
Строительные и дорожные машины. Основы автоматизации
.pdf474
Принцип работы глубиномера основан на измерении длины троса, вытравленного с барабана главной лебедки, и угла подъема стрелы. Ползунки потенциометров RT и Rc связаны посредством передач с барабаном главной лебедки и стрелой экскаватора. Перед началом работы переменными сопротивлениями R1 и R2 микроамперметр, включенный в диагональ моста M, устанавливается на нуль. При этом загорается лампа ЛC. Затем устанавливается глубина разработки с помощью этих же сопротивлений. Сигнал, обусловленный разбалансом моста, подается на вариатор, усилитель и выходное реле PC. Когда в процессе работы экскаватора будет достигнута заданная величина заглубления, сопротивления RT и Rc примут такое значение, что мост будет сбалансирован и реле PC выдаст соответствующий сигнал в систему управления и на сигнальную лампу ЛС.
Автоматический учет работы строительных машин. Увеличение произ-
водительности строительного оборудования зависит от наиболее полного использования мощности и времени работы, что неразрывно связано с более эффективным проведением учета работы машин.
Последнее обеспечивает: контроль за работой машин и принятие соответствующих мер для их правильного использования, возможность планирования выполнения ремонта не по времени нахождения машины на строительной площадке, а в зависимости от фактического времени работы и выработки машин уточнение, и разработку норм времени и расценок, возможность оплаты труда персонала в точном соответствии с фактически выполненной работой.
Рассмотрим систему автоматического учета работы скреперов, которая заключается в регистрации количества рейсов, затраченных на перевозку грунта с места разработки к объекту выгрузки, учете числа полногрузных рейсов скрепера и средней дальности перевозки грунта. Датчик веса 1 (рис.11.22) предназначен для замыкания электрической цепи при номинальной величине загрузки скрепера. Датчик угла наклона 2 служит для блокировки датчика веса с целью защиты устройства от ложных и непреднамеренных срабатываний. Датчик электроспидометра 4 и электроспидометр5 фиксируют километраж, пройденный скрепером с номинальным грузом. Датчик угла подъема днища предназначен для замыкания цепи счетчика рейсов 7, реле 11 и элемента задержки 13, 14. Датчик заполнения ковша скрепера сигнализирует о достаточном заполнении ковша.
При наполнении ковша срабатывает датчик 6, сигнализируя об окончании набора грунта, после чего начинается подъем ковша. При помощи датчика веса 1 по величине усилия в канате определяется достаточность заполнения ковша. При соответствии веса ковша номинальному (заданному) и при определении значения угла наклона ковша сигналы с датчиков поступают на реле 8, 9 и 10, и датчик электроспидометра 4 получает питание. Процесс набора грунта закончен. При транспортировании грунта к месту выгрузки датчик 4 посылает в электроспидометр сигналы в виде импульсов для подсчета пройденного пути.
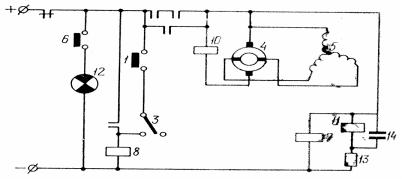
475
Операция подъема ковша днища фиксируется датчиком угла подъема днища 3, который подает сигнал на счетчик рейсов. Фиксация очередного рейса возможна лишь при условии последовательного срабатывания датчиков веса, угла наклона ковша скрепера, электроспидометра и угла наклона днища.
Рис. 11.22. Принципиальная схема системы автоматического учета работы скрепера: 1− датчик веса; 2 − датчик угла наклона; 3 − переключатель; 4, 5 − электроспидометры; 6 − датчик наполнения ковша; 7 − счетчик рейсов; 8,11 −реле; 12 − лампа сигнальная;
13, 14 −элементы задержки
Автоматический учет работы других строительных машин может отличаться от рассмотренного в связи с особенностями технологического процесса машины. Так, например, система автоматического учета работы экскаватора может включать приборы для учета числа циклов, суммарного времени и веса перегруженного грунта. Последнее может быть осуществлено при помощи двух потенциометрических датчиков усилия, параллельно используемых в системах автоматической защиты технологического оборудования, по результирующему сигналу, величина которого пропорциональна весу грунта в ковше. Следует заметить, что в большинстве случаев для автоматического учета используются средства автоматики, имеющие, кроме того, и другие задачи.
