
книги из ГПНТБ / Челюсткин А.Б. Применение вычислительной техники для управления металлургическими агрегатами
.pdfле из сопла непрерывно вытекает струя ртути, по очереди кон тактирующая со всеми контактами поля.
Однако для контроля технологических параметров металлур гических процессов не требуется такая скорость обегания, поэ
тому шире всего используется обегающее устройство в виде ша гового искателя. Быстродействие рассмотренной системы в ос новном определяется скоростью печатания. В среднем один па раметр печатается немногим дольше 1 сек. Помимо печатания
цифр в таблицу, печатающее устройство записывает данные значений параметров на перфорированные карты или магнитную ленту, которые могут быть переданы в цифровую вычислитель ную машину, где анализируется работа агрегата. Запись осуще ствляется через равные промежутки времени (например, через 1 час), длительность которых устанавливают в зависимости от
величины постоянной времени, характеризующей процесс. В про цессе «обегания» показаний приборов система периодически подключается к некоторому эталонному источнику напряжения,
и результат всех преобразований сравнивается с эталонным чис
лом, отображающим это напряжение. Этим достигается само
проверка работы системы.
Впромежутках между периодическими записями значений параметров в таблицу система обегает с большой скоростью все значения и сравнивает их с заранее установленными пределами. Если какой-либо из параметров выходит за эти пределы, что указывает на нарушение хода процесса, система дает сигнал
оператору и осуществляет внеочередное печатание этих парамет ров (красным цветом)..
Применение системы автоматической регистрации резко сокращает время, необходимое для выявления нарушений хода технологического процесса, и позволяет своевременно принимать меры для их устранения. Система дает возможность также осу ществлять запись комплексных параметров (например, экономи ческих показателей), рассчитываемых вычислительной машиной или вычислительными устройствами на основании показаний ря да приборов и данных, вводимых вручную.
Втех случаях, когда отдельные параметры измеряются элек трическими приборами, их выход может быть подключен непо средственно к обегающему устройствуОднако в большинстве
случаев приходится применять специальные датчики для преоб разования измеряемой величины в электрическую. Так, при ис пользовании пневматических приборов в качестве датчиков применяются реостатные, индуктивные и проволочные тёнзомет- ’ рические датчики, обладающие линейными характеристиками.
При измерении расходов с помощью трубок Вентури или диа
фрагм особое внимание должно быть обращено на получение
линейной зависимости между выходным напряжением датчика и измеряемым расходом. Наиболее удобен для этого измерения компенсационный дифманометр, в котором усилие, развиваемое
4* 51
мембраной дифманометра, пропорциональное квадрату скоро сти движения жидкости или газа через диафрагму, вызывает перемещение якоря трансформаторного датчика. Напряжение, снимаемое с этого датчика, питает через усилитель электромаг нит, который создает усилие, уравновешивающее усилие на мем
бране. Так как усилие электромагнита пропорционально квадра ту тока в его катушке, то этот ток оказывается прямо пропор циональным измеряемому расходу.
Рис. 40. Схема сравнения значений параметров с граничными значениями в пневматической измери тельной системе:
/ — диффренциальные манометры; 2 — контактные устройства; 3 — генератор пилообразного давления
Как уже указывалось выше, в системе автоматической реги страции имеется устройство, сравнивающее текущие значения отдельных параметров с их граничными значениями и подающее
сигнал при выходе параметра за пределы этих значений.
При наличии пневматических приборов применяется схема,
приведенная на рис. 40. Давления Pi—Р$, пропорциональные
измеряемым величинам, подаются на контактные дифференци альные манометры. Специальное поршневое устройство созда ет противодавление Рь, величина которого периодически линей но изменяется по времени t, как показано на графике в нижней части рис. 40. Давление, создаваемое измерительным прибором, определяется как интервал времени между началом цикла и мо ментом замыкания контактов сооветствующего дифференциаль ного манометра. Выход измеряемого параметра за пределы ус тановленных значений оценивается по величине соответствую щего интервала времени.
