
книги из ГПНТБ / Писаренко Г.А. Отливки металлургического оборудования из чугуна с шаровидным графитом
.pdfЛистопрокатные валки |
49 |
из сердцевины валка отбеленный чугун. Избыток чугуна из фор мы сливают через верх прибыли [49] или через летку, сделанную в форме верхней шейки [50]. Такой способ получения двухслой ных валков называют способом отливки с промывкой.
Производство двухслойных валков по такому способу вызы
вает необходимость строгого сочетания работы двух плавильных агрегатов, высокий расход чугуна и потребность в удвоенном ко личестве кранов и ковшей.
С целью упрощения технологии изготовления двухслойных валков и снижения их стоимости в 1939 г. инженеры Г. Э. Аркулис, А. С. Бешлык и А. Я. Розенберг разработали способ отлив ки двухслойных валков чугуном из одного ковша [42; 51].
Сущность этого способа заключается в том, что для форми
рования отбеленного слоя и сердцевины применяется один и тот
же чугун, но при промывке в литниковую воронку на струю при саживаются графитизирующие добавки — ферросилиций или си-
ликокальций для предотвращения образования карбидов в серд
цевине валков и увеличения ее прочности. Металл, вытесняемый из сердцевины валка, через верх прибыли отводится по желобу. Этот способ отливки обычных листопрокатных валков с пластин
чатым графитом не был внедрен в производство, так как не дал положительных результатов — валки быстро выходили из строя вследствие поломки их по бочке.
Низкая стойкость двухслойных валков, полученных указанным способом, объясняется малой прочностью сердцевины валков.
Структура чугуна с пластинчатым графитом не обеспечивает до статочного сопротивления усилиям, возникающим в процессе про катки.
Этот же способ отливки двухслойных валков металлом из од ного ковша был испытан на валках из магниевого чугуна. Для получения более чистого отбеленного слоя содержание кремния в чугуне было значительно снижено по сравнению с содержанием его в однослойных валках, отливаемых из магниевого чугуна.
Понижение в чугуне содержания кремния уменьшает количе
ство графита в отбеленном слое и повышает твердость чугуна, что видно из данных, приведенных в табл. 17.
Высокая твердость белого магниевого чугуна получается при содержании 0,70% Si и менее; значительное понижение твердо сти происходит при увеличении содержания кремния до 0,90% и более.
Следовательно, для отливки листопрокатных валков целесо образно применять магниевый чугун с низким содержанием крем ния, но в сердцевине валка содержание кремния должно быть повышено, чтобы избежать появления в структуре цементита.
Согласно техническим условиям (ЧМТУ 4893—54), в валках для более ответственного проката (жести, электротехнического
4 Г. А. Писаренко, А. С. Филиппов
50 |
|
Листопрокатные |
валки |
|
||
|
|
|
|
|
|
Таблица 17 |
Влияние содержания кремния в чугуне на твердость и количество |
||||||
|
|
графита |
в отбеленном |
слое |
|
|
|
Химический состав, |
% |
|
Чугун после обработки |
||
|
|
|
магнием |
|||
Si |
с |
Мп |
Р |
S |
содержание твердость Нв |
|
|
|
|
|
|
графита, |
% |
0,35 |
3,07 |
0,61 |
0,41 |
0,008 |
0,059 |
477 |
0,56 |
3,04 |
0,63 |
0,41 |
0,010 |
0,064 |
477 |
0,63 |
3,04 |
0,64 |
0,42 |
0,008 |
0,068 |
460 |
0,72 |
3,02 |
0,64 |
0,42 |
0,009 |
0,085 |
444 |
0,91 |
3,06 |
0,62 |
0,41 |
0,009 |
0,110 |
415 |
1,10 |
3,08 |
0,60 |
0,41 |
0,010 |
0,185 |
388 |
листа и пр.) максимальное содержание кремния допускается до
0,6—0,7%’, а для менее ответственного проката (толстых листов,
декапированных и пр.) до 0,8—0,9 %; (табл. 14). Длительная практика эксплуатации валков из магниевого чугуна показала, что содержание кремния в отбеленном слое можно повысить без
существенного ухудшения качества поверхности прокатываемых
листов: для жестепрокатных валков до 0,8 %', а для тонколисто
вых—до 1,0%’.
