
книги из ГПНТБ / Писаренко Г.А. Отливки металлургического оборудования из чугуна с шаровидным графитом
.pdfДетали воздухонагревательных аппаратов и печей |
189 |
Конструкция центрального стержня и условия, в которых он находится в форме, требуют особо тщательного выполнения пра вил изготовления стержня, начиная от стержневой смеси до вы хода из сушила и доставки к формам.
Стержни изготовляются обычно из смеси следующего состава:
Кварцевый песок 2К 70/40(кичнгинскнй).................................. |
90% |
Огнеупорная глина ....................................................... |
6% |
Сульфитный щелок уд. весом 1,25............................................ |
3% |
Крепитель 4ГУ............................................................................... |
1% |
Физико-механические свойства стержневой смеси:
Проницаемость.................................... ................... |
не ниже 250 |
Прочность на сжатие........................................... |
0,25—0,30 ке* /см |
Влажность................................................................ |
4—6% |
Прочность на растяжение сухих образцов . . 4—5 кг!смг
Несколько повышенное содержание глины вызвано тем, что при больших размерах стержня и ручном изготовлении обра зуется большое количество поломок и нарушений геометрических размеров до сушки стержней. Особенно трудным оказывается выполнение полостей 'для игл в стержнях. При небольших зади рах, образующихся во время выемки стержня из ящика, прихо дится полностью заделывать иглы, так как исправить поврежде
ние затруднительно.
Стержни изготовляют в металлических ящиках; их сушат на
драйерах в камерных сушилах при температуре 190—200° в те чение 4 час.
После сушки стержни тщательно проверяют, особенно в иг
лах, так как толщина стенки в этих местах |
составляет |
всего |
3 мм, и при нарушении сплошности металл |
проникает в |
газо |
вый канал, вызывая брак по газовым раковинам. Проверенные
стержни |
окрашивают с |
помощью пульверизатора |
графитной |
||
краской |
и подсушивают |
при |
температуре |
140—160° |
в течение |
2 час. |
|
|
|
|
|
Нельзя устанавливать в форму теплые или горячие стержни, |
|||||
так как при этом происходит |
отпотевание |
формы и стержня. |
В период освоения массового производства труб было боль шое количество брака по газовым раковинам и пузырям. Изуче ние причин брака показало, что малейшее несоблюдение режима изготовления и сушки стержней вызывало брак труб. Иногда достаточно было сменить марку песка или взять другую пар тию сульфитного щелока, чтобы возник массовый брак труб по газовым раковинам. Все это является результатом не техноло гичной конструкции отливки.
190 Детали воздухонагревательных аппаратов и печей
Форма набивается вручную из смеси следующего -состава:
Горелая земля ............................................ |
70% |
Песок П70/140 (калюткинский) .... |
12% |
Песок Т140/70 ............................................ |
18% |
Каменный уголь ПЖ...................................... |
6% |
(сверх 100%)
Физико-механические свойства формовочной смеси:
Проницаемость................................ |
не ниже 80 |
Прочность на сжатие |
сырых об |
разцов ........................................ |
0,4—0,5 кг* /см |
Влажность........................................ |
5—6% |
Модели делают из дерева. Попытки применить металличе ские (алюминиевые) модели оказались неудачными потому, что
По II
Рис. 81. Схема формовки игольчатых труб рекуператора:
1 — жеребейка в центре; 2 — жеребейка |
на равном |
расстоянии. |
без закрепления на подмодельных плитах они |
быстро деформи |
|
ровались и выходили из строя. |
-результаты получаются |
|
Практика показала, что наилучшие |
при расположении одной отливки в форме (рис. 81). При. ином
расположении, по 2—4 отливки ,в форме, качество снижается из-за засоров, раздутия и т. п. и экономические показатели в
целом оказываются -неудовлетворительными.
Литниковая система. Склонность кремнистых спла вов к насыщению газами и выделение -большого количества га зов из центрального стержня приводит к образованию газовых раковин в местах подвода питателей к отливке. Это вызвало необходимость устройства литниковой системы с питающими бо
бышками -по типу систем, применяющихся при производстве от ливок из ковкого чугуна (рис. 81, 82).
Детали воздухонагревательных аппаратов и печей |
191 |
Литниковая система для данного типа отливок должна обес печивать быстрое заполнение формы, чтобы избежать образова ния спаев и газовых раковин, и рассредоточенный подвод ме талла для предупреждения возможного размыва формы и стержня.