11.5. Автоматизация машин и оборудования производства бетонных смесей и растворов
При приготовлении бетонных смесей и растворов автоматизируются следующие операции: подача материалов в подготовительное отделение, дозирование компонентов, перемешивание, выгрузка смеси и подача ее на посты формования (на заводах).
На заводах железобетонных изделий заполнители со склада транспортируются в расходные бункера подготовительного отделения при помощи различных транспортирующих устройств. Кроме того, перед поступлением в дозировочное отделение материалы подвергаются подогреву (в зимнее время) и сушке.
476
При транспортировании материалов с целью повышения производительности и надежности работы систем осуществляются автоматическое управление приводами механизмов конвейерных линий, автоматический контроль за наличием материалов, их влажности, контроль целостности ленты и забивки течек. Для нормального хода технологического процесса необходимо соблюдать следующие правила:
1)обеспечивать определенную последовательность запуска двигателей отдельных звеньев транспортирующей цепи; во избежание завала конвейера материалом пуск двигателей должен протекать в направлении, противоположном грузопотоку;
2)производить остановку двигателей в направлении, противоположном грузопотоку;
3)отключать все двигатели, посредством которых осуществляется подача материала к поврежденному звену, при аварийном отключении какого-либо из двигателей. Двигатели, находящиеся за поврежденным участком (по ходу материала), должны продолжать работать;
4)предусматривать возможность раздельного пуска двигателей, необходимого для наладки и опробования системы;
5)предусматривать возможность аварийной остановки конвейерной линии
слюбого места;
6)подавать перед пуском предупредительный сигнал.
На рис. 11.23 приведена схема автоматического управления тремя двигателями конвейерной линии, состоящей из трех звеньев, отвечающая сформулированным выше требованиям.
Выбор режима осуществляется универсальным переключателем УП, имеющим три положения: М — местный; Л — автоматический; О — отключено. При местном режиме управления каждый из механизмов может быть включен самостоятельно при помощи кнопок КП. При автоматическом режиме пуск системы производится при наличии нижнего уровня в приемном бункере НУП и при наличии материала в расходном бункере. НУР. Отключение происходит при достижении верхнего уровня в приемном бункере ВУП или при помощи дистанционной кнопки остановки системы КСД. Пуск последующих механизмов осуществляется при включенных предыдущих при помощи реле PC.
Вентиль расходного бункера СРВ открывается при включенном транспортере № 3 (реле РСЗ). Подача материала на транспортер из бункеров может осуществляться также вибролотками или виброзатворами-питателями.

477
Рис. 11.23. Схема управления механизмами загрузки и разгрузки конвейеров
На рис. 11.24, а приведена схема управления виброзатвором-питателем.
Рис.11.24. Схема управления механизмами загрузки (а) и разгрузки конвейеров (б)
При нажатии кнопки КМ или КП ставится под напряжение катушка промежуточного реле 1РПВ, которое, срабатывая, подключает катушку контактора 1KB. Последний подает напряжение на электромагнит виброзатворапитателя. Кнопка КМ установлена около виброзатвора-питателя, а кнопка КП — на пульте диспетчера.
Разгрузка ленточных конвейеров может осуществляться посредством плужковых сбрасывателей, представляющих собой стальную пластину, опускаемую на ленту. Под воздействием противовеса плужок-сбрасыватель приподнимается. Для осуществления разгрузки необходимо поставить плужок-сбрасыватель в рабочее положение — опустить его. Это осуществляется с помощью электромагнита.
Схема автоматического управления плужковым сбрасывателем приведена на рис. 11.25, б. При неполном бункере контакты реле уровня IУ замкнуты. Промежуточное реле РП обтекается током и своими контактами включает катушку магнитного пускателя П. Последний подключает к сети электромагнит

478
плужкового сбрасывателя ЭПС, происходит опускание плужка на транспортер, в результате чего материал начинает поступать в бункер.
