
Строительные и дорожные машины. Основы автоматизации
.pdf
484
чески неограниченного числа составов бетонных, растворных или сухих смесей.
Находит применение новая схема компоновки оборудования непрерывного действия — вертикальная, прямоточная, без промежуточных транспортных устройств между дозаторами и бетоносмесителем. При такой компоновке значительно сокращаются размеры завода.
Автоматические дозаторы непрерывного действия снабжаются бесступенчатыми вариаторами скорости с жестким зацеплением и системой автоматики, обеспечивающей дистанционное изменение производительности дозаторов и высокую точность дозирования. Наличие весовой тензометрической платформы позволяет автоматически производить загрузку автомобилей необходимым количеством бетонной или растворной смеси, а также регистрировать число нагруженных автомобилей и фиксировать суммарный вес отпущенного бетона или раствора. В качестве бетоносмесителя для приготовления пластичных и жестких бетонных смесей (с вязкостью до 150 стоксов и крупностью заполнителя до 80 мм), цементно-песчаных растворов любой консистенции и сухих смесей используется двухвальный лопастной бетоносмеситель принудительного действия.
В состав завода-автомата входят: закрытый эстакадно-траншейный склад заполнителей, транспортерные галереи, узел сортировки песка, склад цемента силосного типа, бетоносмесительное отделение, установка автоматической выгрузки смеси. Завод размещается в двух зданиях.
На рис. 11.29 изображена блок-схема управления завода по программе с использованием порционных дозаторов. В такой системе контакты сигнальных реле коммутируют резисторы измерительного семиплечного моста, в котором при этом происходит нарушение равновесного распределения напряжений.
Рис. 11.29. Блок-схема управления заводом:
I) − электрическая связь; II) − механическая связь;1 −компьютер с процессором; 2 − дешифратор; 3 − релейный блок; 4 − усилитель; 5 − серводвигатель; б − реохорд обратной связи; 7 − задающая стрелка с фотореле; 8 − пневмопривод; 9 − впускной затвор дозатора
Сигнал появляется при разбалансе моста и подается на вход электронного усилителя. На выход усилителя подключен двухфазный серводвигатель, перемещающий стрелки с фоторезисторами на угол, соответствующий заданной ве-
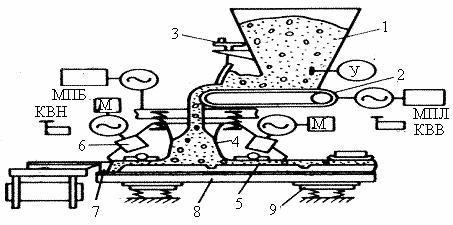
485
личине дозируемого компонента. Со стрелкой сочленен движок реохорда обратной связи, который при движении серводвигателя также получает угловое перемещение.
Движение серводвигателя будет продолжаться до того момента, пока не наступит равновесное состояние измерительного моста.
После остановки стрелки с фотоприставкой в фиксированном положении электрическая схема дозирования получает сигнал на открытие впускного затвора, и дозатор начинает наполняться материалом.
Режимы «грубого» и «точного» взвешивания обеспечиваются установкой на задающей стрелке двух фотореле. При пересечении флажком, укрепленным на подвижной стрелке циферблатного устройства, луча света, направленного на первый фотодатчик, привод впускного затвора включается на импульсный режим работы (досыпка материала).
При достижении номинальной массы флажок на стрелке затемняет второй фотодатчик, после чего закрывается впускной затвор и поступление материала в дозатор прекращается. Аналогичным путем происходит дозировка других компонентов.
Автоматизированное управление бетоноукладчиком. Одним из основных агрегатов при поточно-агрегатном производстве изделий является бетоноукладчик. В зависимости от принятой технологической схемы бетоноукладчики могут иметь различный принцип укладки бетона при формовании. Однако основной принцип – укладка в несколько заходов с вибрированием — сохраняется при любой технологической схеме формования изделия.
Принципиальная технологическая схема с элементами автоматики такого бетоноукладчика изображена на рис. 11.30.
