реагента.
Для осуществления процесса алкилирования необходимо определить его ли митирующую стадию.
В качестве главных причин, снижающих выход целевых продуктов и способ ствующих протеканию побочных реакций, можно отметить следующие:
S недостаточная чистота исходного сырья и наличие примесей приводит к дезактивации катализатора, затруднению выделения целевых продуктов из-за образования азеотропов или трудно разделяемых смесей, к их накоплению в не которых местах установки, что также может через некоторое время привести к ухудшению условий протекания процесса или качества продукта;
S изменение состава катализаторного комплекса приводит к снижению се лективности реакции, а в ряде случаев — к прекращению протекания реакции переалкилирования;
■S образование прочных комплексов полиалкилароматических соединений с катализатором приводит к его дезактивации;
S изомеризация целевых продуктов реакции и превращение их в побочные продукты за счет вторичных реакций приводят к снижению селективности реак ции.
201
Эти и другие причины обязательно необходимо учитывать как при выборе катализатора и условий проведения процессов и реакций, так и при управлении процессами.
Указанные причины являются общими, т.е. относятся и кдругим технологи ческим объектам, предназначенным для получения продуктов основного орга нического и нефтехимического синтеза.
Рассмотрим влияние указанных выше причин на процесс алкилирования. В качестве примесей, отрицательно влияющих на процесс, можно отметить аце тилен, бутадиен-1,3, СО, С 02, ацетальдегид, эфиры и др. Они по-разному ска зываются на уменьшении выхода целевых продуктов. Так, ацетилен и бутади ен-1,3 полимеризуются на кислых катализаторах с образованием смолистых ве ществ, которые забивают катализаторы и тем самым дезактивируют их. Так же дезактивирует катализатор оксид углерода, который трудно отделить от олефи нов.
Наличие вуглеводородных газах кислорода приводит к резкому увеличению выхода полиалкилбензолов и заметному изменению активности катализаторного комплекса. Это может происходить за счет образования катион-радикалов, изменяющих направленность основного процесса. Альдегиды и эфиры также приводят к увеличению выхода полиалкилбензолов и дезактивации катализато ра. Тиофен и другие серосодержащие соединения способствуют образованию смолистых веществ, не только снижающих активность катализатора, но и за грязняющих целевые продукты. Наличие в бензоле и алкилирующем агенте вла ги приводит к необратимой дезактивации хлорида алюминия, который превра щается в гидроксид алюминия. Следовательно, исходное сырье необходимо подвергать дополнительной очистке и глубокой осушке.
Наконец, при повышении температуры, увеличении времени контакта и концентрации катализатора, при ухудшении перемешивания, изменении соот ношения реагентов наблюдается увеличение концентрации примесей в алкила те. Правда, влияние этих параметров различно. Например, при алкилировании бензола этиленом и пропиленом на А1С13 выход побочных продуктов в большей
степени зависит от концентрации катализатора, чем от температуры. Следова тельно, процесс лучше проводить при повышенных температурах с малым коли чеством активного катализатора.
Обычно выбирают оптимальные условия проведения процесса и поддержи вают их втечение всего периода работы установки на рекомендованном уровне.
Кроме того, для образования комплекса в исходном сырье должен присутст вовать хлорид водорода (0,5 моль на 1 моль А 1 С 1 з). Его можно получить, добав
ляя к сырью соответствующее количество алкилхлорида, который реагирует с бензолом с образованием алкилбензола и хлорида водорода, или за счет частич ного разложения хлорида алюминия водой.
Процесс алкилирования бензола олефинами (наиболее распространенными промышленными алкилирующими агентами) может проводиться как в жидкой, так и в паровой фазе. Следовательно, процесс может быть как жидкофазным, так и парофазным. Используют катализаторы кислотного типа (А1С1 3, H2S 04.
безводный HF, BF3, фосфорная кислота на носителях, алюмосиликаты, цеоли ты, ионообменные смолы). Наиболее перспективными катализаторами являют ся цеолиты и ионообменные смолы, которые позволяют исключить проблемы, связанные с загрязнением окружающей среды.