Этим условиям удовлетворяет литниковая система, показан
ная на рис. 81, 82. Она состоит из двух стояков диаметром 28 мм и площадью сечения 6 см2 каждый с общей литниковой чашей, двух шлакоуловителей с площадью поперечного сечения
3 см2 каждый и восьми питателей с бобышками (сечение каж дого питателя 1,5 см2).
б
Рис. 82. Вид сверху (а) и разрез литниковой системы (б).
Соотношение площадей поперечного сечения стояка, шлако уловителя и питателей FcT : Гшл: Fr.m =1:1:1. При таком се чении элементов литниковой системы и весе отливки, равном 85 кг, время заполнения формы составляет 15—17 сек. и в от ливках не обнаруживается шлаковых включений. Зато в питаю щих бобышках, как правило, имеются включения шлака и неме таллических частиц. Это подтверждает правильность выбора сечений литниковой системы для данной отливки.
Первые трубы, отлитые по описанной выше технологии, име ли чистую гладкую поверхность без спаев и ужимин, плотную
мелкозернистую структуру с шаровидным графитом. Однако большая часть их была поражена холодными трещинами.
Возникла необходимость более глубокого изучения свойств чугуна и технологии с целью изыскания средств для предотвра щения трещин.
Сравнение механических свойств, в частности ударной вязко
сти (табл. 76), как до, так и после термической обработки,
192 |
|
Детали воздухонагревательных |
аппаратов и |
печей |
|
|||
|
|
|
|
|
|
|
Таблица 76 |
|
|
|
|
Ударная |
вязкость некоторых чугунов |
|
|
||
|
Кремнистые чугуны |
Кремнистые чугуны, обработанные магнием |
||||||
химический состав, |
% |
химический |
состав, % |
|
ударная |
вязкость |
||
|
|
|
|
|
|
|
KtM/CM2 |
|
С |
Si Мп |
Р |
S |
|
|
|
ДО теРМ0‘ |
после тер- |
|
|
|
мообработ- |
|||||
|
|
|
|
|
|
|
обработки |
ки |
|
|
|
0,33 |
|
0,013 |
0,4 |
0,32 |
0,48 |
|
|
|
0,49 |
|
0,022 |
0,4 |
0,33 |
0,29 |
|
|
|
0,26 |
|
0,008 |
0,8 |
0,32 |
0,34 |
|
|
|
0,35 |
|
0,018 |
0,6 |
0,33 |
0,40 |
показывает, что вязкость чугуна с шаровидным графитом выше вязкости кремнистого чугуна.
После термической обработки у чугуна с шаровидным гра
фитом несколько повышается ударная вязкость, хотя абсолют ные значения ее крайне низки. Таким образом, механические свой ства не являются причиной образования холодных трещин.
Анализ явлений, сопутствующих выплавке, заливке и кри сталлизации магниевых чугунов, приводит к тому, что причиной хрупкого разрушения отливок являются значительные остаточ ные литейные напряжения.
Согласно существующим представлениям [56], литейные на пряжения образуются вследствие торможения усадки. В зависи
мости от причин, вызывающих это торможение, напряжения мо
гут быть термические, фазовые |
и усадочные; они бывают I, II |
и III рода. |
|
Напряжениями I рода называют макроскопические, уравно |
|
вешивающиеся в пределах всей |
отливки, II рода — микроскопи |
ческие, уравновешивающиеся в пределах отдельных кристаллов,
и III рода — ультрамикроскопические, уравновешивающиеся в пределах отдельных кристаллических решеток.
Для магниевого чугуна имеют значения напряжения всех трех родов, хотя некоторые исследователи [112; 114] отмечают,
что магниевый чугун обладает большой склонностью к образо ванию напряжений II и III рода.
Это объясняется, по мнению авторов, самоуплотнением маг ниевого чугуна. Необходимо учесть, что его удельный вес зна чительно выше удельного веса обычного серого чугуна такого же состава и равен в среднем 7,2—у модифицированного; 7,3—7,5-—у немодифицированного и 7,05—7,10 — у серого чу гуна.
