
книги из ГПНТБ / Бобровников Г.А. Применение синтетических материалов при ремонте и модернизации машин
.pdfи порошка пластмассы. Порошок проходит через распыляющее сопло и, пролетая через пламя кольцевой ацетиленовой горелки, переходит в пластическое состояние и наносится на поверхность изделия, образуя монолитный слой покрытия.
В аналогичной по своему назначению установке WSIII резерву ар для порошка (пасты) расположен отдельно и соединен с аппа ратом для напыления шлангами.
При нанесении покрытий способом газопламенного напыления трудно полностью сохранить физико-химические свойства данной пластмассы, так как прохож дение частичек порошка через пламя горелки не остается без последствий даже при тща тельном соблюдении режимов технологического процесса. В целях возможно большего со хранения указанных свойств пластмассы напыление следу ет производить при возможно более низких температурах, обеспечивающих, однако, до статочно хорошую сцепляемость покрытия с основным
материалом.
Контроль качества покрытия производится электроискровыми или электромагнитными дефектоскопами. Особенно тщательно должны проверяться защитные, антикоррозионные покрытия.
Действие электроискрового дефектоскопа основано на том, что при контактировании щупа с дефектными участками покрытия, имеющего поры, трещины или повреждения, электрическая цепь прибора замыкается, что вызывает искрение. Выявленные дефект ные места очерчивают карандашом и исправляют повторным мест ным напылением. Мелкие повреждения и пористые покрытия ис правляют с помощью горячего утюга (если, разумеется, выполне нию этой операции не препятствует форма и размеры поверхности детали).
Способом газопламенного напыления пользуются в основном для нанесения защитных, антикоррозионных покрытий на деталях и изделиях из стали, чугуна и цветных сплавов, требующих защиты от воздействия влаги и химически активной среды. В настоящее время такие покрытия применяются в химической, пищевой и дру гих отраслях промышленности. Это позволило снизить себестои мость многих деталей и изделий, сэкономить большое количество
цветных металлов и сплавов, применяющихся в качестве защитных покрытий.
Широкое применение способ газопламенного напыления полу чил также для защитных покрытий баков, резервуаров и других емкостей. В частности, полиэтиленовые покрытия применяют для
120
зашиты емкостей питьевой воды на морских судах, покрытия бутваром — для защиты бензохранилищ и т. д.
Интересно отметить, что в ГДР способ газопламенного напыле ния успешно применяют для внутренней облицовки бетонных ре зервуаров пластифицированным поливинилхлоридом. Для этого на очищенную от пыли поверхность резервуара наносят слой перхлорвинилового клея и после просушки его в течение 20 мин произво дят газопламенное напыление покрытия.
В настоящее время проводятся экспериментальные работы и по облицовке внутренних поверхностей деревянных резервуаров.
Способ суспензий. Большой практцческий интерес представляют защитные покрытия на основе фторопластов, обладающих хороши ми диэлектрическими свойствами и особенно высокой химической стойкостью. Покрытия из фторопластов могут надежно защищать металлические детали и оборудование, работающие в условиях агрессивной среды, в частности в среде концентрированных кислот
ищелочей.
Внастоящее время разработана и успешно применяется в на
шей стране и за рубежом технология нанесения покрытий из фто- ропласта-3 и фторопласта-4 способом суспензий.
Сущность способа заключается в том, что суспензию фторопла ста-3, состоящую из тончайшего порошка полимера и органиче ской жидкости, наносят на поверхность изделия. Нанесенный слой суспензии подсушивается вначале на воздухе, а затем в термостате при 120—150° С, в результате чего органический растворитель ис паряется и на поверхности изделия остается тонкий слой сухого полимера, который затем оплавляют- в монолитное покрытие на греванием до 260—270° С с выдержкой в течение 20—60 ч в зависи мости от габаритов изделия.
Поверхность изделия, на которую наносят полимер, должна быть тщательно очищена и обезжирена. Хорошие результаты дает гидропескоструйная обработка поверхности с последующим обез жириванием растворителями.
Такая предварительная обработка существенно повышает адге зию' покрытия фторопластом.
На поверхность изделия суспензия может быть нанесена раз личными способами: поливом, окунанием, кистью или с помощью пульверизатора. Во всех случаях нанесенный слой суспензии дол жен быть равномерной толщины по всей поверхности. Образовав шиеся подтеки и утолщения могут быть удалены кистью в период предварительной подсушки покрытия на воздухе.