202
7.2.ТЕХНОЛОГИЯ АЛКИЛИРОВАНИЯ БЕНЗОЛА ОЛЕФИНАМИ
Впоследние годы за рубежом получил распространение процесс фирмы «Mobil» и «Badger» (США), в котором используется катализатор на основе цео
литов. Эта технология применена на нескольких действующих крупных уста новках получения этилбензола с единичной мощностью 335—465 тыс. т этил бензола в год. Процесс производится при 370—500 °С и 1,4—2,8 МПа. По этой технологии образующиеся в процессе полиалкилбензолы возвращаются в узел алкилирования. Конверсия этилена составляет 100 %, а выход этилбензола в расчете на этилен достигает = 98 %.
Однако свое значение сохраняют и технологии, базирующиеся на использо вании в качестве катализатора комплексов на основе хлорида алюминия. Это обусловлено тем, что в его присутствии протекает изомеризация алкилбензолов и переалкилирование диалкилбензолов. Поэтому технологию процесса алкили рования мы рассмотрим на примерах с использованием различных каталитиче ских систем.
Производство этилбензола и изопропилбензола в присутствии хлорида алюми ния (А1С1з). Исходные продукты (бензол и олефины) для процесса алкилирова
ния необходимо очищать от разных примесей, в том числе и воды, так как при наличии влаги будет гидролизоваться А1С13 с образованием НС1. Как очистка,
так и осушка требуют значительных энергетических затрат. В связи с этим чаще всего осуществляют гетероазеотропную осушку исходных продуктов только до 0,002—0,005 %. С другой стороны, необходимая активность А1С13 достигается
только в присутствии НС1, который требуется для образования каталитического комплекса. Для образования комплекса, как правило, используют алкилхлориды (например, C2H5CI). Можно использовать и безводный НС1 (если таковой
имеется на производстве), однако его содержание в реакционной массе регули ровать трудно.
При наличии безводного НС1 катализаторный комплекс готовится центра лизованно из отходов алюминия по следующей реакции:
А1 + 6АгН + НС1 -> (АгН)б • А1С13 НС1
В противном случае в качестве исходного сырья для получения каталитиче ского комплекса используют хлорид алюминия.
Процесс алкилирования бензола олефинами, катализируемый комплексом на основе AICI3 , является жидкофазным и протекает с выделением тепла. Для проведения процесса можно предложить три типа реактора. Наиболее простым является трубчатый аппарат (рис. 7.1, а), в нижней части которого размещается мощная мешалка, предназначенная для эмульгирования катализаторного рас твора и реагентов. Такой тип аппарата часто используется при организации пе риодического процесса.
Реагенты (бензол и олефины), а также катализаторный раствор подают в нижнюю часть реактора. Эмульсия поднимается вверх по трубам, охлаждаясь за счет воды, подаваемой в межтрубное пространство. Продукты синтеза (алкила ты), непрореагировавшие бензол и олефины, а также катализаторный раствор выводятся из верхней части реактора и поступают в сепаратор. В сепараторе про исходит отделение катализаторного раствора от остальных продуктов (алкила та). Катализаторный раствор возвращается в реактор, а алкилаты направляются на разделение.
