
Пылисистемы_Жуков
.pdf
шнек; 28 - бункер пыли; 29 - трубопровод влагоотсоса; 30 - трубопровод рециркуляции; 31 - короб сбросного воздуха; 32 - сбросная горелка; 33 - вентилятор горячего воздуха; Рисунок 3.7 – Индивидуальная разомкнутая после мельничного устройства схема пылеприготовления с
промежуточным бункером
Регулирование температуры газов перед мельницей при изменении влажности угля или нагрузки котла производится регулятором температуры.
Особенностью схемы, показанной на рисунке 3.7 , является использование всех уходящих газов для сушки топлива, что существенно повышает экономичность котельной установки.
Регулирование температуры сушильного агента перед мельницей осуществляется изменением количества газов, отбираемых из топки, а также пропуском части или всего воздуха через обводные линии мимо первой ступени воздухоподогревателя, непосредственно во вторую ступень или мимо всего воздухоподогревателя. Схема (рис. 3.7) целесообразна при резких колебаниях влажности топлива.
Для котлов производительностью меньше 50 т/ч в отдельных случаях может применяться менее экономичная схема (рис. 3.8). В этой схеме предусматривается частичный съем влаги в трубе-сушилке или в другом типе подсушивающего устройства со сбросом отработавших газов в атмосферу (или газоход котлоагрегата) после предварительной их тщательной очистки в пылеулавливающих устройствах. Топливо подсушивается в мельничном устройстве, где снимается дополнительно часть влаги.
1 - бункер сырого угля; 2 - автовесы; 3 - весовой бункер; 4 - питатель угля; 5 - устройство для исходящей сушки; 6 - мигалка; 7 - мельница; 8 - сепаратор; 9 -мельничный вентилятор; 10 - короб первичного воздуха; 11- клапан присадки холодного воздуха; 12 - горелка; 13 - короб вторичного воздуха; 14 - парогенератор; 15 - газопровод; 16 - воздухопровод горячего воздуха; 17 - воздухоподогреватель; 18 - дутьевой вентилятор; 19 - взрывной клапан; 20 - смесительная камера; 21 - течка сырого угля; 22 - отсекающий шибер; 23 - расходомер; 24 - циклон; 25 - атмосферный клапан; 26 - перекидной шибер; 27 - шнек; 28 - бункер пыли; 29 - трубопровод влагоотсоса; 30 - трубопровод рециркуляции; 31 - короб сбросного воздуха; 32 - сбросная горелка; 33 - вентилятор горячего воздуха; Рисунок 3.8 – Индивидуальная разомкнутая после подсушивающего устройства схема
пылеприготовления с промежуточным бункером
3.8 Центральные разомкнутые схемы пылеприготовления
На рис. 2.8, а показана схема центрального пылезавода для бурых углей. В этой схеме предусмотрена подсушка топлива в паровой трубчатой сушилке, обогреваемой отборным или отработавшим паром турбин, а размол – в молотковой мельнице, имеющей замкнутую циркуляцию воздуха. Отработавший воздух сушилок, а также часть циркулирующего в мельнице воздуха после очистки от пыли выбрасываются в атмосферу.

В схеме на рис. 2.8, а вместо электрофильтра может быть применена двухступенчатая очистка воздуха от пыли в циклоне и мокрой шахте. Пыль транспортируется в котельную винтовыми пневматическими насосами.
На рис. 2.8, б показана схема центрального пылезавода для АШ, полуантрацитов и каменных углей. Особенностью схемы является применение шаровых барабанных мельниц с механической выгрузкой мельничного продукта, механического транспорта топлива в пылесистеме, а также сепаратора пыли с замкнутой циркуляцией воздуха. При использовании схемы, показанной на рис. 2.8, б, для АШ и полуантрацитов взрывные предохранительные клапаны не устанавливаются.
