
книги из ГПНТБ / Бобровников Г.А. Применение синтетических материалов при ремонте и модернизации машин
.pdfподдерживалась постоянной (20° С), так как испытания проходи ли в проточной воде при различных удельных давлениях и пути трения.
Поскольку капрон способен поглощать влагу, то для получе ния правильных показаний износа непосредственно перед испы танием образцы выдерживались в воде до полного их насыщения, т. е. до тех пор, пока не устанавливался их постоянный вес.
В результате было установлено, что величина износа капро новых образцов при смазке водой в зависимости от удельного дав ления и'пути трения колеблется в значительно более широких пре делах, чем при трении без смазки. Однако так же, как и в предыдущих испытаниях, величина износа всех образцов, обрабо танных механическим способом, больше литых в среднем на 50— 150%, а в отдельных случаях еще больше. Так, например, мини мальная величина износа литых образцов при удельном давлении 30 кГ/см2 и пути трения 10 тыс. оборотов шпинделя составила всего 1 мг\ при этом образцы второго вида имели в несколько разбольший износ.
Измерения моментов трения при различных удельных давле ниях и смазке водой проводились при постоянной скорости сколь жения, равной 0,4 м/сек. Время приработки капроновых образцов было различным и зависело от удельного давления. Так, при удельном давлении 20 кГ/см2 заметное постоянство момента тре ния наступило после 9—10 тыс. оборотов ролика, а при 50 кГ/см2 уже после 3—6 тыс. оборотов. Во всех случаях в литых образцах относительное постоянство момента трения наступало быстрее, нежели у образцов, обработанных механическим способом.
График изменения момента трения в зависимости от величины нагрузки и характера смазки при испытании обоих видов образ цов приведен на фиг. 8. Из графика видно, что с увеличением на грузки момент трения возрастает как при испытаниях со смазкой (машинное масло, вода), так и без смазки. Однако при смазке машинным маслом момент трения при всех значениях удельного давления для образцов обоих типов значительно меньший, неже ли без смазки или со смазкой водой.
Изменения величины коэффициента трения при удельных дав лениях 15—60 кГ/см2 и различных видах смазки характеризуются следующими данными. При сухом трении литые образцы, как правило, имеют меньший коэффициент трения по сравнению с ко эффициентом трения образцов, обработанных механическим спосо бом. При смазке маслом и водой наблюдается аналогичное поло жение, только сама величина коэффициента трения значительно меньше. Так, среднее значение коэффициента трения литых об разцов при смазке машинным маслом составляет 0,035, а механи чески обработанных образцов — 0,055.
Следует сказать, что нормальная длительная работа как ли тых, так и механически обработанных капроновых образцов в па ре со стальным при скорости скольжения 0,4—0,5 м/сек происхо
дя
дит без смазки до удельного давления 25—30 кГ/см2, при смазке водой до 50—60 кГ/см2 и при смазке машинным маслом до 100— 150 кГ1см2 и более в зависимости от.температуры в процессе тре ния. При всех условиях эта температура не должна превышать 70—80° С, в противном случае резко увеличивается износ капро новых образцов.
Так |
как |
капрон обладает |
сравнительно плохой |
теплопровод |
ностью, |
то |
при значительных |
удельных давлениях |
поверхность |
трения |
его, |
особенно при трении без смазки, быстро |
нагревается, |
в результате чего снижаются качественные характеристики мате риала. Так, например, при скорости скольжения 0,5 м/сек, удель
ном давлении 150 кГ/см2 и су |
|
||||
хом трении уже через 3—4 тыс. |
|
||||
оборотов |
шпинделя |
происхо |
|
||
дит катастрофически |
быстрый |
|
|||
износ |
испытуемого |
капроново |
|
||
го образца, поверхность тре |
|
||||
ния которого начинает пла |
|
||||
виться. |
|
|
|
|
|
Поэтому при больших удель |
О -атомысеры; ф -атомымолибдена |
||||
ных |
давлениях и |
|
скоростях |
||
|
|
||||
скольжения необходимо идти |
Фиг. 9. Молекулярное строение |
||||
по пути |
применения |
капрони- |
дисульфата молибдена. |
||
рования, т. е. нанесения на ра- |
стальных деталей (эксцентрики, |
||||
бочие |
(трущиеся) |
поверхности |
ползуны, шейки валов и пр.) тонкого слоя капрона с помощью специальной аппаратуры. При тонком слое капрона создаются лучшие условия для отвода тепла от поверхности трения, что способствует сохранению высокой износостойкости и антифрик ционных свойств покрытия.