52

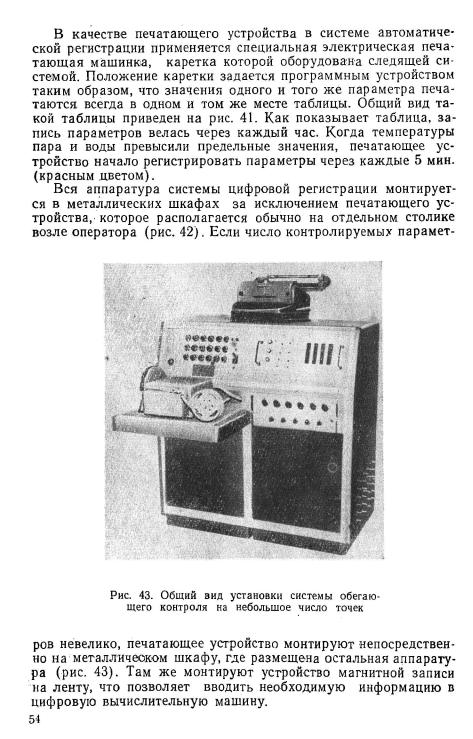
Глава II
ПРИМЕНЕНИЕ ВЫЧИСЛИТЕЛЬНОЙ ТЕХНИКИ В СИСТЕМАХ УПРАВЛЕНИЯ МЕТАЛЛУРГИЧЕСКИМИ
АГРЕГАТАМИ
1. ОСОБЕННОСТИ МЕТАЛЛУРГИЧЕСКИХ ПРОЦЕССОВ С ТОЧКИ ЗРЕНИЯ ИСПОЛЬЗОВАНИЯ ВЫЧИСЛИТЕЛЬНОЙ ТЕХНИКИ ДЛЯ ИХ УПРАВЛЕНИЯ
Большинство технологических процессов металлургического
производства являются сложными физико-химическими процес сами, сопровождающимися экзо- и эндотермическими явлениями. Все эти процессы характеризуются многосторонними связями от дельных параметров и сопровождаются значительными объема ми потоков материалов и энергий.
Управление процессом осуществляется путем количественно го и качественного изменения этих потоков в соответствии с его внутренними и выходными параметрами. Таким образом, управ ление процессом требует наличия контроля этих параметров и знания взаимосвязей между ними. Контроль осуществляется при помощи измерительных приборов, показания которых яв ляются основным источником информации о ходе технологиче ского процесса. Причем ход .процесса характеризуется не только
самими показаниями, но и сочетанием показаний отдельных при боров, а также общей тенденцией изменения этих показаний.
Из-за недостаточного развития современной измерительной техники целый ряд параметров процесса еще не удается контро лировать. Так, не контролируются такие существенные парамет
ры ванны мартеновской печи, как скорость выгорания углерода
и скорость раскисления стали; химический состав металла в ван не определяется лишь периодически и с большими запаздыва ниями.
Кроме того, целый ряд параметров невозможно измерить не посредственно, они могут быть вычислены лишь на основании по казаний нескольких приборов. Применение средств вычислитель ной техники позволяет во многих случаях непрерывно и автома тически вычислять эти параметры и осуществлять по ним регули рование процесса.
55
Обычно целью автоматического управления процессом яв ляется достижение наиболее высоких технико-экономических по казателей, которые возможны лишь при определенном соотноше нии входных и внутренних параметров процесса. В ряде случаев это соотношение выражено неявно и может быть найдено лишь опытным путем или расчетом.
Применение вычислительной техники позволяет находить
оптимальные соотношения параметров либо на основании стати стической обработки результатов работы агрегата, либо на осно вании исследования математического описания—-уравнения
процесса.
Обычно на процесс непрерывно воздействуют возмущения,
вызывающие нежелательные отклонения параметров. В первую очередь такими возмущениями являются количественные и ка чественные нарушения потоков материалов и энергий. Кроме этих возмущений, на -процесс воздействуют нарушения работы агрегата, связанные с ограниченным срокам его службы и вызы вающие изменения характеристик агрегата. Так, износ огнеупо ров, зашлакование изменяют величины тепловых сопротивлений и гидродинамику газовых потоков мартеновской печи; износ вал ков вызывает увеличение зазора между валками и изменение толщины полосы на прокатном стане; отложения в трубопрово
дах химических производств повышают их сопротивление, что приводит к росту давлений или температур, и т. д.