По «Нормам технологического проектирования электростанций» центральный пылезавод, как правило, применяется для блоков 500 ÷ 800 МВт, за исключением блоков, работающих на сухих каменных углях типа экибастузского. В последнем случае, как правило, применяется индивидуальная схема пылеприготовления с прямым вдуванием и молотковыми мельницами.
Для блоков 300 МВт применяется, как правило, индивидуальная схема пылеприготовления. Для этих же блоков, работающих на влажных бурых углях, выбор схемы пылеприготовления должен быть обоснован технико-экономическим расчетом.

4 ОСНОВНЫЕ ХАРАКТЕРИСТИКИ МЕЛЬНИЧНОГО ОБОРУДОВАНИЯ
Измельчение и подсушка топлива осуществляется в пылеприготовительной системе, основным элементом которой является мельница. В настоящее время в энергетике используют следующие типы мельниц:
∙шаровые барабанные мельницы (ШБМ);
∙среднеходные мельницы (СМ);
∙молотковые мельницы (ММ);
∙мельницы-вентиляторы (MB).
Выбор схемы и оборудования пылесистем зависит от физических и технических характеристик сжигаемого топлива.
Качество топливной пыли оказывает большое, а иногда решающее влияние на экономичность сжигания и на работу отдельных элементов топки и котельного агрегата в целом.
При сопоставлении и выборе типа мельниц в общем случае необходимо провести анализ следующих данных:
∙возможность получения пыли требуемого качества при измельчении конкретного топлива;
∙капитальные расходы;
∙эксплуатационные расходы на привод пылеприготовительного оборудования;
∙эксплуатационные расходы на изменение КПД котла при равной тонкости пыли (учет изменения присосов холодного воздуха для пылесистем, работающих под разрежением), равномерности структуры пыли;
∙эксплуатационные расходы на ремонт пылеприготовительного оборудования;
∙условия взрывобезопасной эксплуатации; маневренности котла, оборудованного сравниваемыми типами мельниц;
∙простота управления и автоматизации.
Из всех типов мельниц наиболее универсальными являются шаровые барабанные мельницы (ШБМ), однако по сравнению с другими мельницами они более металлоемки, расходуют больше энергии на размол и пневмотранспорт пыли. Поэтому они используются в основном для тонкого
размола ( R90 =10-25%) топлив с малым выходом летучих веществ, многозольных и трудноразмалываемых топлив, где применение других типов мельниц невозможно, в пылесистемах с промбункером, под разрежением.
Молотковые мельницы (ММ) имеют высокие экономические показатели при относительно
грубом размоле ( R90 >40%) топлив с высоким выходом летучих веществ( Vdaf >28%). Они используются как в системах с прямым вдуванием топлива, так и с промбункером, и могут работать под наддувом и разрежением.
Валковые среднеходные мельницы (СМ) применяются для размола каменных и маловлажных бурых углей, однако они очень чувствительны к попаданию вместе с топливом посторонних
металлических предметов и быстро изнашиваются при размоле топлив с повышенной абразивностью.
Мельницы-вентиляторы (МВ) используются для размола высоковлажных бурых углей с предварительной сушкой их топочными газами в специальной трубе-сушилке.
В соответствии с этими общими положениями и согласно рекомендациям по расчету и проектированию пылеприготовительных установок /2/ выбор типа мельницы производится в
'
зависимости от вида и марки топлива, его размолоспособности (Gr VTi ), выхода летучих веществ
( Vdaf ) и требуемой тонкости пыли ( R90 ) по данным таблиц 3.1 и Приложения А. Схема пылеприготовления определяется видом топлива, его приведенной влажностью, количеством влаги, которое необходимо испарить в процессе сушки, типом мельницы, типом топочного устройства, производительностью котла и характером его нагрузки.