Содержание углерода в чугуне двухслойных валков бывает 2,8—3,5%. Обычно при плавке в отражательных печах углерода в чугуне содержится до 3,2%, а при плавке в вагранке 3,2—3,5 %; С увеличением содержания углерода повышается твердость и из носостойкость отбеленного чугуна, но ухудшается его термиче
ская стойкость. Так, высокоуглеродистые валки из чугуна,
содержащего 3,6—3,9%'С, отлитые на Лутугинском заводе про
катных валков, при испытании их на прокатке жести на Лысь венском металлургическом заводе показали низкую стойкость
вследствие образования в отбеленном слое волосных трещин. При низком содержании углерода (менее 2,8%) жидкотеку честь чугуна значительно ухудшается и возникают затруднения в получении чистой и плотной отливки. В отбеленном слое увели чивается количество неметаллических включений, ускоряющих
износ рабочего слоя валков.
Марганец в чугуне обычных углеродистых валков содержится в количестве 0,2—0,4%. При более высоком содержании марган ца переходная зона увеличивается. В двухслойных же валках из магниевого чугуна содержание марганца можно доводить до 0,9%' без ущерба для качества валков.
В чугуне отбеленных листовых валков обычно содержится 0,4—0,5 % Р. Высокое содержание фосфора ухудшает механиче
ские свойства чугуна сердцевины валков, но это вызывается не обходимостью, так как уменьшается возможность возникновения
Листопрокатные валки |
51 |
продольных горячих трещин на бочках валков. При содержании фосфора ниже 0,35 %' возникают также и волосные трещины, ко торые обнаруживаются, главным образом, при механической об
работке валков. Практика вальцелитейных заводов [42] показала,
что мелкие волосные трещины чаще всего появляются при со держании фосфора в пределах от 0,20 до 0,35% и количество их уменьшается при содержании фосфора менее 0,15%. Однако при менять чугун с малым содержанием фосфора в массовом произ
водстве валков нельзя. Низкая жидкотекучесть такого чугуна вы
зывает |
образование |
пороков в отливках. |
Фосфор в валковом |
|||||
чугуне |
при |
содержании до 0,5% |
не оказывает |
существенного |
||||
влияния на твердость |
и глубину |
отбеленного |
слоя |
валков. |
||||
Содержание серы |
в обычных углеродистых валках допускает |
|||||||
ся до |
0,10%, |
в валках |
же из магниевого |
чугуна — до |
0,02%.. |
Несмотря на то, что содержание серы в магниевом чугуне полу чается небольшим вследствие обессеривающего действия магния,
необходимо стремиться получать чугун, до обработки его магни ем, с минимальным содержанием серы, так как сернистые
соединения магния образуют неметаллические включения, ухуд шающие качество отбеленного слоя.
Плавка чугуна для отливки валков производится в отража
тельных печах и вагранках. Шихта, при плавке в печах, состав ляется из чушкового чугуна (валкового, передельного и литейно го) в количестве 30—60% и чугунного валкового лома 40—70%'. При плавке в вагранке шихта составляется из 80—85% чушково го чугуна и 15—20%' стального лома. Добавление в шихту прибылей валков не рекомендуется, так как они загрязнены
шлаковыми включениями.
Лом валков является дешевым и хорошим шихтовым мате
риалом, поэтому его следует использовать в максимально воз можном количестве. Чушковые чугуны необходимы для освеже ния шихты.
Доводка чугуна до требуемого химического состава произво дится добавками ферросплавов.
При введении в шихту лома валков из магниевого чугуна в расплаве получается низкое содержание серы и сохраняется оста точный магний до 0,02%', поэтому расход магния, идущего на об работку чугуна, сокращается до 30%.
Для уменьшения угара |
углерода и окисления чугуна плавку |
в печах необходимо вести |
быстро, но без сильного перегрева. |
Контроль готовности чугуна к заливке форм осуществляется от
ливкой пробы на отбел размером 40 X 100 X 120 мм и по данным экспресс-анализа. Глубина отбела пробы в изломе от поверхно сти, прилегающей к кокилю, до первой группы ясно видимых не вооруженным глазом точек графита, в чугуне нормального соста ва обычно равна 40—60 мм.
82 Листопрокатные валки
Температура чугуна на желобе при выпуске его из печи долж
на быть 1390—1420° в случае, когда магний вводят одновремен
но с расчетом на всю массу чугуна, и 1370—1380° при примене нии чугуно-магниевой лигатуры. При плавке чугуна в вагранке температура его на желобе должна быть не менее 1340°.
Изготовление формы валка производится обычным способом,
но для получения в валке равномерного отбеленного слоя литник подводится к нижней части формы (рис. 17). Перед сборкой формы кокили нагревают в печи до 90—120° в те чение 6—8 час.; длительная выдержка
впечи необходима для равномерного
прогрева стенок кокиля. Температура кокилей при заливке форм должна быть не менее 60°.
