
Строительные и дорожные машины. Основы автоматизации
.pdf494
ществует линейная зависимость между их твердостью и износостойкостью [13]bH , где относительная износостойкость материала при абразивном изнашивании (отношение износа эталонного материала к износу испытуемого); b коэффициент пропорциональности ((b 7,3); H твердость по Виккерсу (отношение нагрузки к площади пирамидальной поверхности отпечатка). Для термически обработанных сталей износостойкость также возрастает с увеличением твердости, но в меньшей степени. Если твердость повышена за счет наклепа поверхности, то абразивная износостойкость материала при этом практически не повышается.
Таким образом, с точки зрения износостойкости важно не только значение, но и происхождение твердости материала – получена ли она естественным путем, т. е. без искажения кристаллической решетки (за счет химического изменения состава металла или путем термообработки), или наклепом.
12.3. Изнашивание сопряженной пары во времени
Оценка скорости процесса изнашивания детали во времени vизн является необходимым этапом при решении задач эксплуатационной надежности. Зная временную характеристику, можно определить степень повреждения как функцию времени, т. е.
t |
|
u t vизн t dt, |
(12.4) |
0 |
|
Поскольку при изнашивании рассматриваются необратимые явления, то зависимость (12.4), как правило, будет монотонно убывающей функцией. Исключение могут составить случаи, когда степень повреждения характеризуется изменением какого-либо физико-химического фактора, оценивающего свойство материала (твердость, прочность структуры, химический состав и др.).
На практике при различных процессах изнашивания, чаще всего при изменении физической сущности процесса, соответственно меняется и закономерность, описывающая данное явление. Такие процессы получили название многостадийных. Типичным процессом многостадийного процесса может служить изнашивание сопряжение трущейся пары, когда многостадийность процесса повреждения возникает как следствие одновременного протекание нескольких процессов изнашивания, которые взаимодействуют между собой. Классическая форма кривой износа состоит из трех участков: период приработки tn , период установившегося, или нормального, изнашивания ty и период прогрессивного
или зоны катастрофического изнашивания tk . Каждый из этих периодов отражает качественное состояние пары. Переход из одного состояния в другое определяется количественным накоплением элементарных повреждений.
В период приработки за счет микронеровностей трущихся поверхностей трение происходит зачастую при граничной смазке и сопровождается выделением теплоты. Именно в этот период, согласно имеющимся теориям о трении,
495
наблюдается суперпозиция рассмотренных выше явлений при трении: упругое и пластическое оттеснение, микрорезание, адгезия и когезийный отрыв, а вследствие высоких температур – структурное изменение трущихся поверхно-
стей [8, 9].
Таким образом, в период приработки происходит не только количественное, но и качественное изменение трущихся поверхностей, т.е. объект как бы приспосабливается к условиям нагружения. Например, в процессе приработки трущейся пары вал-подшипник идет направленное изменение шероховатости поверхности и структуры поверхностных слоев. При этом скорость изменения микронеровностей поверхностей трения, а вместе с ней и скорость изнашивания постепенно уменьшается, и наступает второй более продолжительный период – период установившегося изнашивания.
Зона установившегося изнашивания характеризуется постоянством рельефа микронеровностей и увеличением зазора без существенных качественных изменений характера работы пары. В этой зоне объект приобретает некоторые стабильные свойства, отвечающие условиям нагружения. Если в зоне нормального изнашивания изменения, протекающие в элементе, носят в основном количественный характер, то с накоплением некоторого износа возникает качественный скачок в состоянии элемента, который заключается в существенном изменении происходящих явлений. На скорость изнашивания машины в целом начинают оказывать влияние новые факторы: вибрация (в результате увеличения зазоров отдельных сочленений или в результате износа и ослабления крепежных деталей), интенсивное изнашивание отдельных деталей и сочленений (вследствие нарушения или износа поверхностного упрочненного слоя, которые ранее не ощущались). Все это приводит к ухудшению состояния отдельных деталей и, наконец, к их разрушению.
Линейный износ в установившийся период можно определить по формуле
u kt vизнt, |
(12.5) |
где к vизн tg угол наклона прямой к оси абсцисс при установившемся износе.