4.1 Шаровые барабанные мельницы
Шаровая барабанная мельница (ШБМ) состоит из цилиндра (барабана) диаметром 2÷4 м и длиной 3÷10 м, частично заполненного шарами диаметром 30÷60 мм (рис.4.1). Внутренние стенки
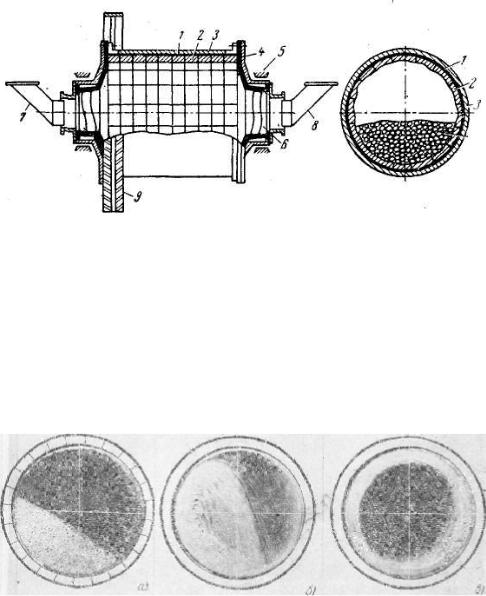
барабана покрыты толстыми плитами (броней). Барабан от электродвигателя через редуктор вращается со скоростью 16÷25 об/мин.
При вращении барабана шары поднимаются на определенную высоту и падают. Размол топлива происходит как за счет удара шаров, так и вследствие истирания топлива переме- щающимися шарами (рис.4.2).
1 – корпус барабана; 2 – броневые плиты; 3 – изоляция; 4 – торцовый фланец мельницы с укрепленным вкладышем подшипника; 5 – корпус подшипника; 6 – винтовые выступы; 7 – входной патрубок; 8 – выходной патрубок; 9 – ведомая шестерня (зубчатый венец); 10 –шары
Рисунок 4.1 – Шаровая барабанная мельница (схематический чертеж)
Броня слабо участвует в размоле топлива. Она нужна главным образом для организации подъема шаров и защиты барабана от удара. Подъем шаров зависит от формы броневых плит, которые обычно выполняются волнистыми. Снаружи барабан мельницы обшивается тепловой и звуковой изоляцией.
Барабан опирается полыми цапфами передней и задней горловины мельницы на подшипники скольжения, охлаждаемые водой. Это допускает надежную работу подшипников при протекании через цапфы газа с температурой до 350° С.
Рисунок 4.2 – Движение шаров в мельнице в зависимости от числа оборотов.
Топливо подается через соединительный патрубок в переднюю горловину мельницы, а пыль выносится из задней. Соединительные патрубки располагаются под углом 45°, что предотвращает забивание их углем или пылью. В месте соединения неподвижных патрубков с полыми цапфами имеются сальниковые уплотнения с войлоком или фетром.
Размолотое топливо выносится из мельницы потоком сушильного газа, скорость которого определяет крупность вынесенной пыли. Обычно скорость газа, отнесенная к полному сечению барабана, составляет 1÷3 м/сек, чему соответствует сопротивление мельницы 100÷250 мм вод. ст. Пыль из слоя шаров выносится с трудом и подвержена истирающему действию шаров, поэтому мельницы выдают переизмельченную пыль.
Эффективность размола зависит от шаровой загрузки мельницы. Обычно барабан мельницы загружается шарами на 20÷35% от своего объема. В процессе размола шары изнашиваются, уменьшаются в диаметре. По мере износа добавляют шары наибольшего первоначального размера, износ шаров и брони составляет 100÷300 г/т топлива.
Производительность и эффективность размола зависят от числа оборотов мельницы. При малых оборотах шары поднимаются на небольшую высоту и скатываются вниз (рис. 4.2). В этом случае размол протекает плохо, а отвеивание готовой пыли из плотного слоя шаров затруднено.