После оплавления одного слоя покрытия изделие охлаждают, после чего наносят следующий слой. Однократное нанесение су спензии дает возможность получить слой покрытия толщиной все го 10—15 мк, который к тому же имеет многочисленные поры. По этому для получения сплошного покрытия требуется последова тельное наложение до 10—16 слоев, что обеспечивает получение устойчивой антикоррозионной пленки толщиной 100—200 мк.
121
Попытки увеличить толщину покрытия за счет увеличения слоя суспензии не дали положительных результатов ввиду растрескива ния слоя при сушке.
После нанесения и оплавления последнего слоя (обычно деся того) производят закалку изделия путем резкого охлаждения с расплавленным покрытием в холодной воде. Закалка уменьшает степень кристалличности полимера, повышает эластичность покры тия, не снижая его адгезии к металлу. При закалке мелкие изде лия целиком погружают в бак с водой. Крупные изделия охлажда ют путем орошения водяным душем.
Как видно из самого описания, технология нанесения покрытий способом суспензий характеризуется сложностью и низкой произ водительностью в сравнении с предыдущими способами покрытий. Поэтому применять его следует в случаях необходимости получе ния покрытий из фторопластов, так как вихревой и газопламенный способы в обычном виде не обеспечивают получения высококаче ственных покрытий из этих пластмасс.
В последнее время разработан ускоренный процесс получения антикоррозионного покрытия из фторопласта-3 способом газопла менного напыления с применением специальных пластификаторов, введение которых в суспензию дало возможность наносить утол щенные слои без растрескивания их при сушке [30]. В качестве пластификаторов были использованы различные фторхлоруглеродные масла и смазки: ЗФ (ВТУ ГИПХ ЕУ-96-57), 4Ф (ВТУ ГИПХ ЕУ-160-57), Ю-ОК (ВТУ ГИПХ ЕУ-159-57) и жидкость № 12 (ВТУ ГИПХ ЕУ-158-57).
Хорошие результаты были получены при использовании жид кости № 12 в количестве 2,0—2,5 % от веса суспензии. Этот пла стификатор представляет собой маслянистую жидкость (удельный вес 1,89 Г/см3, температура кипения около 200° С ), получаемую при производстве фторированных масел и смазок.
Проведенные исследования механических свойств покрытий из суспензии фторопласта-3 с добавкой жидкости № 12 показали, что они не уступают свойствам покрытий, получаемых без пластифи катора. Однако при введении этого пластификатора можно полу чить качественное покрытие толщиной 40—55 мк за один прием и толщиной до 200—220 мк соответственно за 4—5 приемов (вместо 16). Следовательно, это мероприятие дало возможность значитель но упростить технологию и ускорить в 3—4 раза процесс нанесения защитных покрытий из фторопласта-3 по сравнению с обычным способом суспензий.
В дальнейшем было обнаружено, что при нанесении первого слоя покрытия из суспензии фторопласта-3 с добавкой жидкости № 12 на стальных поверхностях, прошедших предварительную гидропескоструйную обработку, появляется налет продуктов кор розии. Явление это может быть устранено путем нанесения первых двух слоев покрытия из суспензии без добавки жидкости № 12, а последующих слоев — с добавкой этого пластификатора либо за
122
счет введения ингибитора коррозии — нитритдициклогексиламина в количестве 1,5% от веса сухого остатка суспензии. В обоих, слу чаях полностью исключается коррозия металла и достигается ка чественное покрытие, обладающее высокой химической стойкостью, характерной для фторопласта-3.
Способ газопламенного напыления фторопласта-3 может быть использован для получения покрытий на наружных поверхностях змеевиков, труб, вентиляторов и других изделий сложной конфи гурации, а также на внутренних поверхностях открытых крупно габаритных изделий типа ванн и других емкостей.
При необходимости защитные покрытия из суспензии фторопла ста-3 с добавкой пластификатора можно наносить и обычными способами, т. е. окунанием, с помощью кисти, пульверизатора и др.
Среди других способов нанесения пластмассовых покрытий все большее внимание привлекают облицовка металлических изделий пленками, напрессование готовых пластмассовых оболочек и так называемый литьевой способ.
Первый способ применяется в основном для облицовки метал лических резервуаров. После дробеструйной или гидропескоструй ной обработки стенки резервуара покрывают слоем клея в 2—3 приема.