Заливка формы валка производится
вдва приема. В первый прием залива ют бочку и часть верхней шейки на вы
|
|
|
|
соту 200—300 мм от |
уровня |
бочки. |
||||
|
|
|
|
Вначале |
форма заливается небольшой |
|||||
|
|
|
|
струей, но после того, как чугун под |
||||||
|
|
|
|
нимется на 50—100 мм над |
уровнем |
|||||
|
|
|
|
питателя, скорость заливки резко уве |
||||||
|
|
|
|
личивается. Литниковая воронка в пе |
||||||
|
|
|
|
риод заливки формы должна быть пол |
||||||
|
|
|
|
ной; продолжительность заливки фор |
||||||
|
|
|
|
мы для валков весом 4—6 т составля |
||||||
Рис. 17. Форма для отливки |
ет |
30—40 сек. |
По |
истечении 100— |
||||||
180 |
сек., |
т. е. |
после |
затвердевания |
||||||
валка из магниевого чугуна: |
||||||||||
1 — песчаная |
форма |
нижней |
отбеленного слоя, |
заливку формы про |
||||||
шейки; 2— кокиль; |
3 — песча |
должают из того же ковша, НО' более |
||||||||
ная форма верхней шейки и |
||||||||||
прибыли; 4 — сигнал-планка для |
медленно. |
Продолжительность |
переры |
|||||||
определения |
уровня |
чугуна в |
ва заливки зависит от температуры чу |
|||||||
форме; 5 — литник; 0 — литнико |
||||||||||
вая воронка; |
7 — дозатор |
для |
гуна, размера валка, содержания угле |
|||||||
ферросилиция, |
|
|||||||||
рерыв тем |
больше, |
чем |
рода и толщины отбеленного слоя. Пе- |
|||||||
зыше температура |
чугуна, больше глу- |
бина отбеленного слоя и выше содержание углерода. Оптималь ная температура чугуна при заливке форм 1270—1290°.
При длительном перерыве в заливке чугун в литнике может
затвердеть. Чтобы этого не допустить, после прекращения дви жения металла в форме, а затем через каждые 50—60 сек. дела ют «толчки», т. е. из ковша выливают в литниковую воронку по
100—120 кг чугуна. Это особенно необходимо производить, когда заливка ведется при пониженной температуре (1240—1260°).
Для модифицирования чугуна сердцевины валка и повышения содержания кремния в течение всего второго периода заливки
Листопрокатные валки |
53 |
формы, продолжающегося 50—70 сек., в литниковую воронку при помощи специального дозатора или по закрытому желобу вво дится порошкообразный 75%-ный ферросилиций в количестве
10—20 кг/т чернового веса валка. Количество вводимого ферро силиция устанавливается в зависимости от содержания в чугуне углерода и кремния. Кремний, входящий в состав ферросилиция, при модифицировании чугуна усваивается на 70—90%; и тем в большей мере, чем выше температура чугуна. Содержание крем ния в сердцевине валка возрастает до 1,2—1,5%, т. е. увеличи вается по сравнению с содержанием в отбеленном слое на
0,5—1,0%'.
Модифицирование и повышение содержания кремния в серд цевине двухслойных валков необходимо для предотвращения об разования структурно свободного цементита, наличие которого понижает пластические свойства чугуна и ухудшает термическую стойкость. Вследствие этого- в эксплуатации валки выходят из строя в основном по поломкам. Чем больше в сердцевине валков структурно свободного цементита, тем хуже их стойкость против
поломок, что подтверждается практикой |
эксплуатации |
валков |
|||||
на Северском металлургическом |
заводе |
при |
прокатке |
жести |
|||
(табл. 18)!. |
|
|
|
|
|
|
|
|
|
|
|
|
Таблица 18 |
||
Стойкость валков в зависимости от количества структурно свободного |
|||||||
цементита в |
сердцевине |
|
|
|
|
||
|
|
Суммарное количество цементита на рас |
|||||
Показатели |
|
стоянии 85 — 1 |
25 мм от поверхности бочки,% |
||||
|
нет |
2 — 5 |
6-15 16 — 30 31—45 более |
||||
|
|
||||||
|
|
|
|
|
|
|
45 |
Количество исследованных |
валков, |
78 |
8 |
10 |
18 |
11 |
4 |
шт.................................................... |
|||||||
Средняя стойкость сломавшихся вал |
10,6 |
7,6 |
7,0 |
6,3 |
5,4 |
2,2 |
|
ков, количество постановок . . . |
|||||||
Относительная стойкость, |
% . . . . |
100 |
72 |
66 |
60 |
51 |
21 |
Микроструктура отбеленного слоя валков из магниевого чугу на состоит из цементита и перлита и незначительного количества графита в мелкораздробленном виде. Структура чугуна сердце вины валков состоит из мелкопластинчатого перлита, фосфидной эвтектики и шаровидного графита. Выделения графита к центру валка становятся крупнее и приобретают неправильную форму.