При увеличении числа оборотов барабана шары поднимаются на большую высоту и падают по
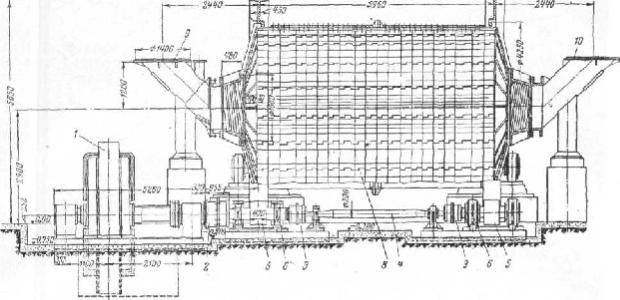
параллельным траекториям, что улучшает размол и отвеивание готовой пыли. При дальнейшем
увеличении числа оборотов шары центробежной силой прижимаются к барабану и перестают падать. Размол ухудшается, и производительность мельницы резко падает. Число оборотов, при котором прекращаются отрыв и падение шаров, называется критическим. Это число оборотов может быть подсчитано из баланса сил, действующих на шар (силы тяжести и центробежной силы). Таким образом, критическое число оборотов падает с увеличением диаметра барабана Dб. Эффективная работа ШБМ может иметь место только при скорости, меньшей критической (обычно 75% от нее).
Шаровые барабанные мельницы выпускаются нескольких размеров. Типоразмер мельницы обозначается дробью, числитель которой определяет диаметр, а знаменатель – длину барабана, выраженные в сантиметрах. Диаметр барабана измеряется по средней линии волны броневых плит, а длина – по внутреннему размеру цилиндрической части.
Барабан мельницы приводится в движение двигателем переменного тока обычно посредством зубчатой передачи. При малом числе оборотов двигателя (100÷150 об/мин) передача состоит из ведущей шестерни, насаженной на вал двигателя, и ведомого зубчатого венца, посаженного на барабан мельницы. Если число оборотов двигателя велико, то между двигателем и ведущей шестерней устанавливают редуктор. При небольшой мощности обычно предпочитают высокоскоростной мотор и редуктор, поскольку стоимость и эксплуатационные расходы низкооборотного двигателя превышают расходы, связанные с установкой редуктора. С
повышением единичной мощности оказывается более экономичным применение безредукторного привода.
Из-за больших размеров зубчатого венца (до 4 м) трудно выполнить точную нарезку зубьев, поэтому к.п.д. зубчатого привода может быть сравнительно невысоким. Это в некоторых случаях делает целесообразным применение фрикционного привода.
1 – электродвигатель; 2 и 3 – муфты; 4 – вал; 5 (7) – ведущий (опорный) ролики; 6 – подшипники; 8 – барабан; 9 и 10 – передняя и задняя горловины.
Рисунок 4.3 – Шаровая барабанная мельница производительностью 32 г/ч (продольный разрез).
На рисунке 4.3 показана конструкция мельницы производительностью 32 т/ч с фрикционным приводом. Барабан мельницы приводными колесами опирается на четыре ролика, два из которых являются ведущими, непосредственно соединенными с низкооборотным двигателем.
В мельнице происходят размол и сушка. В соответствии с этим производительность мельницы разделяют на размольную и сушильную. Размольная производительность характеризует количество топлива, которое может быть размолото по условиям затраты энергии на помол. Этой производительности соответствует определенный расход сушильного газа, необходимый для отвеивания топлива.
Сушильная производительность мельницы определяется условиями сушки и показывает количество топлива, которое может быть подсушено в мельнице до требуемой влажности при заданном (по размолу) расходе сушильного газа.

Рабочая производительность мельницы может быть ограничена условиями либо размола, либо сушки. Для сухих и твердых топлив рабочая производительность определяется по размольной. Напротив, для мягких и влажных топлив рабочая производительность ограничивается сушильной производительностью.
Размольная производительность определяется эмпирическими зависимостями, форма которых определяется видом топлива, тонкостью его размола, конструкцией мельницы и режимом ее работы. В ШБМ производительность растет с увеличением диаметра, длины и числа оборотов барабана, степени заполнения мельницы шарами, коэффициента размолоспособности топлива. Производительность снижается с повышением тонкости размола, крупности кусков сырого топлива и ухудшения условий вентиляции мельницы.