203
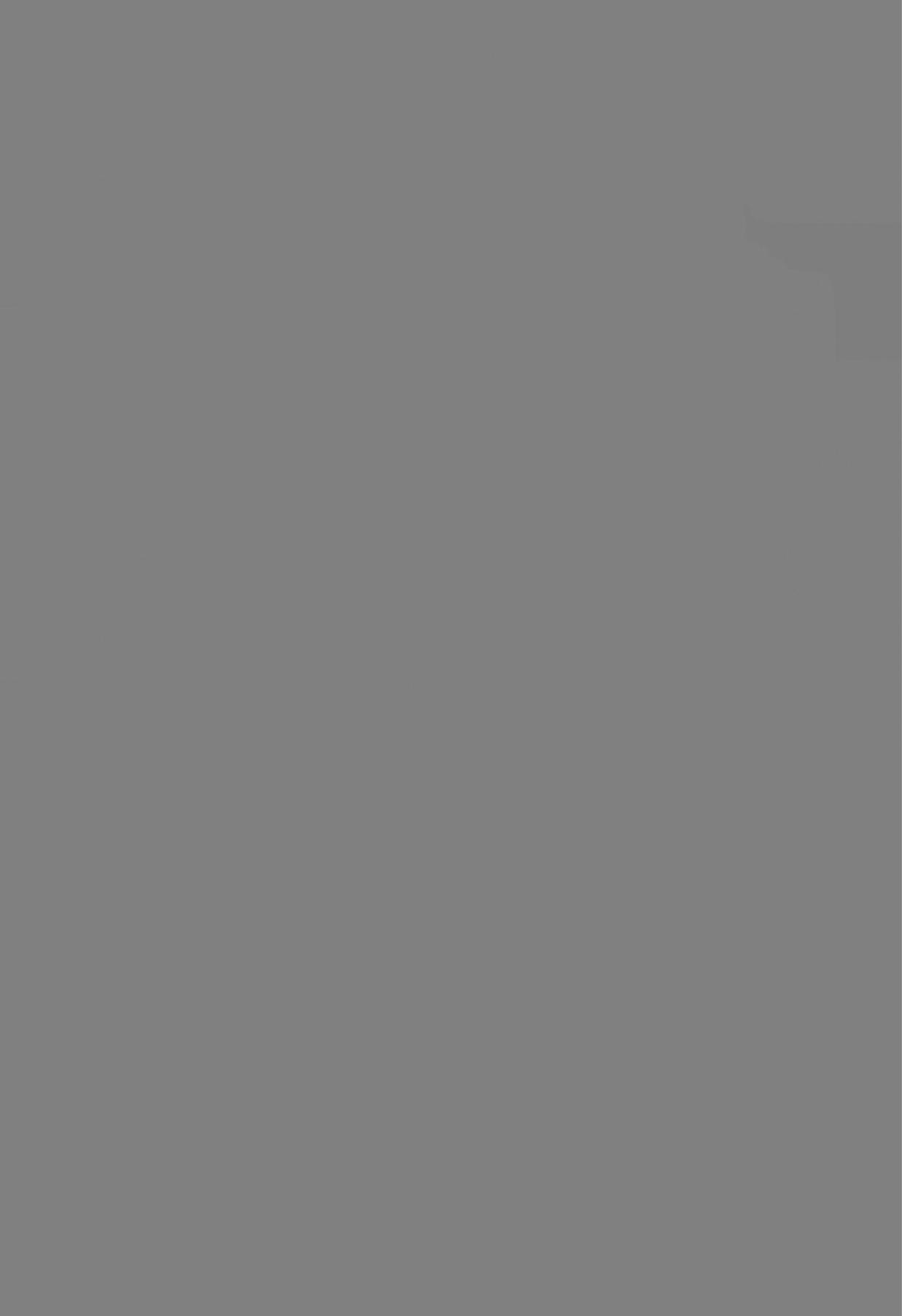
«рубашку», разделенную на секции, а основная часть тепла — за счет нагрева реагентов и испарения избыточного количества бензола. Пары бензола вместе с другими газами, содержащимися в олефине, поступают в конденсатор, в кото ром конденсируется главным образом бензол. Конденсат возвращают в реактор, а несконденсированные вещества выводят из системы для утилизации. В этом случае можно установить автотермический режим, варьируя давление и количе ство отходящих газов (концентрацию исходной олефиновой фракции). При ра боте на разбавленных фракциях олефинов желательно применять давление 0,5—0,6 МПа для облегчения конденсации бензола и поддерживать температуру 130—140 °С. Однако увеличение температуры приводит к повышению степени смолообразования и, соответственно, дезактивации катализатора. В связи с этим процесс целесообразно проводить при р = 0,15—0,20 МПа и незначитель ном количестве отходящих газов. В этом случае температура не превышает 100 °С и уменьшается смолообразование. Катализаторный раствор вместе с про дуктами алкилирования и непрореагировавшим бензолом выводят из верхней части колонны (перед насадкой) и направляют в сепаратор. Нижний (катализа торный) слой возвращают в колонну, а верхний (алкилатный) слой направляют на разделение.