Наибольший интерес представляют напряжения I рода, по скольку известно, что именно они являются главной причиной
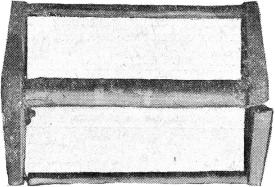
|
Детали воздухонагревательных |
аппаратов |
и печей |
193 |
|
хрупкого |
разрушения отливок. |
Что |
касается |
напряжений II и |
|
III рода, |
то существование их |
доказывается |
лишь |
косвенным |
|
путем на |
основании некоторых |
практических |
данных |
и до сих |
|
пор не существует методики их |
определения. |
|
|
На образование напряжений I рода решающее влияние ока зывает усадка как доперлитная, в области пластических дефор маций, так и послеперлитная, в области упругих деформаций.
Специально поставленными опытами были определены усад ки кремнистых чугунов различного состава (табл. 69).
Из данных табл. 69, следует, что величины усадки полной и литейной не сильно различаются между собой у разных сортов
Рис, 83. Усадочная решетка для определения ли тейных напряжений.
чугуна. Тем самым подтверждается высказанное предположение, что на образование холодных трещин влияют не только напря жения I рода, но и напряжения II и III рода.
Однако из данных табл. 68 видно, что кремнистый чугун с повышенным содержанием углерода, обработанный магнием, имеет лучшие свойства. Это подтвердилось позже при непосред ственном измерении суммарных напряжений. Определение сум
марных остаточных напряжений производилось с помощью стан дартных усадочных решеток (рис. 83).
Решетки заливались чугуном разного состава, при одинако вых условиях изготовления форм, температурного режима заливки и т. п. Затем часть решеток разрезалась до отжига, а другая часть — после низкотемпературного и высокотемператур
ного отжига.
Разрезался |
тонкий брусок диаметром 20 мм. Согласно тео |
рии линейных |
напряжений, такой брусок должен быть сжат и |
13 Г. А. Писаренко, А. С. Филиппов
194 Детали воздухонагревательных аппаратов и печей
величина сжатия должна характеризовать собой значение оста точных литейных напряжений в отливках.
Для снижения остаточных напряжений были опробованы раз личные составы и способы обработки чугуна, причем при выбо ре их исходили из предположения, что графитизирующие эле менты должны способствовать уменьшению, а карбидообразую щие — увеличению напряжений. Учитывалась также практиче ская ценность этих методов, так как количество легирующих элементов не должно быть слишком высоко, а ' технология
выплавки не должна сильно усложняться.
Естественно, максимальное внимание уделялось модифициро ванию чугуна малыми добавками различных элементов — крем ния, алюминия, титана, углерода, поскольку известно, что тако го рода обработка способствует максимальной графитизации чугуна, не увеличивает стоимости передела и не усложняет
технологию.
Результаты определения напряжений приведены в табл. 77.
Таблица 77
Величины сжатия тонких брусков в решетках, отлитых из чугуна, обработанного магнием
|
|
До термообра |
После термо |
||
|
|
ботки |
обработки |
||
|
Чугун |
сжатие |
|
сжатие |
|
|
|
% |
% |
||
|
|
мм |
мм |
||
Обычный кремнистый ............................................... |
1,55 |
1,84 |
0,00 |
0,00 |
|
То же, легированный хромом (1,03%)................ |
2,40 |
2,51 |
0,10 |
0,12 |
|
Высокоуглеродистый |
кремнистый с присадкой |
1,65 |
1,75 |
0,30 |
0,33 |
части кремния в |
ковш....................................... |
||||
С пониженным содержанием углерода................ |
2,20 |
3,50 |
0,50 |
0,60 |
Из данных табл. 77 следует, что абсолютная величина сжа тия тонкого бруска до термической обработки находится в пре
делах 1,75—3,50 мм. Лучшие результаты получены для чугуна с повышенным содержанием углерода и с присадкой части крем ния в ковш одновременно с модифицированием магнием.
Наиболее высокие напряжения оказались у чугунов с пони женным содержанием углерода и до 1,0% Сг. Не дало положи тельных результатов легирование чугунов медью и никелем, а также модифицирование графитом.
Режимы термической обработки выбирались исходя из дан ных определения критических точек: высокотемпературный — при 910—930°, для разложения карбидов и снятия напряжений, и низкотемпературный — при 720°, для снятия напряжений.
|
Детали воздухонагревательных аппаратов и печей |
196 |
В результате высокотемпературного отжига снимается более |
||
80% |
остаточных литейных напряжений. После низкотемператур |
|
ного |
отжига остаточные напряжения также значительно |
сни |
жаются, однако в производственных условиях, видимо, целесооб разнее применять высокотемпературный отжиг для устранения
возможных неудач.