В качестве облицовочного материала используют поливинил хлоридную пленку, на которую также наносят слой клея [31]. Вы полнение непосредственно облицовочной операции начинается с нагрева наружных стенок резервуара до тех пор, пока не прогре ются внутренние стенки, на которые нанесен клей, до определен ной температуры в зависимости от вида клея. Нагрев стенок ре зервуара целесообразнее всего производить водородной горелкой. Нанесенная прозрачная пленка клея по мере нагрева приобретает мутно-молочный цвет, что используется для определения момента, когда необходимо приступить к накладыванию облицовочной по ливинилхлоридной пленки. Коричневый оттенок пленки клея сви детельствует о перегреве стенок, чего, естественно, допускать нельзя.
После наложения на нагретую внутреннюю поверхность резер вуара поливинилхлоридная пленка становится пластичной и хоро шо облегает эту поверхность.
Для обеспечения надежного сцепления облицовочного покры тия пленку вручную с помощью куска шерстяного войлока при жимают к поверхности резервуара.
Опыт применения полиамидных подшипников скольжения по казывает, что подшипники, представляющие собой стальную втул ку, покрытую с внутренней (рабочей) стороны тонким слоем по лиамида, имеют преимущества перед толстостенными цельнопо лиамидными подшипниками. Тонкий слой полиамида обеспечивает лучший отвод тепла из зоны трения и снижает влияние повышен ного линейного расширения пластмассы на изменение размеров и зазоров трущейся пары.
123
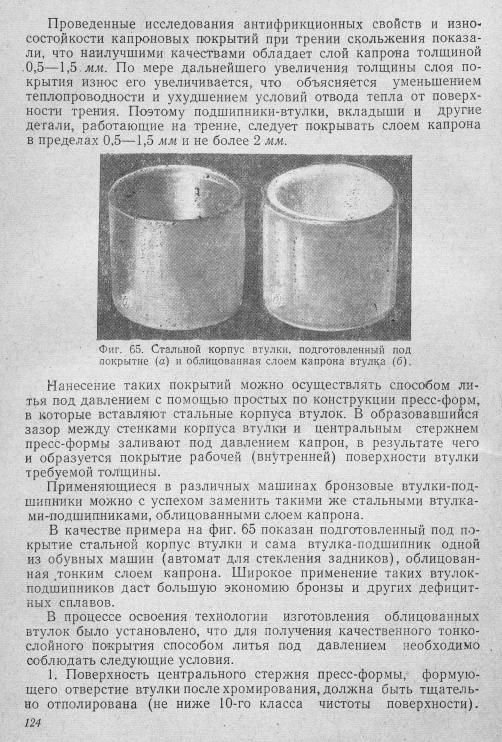
Диаметр центрального стержня должен определяться с учетом усадки слоя капрона и вида посадки при сопряжении втулки с валом.
2. Для покрытия необходимо применять капрон-крошку, кото рый должен быть тщательно просушен (содержание влаги не бо лее 0,3%). Время выдержки капрона в нагревательном цилиндре должно быть минимальным. Температура расплавленного капро
на не должна превышать 240—250° С, давление |
при заполнении |
||||
пресс-формы — 40—50 кГ/см2. |
Пресс-форма, |
а |
также |
стальная |
|
вставка (корпус втулки) перед |
заполнением |
капроном |
должны |
||
быть нагреты до 80— 100° С. |
|
|
|
|
|
3. |
Для обеспечения надежной адгезии капронового покрытия на |
рабочей поверхности стального корпуса втулки необходимо наре зать мелкую резьбу шагом 0,5 мм и выточить по краям заплечики размером 2 X 5 мм. Обработку этих поверхностей следует произ водить без применения смазки или охлаждающей эмульсии.
Большое значение имеет конструкция литника. Многочислен ные опыты показали, что литники обычной конструкции не обеспе чивают получения качественного тонкослойного (1—1,5 мм) по крытия, которое имеет ряд дефектов: недолив, пропуски (т. е. наличие непокрытых участков), неровную толщину и т. п. В резуль тате было установлено, что для получения качественного покрытия необходимо применение «кругового» литника, обеспечивающего подвод расплавленной массы капрона по всей внутренней окруж ности втулки.
Разгрузка пресс-формы и извлечение облицованной втулки тре буют значительного усилия. Поэтому эта операция должна выпол няться с помощью специального приспособления — съемника под прессом с ручным или гидравлическим приводом.