Для износа с учетом приработки
u un vизнt,
где un износ за период приработки.
Вся трудность заключается в том, как определить скорость изнашивания. При интенсивном изнашивании изменения в состоянии элемента, так же как и при приработке, носят направленный характер. С момента начала интенсивного изнашивания идет направленное ухудшение качества поверхности, рост шероховатостей, появляются схватывания с последующим выравниванием крупных частиц и в конечном счете вызывает отказ. Скорость изнашивания характеризуется тангенсом угла наклона прямой на линейном участке (рис.12.2)
vизн du/dt tg ,
где dt ty .

496
Тогда скорость изнашивания детали можно представить в виде
umax un tg , ty
откуда ty umax un /tg .
Рис.12.2. Графическая интепретация влияния процесса изнашивания сопряжений
Из рис.12.2 видно, что срок службы
Tсл tn ty
или |
|
|
umax un |
|
|
|
T t |
, |
(12.6) |
||
|
|
||||
|
сл |
|
tg |
|
|
|
|
|
|
||
где tn время приработки; |
ty установившееся время работы (от конца прира- |
||||
ботки до появления предельного износа детали). |
|
||||
Величины umaxи tn |
для |
данной сопряженной пары |
постоянны, т. е. |
||
umax соnst и tn const. |
|
|
|
|
|
Из формулы (12.6) видно, что срок службы детали Tсл |
зависит от зазора в |
||||
конце приработки un |
и скорости изнашивания tg . С уменьшением tg срок |
службы сопряженной детали увеличивается на ty , т. е.
Tсл tn umax un ty . tg
Из рисунка видно, что чем меньше un1, тем больше Tсл. С уменьшением un1 до un2 cрок службы увеличивается на ty
Tсл tn umax un ty . tg
Если сопряжение подвергалось разборке, то происходит вторичная приработка и соответственно увеличение зазора на t .
Тогда
Tсл tn umax un ty . tg
497
Исследованиями установлено, что одна разборка сборочной единицы без какого-либо ремонта и обезличивания деталей, т. е. при сборке того же сочленения, в отдельных случаях снижает срок службы сопряженных деталей на 25…30 %. Поэтому разборка машин в процессе эксплуатации должна производиться только в случае крайней необходимости.
В общем виде формулу кривой изнашивания, отражающей особенности каждого участка, можно представлять следующим образом:
|
k tm |
|
|
1 n |
|
un k2ty |
||
u |
umax k3tmy ,
где k1, k2, k3 скорости протекания процесса изнашивания по стадиям. Повышение срока службы в условиях эксплуатации может быть реализова-
но за счет соблюдения правил приработки, своевременной замены смазочного материала, а также при соблюдении норм и правил эксплуатации, технического обслуживания и ремонта машин.
12.4. Техническое обслуживание и ремонт машин
Техническое обслуживание машин – это комплекс работ по поддержанию работоспособности при использовании по назначению, при хранении и транспортировании, который направлен на предупреждение повышенного износа деталей, отказов и повреждений всей машины. Техническое обслуживание машины проводят в принудительном порядке. Техническое обслуживание подразделяют на ежесменное (ЕО), проводимое перед началом или после каждой рабочей смены; периодическое (ТО-1, ТО-2, ТО-3), проводимое после отработки машиной установленного заводом-изготовителем количества часов; сезонное (СО), выполняемое два раза в году при подготовке машины к использованию в период последующего сезона (летнего или зимнего). В состав ЕО входят работы по смазке машины, предусмотренные схемой смазки, контрольный осмотр перед пуском в работу действий рабочих органов машины, ходовой части, тормозов, освещения, сигналов, автоматического управления. Затраты времени на ЕО определяются сложностью машины и учтены в Единых нормах и расценках на строительные, монтажные и ремонтно-строительные работы. При ТО выполняются операции технического ухода (очистка, мойка), осмотр и контроль состояния деталей, агрегатов, систем гидропривода, рабочего оборудования с целью выявления неисправностей, устранения обнаруженных дефектов, проведение крепежных, контрольно-регулировочных и смазочных работ.