Рис. 11.30. Принципиальная технологическая схема бетоноукладчика с элементами автоматики: 1− бункер; 2 − ленточный питатель; 3 − винтовой привод затвора объемного дозирования бетонной смеси; 4 − копильник вибронасадки; 5 − скользящая плоскость; 6 − вибраторы; 7 − бортовая оснастка; 8 − поддон; 9 − виброплощадка
Для плитных элементов шириной до 3 м смесь из бункера подается ленточным питателем 2 в вибронасадок, равномерно распределяющий ее по форме и уплотняющий поверхность изделия. Корпус вибронасадки подвешен на пру-

486
жинах и образует копильник, в котором автоматически поддерживается постоянный уровень путем изменения величины щели объемного дозатора 3.
На скользящей части вибронасадки установлены маятниковые вибраторы, создающие вертикально направленные колебания, под воздействием которых смесь в копильнике приобретает повышенную подвижность и непрерывно поступает под скользящую поверхность вибронасадка, выполняющую роль неподвижного поверхностного вибратора, опирающегося на борта формы.
При укладке смеси в несколько приемов может быть применена схема, приведенная на рис. 11.31.
Рис.11.31. Принципиальная электрическая схема управления бетоноукладчиком
Бетоноукладчик имеет два крайних положения, которые фиксируются конечными выключателями КВН и КВВ. В автоматическом режиме после нажатия кнопки КПА включается реле Р1, если бетоноукладчик находится в начальном положении. Движение бетоноукладчика будет осуществляться автоматически из одного крайнего положения в другое до тех пор, пока не израсходуется смесь, предназначенная для данного изделия, что фиксируется контактом уровнемера (У).
11.5. Автоматизированное управление конвейером отделки стеновых панелей
Развитие конвейерных линий нашло воплощение не только в технологических линиях по изготовлению строительных элементов, но и в конвейерах для их отделки. На автоматический или полуавтоматический режим могут быть переведены конвейеры отделки наружных и внутренних стеновых панелей. С помощью специальной траверсы изделие краном устанавливается на конвейер, оборудованный цепным приводом. Траверса на катках катится по монорельсу с навешенным на нее изделием. Перемещаясь от поста к посту, изделие отделывается.
На любом посту отделки задача сводится к перемещению механизма, осуществляющего отделку, по определенной траектории, обеспечивающей за полный проход охват всей площади изделия (например, перемещение каретки с

487
распыляющей форсункой). Это могут быть последовательные перемещения вдоль изделия и в направлении вверх − вниз. На рис. 11.32 представлена схема, обеспечивающая автоматический цикл работы на посту в такой последовательности движений механизма отделки поверхности изделия: перемещение каретки механизма слева направо (вперед), перемещение механизма в вертикальной плоскости на некоторую высоту, определяемую шириной отделки, перемещение каретки справа налево (назад), перемещение механизма в вертикальной
плоскости. Далее |
цикл повторяется. |
По окончании |
отделки механизм останавливается. Магнитные пускатели В |
и Н осуществляют пуск двигателя каретки в горизонтальной плоскости, П и С – перемещение механизма отделки в вертикальном направлении (подъем-спуск). Режим (ручной или автоматический) выбирается при помощи универсального переключателя УП: автоматическое управление – положение А, ручное управление — положение Р.
Рис. 11.32. Принципиальная схема работы механизмов на постах отделки конвейера
При ручном режиме нажатием на кнопку П, С, В или Н двигатели включаются на соответствующее направление движения. При автоматическом управлении замыкают последовательно тумблеры Т1 и Т2 или наоборот, в зависимости от того, в каком направлении желательно первоначальное перемещение каретки.
При первоначальном включении тумблера Т1 под напряжение ставится контактор В, включающий двигатель каретки на движение вперед. По достижении кареткой крайнего положения размыкаются контакты конечного выключателя KB В. Контактор В отключается, и движение каретки прекращается. Замкнувшийся контакт контактора В включает пускатель С, а разомкнувшийся контакт В лишает питания обмотку реле времени РВ. Катушка контактора С будет обтекаться током в течение определенного времени, что обеспечивает перемещение механизма отделки на определенную высоту. По окончании выдержки времени катушка контактора С отключается. При этом она замыкает свои блок-контакты
488
вцепях контакторов В и Я. Так как конечный выключатель КВВ разомкнут (каретка находится в крайнем положении вперед), включения контактора В не произойдет. На контактор Н будет подано напряжение, и начнется передвижение каретки в обратном направлении.