Включение в систему управления процессом вычислительного устройства позволяет заранее определить на основании матема тического описания процесса, какое влияние окажут возмущения на выходные параметры процесса, и своевременно принять меры для компенсации этого влияния.
Так, например, изменение температуры прокатываемого ме
талла вызывает изменение толщины конечного продукта, кото рое может быть компенсировано соответствующим изменением положения нажимных винтов клетей. Вычислительное устройство рассчитывает на основании известных соотношений — уравнеяий, заложенных в это устройство,—как следует изменить обжатие по клетям.
Однако из-за чрезвычайного многообразия взаимосвязей меж
ду параметрами процесса и недостаточной изученности их точное математическое описание процесса обычно невозможно. В ре зультате анализа процесса могут быть установлены лишь приб лизительные соотношения в виде полуэмпирических формул, коэффициенты которых могут изменяться в каких-то ограничен ных пределах. Это обстоятельство является одним из основных препятствий на пути широкого применения вычислительных устройств в системах автоматического регулирования. Чтобы устранить этот недостаток, системы автоматического регулиро вания снабжают вторым вычислительным устройством, которое, сравнивая расчетные данные с фактическими, уточняет значения
56
коэффициентов приближенного уравнения, вводя поправки в работу первого вычислительного устройства.
На рис. 44 приведена структурная схема системы автомати ческого регулирования с двумя вычислительными устройствами. В общем случае объект может быть оборудован обычными авто матическими регуляторами АР, которые поддерживают неизмен
ными выходные параметры.
Нагрузка
Управляющее (вычислительное устройство ВУ1 на основании из мерений возмущающих воздей ствий, действующих на вход объ екта (регулирования, рассчитывает
(необходимые изменения устаню--
врк регуляторов АР. В таком виде система регулирования по вели чине возмущающих воздействий является разомкнутой. Замыкание системы осуществляется через второе вычислительное устройство ВУ2, куда подаются результаты измерений как выходных, так и
входных параметров системы.
В частных случаях регуляторы АР могут отсутствовать, и коман ды, вырабатываемые устройством
ВУ1, подаются на соответствую
Рис. 44. Система автоматического
управления с двумя вычисленны ми устройствами
щие .исполнительные устройства, Замыкание системы вания через вычислительное устройство ВУ2 позволяет осуще
ствить ее самонастройку, т. е. установление таких параметров си стемы, при которых регулируемый процесс имеет .оптимальные
показатели.
Управление металлургическими процессами усложняется тем, что большинство этих процессов циклические. Это связано с рез
кими изменениями характеристик агрегатов на различных стади ях цикла. Так, в мартеновской печи после расплавления, являю
щегося чисто эндотермическим процессом, начинается процесс кипа, связанный с выделением тепла самой ванной. По мере по
вышения температуры мартеновской печи изменяются ее гидрав лические характеристики и т. д.
В циклических процессах потоки материалов и энергий дол жны непрерывно изменяться в количественном и качественном
отношениях по определенной программе, которая в свою оче редь должна изменяться в соответствии с указанными выше внешними возмущениями, воздействующими на процесс. Чрез вычайная сложность взаимосвязей, характеризующих технологи
ческий процесс в этих условиях, не позволила еще установить их количественные соотношения, т. е. до сего времени отсутствует
57
математическое описание металлургических процессов с учетом их динамики.
В настоящее время для ряда агрегатов (например, для мар
теновских печей) практикуется программное управление, которое обеспечивает изменение уставок регуляторов по ходу процесса на основании «уточненной технологической инструкции». Эта инструкция составляется на основе статистической обработки опытных данных о работе агрегата. Хотя такое программное
управление и улучшает ход процесса, однако оно не обеспечивает его оптимальности при данных конкретных условиях. В связи с
этим возникает необходимость непрерывной коррекции програм мы с учетом фактического влияния возмущений, воздействующих на процесс. Такая коррекция принципиально может быть достиг нута включением в систему управления вычислительной машины или устройства, выявляющего изменение характеристики агрега
та, вызванное влиянием возмущений.