При выполнении ТО-1 в него включаются все работы, предусмотренные ЕО, при проведении ТО-2 – все работы ТО-1, а работы при ТО-3 совмещают с текущим ремонтом. Высокие требования предъявляют к сезонному обслуживанию, а также к техническому обслуживанию при хранении машин. Сезонное
498
обслуживание включает подготовку машины к эксплуатации в осенне-зимний или весенне-летний периоды: в системах машины (тормозной, охлаждения, смазки, гидропривода и др.) заменяют сезонные эксплуатационные масла и жидкости, устанавливают или снимают утепления, приборы для запуска двигателей. Во время смены смазочных материалов и технических жидкостей тщательно промывают соответствующие системы. Состав работ по техническому обслуживанию при хранении машин зависит от предполагаемой длительности хранения и выполняют в соответствии с требованиями эксплуатационной документации.
В общем случае перед постановкой машины на хранение ее тщательно очищают и моют, окрашивают поврежденные участки окраски, проводят очередное ТО, промывают систему и заполняют ее новыми эксплуатационными жидкостями, на подверженные коррозии металлические части наносят антикоррозионную смазку, защищают машину от атмосферных осадков. В процессе хранения машина проходит периодическое консервационное обслуживание. Важное значение при техническом обслуживании придается диагностическим осмотрам, которые позволяют предотвратить возможные поломки отдельных элементов, заменить или отрегулировать положение детали до выхода ее из строя, получить информацию о состоянии различных частей машины, сократить потребность в деталях путем заблаговременно их ремонта, не допускать преждевременный ремонт машин, находящихся в достаточно хорошем состоянии. С помощью переносных диагностических средств оценивают параметры двигателя, электрической и гидравлической систем. По взятым пробам масла из картера двигателя с помощью спектрофотометра оценивают степень его старения, наличие в нем воды и антифриза, концентрацию железа, алюминия и меди. При данном виде анализа учитывают закономерность изменения концентрации металлических частиц в масляной системе.
Повышение концентрации частиц свидетельствует об интенсивности износа и о нарушении условий работы сопряжений. На основании таких анализов принимают решение о проведении внеплановых работ по ТО или ТУ, о сроках замены и восстановления элементов двигателя. Особое внимание уделяется диагностическому обследованию и техническому обслуживанию гидропривода. В гидроприводе используется сложное оборудование с парами трения, изготовляемыми с высокой (прецизионной) точностью. Опыт эксплуатации машин с объемным гидроприводом и анализ влияния условий эксплуатации показали, что основными факторами, влияющими на долговечность гидропривода, являются климатические условия, эксплуатационные свойства и степень чистоты рабочей жидкости, регулярность замены фильтров, а также уровень технического обслуживания. Определение неисправностей гидравлических систем обычно осуществляют в несколько этапов. Сначала проводят визуальную проверку, после этого в рабочем режиме и в заключение — на стендах и приборами. Визуальный осмотр проводят при отключенном двигателе. Прежде всего выясняют дату последней замены жидкости и фильтров, затем оценивают сте-
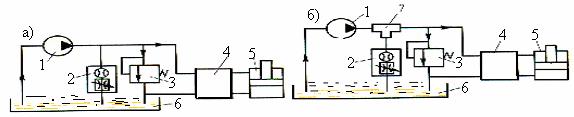
499
пень засоренности фильтров и наличие в них частиц металла, резины и пр. Выявляют течи и повреждения в трубопроводах, соединениях и цилиндрах. Проверяют рычажные механизмы управления на регулировку, заедание, повреждение и износ. Проверку в рабочем режиме осуществляют при холостом движении и под нормальной нагрузкой. При этом замеряют продолжительность рабочих движений и сравнивают ее с нормативной.