Технология жидкофазного алкилирования имеет следующие подсистемы: гетероазеотропной осушки бензола; реакторного узла; очистки газов от НС1; очистки продуктов алкилирования от НС1; разделения продуктов алкилирова ния.
Рециклы по бензолу и полиалкилбензолам (для приготовления катализаторного комплекса и улавливания бензола) объединяют эти подсистемы в систему. В систему входят потоки: А1С13, этилхлорид (изопропилхлорид), бензол, этан-этиленовая (пропан-пропиленовая) фракция, бензол, водный раствор ще лочи. Выходят из системы следующие потоки: алкилбензолы (этилбензол или изопропилбензол, полиалкилбензолы), газовый, водный раствор щелочи, вод ный раствор хлороводородной кислоты, катализаторный раствор. Следователь но, наряду с продуктами выводятся потоки, которые требуют утилизации, ней трализации и очистки. От этих процессов в значительной степени зависит как экономическая, так и экологическая эффективность предлагаемой технологии.
Технологическая схема рассматриваемой технологии представлена на рис. 7.2. В двухколонном агрегате гетероазеотропной ректификации, состоящем из ректификационной колонны /, отгонной колонны 3 и флорентийского сосуда 2, происходит осушка исходного бензола. Из куба колонны 1 выводится обезво женный бензол, часть которого поступает в аппарат 4 для приготовления катализаторного раствора, а остальная часть в качестве реагента — в реактор 5. В ко лонну 1 поступает как свежий, так и возвратный бензол. Верхние паровые пото ки колонн / и 3 представляют гетероазеотропные смеси бензола и воды. После конденсации в конденсаторе и расслаивания во флорентийском сосуде 2 верх ний слой — обводненный бензол — поступает в колонну 1, а нижний слой — вода, содержащая бензол (по растворимости), направляется в колонну 3.
Каталитический комплекс готовится в аппарате 4 с мешалкой, в который по дают бензол, а также хлорид алюминия, этиленхлорид и полиалкилбензолы. Максимальной активностью обладают комплексы, полученные на шихте, в ко торой мольное соотношение бензол : алкилбензолы составляет (3—5): 1, а моль ное соотношение А1С13: ароматические углеводороды — 1 : (2,5—3,0). Реактор
заполняют катализаторным раствором, а затем входе процесса для подпитки по-
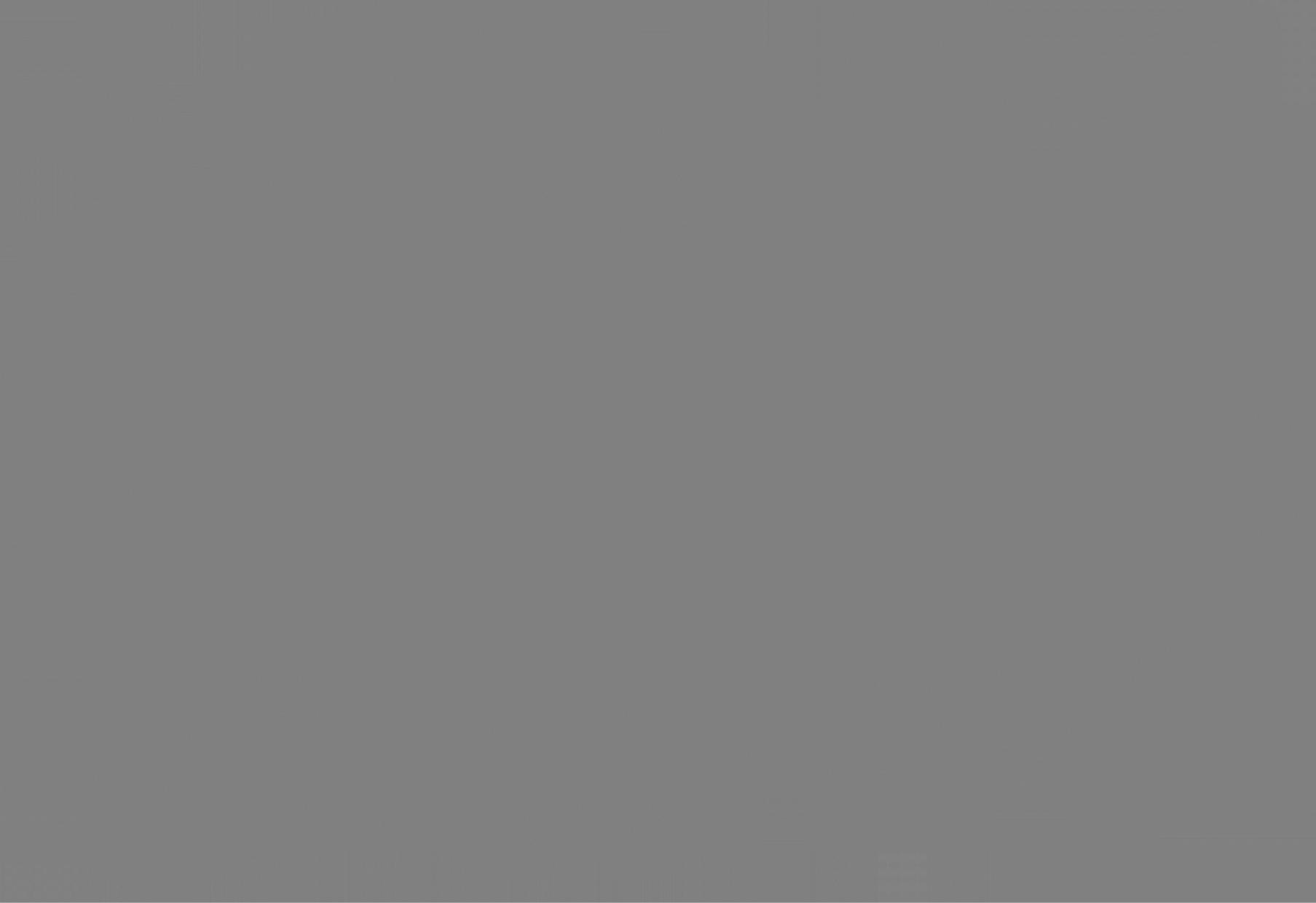
дают катализаторыый раствор, так как он частично выводится из реактора для регенерации, а также с реакционной массой.