Таким образом, в результате проведенных опытов установ лено, что наименьшую усадку, минимальные остаточные на пряжения и максимальные механические свойства имеет вы сокоуглеродистый нёлегированный чугун, модифицированный
ферросилицием..
Однако получение высокого содержания углерода при вы плавке кремнистого чугуна в вагранке оказалось нелегкой за дачей. В обычных условиях плавки в соответствии с уравнением
эвтектичности при 5—6% Si содержание углерода в чугуне авто матически устанавливается 2,6—2,8 %:.
Чтобы повысить содержание углерода в чугуне из вагранки, пришлось понизить содержание кремния до 3,5—4,5%, а недо стающее количество его вводить в ковш вместе с магниево-крем
нистой лигатурой. Этот способ |
в производственных |
условиях |
||
удобен тем, что включает в себя |
одновременно |
три процесса: |
||
обработку магнием, модифицирование и пополнение |
до |
задан |
||
ного содержания кремния. |
|
|
|
|
Оказалось необходимым изменить также состав шихты, |
||||
исключив из нее стальной лом, |
феррохром и хромсодержащие |
|||
отходы. |
|
|
|
чугуна |
Состав шихты для получения высокоуглеродистого |
||||
был следующий: |
|
|
|
|
Литейные чушковые'чугуны ЛКЗ и ЛК 4 . . |
70—75% |
|
||
Лом чугунный покупной....................................15—20% |
|
|||
Ферросилиций 45%-ный ....................................5—10% |
|
|
Впоследствии, когда накопятся отходы этого чугуна, часть литейного чугуна и привозного лома можно будет заменить от ходами.
Указанными изменениями состава шихты, процесса плавки и
обработки чугуна удалось получать в отливках до 3,25% С (вме сто 2,6—2,8%) при содержании 5,0—5,5% Si.
Из высокоуглеродистого кремнистого чугуна, обработанного магнием, были отлиты опытные игольчатые трубы рекуператоров
длиной 1640 мм.
Количество холодных трещин резко сократилось, но пол ностью они не устранены. При небрежной выбивке из форм, при выбивке стержней на вибрационной машине, а также при обруб ке часть труб получается с трещинами. Это привело к необходи мости применять высокотемпературный отжиг, причем отливки
13*
196 Детали воздухонагревательных аппаратов и печей
во избежание поломок загружались в печь вместе с невыбнты-
ми стержнями.
При наличии соответствующего оборудования можно |
заме |
||
нить отжиг в специальных печах томлением |
отливок в |
колод |
|
цах так, как это делается |
при производстве |
чугунных |
колес. |
С применением высотемпературного отжига количество бра |
|||
ка по холодным трещинам, |
так же как и по |
другим видам, не |
превышает брака рекуператоров, отливаемых из обычного чугуна.
Короба для отжига тонких листов
В отечественной промышленности применяется большое ко
личество отжигательных коробов и поддонов для отжига тонких
Рис. 84. Отжигательный короб Лысьвенского ме таллургического завода.
листов (жести, кровельной, трансформаторной и динамной ста ли), а также для отжига отливок при производстве ковкого чу
гуна. Эти детали, как правило, отливаются из нелегированной
малоуглеродистой стали или чугуна и имеют низкую стой кость.
Расходы на пополнение парка коробов и поддонов только по группе ряда уральских заводов составляют ежегодно' несколько миллионов рублей.
Типичная конструкция стального литого короба для отжига
жести показана на рис. 84. Производство такой детали является нелегкой задачей, так как отливка должна быть здоровой и плот
|
Детали воздухонагревательных аппаратов и печей |
197 |
||
ной, |
а усложнять технологический |
процесс |
установкой |
прибы |
лей, |
мерами облегчения усадки |
и т. п. |
нежелательно, так |
как это снижает производительность, увеличивает расход метал
ла и, в конечном счете, намного повышает себестоимость от ливок.
Работают короба в тяжелых температурных условиях. В не которых печах для увеличения производительности повышают температуру до 1100°. В среднем же можно считать, что короба работают в интервале температур от 900 до 1000°.