При сборке машин запрессовка облицованных втулок может осуществляться обычным способом, т. е. с помощью пресса. Если при этом возникают чрезмерные деформации втулок, то следует применить сборку с помощью искусственного холода.
Специально проведенные опыты показали, что при охлаждении цельнокапроновых втулок в жидком азоте возникают трещины. Объясняется это не только повышением хрупкости полиамидов при отрицательных температурах, но и низкой их теплопроводно стью, вследствие чего при резком охлаждении возникают большие температурные напряжения.
При охлаждении облицованных втулок в жидком азоте тонкий слой полиамида, обладая достаточной теплопроводностью, не раз рушается, а после нагрева до нормальной температуры механиче ские свойства его (твердость, эластичность и др.) полностью вос станавливаются. Поэтому охлаждение облицованных втулок мож но осуществлять путем погружения их непосредственно в жидкий азот.
При значительном диаметре втулок (более 80—100 мм) охлаж^ дение их в жидком азоте (—196° С) является чрезмерным, так как
125
образующееся при этом Сжатие намного превосходит требуемый натяг. В таких случаях при сборке может быть использована ван на, состоящая из смеси спирта (денатурированного) и твердой уг лекислоты, обеспечивающей охлаждение деталей до более умерен
ных температур (—80° С ).
В тех случаях, когда возникают трудности, связанные с нане сением тонкого слоя полиамида на внутреннюю поверхность втулокподшипников, или замена вала при ремонте крайне нежелательна,
применяют другой вариант |
тонкослойных |
антифрикционных по |
||
крытий. |
|
подшипника изготов |
||
В |
этом случае вкладыши (втулки) |
|||
ляют |
цельнометаллическими, а трущиеся части вала |
покрывают |
||
тонким слоем полиамида |
способом газопламенного |
напыления |
либо с помощью облицовывания полиамидной трубкой, заменяе мой в дальнейшем по мере износа.
Полиамидные трубки изготовляют литьем под давлением или способом непрерывного выдавливания с помощью экструдеров.
Облицовку валов производят следующим образом [32]. Полиа мидную втулку надевают на специальную оправку (фальшвал), ус тановленную в патроне токарного станка. Выступающую часть втулки (около lU длины) при ее вращении развальцовывают и од новременно напрессовывают на вал. После облицовки валов поли амидными втулками не требуется дополнительной механической обработки, отпадает необходимость в термической обработке шеек вала, обычно применяющейся для повышения их износостойкости, упрощается и ускоряется ремонт подшипников.
Существенный интерес представляет также изготовление обли цованных капроном кулачков и эксцентриков, которые являются массовыми деталями обувных, текстильных и многих других машин.
При изготовлении пресс-форм для таких деталей возникают большие трудности, связанные с обработкой формующих ее частей,- Для этих целей требуется применение специальных копировальных приспособлений, что резко повышает стоимость пресс-форм. В ре монтных условиях, когда требуются небольшие партии эксцентри ков и кулаков одного и того же типоразмера, применение таких пресс-форм экономически не оправдывается. Поэтому автором * была разработана конструкция и технология изготовления более простых и дешевых пресс-форм, формующие части которых изго товлялись литьем.
Схема одной из таких пресс-форм показана на фиг. 66. Данная пресс-форма предназначена для изготовления облицованных ка проном кулачков обувной машины АСГ-4. На фиг. 67 показан один из таких кулачков и формующая часть пресс-формы, полученная литьем. Рабочая (трущаяся) часть кулачка покрыта слоем капро на толщиной 3 мм.
* С овм естно с А . А. С вен ц и ц ки м .
126

Предварительные данные показывают, что такие пресс-формы целесообразно применять при изготовлении небольших партий ку лачков и эксцентриков (до 50—100 шт.). При более значительных размерах партий деталей необходимо изготовлять более долговеч ные пресс-формы с формующей частью, изготовленных из алюмини евых, цинковых и других литейных сплавов литьем под давлением.
По срокам службы кулачки и эксцентрики, облицованные ка проном, не уступают стальным при значительно меньшей стоимо сти. После износа покрытия они могут многократно и легко восста навливаться. Изготовление таких деталей доступно любому ремонтному цеху и не требует применения специальных дорогосто ящих приспособлений.
Литьевой способ с успехом применяют для восстановления ряда изношенных деталей [17]. Так, например, нанесением слоя капрона освоено восстановление поршней переднего и заднего тормозных цилиндров, поршня амортизатора, шестерни распределительного вала и рулевого колеса автомобиля. Если ранее при капитальном ремонте автомобиля все изношенные поршни тормозных цилинд ров, изготовляемых из алюминиевого сплава, выбраковывались, то в настоящее время их восстанавливают.