Реактором алкилирования служит колонный аппарат 5, отвод тепла реакции в котором осуществляется за счет подачи охлажденного сырья и испарения бен зола. Катализаторный раствор, осушенный бензол и этан-этиленовую (про- пан-пропиленовую) фракцию подают в нижнюю часть реактора 5. После барбо тажа из колонны (реактора) выводят непрореагировавшую парогазовую смесь и направляют ее в конденсатор 6, где прежде всего конденсируется бензол, испа рившийся в реакторе. Конденсат возвращают в реактор, а несконденсированные газы, содержащие значительное количество бензола (особенно при исполь зовании разбавленного олефина в качестве реагента), и НС1 поступают в ниж нюю часть скруббера 8, орошаемого полиалкилбензолами для улавливания бен зола. Раствор бензола в полиалкилбензолах направляют в реактор, а несконденсированные газы поступают в скруббер 9, орошаемый водой для улав ливания НС1. Водный раствор НС1 (разбавленная соляная кислота) направля ют на нейтрализацию, а газы — на утилизацию тепла.
Катализаторный раствор вместе с продуктами алкилирования поступает в сепаратор 7, нижний слой которого (катализаторный раствор) возвращается в реактор, а верхний слой (продукты алкилирования) с помощью насоса 10 на
правляется в нижнюю часть скруббера 11. Скрубберы 7 /и 13предназначены для отмывки хлороводорода и хлорида алюминия, растворенных в алкилате. Скруб бер 11 орошается раствором щелочи, который перекачивается насосом 12. Для подпитки в рециркуляционный поток щелочи подают свежую щелочь в количе стве, необходимом для нейтрализации НС 1. Далее алкилат поступает в нижнюю часть скруббера 13, орошаемого водой, которая вымывает щелочь из алкилата. Водный раствор щелочи направляют на нейтрализацию, а алкилат через подог реватель 14— на ректификацию в колонну 15. В ректификационной колонне 15 в дистиллят выделяется гетероазеотроп бензола с водой. Бензол направляется в колонну 1для обезвоживания, а кубовый продукт — на дальнейшее разделение. Если производство предназначено для получения этилбензола, то кубовый про дукт колонны 15 направляют в ректификационную колонну /бдля выделения в качестве дистиллята продуктового этилбензола. Кубовый продукт колонны 16 направляют в ректификационную колонну П аля разделения полиалкилбензолов на две фракции. Эта колонна работает под вакуумом (р = 5,3 кПа). Верхний продукт направляют в аппарат 4 и реактор 5, а нижний продукт (продукты осмоления) выводят из системы в качестве целевого продукта. Выход целевых про дуктов достигает 94—95 % при расходе 5—10 кг А1С13 на 1 тмоноалкилбензола.