При высоких удельных давлениях и скоростях скольжения хо рошие результаты дает также применение в качестве смазки ди сульфида молибдена (MoS2). Высокие смазывающие свойства ди сульфида молибдена объясняются его слоистой (пластинчатой) структурой, подобной графиту, антифрикционные свойства которо го хорошо известны.
На фиг. 9 показано молекулярное строение дисульфида молиб дена. Внутренний слой атомов молибдена окружают с двух сто рон атомы серы. Вследствие такого молекулярного строения соз дается слоистая структура дисульфида и молибдена. При этом, отдельные пластинки этого материала могут легко сдвигаться отно сительно друг друга (фиг. 10).
Установлено, что хорошими смазывающими свойствами обла дает только природный дисульфид молибдена, в то время как
синтетический такими |
свойствами |
не обладает [12]. |
Как смазывающий |
материал дисульфид молибдена отличается |
|
рядом весьма ценных |
качеств: |
не теряет своих смазывающих |
свойств в широком |
интервале |
температур от — 70 до 450° С, |
41
имеет высокую химическую стойкость, так как не растворяется в холодной и кипящей воде и почти во всех кислотах и других хими катах. Правильно нанесенная на трущуюся поверхность пленка ди сульфида молибдена выдерживает очень высокие удельные давле ния и настолько прочно удерживается, что ее нельзя удалить без повреждения самой поверхности детали.
Исследования показали, что этот вид смазки может быть с ус пехом использован для улучшения условий работы и продления сроков службы многих деталей и узлов машин, работающих на трение. Однако область применения дисульфида молибдена мо жет быть расширена за счет применения его в качестве высоко-
атомы серы, ч ^ ^ - а т о м ы молибдена
Фиг. 10 Схематическое изображение слоистой (пластинчатой), структуры дисульфида молибдена.
эффективной смазки пластмассовых, в частности капроновых де талей.
Проведенные опыты показали, что дисульфид молибдена обес печивает очень низкий коэффициент трения капрона в паре со сталью (0,015—0,020). Особенно эффективно применение дисуль фида молибдена при высоких скоростях трения и удельных давле ниях (200—300 кГ/см2 и более).
Таким образом, можно сделать следующие выводы.
1. При правильном применении капрон обладает высокой из носостойкостью и является вполне надежным антифрикционным материалом, обеспечивающим достаточно быструю прирабатываемость и устойчивость режима трения.
2. Хорошие антифрикционные свойства и небольшой коэффи циент трения капрона в паре со сталью позволяют применять его для изготовления подшипников скольжения, различного рода вту лок, шестерен и других деталей, работающих в узлах трения ма шин и механизмов. Однако для обеспечения длительной и надеж ной работы подобного рода деталей необходимо учитывать опре деление ограничения не только в отношении удельных давлений и скоростей скольжения, но и в отношении температурного режи ма трения.
3. При небольших удельных давлениях (25—30 кГ/см2) и уме ренных скоростях (0,5—1,0 м/сек) детали из капрона могут рабо тать без смазки (сухое трение) или при недо'статочной смазке (полусухое и граничное трение), когда температура на трущихся поверхностях не превышает 80—90° С. При более высоких скоро стях и удельных давлениях повышается температура и увеличивает ся износ трущейся пары, поэтому необходимо применение смазки.
42
4. Наличие смазки существенно улучшает антифрикционные свойства и износостойкость капрона, что дает возможность приме нять его для более нагруженных деталей. Кроме машинного мас ла, в качестве смазки может быть с успехом использована вода, что представляет особый интерес для водного транспорта, коже венно-обувной и текстильной промышленности. При смазке водой
удельное давление может быть увеличено до 50—60 |
кГ/см2, |
а |
|
при смазке машинным |
маслом — до 100—150 кГ/см2 и |
более |
в |
зависимости от скорости скольжения и температуры в |
процессе |
||
трения, которая не |
должна превышать указанного выше |
||
предела. |
|
|
|
При более высоких нагрузках и скоростях необходимо идти по пути применения тонких покрытий из капрона деталей с целью улучшения условий отвода тепла от трущейся поверхности и обес печения нормального температурного режима трения.