При наличии нескольких бункеров отыскание незаполненного бункера производится при помощи шаговых искателей, которые включают в работу соответствующие плужковые сбрасыватели путем подачи импульсов в цепь реле управления плужками. Для контроля наличия материалов на ленте конвейера применяется датчик наличия материалов (рис. 11.24). Датчик устанавливается над конвейерной лентой у места ссыпки материала. Если материал на конвейерной ленте отсутствует, то рычаг 4 находится в вертикальном положении, и контакт выключается. При прохождении материала рычаг 4 отклоняется влево, поворачиваясь относительно точки 5, и замыкает контакт. Чувствительность датчика регулируется соотношением плеч рычагов. При обычном соотношении плеч ртутный контакт включается после отклонения рычага на 5…7°, что соответствует высоте слоя 3…5 мм.
Рис. 11.25. Контактный датчик наличия материала на ленте конвейера: 1− лента конвейера; 2 − материал; 3 − резина; 4 − рычаг; 5 − шарнир;
6 − конечный выключатель
Для контроля целостности ленты может быть использован обычный конечный выключатель, воспринимающий натяжение ленты.
Определение влажности строительных материалов в заводских условиях является важной технологической операцией, необходимой для правильной дозировки воды при приготовлении бетонной смеси. Наибольшее значение имеет определение влажности песка.
Сведения о водоцементном отношении свежеприготовленного бетона позволяют корректировать процесс тепловлажностной обработки для получения гарантированного качества железобетонных изделий.
Наиболее широкое распространение получил метод высушивания образца. Сущность метода состоит в определении разности веса образцов до и после высушивания. В последнее время получают применение электрофизические и радиофизические методы определения влажности, для которых характерна быстрота анализа. Рассмотрим наиболее перспективные приборы для контроля влажности разнообразных строительных материалов и изделий.
В настоящее время широкое распространение получают СВЧ-методы измерения влажности строительных материалов, которые основаны на зависимости

479
поглощения СВЧ-энергии от количества воды в материале. Эта зависимость линейна в широком диапазоне измерения влагосодержания. Источниками электромагнитного излучения являются клистроны, генерирующие в диапазоне сверхвысоких частот. СВЧ-влагомер состоит из пяти функциональных блоков, смонтированных в общем каркасе: генератора СВЧ, выпрямителей, преобразователя, аттенюатора и узкополосного усилителя. На рис. 11.26 показана принципиальная схема СВЧ-влагомера. Генератор СВЧ 1 собран на клистроне типа К-29. Высокочастотная энергия возбуждает волновод прямоугольного сечения с помощью петли связи. Модуляция клистрона осуществляется путем подачи прямоугольного импульса через разделительный конденсатор С с обмотки трансформатора блока 2. Блок питания 2 обеспечивает подачу на клистрон постоянных стабилизированных напряжений 350, 150 и 12 В.
Рис. 11.26. Схема СВЧ-влагомера:
1 − генератор СВЧ; 2 − блок питания; 3, 4 − блоки преобразования; 5 − блок узкополос ного усилителя; 6 − оконечный усилитель; 7 − испытуемый материал;
AT− блок аттенюаторов; ин −индикатор
Блок преобразования 3 обеспечивает преобразование постоянного напряжения 12 В, получаемого от аккумуляторов, в переменное напряжение прямоугольной формы частотой 1000 Гц, которое вырабатывается генератором, собранным по схеме мультивибратора, с парафазным усилителем на транзисторах. Мощный усилитель 4 работает в ключевом режиме, что обеспечивает хорошую прямоугольную форму сигнала. Принятые меры стабилизации дают возможность получить стабильные напряжения на выходе преобразователя.
Блок аттенюаторов АТ1,2 состоит из двух секций, дающих различное ослабление. Плавная регулировка ослабления осуществляется перемещением поглотителей. Блок узкополосного усилителя 5 на 1000 Гц собран на трех транзисторах типа МП-42 и МП-103.
В зависимости от количества воды в материале генерируемая блоком 1 СВЧ-энергия поглощается в волноводе в разной степени, что фиксируется прибором ИП-1, являющимся нагрузкой последнего каскада усилителя 6. В качестве прибора используется микроамперметр, включенный в диагональ моста. Не менее перспективными, чем СВЧ-влагомеры, являются приборы и устройства, основанные на нейтронном методе. Принцип действия этих влагомеров построен на зависимости числа медленных нейтронов, прошедших через толщу испытуемого материала, от влажности последнего. Нейтронные влагомеры со-

480
стоят из источника нейтронов, например смеси полония и бериллия, и счетнозапоминающего устройства. Эти приборы могут быть применены как в лабораторных, так и в заводских условиях.