Удельный расход электроэнергии на помол зависит от конструктивных особенностей мельниц, влажности топлива, свойств угля и тонкости помола. Для данной конструкции мельницы удельный расход электроэнергии на помол возрастает с уменьшением ее производительности.
Шаровые барабанные мельницы относятся к классу тихоходных мельниц, работающих; по принципу удара и истирания. Они пригодны для размола углей всех сортов. Однако при размоле
мягких углей с большим выходом летучих расход электроэнергии на помол у ШБМ получается выше, чем у других мельниц.
В ШБМ описанного типа пыль выносится потоком сушильного газа, который продувает (вентилирует) мельницу. В соответствии с этим такие мельницы называются вентилируемыми.
При размоле сухого или предварительно подсушенного топлива применяют невентилируемые мельницы, в которых топливо только размалывается, но не подсушивается. Сухая пыль, образуемая в мельнице, легкотекуча. Ее движение, как и маловязкой капельной жидкости, может происходить под действием небольшого гидростатического напора.
Отобранная пыль механическим элеватором подается в сепаратор с так называемым замкнутым воздушным потоком.
Основные характеристики мельниц приведены в таблице 3.1[1] для ШБМ, а таблице 4.1 (3.2 в [1]) для ШКМ и в таблице 3.3[1] для ШБММ (шаровая барабанная мельница с механической выгрузкой продукта). В табл. 3.1[1] номинальные производительности ШБМ соответствуют ГОСТ
6795-63.
Типоразмер шаровой мельницы с цилиндрическим (ШБМ) и коническим (ШКМ) барабаном обозначается в виде дроби, в числителе которой дается диаметр цилиндрической части, а в знаменателе – длина барабана, выраженная в сантиметрах. Диаметр измеряется по средней линии выступов брони, а длина для ШБМ – по внутреннему размеру барабана между торцевыми крышками, а для ШКМ – между горловинами.
Шаровые барабанные мельницы при наличии подсушивающих устройств с восходящим или нисходящим потоком позволяют использовать сушильный агент с температурой до 900° С. При этом температура сушильного агента у входной горловины (перед подшипником) не должна превышать 450° С.
Шаровые барабанные мельницы снабжаются сепараторами пыли центробежного типа (см. гл. 6). Мельницы приспособлены для работы под резрежением. Мельницы с механической выгрузкой продукта снабжаются механическими сепараторами с замкнутой циркуляцией воздуха.
Таблица 4.1 – Шаровые мельницы с коническим барабаном Новокраматорского завода тяжелого машиностроения
|
Единица |
|
ШКМ |
|
|
ШКМ |
|
Наименование |
|
380 |
|
|
380 |
|
|
измерения |
|
|
|
||||
|
|
550 |
|
550 |
|
||
|
|
|
|
|
|||
Диаметр цилиндрической части барабана |
мм |
3800 |
3800 |
|
|||
Эквивалентный диаметр барабана |
мм |
3180 |
3180 |
|
|||
Длина барабана между горловинами |
м3 |
5500 |
5500 |
|
|||
Объем барабана |
43,7 |
43,7 |
|
||||
Номинальная скорость вращения барабана |
об/мин |
14,7 |
18,5 |
|
|||
Наибольшая мощность электродвигателя |
кВт |
2X520 |
|
|
2X630 |
|
|
Вес мельницы без электродвигателя и |
|
|
|
|
|
|
|
шаров |
т |
90 |
90 |
|
|||
Предельный вес загруженных шаров |
т |
70 |
70 |
|
|||
Диаметр патрубков |
мм |
1000 |
1000 |
|

|
|
1150 |
1150 |
Номинальная производительность |
т\ч |
25 |
30 |
4.2 Молотковые мельницы
Молотковые мельницы (ММ) по способу подвода газовоздушной смеси выполняются аксиальными и тангенциальными, соответственно они обозначаются ММА и ММТ. Типоразмер молотковой мельницы обозначается тремя цифрами: первая цифра – диаметр ротора, мм; вторая – его длина, мм; третья – скорость вращения, об/мин.