Чтобы определить, какой материал в этих условиях будет наиболее подходящим для коробов, были проведены специаль ные определения окалиностойкости хромистой стали с различ
ным содержанием кремния, обычной малоуглеродистой стали и
чугуна с пластинчатым и шаровидным графитом при температу рах 700—1100°.
Данные этих |
определений |
приведены в |
табл. 78. |
|||||||||
|
Результаты определения |
окалиностойкости |
|
|
|
Таблица 78 |
||||||
|
|
различных сплавов |
||||||||||
|
|
|
|
Химический состав, % |
|
|
Окалиностойкость (в г'м^час) |
|||||
|
|
|
|
|
|
при температуре, °C |
||||||
|
Сплав |
|
|
|
|
|
|
|
|
|||
|
|
|
с Si |
Мп |
Р |
S |
Сг |
|
700 |
800 |
900 1 000 1100' |
|
|
|
|
|
|
||||||||
Хромистая сталь . |
. |
0,30 0,26 0,37 0,02 0,011 5,49 1,08 |
3,20 12,55 29,10 46,92 |
|||||||||
То же . . ................ |
0,30 1,01 0,37 0,02 0,011 5,49 |
0,00 |
0,03 10,40 24,48 26,48 |
|||||||||
> » . . . . |
. |
0,30 2,25 0,37 0,02 0,011 5,49 |
0,03 |
0,03 |
0,03 19,58 25,43 |
|||||||
Мягкая углеродистая |
|
|
|
|
— |
5,68 16,79 19,99 40,05 46,75 |
||||||
сталь |
. |
... 0,18 0,35 0,40 0,03 0,63 |
||||||||||
Чугун |
с пластинча- |
3,63 2,58 1,17 0,22 0,042 |
— 2,99 |
6,90 17,34 35,08 58,75 |
||||||||
тым графитом . |
. |
|||||||||||
То же, с шаровидным |
3,52 2,72 1,17 0,'22 0,004 |
— |
1,49 |
— |
3,70 27,98 39,47 |
|||||||
графитом .... |
|
|||||||||||
Из данных табл. 78 следует, что обычный чугун с шаровид |
||||||||||||
ным графитом |
при температуре |
900° |
в 5 |
раз |
превосходит по |
окалиностойкости .сталь и чугун с пластинчатым графитом, а при
1000° |
окалиностойкость |
его соответственно на |
30—50% выше. |
В этом отношении он |
превосходит даже сталь |
с содержанием |
|
5,49% |
Сг. |
|
|
Следует также отметить, что чугун с шаровидным графитом менее подвержен короблению, чем сталь, причем коробление ча сто является причиной преждевременного выхода отливок из строя. Кроме того, отливка чугунных коробов намного проще стальных, а это снижает их стоимость.
Для печей, в которых температура превышает 1000°, отливать
чугунные короба не рекомендуется, поскольку в таких печах в местах, расположенных против форсунок, температура настолько
198 Детали воздухонагревательных аппаратов и печей
высока, что вызывает плавление чугуна, и короба быстро вы ходят из строя. В этом случае недорогим, но достаточно стой
ким материалом оказывается кремнехромистая сталь с содержа нием 5,5%; Сг и 1,5—2% Si.
Другие марки стали, например, высокохромистые с содержа
нием 25—30% Сг, а также чугун марки ЖЧСШ-5,5-0,1, несмотря на высокую стойкость против окисления, мало пригодны для отливки коробов .из-за большой склонности к образованию тре
щин. Неоднократные попытки отливать короба из указанных
Рис. 85. Форма для отливки короба Лысьвенского металлургического завода, собранная под заливку.
сплавов окончились неудачно —все короба были забракованы по холодным трещинам в литейном цехе или в процессе хране ния и транспортировки.
В отличие от стальных, отливка коробов из чугуна с шаро видным графитом производилась дном кверху, без прибылей (рис. 85) и в сырые формы. Такой способ намного сокращает
процесс изготовления формы и не приводит к повышению рас хода металла.
Чугун выплавлялся в вагранке. Чтобы не вводить в поток специальную шихту, состав исходного чугуна принимался такой
же, какой обычно применялся |
в цехе для отливки изложниц: |
|
3,25—3,55%' С; 2,2—2,6%; Si; |
0,5—0,6 %| Мп; 0,11—0,15%' Р и |
|
0,06—0,08%' S. |
> |
> /о |