Процесс восстановления тормозных цилиндров происходит сле дующим образом. Производится обточка и подрезка донышка, а также проточка канавки на наружной поверхности, после чего производится заливка капроном и окончательная обточка по диа метру, так как требуется высокая точность. При восстановлении шестерни распределительного вала срезаются изношенные зубья, деталь помещается в пресс-форму и заполняется капроном. В ре зультате получается шестерня с капроновым ободом и готовыми зубьями, не требующими последующей обработки. Такой способ нанесения покрытий и восстановления изношенных деталей может оказаться весьма перспективным при ремонте машин, особенно в связи с возможностью прим'енения для этих целей временных де шевых литых пресс-форм.
М ЕХАНИЧЕСКАЯ ОБРАБОТКА ПЛАСТМАСС
При механической обработке пластмасс необходимо учитывать их низкую теплопроводность, неоднородность строения, сравни тельно низкую теплостойкость и т. п. Вследствие указанных специ фических свойств пластмасс обработка их резанием существенно отличается от подобной обработки стали и других сплавов. Разли чие это заключается в том, что в результате низкой теплопровод ности пластмасс выделяющееся при их резании тепло почти пол ностью концентрируется в режущем инструменте. Поэтому к теп лостойкости материала режущего инструмента должны быть предъявлены высокие требования.
Весьма часто в состав пластмасс входят наполнители, обладаю щие по отношению к инструменту абразивными свойствами. Это
128
увеличивает механический износ инструмента, который, как пра вило, бывает более значительным, чем при обработке стали. Таким образом, основным требованием, предъявляемым к материалу режущего инструмента, кроме высокой теплостойкости, является и высокая износостойкость. Вместе с тем для качественной обработ ки важным является то, чтобы режущая кромка инструмента была очень острой и не выкрашивалась.
Таким требованиям в большей степени отвечают твердые спла вы и отчасти быстрорежущая сталь. Поэтому при обработке пласт масс следует применять резцы, фрезы и другие инструменты, осна щенные пластинками твердых сплавов (ВК8, Т15К6 и др.), а так же из быстрорежущей стали марки Р18 и Р9. Вполне естественно, что при обработке пластмасс без наполнителей (например, поли стирола) можно с успехом применять менее дефицитную легиро ванную и углеродистую инструментальную сталь.
Трудность механической обработки пластмасс связана с их низ кой теплостойкостью и опасностью деструкции материала вслед ствие нагревания его поверхностных слоев. Эту особенность необ ходимо учитывать главным образом при обработке термопластиче
ских масс, когда выделяющееся тепло может |
размягчать их уже |
п,ри нагреве до 150° С с образованием задиров |
и других дефектов |
на поверхности детали. |
|
При обработке металлов для охлаждения инструмента и обра батываемой детали широко применяют охлаждающиеся жидкости.
Однако |
при обработке пластмасс такой способ охлаждения, как |
|
правило, |
не применяется ввиду их способности поглощать влагу. |
|
В некоторых случаях применяются мыльные растворы |
(например, |
|
при обработке полистирола) или сжатый воздух. |
предвари |
|
Следовало бы провести испытания по применению |
тельного охлажденного сжатого воздуха. Для этой цели может быть использовано простейшее холодильное устройство, представляю щее собой сосуд с вакуумной изоляцией, в который заливается жидкий азот. Сжатый воздух от заводской воздушной сети, прохо дя через змеевик, омываемый парами хладоносителя, охлаждается и подается в виде струи непосредственно к месту резания. Темпе ратуру воздуха в нужных пределах можно легко регулировать за счет количества испаряемого хладоносителя.
Проведенные исследования [35, 36, 37, 41} различных видов ме ханической обработки позволили установить зависимость стой кости режущего инструмента и чистоты обрабатываемой поверх ности от скорости резания и других факторов, дать рекомендации в отношении геометрии режущего инструмента и режимов резания при обработке различных пластмасс. Однако до настоящего вре мени все еще отсутствуют обобщенные данные как полученных результатов исследований, так и накопленного промышленностью опыта по обработке пластмасс резанием, что нередко затрудняет выбор наиболее рациональных режимов резания и геометрию ре жущих инструментов.
9 1431 |
п э |