Прибор для определения влажности при помощи двух термометров (сухого и влажного) называется психрометром. Влажный термометр отличается от сухого тем, что его термоприемник (например, резервуар с ртутью у ртутного термометра) в процессе измерения поддерживается увлажненным. По показаниям сухого и влажного термометров с помощью психрометрических таблиц, номограмм или счетных линеек, рассчитанных по психрометрической формуле, определяется упругость водяного пара в миллиметрах (миллибарах) или относительная влажность. Измерения при помощи психрометра производятся главным образом при положительных температурах воздуха, так как при отрицательных температурах (в особенности ниже –5 °С) определение влажности по психрометру становится ненадежным.
Существует несколько типов психрометров: а) аспирационные, состоящие из двух одинаковых ртутных термометров и имеющие искусственную вентиляцию термоприемников; б) стационарные, состоящие из двух одинаковых ртутных или спиртовых термометров, помещаемых на специальном штативе в метеорологическую будку; в) дистанционные и самопишущие, в которых вместо ртутных термометров используют два электрических термометра сопротивления, термисторы и термопары. Некоторые из этих психрометров указывают непосредственно относительную влажность в процентах.
Реле влажности психрометрическое (рис. 11.27) позволяет получить сигнал о достижении влажности определенного значения (контролировать влажность).
Рис. 11.27. Реле влажности психрометрическое:
1 − влажный термометр; 2 , 8 − сильфоны; 3 − пружина; 4, 6 − гайки; 5 − рычаг; 7 − сухой термометр; 9 − магнит; 10 −контакты
В этом приборе в качестве чувствительного элемента использованы сухой 7 и влажный 1 манометрические термометры. Рычаг 5, переключающий контакты 10, находится под действием разности усилий, возникающих при переме-

481
щении сильфонов 2 и 8. Настройка диапазона производится натяжением пружины 3 гайкой 4. Гайка 6 позволяет регулировать дифференциал. Магнит 9 обеспечивает четкость размыкания контактов.
Рассмотрим технологическую схему с элементами автоматики, изображенную на рис. 11.28.
Рис 11.28. Технологическая схема с элементами автоматики приготовления бетонной смеси
Согласно этой схеме, компоненты бетонной смеси — песок и щебень необходимых фракций — подаются со склада заполнителей наклонным ленточным конвейером и при помощи поворотной воронки засыпаются в соответствующие отсеки питающего бункера.
Цемент со склада по пневмопроводу поступает в циклон, откуда посредством шнека через течки направляется в соответствующие отсеки бункера. Заполнение материалами отсеков питающих бункеров контролируется уровнемерами типа УКМ. Поступление материалов в весовые бункера дозаторов осуществляется через соответствующие впускные затворы. Отдозированные компоненты через выпускные затворы дозаторов подаются в одну из бетономешалок. Загрузка ее производится при помощи перекидного шибера для сухих компонентов ПШ.
482
Технологической схемой предусмотрено весовое дозирование воды. Вода из расходных баков через впускной клапан поступает в дозатор и далее в один из бетоносмесителей. Выбранный бетоносмеситель загружают при помощи перекидного шибера для воды ПШВ. Схемой управления предусматривается одновременное переключение шиберов ПШ и ПШВ.
Отдозированные компоненты перемешиваются в бетоносмесителе в течение определенного времени контролируемым командным прибором, при помощи которого задается очередность загрузки работающей бетономешалки отдозированными компонентами. По окончании цикла перемешивания готовая смесь поступает в расходные бункера. Управление впускными и выпускными затворами дозаторов, перекидными шиберами, опрокидывание бетономешалок, открытие люков расходных бункеров осуществляют посредством пневмоприводов с электромагнитными клапанами. Конечные положения рабочих органов перечисленных механизмов фиксируются конечными выключателями, подающими соответствующие команды в схему управления. Автоматизация дозирования материалов выполнена на весовых циферблатных указателях, оснащенных бесконтактными электронными датчиками. Предусмотрена дистанционная передача показаний веса дозируемых компонентов на центральный пульт оператора и дистанционная задача рецептов. Для этой цели дистанционные циферблатные указатели всех дозаторов устанавливаются в пультовом помещении бетоносмесительного цеха.