Увеличение продолжительности свидетельствует об изнашивании насоса, неисправности предохранительных клапанов, потере герметичности в сопряжении поршень — цилиндр. Для определения мест неисправностей, выявлении их причины и характера применяют специализированные стационарные посты и мобильные установки, оснащенные специальной диагностической аппаратурой. Для диагностического обследования непосредственно на машинах широко применяют легкие, компактные приборы — гидравлические тестеры (дросселирасходомеры), измеряющие с высокой точностью производительность насосов, температуру масла, рабочее давление в гидравлической системе. Пропуск потока жидкости осуществляется через входное отверстие в корпусе прибора. С помощью нагрузочного клапана (дросселя), регулируемого вручную, можно изменять размер сечения отверстия и тем самым варьировать в широких пределах давление в системе, измеряемое манометром. При измерении характеристик гидравлической системы применяют два вида подключений гидравлического тестера. При последовательном подключении (рис. 12.3, а) входное отверстие тестера включают после определенного элемента системы (насоса, предохранительного клапана, гидрораспределителя), а выходное соединяют с гидравлическим баком.
Рис.12.3. Схема подключения гидравлического тестера:
а) − последовательное включение; б) − включение через тройник;1−насос; 2 − тестер; 3 −предохранитьельныйклапан;4 − распределитель;5 −цилиндр;6 − бак; 7 −тройник
Затем при одинаковой скорости вращения вала насоса измеряют поток жидкости без нагрузки и поток жидкости с нагрузкой, создаваемой искусственно с помощью дросселя. Разница между двумя показаниями характеризует утечку в элементах системы от насоса до точки подключения тестера. Сравнивая показания утечки с допустимыми значениями, можно определить техническое состояние элемента системы. Расположив тестер непосредственно после предохранительного клапана, можно определить правильность его регулировки путем изменения нагрузки в системе за счет дросселя. При другом соединении тестер подключают после насоса с помощью тройника (рис. 12.3, б). Разница в показаниях тестера при открытом нагрузочном клапане и при рабочем давлении
500
жидкости, поступающей к цилиндру (нагрузочный клапан прикрыт), характеризует утечку во всей системе. Прекращение потока жидкости через прибор при отключенном распределителе соответствует открытию предохранительного клапана. Показания манометра тестера в этом случае характеризуют регулировку предохранительного клапана. Для определения места и величины утечки замеряют расход жидкости с открытым и прикрытым нагрузочным клапаном тестера при последовательном отключении элементов гидросистемы, начиная с наиболее удаленных от насоса. При использовании тестера в конструкции машины должна предусматриваться возможность подключения его частей, а также отключение отдельных элементов гидросистем (при второй схеме подключения).
Текущий ремонт (ТР). Текущий ремонт осуществляют в плановом порядке, а также по потребности согласно данным диагностических осмотров. При этом выполняются все виды работ по техническому обслуживанию машины, замене или восстановлению изношенных деталей и агрегатов (кроме базовых) при частичной разборке машины. Ремонтные работы включают также сварку, слесарные и станочные работы, нанесение наплавок на изношенные детали и поверхности. Основной метод текущего ремонта — агрегатно-узловой. Несложные текущие ремонты выполняются на рабочих местах с помощью мобильных мастерских, находящихся в ведении ремонтно-эксплуатационной базы треста или управления механизации. Сложные виды текущего ремонта выполняют в полустационарных или стационарных мастерских, обладающих обменным фондом агрегатов, пользующихся частым спросом. Агрегаты, требующие капитального ремонта, направляют в специализированные мастерские по капитальному ремонту машин. Ремонт гидроаппаратуры производят на специализированном ремонтном предприятии, использующем заводскую технологию и оборудование с соблюдением соответствующих квалитетов точности (5...6-й квалитеты). Отремонтированные элементы гидропривода подвергают приемо-сдаточным испытаниям на специализированных стендах в соответствии с техническими условиями на изделие. При текущем ремонте гидроаппаратуры проводятся регулировочные, а также работы по устранению мелких неисправностей. При серьезных неисправностях элементы гидропривода заменяют на новые или из обменного фонда.