В двухслойных валках при описанном выше способе введения ферросилиция переходная зона между отбеленным слоем и серд
цевиной отсутствует (рис. 18), но когда промывка сердцевины валка производится более медленно — появляется небольшая пе-
1 Исследования проведены индс, К. Г. Исерсон.
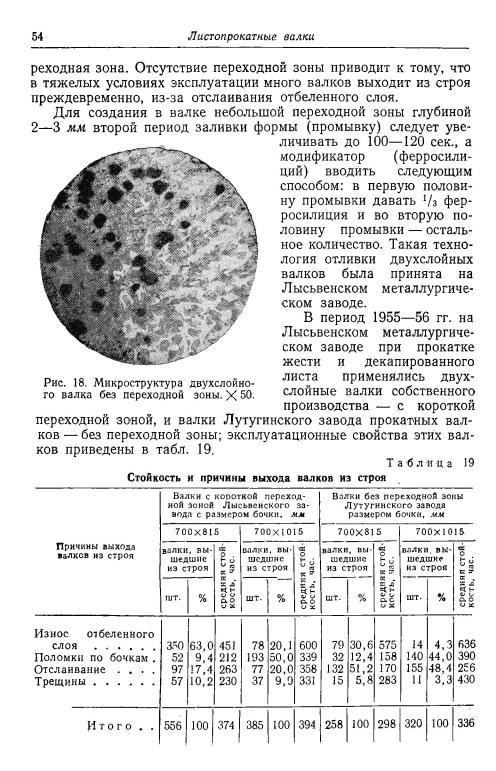
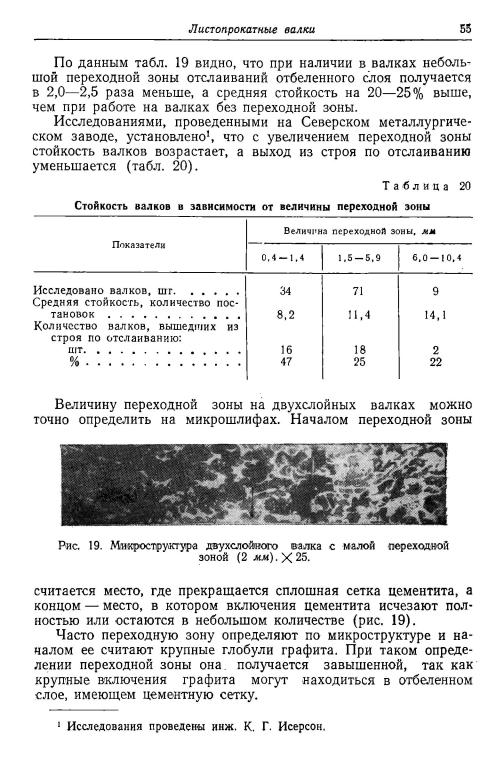
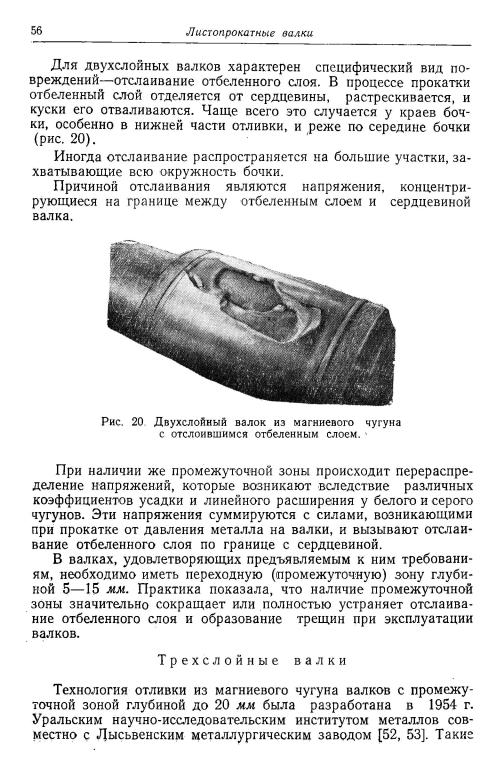
Листопрокатные |
валки |
57 |
валки называют трехслойными, так |
как в |
поперечном сечении |
бочки имеют три зоны: рабочий отбеленный слой, сердцевину из
серого чугуна и промежуточную зону из половинчатого чу
гуна.