Работа механизмов при движении в обратном направлении происходит аналогично. В конце пути замыкается конечный выключатель «назад», механизм делает один шаг в вертикальном направлении, и цикл повторяется.
Управление перемещением по конвейерной линии от поста к посту заключается
всблокированном включении и отключении механизмов подачи. Конвейер имеет две линии (ветви): по одной совершаются рабочие операции, по другой
— освобождение траверсы и возвращение в исходное положение. В начале и в конце конвейера установлены поворотные секции для передачи траверс. Траверсы без изделия передаются с рабочей ветви на холостую в одном конце, а на другом конце, наоборот, с ветви возврата на рабочую ветвь. Привод в таких секциях гидравлический. Направляющая для передвижения траверс выполнена
ввиде двутавровой балки, к которой сверху приварена специальная труба, а по ней перекатывается траверса. Для передвижения траверс с панелями предназначены специальные толкатели холостой и рабочей ветвей, перемещающиеся по своим направляющим.
Конвейер работает следующим образом: траверса с панелями навешивается краном на конвейер отделки, где она проходит все посты. Затем панели снимаются с конвейера и передаются на склад готовой продукции, а пустая траверса навешивается краном на нерабочую ветвь конвейера. Здесь установлены два толкателя: задний – для перекатывания траверсы с приспособлением перевода с рабочей на нерабочую ветвь, передний –для сталкивания траверсы с холостой ветви на рабочую. Перевод траверсы с одной ветви на другую осуществляется автоматически.
Контрольные вопросы по одиннадцатой главе. 1.Основные задачи автоматизации машин. 2. Одинаковы ли схемы электронного управления приводами машин ? 3. Какую функцию выполняет лазерная установка на скрепере ? 4. В каком положении находятся контакты контроллера грузопассажирского подъемника ? 5. Что используют в качестве ограничителя грузоподъемности башенного крана ? 6. Приведите схему ограничителя грузоподъемности с концевым выключателем башенного крана. 7. С помощью какого прибора определяют скорость ветра ? 8. Что из себя представляет датчик креномер. 9. Приведите схему радиоуправления краном. 10. Из каких элементов состоит программное управление для механизмов поворота и вылета стрелы крана ? 11. Показать блок-схему телерадио управления башенным краном. 12.Основные элементы системы управления отвалом автогрейдера.13. По какой схеме работает датчик поперечной стабилизации ? 14. Для чего применяют следящие системы в гидравлических экскаваторах. 15. Показать принципиальную схему глубиномера. 16. Какой метод измерения влажности материалов применяют ? 17. Показать технологическую схему с элементами автоматики приготовления бетонной смеси.
489
12.ОСНОВЫ ЭКСПЛУАТАЦИИ МАШИН
12.1.Понятие «техническая эксплуатация машин»
Под эксплуатацией строительно-дорожных машин принято понимать комплексную систему инженерно-технических и организационных мероприятий, обеспечивающих наиболее эффективное использование возможностей машин, высокую их эксплуатационную надежность, а также минимальные простои при техническом обслуживании (ТО) и ремонте с минимальными затратами. Поэтому как только машина введена в эксплуатацию, возникает ряд вопросов: как спланировать и организовать ТО и ремонт, какие формы наиболее целесообразны для данного типа машин и конкретных условий эксплуатации, что, когда, как и зачем необходимо проверить и отрегулировать.
Технический прогресс в строительном и дорожном машиностроении способствовал принципиальным изменениям в структуре парка машин, повышению единичной мощности и технического уровня конструкций, широкому внедрению во многих типах машин объемного гидропривода, гидрофикации и автоматизации управления, внедрению электроники и микропроцессорной техники, созданию манипуляторов на базе одноковшовых экскаваторов, используемых на практике. Существующий парк машин и его технический уровень позволяют комплексно механизировать основные работы на всех стадиях производства и создают реальные возможности для интенсификации строительства, значительного повышения производительности труда, экономии трудовых и материальных ресурсов.