Чрезвычайная сложность решения задач комплексного управ ления металлургическими процессами с помощью вычислитель ной машины не позволила до настоящего времени осуществить такое управление. Однако вычислительная техника, главным об разом непрерывная, находит все более широкое применение в отдельных системах управления и контроля параметров процес
са. Применение ее значительно улучшает качество управления, а также позволяет создавать системы управления и контроля параметров, не поддающихся непосредственному физическому измерению.
Ниже описаны примеры использования вычислительной тех ники в системах регулирования в доменном, сталеплавильном и
прокатном производствах.
2. НЕПРЕРЫВНЫЕ ВЫЧИСЛИТЕЛЬНЫЕ УСТРОЙСТВА В СИСТЕМЕ РЕГУЛИРОВАНИЯ АГЛОМЕРАЦИОННОЙ МАШИНЫ
Процесс производства агломерата заключается в спекании кусков шихты под действием высокой температуры при горении кокса, входящего в состав шихты. Спекание осуществляется на движущейся агломерационной ленте, на которую ровным слоем насыпана заранее подготовленная шихта. Зажигание кокса в шихте производится специальными горелками; процесс горения поддерживается по всей рабочей длине аглоленты за счет кис лорода воздуха, просасываемого эксгаустером через слой шихты.
По мере движения аглоленты слой выгоревшего кокса в шихте все увеличивается, и полное выгорание должно закончиться пе ред выдачей агломерата, образовавшегося в процессе спекания, с заднего конца ленты.
Исследования показали, что процесс выгорания кокса, а сле довательно, и процесс агломерации, идет равномерно по длине ленты.
58 .
На рис. 45 приведена схема распределения агломерата по длине ленты. Заштрихованный участок показывает расположение
шихты с невыгоревшим коксом. Скорость выгорания V зависит от толщины слоя шихты Н и скорости движения аглоленты vh\
где L — длина участка ленты, на котором процесс агломерации заканчивается.
Рис. 45. Схема распределения шихты с выгоревшим коксом по длине аглоленты
Для получения максимальной производительности агломера
ционной машины необходимо, чтобы рабочая |
длина |
ленты Lh |
полностью использовалась, т. е. L = Lh. При |
данной |
толщине |
слоя Н этому условию соответствует скорость |
, равная |
Скорость выгорания кокса зависит также от количества про сасываемого через шихту воздуха, т. е. от разрежения, создавае мого эксгаустером в камерах, расположенных под аглолентой, и проницаемости шихты, что, в свою очередь, определяется соста вом шихты и качеством ее обработки.
На рис. 46 приведена схема взаимосвязей, определяющих
скорость выгорания кокса и качество агломерата. Если процесс выгорания полностью заканчивается на ленте, то качество агло мерата зависит только от состава шихты и качества ее обработ ки. При данной руде подбирается такой состав шихты, который отвечает заданному качеству агломерата. Поэтому одной из за
дач автоматического регулирования агломерационной машины является поддержание постоянного состава шихты. Наилучшим образом это достигается при весовом дозировании отдельных компонентов.
На рис. 47 приведена блок-схема автоматического весового дозирования шихты. В состав шихты входят руда, горячий воз врат, колошниковая пыль, кокс и вода. Изменение веса подавае мой руды и горячего возврата вызовет изменение задания регу ляторов весового дозирования кокса и колошниковой пыли, до бавляемых в шихту в заданной пропорции. Вода дозируется в
59
Рис. |
46. |
Схема |
взаимосвязей |
параметров в |
процессе |
|
|
|
агломерации: |
|
|
а |
— бункера; |
б — миксер; в — эксгаустер; г — аглолента; |
|||
1— состав |
шихты; |
2—качество перемешивания; 3—проницаемость |
|||
шихты; 4 |
— разрежение в камерах; |
5 — качество |
агломерата; |
6 — скорость спекания
Рис. 47. Блок-схема весового дозирования шихты:
/—бункера с рудой; 2—задатчик питателей руды; 3 — весы; 4—бункер с коксом; 5 — бункер с колошниковой пылью; 6—задатчик регулятора соотношений; 7 — вентиль; 8—миксер; 9—элемент сравнения; 10 — изме ритель уровня горячего возврата; И — бункер горячего возврата