Основные характеристики выпускаемых мельниц ММА и ММТ приведены в таблице 3.4 и 3.5[1].
Мельницы больших типоразмеров с диаметром D > 1500 мм снабжаются полыми охлаждаемыми водой валами; допускается подача сушильного агента в эти мельницы с температурой: при диаметре ротора D > 1500 мм – до 450° С; при D = 1300 мм – до 400° С. Мельницы меньших типоразмеров снабжаются сплошными валами и оборудуются холо- дильниками. В эти мельницы допускается подача сушильного агента с температурой до 350° С.
Молотковые мельницы снабжаются инерционными и центробежными сепараторами, а мельницы производительностью до 20 т/ч по бурому углю также и шахтными сепараторами.
Все молотковые мельницы изготавливаются плотными и допускают давление сушильного агента 300 ÷ 400 мм вод. ст.
1 – корпус мельницы; 2 – сепаратор; 3 – ротор; 4 – била; 5 – течка топлива; 6 – короб горячего воздуха; 7 – выход готовой пыли.
Рисунок 4.4 – Молотковая мельница (аксиальная)
Молотковая мельница состоит из ротора и кожуха (рис. 4.4). Топливо подается на вращающийся ротор и размельчается ударами бил. Горячий воздух подводится пли по оси (аксильно), или по окружности (тангенциально). Поток воздуха подхватывает мелкие частицы топлива и выносит их в сепаратор, составляющий с мельницей один агрегат. Крупные частицы отделяются в сепараторе и снова размалываются. Сушка топлива происходит в процессе его дробления очень интенсивно и практически заканчивается в области ротора.
Обычно мельницы работают под наддувом. От сепаратора с помощью пылепроводов пылевоздушная смесь подводится к горелкам.

Ротор молотковой мельницы состоит из вала, на котором на шпонках укреплены диски. К дискам на шарнирах прикреплены билодержатели, с которыми шарнирно соединены била.
У мельниц большой производительности иногда применяют ротор, откованный целиком вместе с дисками. Ротор охлаждается водой, прокачиваемой по каналу, высверленному в центре вала.
В результате абразивного действия топлива била изнашиваются, что вызывает необходимость их замены. Степень износа бил зависит от абразивных свойств топлива и конструктивных особенностей мельницы.
Молотковые мельницы высокой производительности (30–50 т/ч) выполняются с танген- циальным подводом сушильного агента. Ротор мельниц этой серии имеет диаметр 1500 мм при числе оборотов 735 об/мин. При этом окружная скорость составляет 58 м/сек. Зазор между билами и корпусом в этих мельницах доведен до 30 мм. Все это увеличивает удельную производительность мельниц и снижает расход электроэнергии на помол.
4.3 Мельницы-вентиляторы
Мельница-вентилятор (MB) состоит из колеса с неподвижными лопатками, бронированного корпуса и сепаратора (рис. 4.5). Все они совмещены в одном агрегате, что делает эту мельницу компактной.
Сырой уголь подводится с торца мелющего колеса. За счет удара о лопатки уголь из- мельчается. Пыль из мельницы сушильным газом выносится в сепаратор. Крупные фракции отделяются в сепараторе, снова попадают на мелющее колесо, а мелкие выносятся потоком газа из сепаратора и под напором газа подаются к горелкам. Мельница-вентилятор с числом оборотов до 1 500 об/мин преодолевает сопротивление тракта и создает напор 150 - 200 мм вод. ст. В камере мелющего колеса имеет место разрежение, что позволяет подать на сушку топочные газы.