Увеличение сложности конструкций машин и повышение интенсивности использования строительной техники неразрывно связаны с поддержанием качества машин при их технической эксплуатации, т. е. обеспечением длительной работы машин с максимально возможной производительностью при наименьших затратах. Эти показатели являются критерием оценки оптимальности проведения ТО. Техническое состояние машины устанавливают путем осмотра и испытания на холостом ходу и под нагрузкой. Машины, на которые распространяются требования Госгортехнадзора, при приемке и сдаче в эксплуатацию подвергаются полному техническому освидетельствованию, включающему статические и динамические испытания. Новые и капитально отремонтированные машины перед сдачей в эксплуатацию подвергаются эксплуатационной обкатке. При обкатке происходит приработка деталей. Режим обкатки определяется заводом-изготовителем. Первоначально обкатка ведется на холостом ходу, а затем с постепенным или мелкошаговым увеличением действующих нагрузок. На последнем этапе обкатки машину эксплуатируют в легком режиме в течение 20...25 ч. После завершения обкатки выполняют все крепежные и контрольнорегулировочные работы, устраняют замеченные неисправности, заменяют смазку и эксплуатационные жидкости. О вводе машины в эксплуатацию делают соответствующую запись в паспорте. Каждая машина, находящаяся в эксплуа-
490
тации, проходит ежесменную сдачу и приемку, при которой машину смазывают, проверяют работу на холостых движениях и под нагрузкой, работу тормозов, управления и приборов безопасности. Замеченные неисправности устраняют, о чем делается запись в журнале. Комплекс организационно-технических мероприятий, проводимых в плановом порядке для обеспечения работоспособности машин в течение всего срока их службы при соблюдении заданных условий и режимов эксплуатации, называется системой планово-
предупредительного технического обслуживания и ремонта (ППР). Система называется плановой потому, что все ее мероприятия выполняют по разработанному плану, а предупредительной потому, что входящие в нее мероприятия носят профилактический характер, т. е. направлены на предупреждение износа оборудования и внезапных выходов его из строя. Данная система основана на обязательном планировании и проведении по каждой машине, находящейся в эксплуатации, соответствующих видов технических обслуживании и ремонтов с заданной последовательностью и периодичностью.
Периодичность проведения технических обслуживании и ремонтов определяется наработкой машины, измеряемой в мото-часах, километрах пробега, часах и киловатт-часах (кВт∙ч). Время работы от начала эксплуатации машины до первого капитального ремонта, измеренное в часах работы машины, называется межремонтным, циклом, а число часов работы машины между одноименными техническими обслуживаниями или ремонтами — периодичностью технических обслуживании и ремонтов. Система ППР предусматривает проведение технического обслуживания (ТО), текущих (Т) и капитальных (К) ремонтов. Рекомендациями по организации технического обслуживания и ремонта строительных машин установлены нормы периодичности и количество технических обслуживании и ремонтов, средняя трудоемкость и продолжительность их. Так, для одноковшовых экскаваторов четвертой размерной группы установлена периодичность межремонтного цикла до первого капитального ремонта 12 000 ч. За это время экскаваторы проходят 72 технических обслуживании и семь текущих ремонтов с определенной для каждого из них периодичностью. Конкретно периодичность, состав работ по каждому виду ТО и ремонту указываются в технической документации, прилагаемой в обязательном порядке к каждой машине. Увеличение сложности машин и их интенсивное использование обусловили широкое применение для технического обслуживания и ремонта специализированных организаций. Такие специализированные службы ТО и ремонта сосредоточены в специализированных трестах и управлениях механизации, при которых созданы ремонтно-эксплуатационные базы. Они включают участки диагностирования, которому подвергаются машины, проходящие ТО и Т, участки ТО со специализированными постами, участки ТО, специализирующиеся в ремонте гидропневмоаппаратуры и наиболее ответственных узлов машин — двигателей, коробок передач, редукторов, мостов и т. п. Значительную часть объемов работ по ТО выполняют на рабочем месте с помощью мобильных средств. Для этих целей созданы передвижные станции технического обслужи-
491
вания, оснащенные необходимым, в том числе диагностическим оборудованием. Передвижные ремонтные мастерские специализированы по типам машин: для башенных кранов, экскаваторов, общестроительных машин.