Для улучшения экологической чистоты рассматриваемого производства не обходимо организовать взаимную нейтрализацию кислых и щелочных вод. Для этого необходимо создать такие условия, чтобы соблюдалось определенное со отношение кислоты и щелочи. В этом случае рассмотренная технология будет более приемлемой. Необходимо отметить, что раствор хлорида алюминия (отра ботанный катализатор) может быть использован как коагулянт для очистки сточных вод в нефтеперерабатывающей и целлюлозно-бумажной промышлен ности. Смола, получаемая в процессе, в настоящее время используется как топ ливо. Однако это не лучший способ ее применения, она может быть использова на более эффективно в строительстве. Основным недостатком этой технологии является отсутствие регенерации теплоты реакции, которая отводится водой в конденсаторе 6.
207
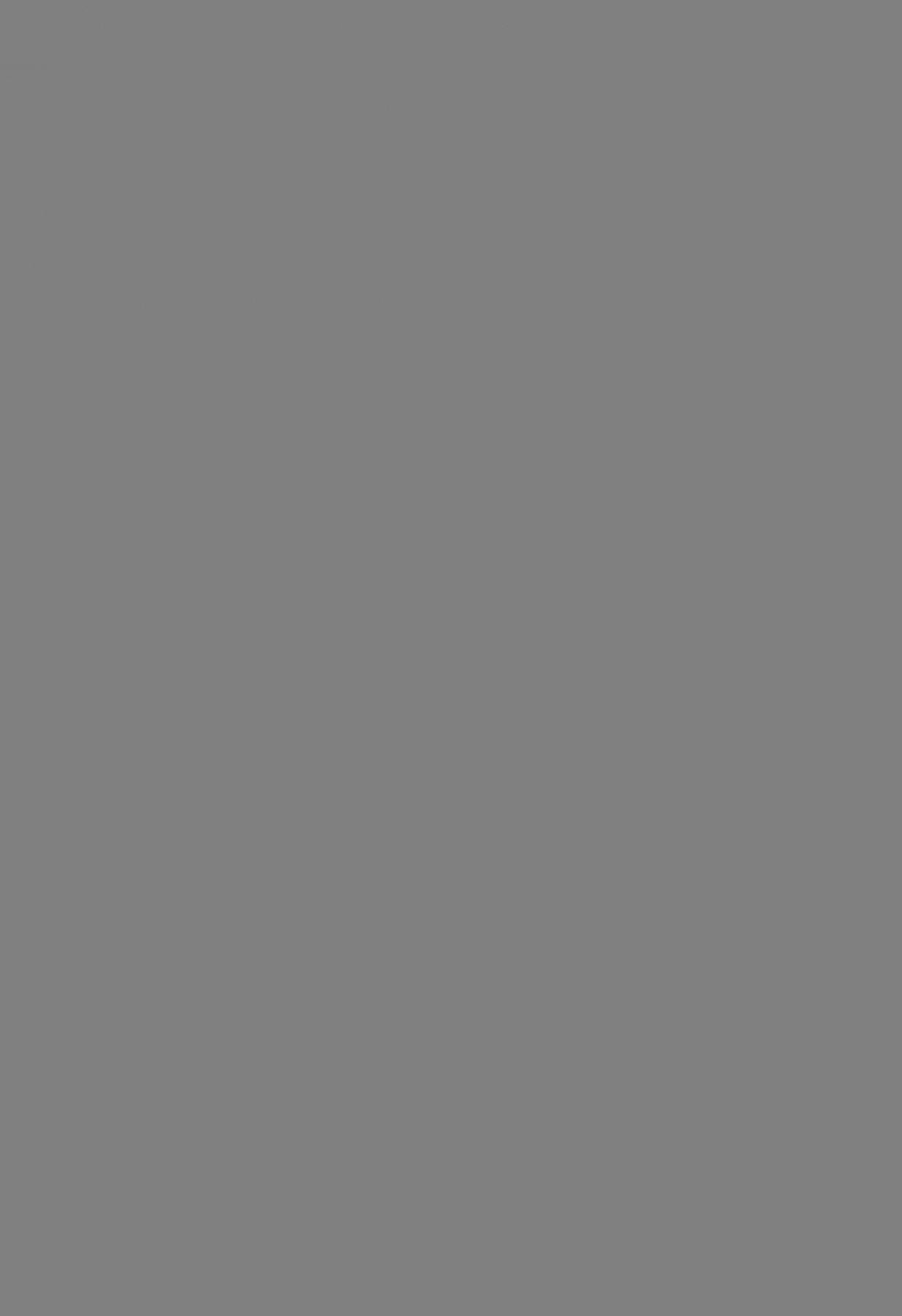
Конверсия пропилена за один |
|
изопропилбензол. |
28—33 |
проход, % (мае.) |
99 |
полиалкилбензолы, смолы |
7—9 |
Расход катализатора, кг/1 т про |
|
|
|
дукта . |
20 |
|
|
Таким образом, жидкофазное алкилирование ароматических углеводородов позволило решить многие технологические задачи и получить ряд ароматиче ских углеводородов в промышленности. Вместе с тем данная технология имеет ряд недостатков: промышленные катализаторы являются недостаточно ста бильными и высокоактивными; такие промышленные катализаторы, как AICI3, H2SO4 и другие, вызывают коррозию аппаратуры и плохо регенерируют
ся; протекание вторичных реакций не только снижает селективность основной реакции, но и требует затрат на очистку основных алкилбензолов и регенерацию вторичных продуктов; образуется большое количество сточных вод, в том числе
икислых, что требует затрат на их очистку.
Всвязи с этим необходимо искать другие технологические решения. В част ности, ряд недостатков можно избежать, если использовать в качестве катализа торов цеолиты и ионообменники.