Содержание кремния в чугуне каждой зоны различное: в про
межуточной зоне на 0,15—0,40%' больше, чем в отбеленном слое,
а в сердцевине на 0,25—0,60% больше, чем в промежуточной зоне.
Отливка трехслойных валков так же, как и двухслойных, про
изводится чугуном из одного ковша. Формирование промежуточ
ной зоны при отливке трехслойных валков достигается заливкой формы с несколькими перерывами. Такая заливка называется ступенчатой. Вначале форму валка заполняют, примерно, до се редины верхней шейки и заливку прерывают. После образования
отбеленного слоя через 100—180 сек. заливку формы медленно продолжают, делая дополнительно еще два перерыва продолжи тельностью каждый по 60—150 сек.
После первого и второго перерыва на струю чугуна вводится
75%-ный ферросилиций каждый раз по 3—5 кг!т из расчета чер нового веса валка, а после третьего перерыва еще 4—10 кг]т из такого же расчета.
Для предупреждения преждевременного затвердевания литни ка в период перерывов в заливке формы «проталкивают» чугун через литник, доливая небольшое количество металла в литни ковую воронку.
Когда из одного ковша требуется отливать более двух валков, то применение описанного способа отливки валков с промежуточ
ной зоной затруднительно, так как из-за |
длительной выдержки |
||||||||||
температура чугуна в ковше значительно снижается. |
|
|
следует |
||||||||
При отливке 3—5 валков |
промывку |
сердцевины |
|
||||||||
производить |
чугуном из другого |
ковша. |
В |
этом |
случае |
для |
|||||
промывки применяется кремнистый |
магниевый чугун, |
содер |
|||||||||
жащий 5—8%i Si, выплавленный |
непосредственно |
в |
вагранке |
||||||||
или полученный присадкой в |
малый ковш |
75%-ного |
ферро |
||||||||
силиция [54]. |
|
зону |
в |
валках |
можно |
получить, |
|||||
Небольшую переходную |
|||||||||||
увеличивая |
содержание |
кремния |
в |
исходном |
чугуне; |
в |
|||||
этом случае разница между содержанием |
кремния |
в |
отбелен |
||||||||
ном слое и сердцевине будет |
минимальной. |
Но следует |
иметь |
в виду, что увеличение кремния в отбеленном слое выше уста
новленных пределов снижает его качество вследствие понижения твердости.
Микроструктура промежуточной зоны в трехслойных валках состоит из перлита, отдельных участков цементита и шаровидно го графита. Макроструктуры поперечных изломов бочек двух- и
трехслойных валков резко отличаются (рис. 21).
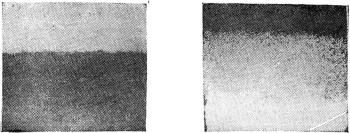
58 Листопрокатные валки
На рис. 22 приведены кривые, характеризующие изменение твердости валков, отлитых различными методами. Твердость от беленного слоя у двух- и трехслойных валков одинакова почти
на всю глубину отбеленного слоя, а затем она снижается: |
у двух |
слойных валков — резко, а у трехслойных — довольно |
плавно, |
от отбеленного слоя к промежуточному и от промежуточного к сердцевине.
У валков с повышенным содержанием кремния наблюдается уменьшение твердости отбеленного и переходного слоя в направ лении к сердцевине; твердость сердцевины также снижается, но незначительно.
а - |
5 |
Рис. 21. Макроструктура валков;
а — двухслойного; б — трехслойного.
Твердость отбеленного слоя в валках из магниевого и обыч ного чугуна одинаковая, а твердость сердцевины в магниевых валках на 30—50 Нв больше.
В результате внедрения на заводах прокатных валков спосо бов отливки валков с промежуточной зоной случаи отслаивания
отбеленного слоя значительно сократились |
(табл. 21). |
|
|
|||
|
|
|
Таблица 21 |
|||
Выход валков из |
строя по |
отслаиванию отбеленного слоя, % |
|
|||
Завод-изготовитель |
Завод-потребитель |
|
Годы |
|
||
1956 |
1957 |
1958 |
||||
|
|
|
||||
Лутугинский |
Северский: |
|
|
|
||
|
цех № 1 ............................ |
42 |
44 |
20 |
||
|
» |
№ 2............................ |
81 |
69 |
52 |
|
То же |
» |
№ 3............................ |
53 |
45 |
19 |
|
Лысьвенский: |
36 |
27 |
8 |
|||
|
цех № 1 ............................ |
|||||
Днепропетровский |
> |
№ 2............................ |
33 |
39 |
4 |
|
Алапаевский ................................ |
24 |
27 |
11 |