Капитальный ремонт (КР). Капитальный ремонт в целом осуществляют по потребности. Решение о проведении такого ремонта принимается комиссией в составе главного инженера или главного механика организации, на балансе которой находится машина. Основанием для решения о проведении капитального ремонта или отказа от него являются технические и экономические признаки. Наиболее распространенными являются следующие технические признаки: повреждение базовой детали (станины, рамы, несущего кузова), устранимое только путем полной разборки машины; необходимость замены двух и более сложных агрегатов – двигателя, сложных редукторов отбора мощности, коробок перемены передач. Такие агрегаты направляют в капитальный ремонт, если они

501
не могут быть восстановлены путем текущего ремонта, а также если для ремонта базовой и основной детали требуется полная их разборка.
Комиссия может разрешить дальнейшую эксплуатацию машины, если на основе визуального осмотра и данных диагностики установлено, что машина сохранила определенный ресурс работоспособности. В этом случае составляется соответствующий акт. Капитальный ремонт машин выполняется централизованно на специализированных ремонтных заводах. Различают два основных вида организации капитального ремонта: необезличенный и обезличенный. При необезличенном виде ремонта восстановление деталей из сборочных единиц проводят с учетом их принадлежности к данной машине. Отремонтированные детали и сборочные единицы устанавливают на ту же машину, с которой они были сняты.
При обезличенном виде ремонта изношенные детали и сборочные единицы заменяют новыми или отремонтированными из числа снятых ранее с других машин. Такой вид ремонта называют агрегатным. Широкое применение агрегатного метода ремонта позволяет существенно сократить срок пребывания машины в ремонте при сравнительно высоком уровне его качества. Ресурс отремонтированных сборочных единиц на передовых отечественных ремонтных предприятиях составляет не менее 80 % новых. С увеличением парка машин, повышением их годовой выработки возрастает потребность в запасных частях. Одновременно наблюдается рост ущерба от простоя машин вследствие отсутствия деталей при ремонте. Неравномерность потребления и поставок запасных частей вызывает необходимость создания их запасов. Величина запасов, их состав, а также способ доставки сказываются на единовременных затратах, затратах на хранение, транспортировку и управление. Как показывает отечественный и зарубежный опыт, обеспечение запасными частями при минимальных затратах возможно при создании рациональной системы обеспечения запасными частями. Такая система строится на нескольких уровнях (4, 5 уровней – рис. 12.4). В ее основу положены учет заказов потребителей, изучение закономерностей спроса на детали определенной машины, пополнение запасов деталей и агрегатов, поступающих с заводов-изготовителей, и за счет восстановленных деталей и агрегатов, учет израсхо-
дованных деталей, инвентаризация запасов, доставка запас- |
|
ных частей потребителю и др. Различают детали, |
Рис. 12.4. Структурная |
пользующиеся большим спросом группа А) – до 10 % по |
схема обеспечения |
номенклатуре и 90 % стоимости; редим спросом (группа В) запасными частями-
–до 15% по номенклатуре и 6 % стоимости; малым спросом (группа С) – до 75 % по номенклатуре и около 4 % стоимости. На складах 1-го уровня хранятся все виды частей: А, В, С – 100 % номенклатуры; на складах 2-го уровня – до 30 % номенклатуры запасных частей к одной машине (группы А и В); на складах 3-го уровня – до 10 % группы А; на складах 4-го уровня – до 5 % номенклатуры группы А.

502
На складах 1-го и 2-го уровней могут храниться трех-, четырехмесячные запасы, на складах 3-го и 4-го – одно-, двухмесячные запасы. Склады 3-го и 4- го уровней территориально совмещают со службами ремонтов и технического обслуживания. Эффективное управление процессами технической эксплуатации машин возможно лишь при наличии действенной системы учета и отчетности. Для комплексного учета всех данных, связанных с осуществлением технической эксплуатации машин, применяют ЭВМ, с помощью которых представляется возможным значительно углубить анализ действия службы ППР, контролировать выполнение графиков технического обслуживания и ремонтов, управлять запасами запасных частей и эксплуатационных материалов, повысить оперативность учета и отчетности.