1 – корпус (типа улитка); 2 – мелющее колесо–вентилятор; 3 – предвключенная бильная часть; 4
– сепаратор; 5 – подвод топлива и воздуха.
Рисунок 4.5 – Мельница-вентилятор (с предвключенной бильной частью).
В этом случае интенсивная подсушка угля происходит в шахте, расположенной перед мельницей, за счет топочных газов с высокой температурой (900 ÷ 1100° С). Температура сушильного газа изменяется путем смешения воздуха и газа. Возможность организации
предварительной подсушки угля делает целесообразным применение мелющих вентиляторов для высоковлажных мягких углей с большим выходом летучих. Эти мельницы выполняются производительностью по бурому углю до 100 т/ч и более.
С повышением производительности мельниц растет размер колеса. Это ухудшает рав- номерность распределения топлива по отдельным лопаткам, что снижает экономичность и повышает местный износ. Экономичность дробления существенно повышается при выполнении мелющих вентиляторов с предвключенной бильной частью (рис. 4.5). В бильной части происходит частичный размол топлива и более равномерное распределение его по кольцевому зазору, примыкающему к лопаточному аппарату вентилятора.

Типоразмер мельницы-вентилятора (М-В) обозначается тремя цифрами: первая цифра – диаметр ротора, мм; вторая – рабочая ширина лопатки, мм; третья – скорость вращения, об/мин.
Основные характеристики М-В приведены в таблице 3.6[1].
1 - корпус; 2 - броневое покрытие; 3 - вал ротора; 4 - ступица ротора; 5 - основной диск; б - мелющие лопатки; 7 - блок подшипников; 8 - муфта; 9 – электродвигатель; 10 — корпус дверки; 11 – била; 12 - подшипники бильной части; 13 – электродвигатель бильной части; 14 – окно течки возврата; 15 – сепаратор; 16 – ловушка для металла и колчедана.
Рисунок 4.6 – Мельница-вентилятор консольного типа Мельницы-вентиляторы при наличии подсушки топлива в опускной шахте позволяют
использовать сушильный агент с температурой до 900° С. При этом температура сушильного агента на входе в мельницу не должна превышать 450° С.
Мельницы-вентиляторы снабжаются инерционными сепараторами пыли.
1 - бункер топлива; 2 – отсекающий шибер; 3 – питатель сырого топлива; 4 - сушильная шахта; 5 - мельница- вентилятор; 6 - инерционный сепаратор пыли; 7 - горелочное устройство; 8 - окно отбора газов для сушки топлива; 9 - смесительная камера; 10 - отключающий шибер; 11 - котел; 12 - дутьевой вентилятор; 13 - воздухопровод горячего воздуха; 14 - воздухоподогреватель; 15 - взрывной клапан; 16 — клапан присадки холодного воздуха; 17 - мигалка; 18
-форсунка для впрыска воды; 19 - пыледелитель; 20 - устройство для понижения температуры сушильного агента; 21
-газопровод дымовых газов
Рисунок 4.7 – Схема пылеприготовления с мельницей-вентилятором М-В 3400/900/490 к котлу П- 67 производительностью 2650 т/ч:
Использование мельниц-вентиляторов для подготовки к сжиганию высокореакционных бурых углей, лигнитов и фрезерного торфа с высокими значениями выхода летучих Vdaf > 40%, допускающих относительно грубый помол пыли R90 = 40 ÷ 50% и R1000 = 3 ÷ 6%, возможно, в

замкнутых системах пылеприготовления прямого вдувания пыли в топочную камеру котла вместе с отработанным влажным сушильным агентом через горелочные устройства (рис.4.7).
1 - муфта; 2 - система смазки; 3 - ходовая часть откатной дверки
Рисунок 4.8 – Мельница-вентилятор М-В 3300/800/490
1 – била; 2 – мелющее колесо.
Рисунок 4.9 – Мельница-вентилятор консольного типа с предвключенными билами: а – на одном валу с колесом; б – на отдельном валу с автономным приводом