Хорошие результаты дает также использование дисульфида молибдена как нового высокоэффективного вида смазки деталей из капрона, работающих на трение при больших нагрузках и ско ростях.
5. Износ литых образцов во всех случаях испытаний при смаз ке машинным маслом, водой и без смазки существенно меньший, чем у образцов, обработанных механическим способом. Таким об разом, детали, работающие на трение, желательно получать лить ем под давлением при указанных выше режимах (температура пресс-формы 60—70° С, последующее медленное охлаждение де тали вместе с пресс-формой до комнатной температуры и норма лизация кипячением в воде в течение 2 ч).
При медленном охлаждении расплава снижается производи тельность труда. Поэтому такая технология может быть приемле мой только при изготовлении небольших количеств деталей. При изготовлении значительных партий деталей, безусловно, целесооб разней будет более быстрое охлаждение их в пресс-форме с по следующей термической обработкой в масле при 170—180° С, которая также обеспечивает получение однородной кристалличе ской структуры капрона [13].
Имеющийся опыт по применению капрона при ремонте и мо дернизации машин показывает, что из этого полимера наиболее целесообразно изготовлять:
1) детали, работающие на трение, изготовленные как из од ного капрона (вкладыши подшипников, втулки, маломодульные шестерни и пр.), так и с антифрикционными капроновыми покры тиями (кулачки, эксцентрики, втулки, шейки валов, шестерни
идр.);
2)ненагруженные или малонагруженные (несиловые) детали;
3)крепежные детали;
4)некоторые детали, подверженные воздействию значитель
ных нагрузок (силовые детали) с предварительной проверкой их в лабораторных или производственных условиях.
43


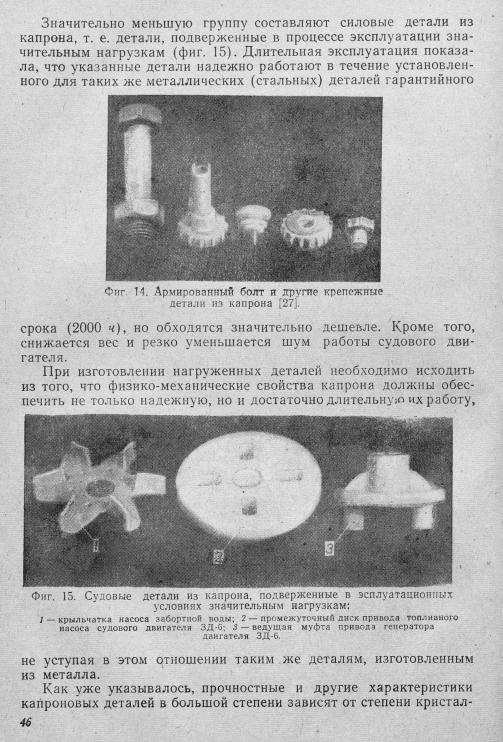
личности полимера. Для деталей, работающих на изгиб и удар, необходимо, например, стремиться получить аморфную структуру, повышающую эластичные свойства и ударную вязкость полимера, что достигается увеличением скорости охлаждения детали в прессформе. Поэтому детали, работающие на изгиб, и тем более ударную нагрузку, необходимо отливать в холодных пресс-формах.