Производство этилбензола и изопропилбензола на гетерогенных катализаторах.
Внастоящее время известны следующие гетерогенные катализаторы алкилиро вания бензола пропиленом: фосфорнокислотный, катализаторы на основе ок сидов и солей металлов, оксиды, модифицированные ВР3, аморфные алюмоси
ликаты, цеолиты и катиониты. Применение твердых катализаторов намного уп рощает технологическую схему, позволяет автоматизировать процесс, исключа ет проблему коррозии аппаратуры, облегчает отделение продуктов реакции, не требующих дополнительной очистки, которая в гомогенном катализе приводит к образованию стойких эмульсий и больших объемов сточных вод. Эти катали заторы можно регенерировать и использовать многократно. Вданном случае мы рассмотрим технологию алкилирования на цеолитах и катионитах. Первый при мер промышленной реализации процесса позволяет приблизить производство к безотходному, а второй — применить совмещенный реакционно-ректификаци онный процесс. Перспективными представляются цеолитсодержащие катали заторы «СаНУ», содержащие редкоземельные элементы, на которых переалкилирование протекает вусловиях реакции алкилирования, так как указанные ра нее побочные реакции снижают селективность цеолитсодержащих катализато ров, вызывают их дезактивацию и старение. В связи с этим катализаторы периодически необходимо регенерировать при 400—500 °С кислородсодержа щим газом или воздухом.
При использовании цеолитов в качестве катализаторов алкилирования ис пользуется простой адиабатический реактор со стационарным слоем катализа тора. Процесс сопровождается выделением значительного количества тепла, что влияет на температуру и отражается на скорости протекающих реакций. За висимость температуры от скорости образования /-го компонента описывается
уравнением |
|
п |
л |
dT/dx = (М /С.) X*,AЯ,° |
(7.2) |
V /=1 |
J |
14 -2515 |
209 |