Оператор имеет возможность по требованию лаборатории устанавливать дозы взвешиваемых компонентов или вносить необходимые коррективы в рецептуру, а также контролировать процесс взвешивания непосредственно в пультовом помещении.
Автоматизация управления операциями технологического процесса в функции времени осуществляется командным электропневматическим прибором КЭГ1-12У.
Заданный вес дозируемых компонентов (цемента, песка, щебня первой фракции, щебня второй фракции и воды) устанавливается при помощи переключателей, расположенных на пульте управления. Количество задаваемых доз каждого компонента при этом равно числу датчиков, установленных на дистанционном циферблатном указателе (пять). Шестой датчик устанавливается в начало шкалы для фиксации нулевого веса. Датчики расставляются по окружности шкалы циферблатных указателей в соответствии с заданной рецептурой, составляющей в определенных весовых соотношениях пять различных марок бетонной смеси.
При помощи переключателей выбирается нужный отсек питающего бункера, содержащий определенную фракцию материала (цемента, песка, щебня). Задается автоматический режим работы дозаторов, бетоносмесителя и другого оборудования. Начинается одновременная загрузка компонентов в весовые бункера всех дозаторов. По мере поступления в них материала стрелки на дистанционных циферблатных указателях соответствующих дозаторов достигают вклю-
483
ченных датчиков. В момент прохождения стрелок с флажками через прорезь включенных датчиков срабатывают реле, находящиеся в блоках питания.
По окончании взвешивания компонентов производится загрузка свободного бетоносмесителя.
С момента включения двигателя одного из командных аппаратов начинается поочередная загрузка компонентов в работающий бетоносмеситель.
По мере загрузки дозаторов стрелки циферблатных указателей возвращаются в нулевое положение, в котором устанавливаются датчики нулевого веса. В момент прохождения стрелок с флажками через прорези этих датчиков срабатывают реле нулевого веса, расположенные в блоках питания дозаторов соответственно цемента, песка, щебня и воды.
После разгрузки дозаторов в один из бетоносмесителей оператор нажатием кнопки может повторить цикл автоматического взвешивания компонентов и последующей загрузки их в другой бетоносмеситель.
Далее следует операция перемешивания. Время перемешивания устанавливается технологической лабораторией. Затем следуют операции опрокидывания, освобождения бетоносмесителя и возврата его в исходное горизонтальное положение.
Начало отсчета времени разгрузки бетономешалки фиксируется конечным выключателем, который срабатывает на отключение при выгрузке. При этом бетоносмеситель возвращается в исходное положение.
Порядок работы второго бетоносмесителя аналогичен рассмотренному. Управление электродвигателями вращения первого и второго бетоносмесителей может осуществляться путем нажатия кнопок. Для обеспечения безопасных условий работы схемой предусмотрена звуковая сигнализация, включающаяся перед пуском бетоносмесителей. Запуск электродвигателей вращения бетоносмесителей возможен только после подачи звукового сигнала. Количество замесов, приготовленных на обоих бетоносмесителях, фиксируется при помощи импульсного счетчика.
Кроме автоматического управления предусматривается дистанционное ручное управление механизмами. Режим управления выбирается при помощи ключа на пульте управления.
Для выполнения наладочных и ремонтных работ в надбункерном, дозаторном и смесительном отделениях предусмотрены пульты местного управления.
Управление всеми производственными процессами бетоносмесительного узла осуществляется одним оператором с центрального пульта. В операторской кроме центрального пульта управления размещены циферблатные дистанционные указатели и щит технологической световой сигнализации.
На бетонорастворных заводах-автоматах подача исходных материалов, выбор марки бетона или раствора, дозирование, смешивание и выдача бетонных и растворных смесей осуществляются автоматически по программе, закодированной на перфокарте. Применение бесконтактного программно-считывающего устройства на полупроводниковых элементах обеспечивает получение практи-