Кристаллическая структура полимера повышает его износо стойкость, разрывную прочность, твердость и жесткость. Поэтому, кроме деталей, работающих на истирание, такая структура пред
почтительна |
также и для деталей, |
работающих на |
растяжение |
|||||||
или подвергающихся воздей |
12 |
|
|
|
||||||
ствию |
значительных |
удель- |
|
|
|
|||||
ных давлений. |
|
|
|
|
|
1 |
|
|||
Повышение |
кристаллич |
е |
|
|
|
|||||
ности |
полимера |
достигается |
сг. |
|
2 |
|
||||
уменьшением |
скорости |
ох |
|
|
||||||
|
|
|
||||||||
лаждения детали, поэтому в |
8 0 |
|
|
|
||||||
таких |
случаях |
отливку |
де |
1 2 |
3 4 - 5 6 |
7 8 9 10 |
||||
талей |
следует |
производить |
|
|
Время Выдержки (д Ванне) д ч |
|||||
Фиг. 16. График изменения |
твердости |
|||||||||
в пресс-формах, |
нагретых до |
|||||||||
50—70° С. |
|
|
|
|
образцов из поликапролактама, подверг |
|||||
|
|
|
|
нутых термической обработке в воде [13]: |
||||||
В заводской практике от |
|
1 — при |
100° С; 2 — при |
90° С. |
||||||
литые |
из капрона |
детали |
|
|
|
|
обычно подвергают нормализации путем кипячения в воде. Такую термическую обработку с продолжительностью кипячения до 2—4 ч (в зависимости от толщины сечения детали) применяют в основном для снятия литейных напряже ний и повышения стабильно сти геометрических размеров деталей в эксплуатационных условиях. Однако исследова ния [13] показывают, что при
|
|
этом |
могут |
происходить |
и су |
||
|
|
щественные |
изменения |
меха |
|||
|
|
нических |
свойств, |
в частности |
|||
|
|
предела |
прочности |
полимера. |
|||
|
|
На фиг. 16 показан график |
|||||
|
|
изменения |
твердости, |
а на |
|||
Фиг. 17. График изменения |
предела |
фиг. |
17 — предела |
прочности |
|||
при |
растяжении |
поликапро- |
|||||
прочности при растяжении поликап- |
лактамовых образцов, подверг |
||||||
ролактамовых образцов, подвергну |
|||||||
тых термической обработке |
в воде |
нутых термической |
обработке |
||||
при 100° С [13]: |
|
путем кипячения в воде. С уве |
личением времени кипячения в воде твердость образцов из поликапролактама несколько
47
увеличивается, но зато резко снижается предел прочности при ра стяжении, который затем повышается, но уже при весьма значитель ной выдержке при 100° С. Таким образом, только при длительном кипячении в воде достигается наиболее благоприятная кристалли ческая структура полимера без снижения предела прочности.
Исследования показали, что при нагреве полиамидных деталей до более высоких температур твердость их возрастает значительно
быстрее, чем |
при |
100° С |
(фиг. |
18). |
|
|
|
|
|
|
|
||||||
Поэтому для более ответственных деталей применяется терми |
|||||||||||||||||
ческая обработка — отжиг, заключающийся в нагреве деталей |
до |
||||||||||||||||
температуры, несколько ниже температуры |
плавления |
данного |
|||||||||||||||
полиамида |
(для |
поликапролактама, например, |
до |
170—180° С) |
|||||||||||||
с последующей выдержкой в течение определенного времени |
(в за |
||||||||||||||||
висимости от размеров сечения детали) |
и медленном охлаждении |
||||||||||||||||
|
|
|
|
|
|
|
|
|
|
до |
комнатной |
темпера |
|||||
|
|
|
|
|
|
|
|
|
|
туры. Такая |
термическая |
||||||
|
|
|
|
|
|
|
|
|
|
обработка |
способствует |
||||||
|
|
|
|
|
|
|
|
|
|
получению |
более |
одно |
|||||
|
|
|
|
|
|
|
|
|
|
родной |
кристаллической |
||||||
|
|
|
|
|
|
|
|
|
|
структуры |
полимера. |
В |
|||||
|
|
|
|
|
|
|
|
|
|
тех случаях, когда требу |
|||||||
|
|
|
|
|
|
|
|
|
|
ется |
увеличить |
вязкость |
|||||
|
|
|
|
|
|
|
|
|
|
материала, детали |
после |
||||||
|
|
|
|
|
|
|
|
|
|
отжига в масле дополни |
|||||||
|
|
|
|
|
|
|
|
|
|
тельно проходят обработ |
|||||||
|
|
|
|
|
|
|
|
|
|
ку в кипящей воде в тече |
|||||||
|
|