12.2. Понятие об эксплуатационной надежности машин
Любая машина, выполняя определенные функции, находится во взаимодействии со средой и человеком, управляющим этой машиной. При этом возникают разнообразные причинно-следственные связи как формы проявления всеобщей универсальной связи явлений в природе. Накопление различных воздействий на машину приводит к эволюции ее качественных показателей и, в соответствии с законами диалектики, к возможности перехода в иное качественное состояние. Поэтому изменения, которые происходят в машине при ее эксплуатации, являются закономерным проявлением важнейшего неотъемлемого свойства всех материальных объектов движения в его философском понимании, ибо ничего неизменного в природе нет. Мы можем замедлить нежелательные для нас изменения, сделать так, чтобы отклонения качественных показателей машины находились в течение необходимого времени в допустимых пределах, но исключить их полностью нельзя. На машину действуют все виды энергии: механическая, тепловая, химическая, электромагнитная и вызывают в ней необратимые изменения. Машину нельзя изолировать от влияния среды, в которой она работает, от влияния процессов, которые протекают в ней самой при осуществлении рабочих функций, от действия остаточных напряжений, являющихся следствием технологических процессов, применявшихся при изготовлении машины. Но поскольку любая машина используется по назначению в течение определенного длительного времени, под влиянием различных факторов могут изменятся свойства, которые определяют ее качество. Поэтому надежность, изучающая изменение показателей качества во времени, является как бы динамикой качества, его разверткой во времени. При этом количественное накопление необратимых процессов в машине приводит к ее качественным изменениям, т. е. протекающие явления подчиняются закону перехода количества в качество.
С изменением качественных показателей машины во времени для поддержания ее в работоспособном состоянии прежде всего необходимо учитывать причины и источники вредных воздействий на машину, исследовав физическую сущность процессов, снижающих ее работоспособность, изучить реакцию машины на различные воздействия и на основании этого создать такие системы, которые могли бы в течение необходимого периода выполнять заданные функции в установленных пределах.
Умение управлять техническим состоянием машин и, как следствие, работоспособностью в период ее использования по назначению и является основной задачей технической эксплуатации.


493
определенного вида изнашивания, при установленных условиях его протекания и для выбранного сечения материала, т.е. устанавливают определенный круг ограничений. Это дает возможность решить многие вопросы прогнозных расчетов и прогнозирования работоспособности изделий. Основными параметрами, влияющими на изнашивание, являются скорость относительного скольжения vск и давление на поверхности трения р.
Анализ исследований изнашивания различных материалов в условиях граничной смазки и трения без смазки при установившемся процессе показывает, что в общем случае скорость изнашивания может быть выражена зависимостью
(12.1)
где k коэффициент пропорциональности, характеризующий материал пары и условия изнашивания, в частности, смазочный материал. Размерность коэффициента к обратная размерности давления; р– давление на поверхности трения; m=0,5…3 – коэффициент.
Для большинства пар трения n 1. Для абразивного и ряда других видов из-
нашивания m n 1, тогда |
|
|
|
|
||||||
|
vск кр vck , |
|
|
|
(12.2) |
|||||
а линейный износ |
|
|
|
|
||||||
|
u vизнt kpvckt kpS , |
(12.3) |
||||||||
где S путь трения; t – время. |
|
|
|
|
||||||
|
Интенсивность изнашивания, исходя из дискретного касания твердых тел, |
|||||||||
в общем виде может быть выражена зависимостью |
|
|||||||||
|
|
pн |
|
К0 |
|
|
|
|
|
|
|
I |
|
|
|
h |
, |
|
|||
|
рф nц |
|
|
|||||||
|
|
R |
|
|||||||
где |
pн / pф отношение номинального давления к |
фактическому |
pн / pф 0,1...0,001 ; К0 0,18...0,22 постоянная, характеризующая распреде-
ление неровностей по высоте; nц базовое число циклов до разрушения неров-
ностей nц 105....1012 . Величину nц определяют экспериментально, исходя из фрикционной зависимости или по формуле
nц К0 fТТ рф y ,
где Т предел текучести; fТ коэффициент трения; у – показатель, завися-
щий от смазки и механических свойств трущихся тел ( в условиях упругого контакта у =10…15); h/R отношение глубины внедрения единичной неровности к ее радиусу (h/R характеризует вид взаимодействия: упругое, пластическое, микрорезание. Обычно контакт бывает упругим, поэтому
h/R 0,1...0,0001).
На скорость изнашивание существенное влияние оказывают механические характеристики материалов, их химический состав и структура. Для чистых металлов и термически необработанных сталей при абразивном изнашивании су-