12.5. Планирование оптимальной периодичности диагностики
В процессе эксплуатации строительные машины многократно восстанавливаются путем замены отдельных деталей, сборочных единиц, проведения регулировочных работ, ремонтов, поэтому интенсивность отказов, как правило, не достигает максимальной величины, а носит волнообразный характер. Если рассматривать отказы какой-либо детали, то в соответствии с правилом 3 все от-
казы деталей первого поколения уложатся в интервале времени t 3 , т. е. отказы начнут появляться к моменту времени t 3 и будут заканчиваться к моменту t 3 , т. е. в этот период почти полностью заменяются детали первого поколения. Здесь t средний срок службы детали; среднее квадратичное отклонение.
Поскольку элементы первого поколения заменяются не одновременно, то и плотность распределения отказов элементов второго поколения будет иной – более пологой, т. е. максимум наступит примерно при 2t, но меньший по абсолютной величине; среднеквадратичное отклонение также увеличится, с момен-
та 2t 3 начнется замена деталей второго поколения, и в дальнейшем поток отказов стабилизируется. Следовательно, на основе закономерностей изменения параметров потока отказов должна разрабатываться система технического обслуживания и ремонта.
Процессы технических обслуживаний и ремонтов можно описать при помощи аппарата теории вероятностей математически и найти лучший вариант технического обслуживания за счет оптимизации этого процесса. Критерием оптимальности могут служить максимум коэффициента готовности при минимальных затратах на техническое обслуживание и ремонты. Задача определения оптимальной периодичности профилактики должна рассматриваться как задача управления случайным процессом (недетерминированным).
Наибольший интерес представляет проведение профилактических работ по прогнозирующему параметру, в тот момент, когда он достигает критической величины (появление предельно допустимых зазоров, предельного износа, уве-

503
личение расхода топлива или энергозатраты на единицу продукции); при таком положении удельные затраты при проведении профилактических работ будут минимальными, поскольку ремонты машин будут производиться только при действительной необходимости, исключатся лишние ремонты, снизится потребность и расход запасных частей. Это возможно осуществить при проведении постоянного контроля технического состояния машин и сборочных единиц контрольно-диагностической аппаратурой.
Функциональный модуль Фкэ 2,j 6 Ее может быть использован для плани-
рования технической эксплуатации транспортных средств, путем организации оптимального проведения диагностирования технического состояния, технического обслуживания и режимов нагружения их в различных условиях эксплуатации. Техническим состоянием транспортных средств будем называть совокупность подверженных изменению в процессе эксплуатации свойств машины, характеризуемых в определенный момент времени признаками, установленными заво- дом-изготовителем. Техническое состояние имеет следующие градации: исправность, работоспособность, неисправность, неработоспособность, правильное функционирование, неправильное функционирование. Следует отметить, что работоспособность машины может определятся по таким показателям, как небольшой расход топлива, отсутствие шума при включении передачи, равномерное торможение механизмов, легкость управления и т. д. Переход из работоспособного состояния в неработоспособное связан с понятием отказа. При этом машина имеет одно работоспособное состояние, когда все параметры лежат в соответствующих допусках, и множество неработоспособных состояний. Совокупность этого множества соответствует интенсивному числу отказов. Если продолжать эксплуатировать машину за пределами допуска, то наступает отказ, т. е. событие, заключающееся в нарушении работоспособности и приводящее к прекращению выполняемого процесса. Предметом диагностирования является анализ полученных в результате испытаний агрегатов машины с целью выявления вида технического состояния и вида отказа.
Существуют два вида диагностирования: тестовое и функциональное. В процессе диагностирования используются диагностические признаки состояний, которые являются результатами сопоставления параметров или их функций с пределенными областями их значений. Первое осуществляется с помощью специально выбранных воздействий на машину, второе − с помощью эксплуатационных воздействий, соответствующих конкретным различаемым техническим состояниям объ-
екта. Построение алгоритма Фкэ 2,j 6 Ее технологических |
модулей |
под- |
|
системыдиагностики Ек 2 предшествует изучение объекта |
испытаний при |
его |
|
нормальном функционировании, а также определение необходимого |
перечня наи- |
||
более вероятных состояний перехода к неработоспособным |
свойствам узлов ав- |
томобиля, т. е. отказов деталей агрегатов и их комбинаций в машине, которые сле-