Температура отжига в °С |
ние 2 ч. |
|
|
|
|
|
|||||||||
|
|
Некоторые |
авторы |
||||||||||||||
Фиг. 18. График изменения твердости |
|||||||||||||||||
[13] |
рекомендуют |
и более |
|||||||||||||||
капроновых образцов, подвергнутых тер |
сложные |
режимы |
терми |
||||||||||||||
мической обработке в масле при различ |
|||||||||||||||||
ных температурах |
|
и |
выдержках |
[13]: |
ческой |
обработки. |
Так, |
||||||||||
/ — в ы д е р ж к а |
в |
м а с л е |
8 |
ч\ |
2 — |
т о |
ж е , 6 |
ч; 3 — |
для |
получения оптималь |
|||||||
т о ж е , |
4 |
ч; |
4 |
■т о ж е , |
2 |
ч,. |
|
ных |
физико-механических |
||||||||
|
|
|
|
|
|
|
|
|
|
характеристик силовых деталей из полиамидной капроновой смо лы рекомендуется такой режим: нагрев в минеральном масле до 170° С с выдержкой в течение 2 ч и последующим нагревом в воде также в течение 2 ч, но при температуре 70—75° С. Таким образом, выбор режимов литья под давлением и последующей термической обработки деталей из капрона следует производить в каждом кон кретном случае в зависимости от различных факторов и прежде всего с учетом их назначения и условий эксплуатации.
Несмотря на то, что многие вопросы, связанные с рациональ ным применением полиамидов как конструкционного материала, находятся еще в стадии исследования, эти материалы уже нашли широкое применение при изготовлении, ремонте и модернизации автомобилей, сельскохозяйственных машин, в судостроении, торго вом, химическом машиностроении и многих других отраслях про мышленности как в СССР, так и за рубежом [3, 14, 15].
48
СПОСОБЫ ПЕРЕРАБОТКИ И ОСОБЕННОСТИ КОНСТРУИРОВАНИЯ ДЕТАЛЕЙ
ИЗ ПЛАСТМАСС
СПОСОБЫ ПЕРЕРАБОТКИ ПЛАСТМАСС
Изготовление деталей и изделий из пластмасс осуществляется различными способами. Выбор наиболее рациональных способов переработки пластмасс в готовые изделия зависит прежде всего от характера и технологических свойств самой пластмассы (термо реактивная, термопластическая), вида и размеров изделий, харак тера производства (индивидуальное, серийное, массовое).
Наиболее распространенными способами переработки пласт масс в детали и изделия являются:
1)прессование прямое и литьевое из порошковых и волокни стых пресс-материалов;
2)литье под давлением из термопластических масс;
3)непрерывное выдавливание (экструзия);
4)холодное литье;
5)механическая обработка;
6)вихревое и газопламенное нанесение пластмассовых по крытий.
Кроме того, при ремонте и модернизации машин могут найти применение: пневматическое формование, сварка, склеивание, горя чая накатка и др.
Ниже приведена краткая характеристика и сущность указанных способов переработки пластических масс в изделия.
Прессование. Способом прямого прессования получают детали и изделия преимущественно из порошкообразных и волокнистых пресс-материалов термореактивного и значительно реже — термо пластического типа.
Сущность способа заключается в том, что пресс-материал за гружают непосредственно в рабочую полость формы, где он раз мягчается в результате нагрева и заполняет форму под действием давления верхней ее части. При изготовлении из термореактивных масс изделие извлекают из горячей формы, так как оно переходит из пластического в твердое состояние непосредственно после фор мования, т. е. при повышенных температурах.
На фиг. 19 показана схема технологического процесса прессо вания изделий из термореактивных масс.
При изготовлении деталей из термопластов технологический процесс отличается тем, что после прессования пресс-форма вместе с деталью охлаждается, после чего осуществляется ее выгрузка
(фиг. 20).
В обоих случаях загрузка пресс-материала и его формование происходят в нагретой до 145—185° С (в зависимости от состава пресс-материала) форме, вследствие чего такой способ называют горячим прессованием.
4 |
1431 |
49 |